10吨发酵罐物料衡算
酒精发酵中的物料衡算
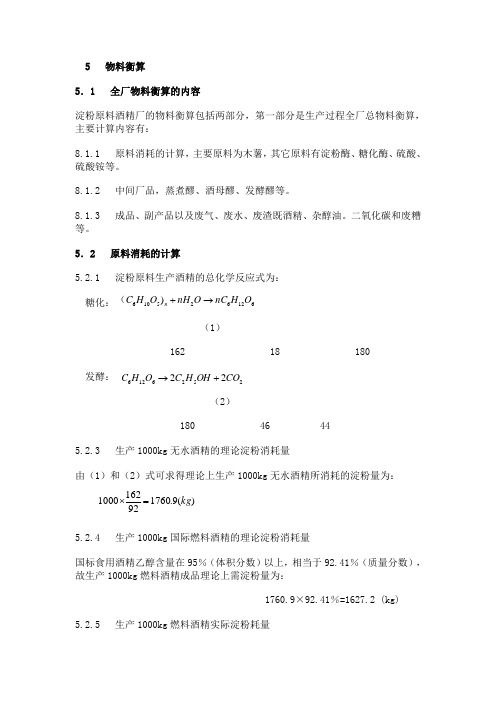
5 物料衡算5.1 全厂物料衡算的内容淀粉原料酒精厂的物料衡算包括两部分,第一部分是生产过程全厂总物料衡算,主要计算内容有:8.1.1 原料消耗的计算,主要原料为木薯,其它原料有淀粉酶、糖化酶、硫酸、硫酸铵等。
8.1.2 中间厂品,蒸煮醪、酒母醪、发酵醪等。
8.1.3 成品、副产品以及废气、废水、废渣既酒精、杂醇油。
二氧化碳和废糟等。
5.2 原料消耗的计算5.2.1 淀粉原料生产酒精的总化学反应式为:糖化:(1)162 18 180 发酵: (2)180 46 44 5.2.3 生产1000kg 无水酒精的理论淀粉消耗量由(1)和(2)式可求得理论上生产1000kg 无水酒精所消耗的淀粉量为:5.2.4 生产1000kg 国际燃料酒精的理论淀粉消耗量国标食用酒精乙醇含量在95%(体积分数)以上,相当于92.41%(质量分数),故生产1000kg 燃料酒精成品理论上需淀粉量为:1760.9×92.41%=1627.2 (kg) 5.2.5 生产1000kg 燃料酒精实际淀粉耗量612625106)O H nC O nH O H C n →+(252612622CO OH H C O H C +→)(9.1760921621000kg =⨯实际上,整个年产过程经历原料处理、发酵及蒸馏等工序,要经过复杂的物理化学和生物化学反应,产品得率必然低于理论产率。
假定发醇阶段系统设有酒精捕集器,则淀粉总损失率为8.55%,故生产1000kg 用酒精需淀粉量为:5.2.6 酒精生产给各过程各阶段淀粉损失如表所示5.2.7 这个原料消耗水平相当于淀粉出酒率为91.45%,这达到了我国现阶段木薯原料生产酒精的先进出酒率水平。
5.2.8 生产1000kg 燃料酒精木薯原料消耗量据基础数据给出,木薯原料含淀粉70%,故1吨酒精耗薯干量为:5.2.9 α-淀粉酶消耗量应用酶活力为2000u/g 的α-淀粉酶使淀粉液化,促进糊化,可减少蒸汽消耗。
酒精生产总物料衡算

一、10000t/a玉米淀粉燃料酒精厂物料衡算项目、工艺流程及基础数据1、全厂物料衡算内容:原料消耗计算、中间产物量计算、成品及副产品量计算。
2、生产工艺流程图:生产工艺采用改良湿法、双酶糖化、连续发酵和半直接式三塔蒸馏流程,如图空气酶母种原料(玉米)耐高温空压机斜面试管 a-淀粉酶预处理辅料(酸、碱)过滤器摇瓶培养脱胚制浆玉米油车间无菌空气小酒母罐连续蒸煮器大酒母罐蒸煮醪酒母醪糖化锅糖化酶糖化醪发酵醪 CO2成熟发酵醪蒸馏DDGS车间分子筛脱水杂醇油燃料酒精图改良湿法双酶糖化连续发酵燃料酒精流程示意图3、工艺技术指标及基础数据(1)生产规模:10000t/a燃料酒精。
(2)生产方法:改良湿法、、双酶糖化、连续发酵和塔蒸馏。
(3)生产天数:300d/a(4)燃料酒精日产量:34t(5)燃料酒精年产量:10200t(6)产品质量:国际燃料酒精,乙醇含量99.5%以上(V)。
(7)主原料:国内酒精企业玉米粉(脱胚去皮)淀粉含量68%,利用率为80%-92%,水分14%。
