第九讲 夹紧力的分析与估算
夹紧力计算

夹紧力计算及夹紧气缸的设计1、夹紧力的计算工件资料为 AS9U3,大平面加工余量为,采纳硬质合金端铣刀加工,切削力查参照文件〔 1〕可依据以下公式计算:F0.25 cFX FaPX F a f y f a w V F Z KFZZd0q F n w f? 式中: Fz ---铣削力 (N)a f ---每齿进给量 (mm/r)a w---铣削宽度 (mm)---铣削力修正系数K FZd0---铣刀外径 (mm)a ---铣削深度 (mm)pz---? 铣刀齿数确立各参数值 :(1). 铣刀外径d0=315mm;(2). 铣刀齿数 Z=16;(3). 每齿进给量 af 是铣刀每转一个刀齿时铣刀对工件的进量:a f =V f/(z·n)=360/(16×720)=r(4). 铣削深度a p关于端铣刀是指平行于铣刀轴线丈量的被铣削层尺寸:a p=(5).铣削宽度a w关于端铣刀是指垂直于铣刀轴线丈量的被切削层尺寸:a w=240mm(6).修正系数K FZ取;由表查得 : c F=7750x F=y F=u F=w F=q F=1.00.75 1.11677501.50.031240F0.25 1.30.2 1.6Z315720Fz==28Kg(7).理论所需夹紧力计算确立安全系数 :总的安全系数 k=k1·k2· k3·k4k 1----一般安全系数;k1取;k 2----加工状态系数;因为是精加工,所以 k2取 1;k 3----刀具钝化系数;k 3取;k 4----断续切削系数;k 4取;∴ k =× 1××≈ 3W=k·p=3×28kg= 84kg2.气缸的选择Q=W /(i ·η 1·n) = 84/ ×× 3) =44kg 由气缸传动的计算公式:Q=P· ( πD 2/4) ·η式中 :P--压缩空气压力=6atm=6kg/cm2η-- 气缸摩擦系数,取i—压板与工件的摩擦系数 , 取n—夹紧气缸个数 , 本夹具为 3D-- 气缸直径 (cm)4Q444Dp 6 3.140.8D=经过以上理论计算,能够选择直径为50mm的气缸。
夹具压紧力计算公式
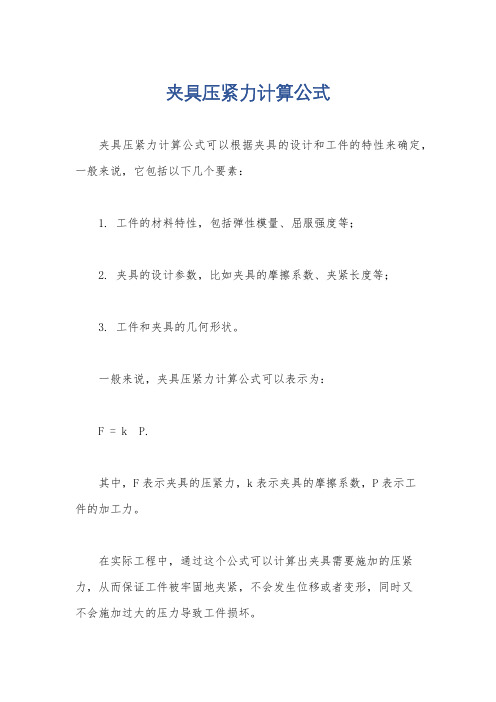
夹具压紧力计算公式
夹具压紧力计算公式可以根据夹具的设计和工件的特性来确定,一般来说,它包括以下几个要素:
1. 工件的材料特性,包括弹性模量、屈服强度等;
2. 夹具的设计参数,比如夹具的摩擦系数、夹紧长度等;
3. 工件和夹具的几何形状。
一般来说,夹具压紧力计算公式可以表示为:
F = k P.
