乳化液各参数的控制方法
乳化液MSDS
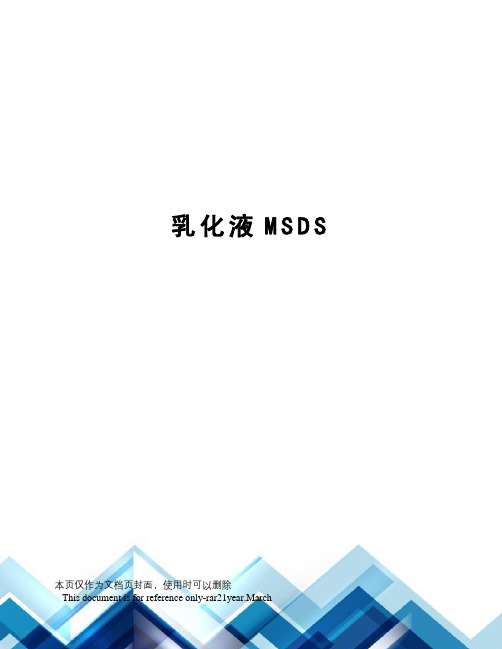
立即用清水或生理盐水冲洗
吸入:
误服者可催吐、就医
食入:
/
第五部分消防措施
危险特性:
/
有害燃烧物质:
/
灭火方法:
/
第六部分泄露应急处理
应急处理:
/
第七部分操作处置与储存
操作注意事项:
操作过程中应防止溅射
储存注意事项:
可采用塑料桶和铁桶进行包装,存放于干净、干燥的地方,存放过程中应防止容器泄露,不要于强酸混合,分装时注意不要溅射到眼睛和口中
危险性类别:
本品为水溶性,不易燃、不易爆,无放射性、无腐蚀性
侵入途径:
误食
健康危害:
本品挥发性低,大量食入会刺激中枢神经,引起呕吐等症状,严重时会导致支气管炎、肺炎等病症。
环境危害:
该物质对大气无影响,但应防止该物质对饮用水的污染
燃爆危险:
该物质无燃爆危险
第四部分急救措施
皮肤接触:
该品在应用条件下不会对皮肤引起刺激反应,个别情况若出现瘙痒症状,请用清水冲洗,情况严重者可涂以硼酸软膏、皮或200公斤铁桶包装
运输注意事项:
避免挤压,防止包装桶泄露,小心轻放
第十五部分法规信息
法规信息:
《危险化学品安全管理条例》(国务院令第344号)
《危险货物品名表》(GB12268-2005)
《危险货物分类和品名编号》(GB6944-2005)
《危险化学品安全技术说明书编写规定》(GB16483-2000)
第八部分
接触控制/个体防护
第十六部分
其他信息
第一部分化学品名称
化学品中文名称:
混合物,也叫冷却液、切削液
化学品英文名称:
/
电液控制液压支架乳化液要求
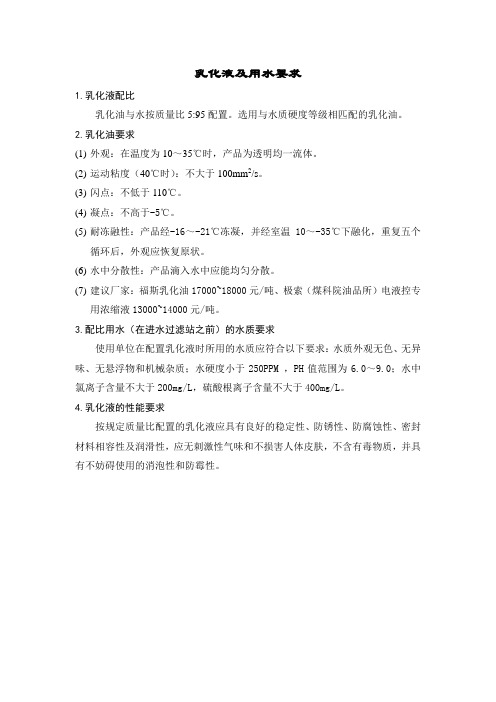
乳化液及用水要求
1.乳化液配比
乳化油与水按质量比5:95配置。
选用与水质硬度等级相匹配的乳化油。
2.乳化油要求
(1)外观:在温度为10~35℃时,产品为透明均一流体。
(2)运动粘度(40℃时):不大于100mm2/s。
(3)闪点:不低于110℃。
(4)凝点:不高于-5℃。
(5)耐冻融性:产品经-16~-21℃冻凝,并经室温10~-35℃下融化,重复五个
循环后,外观应恢复原状。
(6)水中分散性:产品滴入水中应能均匀分散。
(7)建议厂家:福斯乳化油17000~18000元/吨、极索(煤科院油品所)电液控专
用浓缩液13000~14000元/吨。
3.配比用水(在进水过滤站之前)的水质要求
使用单位在配置乳化液时所用的水质应符合以下要求:水质外观无色、无异味、无悬浮物和机械杂质;水硬度小于250PPM ,PH值范围为6.0~9.0;水中氯离子含量不大于200mg/L,硫酸根离子含量不大于400mg/L。
4.乳化液的性能要求
按规定质量比配置的乳化液应具有良好的稳定性、防锈性、防腐蚀性、密封材料相容性及润滑性,应无刺激性气味和不损害人体皮肤,不含有毒物质,并具有不妨碍使用的消泡性和防霉性。
预乳化法的注意事项

预乳化法的注意事项预乳化法是一种常用的乳化方法,用于制备乳化液,广泛应用于食品、化妆品、医药等行业。
