合成氨生产工艺
合成氨生产工艺流程
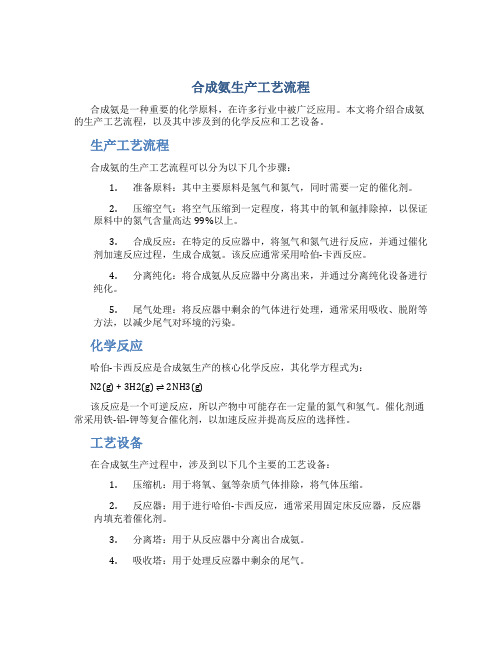
合成氨生产工艺流程合成氨是一种重要的化学原料,在许多行业中被广泛应用。
本文将介绍合成氨的生产工艺流程,以及其中涉及到的化学反应和工艺设备。
生产工艺流程合成氨的生产工艺流程可以分为以下几个步骤:1.准备原料:其中主要原料是氢气和氮气,同时需要一定的催化剂。
2.压缩空气:将空气压缩到一定程度,将其中的氧和氩排除掉,以保证原料中的氮气含量高达99%以上。
3.合成反应:在特定的反应器中,将氢气和氮气进行反应,并通过催化剂加速反应过程,生成合成氨。
该反应通常采用哈伯-卡西反应。
4.分离纯化:将合成氨从反应器中分离出来,并通过分离纯化设备进行纯化。
5.尾气处理:将反应器中剩余的气体进行处理,通常采用吸收、脱附等方法,以减少尾气对环境的污染。
化学反应哈伯-卡西反应是合成氨生产的核心化学反应,其化学方程式为:N2(g) + 3H2(g) ⇌ 2NH3(g)该反应是一个可逆反应,所以产物中可能存在一定量的氮气和氢气。
催化剂通常采用铁-铝-钾等复合催化剂,以加速反应并提高反应的选择性。
工艺设备在合成氨生产过程中,涉及到以下几个主要的工艺设备:1.压缩机:用于将氧、氩等杂质气体排除,将气体压缩。
2.反应器:用于进行哈伯-卡西反应,通常采用固定床反应器,反应器内填充着催化剂。
3.分离塔:用于从反应器中分离出合成氨。
4.吸收塔:用于处理反应器中剩余的尾气。
合成氨是一种十分重要的化学原料,其生产工艺流程麻烦且多种化学反应涉及其中,因此需要一系列的工艺设备来完成整个生产过程。
哈伯-卡西反应是该生产过程的核心反应,通过复合催化剂加速反应过程并提高反应的选择性。
通过合理的工艺流程设计和设备选型,能够实现高效、稳定的合成氨生产。
合成氨的工艺流程
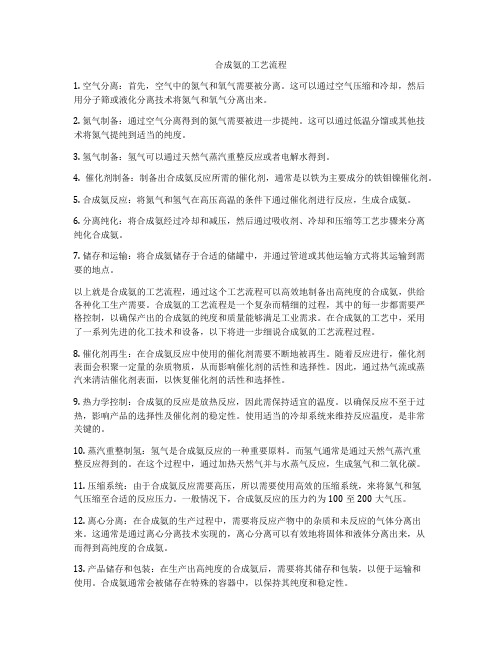
合成氨的工艺流程1. 空气分离:首先,空气中的氮气和氧气需要被分离。
这可以通过空气压缩和冷却,然后用分子筛或液化分离技术将氮气和氧气分离出来。
2. 氮气制备:通过空气分离得到的氮气需要被进一步提纯。
这可以通过低温分馏或其他技术将氮气提纯到适当的纯度。
3. 氢气制备:氢气可以通过天然气蒸汽重整反应或者电解水得到。
4. 催化剂制备:制备出合成氨反应所需的催化剂,通常是以铁为主要成分的铁钼镍催化剂。
5. 合成氨反应:将氮气和氢气在高压高温的条件下通过催化剂进行反应,生成合成氨。
6. 分离纯化:将合成氨经过冷却和减压,然后通过吸收剂、冷却和压缩等工艺步骤来分离纯化合成氨。
