非晶硅锗薄膜电池生产工艺流程简介
薄膜电池工艺流程
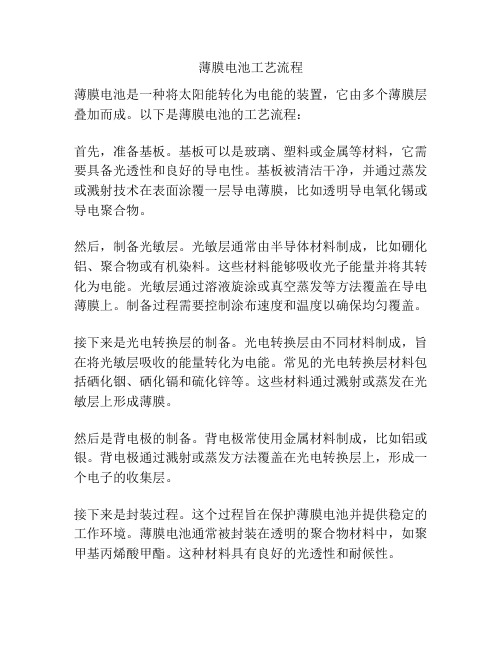
薄膜电池工艺流程薄膜电池是一种将太阳能转化为电能的装置,它由多个薄膜层叠加而成。
以下是薄膜电池的工艺流程:首先,准备基板。
基板可以是玻璃、塑料或金属等材料,它需要具备光透性和良好的导电性。
基板被清洁干净,并通过蒸发或溅射技术在表面涂覆一层导电薄膜,比如透明导电氧化锡或导电聚合物。
然后,制备光敏层。
光敏层通常由半导体材料制成,比如硼化铝、聚合物或有机染料。
这些材料能够吸收光子能量并将其转化为电能。
光敏层通过溶液旋涂或真空蒸发等方法覆盖在导电薄膜上。
制备过程需要控制涂布速度和温度以确保均匀覆盖。
接下来是光电转换层的制备。
光电转换层由不同材料制成,旨在将光敏层吸收的能量转化为电能。
常见的光电转换层材料包括硒化铟、硒化镉和硫化锌等。
这些材料通过溅射或蒸发在光敏层上形成薄膜。
然后是背电极的制备。
背电极常使用金属材料制成,比如铝或银。
背电极通过溅射或蒸发方法覆盖在光电转换层上,形成一个电子的收集层。
接下来是封装过程。
这个过程旨在保护薄膜电池并提供稳定的工作环境。
薄膜电池通常被封装在透明的聚合物材料中,如聚甲基丙烯酸甲酯。
这种材料具有良好的光透性和耐候性。
最后,进行测试和质检。
每个制造的薄膜电池都需要经过一系列的测试和质量控制来确保其性能稳定和可靠。
常见的测试项目包括光电转换效率、开路电压、短路电流和稳定性等。
以上是薄膜电池的大致工艺流程。
随着技术的不断发展,薄膜电池制造工艺也在不断改进。
希望通过不断创新和优化,薄膜电池能够更加高效、环保地转化太阳能。
薄膜电池工艺
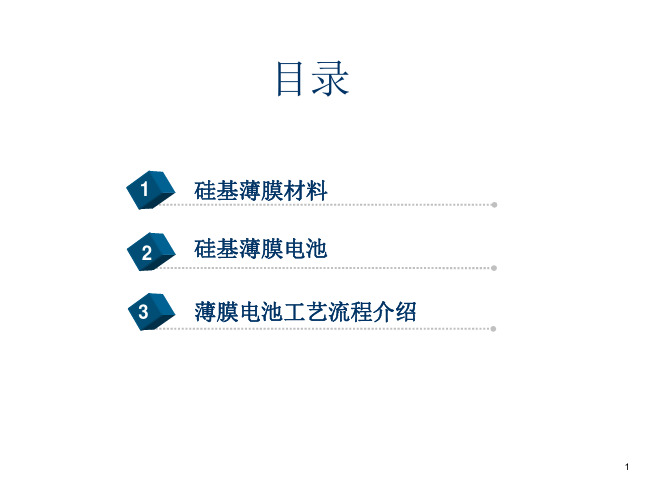
单晶\多晶\微晶\纳晶\非晶
非晶硅\微晶硅\晶体硅
硅基薄膜电池
硅基薄膜电池
玻璃衬底 a-Si单结电池 a-Si/a-Si双结电池 a-Si/u-Si双结电池 a-Si/a-SiGe双结电池 a-Si/a-SiGe/u-Si三结电池 Poly-Si薄膜电池(CSG)