(8)酶用量:耐高温α-淀粉酶用量8u/g 原料,糖化酶用量为100u/g 原料, 酒母糖化醪用糖化酶量200u/g 原料。
(9)硫酸铵用量:8kg/t 酒精(提供氮源)。
(10)硫酸用量:5.5kg/t 酒精(调节pH)。
二、10000t/a 玉米淀粉燃料酒精厂全厂总物料衡算 1、原料消耗计算现以生产99.5%(V )成品酒精1000kg 作为计算的基准。
(1)淀粉原料生产乙醇的总化学反应式为:6105n 26126252(C H O )+nH O nC H O 2C H OH+2CO →→(4-2-1)糖化阶段:6105n 26126(C H O )+nH O nC H O → (4-2-2)162 18 180 发酵阶段:6126252C H O 2C H OH+2CO → (4-2-3)180 2×46 2×44(2)每生产1000kg 燃料酒精的理论淀粉消耗量:由式(4-2-2)和(4-2-3)可求得理论上生产1000kg 燃料酒精(99.5%(V)的燃料酒精相当于99.18%(W))所消耗淀粉量为:(3)生产1000kg 燃料酒精实际淀粉耗量:实际上,整个年产过程经历的各工序,如原料处理、发酵及蒸馏等,要经过复杂的物理化学和生物化学反应,所以产品得率必然低于理论产率。
年产6万吨味精厂谷氨酸机械搅拌通风发酵罐设计
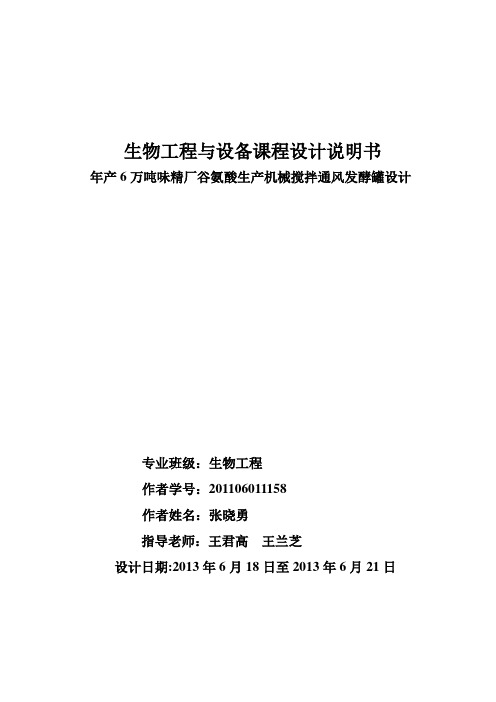
生物工程与设备课程设计说明书年产6万吨味精厂谷氨酸生产机械搅拌通风发酵罐设计专业班级:生物工程作者学号:201106011158作者姓名:张晓勇指导老师:王君高王兰芝设计日期:2013年6月18日至2013年6月21日山东轻工业学院课程设计任务书食品与生物工程学院11 级生物工程专业学生张晓勇题目:年产6万吨味精厂谷氨酸生产机械搅拌通风发酵罐设计一、主要内容:1、物料恒算,计算发酵罐总容积;2、求发酵罐个数,取单罐公称容积200m3;3、公称容积200m3发酵罐设计(罐体尺寸、壁厚、搅拌器类型选择及尺寸设计、搅拌功率计算、搅拌轴直径计算、冷却面积计算与设计)二、基本要求1、编写计算设计说明书(有前言、设计参数、物料恒算、发酵罐工艺设计,设计体会)2、用CAD绘出发酵罐结构图。
三、设计参数1、糖酸转化率61%2、发酵产酸水平11%3、发酵周期32小时4、发酵罐充满系数为0.75、味精分子式187.13(C5H8NO4Na).H2O6、谷氨酸分子式147.13(C5H9NO4)7、谷氨酸密度取1.553g/cm3 8、残还原糖0.8%,干菌体1.7%9、谷氨酸提取率97.5%。
10、谷氨酸生产味精精制率为125%11、空罐灭菌压力0.25MPa 12、年工作日安330天计算四、主要参考资料〔1〕郑裕国《生物工程设备》化学工业出版社2007〔2〕高孔荣《发酵设备》轻工业出版社1991.10〔3〕梁世中《生物工程设备》轻工业出版社2002.2〔4〕化工设备设计全书编辑委员会编《搅拌设备设计》上海科学技术出版社1985〔5〕吴思方《发酵工厂工艺设计概论》中国轻工业出版社2007(6)化工工艺设计手册(7)于令信《味精工业手册》(8)张克旭《氨基酸发酵工艺学》轻工业出版社完成期限:自2013年6月18 日至2012 年 6 月21日指导教师:王君高王兰芝教研室主任:一、计算设计说明书前言机械搅拌式发酵设备和技术在整个制药、生物产品的开发过程中起着特别重要的作用。