7. 储存和运输:将合成氨储存于合适的储罐中,并通过管道或其他运输方式将其运输到需要的地点。
以上就是合成氨的工艺流程,通过这个工艺流程可以高效地制备出高纯度的合成氨,供给各种化工生产需要。
合成氨的工艺流程是一个复杂而精细的过程,其中的每一步都需要严格控制,以确保产出的合成氨的纯度和质量能够满足工业需求。
在合成氨的工艺中,采用了一系列先进的化工技术和设备,以下将进一步细说合成氨的工艺流程过程。
8. 催化剂再生:在合成氨反应中使用的催化剂需要不断地被再生。
随着反应进行,催化剂表面会积聚一定量的杂质物质,从而影响催化剂的活性和选择性。
因此,通过热气流或蒸汽来清洁催化剂表面,以恢复催化剂的活性和选择性。
9. 热力学控制:合成氨的反应是放热反应,因此需保持适宜的温度。
以确保反应不至于过热,影响产品的选择性及催化剂的稳定性。
使用适当的冷却系统来维持反应温度,是非常关键的。
10. 蒸汽重整制氢:氢气是合成氨反应的一种重要原料。
而氢气通常是通过天然气蒸汽重整反应得到的。
在这个过程中,通过加热天然气并与水蒸气反应,生成氢气和二氧化碳。
11. 压缩系统:由于合成氨反应需要高压,所以需要使用高效的压缩系统,来将氮气和氢气压缩至合适的反应压力。
一般情况下,合成氨反应的压力约为100至200大气压。
30万吨合成氨流程
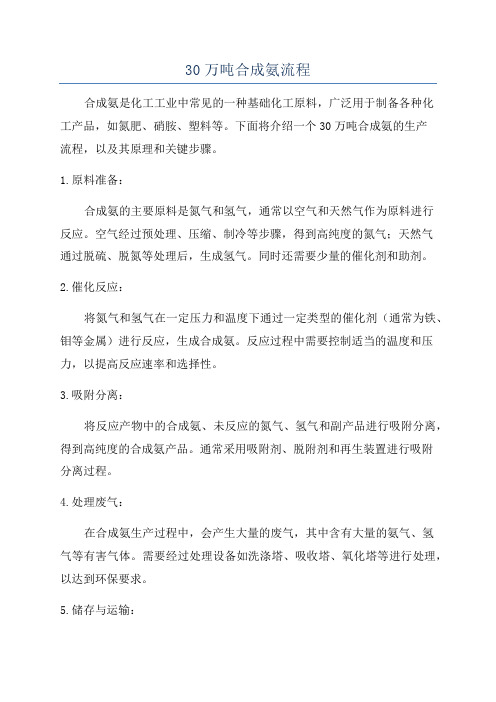
30万吨合成氨流程
合成氨是化工工业中常见的一种基础化工原料,广泛用于制备各种化
工产品,如氮肥、硝胺、塑料等。
下面将介绍一个30万吨合成氨的生产
流程,以及其原理和关键步骤。
1.原料准备:
合成氨的主要原料是氮气和氢气,通常以空气和天然气作为原料进行
反应。
空气经过预处理、压缩、制冷等步骤,得到高纯度的氮气;天然气
通过脱硫、脱氮等处理后,生成氢气。
同时还需要少量的催化剂和助剂。
2.催化反应:
将氮气和氢气在一定压力和温度下通过一定类型的催化剂(通常为铁、钼等金属)进行反应,生成合成氨。
反应过程中需要控制适当的温度和压力,以提高反应速率和选择性。
3.吸附分离:
将反应产物中的合成氨、未反应的氮气、氢气和副产品进行吸附分离,得到高纯度的合成氨产品。
通常采用吸附剂、脱附剂和再生装置进行吸附
分离过程。
4.处理废气:
在合成氨生产过程中,会产生大量的废气,其中含有大量的氨气、氢
气等有害气体。
需要经过处理设备如洗涤塔、吸收塔、氧化塔等进行处理,以达到环保要求。
5.储存与运输:
合成氨产品需要进行储存和运输,通常采用液氨或氨水的形式进行储存,并通过专用容器和管道进行运输。
同时需要注意氨的毒性和易燃性,
