零件选材及其热处理工艺
零件选材及工艺路线

(5)选材时应考虑我国的资源和供应情况,尽量选 用我国资源丰富的合金钢系列,如锰钢、硅锰钢 等;少选或不选含镍、铬、钴等我国资源缺乏的 钢种。 (6)应根据厂家的具体情况选择工艺成熟的材料, 以降低加工费,提高成品率。同时,还应考虑所 选材料的品种尽量少而集中,以减少管理费用; 尽量选用本地区或就近可以供应的材料,以降低 运输费用。此外,所选材料还应考虑环保问题等。
§ 1 选材的原则
1.2工艺性能选材原则(陶瓷材料)
硬而脆且导热性较差。根据陶瓷制品的材料、性能 要求、形状尺寸精度及生产率不同,可选用粉浆成形、
压制成形、挤压成形、可塑成形等方法。陶瓷材料的
切削加工性能极差,除极少数陶瓷外 ( 如氮化硼陶瓷 ) , 其它陶瓷均不可切削加工;陶瓷虽可磨削加工,但其
§ 3 典型零件选材与工艺分析
工程材料的应用概况
复合材料克服了高分子材料和陶瓷材料的不足,综
合了各种不同材料的优良性能,具有高的比强度、比刚 度、抗疲劳、减振、耐磨性能优良等特点。尤其是金属 基复合材料,从力学性能角度看,可能是最理想的机械 工程材料。但复合材料价格昂贵,除在航天航空、船舶、 武器装备等国防工业中的重要结构件上应用外,在一般 的民用工业上应用有限。但应注意的是,随着复合材料 的生产成本降低,其应用潜力巨大、前景极其广阔。
预防和控制热处理变形的方法与措施
预防和控制热处理变形的方法与措施
1.2工艺性能选材原则(高分子材料)
机械零件选材及热处理设计手册
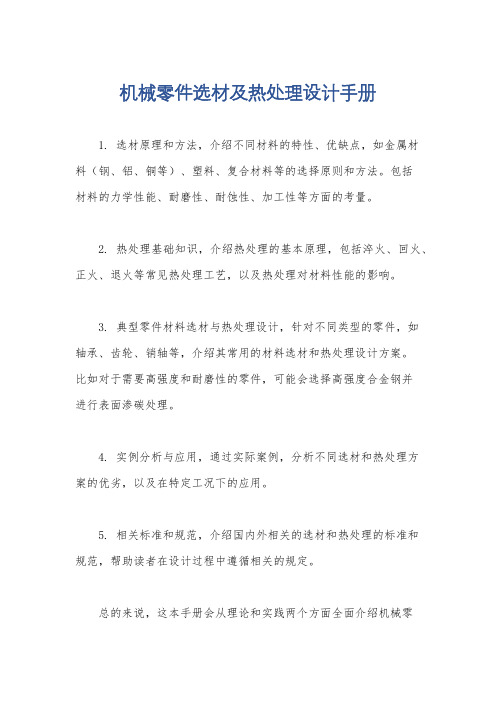
机械零件选材及热处理设计手册
1. 选材原理和方法,介绍不同材料的特性、优缺点,如金属材
料(钢、铝、铜等)、塑料、复合材料等的选择原则和方法。
包括
材料的力学性能、耐磨性、耐蚀性、加工性等方面的考量。
2. 热处理基础知识,介绍热处理的基本原理,包括淬火、回火、正火、退火等常见热处理工艺,以及热处理对材料性能的影响。
3. 典型零件材料选材与热处理设计,针对不同类型的零件,如
轴承、齿轮、销轴等,介绍其常用的材料选材和热处理设计方案。
比如对于需要高强度和耐磨性的零件,可能会选择高强度合金钢并
进行表面渗碳处理。
4. 实例分析与应用,通过实际案例,分析不同选材和热处理方
案的优劣,以及在特定工况下的应用。
5. 相关标准和规范,介绍国内外相关的选材和热处理的标准和
规范,帮助读者在设计过程中遵循相关的规定。
总的来说,这本手册会从理论和实践两个方面全面介绍机械零
件选材和热处理设计的相关知识,旨在帮助工程师和设计人员在实际工程中做出合理的材料选择和热处理设计,以确保零件具有良好的性能和可靠性。
机械零件选材原则及工艺设计

机械零件选材原则及工艺设计机械零件的选材原则及工艺设计在机械设计中,选择合适的材料和有效的工艺是非常重要的,因为这直接影响了零件的质量、性能和使用寿命。
下面是一些机械零件选材原则及工艺设计的重要考虑因素。
1. 材料的机械性能:机械零件必须具有足够的强度、硬度和耐磨性,以承受预期的工作载荷和环境条件。
因此,在选择材料时,应该考虑其拉伸强度、屈服强度、断裂韧性和硬度等机械性能指标。