其中,F表示夹具的压紧力,k表示夹具的摩擦系数,P表示工
件的加工力。
在实际工程中,通过这个公式可以计算出夹具需要施加的压紧力,从而保证工件被牢固地夹紧,不会发生位移或者变形,同时又
不会施加过大的压力导致工件损坏。
因此,夹具压紧力计算公式在工程领域中具有重要的意义,它可以帮助工程师们设计出合理的夹具结构,确保工件加工的质量和效率。
夹紧力计算
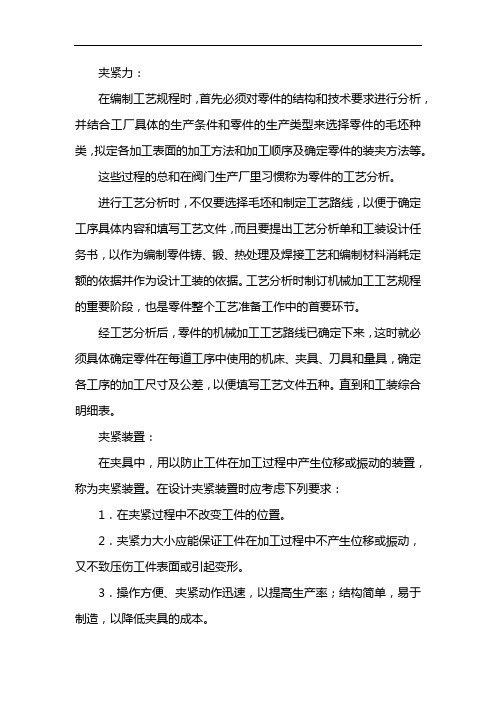
夹紧力:在编制工艺规程时,首先必须对零件的结构和技术要求进行分析,并结合工厂具体的生产条件和零件的生产类型来选择零件的毛坯种类,拟定各加工表面的加工方法和加工顺序及确定零件的装夹方法等。
这些过程的总和在阀门生产厂里习惯称为零件的工艺分析。
进行工艺分析时,不仅要选择毛坯和制定工艺路线,以便于确定工序具体内容和填写工艺文件,而且要提出工艺分析单和工装设计任务书,以作为编制零件铸、锻、热处理及焊接工艺和编制材料消耗定额的依据并作为设计工装的依据。
工艺分析时制订机械加工工艺规程的重要阶段,也是零件整个工艺准备工作中的首要环节。
经工艺分析后,零件的机械加工工艺路线已确定下来,这时就必须具体确定零件在每道工序中使用的机床、夹具、刀具和量具,确定各工序的加工尺寸及公差,以便填写工艺文件五种。
直到和工装综合明细表。
夹紧装置:在夹具中,用以防止工件在加工过程中产生位移或振动的装置,称为夹紧装置。
在设计夹紧装置时应考虑下列要求:1.在夹紧过程中不改变工件的位置。
2.夹紧力大小应能保证工件在加工过程中不产生位移或振动,又不致压伤工件表面或引起变形。
3.操作方便、夹紧动作迅速,以提高生产率;结构简单,易于制造,以降低夹具的成本。
4.能自锁,即在原始力去除后,仍能保持工件的夹紧状态。
5.操作安全、劳动强度小。
现代夹具设计手册:内容简介:本手册全面总结了我国半个世纪来的工业化过程中机械制造业内设计制造各类夹具的丰富经验,绝大部分资料都通过生产实践的考验,包括从国外引进后消化、吸收和改进的内容,也包含作者以往亲历的研发项目的成果。
图书目录:序第1章夹具总论1.1 夹具产生和发展的背景1.1.1 夹具和机床附件1.1.2 机床专用夹具催生了现代大批大量生产1.1.3 夹具是现代制造系统的重要组成部分1.2 夹具的功能、组成和设计要求1.2.1 夹具的基本结构和组成1.2.2 夹具的各种功能1.2.3 设计夹具的基本要求1.3 夹具和机械零件的分类1.3.1 夹具的各种分类方法1.3.2 根据生产规模或品种和批量的分类最重要1.3.3 机械零件和夹具分类编码系统1.4 夹具系统的选择和技术经济指标1.4.1 选择夹具系统的基本原则1.4.2 选择夹具系统的步骤1.4.3 常用夹具系统的技术经济指标1.4.4 夹具设计制作成本的估算1.4.5 使用专用夹具的简易经济分析1.4.6 夹具系统的经济分析1.5 现代夹具发展趋势1.5.1 夹具柔性化1.5.2 夹具自动化和智能化1.5.3 计算机辅助夹具设计(CAD)1.5.4 应对“寻位-加工”的挑战1.5.5 结语第2章夹具功能部件的典型结构2.1 定位装置典型结构2.1.1 插销定位装置2.1.2 V形块定位装置2.1.3 齿轮齿形定位装置2.1.4 其他特殊定位装置2.2 定位支承装置典型结构2.2.1 可调支承典型结构2.2.2 辅助支承典型结构2.3 夹紧装置典型结构2.3.1 螺旋夹紧典型结构2.3.2 快速螺旋夹紧典型结构2.3.3 斜楔夹紧典型结构2.3.4 偏心(凸轮)夹紧典型结构2.3.5 端面凸轮夹紧典型结构2.3.6 铰链夹紧典型结构2.3.7 联动夹紧典型结构2.3.8 可移动位置的典型夹紧结构2.3.9 气(液)动自动夹紧装置典型结构2.3.10 自动定心夹紧典型结构2.3.11 肘节式快速夹紧装置2.3.12 其他特种类型夹紧装置2.4 分度装置典型结构2.4.1 分度定位销2.4.2 典型分度装置2.4.3 精密分度装置第3章夹具设计计算3.1 定位尺寸的相关计算3.1.1 V形块的计算3.1.2 夹具上两定位销的尺寸及定位误差的计算3.1.3 