流态化技术在世界熔融还原工艺中的应用
流态固化再生混合料、制备方法及其在坑槽回填中的应用
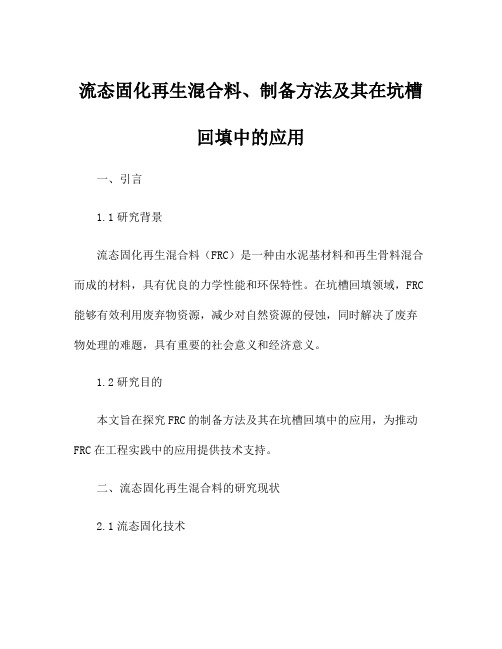
流态固化再生混合料、制备方法及其在坑槽回填中的应用一、引言1.1研究背景流态固化再生混合料(FRC)是一种由水泥基材料和再生骨料混合而成的材料,具有优良的力学性能和环保特性。
在坑槽回填领域,FRC 能够有效利用废弃物资源,减少对自然资源的侵蚀,同时解决了废弃物处理的难题,具有重要的社会意义和经济意义。
1.2研究目的本文旨在探究FRC的制备方法及其在坑槽回填中的应用,为推动FRC在工程实践中的应用提供技术支持。
二、流态固化再生混合料的研究现状2.1流态固化技术流态固化是一种通过控制颗粒材料在流态状态下进行混合和固化的技术,它具有良好的工艺适应性和高效的固化效果,是FRC制备的关键技术。
2.2再生骨料再生骨料是指通过废弃物资源进行再生加工得到的骨料,其来源广泛,可以是建筑废弃材料、废旧混凝土、废弃玻璃等,能够有效减少对原始资源的需求。
2.3 FRC的应用领域FRC在道路工程、地基工程、坑槽回填等领域具有广泛的应用前景,已经在一些工程实践中得到了应用。
三、流态固化再生混合料的制备方法3.1再生骨料处理通过筛分、清洗等方式将再生骨料进行预处理,去除其中的杂质和附着物,提高其质量和稳定性。
3.2流态固化剂的选择选择适宜的水泥基材料和固化剂,并进行配比设计,以保证FRC 具有良好的坚固性和耐久性。
3.3流态固化混合将经过处理的再生骨料和流态固化剂进行混合,并在适宜的条件下进行流态固化,形成FRC产品。
3.4 FRC的养护对制成的FRC产品进行合理的养护,以保证其力学性能和耐久性能。
四、流态固化再生混合料在坑槽回填中的应用4.1 FRC的优势FRC具有优良的力学性能和环保特性,能够有效利用再生资源,减少对原始资源的需求。
4.2坑槽回填的要求坑槽回填是指利用废弃物填埋填方体,其中填方体需要具有一定的强度和稳定性,以保证填埋的安全和效果。
4.3 FRC的应用实例将FRC用于坑槽回填,具有节省成本、减少对原材料需求、环保等显著优势,已经在一些工程实践中得到应用。
直接还原铁工艺技术的对比分析论述

直接还原铁工艺技术的对比分析论述张建国【期刊名称】《资源再生》【年(卷),期】2018(000)002【总页数】5页(P57-61)【作者】张建国【作者单位】北京瀚川鑫冶工程技术有限公司【正文语种】中文在低于矿石融化状态下,通过固态还原,把铁矿石炼制成铁的工艺称作直接还原法,用这种方法生产出的铁也叫作直接还原铁(DRI),由于这种铁保留了失去氧时形成的大量微小气孔,在显微镜下观察形似海绵,所以直接还原铁也称为海绵铁。
直接还原铁是精铁粉在炉内经低温还原形成的低碳多孔状物质,其化学成分稳定,杂质含量少,主要用作电炉炼钢的原料,也可作为转炉炼钢的冷却剂,如果经过二次还原还可供给粉末冶金用。
从上世纪80年代末以来,我国一直宣传推广使用直接还原技术,并对直接还原技术进行了广泛的开发研究,取得了众多成果,为直接还原技术发展奠定了基础。
