热加工实训心得体会
金工实习热加工实习报告

金工实习热加工实习报告金工实习是机械专业学生重要的一段实践旅程,通过实习,我们可以将书本上的理论知识与实际操作相结合,提高自己的动手能力和实践技能。
在实习期间,我接触了多种热加工工艺,如锻造、焊接、热处理等,下面我就这次实习的经历做一个简要的汇报。
首先,我了解了锻造的基本原理和工艺过程。
锻造是利用压力使金属材料产生塑性变形,从而获得所需形状和尺寸的工艺。
在锻造过程中,我学会了如何选择合适的模具和压力设备,以及如何控制锻造温度和变形程度。
通过实际操作,我深刻体会到了锻造过程中力量和技巧的重要性。
其次,我学习了焊接工艺。
焊接是将两个金属部件通过加热和压力使其熔接在一起的过程。
在实习中,我掌握了多种焊接方法,如气体保护焊、电弧焊、激光焊等。
通过实践,我了解了各种焊接方法的特点和适用范围,并学会了如何选择合适的焊接材料和参数。
同时,我也明白了焊接过程中安全操作的重要性。
此外,我还了解了热处理工艺。
热处理是通过加热、保温和冷却等过程改变金属材料的组织结构和性能的方法。
在实习中,我学习了退火、正火、淬火等热处理工艺,并掌握了如何控制热处理过程中的温度和时间。
通过实际操作,我深刻体会到了热处理对金属材料性能的重要影响。
在实习过程中,我还学习了金属材料的选用和加工方法。
了解了不同金属材料的特性,如强度、韧性、硬度等,并学会了如何根据实际需求选择合适的材料。
同时,我也了解了各种加工方法的特点和适用范围,如切削、磨削、抛光等。
通过这次金工实习,我不仅学到了热加工方面的理论知识,还提高了自己的动手能力和实践技能。
我深刻体会到了理论与实践相结合的重要性,以及在实际操作中注意安全和技术要求的重要性。
我相信这次实习对我今后的学习和职业发展将产生积极的影响。
总之,金工实习是一次富有挑战和收获的经历。
在实习过程中,我学到了很多宝贵的知识和技能,锻炼了自己的实践能力,提高了自己的综合素质。
我将珍惜这次实习的经历,继续努力学习,为将来的工作打下坚实的基础。
热加工实训总结

热加工实训总结实践是知识的巩固,也是能力的培养。
在我的专业学习中,热加工实训课程是我收获最多的一门课程之一。
通过实际动手操作,我不仅学到了理论知识的应用,还培养了解决问题和团队合作的能力。
在这篇文章中,我将总结我在热加工实训中的经验和体会。
首先,热加工实训课程涉及到许多工艺和技术。
课上,我们学习了金属的切削加工、焊接与热处理等内容。
在实际操作中,我深刻体会到了每一个步骤的重要性。
精确的测量、准确定位、合理的切削与焊接等,都是确保加工质量的关键因素。
更进一步,我还学到了如何选择适当的刀具、工艺参数和热处理方法。
这些知识的掌握不仅提升了我在实践中的效率,也对我的专业素养有着积极的影响。
其次,热加工实训过程中,我也感受到了团队合作的重要性。
在实验课上,我们分组进行实践操作。
每个人都有自己的任务,同时需要和组员密切配合。
只有团队协作才能保证工作的高效进行。
我与组员一起商讨方案、交流经验并共同解决问题。
通过与他们的合作,我学到了如何倾听他人的意见、尊重他人的观点,并能够有效地与他人进行沟通和协调。
这些团队合作的技能和经验对我的未来职业发展也有着重要的意义。
除了技术和团队合作,热加工实训还培养了我解决问题的能力。
在实际操作过程中,往往会遇到各种各样的问题和困难。