2. 材料的耐腐蚀性:机械零件往往要在各种恶劣的环境条件下工作,如高温、湿度或腐蚀性介质。
因此,应选择具有良好耐腐蚀性能的材料,以保证零件的长期稳定性和可靠性。
3. 材料的热处理性:有些机械零件需要进行热处理,以改善其机械性能和硬度。
因此,在选材时,应选择适合热处理的材料,以便在工艺设计中能够获取所需的材料性能。
4. 材料的可加工性:机械零件的制造通常需要各种加工操作,如切削、铣削、焊接等。
因此,材料的可加工性也是选材的重要因素,应选择易于加工的材料,以保证制造成本和质量。
5. 材料的经济性:在选材时,还必须考虑材料的成本因素。
有时候,高性能材料可能很昂贵,但在某些应用中,可以使用性能适当的低成本材料来替代。
工艺设计也是机械零件设计中重要的一环。
下面是一些常见的工艺设计考虑因素:1. 制造工艺的可行性:在工艺设计中,应考虑零件的复杂度和制造难度。
有时候,可能需要进行多道复杂的加工操作,而在其他情况下,使用简单的加工过程就可以完成。
因此,在工艺设计中应选择最合适和最经济的制造工艺。
2. 精度要求:机械零件的精度直接影响其质量和功能。
因此,在工艺设计中,应根据零件的功能需求和装配要求,确定适当的制造精度和加工工艺。
3. 工艺的可重复性和稳定性:工艺的可重复性和稳定性对零件的质量和一致性至关重要。
因此,在工艺设计中,应选择稳定可靠的加工工艺和设备,以确保批量生产的一致性和质量可控。
总之,在机械设计中,选材和工艺设计是同等重要的。
耐磨零件选材 工艺方案举例 论文

耐磨零件的选材与工艺方案举例摘要:目前各种汽车零部件,特别是传动、转向系统中普遍需要安装一些结构简单但是需要有较好耐磨性能的垫片等零件。
本文将通过列举方案进行对比的形式分析耐磨垫片的材料选择及热处理、表面处理的工艺。
关键词:耐磨热处理材料首先,假设我们需要的是一种垫片。
因为需要与持续旋转的轴或齿轮配合,所以需要垫片表面有一定的硬度,很好的耐磨性能和光洁度。
根据零件的要求,我们列举一下五种选材及热处理的方案:1 方案一低碳钢冲压成型→渗碳处理→表面磨削这里所指的低碳钢主要是st12、q235、08al等容易冲压成型的材料,这些材料应用比较普遍,成本低容易采购、强度低、韧性好容易冲压成型。
渗碳是工艺成熟,已经被广泛采用的热处理方法,成本低、容易控制,可以很大程度上提高垫片表面的硬度和耐磨性。
表面经过平磨后,提高了垫片的平面度,保证有很好的配合精度。
但是方案一有其工艺本身难以克服的难点!首先,因为热处理工艺本身的限制,渗碳层的厚度一般单边≥0.5mm.也就是说,如果零件的厚度在1mm以下的话将很容易被渗透。
一旦零件整体被渗透,那零件整体将变得很脆,当受到大的压力或冲击力时会碎裂。
再者,比较薄或小的零件在渗碳的过程中会发生变形。
拿一个垫片为例,如果渗碳过程中垫片变形的话,唯一的办法就是在后续的磨削过程中加大磨削量。
但是这样一来就会导致渗碳层与越磨越薄或者不能保证需要的零件厚度。
这样看来,方案一主要适用于厚度≥2mm的零件的加工。
2 方案二低碳含铝合金钢冲压成型→表面平磨→渗氮处理细心的朋友可能已经注意到,该方案把渗氮处理和表面磨削加工的顺序前后进行了对调。