柔性衬底-不锈钢、聚酰亚胺 a-Si/a-Si双结电池 a-Si/a-SiGe双结电池 a-Si/a-SiGe/u-Si三结电池 a-Si/a-SiGe/a-SiGe三结电池
Busline
电池封装
1、薄膜电池组件与边框的粘接和密封 2、薄膜电池与玻璃或背板的粘接和密封 3、接线盒的粘接和灌封
真空层压及滚压封装
层压工艺
EVA:乙烯-醋酸乙烯共聚物膜 是太阳电池封装中应用最广泛的 一种热熔胶,真空层压工艺是针对EVA的特性来设计的, 封 装 材 料 EVA经过一定条件热压发生熔融粘接与交联固化,并变成高 透光材料。 PVB:聚乙烯醇缩丁醛树脂膜是一种标准的层压玻璃用的安全材 料,优点是用于玻璃面的屋顶和建筑一体化的幕墙时能满 足建筑规范的要求。
ZnO:Al (AZO,100nm) 532nm n (30nm) i (200nm) p (20nm) 1064nm SnO2:F (TCO,350nm) Glass substrate (3.2mm) Front electrode a-Si
长波长,利用较 大热量使物质被 气化而去除。
单节a-Si薄膜太阳能电池膜层示意
MOCVD沉积ZnO:B透明导电膜
1、温度均匀性;2、气流均匀性
LPCVD ZnO:B for a-Si:H cell(Oerlikon)
ZnO:B for Tandem cell with plasma etching(Oerlikon)
非晶硅太阳电池的原理
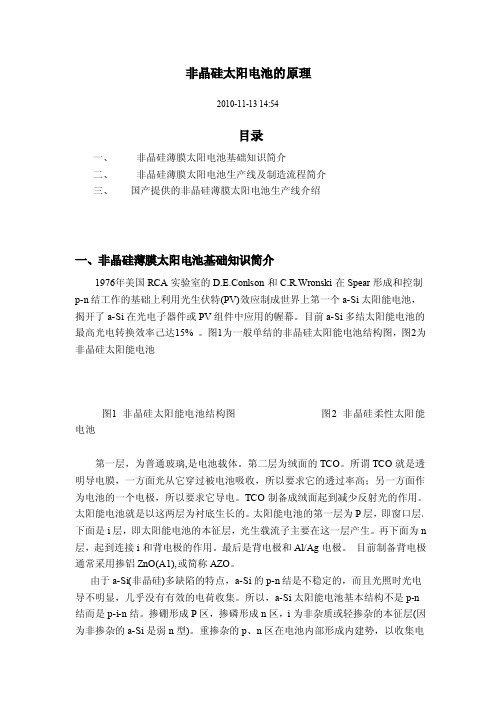
非晶硅太阳电池的原理2010-11-1314:54目录一、非晶硅薄膜太阳电池基础知识简介二、非晶硅薄膜太阳电池生产线及制造流程简介三、国产提供的非晶硅薄膜太阳电池生产线介绍一、非晶硅薄膜太阳电池基础知识简介1976年美国RCA实验室的D.E.Conlson和C.R.Wronski在Spear形成和控制p-n结工作的基础上利用光生伏特(PV)效应制成世界上第一个a-Si太阳能电池,揭开了a-Si在光电子器件或PV组件中应用的幄幕。
目前a-Si多结太阳能电池的最高光电转换效率己达15%。
图1为一般单结的非晶硅太阳能电池结构图,图2为非晶硅太阳能电池图1非晶硅太阳能电池结构图图2非晶硅柔性太阳能电池第一层,为普通玻璃,是电池载体。