但是,因铁矿、煤炭、气源等原燃料条件限制,中国直接还原发展的实际成效不大,与钢材、生铁等行业相比还有相当差距。
一、直接还原铁的应用优势直接还原铁生产是指在低于熔化温度之下将铁矿石还原成海绵铁的过程,与传统高炉炼铁方法相比取消了焦炉、烧结等工序,具有流程短、污染小、消耗少,不受炼焦煤短缺影响等优点。
同时海绵铁中硫、磷、硅等有害杂质含量低,有利于电炉冶炼优质纯净钢种。
近年来,由于钢铁产品向小型轻量化、功能高级化、复合化方向发展,因此钢材产品中的非金属材料和有色金属的使用比例在增加,在废钢的破碎分拣过程中,又不能完全有效的剔除非金属和有色金属材料,况且,即使是纯粹完全的黑色废钢料,由于来源不同,化学成分波动也是较大的。
致使加工后的成品入炉废钢的质量很难掌握控制,给电炉炼钢作业带来一定的困难。
如果用一定比例的直接还原铁(30~50%)作为稀释剂与废钢搭配使用,不仅可增加钢的均匀性,还可以改善和提高钢的物理性质,从而达到生产优质钢的目的。
因此,直接还原铁不仅仅是优质废钢的替代品,还是生产优质钢必不可少的高级原料(如天津无缝钢管公司的国外产品设计中就明确要求,必须配置50%的直接还原铁)。
碳吸附赤铁矿粉流态化预还原过程中物性、结构变化规律的研究
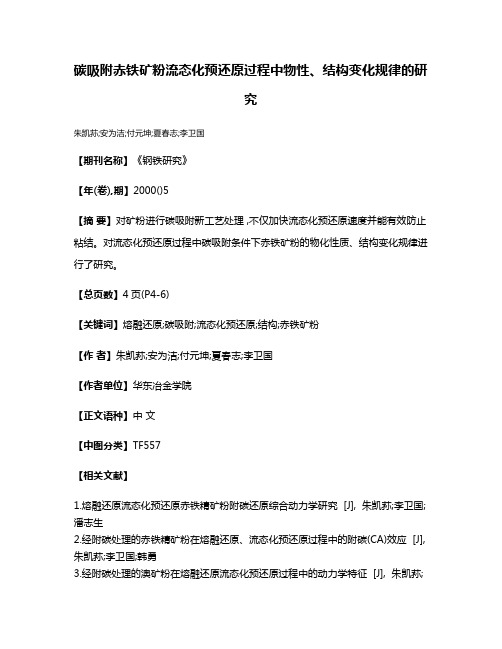
碳吸附赤铁矿粉流态化预还原过程中物性、结构变化规律的研
究
朱凯荪;安为洁;付元坤;夏春志;李卫国
【期刊名称】《钢铁研究》
【年(卷),期】2000()5
【摘要】对矿粉进行碳吸附新工艺处理 ,不仅加快流态化预还原速度并能有效防止粘结。
对流态化预还原过程中碳吸附条件下赤铁矿粉的物化性质、结构变化规律进行了研究。
【总页数】4页(P4-6)
【关键词】熔融还原;碳吸附;流态化预还原;结构;赤铁矿粉
【作者】朱凯荪;安为洁;付元坤;夏春志;李卫国
【作者单位】华东冶金学院
【正文语种】中文
【中图分类】TF557
【相关文献】
1.熔融还原流态化预还原赤铁精矿粉附碳还原综合动力学研究 [J], 朱凯荪;李卫国;潘志生
2.经附碳处理的赤铁精矿粉在熔融还原、流态化预还原过程中的附碳(CA)效应 [J], 朱凯荪;李卫国;韩勇
3.经附碳处理的澳矿粉在熔融还原流态化预还原过程中的动力学特征 [J], 朱凯荪;
李卫国;罗浩
4.熔融还原流态化预还原附碳铁精矿粉的热力学研究 [J], 朱凯荪;陆克从;李卫国
5.熔融还原流态化预还原附碳铁精矿粉的动力学研究 [J], 朱凯荪;陆克从;李卫国因版权原因,仅展示原文概要,查看原文内容请购买。
流态化还原炼铁技术

流态化还原炼铁技术流态化(fluidization)是一种由于流体向上流过固体颗粒堆积的床层而使得固体颗粒具有一般流体性质的物理现象,是现代多相相际接触的工程技术。
使用流态化技术的流化床反应器因具有相际接触面积大,温度、浓度均匀,传热传质条件好,运行效率高等优点而应用于现代工业生产。
高炉炼铁技术在矿产资源受限和环保压力增大等形势下,将面临着前所未有的挑战。
铁矿石对外依存度过高、铁矿石粒度越来越小和焦炭资源枯竭等状况,迫使人们加快步伐探索改进或替代高炉工艺的非高炉型炼铁工艺。