夹具上定位销的尺寸及定位误差的计算3.1.4 定位销高度的计算3.1.5 小锥度心轴尺寸的计算3.1.6 带圆柱部分的锥度心轴尺寸的计算3.1.7 压入配合光滑心轴尺寸的计算3.1.8 滚柱心轴的尺寸及有关计算3.1.9 齿轮按渐开线齿形定位时的计算3.1.10 三圆弧自定心夹紧机构偏心圆弧尺寸的计算3.1.11 钻斜孔钻模工艺基准孔中心至钻套孔轴线间的距离x的计算3.1.12 弹簧夹头结构尺寸的计算3.2 定位误差的计算3.2.1 常见定位形式的定位精度计算3.2.2 钻模的钻孔精度计算3.2.3 用定位销定位的分度装置的分度概率精度3.3 典型夹紧形式的夹紧力计算3.3.1 计算时的计算系数3.3.2 常见典型夹紧形式所需夹紧力的计算3.4 典型夹紧机构的作用力计算3.4.1 螺旋夹紧机构3.4.2 圆偏心夹紧机构3.4.3 复合圆偏心轮夹紧机构3.4.4 端面凸轮夹紧机构3.4.5 复合端面凸轮夹紧机构3.4.6 斜锲夹紧机构3.4.7 压板夹紧机构3.4.8 切向夹紧机构3.4.9 齿条滑柱钻模圆锥锁紧机构3.4.10 铰链杠杆增力机构3.4.11 离心式夹紧机构3.4.12 楔槽式夹紧机构3.4.13 复合气(液)动夹紧机构3.5 自定心夹紧机构的相关计算3.5.1 碗形弹簧片定心夹具的设计计算3.5.2 碟形弹簧片定心夹具的设计计算3.5.3 V形弹性夹盘定心夹具的设计计算3.5.4 弹性薄壁膜片卡盘的设计计算3.5.5 薄壁波纹套定心夹具的设计与计算3.5.6 自定心夹紧装置的定心精度3.5.7 液性塑料薄壁套筒夹具的设计与计算3.6 端齿分度盘的相关计算3.6.1 直齿端齿分度盘的结构及其参数的确定3.6.2 端齿分度盘的锁紧力计算3.6.3 YX-DZ系列直齿端齿盘的规格、主要尺寸及精度3.6.4 差动端齿分度装置的设计与计算3.7 夹具夹紧误差的估算3.8 多轴传动头的齿轮系几何尺寸计算3.8.1 外啮合标准直齿圆柱齿轮的几何尺寸计算3.8.2 外啮合高变位直齿圆柱齿轮的几何尺寸计算3.8.3 外啮合标准斜齿圆柱齿轮的几何尺寸计算3.8.4 外啮合高变位斜齿圆柱齿轮的几何尺寸计算3.8.5 内啮合高变位直齿圆柱齿轮的几何尺寸计算3.8.6 内齿直齿圆柱齿轮测量尺寸的计算3.9 典型加工方法切削力的计算3.9.1 车削力的计算3.9.2 钻削力的计算3.9.3 铣削力的计算第4章专用夹具常用零部件及其标准或规范4.1 概述4.2 夹具常用紧固件与连接件国家标准索引4.2.1 螺栓4.2.2 螺柱4.2.3 螺钉4.2.4 螺母4.2.5 垫圈4.2.6 销4.2.7 挡圈4.2.8 键4.3 定位件4.3.1 定位销及定位插销4.3.2 定位轴4.3.3 键4.3.4 V形块及挡块4.3.5 定位器4.4 支承件4.4.1 标准支承件4.4.2 非标准支承件4.4.3 辅助支承4.5 夹紧件4.5.1 压块、压板4.5.2 偏心轮4.5.3 支座、支柱4.5.4 夹具专用螺钉和螺栓4.5.5 夹具专用螺母4.5.6 夹具专用垫圈4.6 导向件4.6.1 钻套4.6.2 其他导向件4.7 对刀块及塞尺4.7.1 对刀块4.7.2 塞尺4.8 操作件4.8.1 夹具常用操作件4.8.2 其他操作件4.9 与夹具相关的机床附件4.9.1 顶尖4.9.2 卡夹件4.9.3 拨盘、花盘及过渡盘4.9.4 活铁爪4.9.5 角铁4.10 其他件4.10.1 圆柱螺旋压缩弹簧4.10.2 圆柱螺旋拉伸弹簧4.10.3 弹簧用螺钉4.10.4 弹簧用吊环螺钉4.10.5 切向夹紧套4.10.6 焊接环首螺钉4.10.7 带锁紧槽圆螺母4.10.8 带扳手孔圆螺母4.10.9 堵片4.10.10 螺塞4.10.11 锁口4.11 夹具体4.11.1 夹具体的毛坯种类及基本要求4.11.2 夹具体座耳尺寸4.11.3 夹具体的排屑结构4.11.4 夹具体的标准毛坯和零件4.11.5 标准毛坯件和零件组合的夹具体图例4.11.6 夹具体结构的正误分析4.12 机床夹具零部件标准件应用图例4.12.1 定位件及辅助支承应用图例4.12.2 