在进行预乳化过程中,需要注意以下几个方面:1、选择适当的乳化剂和溶剂:乳化剂是实现乳化作用的关键。
应选择具有良好乳化性能的乳化剂,例如表面活性剂、胶体稳定剂等。
此外,溶剂的选择也要考虑乳化剂的溶解度和稳定性,以保证乳化剂能够充分溶解并发挥作用。
2、控制乳化温度:乳化温度对乳化效果有重要影响。
一般来说,较高的温度可以提高乳化速度,但过高的温度可能导致乳化剂分解或失去活性,影响乳化效果。
因此,在预乳化过程中应控制合适的温度,一般在乳化剂的最佳工作温度范围内进行操作。
3、搅拌参数的控制:搅拌是预乳化的关键步骤之一,可以通过增加界面面积和剪切力来促进乳化。
搅拌速度和时间的选择要根据具体情况进行调整,一般来说,速度过快可能导致乳化剂的分解,速度过慢则会影响乳化效果。
此外,还应注意选择合适的搅拌器形式和参数,以确保乳化剂在搅拌过程中能够充分分散和混合。
4、逐步加入油相和水相:预乳化法通常是将油相和水相逐步加入到乳化剂中,并进行搅拌,以便充分混合和乳化。
在添加过程中,应注意速度的控制,避免过快或过慢导致乳化不充分。
此外,应注意加入顺序,一般来说,应先将乳化剂溶解在水相中,再加入油相,以提高乳化效果。
5、控制pH值和盐浓度:pH值和盐浓度对乳化效果和稳定性都有影响。
乳化过程中,应根据具体要求控制介质的pH值和盐浓度,以促进乳化剂的溶解和乳化作用。
一般来说,pH值的选择要考虑乳化剂的最适工作pH范围,并根据油相和水相的性质进行调整。
盐浓度的选择一般要避免过高或过低,过高的盐浓度可能会引起乳化剂失活,过低的盐浓度则可能影响乳化的稳定性。
6、对乳化液的后续处理:乳化液制备完成后,还需要进行适当的后续处理,以提高其稳定性和质量。
例如,可以通过调整pH值、温度或添加稳定剂等方式来进一步改善乳化液的品质和稳定性。
总之,预乳化法是一种常用且有效的乳化方法,通过选择适当的乳化剂和溶剂、控制乳化温度、搅拌参数、逐步加入油相和水相、控制pH值和盐浓度,以及进行适当的后续处理,可以获得良好的乳化效果和稳定性。
乳化液混合使用注意事项
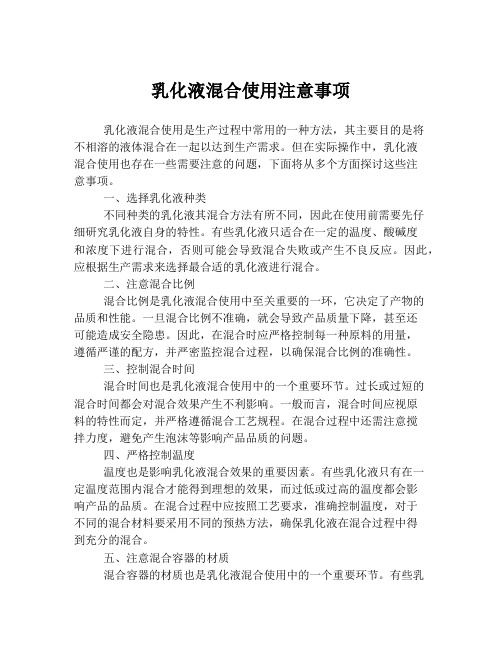
乳化液混合使用注意事项乳化液混合使用是生产过程中常用的一种方法,其主要目的是将不相溶的液体混合在一起以达到生产需求。
但在实际操作中,乳化液混合使用也存在一些需要注意的问题,下面将从多个方面探讨这些注意事项。
一、选择乳化液种类不同种类的乳化液其混合方法有所不同,因此在使用前需要先仔细研究乳化液自身的特性。
有些乳化液只适合在一定的温度、酸碱度和浓度下进行混合,否则可能会导致混合失败或产生不良反应。
因此,应根据生产需求来选择最合适的乳化液进行混合。
二、注意混合比例混合比例是乳化液混合使用中至关重要的一环,它决定了产物的品质和性能。
一旦混合比例不准确,就会导致产品质量下降,甚至还可能造成安全隐患。
因此,在混合时应严格控制每一种原料的用量,遵循严谨的配方,并严密监控混合过程,以确保混合比例的准确性。