做好安全保护。
综上所述,30万吨合成氨的生产流程主要包括原料准备、催化反应、吸附分离、处理废气和储存与运输等步骤。
通过精细控制各个环节的参数
和操作,可以获得高品质的合成氨产品,满足市场需求,并实现生产目标。
同时需要关注环保和安全等方面,确保生产过程安全高效,符合相关法规
标准。
合成氨的工艺流程
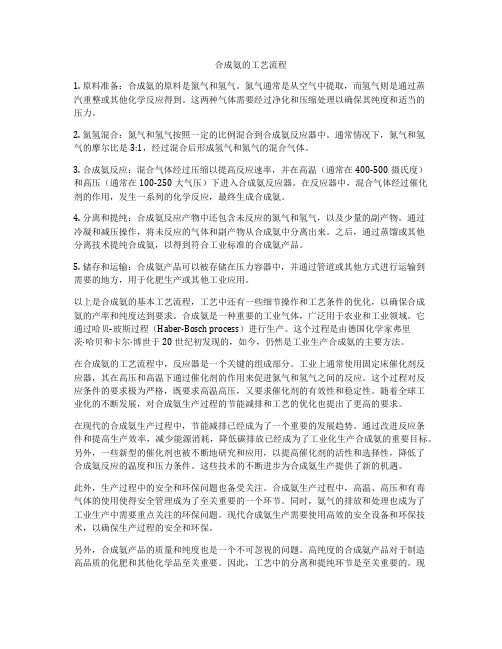
合成氨的工艺流程1. 原料准备:合成氨的原料是氮气和氢气。
氮气通常是从空气中提取,而氢气则是通过蒸汽重整或其他化学反应得到。
这两种气体需要经过净化和压缩处理以确保其纯度和适当的压力。
2. 氮氢混合:氮气和氢气按照一定的比例混合到合成氨反应器中。
通常情况下,氮气和氢气的摩尔比是3:1,经过混合后形成氢气和氮气的混合气体。
3. 合成氨反应:混合气体经过压缩以提高反应速率,并在高温(通常在400-500摄氏度)和高压(通常在100-250大气压)下进入合成氨反应器。
在反应器中,混合气体经过催化剂的作用,发生一系列的化学反应,最终生成合成氨。
4. 分离和提纯:合成氨反应产物中还包含未反应的氮气和氢气,以及少量的副产物。
通过冷凝和减压操作,将未反应的气体和副产物从合成氨中分离出来。
之后,通过蒸馏或其他分离技术提纯合成氨,以得到符合工业标准的合成氨产品。
5. 储存和运输:合成氨产品可以被存储在压力容器中,并通过管道或其他方式进行运输到需要的地方,用于化肥生产或其他工业应用。
以上是合成氨的基本工艺流程,工艺中还有一些细节操作和工艺条件的优化,以确保合成氨的产率和纯度达到要求。
合成氨是一种重要的工业气体,广泛用于农业和工业领域。
它通过哈贝-玻斯过程(Haber-Bosch process)进行生产。
这个过程是由德国化学家弗里茨·哈贝和卡尔·博世于20世纪初发现的,如今,仍然是工业生产合成氨的主要方法。
在合成氨的工艺流程中,反应器是一个关键的组成部分。
工业上通常使用固定床催化剂反应器,其在高压和高温下通过催化剂的作用来促进氮气和氢气之间的反应。
这个过程对反应条件的要求极为严格,既要求高温高压,又要求催化剂的有效性和稳定性。
随着全球工业化的不断发展,对合成氨生产过程的节能减排和工艺的优化也提出了更高的要求。
在现代的合成氨生产过程中,节能减排已经成为了一个重要的发展趋势。
通过改进反应条件和提高生产效率,减少能源消耗,降低碳排放已经成为了工业化生产合成氨的重要目标。
合成氨各工序工艺详细流程

合成氨各工序工艺详细流程合成氨是一种重要的化工原料,广泛用于合成各类农药、肥料、化学品等。
下面将详细介绍合成氨的工序和流程。