以气固流态化还原技术为代表的非高炉炼铁工艺逐步受到重视。
新工艺的建立和发展需要理论研究作为支撑。
目前国内对于流态化还原炼铁过程中的气固两相流规律的认识还不够深入,特别是对不同属性铁矿粉的流态化特性、不同操作条件下的流态化还原特性,以及反应器结构对流态化还原过程的影响等相关研究还不够充分,基于流态化还原技术的新工艺要成熟应用于大规模工业生产还有明显距离。
发展流态化技术须重视基础研究流态化技术可以把固体散料悬浮于运动的流体之中,使颗粒与颗粒之间脱离接触,从而消除颗粒间的内摩擦现象,使固体颗粒具有一般流体的特性,以期得到良好的物理化学条件。
流态化技术很早就被引入冶金行业,成为非高炉炼铁技术气基还原流程中的一类重要工艺。
流态化技术在直接还原炼铁过程中主要有铁矿粉磁化焙烧、粉铁矿预热和低度预还原、生产直接还原铁的冶金功能。
我国从上世纪50年代后期开始流态化炼铁技术的研究。
1973年~1982年,为了开发攀枝花资源,我国进行了3次流态化还原综合回收钒钛铁的试验研究。
中国科学院结合资源特点对贫铁矿、多金属共生矿的综合利用,开展了流态化还原过程和设备的研究;钢铁研究总院于2004年提出低温快速预还原炼铁方法(FROL TS),并随后对工艺流程进行了探索,取得一定效果。
除此之外,还有针对铁矿及铁氧化物微粉的低温还原特性的研究,探索了小粒径矿粉进行流态化还原的技术特点。
熔融还原工艺

熔融还原工艺熔融还原工艺是一种常用于金属冶炼和废物处理的技术。
它通过在高温下将金属或废物加热至熔点,然后添加还原剂,使有害物质被还原为无害物质,同时将目标金属分离出来。
这种工艺有助于资源的回收利用和环境的保护。
熔融还原工艺的基本原理是利用高温下物质的熔融性和还原性。
在高温下,金属或废物中的有害物质可以被还原为无害物质。
为了实现这个过程,通常需要添加还原剂。
还原剂是一种能够将有害物质还原为无害物质的物质,常用的还原剂有焦炭、燃料和还原气体等。
熔融还原工艺的应用非常广泛,主要包括金属冶炼和废物处理两个方面。
在金属冶炼中,熔融还原工艺可以用来分离出目标金属,并去除杂质。
例如,熔融还原工艺可以用于从废旧电子产品中提取有价金属,如金、银和铜等。
同时,这种工艺还可以用于冶炼废旧钢铁,将其还原为可再利用的原材料。
在废物处理方面,熔融还原工艺可以将废物中的有害物质转化为无害物质,并分离出有价值的物质。
例如,废电池中的有害重金属可以通过熔融还原工艺被还原为无害的物质,并可以回收利用。
另外,熔融还原工艺还可以用于处理含有有机物的废物,将有机物还原为无害的气体和灰渣。
熔融还原工艺的优点是可以高效地分离出目标金属,并处理废物中的有害物质。
与传统的冶炼和废物处理方法相比,熔融还原工艺具有以下优势:1. 高效性:熔融还原工艺可以在较短的时间内将金属分离出来,并将有害物质转化为无害物质,提高了资源的回收利用率和废物处理效率。
2. 环保性:熔融还原工艺能够有效地处理废物中的有害物质,减少对环境的污染。
3. 经济性:熔融还原工艺可以回收有价值的金属,并将废物转化为可再利用的原材料,节约了资源和能源。