这主要是因为渗氮处理的两大特点!首先,渗氮是一种钢件的化学处理,可以大大提高零件表面的耐磨性能。
但是,渗氮层的厚度一般只有单边0.1mm左右。
所以,如果先进行渗氮处理再磨平的话,很容易将薄薄的渗氮层磨掉。
其次,渗氮不同于渗碳,它对零件表面的光洁度影响很小,所以可以把渗氮放到最后一道工序!但是,渗氮处理对低碳钢的要求是最好用低碳含铝合金钢,因为铝和氮的结合效果最好,所以,在各种冲压用低碳钢中08al的渗氮效果是比较理想的。
机械零件的常用材料特性及应用

用途、工作条件、物理、化学、机械工艺性能、经济性。
零件材料 各种材料的化学成分和力学性能可在相关国标、行标 和机械设计手册中查得。
以功能來分: 依其機械、電氣、熱學及其他性質功能來分。
1 )泛用塑膠: 通常以美觀及低功能使用要求,為訴求重點。 如:PE 、 PVC 、 PMMA、ABS
轴用材料
要求: 充分強度/耐磨性/耐疲勞性/充分硬度/充 分橈度
選用
一般用軸材料(A3/S10C/S45C) 強力用軸材料(SNCM240(价高)/42CrMo)
齿轮用材料
要求: 充分強度/耐磨性/充分硬度/耐衝擊性/易 加工性
選用
高周波淬火處理材料(S45C/42CrMo) 滲碳淬火處理材料(42CrMo) 氮化相比,钢具有高的强度、韧性和塑性。 可用热处理方法改善其力学性能和加工性能。
选用原则: 优选碳素钢(A3.S45C),其次是硅、锰、硼、钒类合
金钢,特殊硬度可以选合金工具钢(Cr12).
金属热处理方式
热处理方式:退火、正火、淬火和回火四种基本工艺,俗称金 属热处理的“四把火”。 1.退火:是将工件加热到适当温度,根据材料和工件尺寸采用不 同的保温时间,然后进行缓慢冷却,目的是使金属内部组织达 到 或接近平衡状态,获得良好的工艺性能和使用性能,或者为 进一步淬火作组织准备。 2.正火:是将工件加热到适宜的温度后在空气中冷却,正火的效 果同退火相似,只是得到的组织更细,常用于改善材料的切削 性能,也有时用于对一些要求不高的零件作为最终热处理。 3.淬火:是将工件加热保温后,在水、油或其它无机盐、有机水 溶液等淬冷介质中快速冷却。淬火后钢件变硬,但同时变脆。 (S45C可以达到42-50HRC, Cr12可以达到52-60HRC) 4.回火:是为了降低钢件的脆性,将淬火后的钢件在高于室温而 低于 710℃的某一适当温度进行长时间的保温,再进行冷却,这 种工艺称为回火
轴类零件选材及热处理

本章结束
返回
精品
图8-1 CM6140车床主轴
精品
返回
表8-1 机床主轴工作条件、用材及热处理
返回
精品
图8-2 汽车半轴
精品
返回
图8-3 解放牌汽车变速齿轮简图
精品
返回
表8-2 部分箱体支承类零件用材情况
代表性零件
机床床身、轴承座、 齿轮箱、缸盖、变速
器壳、离合器壳
承力支架、箱体底座 铸钢ZG270-500
刚度、强度、耐冲击
正火
支架、挡板、盖、罩、 钢板Q235、08、20、
壳
16Mn
车辆驾驶室车箱
钢板08
精品
刚度、强度
不热处理
刚度0 ~ 55HRC)。如机床齿轮。 •重载、中高速、大冲击载荷齿轮: 低 碳 ( 合 金 ) 钢 ( 20Cr 、 20MnB 、 20CrMnTi ) 渗 碳