比如,当我们在焊接时发现焊缝有裂纹,我们需要仔细分析出现问题的原因,并采取措施进行修复。
这个过程不仅要求我们具备专业的知识和技能,更需要我们具备分析问题的能力和解决问题的思维方式。
通过实训,我学会了更加全面地思考问题,不再仅仅停留在表象上,而是能够从根本上找到解决问题的方法。
此外,热加工实训也让我理解了劳动的价值和尊重。
在实训中,我们需要亲自动手,进行繁重的操作和劳动。
通过亲身体验,我深刻感受到了劳动的辛苦和付出的价值。
这让我对劳动者们的辛勤付出有了更为深刻的理解和尊重。
同时,也激发了我对技能的热爱和追求。
我希望通过不断学习和实践,能够提升自己的技能水平,为社会做出更多的贡献。
热加工实训总结

热加工实训总结热加工是一种重要的金属加工方式,它通过加热金属材料,使其软化,然后进行塑性变形或切削加工,从而得到所需的形状和尺寸。
在工业生产中,热加工广泛应用于各种金属制品的生产和加工,如汽车零部件、机械零件、航空航天部件等。
为了提高学生的热加工技能,我校开设了热加工实训课程,让学生在实践中掌握热加工的基本原理和技术。
在热加工实训中,我们主要学习了以下几个方面的内容:一、热处理工艺热处理是热加工的重要环节,它可以改变金属材料的组织结构和性能,使其具有更好的机械性能和耐腐蚀性能。
在实训中,我们学习了常见的热处理工艺,如退火、正火、淬火、回火等。
通过实际操作,我们了解了每种热处理工艺的原理和适用范围,掌握了热处理的基本技能。
二、热加工设备热加工设备是实现热加工的关键,它包括热处理炉、热加工机床、热喷涂设备等。
在实训中,我们学习了各种热加工设备的结构和工作原理,了解了设备的使用方法和注意事项。
通过实际操作,我们掌握了设备的操作技能,提高了设备的使用效率和安全性。
三、热加工工艺热加工工艺是实现热加工的关键,它包括热加工的基本原理、加工工艺和加工参数等。
在实训中,我们学习了各种热加工工艺的原理和适用范围,了解了加工参数的选择和调整方法。
通过实际操作,我们掌握了热加工的基本技能,提高了加工效率和质量。
四、热喷涂技术热喷涂技术是一种新型的热加工技术,它可以在金属表面形成一层坚硬的涂层,提高金属的耐磨性和耐腐蚀性。
在实训中,我们学习了热喷涂技术的原理和适用范围,了解了喷涂设备的结构和工作原理。
通过实际操作,我们掌握了热喷涂的基本技能,提高了涂层的质量和稳定性。
热加工实训是一种非常重要的实践教学方式,它可以让学生在实践中掌握热加工的基本原理和技术,提高学生的实际操作能力和创新能力。
在今后的学习和工作中,我们将继续发扬实践精神,不断提高自己的热加工技能,为国家的工业发展做出更大的贡献。
金工实习报告热加工

一、实习背景为了更好地了解金工实习,提高自己的动手能力和实践能力,我在学校组织的金工实习活动中,选择了热加工这一模块进行深入学习。
热加工是将金属材料加热到一定温度,使其发生一定的塑性变形,然后进行冷却、定型等过程,从而获得所需的形状和性能的加工方法。
在本次实习中,我通过实际操作,对热加工的原理、过程、注意事项等方面有了更深入的了解。
二、实习内容1. 热加工原理及分类热加工原理:热加工是利用金属在加热过程中发生的塑性变形来实现材料形状和性能的改变。
根据加热温度的不同,热加工可分为以下几种类型:(1)退火:将金属材料加热到一定温度,保温一段时间,然后缓慢冷却,以消除材料内部的应力,提高材料的塑性和韧性。
(2)正火:将金属材料加热到一定温度,保温一段时间,然后快速冷却,以获得一定的硬度和强度。