第二层为绒面的TCO。
所谓TCO就是透明导电膜,一方面光从它穿过被电池吸收,所以要求它的透过率高;另一方面作为电池的一个电极,所以要求它导电。
TCO制备成绒面起到减少反射光的作用。
太阳能电池就是以这两层为衬底生长的。
太阳能电池的第一层为P层,即窗口层。
下面是i层,即太阳能电池的本征层,光生载流子主要在这一层产生。
再下面为n 层,起到连接i和背电极的作用。
最后是背电极和Al/Ag电极。
目前制备背电极通常采用掺铝ZnO(A1),或简称AZO。
由于a-Si(非晶硅)多缺陷的特点,a-Si的p-n结是不稳定的,而且光照时光电导不明显,几乎没有有效的电荷收集。
所以,a-Si太阳能电池基本结构不是p-n 结而是p-i-n结。
掺硼形成P区,掺磷形成n区,i为非杂质或轻掺杂的本征层(因为非掺杂的a-Si是弱n型)。
重掺杂的p、n区在电池内部形成内建势,以收集电荷。
同时两者可与导电电极形成欧姆接触,为外部提供电功率。
i区是光敏区,光电导/暗电导比在105~106,此区中光生电子、空穴是光伏电力的源泉。
非晶体硅结构的长程无序破坏了晶体硅电子跃迁的动量守恒选择定则,相当于使之从间接带隙材料变成了直接带隙材料。
第九章---非晶硅薄膜
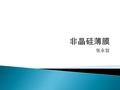
第一个非晶硅太阳电池被研制出(效率:2.4%);随后其效率
增长到4%。
1980年非晶硅太阳电池实现商品化。日本三洋电气公司利
用非晶硅太阳电池率先制成计算器电源,并实现工业化生
产。
当前,非晶硅薄膜电池已发展成为实用廉价的太阳电池品 种之一,具有相当的工业规模。目前世界非晶硅太阳电池 生产600MW/年以上,效率7-8%,应用范围从多种电子消费 产品如手表、计算器、玩具到户用电源、光伏电站。
构等都有重要影响。
氢在非晶硅中会形成Si—H键,以SiH、SiH2、SiH3及 (SiH2)n等集团。这些集团可用红外光谱去检测:
氢的态密度:指单位能量中不同氢键的数目。
氢在非晶硅中的正面作用:补偿悬挂键和改变带隙
改变带隙:随着非晶硅中氢含量的增加,其带隙宽度从1.5eV
开始逐渐增宽致1.7eV,其悬挂键缺陷密度为1015-1016cm-3.