三、控制混合时间混合时间也是乳化液混合使用中的一个重要环节。
过长或过短的混合时间都会对混合效果产生不利影响。
一般而言,混合时间应视原料的特性而定,并严格遵循混合工艺规程。
在混合过程中还需注意搅拌力度,避免产生泡沫等影响产品品质的问题。
四、严格控制温度温度也是影响乳化液混合效果的重要因素。
有些乳化液只有在一定温度范围内混合才能得到理想的效果,而过低或过高的温度都会影响产品的品质。
在混合过程中应按照工艺要求,准确控制温度,对于不同的混合材料要采用不同的预热方法,确保乳化液在混合过程中得到充分的混合。
五、注意混合容器的材质混合容器的材质也是乳化液混合使用中的一个重要环节。
有些乳化液对某些材质具有腐蚀性,因此应根据不同的乳化液选择适当的混合容器。
同时,装载混合容器的设备也要适宜,以确保混合过程的安全和顺利进行。
最后,需要指出的是,乳化液混合使用虽然在生产中常用,但也存在不少的技术和安全隐患。
在实际操作过程中,应注重细节,严格执行操作规程和安全操作程序,确保乳化液混合使用的安全和有效性。
[宝典]乳化液主要参数及其影响
![[宝典]乳化液主要参数及其影响](https://img.taocdn.com/s3/m/befc25b6294ac850ad02de80d4d8d15abe230003.png)
轧制液主要技术指标和其影响乳化液温度当在一台冷轧机上使用我们的弥散液技术时,轧制乳液的温度可以是一个有价值的工具。
我们的技术结合乳化剂的均匀混合:非离子、阳离子和温度的敏感性。
这种乳化剂的动态混合给了我们的弥散型技术产品以实现各种参数范围的能力。
我们有能力利用乳化液的温度在不增加轧制液浓度的情况下以提高带油水平的方式来改进润滑性能。
斯图亚特乳化剂配方的温度敏感性具有改变带油水平的能力。
乳化液的温度影响乳化剂在轧入时的离水展着能力或带油能力。
如果轧制计划从厚料到薄料经常改变,这可以是一个便利的工具。
例如:当生产0.18mm钢板时乳化液可以一般地运行在浓度3.5%和62℃的条件。
如果轧制计划要求快速0.40mm的钢板,乳化液不在需要3.5%的油浓度,而且在轧机上可能会出现与过渡润滑有关的问题。
要改进这种情况,最简单的方法是将轧制液的温度降到50℃,以减少在轧入时的带油量。
反之,当从0.40mm 变为0.18mm时,尽管要添加少量的润滑油,这种方法也能用。
要保持对乳化液的控制也是重要的。
如允许轧制液温度达到极端水平并保持一段时间,将可能对轧制液的质量和协调性带来损害。
如果轧制液或纯润滑油加热到75℃以上并保持一段时间也会产生问题。
在这样的温度上,轧制润滑油中的乳化剂配方开始受损害,而且脂肪酸链也开始分解。
你会发现润滑油变得难于保持在轧制液中,带油水平或展着性能很难控制。
对此,推荐的维护方法是,把乳化液的温度降低到控制要求的水平范围内,撇去浮油,加入一定量的新油,把浓度恢复调整到控制指标范围内。
轧制液的温度太低时也会发生问题,轧制液在42℃以下的温度环境运行容易产生易于细菌繁殖的环境。
