呋喃树脂自硬砂控制技术
酸自硬呋喃树脂砂的工艺要点及缺陷防止

表 4 国产常用磺酸 固化 剂技术 指标
型 号\ /・ 一 ge m
1 原材 料 的选择
般依据铸件 的大小和材质以及成本来选择不
同含氮量的呋喃自硬树脂 , 参见表 2和表 3 。此外 ,
对其粘度 、 游离甲醛含量、 H值等技 术指标也应提 P
出严格要求 。综合考虑 , 一般灰铸铁件和球铁件用 呋喃树脂的含氮量应控制在表 2 所示范围内。目前
自硬砂对原材料 的品质极为敏感 , 铸件质量必 须从原材料抓起。
O3 .
5O . 3O .
1 3 固化 剂和 硅烷 .
4 。对甲苯磺酸的缺点是在温度控制条件较差 的情 况下 , 冬季使用 时固化往往很缓慢. 故某些树脂厂在 冬季用固化剂 中或为降低成本有时可能会采用硫酸 乙脂。这是冬季树脂砂球铁件废品率上升的一个原
因。
游离酸
固化剂对型砂的重要性并不次于树脂。一般都 选用对甲苯磺酸水或醇溶液作 固化剂。通常用 固化 剂的总酸度来衡量其涪 l大小 , 生 固化剂的含量越多 , 其活性越大。国产常用磺酸固化剂 的技术指标见表
1 2 酸硬 化 呋喃 自硬 树 脂( 醛呋 喃树 脂 ) . 尿
一
量不高 、 砂铁 比较小的情 况。但 由于原辅材料性能 不稳定 , 旧砂再生工艺完整性差 , 使用者对 自硬砂的 特点和关键技术认识不足 , 加上疏于工艺控制 和管 理, 所以能实现正 常化生产 的尚不多。 以下简述该 工艺生产铸铁件的若干要点及缺陷防止 。
≥10 .
球铁 、 一般铸钢
D 低氮 ) (
> . ~ . O 3 2O
混合料中加入粘结剂的质量分数为 1 %时所具有的抗 拉强 度 , 它是衡 量树脂粘 结效 率高低的指标 。
呋喃树脂砂在铸造生产中的应用及质量控制

呋喃树脂砂在铸造生产中的应用及质量控制摘要呋喃树脂砂是近20年来发展最快的铸造工艺之一,用呋喃树脂砂生产的铸件,尺寸精确、表面光洁、棱角清晰、废品率低,并能节约造型工时、提高生产效率、改善劳动条件和成产环境。
2007年,山东安信机械制造有限公司对铸造车间进行技术改造,建立了一条树脂砂生产线,再该条生产线正式投产前,通过对员工进行系统的技术培训,制定相关的规章制度和操作规范,顺利实现了由水玻璃砂生产工艺向树脂砂生产工艺的转变。
本文对铸造生产各工序的过程控制作一简单阐述。
关键词呋喃树脂砂;铸造;生产;质量控制1 铸造工艺的控制呋喃树脂砂的特点是瞬间发气量大,高温溃散性好,易产加成气孔、夹渣和冲砂缺陷,在设计浇注系统时,应坚持快速、平稳、分散的浇注原则,浇注系统的截面积要比粘土砂工艺稍大一些,内浇道要分散放置。
树脂砂强度高、刚性好,铸件不容易产生缩孔缺陷,故应采用相对较高的浇注温度,以避免出现气孔和夹渣缺陷,厚大铸铁件的浇注温度也不应低于1 320℃。
2 砂型质量的控制2.1 原材料的选择及要求2.1.1 原砂树脂砂工艺对原砂的要求很高,原砂的粒度应根据主要产品的壁厚来确定,由于我公司主要以生产薄壁铸件为主,且未配备原砂烘干设备,故选用了粒度为50/100目的烘干擦洗砂。
2.1.2 树脂、固化剂国内成产树脂、固化剂的厂家很多,但具有自主研发能力、具备完善的检测设备和严密可靠的质量保证体系的厂家屈指可数。
经检验、对比,我们选用了济南圣泉集团股份有限公司生产的环保型呋喃树脂和磺酸固化剂,树脂加入量一般为原砂重量的1.0%~1.2%。