(碳氮共渗)及淬火低温回火,齿面58~63HRC。如 汽车、拖拉机变速齿轮和后桥齿轮。 •精密传动齿轮或硬面内齿轮,要求热处理变形小: 38CrMoAl、35CrMo等。调质及气体氮化。如非重载、 工作平稳的精密齿轮。
图8-3
•负荷特点: 承载、磨损及冲击负荷较大,工作条件比较繁重。
•材料: 20CrMnTi。
•热处理技术条件: 渗碳层深0.8~1.3mm,表层Wc为0.8%~1.05%,齿面 58~62HRC。心部33~45HRC。
•工艺路线: 锻造→正火→粗加工、半精加工→渗碳淬火、低温回 火。
8.3 弹簧类零件材料选择(spring)
④铬矾弹簧钢: 50CrVA等,φ50mm淬透,应力较大的弹簧(工作温 度≤ 300℃)。
耐磨零件的选材与工艺方案举例

耐磨零件的选材与工艺方案举例目前各种汽车零部件,特别是传动、转向系统中普遍需要安装一些结构简单但是需要有较好耐磨性能的垫片等零件。
本文将通过列举方案进行对比的形式分析耐磨垫片的材料选择及热处理、表面处理的工艺。
标签:耐磨热处理材料首先,假设我们需要的是一种垫片。
因为需要与持续旋转的轴或齿轮配合,所以需要垫片表面有一定的硬度,很好的耐磨性能和光洁度。
根据零件的要求,我们列举一下五种选材及热处理的方案:1 方案一低碳钢冲压成型→渗碳处理→表面磨削这里所指的低碳钢主要是st12、Q235、08Al等容易冲压成型的材料,这些材料应用比较普遍,成本低容易采购、强度低、韧性好容易冲压成型。
渗碳是工艺成熟,已经被广泛采用的热处理方法,成本低、容易控制,可以很大程度上提高垫片表面的硬度和耐磨性。
表面经过平磨后,提高了垫片的平面度,保证有很好的配合精度。
但是方案一有其工艺本身难以克服的难点!首先,因为热处理工艺本身的限制,渗碳层的厚度一般单边≥0.5mm.也就是说,如果零件的厚度在1mm以下的话将很容易被渗透。
一旦零件整体被渗透,那零件整体将变得很脆,当受到大的压力或冲击力时会碎裂。
再者,比较薄或小的零件在渗碳的过程中会发生变形。
拿一个垫片为例,如果渗碳过程中垫片变形的话,唯一的办法就是在后续的磨削过程中加大磨削量。
但是这样一来就会导致渗碳层与越磨越薄或者不能保证需要的零件厚度。
这样看来,方案一主要适用于厚度≥2mm的零件的加工。
2 方案二低碳含铝合金钢冲压成型→表面平磨→渗氮处理细心的朋友可能已经注意到,该方案把渗氮处理和表面磨削加工的顺序前后进行了对调。
这主要是因为渗氮处理的两大特点!首先,渗氮是一种钢件的化学处理,可以大大提高零件表面的耐磨性能。
但是,渗氮层的厚度一般只有单边0.1mm 左右。
所以,如果先进行渗氮处理再磨平的话,很容易将薄薄的渗氮层磨掉。
其次,渗氮不同于渗碳,它对零件表面的光洁度影响很小,所以可以把渗氮放到最后一道工序!但是,渗氮处理对低碳钢的要求是最好用低碳含铝合金钢,因为铝和氮的结合效果最好,所以,在各种冲压用低碳钢中08Al的渗氮效果是比较理想的。
汽车发动机活塞销的选材与热处理工艺课程设计

1汽车发动机活塞销的零件图如下连杆图1汽车发动机活塞销零件尺寸图2服役条件与性能分析活塞销(英文名称:Piston Pin),是装在活塞裙部的圆柱形销子,它的中部穿过连杆小头孔,用来连接活塞和连杆,把活塞承受的气体作用力传给连杆。