(3)淬火:将金属材料加热到一定温度,保温一段时间,然后迅速冷却,使材料获得高硬度和耐磨性。
(4)回火:将淬火后的金属材料加热到一定温度,保温一段时间,然后缓慢冷却,以消除淬火过程中产生的内应力,提高材料的韧性。
2. 热加工设备(1)加热炉:加热炉是热加工过程中必不可少的设备,用于将金属材料加热到所需温度。
常见的加热炉有煤气炉、电炉、油炉等。
(2)热处理炉:热处理炉用于对金属材料进行退火、正火、淬火、回火等热处理过程。
(3)冷却装置:冷却装置用于将加热后的金属材料迅速冷却,以获得所需的性能。
常见的冷却装置有水冷、油冷、空气冷却等。
3. 热加工操作步骤(1)准备:根据加工要求,选择合适的金属材料和热加工方法。
(2)加热:将金属材料放入加热炉中,加热到所需温度。
(3)保温:在加热过程中,保持一定时间,使金属材料充分加热。
(4)冷却:将加热后的金属材料迅速冷却,以获得所需的性能。
(5)检验:对热加工后的金属材料进行外观、尺寸、性能等方面的检验。
三、实习心得1. 增强了动手能力:通过实际操作,我对热加工的原理、过程、设备等方面有了更深入的了解,提高了自己的动手能力。
热加工实训心得体会
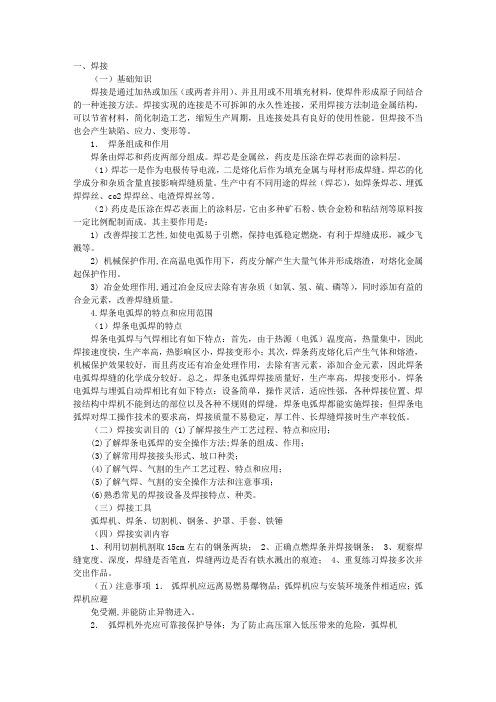
一、焊接(一)基础知识焊接是通过加热或加压(或两者并用)、并且用或不用填充材料,使焊件形成原子间结合的一种连接方法。
焊接实现的连接是不可拆卸的永久性连接,采用焊接方法制造金属结构,可以节省材料,简化制造工艺,缩短生产周期,且连接处具有良好的使用性能。
但焊接不当也会产生缺陷、应力、变形等。
1.焊条组成和作用焊条由焊芯和药皮两部分组成。
焊芯是金属丝,药皮是压涂在焊芯表面的涂料层。
(1)焊芯一是作为电极传导电流,二是熔化后作为填充金属与母材形成焊缝。
焊芯的化学成分和杂质含量直接影响焊缝质量。
生产中有不同用途的焊丝(焊芯),如焊条焊芯、埋弧焊焊丝、co2焊焊丝、电渣焊焊丝等。
(2)药皮是压涂在焊芯表面上的涂料层,它由多种矿石粉、铁合金粉和粘结剂等原料按一定比例配制而成。
其主要作用是:1) 改善焊接工艺性,如使电弧易于引燃,保持电弧稳定燃烧,有利于焊缝成形,减少飞溅等。
2) 机械保护作用,在高温电弧作用下,药皮分解产生大量气体并形成熔渣,对熔化金属起保护作用。
3) 冶金处理作用,通过冶金反应去除有害杂质(如氧、氢、硫、磷等),同时添加有益的合金元素,改善焊缝质量。
4.焊条电弧焊的特点和应用范围(1)焊条电弧焊的特点焊条电弧焊与气焊相比有如下特点:首先,由于热源(电弧)温度高,热量集中,因此焊接速度快,生产率高,热影响区小,焊接变形小;其次,焊条药皮熔化后产生气体和熔渣,机械保护效果较好,而且药皮还有冶金处理作用,去除有害元素,添加合金元素,因此焊条电弧焊焊缝的化学成分较好。
总之,焊条电弧焊焊接质量好,生产率高,焊接变形小。
焊条电弧焊与埋弧自动焊相比有如下特点:设备简单,操作灵活,适应性强,各种焊接位置、焊接结构中焊机不能到达的部位以及各种不规则的焊缝,焊条电弧焊都能实施焊接;但焊条电弧焊对焊工操作技术的要求高,焊接质量不易稳定,厚工件、长焊缝焊接时生产率较低。
(二)焊接实训目的 (1)了解焊接生产工艺过程、特点和应用;(2)了解焊条电弧焊的安全操作方法;焊条的组成、作用;(3)了解常用焊接接头形式、坡口种类;(4)了解气焊、气割的生产工艺过程、特点和应用;(5)了解气焊、气割的安全操作方法和注意事项;(6)熟悉常见的焊接设备及焊接特点、种类。