3 型砂工艺参数的控制3.1 可使用时间在生产过程中,我们将型砂表面开始固化的时间作为型砂的可使用时间,一般情况下,型砂的可使用时间应控制在6~10min,对于大型铸型或砂芯,可使用时间可延长15min,通过调整固化剂的加入量来控制型砂的可使用时间。
3.2 型砂强度初强度:是指型砂在1h的抗拉强度,型砂的初强度应控制在0.1~0.4MPa。
呋喃树脂自硬砂控制技术

呋喃树脂自硬砂控制技术程利军零正技罗勇广西柳工机械股份有限公司广西柳州545007)摘要本文主要从硅砂的性能要求、造型过程的控制和再生砂的回用等对呋喃树脂自硬砂技术进行了探讨,供广大铸造同行参考。
关键词呋喃树脂自硬砂硅砂造型再生砂在线检测随着中国制造业近几年的长足发展,中国的铸造业也迎来了历史上最好的发展机遇。
目前,我国铸件的产量已连续多年位居世界之首。
呋喃树脂自硬砂工艺由于其生产周期短、铸件表面精度高、铸件质量容易控制、柔性化制造能力高等特点,已经被广泛的应用到机床铸件、耐磨铸件、工程机械铸件等产品中。
而铸造企业能否发挥呋喃树脂自硬砂的特点,有效的提高铸件的质量,这与型砂的控制技术有着密切的关系。
砂型铸造行业公认型砂控制技术、熔炼控制技术和管理水平三者决定了一个铸造厂在市场上的竞争能力,由此可见型砂的控制技术在铸造业中的重要性。
本文就呋喃树脂砂的一些控制技术提出一些个人的观点,希望同行提出批评指正。
1硅砂的技术要求1.1 硅砂的粒度组成硅砂的粒度反映了硅砂的颗粒大小和分布状态。
由于自硬砂强度的获得是依靠呋喃树脂“包覆”硅砂表面形成的高分子链,所以硅砂的粒度越细,从理论上说获得同样强度的树脂消耗量就越大,型砂的成本也就越高,所以在保证铸件不发生粘砂缺陷的前提下,尽可能提高硅砂的粒度。
1.2硅砂的角形系数硅砂的角形系数S=Sw/St图l试样抗拉强度与型砂粒度关系注:实验型砂组成的余量为0.212目以下Sw一硅砂的实际比表面积(cm2/g)St一硅砂的理论比表面积(cm2/g)硅砂的角形系数越小,表面就越园整,同样体积的硅砂表面积越小,硅砂和呋喃树脂的物理和化学结合力就越强,获得同样的抗拉强度需要的树脂消耗量就越低。
作为自硬砂用的硅砂角性系数要求≤1.30,最好≤1.15。
1.3硅砂的加工处理由于天然硅砂有大量直径小于0.02的泥分和一些污染物和一些有碱性的物资,泥分的存在极大的降低了硅砂的粒度组成,提高了树脂的消耗量,同时有碱性的物资在树脂砂硬化过程中消耗了大量的催化剂——对甲苯磺酸等物资,造成砂型硬化很慢甚至不硬化,所以硅砂必须经过擦洗和粒度分选处理。
自硬树脂再生砂质量控制

自硬树脂再生砂的质量控制自硬树脂砂一般多采用机械再生法。
通常情况下,自硬树脂砂的质量控制项目有:粒度分布、微粉含量、残留含水量、灼烧减量、残留含氮量、残留含碳量、耗酸量、耗碱量、含硫量、含氧化铁量、砂温、室温等。
一、粒度分布、微粉含量和残留含水量新砂及其再生砂的粒度分布、微粉含量和残留含水量等变化情况见下表所列。
微粉含量指砂中颗粒度在150目以下(有的指200目以下)至底盘以上微粉,以及底盘中至大于20um的粉尘的总含量。
(注:微粉:对30/50、40/70筛号的原砂,140筛号以下称为微粉;对50/100、70/140筛号的原砂,200筛号以下为微粉;对100/200筛号的原砂,270筛号以下为微粉。