为了减轻重量,活塞销一般用优质合金钢制造,并作成空心。
塞销的结构形状很简单,基本上是一个厚壁空心圆柱。
其内孔形状有圆柱形、两段截锥形和组合形。
圆柱形孔加工容易,但活塞销的质量较大;两段截锥形孔的活塞销质量较小,且因为活塞销所受的弯矩在其中部最大,所以接近于等强度梁,但锥孔加工较难。
本次设计选用内孔为原形的活塞销。
服役条件:(1)高温条件下承受周期性强烈冲击和弯曲、剪切作用(2)销表面承受较大的摩擦磨损。
失效形式:由于承受周期性的应力,使其发生疲劳断裂和表面严重磨损。
性能要求:(1)活塞销在高温条件下承受很大的周期性冲击负荷,且由于活塞销在销孔内摆动角度不大,难以形成润滑油膜,因此润滑条件较差。
为此活塞销必须有足够的刚度、强度和耐磨性,质量尽可能小,销与销孔应该有适当的配合间隙和良好的表面质量。
在一般情况下,活塞销的刚度尤为重要,如果活塞销发生弯曲变形,可能使活塞销座损坏;(2)具有足够的冲击韧性;(3)具有较高的疲劳强度。
3技术要求活塞销技术要求:①活塞销全部表面渗碳,渗碳层深度为0.8〜1 . 2mm渗碳层至心部组织应均匀过渡,不得有骤然转变。
②表面硬度58〜64 HRC,同一个活塞销上的硬度差应V 3 HRG③活塞销心部硬度为24〜40 HRC。
④活塞销渗碳层的显微组织应为细针马氏体,允许有少量均匀分布的细小粒状碳化物,不得有针状和连续网状分布的游离碳化物存在。
心部的针状应是低碳马氏体及铁素体。
表活塞销内、外圆渗碳技术要求活塞销的材料一般为低碳钢或低碳合金钢,如20、15Cr、20Cr或2OCrMnTi等。
外表面渗碳淬硬,再经精磨和抛光等精加工。
这样既提高了表面硬度和耐磨性,乂保证有较高的强度和冲击韧性。
- 1、下载文档前请自行甄别文档内容的完整性,平台不提供额外的编辑、内容补充、找答案等附加服务。
- 2、"仅部分预览"的文档,不可在线预览部分如存在完整性等问题,可反馈申请退款(可完整预览的文档不适用该条件!)。
- 3、如文档侵犯您的权益,请联系客服反馈,我们会尽快为您处理(人工客服工作时间:9:00-18:30)。
零件选材及其热处理工艺一、机床主轴1、工作条件及失效形式主轴是机床主轴部件的关键零件之一,主要起支承传动件和传递转矩的作用,其工作条件为:(1)承受交变载荷、交变弯曲载荷或拉—压载荷。
(2)局部(轴颈、花键等处)承受摩擦和磨损。
(3)特殊条件下受高温或介质作用。
主轴的失效形式主要是疲劳断裂和轴颈处磨损,有时也发生冲击过载断裂,个别情况下发生塑性变形或腐蚀失效。
2、性能要求:(1)由于机床的主运动由其提供,主轴工作时的运动精度对工件加工质量将产生直接影响,因此必须保证主轴工作时具有很高的运动精度。
(2)高的疲劳强度,以防轴疲劳断裂。
(3)优良的综合力学性能,即较高的屈服强度和抗拉强度、较高的韧性,以防塑性变形及过载或冲击载荷作用下的折断和扭断。
(4)局部承受摩擦的部位具有高硬度和耐磨性,以防磨损失效。
(5)在特殊条件下工作时应具有特殊性能,如蠕变抗力、耐腐蚀性等。