夹紧件应用图例4.12.3 导向件应用图例4.12.4 其他零部件应用图例4.13 夹具元件公差配合的选择及机床夹具零部件通用技术条件4.13.1 夹具中常用元件间的配合及公差4.13.2 常用夹具元件的配合图例4.13.3 机床夹具零件及部件通用技术条件第5章气动、液压、电力、电磁、真空夹具传动系统及其元件和夹具图例5.1 夹具夹紧动力源概述5.1.1 手动夹紧和动力夹紧5.1.2 动力夹紧的各种动力源5.2 气动夹具5.2.1 气动夹具优缺点和应用场合5.2.2 气源和气压系统5.2.3 气压传动夹紧系统的设计计算及其元件5.2.4 气动夹具应用图例5.3 液压夹具和液压夹紧的动力源5.3.1 夹具用液压系统的特点5.3.2 基本液压夹紧系统、结构及其元件5.3.3 液压夹具常用典型液压回路5.3.4 夹具液压夹紧系统的相关计算5.3.5 液压夹具用液压缸结构和尺寸5.3.6 液压夹紧的各种动力源5.3.7 液压夹紧机构和液压夹具应用示例5.4 电力传动夹具5.4.1 电力传动夹紧装置5.4.2 偏心式电动卡盘5.4.3 电磁铁夹紧装置5.5 电磁夹具及其应用5.5.1 电磁夹具工作原理5.5.2 各种电磁吸盘结构形式和设计要点5.5.3 强力电磁夹具5.5.4 电磁无心夹具5.6 真空夹具及其应用5.6.1 真空系统工作原理及夹紧力计算5.6.2 真空发生装置5.6.3 真空夹具及典型结构5.6.4 真空夹具的设计要点第6章机床专用夹具设计方法6.1 机床专用夹具设计步骤6.2 设计前期准备6.2.1 信息资料收集与研究6.2.2 加工精度和工艺性分析6.2.3 切削力、夹紧力综合平衡计算6.3 夹具结构方案选择6.3.1 定位原则及方案选择6.3.2 辅助支承方式选择6.3.3 对刀与引导方式选择6.3.4 夹紧原则及方案选择6.3.5 其他组成部分结构形式选择6.4 夹具总装配图绘制6.4.1 总体结构确定6.4.2 定位元件结构绘制6.4.3 辅助支承结构绘制6.4.4 对刀与引导装置结构绘制6.4.5 夹紧元件结构绘制6.4.6 夹具体结构绘制6.4.7 其他部分结构绘制6.4.8 夹具总图标注和技术条件给定6.4.9 夹具设计普遍应注意的问题6.4.10 夹具总装配图绘制示例6.5 夹具零件图绘制6.5.1 零件结构确定6.5.2 材料选择与工艺性分析6.5.3 技术要求确定6.5.4 工艺孔在夹具设计中的应用6.6 夹具设计与制造中的信息处理第7章机床专用夹具设计及典型图例7.1 车床专用夹具7.1.1 车床专用夹具的主要类型7.1.2 车床夹具设计要则7.1.3 车床(圆磨床)夹具的技术要求7.1.4 车床(圆磨床)夹具的磨损极限7.1.5 车床专用夹具典型图例7.1.6 车床通用可调夹具典型图例7.2 钻床、镗床专用夹具7.2.1 钻床、镗床专用夹具的主要类型7.2.2 钻床夹具(钻模)设计要则7.2.3 镗床夹具设计要则7.2.4 钻床(镗床)夹具的技术要求7.2.5 钻床(镗床)夹具的磨损极限7.2.6 钻模通用部件7.2.7 钻床专用夹具(钻模)典型图例7.2.8 钻床通用可调夹具典型图例7.2.9 钻床多轴头7.2.10 镗床专用夹具典型图例7.3 铣床专用夹具7.3.1 铣床专用夹具的主要类型7.3.2 铣床专用夹具设计要则7.3.3 铣床夹具的技术要求7.3.4 铣床夹具的磨损极限7.3.5 铣床专用夹具典型图例7.3.6 铣床通用可调夹具典型图例7.4 拉床专用夹具7.4.1 拉床专用夹具主要类型7.4.2 拉床专用夹具设计要则7.4.3 拉床专用夹具典型图例7.5 齿轮机床专用夹具7.5.1 齿轮机床专用夹具主要类型7.5.2 齿轮机床专用夹具设计要则7.5.3 齿轮机床专用夹具技术要求7.5.4 齿轮机床专用夹具典型图例7.6 磨床专用夹具7.6.1 圆磨床专用夹具7.6.2 平面磨床专用夹具7.7 组合机床及其自动线专用夹具7.7.1 概述7.7.2 组合机床及其自动线夹具设计要则7.7.3 定位、夹紧及刀具导向的结构7.7.4 组合机床及其自动线专用夹具典型图例7.8 数控机床和加工中心夹具7.8.1 