金工实习热加工实习报告

竭诚为您提供优质文档/双击可除金工实习热加工实习报告篇一:金工实习报告之(钳工_热加工)金工实习总结报告为期两周地金工实习终于开工啦!第六周的星期二,同学们带着兴奋和忐忑的心来到了实习基地。
对我来说,曾经的期待已成了事实。
接下来的两周,我们就是到一个新的环境去学习,去了解新的模块:钳工和热加工。
一系列的新名词将要渐渐地烙印在心中。
车间的生活有苦有泪,汗水,疲惫,不断地尝试中我们学到的是在教室里学不到的技能,这些将会让我们重新认识社会,准确的定位人生。
可以说,金工实习对于我们这一代新生的大学生来说是非常有意义的。
车间里没有懒惰和松懈,只有认真的用心去工作才有收获。
老师已经强调一定要有纪律性和安全意识。
我在车间的每一个动作都可能成为隐患或者是奇迹,所以要对自己的每个动作负责。
工件将要在我们的努力下被创造出来。
一、钳工实习曾经听闻钳工老师是很严厉的,但我不这样认为。
事实上那只是一种安全要求。
我们首先接触到是一个关于钳工工种和钳工操作安全的视频,我们的钳工实习就是在这里开始的。
这就算是岗前培训吧。
通过视频,我们初步认识到钳工的意义和钳工工作时应注意的问题。
我们来到自己的工位后,首先是认识工具箱里的工具:300mm平锉、半圆锉、三角锉、方锉、手锯、手锤、平刮刀、钢丝刷、毛刷、划针、样冲、300mm钢尺、直角尺、角度规、圆规、半脚规、标测方框和扁錾各一把。
很多的工具都是没有接触过的,看到这些家伙真有点措手无策,不过一股好奇和冲动,我还是和期待用上这些工具的,这些就是陪伴我们度过两天的钳工实习的忠实伙伴。
真正开始了,认识完这些工具后,老师们就开始来讲解我们这两天来要做的考核件:加工一个直角配合件和加工一个方头螺母。
直角配合件加工步骤:1、.锉削长边,直线度“―”,垂直度“⊥”达标。
12、以长边为基准,锉削短边“―”、“⊥”达标。
3、.以加工好的两面为基准,按图划线打样冲。
4、锯割多余的部分(留加工余量)。
5、.锉削至符合图纸尺寸要求。
热加工铸工实习报告

一、实习背景随着我国工业的快速发展,热加工铸工技术作为机械制造行业的重要组成部分,其应用越来越广泛。
为了提高自身专业技能,我于2021年7月至8月参加了为期一个月的热加工铸工实习。
通过实习,我对铸工技术有了更加深入的了解,掌握了铸工的基本操作方法和工艺流程。
二、实习内容1. 铸造材料实习期间,我学习了铸造材料的种类、性能及选用原则。
铸造材料主要包括铸铁、铸钢、铸造铝合金等。
其中,铸铁具有良好的铸造性能和耐磨性,广泛应用于机械制造行业;铸钢具有较高的强度和韧性,适用于承受较大载荷的结构件;铸造铝合金具有优良的铸造性能和耐腐蚀性,广泛应用于航空、汽车等领域。
2. 铸造工艺实习期间,我了解了铸造工艺的基本流程,包括造型、熔炼、浇注、冷却、清理等环节。
其中,造型工艺是铸造过程中的关键环节,主要包括粘土造型、砂型铸造、金属型铸造等。
我重点学习了砂型铸造工艺,包括造型、制芯、合箱、浇注等操作。
3. 铸造设备实习期间,我熟悉了铸造设备的操作方法和维护保养知识。
主要设备包括造型机、熔炼炉、浇注系统、冷却水系统等。
其中,造型机是造型工艺的核心设备,负责将砂料压制成具有一定形状的砂型;熔炼炉用于熔化金属,为浇注提供液态金属;浇注系统负责将液态金属送入砂型中;冷却水系统用于冷却铸件,防止铸件变形。