3、主轴的选材与热处理不同工作要求的机床主轴,其性能要求是不同的,加工工艺也是有差异的,因此选用的材料及相应的热处理工艺也会不同.3.1 普通机床主轴的选材与热处理工艺普通机床往往用于一般精度要求的工件加工.机床主轴通常采用滚动轴承支承,直接影响主轴回转工作精度的轴颈没有直接的运动磨损.因此,针对主轴工作时承受交变载荷的受力特性,一般选用综合机械性能较好的材料.同时,作为提供机床主运动的基准件,主轴的几何质量好坏直接影响机床主运动的精度,因此通常对普通机床主轴关键表面的几何质量提出下列要求⋯:1) 轴颈的直径精度为IT6,圆度、圆柱度应限制在直径公差之内;2) 配合轴颈(装配传动件的轴颈)相对支承轴颈(装配轴承的轴颈)的径向圆跳动为0.01~0.03 mm,端面圆跳动为0.005~0.010mm;3) 支承轴颈的表面粗糙度为Ra0.63~0.16µm,配合轴颈为Ra2.5—0.63µm.从几何精度要求和经济性两方面考虑,主轴的加工一般采用车削基础上的磨削工艺来实现,可见,主轴用材必须同时具有良好的车削工艺性和磨削工艺性.3.1.1主轴选材依据主轴的工作环境和工作要求,普通机床主轴材料通常选用下列3类:1) 中碳结构钢:常用牌号45,50,55结构钢;2) 中碳合金钢:常用牌号40Cr,50Cr合金钢;3) 锰钢:常用牌号65Mn合金钢.3.1.2热处理工艺一般首先采用整体表面淬火或整体调质后主轴头部内外锥、主轴颈及花键表面淬火,然后进行低温回火的常规热处理工艺根据需要,硬度一般可控制在42—47HRC,45—50HRC 或48—53HRC等3种状态.在工程实际中,有时为得到较好的耐磨性,应提高表面硬度,通常选用含碳量较高的50。
,55,50Cr,65Mn等结构钢,其淬火后低温回火的硬度可达52—57HRC。
3.2精密机床主轴的选材及热处理工艺在精密机床上加工的工件精度要求很高,因此精密机床主轴的工作精度要求就更高.为提高机床的使用效率和降低使用成本,同时要求主轴工作精度具有持久的保持性,因此,在进行主轴支承设计时,常采用定心精度很高的动压、静压或动静压滑动轴承支承.从理论上分析,静压轴承支承时主轴颈与轴瓦是不接触的,动压轴承支承时主轴颈仅在启动阶段与轴瓦接触,因此其支承方式极有利于主轴回转精度的持久保持.但在实际运行时,因受运动副几何精度、不平衡力、热变形、冲击载荷、振动等动、静态因素的影响,轴颈支承油楔的刚性并非很稳定,主轴回转中心的漂移运动始终存在,主轴颈与支承轴瓦的直磨损并不能完全避免.为此,必须通过合理的选材及热处理来保证主轴颈的耐磨性和几何精度的稳定性.3.2.1主轴选材依据主轴的使用要求和工作环境,精密机床主轴材料通常选用下列4类:1) 合金渗氮钢:常用牌号38CrMoAIA;2) 合金工具钢:常用牌号9Mn2V;3) 滚动轴承钢:常用牌号GCrl5;4) 合金渗碳钢:常用牌号20Cr,20CrMnTi.3.2.2热处理工艺1) 38CrMoAlA.热处理工艺:退火一调质一高温除应力一渗氮。