数控机床和加工中心夹具设计要则7.8.2 数控机床与加工中心夹具典型图例第8章可调夹具和成组夹具8.1 概述8.1.1 可调夹具和成组夹具的定义和分类8.1.2 可调夹具和成组夹具的结构特点及适用场合8.1.3 可调夹具和成组夹具的标识方法8.1.4 可调夹具和成组夹具的应用效果8.2 成组夹具的设计与应用8.2.1 成组夹具的设计依据、原则、程序和附加说明8.2.2 成组夹具的应用与管理8.3 可调夹具示例8.3.1 回转体类零件用可调夹具示例8.3.2 非回转体类零件用可调夹具示例8.4 成组夹具示例8.4.1 回转体零件用成组夹具示例8.4.2 非回转体零件用成组夹具……第9章组合夹具,数控机床、加工中心、柔性制造系统用夹具第10章检验夹具第11章焊接夹具第12章计算机辅助夹具设计(CAFD)。
冶金吊具参数化计算机辅助设计中摩擦式夹钳夹紧力的分析与计算

冶金吊具参数化计算机辅助设计中摩擦式夹钳夹紧力的分析与计算冶金吊具是一种结构精巧、使用方便、节省人力和能源的取物装置,用于许多高温、高湿、和人员不易接近的场合,除某些由动力驱动外,许多冶金吊具是靠机构本身重量产生起重物所需夹紧力。
在公司生产的吊具中,为数不少的是摩擦式机械夹钳,根据起重物的重量和大小及其他相关参数来确定夹钳机构的主要几何参数时,必须对机构进行夹紧力的计算和调整,由于用户对夹钳功能要求的多样性,随着吊起重物的增加,夹钳的自重和本身结构尺寸将越来越大,这在许多使用夹钳的场合无法容忍。
因此,通过摩擦式夹钳夹持力的分析与计算,通过计算机辅助设计、计算,来优化设计夹钳的结构尺寸参数和运动受力参数,使用户达到最满意的效果。
在我厂近年所开发吊具参数化计算机辅助设计系统中,对夹钳夹紧力计算均采用了公式计算, 以下是该计算公式的推导:进行判别,最后完成夹紧力的效核计算。
如果效核通不过,则可分析(26)式,可知有两个方面加以改进:一是改变夹钳钳口的材料及形状即增大摩擦系数来增加夹持力,这一点在实际操作中条件是有限的。
二是改变机构的几何尺寸。
如果是通过第二方面来改变夹钳机构的几何尺寸来增加夹持力,可从(16)式分析得知:可改变的项有两项,(1)杆长比L2/L4, (2)角度(3)对于杆长L2、L6,它受机构行程及整个结构的制约,在夹取物板坯尺寸参数确定下来以后, L6尺寸就基本确定下来,变化值己不大了,杆长L1基本上受杆长L2 及角度Q确定而确定,变化值也不大,角度c(由于机构结构的制约,变化值范围值较小,所以调整量不大,所以可以改变项实际上只有L2/L4o因此,如夹紧力效核通不过,可以增加L2或减少L4,但值得注意的是增加L2会增加整个夹钳的高度方向,并且使起重机有效起升高度减少,同时也增加了夹钳的宽度,而减少了L4,则会减少夹钳的开口度,并且使夹持有效高度减少。
并且单某一参数改变时,必需根据整个机构各杆间的相互制约关系进行调整,例如增加L2,则应同时按比例增加L1和适当调整角度,这样才能保正机构运动完整合理。
夹紧力计算

盛年不重来,一日难再晨。
及时宜自勉,岁月不待人。
4.1.2 夹紧力计算及夹紧气缸的设计1、夹紧力的计算工件材料为AS9U3,大平面加工余量为1.5mm ,采用硬质合金端铣刀加工,切削力查参考文献〔1〕可根据如下公式计算: •式中:Fz ---铣削力(N)a f ---每齿进给量(mm/r) a w ---铣削宽度(mm) K FZ ---铣削力修正系数 d 0---铣刀外径(mm) a p ---铣削深度(mm) z ---•铣刀齿数 确定各参数值:(1).铣刀外径d 0=315mm ; (2).铣刀齿数Z =16;(3).每齿进给量af 是铣刀每转一个刀齿时铣刀对工件的进量:a f =V f /(z ·n)=360/(16×720)=0.031mm/r(4).铣削深度a p 对于端铣刀是指平行于铣刀轴线测量的被铣削层尺寸:a p =1.5mm(5). 铣削宽度a w 对于端铣刀是指垂直于铣刀轴线测量的被切削层尺寸:a w =240mm(6). 