氢在非晶硅中的负面作用,氢在非晶硅中生成光致亚稳缺陷,
形成S-W效应。
S-W效应:在长期光照下,其光电导和暗电导同时下降,然后 才保持稳定,其中暗电导可以下降几个数量级,从而导致非晶 硅太阳能电池的光电转换效率降低,经150-200度短时间热处 理,其性能可恢复。
制备条件:辉光放电制备的
非晶硅薄膜,衬底温度为
由于辉光放电,因此会再两电极间形成辉光区。当垫子从印记发射时, 能量很小,只有1eV左右,不能和气体分子作用,在电场的作用下, 垫子逐渐具有了更高的能量,可以和气体分子作用,使气体分子激发 发光,形成辉光。
辉光放电过程中,等离子体的温度,电子的温度和浓度是重
要的因素,其中电子的温度最为关键。虽然反应气体的温度
硅太阳能电池制造工艺流程

硅太阳能电池制造工艺流程一、非晶硅薄膜太阳电池基础知识简介1976年美国RCA实验室的D.E.Conlson和C.R.Wronski在Spear形成和控制p-n结工作的基础上利用光生伏特(PV)效应制成世界上第一个a-Si太阳能电池,揭开了a-Si在光电子器件或PV组件中应用的幄幕。
目前a-Si多结太阳能电池的最高光电转换效率己达15% 。
图1为一般单结的非晶硅太阳能电池结构图,图2为非晶硅太阳能电池图1 非晶硅太阳能电池结构图图2 非晶硅柔性太阳能电池第一层,为普通玻璃,是电池载体。
第二层为绒面的TCO。
所谓TCO就是透明导电膜,一方面光从它穿过被电池吸收,所以要求它的透过率高;另一方面作为电池的一个电极,所以要求它导电。
TCO制备成绒面起到减少反射光的作用。
太阳能电池就是以这两层为衬底生长的。
太阳能电池的第一层为P层,即窗口层。
下面是i层,即太阳能电池的本征层,光生载流子主要在这一层产生。
再下面为n层,起到连接i和背电极的作用。
最后是背电极和Al/Ag电极。
目前制备背电极通常采用掺铝ZnO(A1),或简称AZO。
由于a-Si(非晶硅)多缺陷的特点,a-Si的p-n结是不稳定的,而且光照时光电导不明显,几乎没有有效的电荷收集。
所以,a-Si太阳能电池基本结构不是p-n结而是p-i-n结。
掺硼形成P区,掺磷形成n区,i为非杂质或轻掺杂的本征层(因为非掺杂的a-Si是弱n型)。
重掺杂的p、n区在电池内部形成内建势,以收集电荷。
同时两者可与导电电极形成欧姆接触,为外部提供电功率。
i区是光敏区,光电导/暗电导比在105~106,此区中光生电子、空穴是光伏电力的源泉。
非晶体硅结构的长程无序破坏了晶体硅电子跃迁的动量守恒选择定则,相当于使之从间接带隙材料变成了直接带隙材料。
它对光子的吸收系数很高,对敏感光谱域的吸收系数在1014cm-1以上,通常0.5µm左右厚度的a-Si就可以将敏感谱域的光吸收殆尽。
非晶硅薄膜研究进展

非晶硅薄膜研究进展非晶硅薄膜及其制备方法研究进展摘要:氢化非晶硅(a-Si:H)薄膜在薄膜太阳能电池、薄膜晶体管、辐射探测和液晶显示等领域有着重要的应用,因而在世界范围内得到了广泛的关注和大量的研究。
本文主要介绍了a-Si:H薄膜的主要掺杂类型和a-Si:H薄膜的主要制备方法。