发酵罐-计算

4.K值的计算
K 1 1 1 S 1
1
2
1 1 1 0.0035 1 2700 1450 188 16750
= 1.931×103 kJ/(M2 〃h〃℃)
10
5.冷却ห้องสมุดไป่ตู้积
Q A K t m
5.0 2 1 05 2 3.8 5( M 1931 1 0.9
)
P0 、Pg:不通气、通气时的搅拌功率,单位均为kW d,搅拌叶轮直径,m N,转/分
Q,工作状况下的通气量,m3 /min,
22
Q 的换算: 只知道标准状态通气量时
Q与标准状况下(温度为273K、压力为101325Pa)的通 气量 Q0 之间的换算关系,可按气体状态方程:
273 t Q Q0 273
12
1.单层搅拌器、不通气条件下输入搅拌液体的功率计算
搅拌器所输入搅拌液体的功率取决于下列因素: 搅拌罐直径 D 搅拌器直径d 前三项都可用d 来表示 液体高度 HL 搅拌转速 N 液体粘度 μ 液体密度 ρ 搅拌器形式、有无档板等
P=F(N,d, ρ, μ )
13
8
解:
1.总的热量 Q=Q1+Q2-Q3 =4.4×105+7.2×104-1×104 =5.02×105(kJ/h) 2.冷却水耗量
Q W C p (t 2 t1 )
5.02105 4.186 (25 16)
=1.33×104 (kg/h)
9
3.对数平均温度差
t m (t F t1 ) (t F t 2 ) 10.9( oC ) t F t1 2.303lg t F t2
10万吨11°淡色啤酒发酵罐的设计

10万吨11°淡色啤酒发酵罐的设计前言本设计为顺应近几年来啤酒工业飞速发展的需求,在啤酒工艺成熟的基础上,同时体现了啤酒酿造的新工艺,为企业的开源节流提供了新的依据。
设计题目为年产10万吨11度淡色啤酒厂发酵罐设计,此啤酒的酿造方法使用70%的麦芽,30%的大米,经过淋入,糖化,煮熟,过滤器,加热,蒸煮而变成。
蒸煮设备使用圆筒体锥底发酵罐,蒸煮周期就是17天。
本设计内容主要包含物料钢料,热量钢料,冷耗钢料和设备选型的排序及重点设备选型及排序。
糖化方法使用双醪干料糖化法,蒸煮方法使用下面发酵法。
本设计的图纸主要为发酵罐装配图。
本文对啤酒生产线工艺设计中的关键部分―原料的淋入、糖化、麦汁过滤器、煮熟、啤酒过滤器及其设备选型展开了粗略研究。
对蒸煮过程及其设备选型展开了较为详尽的深入探讨。
关键词:啤酒工艺;设备选型;技术经济;发酵;糖化;发酵罐.1第1章绪论1.1设计选题的目的目前,世界上啤酒市场的竞争日益激烈,广大消费者对啤酒品种结构和产品质量的要求也越来越高,相应的新品种也层出不穷。
因而,很有必要将这方面得计书加以科学地总结和分析以推动啤酒产品多样化在广度和深度上的健康发展,随着人们生活水平的提高,饮食消费结构的不断改变,啤酒已进入了千家万户。
但是我国人均啤酒的消费还没有达到世界平均水平。
所以建设新的、大型的啤酒厂,增加产量,就可以满足人们将来物质生活的需求。