然而,熔融还原工艺也存在一些挑战和限制。
首先,高温下的操作需要耗能,并且对设备的要求较高,增加了成本。
其次,熔融还原过程中产生的废气和废渣需要进行处理和处置,否则可能对环境造成污染。
此外,对于一些特殊的废物,熔融还原工艺可能无法完全将其转化为无害物质,仍然需要其他处理方法。
钢铁脱碳——氢基流态化粉矿还原(HYFOR)
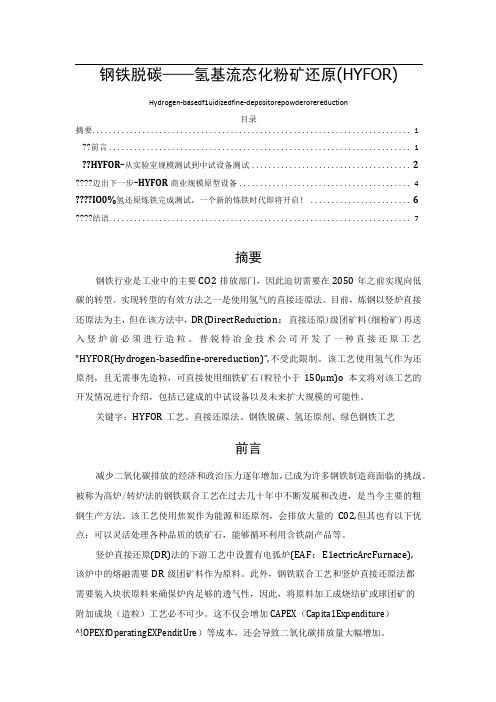
钢铁脱碳——氢基流态化粉矿还原(HYFOR)Hydrogen-basedf1uidizedfine-depositorepowderorereduction目录摘要 (1)前言 (1)HYFOR-从实验室规模测试到中试设备测试 (2)迈出下一步-HYFOR商业规模原型设备 (4)IO0%氢还原炼铁完成测试,一个新的炼铁时代即将开启! (6)结语 (7)摘要钢铁行业是工业中的主要CO2排放部门,因此迫切需要在2050年之前实现向低碳的转型。
实现转型的有效方法之一是使用氢气的直接还原法。
目前,炼钢以竖炉直接还原法为主,但在该方法中,DR(DirectReduction:直接还原)级团矿料(细粉矿)再送入竖炉前必须进行造粒。
普锐特冶金技术公司开发了一种直接还原工艺"HYFOR(Hydrogen-basedfine-orereduction)”,不受此限制。
该工艺使用氢气作为还原剂,且无需事先造粒,可直接使用细铁矿石(粒径小于150μm)o本文将对该工艺的开发情况进行介绍,包括已建成的中试设备以及未来扩大规模的可能性。
关键字:HYFOR工艺、直接还原法、钢铁脱碳、氢还原剂、绿色钢铁工艺前言减少二氧化碳排放的经济和政治压力逐年增加,已成为许多钢铁制造商面临的挑战。
被称为高炉/转炉法的钢铁联合工艺在过去几十年中不断发展和改进,是当今主要的粗钢生产方法。
该工艺使用焦炭作为能源和还原剂,会排放大量的C02,但其也有以下优点:可以灵活处理各种品质的铁矿石,能够循环利用含铁副产品等。
竖炉直接还原(DR)法的下游工艺中设置有电弧炉(EAF:E1ectricArcFurnace),该炉中的熔融需要DR级团矿料作为原料。
此外,钢铁联合工艺和竖炉直接还原法都需要装入块状原料来确保炉内足够的透气性,因此,将原料加工成烧结矿或球团矿的附加成块(造粒)工艺必不可少。
这不仅会增加CAPEX(Capita1Expenditure)^!OPEXfOperatingEXPenditUre)等成本,还会导致二氧化碳排放量大幅增加。
还原精炼条件下炉渣的泡沫化
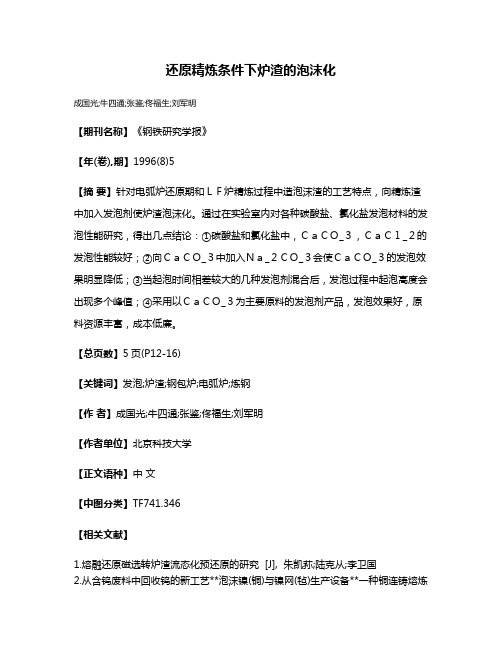
还原精炼条件下炉渣的泡沫化
成国光;牛四通;张鉴;佟福生;刘军明
【期刊名称】《钢铁研究学报》
【年(卷),期】1996(8)5
【摘要】针对电弧炉还原期和LF炉精炼过程中造泡沫渣的工艺特点,向精炼渣中加入发泡剂使炉渣泡沫化。