关键词:非晶硅薄膜;掺杂;制备方法;研究进展Research Progress on a-Si:H Thin Films and Related PreparationMethodAbstract:Hydrogenated amorphous silicon (a-Si:H) thin film has attracted considerable attention and been a subject of extensive studies worldwide on account of its important applications such as thin film solar cells, thin film transistors, radiation detectors, and liquid crystal displays based on its good electrical and optical properties. In this paper, the progress research on a-Si:H thin films and related preparation method are reviewed.Key words: a-Si:H thin films; doped; preparation method; research progress1 引言氢化非晶硅(a-Si:H)是硅和氢的一种合金,网络中Si-H键角和键长的各种分布打乱了晶体硅晶格的长程有序性,从而使非晶硅具有独特的光电性质。
非晶硅薄膜太阳能电池产品技术规格书
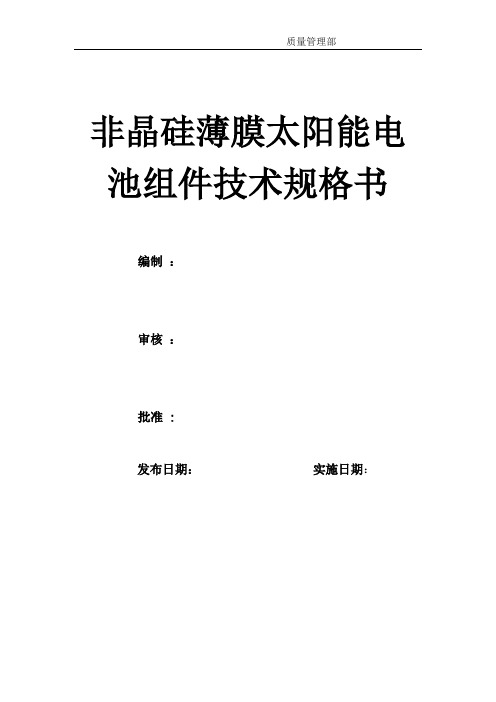
质量管理部非晶硅薄膜太阳能电池组件技术规格书编制:审核:批准:发布日期:实施日期:1 适用范围1.1 本技术标准适用于非晶硅单节薄膜太阳电池组件系列产品1.2 型号: -80,-85,-90,-95,-100,-105。
1.3 结构:a-Si 单节 Thin Film PV Module2 产品结构2.1 产品外形2.1.1 长度:1300mm ± 1 mm2.1.2 宽度:1100mm ± 1 mm2.1.3 厚度:7.9mm ± 0.8 mm电池组件的正面、侧面和背面如图 2-1 所示:正面侧面背面图2-1 电池的正面、侧面和背面示意图2.2 产品组成产品由TCO 导电玻璃、P-I-N 非晶硅薄膜、AZO 薄膜、Al 薄膜、NiV薄膜、引流條、汇流条、绝缘膜、PVB、背板玻璃、接线盒和导线等组成。
2.3 名词解释2.3.1 引流条:即 Side Bus,材料为铝带,采用超声波焊接在背电极膜层上,其作用是将组件的正负极电流顺利引出。
2.3.2 汇流条:即 Cross Bus,材料为铜锡复合带,采用绝缘胶将其粘附在背电极膜层上,其作用是将引流条上的电流汇到接线盒。
2.3.3 接线盒:即 Junction Box,其作用是引出组件的正负极,同时起到防潮、防尘和密封功能。
3 产品规格3.1 产品型号3.1.1 -80,-85,-90,-95,-100,-105 系列3.1.2 分类等级:80W、85W、90W、95W 、 100W和105W 六个等级。
情况如下:80W:77.5~82.5W 85W:82.6~87.5W90W:87.6~92.5W 95W:92.6~97.5W100W:97.6~102.5W 105W:102.6~107.5W3.2 产品属性表 3-1产品属性3.3 电性规格:表3-2电池电性规格3.4 温度系数规格表3-3电池温度系数规格3.5 产品工作范围4 电池构造4.1 子电池构造4.1.1 子电池宽度:8.04mm(正极宽度:6.5mm;负极宽度:8.22mm)4.1.2 子电池数量:133 个4.1.3 清边宽度:12mm4.1.4 汇流条宽度:4mm4.2 引流条与汇流条的相对位置4.2.1 背板玻璃孔洞中心位置距玻璃短边为175mm,距玻璃长边为550mm。