退火:完全退火,消除锻造应力,在切削加工前进行;调质:930℃*3 h油或水冷,650℃*5~6 h高温回火,HB265~295,金相检查离表面10mm 处铁素体量小于5%,在外圆精车前进行;高温除应力:630℃*5 h炉冷,350℃出炉风冷,消除切削加工引起的残余应力,在粗磨外圆后进行;渗氮:500℃~520℃*5 h+550℃~560℃*25 h二段氮化,氮化层深度不小于0.45 mm,硬度大于950HV,脆化不大于2级,在外圆精磨前进行.2) 9Mn2V.热处理工艺:球化退火一调质一中频淬火一人工时效.球化退火:760 ℃*4 h或690℃*6 h,球化1.5~5级,网络1~3级,在切削加工前进行;调质:800℃*3 h油冷,630℃~650℃高温回火,HB250±30,在外圆精车前进行;中频淬火:2 500周连续加热冷却,有明显变形时校直,850℃水冷,过冷度小于5 mm,淬硬层3~5 mm,180℃*8 h低温回火,在外圆精车后进行;人工时效:160℃*12~24 h,在外圆精磨前进行.二、齿轮类零件1、齿轮的工作条件和失效形式齿轮是应用广泛的机械零件,主要起传递扭矩、变速或改变传力方向的作用。
其工作条件是:(1)传递扭矩时齿根部承受较大的交变弯曲应力。
(2)齿啮合时齿面承受较大的接触压应力并受强烈的摩擦和磨损。
(3)换挡、起动、制动或啮合不均匀时承受一定冲击力。
齿轮的失效形式主要是齿的折断(包括疲劳断裂和冲击过载断裂)和齿面损伤(包括接触疲劳麻点剥落和过度磨损)。
2、性能要求根据齿轮的工作条件和失效形式,齿轮材料应具有如下性能:(1)高的抗弯疲劳强度,以防齿轮疲劳断裂。
(2)足够高的齿心强度和韧性,以防齿轮过载断裂。
(3)足够高的齿面接触疲劳强度和高的硬度及耐磨性,以防齿面损伤。
(4)较好的工艺性能,以便于制造和热处理等。
3、齿轮的选材及热处理齿轮用材绝大多数是钢(锻钢与铸钢),某些开式传动的齿轮可用铸铁,特殊情况下还可采用有色金属和工程塑料。
确定齿轮用材的主要依据是:齿轮的传动方式(开式或闭式)、载荷性质与大小(齿面接触应力和冲击负荷等)、传动速度(节圆线速度)、精度要求、淬透性及齿面硬化要求、齿轮副的材料及硬度值的匹配情况等。
(1)钢制齿轮钢制齿轮有型材和锻件两种毛坯形式。
一般锻造齿轮毛坯的纤维组织与轴线垂直,分布合理,故重要用途的齿轮都采用锻造毛坯。
钢制齿轮按齿面硬度分为硬齿面和软齿面:应齿面硬度<350HBW为软面;齿面硬度>350HBW为硬齿面。
1)轻,低、中速,冲击力小,精度较低的一般齿轮,选用中碳钢(如Q255、Q275、40、45、50、50Mn等)制造。
常用正火或调质等热处理制成软齿面齿轮,正火硬度为160~200HBW;调质硬度一般为200~280HBW(≤350HBW)。
此类齿轮硬度适中,齿形加工可在热处理后进行,工艺简单,成本低。
主要用于标准系列减速箱齿轮,以及冶金机械、重型机械和机床中的一些次要齿轮。
2)中载,中速、受一定冲击载荷、运动较为平稳的齿轮,选用中碳钢或合金调质钢(如45、50Mn、40Cr、42SiMn等)制造。
其最终热处理采用高频或中频及低温回火.制成硬齿面齿轮,齿面硬度可达50~55HRC,齿心部保持原正火或调质状态,具有较好的韧性。
大多数机床齿轮属于这种类型。
3)重载,中、高速,且受较大冲击载荷的齿轮,选用低碳合金渗碳钢或碳氮共渗钢(如20Cr、20MnB、20CrMnTi、30CrMnTi等)制造。