通过在实验室内对各种碳酸盐、氯化盐发泡材料的发泡性能研究,得出几点结论:①碳酸盐和氯化盐中,CaCO_3,CaCl_2的发泡性能较好;②向CaCO_3中加入Na_2CO_3会使CaCO_3的发泡效果明显降低;③当起泡时间相差较大的几种发泡剂混合后,发泡过程中起泡高度会出现多个峰值;④采用以CaCO_3为主要原料的发泡剂产品,发泡效果好,原料资源丰富,成本低廉。
【总页数】5页(P12-16)
【关键词】发泡;炉渣;钢包炉;电弧炉;炼钢
【作者】成国光;牛四通;张鉴;佟福生;刘军明
【作者单位】北京科技大学
【正文语种】中文
【中图分类】TF741.346
【相关文献】
1.熔融还原磁选转炉渣流态化预还原的研究 [J], 朱凯荪;陆克从;李卫国
2.从含钨废料中回收钨的新工艺**泡沫镍(铜)与镍网(毡)生产设备**一种铜连铸熔炼
炉的保温炉密封炉盖**紫杂铜一步电解生产阴极铜的方法**粗铜无氧化掺氮还原火法精炼工艺 [J],
3.高碱度转炉渣碳热还原时熔渣泡沫化控制及消除技术 [J], 彭绍强;刘铮
4.含钛高炉渣碳热还原时熔渣泡沫化原因分析 [J], 黄家旭;龙盘忠
5.电炉粉尘造泡沫渣过程中FeO的还原与炉渣发泡行为 [J], 王敏;陈伟庆
因版权原因,仅展示原文概要,查看原文内容请购买。
流态化工程原理

流态化工程原理流态化工程原理是指通过控制流体的运动状态和物理特性来实现特定的工艺目标或应用需求的一种技术。
它在化工、石油、能源、环保等领域中广泛应用,为工业生产提供了重要的技术支持和创新方向。
流态化工程原理的基本概念是将固体颗粒悬浮于气体或液体介质中,通过调节流体的速度和流态化剂的添加来改变固体颗粒的运动状态。
在流态化状态下,固体颗粒的运动呈现出流体的特性,具有类似于液体的流动性和类似于气体的均匀性。
这种特性使得流态化工程成为一种高效的物料搬运和反应控制技术。
流态化工程原理的核心是流体的运动和相互作用。
在流态化过程中,流体中的颗粒受到气体或液体的作用力,呈现出不同的运动状态,如床层流动、颗粒间的碰撞和混合等。
这些运动状态对于实现特定的工艺目标至关重要,如颗粒的分离、搬运和反应等。
流态化工程原理的应用范围非常广泛。
在化工领域,流态化工程可以用于固体颗粒的分离、干燥、反应和催化等过程。
例如,在石化工业中,流态化工程可以用于催化剂的制备和石油的加工。
在环保领域,流态化工程可以用于废气和废水的处理和净化。
在能源领域,流态化工程可以用于燃煤和生物质的燃烧,以及核能的利用等。
流态化工程原理的核心是控制流体的运动和相互作用。
通过调节流体的速度和流态化剂的添加,可以改变固体颗粒的运动状态,从而实现特定的工艺目标。
流态化工程既有理论研究,又有实际应用。
在理论研究方面,流态化工程涉及流体力学、热力学和物质传递等多个学科的知识。
在实际应用方面,流态化工程需要考虑工艺流程、设备设计和操作控制等多个方面的问题。
流态化工程原理的研究和应用对于推动工业生产的发展具有重要意义。
它可以提高物料搬运和反应过程的效率,减少能源和原材料的消耗,降低环境污染和废物排放。
同时,流态化工程也为新材料的研发和应用提供了技术支持和创新思路。
通过研究流态化工程原理,我们可以更好地理解和掌握流体的运动规律和相互作用机制,为工业生产的可持续发展做出贡献。