合成氨的工艺主要分为三个步骤:气体净化、气体压缩和反应制氨。
1.气体净化:合成氨的原料气体主要有空气和甲烷。
在进入反应装置之前,需要进行气体净化处理。
空气首先经过过滤装置去除微小杂质、灰尘和固体颗粒物。
然后通过制冷装置降低气体温度,使其中的水蒸气凝结成液体,然后被排放。
甲烷通过碳分子筛吸附去除杂质。
这样可以保证反应装置中气体的纯度和稳定性。
2.气体压缩:经过气体净化后的空气和甲烷被分别压缩到一定压力,以满足反应器中的需求。
通常使用压缩机进行压缩,然后将压缩后的气体分别输送到反应器中。
3.反应制氨:反应制氨是整个过程的关键步骤。
通常采用哈柏法(Haber-Bosch)来实现反应制氨。
反应器中,高温高压的空气与甲烷的混合气体通过催化剂床进行催化反应。
常用的催化剂是铁与铁-铝的混合物,也可以加入少量的钾、镁等元素。
反应是一个放热反应,反应温度一般在380-550°C 之间,压力一般在1.7-3.5 MPa之间。
催化剂的存在可以提高反应速率,但也会增加反应的等离子体强度,导致了碳催化剂和蒸汽的选择性降低,产生非氮气杂质。
反应过程中,氮气与氢气进行反应生成氨气。
原料气体经过催化剂床后,反应转化率不高,需要多次通过催化剂床进行反应。
一般采用多级反应器和中间冷却装置,提高氨气的产率和纯度。
经过多级反应后,氨气还需要进行冷却和净化处理,以达到合成氨的纯度要求。
以上是合成氨的工序和流程的详细介绍。
合成氨的过程需要进行气体净化、气体压缩和催化反应制氨。
这个过程需要确保原料气体的纯度和稳定性,通过压缩提高原料气体的压力,催化剂的存在可以提高反应速率和转化率。
经过多级反应,最终得到高纯度的合成氨。
合成氨工艺的不断优化和改进,可以提高合成氨的生产效率和氨气的纯度,降低生产成本。
合成氨与尿素生产工艺

合成氨与尿素生产工艺
一、合成氨及尿素的生产工艺
1、氮气合成工艺:
氮气合成是合成氨工艺的前期工序,它是一种利用多种原料,以固定
压力和温度下的反应,将原料转化为氮气的过程。
氮气合成一般采用流动
态铭朱-必利宁反应器,其原料有天然气和空气,原料由高压力投入反应器,在固定的温度及压力下,产物是氮气和水蒸汽,氮气分别在滤筒及吸
收塔中分离产物,最后通过真空泵和低温冷凝法回收氮气。
2、氨合成工艺:
氨合成是合成氨工艺的核心步骤,若采用的是甲烷加氮反应法合成氨,主要采用连续流体层析塔(FCC)-必利宁反应器,原料有氮气、甲烷和水,先将甲烷和氮气在高压力下投入反应器内,在固定的温度及压力下进行反应,反应产物是氨气和水蒸汽,氨气经过滤筒等分离设备中分离产物,最
后由真空泵及低温冷凝法回收氨气。
3、尿素合成工艺:
尿素合成是合成氨工艺的后期工序,常采用的是氨气合成尿素的方法,主要采用的是热交换反应器,其原料有氨气、二氧化碳和水,氨气和二氧
化碳在高压力下输入反应器,在适当的温度和压力下进行反应,反应产物
是尿素气体,尿素气体经过滤筒及吸收塔中分离产物,最后由真空泵及低
温冷凝法回收尿素气体。
合成氨工艺流程
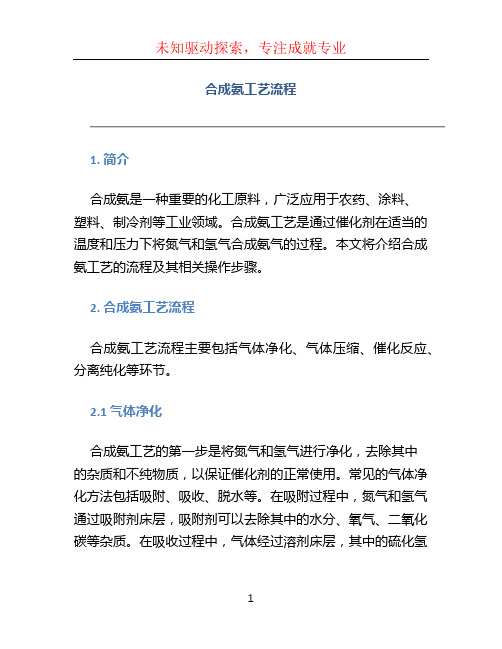
合成氨工艺流程1. 简介合成氨是一种重要的化工原料,广泛应用于农药、涂料、塑料、制冷剂等工业领域。
合成氨工艺是通过催化剂在适当的温度和压力下将氮气和氢气合成氨气的过程。
本文将介绍合成氨工艺的流程及其相关操作步骤。
2. 合成氨工艺流程合成氨工艺流程主要包括气体净化、气体压缩、催化反应、分离纯化等环节。
2.1 气体净化合成氨工艺的第一步是将氮气和氢气进行净化,去除其中的杂质和不纯物质,以保证催化剂的正常使用。
常见的气体净化方法包括吸附、吸收、脱水等。
在吸附过程中,氮气和氢气通过吸附剂床层,吸附剂可以去除其中的水分、氧气、二氧化碳等杂质。
在吸收过程中,气体经过溶剂床层,其中的硫化氢等有毒气体被吸收掉。
同时,还可以使用脱水剂去除气体中的水分。
2.2 气体压缩在气体净化后,将净化后的氮气和氢气进行压缩,提高其压力,以便后续的催化反应。
氮气和氢气分别进入压缩机进行压缩,压缩机通常采用多级压缩,保证气体压力的稳定和可控。
2.3 催化反应经过气体压缩后的氮气和氢气进入催化剂床层,进行合成氨的催化反应。
催化剂通常采用铁、钼或镍等金属催化剂,催化剂在适当的温度和压力下,使氮气和氢气发生反应,生成合成氨气。
催化反应是一个放热反应,需要控制温度以避免过高的温度导致副反应的发生。
2.4 分离纯化经过催化反应生成的合成氨气含有大量的副产物和未反应的氮气、氢气等杂质。
在分离纯化环节中,需要进行吸附、压缩、蒸馏等操作,将合成氨气中的杂质去除,提高纯度。
常见的分离纯化方法包括低温吸附法、压缩法和蒸馏法。
3. 工艺条件和参数合成氨工艺的实施需要满足一定的工艺条件和参数,以确保反应的进行和产出的质量。
常见的工艺条件和参数包括温度、压力、催化剂种类和配比、气体流速等。
3.1 温度催化反应的温度是合成氨工艺中的关键参数之一。
温度过高会导致副反应的发生,影响合成氨气的产量和纯度;温度过低则会降低反应速率。
一般情况下,催化反应的温度在300-500°C之间控制。
合成氨生产工艺流程
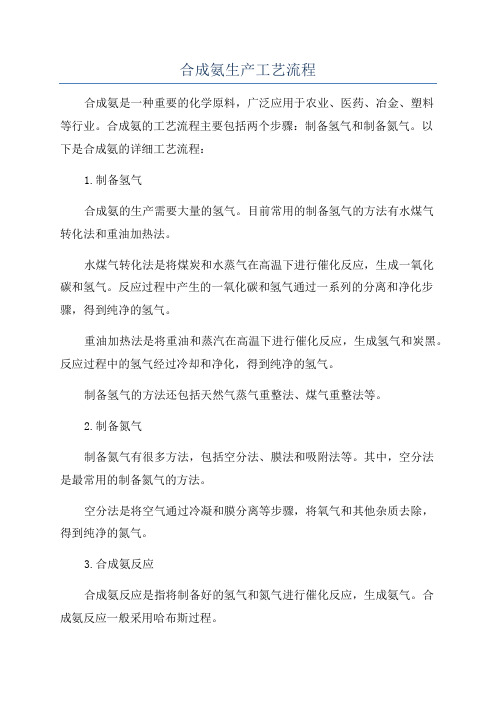
合成氨生产工艺流程合成氨是一种重要的化学原料,广泛应用于农业、医药、冶金、塑料等行业。
