熔融还原
转炉熔融还原炼铁工艺探讨
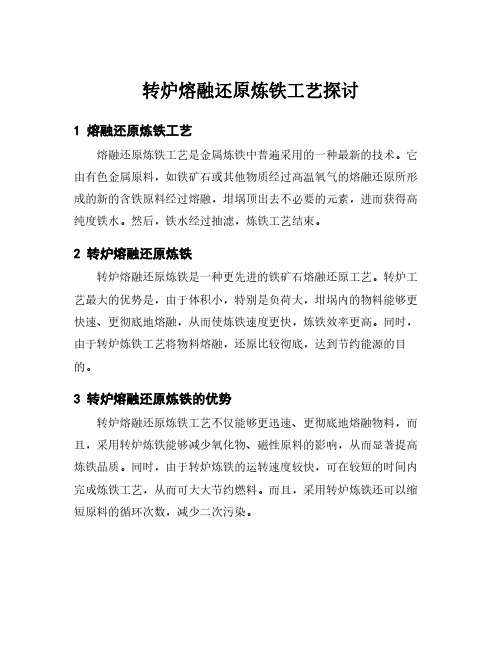
转炉熔融还原炼铁工艺探讨1熔融还原炼铁工艺熔融还原炼铁工艺是金属炼铁中普遍采用的一种最新的技术。
它由有色金属原料,如铁矿石或其他物质经过高温氧气的熔融还原所形成的新的含铁原料经过熔融,坩埚顶出去不必要的元素,进而获得高纯度铁水。
然后,铁水经过抽滤,炼铁工艺结束。
2转炉熔融还原炼铁转炉熔融还原炼铁是一种更先进的铁矿石熔融还原工艺。
转炉工艺最大的优势是,由于体积小,特别是负荷大,坩埚内的物料能够更快速、更彻底地熔融,从而使炼铁速度更快,炼铁效率更高。
同时,由于转炉炼铁工艺将物料熔融,还原比较彻底,达到节约能源的目的。
3转炉熔融还原炼铁的优势转炉熔融还原炼铁工艺不仅能够更迅速、更彻底地熔融物料,而且,采用转炉炼铁能够减少氧化物、磁性原料的影响,从而显著提高炼铁品质。
同时,由于转炉炼铁的运转速度较快,可在较短的时间内完成炼铁工艺,从而可大大节约燃料。
而且,采用转炉炼铁还可以缩短原料的循环次数,减少二次污染。
4转炉熔融还原炼铁的不足转炉in熔融还原炼铁还存在一些缺陷。
首先,转炉运行需要较大的资金投入,这在短期内可能无法收回成本。
其次,因为转炉熔融还原炼铁速度较快,节约能源,但同时也需要更多的处理能力,从而增加系统功耗。
此外,转炉炼铁工艺存在一些复杂的技术要素,操作者需要掌握技术,以保证生产的安全可操作性。
5结论转炉熔融还原炼铁是金属炼铁工艺中一种重要的技术,具有快速熔融、减少耗燃、铁水品质好等优势。
但是,也存在一些不足,投入成本高,处理能力需要增加,技术也非常复杂。
因此,要想更高效地使用转炉熔融还原炼铁,需要精心选择原料,优化运行参数,加强技术的掌握,以确保工艺的有效运行。
熔融还原法炼锌
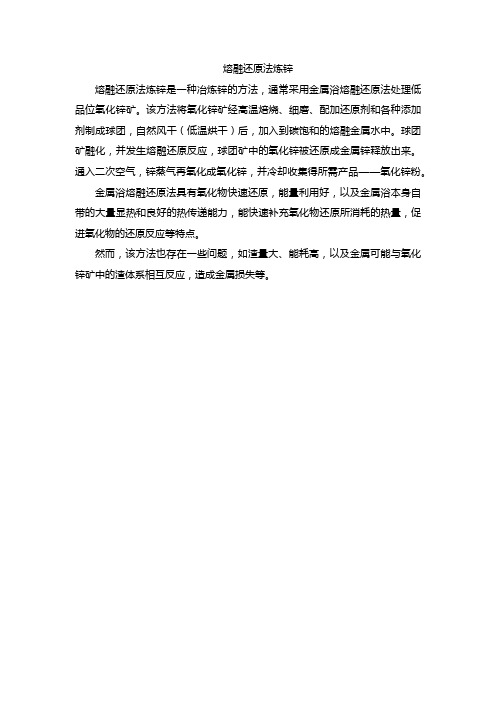
熔融还原法炼锌
熔融还原法炼锌是一种冶炼锌的方法,通常采用金属浴熔融还原法处理低品位氧化锌矿。
该方法将氧化锌矿经高温焙烧、细磨、配加还原剂和各种添加剂制成球团,自然风干(低温烘干)后,加入到碳饱和的熔融金属水中。
球团矿融化,并发生熔融还原反应,球团矿中的氧化锌被还原成金属锌释放出来。
通入二次空气,锌蒸气再氧化成氧化锌,并冷却收集得所需产品——氧化锌粉。
金属浴熔融还原法具有氧化物快速还原,能量利用好,以及金属浴本身自带的大量显热和良好的热传递能力,能快速补充氧化物还原所消耗的热量,促进氧化物的还原反应等特点。
然而,该方法也存在一些问题,如渣量大、能耗高,以及金属可能与氧化锌矿中的渣体系相互反应,造成金属损失等。
熔融还原炼铁工艺
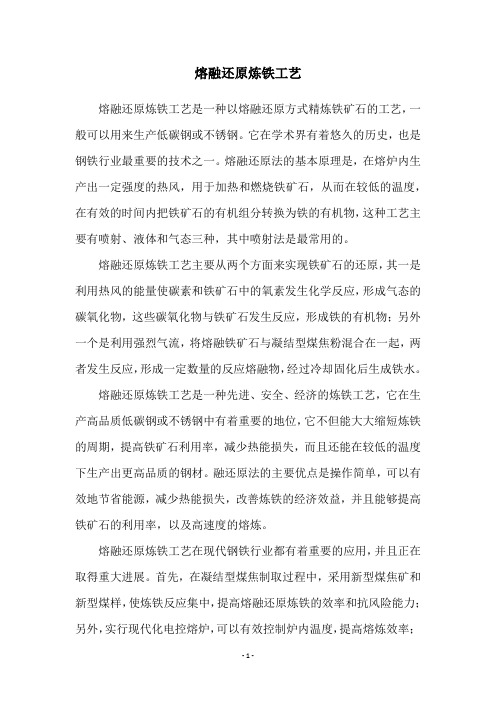
熔融还原炼铁工艺熔融还原炼铁工艺是一种以熔融还原方式精炼铁矿石的工艺,一般可以用来生产低碳钢或不锈钢。
它在学术界有着悠久的历史,也是钢铁行业最重要的技术之一。
熔融还原法的基本原理是,在熔炉内生产出一定强度的热风,用于加热和燃烧铁矿石,从而在较低的温度,在有效的时间内把铁矿石的有机组分转换为铁的有机物,这种工艺主要有喷射、液体和气态三种,其中喷射法是最常用的。