修正系数K FZ 取1.6;由表查得: c F =7750 x F =1.0 y F =0.75u F =1.1 w F =0.2 q F =1.3FZw q 0V wy fX PX FZ K nd Za a a c 25.0F fFFfFF⋅⋅⋅⋅⋅⋅⨯=⋅1.00.751.11.30.277501.50.031240160.25 1.6315720ZF ⨯⨯⨯⨯=⨯⨯⨯Fz=276.5N=28Kg(7). 理论所需夹紧力计算 确定安全系数:总的安全系数k =k1·k2·k3·k4k 1---- 一般安全系数; k 1取1.7;k 2----加工状态系数; 由于是精加工,所以k 2取1; k 3----刀具钝化系数; k 3取1.4; k 4----断续切削系数; k 4取1.2; ∴ k =1.7×1×1.4×1.2≈3 W =k ·p =3×28kg =84kg 2. 气缸的选择Q=W/(i ·η1·n )=84/(0.8×0.8×3)=44kg 由气缸传动的计算公式: Q=P·(πD2/4)·η式中: P--压缩空气压力=6atm =6kg/cm2 η--气缸摩擦系数,取0.8i —压板与工件的摩擦系数,取0.8n —夹紧气缸个数,本夹具为3 D--气缸直径(cm)D ==D=34.2cm通过以上理论计算,可以选择直径为50mm 的气缸。
夹紧力的分析与估算

图1—55
例如,图1—56为铣削加工示意图,试 估算所需的夹紧力。
由于是小型工件,工件重力略去不计。 因为压板是活动的,压板对工件的摩擦力 也略去不计。
不设置止推销时,对夹紧最不利的瞬 时状态是铣刀切入全深、切削力 FP 达到
最用与大夹之时紧平,力衡工,FJ件建1、可立F能静J2 沿平产衡F生P方的的程摩方:擦向力移动F1,、F需2
设 FJ1 FJ2 FJ理
f1f2 f
F 则 F J 理 fL 1 L 2 F P L
J理
FPL f (L1L2)
考虑安全系数,每块压板需给工件的夹紧力(N)是:
F FpLK J需 f (L1L2)
式中L——切削力作用方向至挡销的距离, L1、L 2 ——两支承钉至挡销的距离。
安全系数可按下式计算
设置止推销后,工件不可能斜向移动了,对夹紧最不利的瞬
时状态是铣刀切入全深、切削力达到最大时,工件绕0点转动,形
成切削力矩FP L ,需用夹紧力FJ1、FJ2 产生的摩擦力矩F1L1、F2L2
与之平衡,建立静平衡方程如下:
F 1 L 1F 2 L 2F PL F J1f1L 1F J2f2L 2F P L
如图1—55所示, 夹紧力作用点靠近加工表面略去次要因
素在力系中的影响。估算步骤如下:
1)建立理论夹紧力 F J理 与主要最大切削
力 FP 的静平衡方程:
FJ理 FP
2)实际需要的夹紧力 FJ需 ,应考虑安全系数
(见表1—8),FJ需KFJ理
3)校核夹紧机构产生的夹紧力 F J 是否满足
条件:
FJ FJ需
这样做,有利于保证孔与左端面的垂直度要求。如果夹紧力改朝B面,则由于工件左端面与底面
第九讲夹紧力的分析与估算

1)夹紧力应朝向主要限位面,对工件只施 加一个夹紧力,或施加几个方向相同的夹紧力 时,夹紧力的方向应尽可能朝向主要限位面。 如图1—52a所示,工件被镗的孔与左端面有 一定的垂直度要求。
图1—52
工件以孔的左端面与定位元件的A面接触,限制三个自由度;
以底面与B面接触,限制两个自由度;夹紧力朝向主要限位面A。
上一讲内容提要:
工件以V形导轨面定位 工件以燕尾导轨面定位 工件以渐开线齿形面定位 夹紧装置的组成 对夹紧装置的基本要求
本讲主要内容:
夹紧力的方向和作用点的确定 夹紧力大小的估算
本讲重点和难点:
夹紧力方向和作用点的确定 夹紧力大小的估算
第八节 夹紧力的确定
确定夹紧力的方向、作用点和大小时,要分析工件的结构特点、 加工要求、切削力和其它外力作用工件的情况,以及定位元件的结构 和布置方式。
设置止推销后,工件不可能斜向移动了,对夹紧最不利的瞬
时状态是铣刀切入全深、切削力达到最大时,工件绕0点转动,形
成切削力矩FP L ,需用夹紧力FJ1、FJ2 产生的摩擦力矩F1L1、F2L2
与之平衡,建立静平衡方程如下:
F 1 L 1F 2 L 2F PL F J1f1L 1F J2f2L 2F P L
b)
c)
图1—54
4)夹紧力作用点应靠近工件的加工表面。
如图1—55所示。 在拨叉上铣槽,由于主要夹紧力的作用 点距加工表面较远,故在靠近加工表面的地
方设置了辅助支承,增加了夹紧力 F J 。
这样,不仅提高了工件的装夹刚性,还 可减少加工时工件的振动。
图1—55
二、夹紧力大小的估算
加工过程中,工件受到切削力、离心力、惯性力及重力的作 用。
夹紧力计算

上海德珂斯机械自动化技术有限公司Tuenkers Machinery & Automation Technology Co., Ltd, Shanghai夹紧器夹紧力计算上海德珂斯机械自动化技术有限公司Tuenkers Machinery & Automation Technology Co., Ltd, Shanghai1.压块垂直夹紧时,此时夹紧力处于垂直方向, 其受力分析如下:夹紧力Fs 压块M缸径 5bar气压夹紧力矩L40夹紧力Fs50120Nm 160Nm63380Nm80600NmFs =有效夹紧力 L=夹紧点与转动轴中心距离当压块垂直夹紧时,夹紧力方向与力矩切线方向相同,此时产生的夹紧力最大,计算公式如下: Fs= M ÷ L举例: 当L=200mm时,缸径63mm. 夹紧力Fs=380Nm ÷0.2m=1900N上海德珂斯机械自动化技术有限公司Tuenkers Machinery & Automation Technology Co., Ltd, Shanghai2.压块水平夹紧时,此时夹紧力处于水平状方 向,其受力分析如下:夹紧力Fs压块M L2L1 Fs α FFs =有效夹紧力 L1=夹紧点与转动轴中心距离 F=切向力缸径 5bar气压夹紧力矩M40120Nm50160Nm63380Nm80600Nm当压块水平夹紧时,其有效夹紧力会相对减小,计算公式如下: Cos α =L2 ÷ L1 F= M ÷ L1 Fs= F × Cos α举例: 当L1=200mm,L2=100mm时,缸径63mm。
F=380Nm÷0.2=1900N Fs=F × Cos α=1900N×(100÷200)=950N上海德珂斯机械自动化技术有限公司Tuenkers Machinery & Automation Technology Co., Ltd, Shanghai谢谢!上海德珂斯机械自动化技术有限公司Tuenkers Machinery & Automation Technology Co., Ltd, Shanghai。
- 1、下载文档前请自行甄别文档内容的完整性,平台不提供额外的编辑、内容补充、找答案等附加服务。
- 2、"仅部分预览"的文档,不可在线预览部分如存在完整性等问题,可反馈申请退款(可完整预览的文档不适用该条件!)。
- 3、如文档侵犯您的权益,请联系客服反馈,我们会尽快为您处理(人工客服工作时间:9:00-18:30)。
这样做,有利于保证孔与左端面的垂直度要求。
如果夹紧力改朝B面,
则由于工件左端面与底面
的夹角误差,夹紧时将破源自坏工件的定位,影响孔与左端面的垂直度要求。
再如图1—52b所示,
夹紧力朝向主要限位面
——V形块的V形面,使 工件的装夹稳定可靠。
图1—52
如果夹紧力改朝B面,则由于工件圆柱面与端面的垂直度误差, 夹紧时,工件的圆柱面可能离开V形块的V形面。这不仅破坏了定位, 影响加工要求,而且加工时工件容易
与之平衡,建立静平衡方程:
图1—56
F1 F2 FP
设 FJ1 FJ2 FJ理
FJ1 f1 FJ2 f 2 FP
f1 f2 f
则 2 fFJ理 FP
F FP J理 2 f
考虑安全系数,每块压板需给工件的夹紧力(N)为
F KFP J需 2 f
式中 FP ——最大切削力(N);
FJ ——每块压板的夹紧力(N)
FJ FJ需
图1—55
例如,图1—56为铣削加工示意图,试 估算所需的夹紧力。
由于是小型工件,工件重力略去不计。 因为压板是活动的,压板对工件的摩擦力 也略去不计。
不设置止推销时,对夹紧最不利的瞬 时状态是铣刀切入全深、切削力 FP 达到 最大时,工件可能沿 FP 的方向移动,需