)表:粒度分布、微粉含量和残留含水量表:日本丰田工厂所用新砂和再生砂的对比微粉含量高,不但降低树脂砂的强度(如在再生砂中增加150目以下的微粉0.5%,则树脂砂强度将降低20%),而且会降低它的表面稳定性,同时还要增加粘结剂的加入量,以及使再生砂的灼烧减量大大增高,从而引起铸件的气孔缺陷。
在日常生产中,一般要求微粉含量<1%-1.5%,底盘上的粉尘含量<0.2%。
在旧砂再生时,可以通过调整机械再生装置的除尘抽风量来控制微粉含量;若大于要求值,可加大抽风量,将微粉抽出。
在再生砂质量控制较好的工厂中,经过多次除尘处理后,再生砂中的微粉含量一般比新砂的要低。
在日常生产中为了检查砂子的粒度分布和微粉含量的变化情况,每月至少要测定一次。
因为再生砂反复使用时砂颗粒有变小的趋势(其程度与砂粒结构、新砂的粒度分布等有关),所以要求砂粒结构为单一晶体,而不要是复合结晶的。
新砂的含水量仅与其干净程度和运输过程等有关,而再生砂中的含水量则与生产管理有关。
新砂、再生砂的含水量一般要求<0.2%。
含水量对树脂砂的强度和硬化速度有明显的不利影响,特别是对尿烷系自硬树脂砂。
因此,在回收、再生处理时切不可在循环系统中混入水份。
【坛友分享】浅析呋喃树脂自硬砂铸造的生产技术和应用

【坛友分享】浅析呋喃树脂自硬砂铸造的生产技术和应用1、自硬呋喃树脂砂铸造中所需原材料的选用1) 铸造用砂的要求原砂对呋喃树脂砂的性能粘结剂用量以及铸件表面质量的影响很大,要求原砂中的SiO2含量要高,含泥量和酸耗值要低。
建议粒度:大件42或30组别,中件21组别,小件15或10组别。
2) 呋喃树脂呋喃树脂是由糠醇生产而成的树脂,其糠醇含量较高,树脂的存放性能得以改善,热强度高但增加了成本。
树脂中的游离甲醛是生产中产生刺激性气体的来源,也是恶化环境的因素之一,应加控制(如铸造厂效率较好建议选用低甲醛呋喃树脂,保护环境)。
铸铁件生产应选用低氮或无氮树脂,实际应用根据铸件的技术要求和结构来选择。
3) 固化剂一般采用有机磺酸溶液按其水溶液或醇溶液的浓度来调节固化速度,铸造厂可以根据自己的工艺要求进行固化时间的调节,十分方便。
4) 添加剂(硅烷作偶联剂)为改善呋喃树脂自硬砂的性能,配比中常加入一些添加剂。
加入少量的硅烷作偶联剂,可显著的提高树脂砂强度,但随着时间的延长作用逐渐减弱,一般两个月将消失。
因此在国内由用户在使用之前加入并搅拌均匀,应尽快用完,也有部分呋喃树脂生产厂家为了方便客户,出厂之前便已经添加了硅烷。
(因此使用的时候必须注意时效问题)2、旧砂的再生和回收利用(降低成本)旧砂能很好的回收与再生是呋喃树脂砂的一大优点之一。
如何控制好再生砂的质量,是生产出高质量树脂砂铸件的关键质量树脂砂铸件的关键。
1) 砂温调节稳定砂温是呋喃树脂自硬砂的关键,尤其是再生砂的砂温,因此砂温调节是必不可少的。
如果砂温能控制好的话,它即可提高生产效率,可减少数珠加入量,又可减少砂型损坏和铸造缺陷,降低成本。
2) 关于呋喃树脂再生砂的质量指标@再生砂的酸耗值和PH值对于用酸作固化剂的呋喃树脂,酸耗值通常取负值;PH值过高就较难确定酸固化剂合适的加入量,一般PH值控制在3~6的范围。
@再生砂的灼减量和发气量灼减量是衡量树脂砂型中硬化粘结剂的残留量的大致标准。
再生砂对呋喃树脂自硬砂工艺性能的影响及其控制