熔融还原炼铁工艺主要从两个方面来实现铁矿石的还原,其一是利用热风的能量使碳素和铁矿石中的氧素发生化学反应,形成气态的碳氧化物,这些碳氧化物与铁矿石发生反应,形成铁的有机物;另外一个是利用强烈气流,将熔融铁矿石与凝结型煤焦粉混合在一起,两者发生反应,形成一定数量的反应熔融物,经过冷却固化后生成铁水。
熔融还原炼铁工艺是一种先进、安全、经济的炼铁工艺,它在生产高品质低碳钢或不锈钢中有着重要的地位,它不但能大大缩短炼铁的周期,提高铁矿石利用率,减少热能损失,而且还能在较低的温度下生产出更高品质的钢材。
融还原法的主要优点是操作简单,可以有效地节省能源,减少热能损失,改善炼铁的经济效益,并且能够提高铁矿石的利用率,以及高速度的熔炼。
熔融还原炼铁工艺在现代钢铁行业都有着重要的应用,并且正在取得重大进展。
首先,在凝结型煤焦制取过程中,采用新型煤焦矿和新型煤样,使炼铁反应集中,提高熔融还原炼铁的效率和抗风险能力;另外,实行现代化电控熔炉,可以有效控制炉内温度,提高熔炼效率;此外,引进新型还原剂也可以改善熔融还原炼铁的效果。
总的来说,熔融还原炼铁工艺是当前钢铁行业中最重要的技术之一,它不仅能够节省能源,改善经济效益,而且还能生产出更高品质的钢材。
然而,熔融还原炼铁过程中还有一些不足之处,如反应温度过高、燃料消耗过多等问题,这些问题需要通过合理的技术手段进行研究和改进,以保证钢铁行业的正常生产和运行。
熔融还原工艺

熔融还原工艺熔融还原工艺是一种常用于金属冶炼和废物处理的技术。
它通过在高温下将金属或废物加热至熔点,然后添加还原剂,使有害物质被还原为无害物质,同时将目标金属分离出来。
这种工艺有助于资源的回收利用和环境的保护。
熔融还原工艺的基本原理是利用高温下物质的熔融性和还原性。
在高温下,金属或废物中的有害物质可以被还原为无害物质。
为了实现这个过程,通常需要添加还原剂。
还原剂是一种能够将有害物质还原为无害物质的物质,常用的还原剂有焦炭、燃料和还原气体等。
熔融还原工艺的应用非常广泛,主要包括金属冶炼和废物处理两个方面。
在金属冶炼中,熔融还原工艺可以用来分离出目标金属,并去除杂质。
例如,熔融还原工艺可以用于从废旧电子产品中提取有价金属,如金、银和铜等。
同时,这种工艺还可以用于冶炼废旧钢铁,将其还原为可再利用的原材料。
在废物处理方面,熔融还原工艺可以将废物中的有害物质转化为无害物质,并分离出有价值的物质。
例如,废电池中的有害重金属可以通过熔融还原工艺被还原为无害的物质,并可以回收利用。
另外,熔融还原工艺还可以用于处理含有有机物的废物,将有机物还原为无害的气体和灰渣。
熔融还原工艺的优点是可以高效地分离出目标金属,并处理废物中的有害物质。
与传统的冶炼和废物处理方法相比,熔融还原工艺具有以下优势:1. 高效性:熔融还原工艺可以在较短的时间内将金属分离出来,并将有害物质转化为无害物质,提高了资源的回收利用率和废物处理效率。
2. 环保性:熔融还原工艺能够有效地处理废物中的有害物质,减少对环境的污染。
3. 经济性:熔融还原工艺可以回收有价值的金属,并将废物转化为可再利用的原材料,节约了资源和能源。
然而,熔融还原工艺也存在一些挑战和限制。
首先,高温下的操作需要耗能,并且对设备的要求较高,增加了成本。