用夹紧力 FJ1、F J2 产生的摩擦力 F1、F 2
设 FJ1 FJ2 FJ理
f1 f2 f
则 FJ理 f L1 L2 FP L
F FPL
J理
f ( L1 L2 )
考虑安全系数,每块压板需给工件的夹紧力(N)是:
F FpLK
J需
f ( L1 L2 )
式中L——切削力作用方向至挡销的距离, L1、L 2 ——两支承钉至挡销的距离。
安全系数可按下式计算
K K0 K1K2 K3
各种因素的安全系数见表1—8。 通常情况下,取K=1.5~2.5, 当夹紧力与切削力方向相反时,取K=2.5~3。 各种典型切削方式所需夹紧力的静平衡方程式可参看“夹具手册”
本讲小结:
夹紧力的方向 作用点的确定 夹紧力大小的估算
上一讲内容提要:
工件以V形导轨面定位 工件以燕尾导轨面定位 工件以渐开线齿形面定位 夹紧装置的组成 对夹紧装置的基本要求
本讲主要内容:
夹紧力的方向和作用点的确定 夹紧力大小的估算
本讲重点和难点:
夹紧力方向和作用点的确定 夹紧力大小的估算
第八节 夹紧力的确定
确定夹紧力的方向、作用点和大小时,要分析工件的结构特点、 加工要求、切削力和其它外力作用工件的情况,以及定位元件的结构 和布置方式。
一、夹紧力的方向和作用点的确定
1)夹紧力应朝向主要限位面,对工件只施 加一个夹紧力,或施加几个方向相同的夹紧力 时,夹紧力的方向应尽可能朝向主要限位面。 如图1—52a所示,工件被镗的孔与左端面有 一定的垂直度要求。
图1—52
工件以孔的左端面与定位元件的A面接触,限制三个自由度;
以底面与B面接触,限制两个自由度;夹紧力朝向主要限位面A。
b)
c)
图1—54
4)夹紧力作用点应靠近工件的加工表面。
如图1—55所示。 在拨叉上铣槽,由于主要夹紧力的作用 点距加工表面较远,故在靠近加工表面的地
方设置了辅助支承,增加了夹紧力 FJ 。
这样,不仅提高了工件的装夹刚性,还 可减少加工时工件的振动。
图1—55
二、夹紧力大小的估算
加工过程中,工件受到切削力、离心力、惯性力及重力的作 用。
如图1—55所示, 夹紧力作用点靠近加工表面略去次要因
素在力系中的影响。估算步骤如下:
1)建立理论夹紧力 FJ理 与主要最大切削
力 FP 的静平衡方程:
FJ理 FP
2)实际需要的夹紧力 FJ需 ,应考虑安全系数
(见表1—8),FJ需 KFJ理
3)校核夹紧机构产生的夹紧力 FJ 是否满足
条件:
对工件施加几个方向不同的夹紧力时,朝向主要限位面的夹紧力 应是主要夹紧力。
2)夹紧力的作用点 应落在定位元件的支承 范围内。 如图1—53所示。
图1—53
夹紧力的作用点落到了定位元件的支承范围之外,夹紧时将破 坏工件的定位,因而是错误的。
3)夹紧力的作用点应落在工件刚性较 好的方向和部位。这一原则对刚性差的工 件特别重要。
如图1—54a)所示。 薄壁套的轴向刚性比径向好,用卡爪 径向夹紧,工件变形大,若沿轴向施加夹 紧力,变形就会小得多。
a) 图1—54
夹紧图1—54b所示薄壁箱体时,夹紧力不应作用在箱体的顶 面,而应作用在刚性好的凸边上。
箱体没有凸边时,如图 1—54c所示。
将单点夹紧改为三点夹 紧,使着力点落在刚性较好 的箱壁上,并降低了着力点 的压强,减小了工件的夹紧 变形。
f ——工件与定位元件间的摩擦因数; K ——安全系数。
设置止推销后,工件不可能斜向移动了,对夹紧最不利的瞬
时状态是铣刀切入全深、切削力达到最大时,工件绕0点转动,形 成切削力矩FP L ,需用夹紧力FJ1、F J2 产生的摩擦力矩F1L1、 F2L2 与之平衡,建立静平衡方程如下:
F1L1 F2L2 FP L FJ1 f1L1 FJ2 f 2 L2 FP L
理论上,夹紧力的作用应与上述力(矩)的作用平衡; 实际上,夹紧力的大小还与工艺系统的刚性、夹紧机构的传 递效率等有关。 切削力的大小在加工过程中是变化的,因此,夹紧力的计算 是个很复杂的问题,只能进行粗略的估算。 估算时应找出对夹紧最不利的瞬时状态,估算此状态下所需 的夹紧力。并只考虑主要因素在力系中的影响,