合成氨的工艺流程主要包括两个步骤:制备氢气和制备氮气。
以下是合成氨的详细工艺流程:1.制备氢气合成氨的生产需要大量的氢气。
目前常用的制备氢气的方法有水煤气转化法和重油加热法。
水煤气转化法是将煤炭和水蒸气在高温下进行催化反应,生成一氧化碳和氢气。
反应过程中产生的一氧化碳和氢气通过一系列的分离和净化步骤,得到纯净的氢气。
重油加热法是将重油和蒸汽在高温下进行催化反应,生成氢气和炭黑。
反应过程中的氢气经过冷却和净化,得到纯净的氢气。
制备氢气的方法还包括天然气蒸气重整法、煤气重整法等。
2.制备氮气制备氮气有很多方法,包括空分法、膜法和吸附法等。
其中,空分法是最常用的制备氮气的方法。
空分法是将空气通过冷凝和膜分离等步骤,将氧气和其他杂质去除,得到纯净的氮气。
3.合成氨反应合成氨反应是指将制备好的氢气和氮气进行催化反应,生成氨气。
合成氨反应一般采用哈布斯过程。
哈布斯过程是将氢气和氮气通过铁催化剂进行反应,在高温和高压下,生成氨气。
反应过程中,氮气和氢气经过多级催化剂反应器,进行一系列的反应和净化步骤,得到高浓度的氨气。
为了提高合成氨的产量和效率,可以采用以下措施:1.优化催化剂:改进催化剂的配方和制备工艺,提高催化剂的活性和稳定性。
2.调整反应条件:通过调整反应温度、压力和气体流量等参数,优化反应条件,提高反应效率。
3.循环气体:将反应后的气体进行回收和再利用,减少气体的浪费,提高氨气的产量。
4.节能减排:采用节能的加热和冷却设备,减少能量的消耗和二氧化碳的排放。
5.安全措施:建立完善的安全管理系统,确保生产过程中的安全。
总之,合成氨的生产工艺流程包括制备氢气和制备氮气两个步骤,通过优化反应条件和提高催化剂的活性,可以提高合成氨的产量和效率,从而满足农业、医药、冶金等行业对氨气的需求。
- 1、下载文档前请自行甄别文档内容的完整性,平台不提供额外的编辑、内容补充、找答案等附加服务。
- 2、"仅部分预览"的文档,不可在线预览部分如存在完整性等问题,可反馈申请退款(可完整预览的文档不适用该条件!)。
- 3、如文档侵犯您的权益,请联系客服反馈,我们会尽快为您处理(人工客服工作时间:9:00-18:30)。
合成氨生产工艺
合成氨生产原理:
氨是一种重要的化工原料,特别是生产化肥的原料,它是由氢和氮合成。
合成氨工业是氮肥工业的基础。
为了生产氨,一般均以各种燃料为原料。
首先,制成含H2和CO等组分的煤气,然后,采用各种净化方法,除去气体中的灰尘、H2S、有机硫化物、CO、CO2等有害杂质,以获得符合氨合成要求的洁净的1:3的氮氢混合气,最后,氮氢混合气经过压缩至15Mpa以上,借助催化剂合成氨。