其次,熔融还原过程中产生的废气和废渣需要进行处理和处置,否则可能对环境造成污染。
此外,对于一些特殊的废物,熔融还原工艺可能无法完全将其转化为无害物质,仍然需要其他处理方法。
熔融还原流程
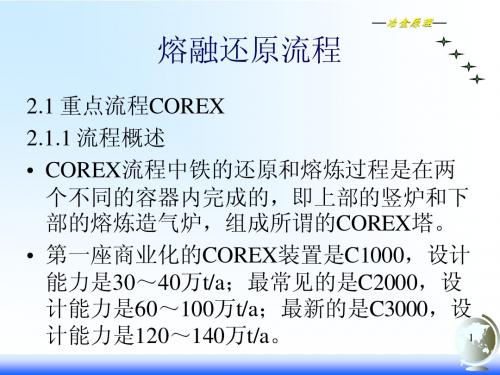
• 对矿石的质量要求与高炉相仿,可使用球团矿、 天然块矿和烧结矿等块状含铁料。冶炼效果以使 用球团矿较佳。 • 入炉矿石的粒度有一定要求。入炉矿以中等的均 匀粒度为佳。 • 矿石还应具有较高的强度和热稳定性,特别是还 原强度。
4
• 对矿石化学成分的要求主要是铁品位、自然碱度和 有害元素含量。 品位较高。使用高品位矿石可获得较低的能耗和较 高的利用系数。COREX要求球团矿品位不低于58%, 天然矿品位不低于55%,烧结矿品位不低于45%。 自然碱度越高越好。 严格控制有害元素的含量。P、S、F、Pb、Zn、As、 K、Na等。
—冶金原理— • COREX竖炉的海绵铁卸料螺旋是COREX的专利之一。 C1000和C2000均使用6个海绵铁卸料螺旋。
12
—冶金原理—
2.1.5 熔炼与造气
• 熔炼与造气是熔融还原流程的基础。COREX的根 本技术就是煤炭流化床熔炼造气技术。 • 煤炭流化床 流化床专利。铁水含C量为2.5~3.5%,含S量为 0.2~0.4%。铁水中未检测出Si,出炉温度为 1300~1350℃。熔炼炉拱顶温度最高为1200℃。除 尘器收得的粉尘量相当高。
—冶金原理—
8
—冶金原理—
• 可见: COREX熔炼造气煤的选择范围是相当宽的。 工业实施应择优选用,一般灰分不应高于25%, 挥发份应在15~36%之间。最佳的熔炼煤灰分 在12%以下,挥发份介于20~30%。 世界范围内的煤种中处于最佳范围的并不多。 我国非焦煤资源丰富,位于可选煤种很多,搭 配出最佳煤种也容易。 熔炼煤对灰分的限制较宽。低挥发分煤种的灰 分可高达30%以上。 9 熔炼煤对挥发分的变化则敏感得多。
—冶金原理—
5
—冶金原理—
熔剂的品种和配比取决于矿石成分、煤比及煤 炭灰分含量与成分,一般以石灰石和白云石为主。 渣中Al 高时,应配入硅石(SiO 渣中Al2O3高时,应配入硅石(SiO2)。
熔融还原炼铁技术

熔融还原炼铁技术熔融还原炼铁技术是一种高效、环保的铁矿石冶炼方法,它在铁矿石中加入还原剂,通过高温熔融反应将铁矿石还原为金属铁。
本文将介绍熔融还原炼铁技术的原理、工艺流程以及其在钢铁工业中的应用。
熔融还原炼铁技术利用高温炉内的化学反应将铁矿石中的氧气去除,从而得到纯净的金属铁。
该技术的核心是还原剂的选择和矿石的熔化。
在炉内加入适量的还原剂,如焦炭或高炉煤气,它们在高温下与铁矿石中的氧气发生反应,生成一氧化碳和二氧化碳。
与此同时,矿石中的其他杂质也会与还原剂发生反应,并被还原为金属态或挥发出去。
通过这些反应,铁矿石中的金属铁被还原出来并熔化成液态。
熔融还原炼铁技术的工艺流程一般包括铁矿石的预处理、炉料的配制、炉内反应和产物处理等步骤。
首先,需要对铁矿石进行破碎、磨矿等预处理,以便提高矿石的反应性和熔化性。
然后,将矿石与还原剂、熔剂等按一定比例混合形成炉料。