单晶硅、多晶硅、非晶硅、薄膜太阳能电池的工作原理及区别1讲课讲稿
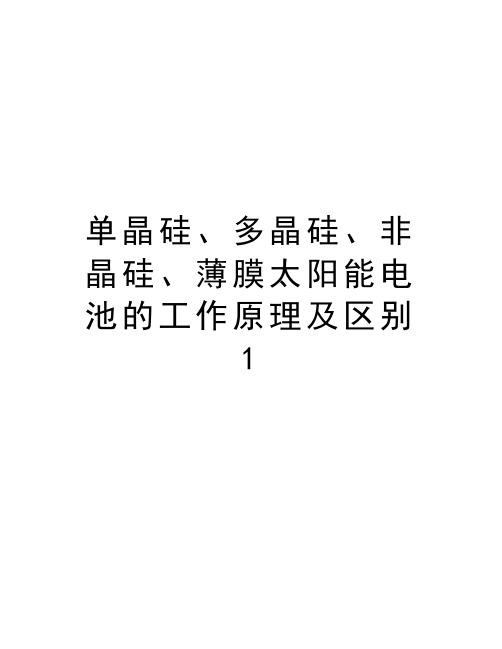
单晶硅、多晶硅、非晶硅、薄膜太阳能电池的工作原理及区别1单晶硅、多晶硅、非晶硅、薄膜太阳能电池的工作原理及区别硅太阳能电池的外形及基本结构如图1。
其中基本材料为P型单晶硅,厚度为0.3—0.5mm左右。
上表面为N+型区,构成一个PN+结。
顶区表面有栅状金属电极,硅片背面为金属底电极。
上下电极分别与N+区和P区形成欧姆接触,整个上表面还均匀覆盖着减反射膜。
当入发射光照在电池表面时,光子穿过减反射膜进入硅中,能量大于硅禁带宽度的光子在N+区,PN+结空间电荷区和P区中激发出光生电子——空穴对。
各区中的光生载流子如果在复合前能越过耗尽区,就对发光电压作出贡献。
光生电子留于N+区,光生空穴留于P区,在PN+结的两侧形成正负电荷的积累,产生光生电压,此为光生伏打效应。
当光伏电池两端接一负载后,光电池就从P区经负载流至N+区,负载中就有功率输出。
太阳能电池各区对不同波长光的敏感型是不同的。
靠近顶区湿产生阳光电流对短波长的紫光(或紫外光)敏感,约占总光源电流的5-10%(随N+区厚度而变),PN+结空间电荷的光生电流对可见光敏感,约占5 %左右。
电池基体域产生的光电流对红外光敏感,占80-90%,是光生电流的主要组成部分。
2.单晶硅太阳能电池单晶硅太阳能电池是当前开发得最快的一种太阳能电池,它的构成和生产工艺已定型,产品已广泛用于宇宙空间和地面设施。
这种太阳能电池以高纯的单晶硅棒为原料,纯度要求99.999%。
为了降低生产成本,现在地面应用的太阳能电池等采用太阳能级的单晶硅棒,材料性能指标有所放宽。
有的也可使用半导体器件加工的头尾料和废次单晶硅材料,经过复拉制成太阳能电池专用的单晶硅棒。
将单晶硅棒切成片,一般片厚约0.3毫米。
硅片经过成形、抛磨、清洗等工序,制成待加工的原料硅片。
加工太阳能电池片,首先要在硅片上掺杂和扩散,一般掺杂物为微量的硼、磷、锑等。
扩散是在石英管制成的高温扩散炉中进行。
这样就在硅片上形成PN结。
- 1、下载文档前请自行甄别文档内容的完整性,平台不提供额外的编辑、内容补充、找答案等附加服务。
- 2、"仅部分预览"的文档,不可在线预览部分如存在完整性等问题,可反馈申请退款(可完整预览的文档不适用该条件!)。
- 3、如文档侵犯您的权益,请联系客服反馈,我们会尽快为您处理(人工客服工作时间:9:00-18:30)。
非晶硅锗薄膜电池生产工艺流程简介
1.玻璃磨边与清洗一
所用的原材料为TCO玻璃,一般薄膜电池所用的TCO玻璃是FTO(SnO:F),AZO(ZnO:Al),目前,AZO是研发的热点,但是应用到产业化程度还不够,绝大多数薄膜电池厂商仍然采用成熟的FTO玻璃。
目前,FTO玻璃制造技术主要被日本的NSG与AGC 两家公司垄断。
国内能够制造TCO玻璃的有信义、南玻等少数几家公司,但产品性价比目前没有优势。
TCO玻璃到厂后,需要进行磨边处理。