1、合成氨生产工艺介绍
造气实质上是碳与氧气和蒸汽的反应,主要过程为吹风和制气。
具体分为吹风、上吹、下吹、二次上吹和空气吹净五个阶段。
原料煤间歇送入固定层煤气发生炉内,先鼓入空气,提高炉温,然后加入水蒸气与加氮空气进行制气。
所制的半水煤气进入洗涤塔进行除尘降温,最后送入半水煤气气柜。
造气工艺流程示意图
2、脱硫工段
煤中的硫在造气过程中大多以H2S的形式进入气相,它不仅会腐蚀工艺管道和设备,而且会使变换催化剂和合成催化剂中毒,因此脱硫工段的主要目的就是利用DDS脱硫剂脱出气体中的硫。
气柜中的半水煤气经过静电除焦、罗茨风机增压冷却降温后进入半水煤气脱硫塔,脱除硫化氢后经过二次除焦、清洗降温送往压缩机一段入口。
脱硫液再生后循环使用。
脱硫工艺流程图
3、变换工段
变换工段的主要任务是将半水煤气中的CO在催化剂的作用下与水蒸气发生放热反应,生成CO2和H2。
河南中科化工有限责任公司采用的是中变串低变工艺流程。
经过两段压缩后的半水煤气进入饱和塔升温增湿,并补充蒸汽后,经水分离器、预腐蚀器、热交换器升温后进入中变炉回收热量并降温后,进入低变炉,反应后的工艺气体经回收热量和冷却降温后作为变换气送往压缩机三段入口。
变换工艺流程图
4、变换气脱硫与脱碳
经变换后,气体中的有机硫转化为H2S,需要进行二次脱硫,使气体中的硫含量在25mg/m3。
脱碳的主要任务是将变换气中的CO2脱除,对气体进行净化,河南中科化工有限责任公司采用变压吸附脱碳工艺。
来自变换工段压力约为1.3MPa左右的变换气,进入水分离器,分离出来的水排到地沟。
变换气进入吸附塔进行吸附,吸附后送往精脱硫工段。
被吸附剂吸附的杂质和少量氢氮气在减压和抽真空的状态下,将从吸附塔下端释放出来,这部分气体称为解析气,解析气分两步减压脱附,其中压力较高的部分在顺放阶段经管道进入气柜回收,低于常压的解吸气经阻火器排入大气。
变换与脱硫工艺流程图
5、碳化工段
1气体流程
来自变换工段的变换气,依次由塔底进入碳化主塔、碳化付塔,变换气中的二氧化碳分别在主塔和付塔内与碳化液和浓氨水进行反
应而被吸收。
反应热由冷却水箱内的冷却水移走。
气体从付塔顶出来,进入尾气洗涤塔下部回收段,气体中的少量二氧化碳和微量的硫化氢被无硫氨水继续吸收,再进入上部清洗段。
气体中微量二氧化碳被软水进一步吸收,最后达到工艺指标经水分离后,送往精脱硫塔进一步脱硫后,送往压缩机三段进口。
2、液体流程
浓氨水由浓氨水泵从吸氨岗位浓氨水槽打入付塔,一方面溶解塔内的结疤,另一方面吸收主塔尾气中的剩余二氧化碳,逐步提高浓氨水的碳化度。