在这种温度条件下细菌在轧制液中会大量繁殖,导致轧制液性能一致性方面的问题。
轧制液发臭并且pH值波动不定是轧制液中出现细菌大量繁殖的典型症状。
推荐的维护方法是,用巴氏法(高温加热)杀菌,在系统循环过程中将温度增加到60℃,循环几个小时,系统循环的时间取决于轧制液系统的大小和细菌污染的程度。
乳化液系统说明

床有2台泵。与系统主泵而是 根据液位不同起泵的数量不同 操作工可以在画面上设置每次走纸的时间和 两次走纸之间的时间间隔。
乳化液系统的运行
乳化液系统在轧钢之前要提前运行,通过旁通回路 平稳运行。保证乳化液总量的充足和各个乳化液箱 液位的平衡。
2.S3_STRIP_SPEED与PASS_SPEED的 比值乘以二级下发的WR_EXIT_CENTER 乳化喷射量值。
PDA
开关量信号包括每一机架的供乳阀开信号, 流量OK信号,LCO给EMU的信号,EMU给 LCO的信号。
模拟量的信号有每架乳化液的流量,压力, 温度信号。系统的压力设定值,压力实际值, 加脱盐水的流量,加基油的流量。
乳化液站的工作模式
根据轧制要求,乳化液有两种工作模式。 模式 1:1#~5#机架都用A 乳化液系统。
模式 2:1#~4#机架用 A乳化液系统, 5#机架用 L 乳化液系统,适用于5#机架对 板形要求较高的情况。 根据需要,两种乳化液的浓度有所不同。
乳化液系统构成
收集槽 供乳系统 喷射梁 平床过滤系统 提升泵站 加脱盐水加基油系统 直喷系统 污泥箱
加基油系统有两台泵,用来给A系统,L系统和直喷 系统加基油。
当乳化液浓度低时,加油的位置在收集槽和系统主 泵之间的主管路上。
污泥箱
共有2个收集槽 1#,2#收集槽共用1个污泥箱, 3#,4#收集槽共用1个污泥箱。 每个污泥箱有一个排污泵,一个排放阀,一
个循环阀。
平床过滤系统
功能:平床用于乳化液的过滤 平床系统共有3个平床,1#和2#平床为A系
当轧机需要供乳时,通过控制旁通回路的调 节阀改变旁通的流量来调节系统的压力。
浅谈乳化液检测指标和日常监控注意事项

浅谈乳化液检测指标和日常监控注意事项发布时间:2021-11-15T07:56:12.798Z 来源:《中国科技人才》2021年第22期作者:化验员许立军[导读] 乳化液:乳化液是由水、基础油、表面活性剂、防锈添加剂、极压剂、抗氧化剂等组分组成的一种高性能的金属加工液。
通过搅拌将油相破碎成油滴,均匀分布于水中形成的液体。
以兼顾润滑剂的润滑性和冷却性。
一汽-大众动力总成事业部成都发动机厂乳化液:乳化液是由水、基础油、表面活性剂、防锈添加剂、极压剂、抗氧化剂等组分组成的一种高性能的金属加工液。
通过搅拌将油相破碎成油滴,均匀分布于水中形成的液体。
以兼顾润滑剂的润滑性和冷却性。
在乳化液的日常使用过程中,需要关注的主要理化指标有:浓度、PH值、消泡、电导率、硬度、菌类、杂油等。
以上各项指标,需要做好日常监控,维持各指标在最优范围。
只有各项指标达到要求,才能使乳化液更好的满足生产加工要求。