将玻璃的四边有棱的地方磨光滑,四角进行倒角,这样,可以消除玻璃边缘及四角的微裂纹,也便于后道工序手动搬运操作,安全。
磨边机就是普通玻璃加工厂所使用的。
玻璃磨边后,TCO玻璃表面要进行清洗,及清洗一。
用液晶玻璃清洗机即可。
主要清洗步骤涉及喷淋,碱液清洗,去离子风刀吹干。
2.激光划线一与玻璃清洗二
TCO玻璃清洗干燥后,需要进行激光划线一。
激光划线一的目的是将TCO玻璃的导电膜划成一定数目的小块区域,各区域称为“cell”,每个cell彼此绝缘,这样,每个cell以后做为一个独立的发电单元,串联起来,不会产生很大的电流。
划断FTO膜现在通用的是用1064nm的红激光。
主流的激光器大部分采用Rofin的,国内购买激光器后,加工成激光划线机,目前,国内激光设备做的份额比较的的有深圳大族激光,武汉三工光电,苏州德龙激光等。
TCO玻璃通过夹子夹住边缘,在直线电机的带动下,做直线往复运动,电池板上方或底部,激光器发出的红激光经过分光,由激光头聚焦在电池板上,通过一定的焦距(DOF),电流,功率的设定,将TCO导电膜划断。
划线速度一般是1m/S。
激光划线后,会产生一些FTO膜残渣,由设备本身自带的排风可以抽走大部分,为了确保进入关键工序CVD的玻璃表面干净,需要进行玻璃二次清洗,即清洗二。
基本清洗步骤同清洗一,这里不用加碱性的清洗剂,可以进行超声波清洗。
3.CVD
CVD是整个生产过程的核心,所谓CVD,是化学气相沉积的意思,这里使用的是PECVD,即等离子增强型CVD。
优点是可以低温镀膜,玻璃的热损伤小。
成膜过程是首先沉积掺碳掺硼的非晶P层,做为窗口层,要求带隙要宽。
所用的气体为:混硅烷的TMB,甲烷,硅烷,氢气,氩气。
之后,沉积非晶I层,I层做为光的吸收层,电池能够吸收多少光,产生多少电,关键在于这一层。
一般,非晶I层H2与硅烷的用量比是4.5:1左右。
所用的气体只有氢气与硅烷。
第三层是非晶N层,N层材料主要通过掺磷或得。
所用的气体是混氢气的磷烷,硅烷和氢气。
以上是第一结PIN结构,也是传统的非晶硅薄膜电池结构。
具体过程由于涉及带隙调节,结构匹配等因素,并非如此简单的镀膜过程。
如P层,会有重掺P层与轻掺P层,N 层会有重掺微晶N层与轻掺非晶N层。
非晶硅PIN结构对于太阳光的吸收波段只是300-800nm,800nm以后波段的太阳光无法利用。
所以,在非晶硅上继续沉积非晶硅锗薄膜,因为非晶硅锗的带隙较窄,可以延长太阳光谱的吸收波段,更多的利用太阳光,这样,产生的电量更高。
具体镀膜过程同非晶硅PIN,不同的是I层掺进了混氢气的锗烷。
4.激光划线二
CVD镀膜结束后,进行激光划线二工艺,设备与激光划线一相同,不同的是激光器是532nm的绿激光,因为硅膜对这一波长的光有吸收,可以产生热量将硅膜烧断。
划线以激光划线一的线为参考,位移一定距离,将硅膜烧断,由于TCO膜能够透过532nm的绿激光,所以TCO膜损伤小(硅膜烧断时,有些会与TCO膜表面的氧起反应,生成氧化硅,使接触电阻很高,对TCO膜有一定损伤)。
5.PVD与激光划线三
接下来需要镀背电极。
TCO膜做为前电极,背电极需要用PVD的方法制成。
PVD,中文的意思是物理气相沉积。
先在硅膜上镀一层AZO,然后再镀一层铝膜。
主要通过磁控溅射的方式,在设备的腔室中通入氩气,直流电离生成氩离子,轰击阴极靶材,靶材就是AZO 和铝靶。
轰击下来的AZO和铝附着在玻璃基板的硅膜上,形成一定厚度。