的使用经济 性考虑 ,粘 结剂膜 的减薄 要 比完全去
除 更 为 有 利 。 因 为 当两 个 再 生 砂 粒 被 新 粘 结 剂 粘
结 时 ,可 产 生 图 2所 示 的 三 种 断 裂 , 即 发 生 在 旧
粘 结剂 与砂 粒表 面之 间 ( A型 ) 新 旧粘 结 剂 之 、 间 ( 型 ) 的 断裂 和 新 粘 结 剂 自身 的 内聚 断 裂 ( B C
降低 生 产 成 本 ,改 善 砂 子 的 性 能 ,提 高 型 砂 的 强 度 、 透 气 性 , 降 低 发 气 量 ,这 些 也 是 呋 喃 树 脂 砂
在 铸 造 行 业 得 到 广 泛 应 用 的 重 要 原 因 。本 文 将 对 再生 砂 性 能 指标 及 其 控 制 进 行一 些 讨 论 。
圃 造n 铸 e FE程 oni u工n ngg di re yr
再 生 砂 对 呋 喃 树 脂 自硬 砂 工 艺 性 能 的影 响 及 其 控 制
涂建平 ( 浙江佳 力风 能技术有 限公 司,浙江 杭州 3 4 ) 1 2 1 1
摘 要 :分析 了呋 喃树 脂 再 生 砂 的 灼 减量 、微 粉 含 量 、含 氮量 、砂 温 、酸耗 值 对 型 砂 工 艺 性 能 的 影 响 。通 过对 砂 铁 比 、 浇注 温度 、粘 结 剂和 固化 剂 用 量加 以控 制 ,优化 型砂 性 能 ,减 少 铸 件 不 良品 的产 生 。
Tu Janp n i ig
(h j n il o e e h oo yC .Ld, a g h u3 1 4 , h j n , hn ) Z ei gJ i w r c n l o, t.H n z o 1 2 1 Z ei g C i a a P T g a a
浅谈呋喃树脂自硬砂的生产及应用
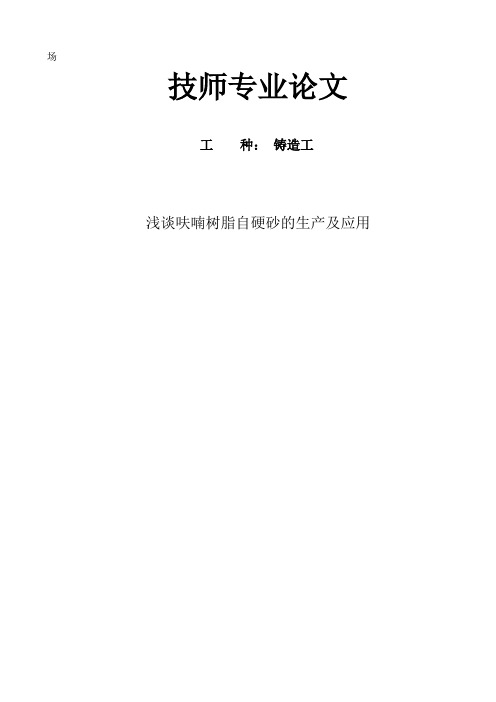
场技师专业论文工种:铸造工浅谈呋喃树脂自硬砂的生产及应用摘要 (2)引言 (2)1.呋喃树脂砂性能的优缺点 (2)2.呋喃树脂自硬砂的生产工艺技术 (3)3.工艺及现场控制 (6)4.呋喃自硬树脂砂铸件的缺陷分析及防止措施 (8)5.结论 (9)参考文献 (10)本论文针对呋喃树脂自硬砂的坭芯生产,阐述了呋喃树脂自硬砂的原材料配比、混制及硬化工艺。
结合作者多年在实际生产工作中的经验,就生产中出现的实际问题进行分析和讨论,通过采取文中提出的控制、解决措施,有效地解决了铸件出现的气孔、粘砂、热裂、冲/夹砂、脉纹等铸造缺陷。
关键词:呋喃树脂自硬砂、铸造缺陷、夹砂、热裂、脉纹引言呋喃树脂自硬砂工艺是指在呋喃树脂砂中加入一定量的酸性固化剂,使之在芯盒或砂箱内经历一定时间后,在常温条件下通过自行硬化成型(不需烘烤或吹入硬化气体)的一种造型制芯工艺。
呋喃树脂自硬砂硬化反应机理可简单描述为:涂敷在砂粒表面的树脂在酸性固化剂的催化作用下,呋喃树脂分子上的活性氢、羟甲基与羟甲基之间发生缩聚反应和呋喃环上的双键打开发生加成聚合反应,形成三维网状结构固体树脂,使型(芯)砂硬化成型。
1.呋喃树脂砂性能的优缺点1.1优点1)铸件的尺寸精度高、外部轮廓清晰、铸件表面光洁,外观质量好、组织致密、铸件综合品质高。
2)呋喃树脂自硬砂具有较好的流动性,容易紧实,脱模时间可调节,硬化后强度高,在其后的搬运及合箱过程中不变形,因树脂砂的强度高,在浇注和凝固过程中基本上不会出现位移现象,所以铸件的尺寸精度高。