- 1、下载文档前请自行甄别文档内容的完整性,平台不提供额外的编辑、内容补充、找答案等附加服务。
- 2、"仅部分预览"的文档,不可在线预览部分如存在完整性等问题,可反馈申请退款(可完整预览的文档不适用该条件!)。
- 3、如文档侵犯您的权益,请联系客服反馈,我们会尽快为您处理(人工客服工作时间:9:00-18:30)。
在20世纪五六十年代,流态化直接还原技术开始工业应用,典型的工艺有菲尼克斯(FINEX)工艺(采用多级串联流化床)、芬麦特(FINMET)工艺(采用多级串联流化床)、黑斯麦尔特(HIsmelt)工艺(采用循环流化床)、瑟科瑞德(Circored)工艺(采用循环流化床与鼓泡流化床的组合)、迪欧斯(DIOS)工艺。
流态化还原的特点是直接利用粉矿,以气体作还原剂,反应在气-固两相中进行。
矿粉在固态下直接还原成金属铁,接着在其他高温设备中熔融炼铁或直接粉末冶金。
相对其他的技术,流化床处理粉矿的成本较低,具有原料和设备利用率较高、热交换效率高等诸多优势,而且高温流化床反应器在化工等领域已广泛应用,也可以为流化床还原粉铁矿的工艺提供良好的借鉴。
1.流态化技术在熔融还原工艺中的应用
流化床在直接还原炼铁过程中有磁化焙烧生产铁精矿粉、预热和低度预还原粉铁矿、生产直接还原铁等冶金功能。
1)磁化焙烧铁精矿粉
磁化焙烧是将Fe2O3在还原气氛中焙烧得到磁化性的Fe3O4,经过磁选使Fe3O4与杂质分离,得到品位高的铁精矿。
1973年~1982年,为了开发攀枝花资源,我国进行了3次流态化还原综合回收钒钛铁的试验研究。
3次的试验结果表明,我国的流态化还原法在理论上是可靠的,工艺上是可行的,主体设备上是成功的,从而为向工业化过渡创造了条件。
2)预热和低度预还原粉铁矿
流化床预热和低度预还原粉铁矿工艺中的典型代表是HIsmelt 工艺和DIOS工艺。
HIsmelt工艺正处于工业化开发阶段。
矿粉经过整粒筛分除去大颗粒矿粉后经皮带输送到矿石预热器中进行预热和初级预还原。
整粒筛分后的粒度小于6mm,预热后的矿粉温度可达700℃~800℃,预还原度为10%~11%,处理后的热矿粉装入热矿仓等待喷吹。
为了缓解铁浴炉的压力,可提高预热粉铁矿的还原度,但是粉铁矿只经一级循环流化床预热还原,其还原度一般不超过25%。
DIOS工艺的预还原采用快速流化床与沸腾流化床组合的复合型流化床系统。
粉铁矿在一级预热流化床中预热到500℃~600℃,预还原度达到8%~9%;在二级流化床中粉铁矿温度升高到约780℃,还原度约为27%。
粗粉还原以沸腾床为主,细粉还原则在循环床中进行,且细粉还原炉在较高的炉压下工作,煤气流速相对缓慢,预还原仍在浮氏体范围内。
实践结果表明,低度预还原的DIOS未获得成功,也未实现工业应用。
3)直接还原生产DRI或HBI
目前,最常用的优质废钢的替代料是直接还原铁(DRI)和热压块铁(HBI)。
流化床是生产直接还原铁的常用装备,典型的工艺有FINEX (预还原预热炉料)、Circored和FINMET工艺等。
FINMET是工业应用较成功的工业装置,该工艺可直接用粒度小于12mm的粉铁矿,其生产装置由四级流化床顺次串联,逐级预热和还原粉铁矿。