然后,付塔的溶液由碳化泵从底部抽出,打入主塔,在主塔内进一步吸收变换气中的二氧化碳,生成含碳酸氢铵结晶的悬浮液,再由底部取出管压入分离岗位进行分离。
回收塔回收段中的无硫氨水来自合成或铜洗工段使用过的无硫
氨水和回收段的稀氨水压入稀氨水压入吸氨岗位母液槽和稀氨水槽
或送脱硫岗位使用,从回收段出来的水直接排污水沟。
碳化工艺流程图
6、甲醇合成工段
联醇是将经变换、脱碳后的净化气中的CO:1-5%、CO2<0.5%(其含量可根据生产所要求的醇氨比调节)与气体中的H2经压缩机加压到15MP后,依次经过洗氨塔、油分、预热器、废热锅炉进入合成塔,在催化剂的作用下合成为甲醇,同时起到气体净化的作用。
醇后气中CO<0.5%、CO2<0.2%。
出塔气体经水冷却到40℃左右,将气体中的甲醇冷凝,使气体中的甲醇含量小于0.5%,经醇分离器分离出甲醇后,一部分气体经甲醇循环机返回甲醇合成塔,大部分气体进入精炼工段。
粗醇生产工艺流程示意图
7、精炼工段
醇后工艺气中还含有少量的CO和CO2。
但即使微量的CO和CO2也能使氨
催化剂中毒,因此在去氨合成工序前,必须进一步将CO和CO2脱除。
我们公司是采用醋酸铜氨液洗涤法,铜洗后的工艺气体中的含量将至25ppm以下。
醇后气体由铜洗塔底部进入,与塔顶喷淋的醋酸铜氨液逆流接触,将工艺气中的CO和CO2脱除到25ppm以下,经分离器将吸收液分离后送往压缩机六段进口。
铜氨液从铜洗塔经减压还原、加热、再生后,补充总铜、水冷却、过滤、氨冷后经铜氨液循环泵加压循环使用。
8、压缩工段
压缩工段的压缩机为六段压缩。
由于合成氨生产过程中,变换、脱碳、粗醇与氨合成分别在0.87MPa、3.7MPa、15MPa、27MPa条件下进行,压缩工段的任务就是提高工艺气体压力,为各个生产工段提供其所需的压力条件。
9、氨合成工段
氨合成工段的主要任务是将铜洗后制得的合格N2、H2、混合气,在催化剂的存在下合成为氨。
压缩机六段来的压力为27?MPa的新鲜补充气,与循环气混合后进入氨冷器、氨分离器、冷交换器,经循环机升压并经过油分离器除油后进入氨合成塔的内件与外筒的环隙,冷却塔壁,出来后经预热器升温后进入氨合成塔内件,完成反应后离开反应器,分别进入废热锅炉、预热器、软水加热器回收热量,最后经水冷器、冷交换器、氨冷器降温冷却,将合成的氨液化分离出系统,未反应的氮氢气循环使用。
10、冷冻工段
由于氨合成工段需要通过液氨气化来产生低温生产条件,因此冷冻工段的任务就是把气态的氨重新液化。
由氨蒸发器蒸发的气氨经气氨总管进入冰机前分离器,分离出液氨后进入氨压缩机加压,加压后的气氨经油分离器后进入水冷器,在此气氨冷凝为液氨并回到冰机液氨贮槽,由支出阀送给氨蒸发器循环使用或氨库。