3)不用烘干,缩短了生产周期、节省了能源、芯砂易紧实、溃散性好、容易清理、大幅度降低了劳动强度,为实现机械化生产创造了条件。
1.2 呋喃树脂自硬砂的不足之处1)对原砂质量要求高2)在生产过程中有刺激性气味3)采用树脂砂生产,成本较高2.呋喃树脂自硬砂的生产工艺技术2.1 原材料的选用1)铸造用砂的要求:原砂对呋喃树脂砂的性能、粘结剂用量、以及对铸件表面质量的影响很大,要求原砂中的SiO2含量要高、含泥量和酸耗值要低。
铸造呋喃树脂自硬砂工艺

目前,世界上最常用的自硬性呋喃树脂有以下三种类型:(1) 脲醛呋喃树脂;(2) 酚醛呋喃树脂;(3) 酚 脲醛呋喃树脂。现分述于下。
1. 脲醛呋喃树脂(UF/FA) 它是由尿素、甲醛和糠醇三种组分缩合而成的。可以认为是糠醇改性的脲醛树脂。不含糠醇的脲醛树 脂常温和高温强度都较低,只能用作轻金属的型砂粘结剂。而100%糠醇的树脂需要加入较多的硬化剂,才 能有良好的硬化性能,型芯比较脆。一般用的酸自硬呋喃树脂,其糠醇含量都大于50%。糠醇含量越高,树 脂的高温强度也越高,耐高温冲刷和浸蚀性能越好,但树脂的价格则越贵。然而,随糠醇含量增加,树脂 的粘度降低,容易包覆在砂粒表面从而减少树脂加入量。反之,糠醇含量低,树脂中的含氮量相应提高, 铸件产生气孔类缺陷的倾向就越大。树脂中的含氮量基本能反映出树脂中脲醛的含量。因为氮的含量是脲 醛的1/4~1/5。例如,呋喃树脂中脲醛含量30%时,含氮量约为 7%。糠醇量低的 UF/FA树脂只用于铝、镁 合金用的自硬树脂粘结剂,可使出砂性良好。铸铁和铸钢件树脂自硬砂用粘结剂中糠醇含量应较高,大多 数铸铁工厂使用含氮量4~5%的UF/FA树脂。脲醛呋喃树脂为淡黄色到深褐色的粘稠液体。 由于分子中含有羟甲基、活性氢原子,以及呋喃环上的不饱和双键等活性基团,在酸性催化剂作用 下,分子间可以进一步发生失水缩聚和双键间聚合等交联反应,变成体型结构而迅速硬化。 2. 酚醛呋喃树脂(PF/FA) 它是由苯酚、甲醛和糠醇三种组分缩合成的。树脂中不含氮,或含极少量氮,适合生产铸钢件。在酚 醛呋喃树脂中,增加糠醇含量,可提高型芯的常温强度,高温强度也高,能够耐钢水的冲刷和压力。树脂 中糠醇含量相等的 UF/FA 和 PF/FA 树脂相比较,后者的常温强度较低,硬透性较差,树脂的脆性增加,有 增加铸件表面飞刺脉纹缺陷的倾向。但酚醛呋喃树脂砂的高温强度却是很好的。 3. 酚脲醛呋喃树脂(UF/PF/FA) 是由尿素、苯酚、甲醛和糠醇四种组分缩合成的共聚物树脂。它既有脲醛呋喃树脂的优点,又有酚醛 呋喃树脂的优点,同时又避免两种树脂的缺点。在合成树脂时,用苯酚代替一部分尿素制得的。
- 1、下载文档前请自行甄别文档内容的完整性,平台不提供额外的编辑、内容补充、找答案等附加服务。
- 2、"仅部分预览"的文档,不可在线预览部分如存在完整性等问题,可反馈申请退款(可完整预览的文档不适用该条件!)。
- 3、如文档侵犯您的权益,请联系客服反馈,我们会尽快为您处理(人工客服工作时间:9:00-18:30)。
呋喃树脂自硬砂控制技术程利军零正技罗勇广西柳工机械股份有限公司广西柳州545007)摘要本文主要从硅砂的性能要求、造型过程的控制和再生砂的回用等对呋喃树脂自硬砂技术进行了探讨,供广大铸造同行参考。