PVD镀完膜后,需要再用激光划断。
用的设备同激光划线二,也是532nm的绿激光,与激光划线二的线再错开一定距离,使三条线平行排列。
将硅膜烧断后,热量向上将金属膜爆开,有排风设施将划断的膜残渣大部分抽走。
经过激光划线三,每个cell在电路上串联了起来,电压相对高,电流相对低。
6.激光扫边
由于镀膜过程是在玻璃表面全镀上,所以玻璃边缘也全有膜存在,受光照时,玻璃边缘会有电流通过,不便于人搬运,有危险。
所以需要将边缘的膜去掉。
一般,将玻璃边缘的膜去掉有两种机械的方法,一是用砂轮磨,将金属膜及硅膜磨掉,二是喷砂的方法,对玻璃边缘喷细砂,用砂子将边缘的膜打掉。
还有一种方法就是激光扫边。
用1064nm的激光,加大功率,将边缘的硅膜及金属膜打掉。
缺点是产生大量膜残留物,不便清理。
扫边区域宽度在8-12nm即可,防止有边缘漏电。
7.退火
激光扫边后,将电池板放进退火炉进行退火处理。
PECVD镀完的膜中含有大量非稳态的氢,需要进行退火处理,变成稳态的。
退火一般在190度的高温室中静置一小时左右即可。
8.反压修补、初测与芯片清洗
电池板退火后,进行反压修补。
用密排金属探针(pop pin)接触金属膜表面,加反向电压,这样,cell与cell之间缝隙中的金属残留物被烧掉,防止了短路情况的发生。
反向修补后,进行太阳光模拟器的初测,看看电池板的效率及峰值功率。
检验前面工艺过程是否出现问题,如果电池板功率很低,直接报废掉,以免浪费后续封装工段的原材料。
初测结束后,为了确保电池板表面的清洁,需要进行芯片清洗,设备及工艺过程基本与清洗二类似。
8.超声波焊接
电池板清洗后,流入焊接工序,所用的焊接方式是超声波焊接,焊接所用的焊带是铝带,与铝膜易焊。
焊接时,用一个表面凹凸不平的金属滚轮压住焊带,通过超声波传导能量,将焊带焊在电池板长边两侧的边缘上,做为引出电流的汇流条。
9.EV A、背板玻璃铺设
焊接后,将边缘多出的铝带成直角像电池板内侧弯折,在电池板上铺好EV A,在EV A 长边边缘两侧用剪子绞两个口,将汇流条从口引上来,压在EV A上面。
将清洗过的背板玻璃盖在EV A及汇流条上面,将汇流条的前端从背板玻璃上的小孔处引出来。
检查一下前板玻璃与背板玻璃的对位情况,放置一边。
这里,EV A是封装材料,轻薄,可以防水,具有粘性,可以通过“交联反应”将前后两块玻璃粘在一起,增加电池板强度与安全性。
背板玻璃是普通的白玻璃,有加工的小孔,引线用。
背板玻璃可以是普通的浮法玻璃,
也可以是钢化玻璃。
10.层压
铺设后的前板与背板玻璃需要经过层压,将EV A树脂模融化,产生粘性,通过交联反应,将前板与背板玻璃粘住,抽真空,将熔融的EV A中的气泡抽走,防止以后气泡变大,水汽进入。
一般,加热温度120-160度即可。
11.接线盒安装、终测
层压后,需要安装接线盒。
接线盒安装部分需要用密封胶和灌封胶保护,增加电池板的耐候性。
首先在无盖的接线盒边缘涂上一圈密封胶,粘在背板玻璃孔的位置,将铝带与接线盒的电极头焊上,多余的铝带剪掉。
测试电性能后,电池板贴上标签,标签上标有防护等级,电性能参数,通过的各项产品认证标识(TUV,UL,CE,MCS)等。
之后,在接线盒内部灌入灌封胶,一般采用A、B双组分胶,增加固化时间。
同时,在电池板组件边缘四周抹上一圈密封剂,防止水汽进入。
扣上接线盒的盖子,组件表面擦拭干净,用塑封膜包好接线盒的引出电缆,将组件装箱。