第一级流化床反应器内温度约为550℃,最后一级流化床反应器内温度约为800℃,析碳反应主要发生在此流化床反应器内。
反应器内的压力保持在1.1MPa~1.3MPa。
产品的金属化率为91%~
92% ,碳质量分数为0.5%~3.0% ,产品热压块后外销或替代优质废钢。
流化床反应器顶部煤气与天然气蒸汽重整炉的新鲜煤气混合后作为还原煤气,混合煤气经过一个CO2脱除系统,在还原煤气炉内加热到830℃~850℃之后被送入流化床还原反应器。
新鲜煤气是为了补偿还原过程中消耗的CO和H2。
Circored工艺流程如下:粉铁矿进入初始阶段的循环流化床反应器之前,在循环流化床预热器中被干燥预热到850℃~900℃。
预还原的金属化率约为70%,粉料流入流化床反应器进行终还原,反应后其金属化率为93%~96%。
流化床被分隔以利于控制。
通过加热矿和循环气体为吸热还原反应提供热能。
整个还原工艺的绝对压力为4个大气压,还原温度在630℃~650℃。
预还原阶段的停留时间短,气体流速高;终还原的停留时间长,气体流速低。
从终还原炉产出的还原矿粉在700℃下被压成块(HBI),所以有利于安全贮存和运输。
FINEX工艺由三级流化床反应器串联组成,可以直接使用粒度小于8mm的粉铁矿,生产较高预还原度的DRI供熔化气化炉冶炼铁水。
粉铁矿和粉状熔剂(石灰石和白云石等)以及焦炭粉的混合炉料经干燥后,由垂直传送带和锁斗仓添加到三级流化床反应器系统。
炉顶煤气经除尘净化后约41%通过加压变压吸附去除CO2,使煤气中的CO2
从33%降到3%,然后返回一级反应器作为补充还原气体循环利用,有效地利用工艺内部能量循环,突破了FINMET工艺需要天然气的能源限制,降低了燃料比。
FINEX工艺的金属化率控制在50%~70%,有效地控制了流化床的黏结,扩大了流化床的产能,与有7米厚半焦床的熔化气化炉匹配更佳。
4)几种流化床处理粉铁矿工艺的比较
采用中高预还原度的FINEX、FINMET和Circored工艺都已经工业化,而低预还原度的HIsmelt和DIOS工艺处在半工业化和小规模工厂试验阶段。
上述几种工艺中预热粉矿多采用循环流化床床型,还原粉矿多使用鼓泡流化床。
除HIsmelt工艺外,其他工艺均采用多级流化床匹配运行,以此提高煤气利用率和增强工艺可行性。
2.熔融还原工艺中采用流态化技术的思考
现有的流态化直接还原工艺中FINEX用于熔融还原的工业化最为成功,浦项制铁把FINMET与克瑞克斯(Corex)这两种成熟的工艺
嫁接在一起,对这两种工艺的参数进行了优化。
这一点非常值得参考和借鉴,对开发熔融还原新工艺有重要的现实意义。
HIsmelt和DIOS工艺因预还原度较低而造成终还原炉负担过重,导致耐火材料侵蚀过快、燃料消耗高和仅能够维持间歇式冶炼等问题,难以实现工业化连续生产。
在开发和设计流态化预热预还原系统时,必须考虑合理的铁浴终还原系统的冶炼强度和还原能力。
在两步法熔融还原工艺中,流态化预还原和预热粉铁矿应达到80%左右的预还原度和800℃左右的温度。