所以,设计啤酒厂是有意义有必要的。
另外,此次选题是教研室下达的任务。
是根据教学的实际需求来选定的。
1.2设计工作的意义啤酒含有17种氨基酸,多种维生素及碳水化合物、矿物盐等物质、每升啤酒的热量可达430卡,相当于6-7枚鸡蛋,0.75升牛奶或50克奶油,被世界营养协会组织列为营养食品,素有“液体面包”之誉。
现代科学研究表明,啤酒中所含各种成份、既有较高的营养价值又具良好的药疗效果,啤酒中酒精含量较低,10度黄啤酒含酒精3%左右,非但对胃和肝脏无损害,而且可平缓地促进人体血液循环;维生素b1、b6已能维持心脏正常活动,而烟酸则能扩张血管,故它们对心血管系统有益,可加速新陈代谢。
年产20吨硫酸庆大霉素车间设计计算部分
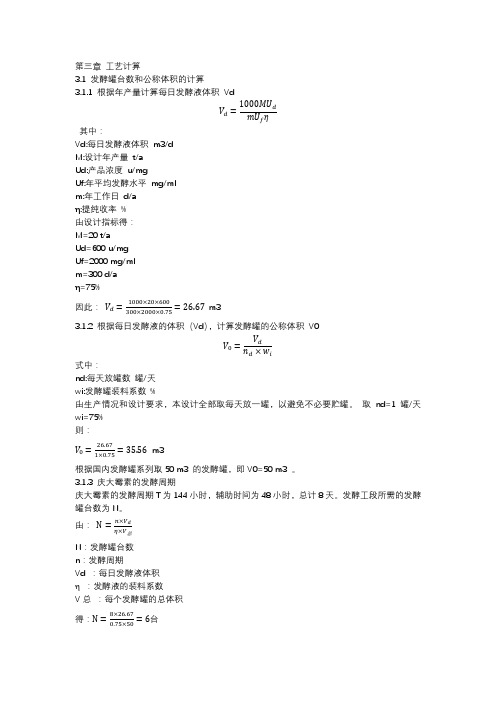
第三章工艺计算3.1 发酵罐台数和公称体积的计算3.1.1 根据年产量计算每日发酵液体积VdV d=1000MU d mU fη其中:Vd:每日发酵液体积m3/dM:设计年产量t/aUd:产品浓度u/mgUf:年平均发酵水平mg/mlm:年工作日d/aη:提纯收率%由设计指标得:M=20 t/aUd=600 u/mgUf=2000 mg/mlm=300 d/aη=75%因此:V d=1000×20×600300×2000×0.75=26.67 m33.1.2 根据每日发酵液的体积(Vd),计算发酵罐的公称体积V0V0=V d n d×w i式中:nd:每天放罐数罐/天wi:发酵罐装料系数%由生产情况和设计要求,本设计全部取每天放一罐,以避免不必要贮罐。
取nd=1 罐/天wi=75%则:V0=26.671×0.75=35.56m3根据国内发酵罐系列取50 m3 的发酵罐,即V0=50 m3 。
3.1.3 庆大霉素的发酵周期庆大霉素的发酵周期T为144小时,辅助时间为48小时,总计8天。
发酵工段所需的发酵罐台数为N。
由:N=n×V dη×V总N:发酵罐台数n:发酵周期Vd :每日发酵液体积:发酵液的装料系数V总:每个发酵罐的总体积得:N=8×26.670.75×50=6台3.2 种子罐的台数与公称体积的计算取发酵罐和种子罐的接种比为15%,液体损失率为15%。
由公式:种子罐体积=发酵罐计量体积×接种比×(1+液体损失率)种子罐的装料系数则: 中罐公称体积= 26.67×0.15×(1+0.15)0.7=6.57 m3发酵时间为24h ,辅助时间24h ,合计2天中罐的台数 N =2×6.570.7×10=2台同理:小罐公称体积=6.57×0.7×0.15×(1+0.15)0.7=1.13m3发酵周期为32小时,16小时辅助时间,合计两天。
发酵罐设计说明书
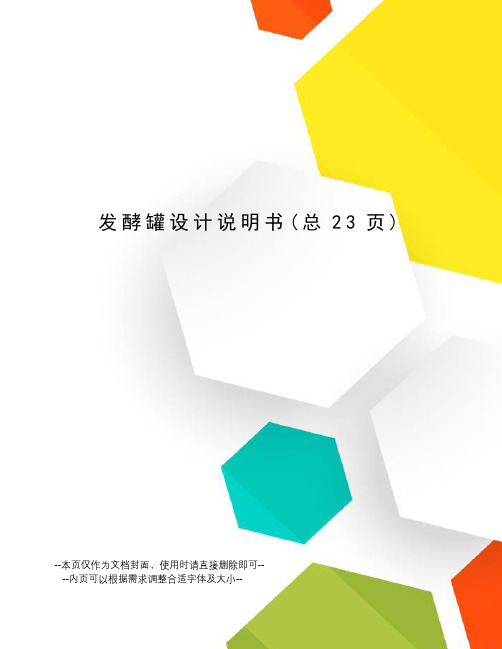