炉料制备完成后,将其加入熔炼炉中,并控制炉内温度、气氛等条件,使反应正常进行。
炉内反应结束后,将炉渣和金属铁分离,并进行相应的处理和后续利用。
熔融还原炼铁技术在钢铁工业中具有广泛的应用。
首先,该技术可以利用低品位的铁矿石资源,提高资源利用率。
传统的炼铁方法需要高品位的铁矿石才能保证炉内反应的进行,而熔融还原炼铁技术可以利用低品位的铁矿石,降低原材料成本。
其次,该技术还可以减少环境污染。
传统炼铁方法中产生大量的烟尘、废气和废水,对环境造成严重污染,而熔融还原炼铁技术中炉内反应相对封闭,可以有效控制废气的排放和废水的处理,减少环境负荷。
此外,熔融还原炼铁技术还可以提高炼铁效率和产品质量,增强钢铁企业的竞争力。
熔融还原炼铁技术是一种高效、环保的铁矿石冶炼方法,通过将铁矿石中的氧气去除,得到纯净的金属铁。
该技术具有广泛的应用前景,可以提高资源利用率、减少环境污染,并提高产品质量。
随着新材料、新技术的不断发展,熔融还原炼铁技术将在钢铁工业中发挥更加重要的作用。
熔融还原炼铁技术
熔融还原炼铁技术
熔融还原炼铁技术是一种新型的炼铁技术,它采用了高温熔融还原的方法,将铁矿石还原成铁水,从而实现了高效、低耗、低污染的炼铁过程。
这种技术的出现,不仅提高了炼铁的效率和质量,还有助于减少环境污染和资源浪费。
熔融还原炼铁技术的原理是将铁矿石和还原剂一起放入高温熔炉中,通过还原剂的还原作用,将铁矿石中的氧化铁还原成铁水。
这种技术的优点在于,它能够在高温下将铁矿石中的氧化铁还原成铁水,从而避免了传统炼铁技术中需要大量燃料来加热铁矿石的问题。
此外,熔融还原炼铁技术还能够将炉渣中的铁还原成铁水,从而提高了炼铁的效率和质量。
熔融还原炼铁技术的应用范围非常广泛,它可以用于炼制各种类型的铁合金和钢铁产品。
此外,熔融还原炼铁技术还可以用于处理废钢和废铁,从而实现了资源的再利用和环境的保护。
总的来说,熔融还原炼铁技术是一种非常有前途的炼铁技术,它能够提高炼铁的效率和质量,同时还能够减少环境污染和资源浪费。
随着技术的不断发展和完善,相信熔融还原炼铁技术将会在未来的钢铁生产中发挥越来越重要的作用。
熔融还原炼铁工艺流程
熔融还原炼铁工艺流程朋友们!今天咱们来唠唠熔融还原炼铁的工艺流程。
这流程啊,听起来可能有点复杂,但其实只要咱们一步一步来,就没那么难啦。
首先呢,咱们得有原料准备这个环节。
这原料啊,主要就是铁矿石啦,当然还有一些其他的辅料。
我觉得这一步要特别细心呢!你得把原料挑选好,要是原料质量不好,后面可能就会出问题哦。
不过这挑选原料也不是特别特别严格啦,只要大体上符合要求就行,这个环节可以根据实际情况自行调整一下。
接下来就是把原料送进熔炉里啦。
这熔炉可是个关键的地方!在送进去的时候呢,要注意控制速度和量。
为什么要注意这个呢?因为如果速度太快或者量太大,可能熔炉就会“吃不消”啦!根据我的经验,这个速度和量啊,要慢慢摸索出一个合适的值。
刚开始可能会觉得不好把握,但习惯了就好了。
在熔炉里呢,就开始进行还原反应了。
这个反应过程啊,其实就是把铁矿石里的铁氧化物还原成铁。
这一步很重要啊!我觉得这时候要密切关注熔炉里的各种情况,像温度啊、压力啊这些。
要是这些参数不对,那还原出来的铁的质量可能就不咋地了。