下面浅谈一下以上各指标日常监控的注意事项1.浓度:对于生产过程中使用的乳化液来说,浓度主要是指乳化液稀释液中的油的含量或乳化液稀释液的碱值。
其中油的作用主要是在加工过程中起润滑作用,碱性主要起维持乳化液稳定和防锈作用。
在生产过程中乳化液浓度变化的原因主要有:水分蒸发、零件与切屑带走、自身组分消耗、污染物混入等。
因水分蒸发、零件与切屑带走、自身组分消耗引起的浓度变化,属于生产过程中的正常消耗,浓度的变化是有规律可循的。
综合每日液位变化与实际浓度情况,按比例对系统进行补水补充乳化液原液来完成浓度和工作液位的调整。
例如:缸盖罩盖集中过滤机F1的运维控制,根据连续3个月的《化学添加记录》和《浓度管理记录表》可以看出,在生产期间,缸盖罩盖集中过滤机每天加水量在3-8吨之间,并对应加入乳化液原液10-80千克,浓度保持在控制范围内,但是浓度波动比较大,可以通过提高乳化液加注比重来减小乳化液浓度波动。
污染物混入:在加工过程中,由于加工环境所致,乳化液中会混入杂质、杂油等外来物质。
乳化切削液标准

乳化切削液标准
乳化切削液标准指的是对乳化切削液的质量、性能和使用等方面的规定和要求,以确保其在使用过程中能够达到理想的切削效果和加工性能。
以下是一些常见的乳化切削液标准:
1.外观:乳化切削液应呈现均匀的乳白色液体,不得有沉淀、悬浮物和机械
杂质。
2.PH值:乳化切削液的PH值应控制在一定范围内,以适应不同的金属材料
和加工要求。
一般来说,PH值在8-9之间较为适宜。
3.乳化稳定性:乳化切削液应具有良好的乳化稳定性,确保在使用过程中不
会出现油水分离或分层现象。
4.防锈性:乳化切削液应具有一定的防锈性能,以防止加工后的工件生锈。
5.润滑性:乳化切削液应具有良好的润滑性能,减少切削过程中的摩擦,降
低切削力和切削温度,提高工件表面质量和刀具寿命。
6.抗菌性:乳化切削液应具有一定的抗菌性能,防止微生物在切削液中滋生。
7.环保性:乳化切削液应符合环保要求,不得含有有毒有害物质,且在使用
和处理过程中对环境和人体健康无害。
此外,根据不同的应用领域和加工要求,还有一些特定的乳化切削液标准,如切削性能、冷却性能、清洗性能等方面的规定和要求。
总结来说,乳化切削液标准指的是对乳化切削液的质量、性能和使用等方面的规定和要求,以确保其在使用过程中能够达到理想的切削效果和加工性能。
这些标准涉及到外观、PH值、乳化稳定性、防锈性、润滑性、抗菌性和环保性等多个方面,是评价乳化切削液性能的重要依据。
- 1、下载文档前请自行甄别文档内容的完整性,平台不提供额外的编辑、内容补充、找答案等附加服务。
- 2、"仅部分预览"的文档,不可在线预览部分如存在完整性等问题,可反馈申请退款(可完整预览的文档不适用该条件!)。
- 3、如文档侵犯您的权益,请联系客服反馈,我们会尽快为您处理(人工客服工作时间:9:00-18:30)。