发酵罐设计说明书(总23页)--本页仅作为文档封面,使用时请直接删除即可----内页可以根据需求调整合适字体及大小--目录前言 (1)第一章、概述 (2)、柠檬酸 (2)、柠檬酸的生产工艺 (2)、机械搅拌通风发酵罐 (3)、通用型发酵罐的几何尺寸比例 (3)、罐体 (3)、搅拌器和挡板 (3)、消泡器 (4)、联轴器及轴承 (4)、变速装置 (4)、通气装置 (4)、轴封 (5)、附属设备 (5)第二章、设备的设计计算与选型 (5)、发酵罐的主要尺寸计算 (5)、圆筒体的内径、高度与封头的高度 (5)、圆筒体的壁厚 (7)、封头的壁厚 (7)、搅拌装置设计 (8)、搅拌器 (8)、搅拌轴设计 (8)、电机功率 (10)、冷却装置设计 (10)、冷却方式 (10)、冷却水耗量 (10)、冷却管组数和管径 (12)零部件 (13)人孔和视镜 (13)接管口 (13)、梯子 (15)发酵罐体重 (15)支座的选型 (16)第三章、计算结果的总结 (16)设计总结 (17)附录 (18)符号的总结 (18)参考文献 (20)生物工程设备课程设计任务书一、课程设计题目“1000m3的机械搅拌发酵罐”的设计。
二、课程设计内容1、设备所担负的工艺操作任务和工作性质,工作参数的确定。
2、容积的计算,主要尺寸的确定,传热方式的选择及传热面积的确定。
3、动力消耗、设备结构的工艺设计。
三、课程设计的要求课程设计的规模不同,其具体的设计项目也有所差别,但其基本内容是大体相同,主要基本内容及要求如下:1、工艺设计和计算根据选定的方案和规定的任务进行物料衡算,热量衡算,主体设备工艺尺寸计算和简单的机械设计计算,汇总工艺计算结果。
主要包括:(1)工艺设计①设备结构及主要尺寸的确定(D,H,H L,V,V L,Di等)②通风量的计算③搅拌功率计算及电机选择④传热面积及冷却水用量的计算(2)设备设计①壁厚设计(包括筒体、封头和夹套)②搅拌器及搅拌轴的设计③局部尺寸的确定(包括挡板、人孔及进出口接管等)④冷却装置的设计(包括冷却面积、列管规格、总长及布置等)2、设计说明书的编制设计说明书应包括设计任务书,目录、前言、设计方案论述,工艺设计和计算,设计结果汇总、符号说明,设计结果的自我总结评价和参考资料等。
发酵罐体积确定

5.2 发酵罐体积的确定本次设计选用锥底发酵罐,由物料衡算可知,糖化设备一次性糖化麦汁发酵液量67.9m3。
一日糖化8次。
选用发酵罐的有效容积(三锅装一罐)为:Vs=67.9×3=203.7 m³发酵罐H:D=1.5—6:1,这里选用4.4:1;锥角60—85°,这里选用60°;装料系数取80%--85%,这里取Φ=85%。
接种量范围在0.7%--0.8%,这里取0.8%。
则容积为:V有=V s(1+0.8%)=203.7×(1+0.8%)=205.3 m³V有效=V有/Φ=205.3÷85%=241.5m³主要尺寸比例:V圆柱=πD²H/4V椭圆=π/4[D²(h+D/6)]=πD³/24V锥底=πD²/12h=3πD³/24对此发酵罐采用标准椭圆形封头为上封头,60°锥角的锥形封头为下封头,柱体部分高与直径比为4:1。
则可得:V O’=πD²×4.4D/4+3πD³/24+πD³/24=(27.4+3)πD³/24241.5=(27.4+3)πD³/24D=3.986 m取D=4,则H=4×4.4=17.6m。
V O=(27.4+3)π4.4³/24=244.1m³最后圆整取V O=244.1 m³的发酵罐体。
校核:V有/V总=205.3/244.1=84.1% ,符合要求。