不过呢,具体这些参数要控制在多少,每个工厂或者每个设备可能都有点差别,所以也要根据实际情况来。
然后呢,铁水就会慢慢形成啦。
这时候就快接近成功啦!不过可别大意哦。
铁水形成后,可能还需要进行一些后续的处理,比如说去除杂质之类的。
这一步也不能马虎,毕竟咱们要得到高质量的铁嘛。
小提示:别忘了最后一步哦!最后呢,就是把处理好的铁水收集起来,然后就可以用于后续的加工啦。
这整个流程下来,虽然有不少需要注意的地方,但只要认真对待,多积累经验,就能够顺利完成熔融还原炼铁这个过程啦。
你看,也没有想象中的那么难吧?。
2024年熔融还原铁市场需求分析
2024年熔融还原铁市场需求分析引言熔融还原铁是一种重要的铁合金产品,被广泛应用于钢铁制造过程中。
在过去的几年里,熔融还原铁市场一直保持着良好的发展势头。
本文旨在对熔融还原铁市场的需求进行分析,并探讨对未来市场发展的影响因素。
市场概况市场规模熔融还原铁市场的规模在过去几年持续增长。
根据市场数据,2017年全球熔融还原铁产量约为1000万吨,较2016年增长了10%。
预计到2025年,全球熔融还原铁市场规模将达到1500万吨。
市场分布熔融还原铁市场主要分布在亚太地区、欧洲和北美地区。
亚太地区是全球最大的熔融还原铁市场,其市场规模占全球总量的60%以上。
欧洲和北美地区也有较大的市场份额。
需求分析需求驱动因素1.钢铁产业需求:熔融还原铁是一种理想的钢铁添加剂,可以改善钢材的品质和性能。
随着全球钢铁产量的增长,对熔融还原铁的需求也在增加。
2.环保要求:熔融还原铁相对于传统的铁矿石炼铁方法更环保,减少了废气排放和固体废物的产生。
环境保护法规的加强以及企业的社会责任意识提高,将促使更多企业选择熔融还原铁作为替代产品。
3.原料价格:熔融还原铁的生产成本主要受到铁矿石价格的影响。
铁矿石价格的波动将直接影响熔融还原铁的市场需求。
市场前景展望熔融还原铁市场的前景看好。
在需求驱动因素的影响下,熔融还原铁市场将继续保持稳定增长。
随着环保意识的增强和环保法规的推动,熔融还原铁将逐渐取代传统的炼铁方法。
未来几年内,亚太地区有望成为全球最大的熔融还原铁市场。
结论熔融还原铁市场的需求正在不断增长,并将继续保持良好的发展态势。
钢铁产业的需求、环境保护要求以及原料价格的波动是市场需求的主要驱动因素。
展望未来,市场前景看好,亚太地区有望成为全球最大的熔融还原铁市场。
为了满足市场需求,企业应加强技术创新和产品品质的提升,不断提高竞争力。
熔融还原法竖炉炼铁工艺流程
熔融还原法竖炉炼铁工艺流程下载温馨提示:该文档是我店铺精心编制而成,希望大家下载以后,能够帮助大家解决实际的问题。
文档下载后可定制随意修改,请根据实际需要进行相应的调整和使用,谢谢!