( 1 )用 P H仪测定 ,必须在环境 温度 下校准后使用 ,并等读盘 稳定后读 数。由于乳化剂要在一定的 P H 范围才 能发挥最佳作用 , 所 以要控制 好乳化 液的 P H值 。 ( 2 )P H值的控制范围 :5 . 5 ~6 . 5 。如果超出正常范 围,通过 适当加 N a 0 H或 H a P 0 来调节。 3电导率 ( 1 ) 用 电导率仪测定 , 电导率 是乳化液水相 中导 电物质 的总反 应 ,电导率过高会对乳化液的稳定性造成不 良影响 ,增加灰分值 , 且板面与导电物质会在 局部发 生化学反应 ,增加钢板生锈 的机会 。 ( 2 )电导率大于 4 0 0 u s / c m时 ,根据所测值 ,加入新轧制油和 脱盐水,直到电导率小于 4 0 0 u s / c m 。 4皂化值 ( 1 ) 用氢氧化钾 乙醇溶液加入到所提取的油品和空白样 中, 冷 凝 回流 3 5 分钟,再 用盐酸标准溶液滴定 的方法测定
在实际轧机的生产中液压油齿轮油等矿物油与轧制油都是有机连结构的有机物在乳化液中经过循环后会与轧制油相融合杂油的粘度大而离水展着性差粘附在带钢表面难以去除且矿物油的润滑性比酯类差很多这些杂油会造成皂化值的降低
T e c h பைடு நூலகம் o l o g y F O r u m
乳化液各参数的控制方法
郭 静 孙 宁涛 贾英英 苏东磊
公 式 : 皂 化 值= ( A — B )* C . 5 6 . 1 1 / D m g K O H / g
化油滴颗粒度增 加,E S I值 下降,降低乳化液的稳定性和润滑性, 轧制板面残 留物增加 , 加大油耗 且乳化液夹带后更容易产生斑迹 。 ( 3 )控制范 围:灰分 小于 4 0 0 m g / g ,铁含量小于 1 5 0 m g / g 。 ( 4 )控制方法:每天定时开启磁此过滤器,每班 1 - 2小时,当 铁粉含 量超 出控制线时,缩短时间间隔,直至铁粉含量在控制范围 内,灰分 总量超标时 ,可加水加油进行稀释 。
7 氯 含 量
式中:A 一 滴定空 白样消耗盐酸溶液 的毫升数 ( m 1 ) B 一 滴定样品消耗盐酸溶液的毫升数 ( m 1 ) c 一 盐酸溶液的摩尔浓度 ( m o l / L ) D 一 样 品重量 ( g ) 5 6 . 1 l = 氢氧化钾的分子量 ( 2 ) 皂化值代表轧制油中酯的含量 。 在 实际轧机 的生产 中, 液 压油,齿轮油等矿物油与轧制油都是有机连结构的有机物 ,在乳化 液中经过 循环后会与轧 制油相 融合 , 杂油 的粘度大而离水展着性差 , 粘附在带钢表面难 以去除,且矿物油的润滑性 比酯类差很多 ,这些
( 山东钢铁集团莱芜分公 司板 带厂 。山东 莱芜 2 7 1 1 0 4)
【 摘 要】 乳化液 的各项指标影响 着冷轧卷的质量 ,为 了生产
出高质量 的产品 ,我们在反复 实验中总结出各 项指标 的控制方法 。 【 关键词 】 乳化液 ;油浓度 ;皂化值 ;酸值 ;铁粉