5.3 发酵罐材料的选择本设备采用不锈钢制作,外壁使用0Cr18Ni9不锈钢,内壁图以T-541涂料。
因为发酵罐里面所装的溶液是酸性的,而CIP清洗液中仅有碱性溶液,因此,选用材料必须耐酸耐碱耐腐蚀,因此,材料应选用不锈钢。
(1) 发酵罐圆柱体部分壁厚确定:Sd=PcDi/(2【б】tΦ-Pc)+C上式:Pc---设计压力工作压力的确定:发酵罐的高度(不加椭圆封头)即筒体与锥体的高度H1=17.6+3/2×4=21.064m封罐之前,由于与外界接触,则罐内的压力只有液柱力,但如封罐以后,罐内压力上升,而封罐之后压力最大0.12Mpa。
- 1、下载文档前请自行甄别文档内容的完整性,平台不提供额外的编辑、内容补充、找答案等附加服务。
- 2、"仅部分预览"的文档,不可在线预览部分如存在完整性等问题,可反馈申请退款(可完整预览的文档不适用该条件!)。
- 3、如文档侵犯您的权益,请联系客服反馈,我们会尽快为您处理(人工客服工作时间:9:00-18:30)。
10吨发酵罐产山东链霉素物料衡算
一、发酵罐底料的物料用量:
=2%×10000=200kg (7400/吨)
淀粉: m
01
豆粉: m
=0.4%×10000=40kg (3100/吨)
02
=0.05%×10000=5kg (3100/吨)
硫酸镁: m
03
氯化钠: m
=0.05%×10000=5kg (10000/吨)
04
=0.128%×10000=12.8kg (18000/吨)
磷酸氢二钾: m
05
=0.001%×10000=0.1kg (15000/吨)
硫酸亚铁: m
06
物料总价格= 200×7.4+40×3.1+5×3.1+5×10+12.8×18+0.1×15=1901.4元二、培养液连续灭菌用蒸汽量:
灭菌加热过程中用0.4MPa,I=2748.5KJ/kg,加热至120°C,冷却水由20°C 升到45°C。
消毒灭菌用蒸汽量(D):
D=[10×2.01×(120-20)×1.07]/(2748.5-120×4.18)=0.95t
考虑到1吨种子罐用量约为0.1t
因此总蒸汽用量为1.05吨
2.01是糖液的比热容[kJ/(kg•K)]
因此总的耗煤量=(1050 ×2748.5 )/29307.6≈100kg
1公斤标煤=29307.6kJ/k
三、发酵罐空罐灭菌蒸汽量:
1、发酵罐体加热用蒸汽量
发酵罐公称容积10m3,材料为碳钢,发酵罐罐体重2.36t,比热容0.5kJ/(kg·℃),使用0.4MPa蒸汽(表压)灭菌,发酵罐罐压保持在0.15MPa(表压)下,由20℃升至127℃,维持1h。
其蒸气用量为:
D=[2.36×1000×0.5×(127-20)]/(2748.5-535.4)=57.02kg
式中2748.5 ——0.4MPa(表压)蒸汽热焓,kJ/kg
535.4——0.15MPa,127℃时蒸汽凝结水热焓,kJ/kg
2、填充发酵罐空间所需蒸汽量
公称容积10m 3发酵罐的全容积为12m 3,其蒸气用量为:
D=12×1.39=16.68kg
式中 ρ——加热蒸汽的密度,ρ=1.39kg/m 3
发酵罐灭菌 (0.15MPa ,表压) 1h 。