并且,本店铺为大家提供各种各样类型的实用资料,如教育随笔、日记赏析、句子摘抄、古诗大全、经典美文、话题作文、工作总结、词语解析、文案摘录、其他资料等等,如想了解不同资料格式和写法,敬请关注!Download tips: This document is carefully compiled by theeditor. I hope that after you download them,they can help yousolve practical problems. The document can be customized andmodified after downloading,please adjust and use it according toactual needs, thank you!In addition, our shop provides you with various types ofpractical materials,such as educational essays, diaryappreciation,sentence excerpts,ancient poems,classic articles,topic composition,work summary,word parsing,copy excerpts,other materials and so on,want to know different data formats andwriting methods,please pay attention!熔融还原法竖炉炼铁工艺是一种较传统的炼铁方法,主要通过竖炉进行。
- 1、下载文档前请自行甄别文档内容的完整性,平台不提供额外的编辑、内容补充、找答案等附加服务。
- 2、"仅部分预览"的文档,不可在线预览部分如存在完整性等问题,可反馈申请退款(可完整预览的文档不适用该条件!)。
- 3、如文档侵犯您的权益,请联系客服反馈,我们会尽快为您处理(人工客服工作时间:9:00-18:30)。
熔融还原炼铁技术分析评估
人们用“有无预还原”将熔融还原分为“一步法”熔融还原和“二步法”熔融还原。
“一步法”熔融还原只有熔态还原,矿石预还原率接近0,是真正意义上的熔融还原炼铁法,如HIsmelt、Romelt、Ausmelt等低预还原率工艺均属于此;而“二步法”熔融还原,即预还原加终还原,如COREX、FINEX工艺等,严格讲“二步法”应该称为还原熔融炼铁法。
COREX工艺
COREX工艺演化了高炉炼铁技术,将高炉从概念的软熔带部分分为两部分。
一部分利用成熟的高炉长寿炉缸技术(包括焦炭床和碳砖结合冷却壁技术)构造成了造气煤炭流化床即熔融气化炉;而另一部分借鉴了成熟的大型MIDREX气基还原技术,构造成了预还原竖炉,使用块煤和块厂炼铁,成功地实现了工业化生产。
COREX的基本工艺流程为:块矿、烧结矿、球团矿或这些原料的块状混合物,通过封闭漏斗系统装入到预还原竖炉中,在原料下行的过程中,被逆向流动的还原气体还原成金属化率约80%~90%的直接还原铁(DRI)。
螺旋卸料器将DRI从预还原竖炉中传送到熔融气化炉中,进行终还原和熔化。
熔融气化炉产生的煤气由于含有煤粉、灰尘和铁尘、CO 和H2等,且温度高于1100℃,不能直接进入预还原竖炉,必须在旋风除尘器中净化,混入冷煤气降温,调整到最佳工作范围800~850℃后作为还原气从下部送入竖式预还原炉。
COREX演化了高炉炼铁技术,取得了商业成功,但同时也继承了高炉炼铁的一些缺点:
1. COREX是典型的炉床法炼铁工艺,与高炉相比,COREX更多地依靠间接还原,间接还原度越高,工艺进行得越容易,难以摆脱料柱透气性问题的困扰。