4. 铸造缺陷及处理实习期间,我学习了铸造缺陷的产生原因及处理方法。
铸造缺陷主要包括缩孔、缩松、裂纹、夹渣等。
针对这些缺陷,我们采取了相应的处理措施,如调整熔炼工艺、优化造型工艺、改进浇注系统等。
三、实习收获1. 理论知识与实践相结合通过实习,我深刻体会到理论知识与实践操作的重要性。
在实习过程中,我不仅巩固了课堂所学知识,还学会了如何将理论知识应用于实际操作中。
2. 提高动手能力实习期间,我参与了铸造工艺的各个环节,从造型、熔炼到浇注、冷却,亲身经历了铸件从无到有的过程。
通过反复实践,我的动手能力得到了很大提高。
3. 培养团队协作精神实习过程中,我与同学们共同完成了铸造任务,学会了与他人沟通、协作。
热加工实训心得体会

热加工实训心得体会导语:我们通过培训进行了热加工工艺的学习,内容主要包含铸造、锻压、焊接以及金属材料的前沿知识知识。
以下是小编为大家整理的热加工实训心得体会,欢迎大家阅读与借鉴!热加工实训心得体会铸造是历史最悠久的制造工艺。
通过铸造,可以得到内腔和外形很复杂的毛坯,可以针对各种合金进行铸造,并且铸造件的尺寸大小可以在一个很大的范围内波动。
但是同时,铸造也存在一些缺点,比如组织疏松,晶粒粗大,力学性能较差和难以精确控制等。
尽管如此,随着铸造技术的发展,特种铸造工艺的诞生,铸造的精确度已经可以提高到CT4,表面粗糙度最小可以提高到0.8um。
各种材料的铸造性能有很大的差距,这主要由金属的液态成形特征决定。
锻压是对金属坯料施加外力,使之产生塑性变形,以改变其形状、尺寸,并改善其内部组织性能,从而获得所需毛坯或零件的加工方法。
锻压包含锻造和冲压两种。
锻压不同于铸造的主要是金属的加工形态,通常锻压的毛坯是由铸造所得到的。
锻压件的组织致密,力学性能明显好于相同化学成分的铸件。
锻造的过程主要是金属晶粒的变形,金属晶粒变形的特性和锻造流线的连贯性决定了所锻造出来的锻件的质量。
锻造分为自由锻和模锻,模锻的精度要高于自由锻。
自由锻投资费用低,但是只适用于单件及小批量生产。
模锻是整体成形,易于实现机械化和自动化,它只适用于中、小型锻件的成批或大批量生产,并且需要专门的模锻设备,投资较高。
冲压主要是正对金属板料的加工,低碳钢、奥氏体不锈钢以及铜、铝等有色金属通常用于冲压板料。
对于板料的冲压通常有冲裁、弯曲、拉深、胀形等。
除此以外,锻压还包括精密模锻、挤压成形、轧制成形以及精密冲裁等。
焊接通常需要加热或加压,使工件的原子互相结合。
由于机械制造基础学习的是关于金属的知识,因此没有涉及到高分子材料的焊接。
焊接是一种不可替代的制造方法,几乎所有工业部门都需要焊接。
焊接方法可分为熔焊、压焊和钎焊三种,主要用于制造金属结构、机器零件和工具等。
- 1、下载文档前请自行甄别文档内容的完整性,平台不提供额外的编辑、内容补充、找答案等附加服务。
- 2、"仅部分预览"的文档,不可在线预览部分如存在完整性等问题,可反馈申请退款(可完整预览的文档不适用该条件!)。
- 3、如文档侵犯您的权益,请联系客服反馈,我们会尽快为您处理(人工客服工作时间:9:00-18:30)。
热加工实训心得体会
导语:我们通过培训进行了热加工工艺的学习内容主要包含铸造、锻压、焊接以及金属材料的前沿知识知识以下是小编为大家整理的热加工实训心得体会欢迎大家阅读与借鉴!