关键词呋喃树脂自硬砂硅砂造型再生砂在线检测随着中国制造业近几年的长足发展,中国的铸造业也迎来了历史上最好的发展机遇。
目前,我国铸件的产量已连续多年位居世界之首。
呋喃树脂自硬砂工艺由于其生产周期短、铸件表面精度高、铸件质量容易控制、柔性化制造能力高等特点,已经被广泛的应用到机床铸件、耐磨铸件、工程机械铸件等产品中。
而铸造企业能否发挥呋喃树脂自硬砂的特点,有效的提高铸件的质量,这与型砂的控制技术有着密切的关系。
砂型铸造行业公认型砂控制技术、熔炼控制技术和管理水平三者决定了一个铸造厂在市场上的竞争能力,由此可见型砂的控制技术在铸造业中的重要性。
本文就呋喃树脂砂的一些控制技术提出一些个人的观点,希望同行提出批评指正。
1硅砂的技术要求1.1 硅砂的粒度组成硅砂的粒度反映了硅砂的颗粒大小和分布状态。
由于自硬砂强度的获得是依靠呋喃树脂“包覆”硅砂表面形成的高分子链,所以硅砂的粒度越细,从理论上说获得同样强度的树脂消耗量就越大,型砂的成本也就越高,所以在保证铸件不发生粘砂缺陷的前提下,尽可能提高硅砂的粒度。
1.2硅砂的角形系数硅砂的角形系数S=Sw/St图l试样抗拉强度与型砂粒度关系注:实验型砂组成的余量为0.212目以下Sw一硅砂的实际比表面积(cm2/g)St一硅砂的理论比表面积(cm2/g)硅砂的角形系数越小,表面就越园整,同样体积的硅砂表面积越小,硅砂和呋喃树脂的物理和化学结合力就越强,获得同样的抗拉强度需要的树脂消耗量就越低。
作为自硬砂用的硅砂角性系数要求≤1.30,最好≤1.15。
1.3硅砂的加工处理由于天然硅砂有大量直径小于0.02的泥分和一些污染物和一些有碱性的物资,泥分的存在极大的降低了硅砂的粒度组成,提高了树脂的消耗量,同时有碱性的物资在树脂砂硬化过程中消耗了大量的催化剂——对甲苯磺酸等物资,造成砂型硬化很慢甚至不硬化,所以硅砂必须经过擦洗和粒度分选处理。
在处理过程中,必须注意对擦洗用水的管理。
一些硅砂供应商擦洗用水控制不严,导致含泥量超标或碱度过大,导致擦洗砂质量较差。
好的擦洗砂泥分的质量分数应≤0.3%,耗酸值应≤5ml。
1.4 SiO2含量作为自硬砂用硅砂的si0:含量应不低于98%,原因在于大多数铸造厂自硬砂都在经过再生后使用。
SiO2含量越低,硅砂经重复使用后的破碎率越高,再生砂的粒度会变细,这就大大的增加了树脂的耗用量(见图2)。
2呋喃树脂自硬砂混碾工艺参数的控制2.1时间的控制混碾时间——是指物料(树脂、催化剂、硅砂)从加料到混合均匀的时间。
可使用时间——是指自硬砂从混碾后到硬化开始反映的时间。
起模时间——是指自硬砂型砂开始固化到强度达到70—80%终强度的时间。
硬化时间——是指自硬砂型砂开始固化到完全固化的时间。
理想的自硬砂时间控制曲线见图图3理想的自硬砂时间控制曲线图混碾时间越长,自硬砂混碾效果越好。
但由于树脂硬化反应的限制,混碾时间不可能很长,工艺控制最好在10—30s左右,这就要求混砂机的混砂效率要高。
可使用时间越长,型砂的充填和紧实性能越好,越有利于砂型的紧实。
2.2紧实率的控制由于树脂砂流动性好,在生产过程中无须通过紧实就可获得所需要的抗拉强度,故树脂砂的紧实很多铸造厂未给予高度的重视,甚至认为没有必要。
经实际测试,在同种材料同样配比的条件下,紧实过的型砂抗拉强度是未紧实过的2倍以上,由此可见型砂紧实的重要性。