其热处理是渗碳、淬火、低温回火,齿轮表面获得58~63HRC的高硬度.因淬透性高,齿心部有较高的强度和韧性。
这中齿轮的表面耐磨性、抗接触疲劳强度、抗弯强度及心部的抗冲击能力都高于表面淬火的齿轮,但热处理变形较大,在精度要求较高时应安排磨削加工。
主要用于汽车、拖拉机变速箱和后桥中。
内燃机车、坦克、飞机上的变速齿轮,其负载和工作条件比汽车的更重要、更苛刻,对材料的性能要求更高,应选用含合金元素较多的渗碳钢(如20Cr2Ni4\18Cr2Ni4W A)制造,以获得更高的强度和耐磨性。
4)精密传动齿轮或磨齿有困难的硬齿面齿轮(如内齿轮),要要求精度高,热处理变形小,宜采用氮化钢(如38CrMoAl等)制造。
热处理采用调质及氮化。
氮化后齿面硬度高达850~1 200H V (相当于65~70HRC),热处理变形极小,热稳定性好(在500~550℃仍能保持高硬度),并有一定耐蚀性。
其缺点是硬化层薄,不耐冲击,不适用重载齿轮,多用于载荷平稳精密传动齿轮或磨齿困难的内齿轮。
(2)铸钢齿轮某些尺寸较大(如直径大于400mm)、形状复杂并受一定冲击的齿轮,其毛坯用锻造难以加工时需要采用铸钢。
常用碳素铸钢为ZG270—500、ZG310—570、ZG340—640等。
载荷较大的采用合金铸钢,ZG40Cr、ZG35CrMo、ZG42MnSi等。
铸钢齿轮通常是在切削加工前进行正火或退火,以消除铸造内应力,改善组织和性能的不均,从而提高切削加工性。
要求不高、转速较慢的铸钢齿轮,可在在退火或正火处理后应用;对耐磨性要求较高的,可进行表面淬火(如火焰淬火)。
(3)铸铁齿轮灰铸铁可用于制造开式传动齿轮,常用的牌号有HT200、HT250\HT300等。
灰铸铁组织中的石墨能起润滑作用,减摩性较好,不易胶合,切削加工性能好,成本低。
其缺点是抗弯强度差,性脆,耐冲击性差。
只适用于制造一些轻载、低速、不受冲击的齿轮。
由于球墨铸铁的强韧性较好,在闭式齿轮传动中,有用球墨铸铁(如:QT600—3、QT450—10、QT400—15等)代替铸钢的趋势。
铸铁齿轮在铸造后一般进行去应力退火或正火、回火处理,硬度在170~269HBW之间,为提高耐磨性还可进行表面淬火。
(4)有色金属齿轮对仪表齿轮或接触腐蚀介质的轻载齿轮,常用抗蚀、耐磨的有色金属型材制造。
常见的有黄铜(如H62)、铝青铜(如QA19—4)、硅青铜(如QSi3—1)、锡青铜(QSn6.5—0.1)。
硬铝和超硬铝(如2A12、7A04)可制作轻质齿轮。
另外,对蜗轮蜗杆传动,由于传动比达、承载力大,常用锡青铜制作蜗轮(配合钢制蜗杆),以减摩、减少咬合和黏着现象。
(5)工程塑料齿轮在轻载、无润滑条件下工作的小型齿轮,可以选用工程塑料制造。
常用的有尼龙、聚碳酸酯、夹布层压热固性树脂等。
工程塑料具有重量轻、摩擦系数小、减震、工作噪音小等特点,适用于制造仪表、小型机械的无润滑、轻载齿轮。
其缺点是强度低,工作温度较低,不宜用于制作承受较大载荷的齿轮。
(6)粉末冶金材料齿轮这种齿轮一般适用于大批量生产的小齿轮,如汽车发动机的定时齿轮(材料Fe-C0.9)、分电器齿轮(材料Fe-C0.9—Cu2.0)、农用柴油机的凸轮轴齿轮(材料Fe-Cu-C)、联合收割机中的油泵齿轮等。