铸造是历史最悠久的制造工艺通过铸造可以得到内腔和外形很复杂的毛坯可以针对各种合金进行铸造并且铸造件的尺寸大小可以在一个很大的范围内波动但是同时铸造也存在一些缺点比如组织疏松晶粒粗大力学性能较差和难以精确控制等尽管如此随着铸造技术的发展特种铸造工艺的诞生铸造的精确度已经可以提高到CT4表面粗糙度最小可以提高到0.8um各种材料的铸造性能有很大的差距这主要由金属的液态成形特征决定
锻压是对金属坯料施加外力使之产生塑性变形以改变其形状、尺寸并改善其内部组织性能从而获得所需毛坯或零件的加工方法锻压包含锻造和冲压两种锻压不同于铸造的主要是金属的加工形态通常锻压的毛坯是由铸造所得到的锻压件的组织致密力学性能明显好于相同化学成分的铸件锻造的过程主要是金属晶粒的变形金属晶粒变形的特性和锻造流线的连贯性决定了所锻造出来的锻件的质量锻造分为自由锻和模锻模锻的精度要高于自由锻自由锻投资费用低但是只适用于单件及小批量生产模锻是整体成形易于实现机械化和自动化它只适用于中、小型锻件的成批或大批量生产并且需要专门的模锻设备投资较高冲压主要是正对金属板料的加工低碳钢、奥氏体不锈钢以及铜、铝等有色金属通常用于冲压板料对于板料的冲压通常有冲
裁、弯曲、拉深、胀形等除此以外锻压还包括精密模锻、挤压成形、轧制成形以及精密冲裁等
焊接通常需要加热或加压使工件的原子互相结合由于机械制造基础学习的是关于金属的知识因此没有涉及到高分子材料的焊接焊
接是一种不可替代的制造方法几乎所有工业部门都需要焊接焊接方
法可分为熔焊、压焊和钎焊三种主要用于制造金属结构、机器零件和工具等焊接省料省工并可以简化工艺所得焊件质量轻而性能好但是
焊接是不可拆卸连接而且焊缝会存在力学与结构上的缺陷因此焊接
质量存在一定问题常用的焊接方法有焊条电弧焊、埋弧自动焊、气体保护电弧焊、等离子弧焊、电阻焊、摩擦焊和钎焊等焊条电弧焊是手工焊接的主要方式主要适用于单件小批生产;埋弧自动焊主要用于成批生产的平焊和平角焊;气体保护焊得到的焊件质量较好并且能对金属起到保护作用;等离子弧焊广泛用于航空航天等军工和尖端工业技术上不同的材料具有不同的焊接性通常按照碳当量来计算和判断金属及其合金可分为黑色金属和有色金属两大类金属材料的力学性能包括强度、塑性、硬度、人性和疲劳强度等金属所具有的性能特性决定了金属的加工方法以及所使用的场合除此以外这一章还介
绍了金属的晶体结构的知识主要类型有体心立方晶格、面心立方晶格和密排六方晶格等三种通常一种金属在固态下存在一种晶格形式有
些金属在固态下存在两种或两种以上的晶格形式在金属里最重要的
是铁碳合金铁碳相图则是这一章的核心内容铁碳合金随着温度的变
化会有不同的结合方式从而产生不同的形态随着碳含量的不同以及
温度的不同铁碳合金会成为不同的材料具有不同的特性对于钢来说热处理包括普通热处理、表面热处理和其他热处理通过热处理以后钢材的力学性质会得到很好的改善这主要是因为热处理使得钢材的晶体结构发生了变化
热加工部分主要就是学习了这些内容对热加工的学习为冷加工奠定了基础冷加工中的坯料都是由热加工所得到并且进行过冷加工以后通常要进行热加工改善零件的性能