高的预还原度虽能减轻铁浴炉的还原压力,但容易使流化床产生黏结和失流,影响流化床的操作稳定性。
流态化预热预还原系统可以直接高效地利用粉铁矿资源,省去造块(球)和烧结工序,减轻了环境污染,降低了生产成本,同时这也是实现高效熔融还原炼铁工艺的有效途径。
流化状态的选择要依据生产工艺的实际要求而定,可以采用同种床型的多级串联或者多种床型的组合系统。
在设计床型时必须考虑高温下粉矿和还原气体的性质及其反应特性。
适度降低粉铁矿的预还原度,能为流化床创造宽松的操作条件,解决或缓解黏结和失流等问题。
另外,将粉铁矿预热,能缓解铁浴终还原炉的热负荷强度,提高整个熔融还原工艺的熔炼效率并降低能耗。
煤气改质的冶金功能定位在调节和变换铁浴终还原炉产出的高
温煤气和流态化预热预还原系统的炉顶煤气。
如何综合利用产生煤气所携带的物理热和炉顶煤气的物理余热,直接关系到能否降低工艺系统的能耗。
煤气改质系统解决了高温煤气物理余热的利用问题。
煤气改质是利用高温煤气携带的物理余热作为改质热源,将物理热转化为煤气的化学能,提高了煤气的还原势和系统能量利用率。
煤气(富氢)改质能为预还原工序提供合格的还原煤气,提高预还原操作的工作效率,更好地匹配二步法熔融还原工艺中预还原和终还原的操作。
另外,循环利用流态化预还原的炉顶煤气的化学能和物理热,能够提高预还原炉料的产能,并进一步降低工艺的燃料消耗,同时也提高了铁浴终还原炉的生产率并延长了其寿命。
选择铁浴炉作为终还原系统的装备,一方面选用非焦煤作为燃料和还原剂,可以扩大冶金工业的能源适用性;另一方面直接使用高温(800℃左右)、较高预还原度(80%)的粉矿为炉料,能省去压块工序,节约成本。
铁浴熔池将熔解喷入的煤粉、矿粉和熔剂,并迅速进行还原反应,产生的气体对熔池进行强烈搅拌,能促进矿粉的快速还原,确保渣中的FeO处于较低的水平,减缓耐火材料的侵蚀,使其达到工业化生产要求。
溶解碳还原FeO比固体碳还原FeO高出1个~2个数量级,可以提高铁浴终还原炉的生产效率。
参考上述工艺,考虑到终还原产生煤气的温度和还原势与预还原工序的匹配,以及终还原炉的冶炼强度等因素,铁浴终还原炉的二次燃烧率控制在20%左右应该可行。
熔融还原工艺的燃料消耗远高于高炉流程,其最终能耗和操作成本在很大程度上依赖于尾气的综合利用。
输出煤气经煤气改质后可用于还原铁矿石生产碳化铁和海绵铁,或作为化工原料生产二甲醚,也可以利用输出煤气直接发电。
经过上述分析和思考,借鉴和参考现有的流态化熔融还原流程,提出一种采用流化床处理粉铁矿的熔融还原炼铁新工艺流程,包括流态化预热预还原系统、煤气改质系统、铁浴终还原系统和综合利用系统4个部分。
3.结语
第一,在炼铁工艺中流态化的应用有磁化焙烧生产铁精矿粉、预热和低度预还原粉铁矿和生产直接还原铁,典型的流化床处理粉铁矿的工艺流程有FINEX、FINMET、Circored和HIsmelt等。
第二,目前主流的熔融还原炼铁工艺流程均为二步法,采用中高预还原度和低二次燃烧率(Corex和FINEX已经工业化)的工艺可行性更佳,开发新的炼铁工艺流程理应遵循这一原则。
第三,新的炼铁流程中设有煤气改制环节,使预还原和终还原工序更加匹配和顺行。