2. 为保证竖式预还原炉料柱的透性必须使用块矿、烧结矿、球团矿或这些原料的块状混合物,因此必须配有造块设备。
对入炉块状原料的理化性能有很高的要求,从而提高了原料成本。
3. COREX的实践证明,要依靠焦炭床来保护炉缸,稳定生产,就无法摆脱对焦炭的依赖(焦比>10%~20%),尤其是大型化后,焦比会超过200kg/THM。
4. 从熔融气化炉抽出的高温煤气经净化后,从>1100℃降至800~850℃,温度损失了250℃左右,热效率比不上高炉。
5. 虽然使用了全氧冶炼,但按炉缸面积计算的生产率仅为高炉的0.7~0.9。
6. 竖炉预还原炉料的金属化率波动大。
7. 操作影响因素多,在炉体中部的高温区使用了排料布料活动部件,使设备维修成本及热损失增加,个别设备还不够成熟,利用率不高。
8. 在高炉冶炼条件下,采用富氧喷吹有一定的限度,传统高炉更不能采用全氧冶炼。
COREX工艺虽然采用全氧冶炼,但其生产率并不高,根本原因在于,虽然全氧熔炼速率很快,但受到上部竖炉铁矿还原速率的
限制,对于一定产能的COREX熔融还原工艺,要求下部熔融气化炉的操作必须与上部的竖炉铁矿还原情况相匹配,才能达到较好的技术经济指标。
综合分析评价
1. 从工艺角度看,COREX更多依靠间接还原工艺,保留着高炉炼铁工艺的特点;FINEX则把COREX的预还原竖炉改变成多极流化床反应器,可以完全使用粉矿;这两种熔融还原工艺可以说是对高炉的“改良”,只是FINEX的改良程度更大一些。
而HIsmelt则完全摆脱了高炉炼铁工艺概念,是炼铁技术的一种“革命”,可有效解决困扰高炉工艺的料柱透气性问题,是真正意义上的熔融还原技术。
2. 在原燃料资源的取用上,COREX可以使用非焦煤,优于高炉,但还须使用块矿和球团及部分焦炭。
FINEX不仅可用非炼焦煤,而且摆脱了对块状原料的依靠,这一点优于高炉和COREX,只是还需要块煤和粉煤造块。
Hismelt则原燃料全部粉状化,且对原燃料性质无特殊要求,资源面最宽,便于就地取材,并且可使用高磷矿石。
3. 在流程设备上,COREX需要球团与块矿等造块设备和部分焦炭;FINEX使用粉矿和粉煤造块,可以不建烧结、球团、炼焦厂;HIsmelt 完全免除了烧结、球团、炼焦厂投资,也不需要煤造块。
但三种工艺均需配套制氧设备和自备电厂。
4. 在生产成本上,FINEX和Hismelt原料成本相对较低,COREX 和FINEX氧气成本较高。
燃料消耗前两种高于Hismelt,因此生铁成本COREX最高,Hismelt最低,但三种均高于高炉。
5. 从一次性投资看,COREX要高一些,FINEX投资成本会较低,HIsmelt冶炼设备相对单一,三者之中投资最低。
6. 现状与前景。
COREX工艺最成熟,已有数家投入生产,并取得很好的成绩,完全实现了商业化。
FINEX在工艺上优于COREX,但目前仍处在示范工厂试生产阶段,再经过一段时间的调整完善,将具备商业化推广价值,成为COREX的有力竞争者。
Hismelt工艺示范工厂投产较晚,又是一种全新的工艺,估计需要一段时间改进、完善,但因其工艺优点多、投资和生产成本低,一旦成功,其竞争优势比较大。