在冷加工的学习过程中最先介绍了加工精度以及表面质量的知识每种加工方法有各自的尺寸公差等级范围和表面粗糙度Ra不同的构件在不同的使用场合具有特定的精度要求如一半的车削加工加工精度随着车削阶段的不同变化粗加工精度可以达到11级而超精密的切削加工可以达到高于3级的精度表面粗糙度仅为0.012或者更低冷加工中最重要的部分就是切削加工它的本质就是将材料从原来的坯料上减去与铸造等恰恰相反切削加工可以分为机械加工和钳工加工两类机械加工的方法又有车、钻、镗、铣、铇、拉、磨、珩磨和超精加工钳工的加工包括划线、锯削、錾削、锉削、钻孔、扩孔等切削过程中切削速度、进给量和吃刀量是切削用量的三要素切削加工中最重要的是刀具不同形状的刀具有不同的用处如端头车(本文是工作实用文档频道提供的范文)刀主要车断面车孔刀主要用来车内孔外圆车刀主要用来车外圆等等金属的切削过程实际上是金属塑性变形的过程在切削力的作用下对金属进行切削切削过程
中会产生积削瘤和切削热对刀具造成一定的影响并且切削会使物体内部具有参与应力不利于优化产品
磨削通常用在对产品的精加工上磨削的本质其实就是无数个小的切削、刻划和摩擦抛光过程的结合在切削的过程中磨粒不断脱落露出里面新的磨粒磨削可以分为普通磨削、无心磨削、高效磨削、低粗糙度磨削和砂带磨削等通常他们都被用来加工高硬度材料塑性很大的金属除外普通刀具的加工中车削加工主要可以加工外圆、孔和平面钻削主要是钻孔、扩孔、铰孔和锪孔孔的加工中第一步通常是通过钻孔得到的铣削加工通常用来铣平面和沟槽刨削也可以加工平面和沟槽但是两者比较来说铣削的效率高于刨削加工范围也更广但是成本高
接下来就是精密加工了精密加工可以使零件的加工精度提高到1~0.1um表面粗糙度为0.1~0.008um主要包含研磨、珩磨、超精加工和抛光等在这些加工方法中研磨需要很多的时间而珩磨可以通过机械化实现广泛用于大批大量生产除此以外各种不同的加工方法都有自己的加工特点
特种加工工艺是为了解决前面的加工方法所不能达到加工目的的问题而探索得到的特种加工可以直接利用电能、电化学能、声能或光能等能量对材料进行加工得到的零件机械应力不明显并且可以加工各种材料
电火花加工是一种运用很广泛的特种加工方法主要运用的是电蚀现象来切割和成形电火花加工必须提供一个脉冲电源采用自动进
给调节装置来保证间隙还要在有一定绝缘度的液体介质中进行运用
这种方法可以加工任何高齐纳高度硬度和韧性的导电材料可以在一
台机床上进行从粗加工到精加工的程序但是电火花加工有可能导致
电极容易损耗并且效率低精度也不高电火花可以用来磨削、镗孔、切割和成形
电解加工是电化学加工中的一种重要方法它主要利用的是金属在电解液中产生阳极溶解的电化学原理来进行的电解加工一个突出
的特点是工件阳极和睡不断消耗而工具阴极和氧化钠并不消耗电解
加工的生产效率较高能以简单的进给运动一次加工出形状复杂的形
状与型面并且不受材料本身的限制但是看它需要的附属设备多且造
价高加工稳定性尚不够高电解加工主要用于电解锻模型腔和整体叶
轮她解决了一直以来叶轮为分体结构最后再连接起来而导致的硬度
与刚性不够的问题除此以外电解还用来去毛刺
超声波加工主要用于加工型孔型腔、进行切削加工、清洗和焊接它还可以用于测距和无损检测并做成超声手术刀激光加工也是特
种结构的一种方法它最大的特点是可以透过透明材料进行加工而且
可以反射和折射具有光的特性电子束加工和离子束加工的主要区别
是粒子种类的区别电子束加工主要靠热效应进行加工可以用于打孔、切割、焊接、蚀刻和光刻等离子束加工可以用来蚀刻、沉积、镀膜和注入
另外培训还介绍了关于结构工艺性的知识例如壁厚原则、拔模斜度原则、圆角原则等在最后老师还带领我们了解了关于数控机床和现代机械制造工业的发展状况让我颇有收益。