有些厂认为强度不足只是由于树脂添加量不足或材料质量有问题,实际上只是由于工人在可使用时间内由于偷懒没有紧实造成的。
砂型没有经过紧实,给铸件质量也容易带来相当不利的影响,如铸件出现大面积粘砂、甚至导致无法清理而报废,砂眼缺陷明显增加等。
所以对于紧实率应给予高度重视,砂型的紧实程度越高越好,不但可以降低树脂的加人量,同时也可减少铸件的粘砂、夹砂等缺陷。
当然,砂型紧实必须在可使用时间内完成,而且越快越好,否则紧实不但不会增加强度,反而会破坏在自硬砂在硬化过程中由树脂化学反应形成的高分子链,大大的降低砂型的强度。
2.3物料加入比例在通常情况下,树脂的加入比例约为硅砂的0.8-1.2%,催化剂为树脂的30—50%。
在实际生产中,由于硅砂的定量原理大多使用气动砂闸依靠压缩空气打开砂门,这样会出现由于压缩空气压力的波动、砂斗砂量的变化、砂闸的机械磨损导致砂量波动较大。
由于砂量的波动,导致树脂和催化剂的加入比例出现异常波动,从而导致砂型的质量出现异常波动。
所以,对于自硬砂三种物料的配比,必须定期测量和纠正,最好在15天左右校正一次,这样才能有效的控制加入比例和砂型质量。
数据的测量不仅为一个测试值,还应给出其合理的波动范围即公差作为控制的依据,图4为树脂定量的拟合线图:2.4.关注催化剂的用量很多使用呋喃树脂自硬砂的铸造厂为了提高造型效率,只是简单通过催化剂的添加量来实现,其实这是非常错误的。
图5为一个催化剂加入比例为60%的情况下自硬砂的可使用时间分析,由此可看出催化剂添加过量所带来的不良影响:由上图可看出,自硬砂的可使用时间仅为一分钟左右,若砂型充填和紧实工作超过一分钟以上,砂型抗拉强度将至少下降20—40%。
实际上可能在一分钟内砂型的充填工作都可能没有完成。
而且,催化剂用量越大,对设备的腐蚀越大,而且催化剂中含有的化学元素s将会使球铁的金相组织产生异常导致团絮状甚至片状石墨的产生,降低铸件的机械性能。
由此可见,催化剂的用量越少越好,适量即可,过量只会增加成本和降低砂型质量。
为了提高白硬砂的生产效率,可采用模具预热、增加砂箱的流转量的方法,同时有些专家建议使用适合树脂砂生产的模具如树脂模等,可有效的提高树脂砂的造型效率。
2.5混砂机好的物料和配比必须经过充分混碾才能达到理想的效果。
通常对呋喃树脂自硬砂混砂机的性能可以通过如下方法进行测定:混砂机的混砂效率=混砂机混碾型砂强度腻验室检测的标准混砂强度x100%由于实际强度接近平台区的升幅极为缓慢,故认为混砂效率能够达到85—90%就可以判定棍砂机的工作基本正常。
对于混砂机我们必须关注混砂轴的转速,只有在单位时间内获得高的转速才能使物料进行足够的搅拌,才能充分发挥树脂的粘结作用。
我们发现,两台不同厂家生产的同样规格的混砂机,混砂效率存在很大的差异,究其原因主要是混砂机的功率不同导致。
对于混砂机的选用,要尽可能使用混砂机的最大混砂量,因为只有这样才能提高生产效率和延长自硬砂的可使用时间,同时可降低大大降低能量的损失。
混砂机的日常使用和保养同样非常关键。
有的铸造厂对此忽视管理,经常发生混砂筒内粘有大量死砂块,造成有效?昆砂通道减少,导致型砂}昆制不均匀而强度大副降低。
同时由于混砂刀片和筒壁的磨损,也会造成无效混砂面积加大而导致型砂混制不均匀。
一般认为,刀头和筒壁的间隙不能超过8mm,超过后强度下降将非常明显。