3、灭菌过程的热损失
辐射与对流联合给热系数α,罐外壁温度60℃。
10m 3发酵罐的表面积为14.6m 2,消耗蒸汽量为:
D=[14.6×41.5×(60-20)]/(2748.5-535.5)=10.9kg
4、罐壁附着洗涤水升温所需蒸汽量
D=[14.6×0.001×1000×(127-20) ×4.18]/(2748.5-535.4)=2.97kg
000——水密度 (kg/m 3)
式中 0.001——附壁水平均厚度
总蒸汽消耗量
灭菌过程蒸汽渗漏,取总汽消耗量的30%,空罐灭菌蒸汽消耗量=(57+16.68+10.9+2.97)/(1-0.3)=125.1kg/h
每空罐灭菌1.5 h ,用蒸汽量:125.1×1.5=187.7(kg/罐)
1吨种子罐蒸汽用量约为发酵罐的0.12倍
因此总蒸汽用量=187.7×1.12=210.224
因此总的耗煤量=(210.224 × 2748.5 )/29307.6≈20kg
1公斤标煤=29307.6kJ/k
四、水用量
1、发酵液水用量≈10t
2、培养基冷却用水量:由120°C 热料通过与生料热交换,降至80°C,再用水冷却至32°C,冷却水由20°C 升至45°C,计算冷却水量(W ):
W=[10000×2.01×(80-32)]/[(45-20) ×4.18]=9.2t
)C h m /(kJ [5.41)2060(19.09.332︒⋅⋅=-⨯+=α
3、发酵过程产生的热量及冷却用水量。
发酵过程的热量通过发酵液温度升高进行计算:关闭冷却水观察罐内发酵液
:
温度升高,计算Q
最大
根据经验山东链霉菌素的发酵热高峰值约18810 KJ/(m3·h)
10 m3发酵罐,冷却水进口温度10°C,出口温度20°C,冷却水用量(W):W=(10×18.81)/[4.18×(20-10)]=4.5t/h
共发酵6天总用水量=4.5×24×6=648t
4、清洗用水
根据经验约为1吨
总用水量=9.2+1+10+648=668.2t
五、发酵液浓缩
10吨发酵液浓缩为500kg,此时抗生素含量为2.6%,符合生产需要。
因此除去9.5吨水所需成本≈ [(9.5 × 2602.7)/(70%×80%×29307.6)] ×0.8=1506.6元
2602.7为水从20°C到100°C蒸汽的热焓
煤价0.8元/kg
干燥机出热效率80%
锅炉效率70%
干燥机耗电成本= 4.75 × (9500/678) ×0.6 = 40元
六、总成本
灭菌理论上共需价格=(100+20)÷0.7×0.8=137.2元
蒸汽锅炉按照70%效率,原煤折合为标准煤价格≈800元/吨
发酵罐搅拌耗电价格=24×6×22×0.6=1900元
发酵罐搅拌功率22kw
用水价格=668.2×3.6=2405.5元
培养基价格=1901.4元
干燥价格 = 40 + 1506.6 = 1546.6
因此总成本=1901.4 + 137.2 + 1900 + 2405.5 +1546.6 = 7890.7元
10吨发酵液共产生10 × 1.3 = 13 kg 抗生素
因此每kg抗生素成本 = 7890.7/13 = 607 元。