莱钢冷轧生产线由酸洗线 ,轧机 ,罩退 , 平整等各道工序组成。 自2 0 0 6年投产以来 主要产 品为冷轧卷 ,随着市场 竞争 日益激烈 ,提 高冷轧板 的质量 成为首 要问题 。 冷轧化验室主要负责各道工序所用溶液指标的测定 ,为配合生 产线生产出满足客户需求的冷轧卷 ,做好乳化液各参数的测定和控 制尤为重要。 1乳化液油浓度 ( 1 ) 化验室用硫酸在提高温度 的条件下处理乳化液 , 使油、水 分离所测得的油浓度为总油浓度,而实际轧制油的浓度即有效浓度 为:总油浓度 轧制油含量 比例 ( 轧制油含量 比例:实测皂化 值/ 原 油皂化值 ) , 因此所取样 品要求是在轧机正常运行时均匀稳定的乳化 液。 ( 2 ) 取样方法 : 每 次取样 必须取 轧机机架喷射 出的乳化液且是 在轧机开始轧制一小时后或打大循环- -, j , 时后取样,取出的乳化液 要全部装入取样 瓶,摇 晃均匀后 ,从 中取 出 l O O m l作为酸分离法测 浓度的样品。 ( 3 )油浓度控制范围:2 . 5 ~4 . 5 %
铁 含 量= A , B * 5 5 . 8 5 . 1 0 0 0 / C m g / K g
式中:A 一 滴定样 品所消耗 的 E D T A 标准溶液的毫升数 ( m 1 ) B 一印 T A 标准溶液 的摩尔浓度 ( m o l / L ) c 一 测定灰分所用乳化液 的量 ( g )
2 P H值
油的部 分氧化会 是酸 值上升,因此 要降低 乳化液 污染,提高乳化液 洁净度 ,及 时撇 除杂油 ,把使杂油量控制在 4 % 以下 ,使酸值小于 2 0
m g K O H / g 。
6 灰分和铁粉含量 ( 1 )灰分一 用称重差量法测定 ;铁含量一 用E D T A标准溶液滴定 法 测定 。 公式:灰分含量=( W s — w ). 1 0 6 / ( W 2 - W 。 ) m g / K g 式 中 :W t 一 空坩 埚 重 量 ( g ) W 2 - 坩埚加乳化液重量 ( g ) W 3 - 坩埚加灰分重量 ( g )
杂 油 会 造 成 皂化 值 的 降低 。
( 1 )用氯离子滴定仪测定 ,乳化液 中 c 1 ‘ 是酸洗卷板面带来, 乳化液 中 c 1 含量随轧制量的增加而增 加,由 c l ‘ 直径小 ,易穿过油 层腐蚀板 面,造 成板面生锈 。 、 ( 2 ) 当c 1 ’ 含量超过 5 0 p p m 时, 应根据检测值排放部分乳化液 , 及时加水 加油进 行稀释 。 8管理和维护 ( 1 )控制乳化液温度在 5 0 ~6 0 ℃之 间。 ( 2 )保证供 液压力 在 0 . 6 ^ 缸 ) a以上。 ( 3 )设备运 行前,应检查油箱 的液位 ,乳化液温度是否正常 , 所有使用 阀门是 否在正确位置 。 ( 4 ) 设备运 行后, 应检查油箱液位供液压力 ( 净油箱应保持满 格液位 ,污油箱 应保持三分之 二液位 ) 。 。 ( 5 ) 设备运行时,每隔两小时巡检一次。检查项 目: 传动泵及 循环泵、过滤系统、乳化液温度及供液压力,如果不在正常范 围应 及时调整。 ( 6 ) 每班根据乳化液皂化值及酸值情况对污油进行撇油、 加水 、 加油处理,顺序为:撇 油一 加水一 循环一 加 油 ( 7 ) 每班定时开启磁过滤 器,铁粉含 量高时, 可 比平时 多开启