3 自硬砂再生砂的处理3.1 再生砂的理论复用次数若再生砂系统砂循环总量为100%,,每天由砂芯补充的型砂为10%,在再生砂的复用次数符合如下公式:(1-0.1/1.1)n≤5%经过计算,大约经过30次循环后,砂系统中大约95%的再生砂将会被砂芯的新砂替代。
由于砂系统的总量为确定的,复用次数主要取决于新砂的补充比例。
若铸件复杂,砂芯重量和数量较大或为了保证砂系统砂量的平衡,则再生砂的复用次数将减少。
3.2砂系统的再生处理技术随着国家和社会对环保的重视,旧砂丢弃的成本已越来越高。
据有关报导,美国丢弃一吨旧砂的成本是购买一吨新砂的成本2—3倍。
相信在不久的将来,我国也会出台相关的法规。
这就需要对旧砂进行再生回收处理。
现在目前的自硬砂再生技术主要采用热法再生和摩擦再生两种方式。
经过处理后再生砂某些指标能够达到甚至超过新砂的性能。
热法再生主要使用沸腾燃烧炉将旧砂加热到600—700度之间,以去除砂粒表面的树脂膜。
经过热法再生处理,旧砂的L.O.I可以得到有效的控制。
但需要注意的是硅砂的强度可能会降低,在使用过程中由于破碎而产生大量的粉尘,另外还需注意由于旧砂耗酸值过高而影响固化的问题。
摩擦再生是将旧砂通过振动、气流或机械冲击的方法去除砂粒表面的树脂膜,降低粉尘和L.O.I值。
由于摩擦再生无法彻底去除砂粒表面的树脂,所以旧砂经过再生处理后不宜采用气力或机械方法发送旧砂而应采用皮带或斗提式等方法运送再生砂,原因在于在输送过程中由于再生砂由于摩擦或破碎而使表面覆盖的树脂膜再次脱落和砂粒破碎会再次产生粉尘,从而降低再生砂的质量。
再生砂的处理技术要结合旧砂的类型和处理后再生砂使用的粘结剂的类型考虑。
不同的使用场合使用不同的处理技术。
4 型砂在线检测技术由于呋喃树脂自硬砂可使用时间对时间的控制较为严格,而传统的终强度检测又要求在24小时后检测,为了实时反映型砂的质量,必须对型砂在线检测技术进行研究。
由于型砂质量的波动是一个长期的过程,对铸件质量存在潜移默化的影响。
砂系统中循环使用的型砂质量一旦出现问题,则将对铸件的质量和成本产生严重的影响,而对其改善也需要很长的时间才能完成。
故加强对型砂质量的监测很有必要。
4.1很多铸造厂对再生砂仅在旧砂再生后检测粒度分布、L.O.I值、含灰量等,但回用砂在经过再生处理到混砂机处使用要经过气力或机械输送,必然会影响型砂质量的波动。
建议在混砂机出砂口处对型砂质量进行检测,找出出砂口型砂的参数和旧砂再生处的参数的相关关系,从而找出再生系统的型砂控制指标。
4.2混砂质量的好坏直接影响砂型的质量,但传统的检测方法使检测的结果在24小时后才能作出,使得无法对生产的质量作出实时监控。
对砂型的实时强度进行检测,这可以通过试样烘干的方法快速检测或检测砂型表面硬度值以寻找这些参数同砂型终强度的相关关系作出分析,从而找出在线监控的指标参数及其范围。
4.3不同厂家要结合自身的实际情况对长期定期搜集的数据进行控制图、趋势图、波动幅度和铸件质量进行相关性等分析,找出影响铸件质量的最佳控制因子及其公差,只有这样才能找出型砂的最佳控制指标以指导实际生产。
5 结束语在砂型铸造中,型砂参数的控制非常关键。
随着中国铸造业的发展,对型砂的研究将越来越科学和充分。
现代铸造的发展,要求业界对技术研究上要精益求精,管理上不断创新,只有这样,中国的铸造业才能尽快的从铸造大国成长为铸造强国。