合成氨厂脱硫系统工艺的设计说明书[1]
合成氨脱硫工艺设计
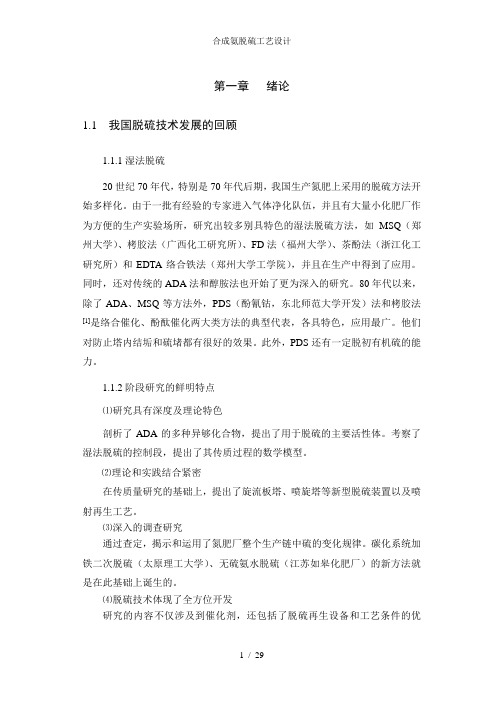
第一章绪论1.1 我国脱硫技术发展的回顾1.1.1湿法脱硫20世纪70年代,特别是70年代后期,我国生产氮肥上采用的脱硫方法开始多样化。
由于一批有经验的专家进入气体净化队伍,并且有大量小化肥厂作为方便的生产实验场所,研究出较多别具特色的湿法脱硫方法,如MSQ(郑州大学)、栲胶法(广西化工研究所)、FD法(福州大学)、茶酚法(浙江化工研究所)和EDTA络合铁法(郑州大学工学院),并且在生产中得到了应用。
同时,还对传统的ADA法和醇胺法也开始了更为深入的研究。
80年代以来,除了ADA、MSQ等方法外,PDS(酚氰钴,东北师范大学开发)法和栲胶法[1]是络合催化、酚酞催化两大类方法的典型代表,各具特色,应用最广。
他们对防止塔内结垢和硫堵都有很好的效果。
此外,PDS还有一定脱初有机硫的能力。
1.1.2阶段研究的鲜明特点⑴研究具有深度及理论特色剖析了ADA的多种异够化合物,提出了用于脱硫的主要活性体。
考察了湿法脱硫的控制段,提出了其传质过程的数学模型。
⑵理论和实践结合紧密在传质量研究的基础上,提出了旋流板塔、喷旋塔等新型脱硫装置以及喷射再生工艺。
⑶深入的调查研究通过查定,揭示和运用了氮肥厂整个生产链中硫的变化规律。
碳化系统加铁二次脱硫(太原理工大学)、无硫氨水脱硫(江苏如皋化肥厂)的新方法就是在此基础上诞生的。
⑷脱硫技术体现了全方位开发研究的内容不仅涉及到催化剂,还包括了脱硫再生设备和工艺条件的优化,以及分析手段的改进。
广西大学、浙江大学和上海化工研究院在这方面做了突出的贡献。
⑸大力宣传国外脱硫新技术对国外脱硫最新动态的情报研究及宣传,为我国开发脱硫技术提供了很好的借鉴。
中国科技情报研究所重庆分所在这方面做的工作对我国当时的脱硫技术的发展起到了很重要的作用。
1.1.3干法脱硫70年代湿法脱硫在氮肥净化系统几乎占到统治地位。
当时化工生产还比较粗放,小化肥厂尤其如此。
人们对干法脱硫的认识也较肤浅,直到70年代后期,郑州大学采用廉价煤种为原料制出RS型活性炭并用于化肥厂煤气粗放硫和原料气二次脱硫;太原理工大学开辟新的原料资源,制备TC系列成型/粉状氧化铁脱硫剂应用于燃气(煤气、沼气等)的粗脱硫及化工原料气的脱硫;西南化工研究院利用贵州锰矿资源[2],制备MF型铁锰复合中温脱硫剂并用于天然气净化,在全国干法脱硫技术上迈出了新的一步。
合成氨厂脱硫系统工艺设计说明书[1]
![合成氨厂脱硫系统工艺设计说明书[1]](https://img.taocdn.com/s3/m/6ec09473cf84b9d529ea7a15.png)
目录1.设计任务 (3)2.脱硫方法的选择 (4)3.工艺流程 (5)4.物料衡算 (8)5.热量衡算 (12)6.设备尺寸计算 (15)7.主要设备及其工艺参数 (20)8.致谢 (24)合成氨脱硫工艺设计说明书第一节设计任务1.设计项目:合成氨脱硫工艺设计2.年生产能力:4000吨3.设计依据:合成氨原料气中,一般总含有不同数量的无机硫化物和有机硫化物,这些硫化物的成分和含量取决于气化所用燃料的性质及其加工的方法。
原料气中的硫含量,可以认为于燃料只能跟硫含量成正比。
一般说来,以焦碳或无烟煤制的的水煤气或半水煤气中,较高者,硫化氢达4-6克/标准米3,有机硫0.5-0.8克/标准米3(主要为硫氧化碳;其次为二氧化碳,约占百分之十几);较低者,硫化氢1-2克/标准米3,有机硫0.05-0.2克/标准米3。
但是近来有些小合成氨厂用当地高硫煤作原料,制得的煤气中硫化氢含量也有高达20-30克/标准米3,有机硫1-2克/标准米3(主要为二氧化碳。
其次为硫氧化碳.硫醇和噻吩)。
天然气中硫化氢的含量,则因地区不同有极大的差异,约在0.5-15克/标准米3的范围内变动,有机硫则以硫醇为主。
重油.轻油中的硫含量亦因不同的石油产地而有极大的差异。
重油部分氧化法的制气过程中,重油只能感的硫分有95%以上转化成硫化氢,只有小部分变成有机硫,其主要组分为硫氧化碳。
例如,含硫分0.3-5.5%的重油,气体得到的气体中含硫化氢1.1-2.0克/标准米3和硫氧化碳0.03-0.4克/标准米3。
原料气中碳化物的存在,会增加气体对金属的腐蚀并使催化剂中毒。
此外,硫本身也是一种重要的资源,应当予以回收。
为此。
必须对原料气进行脱硫4.其它:由于本设计为假定的设计,因此有关设计任务书的其它项目,如进行设计的依据、厂区或厂址、主要经济技术指标、原料的供应、技术规格以及燃料种类、水电汽的主要来源、和其它工业企业的关系、建厂期限、设计单位、设计进度及设计阶段的规定等均从略。
合成氨工艺设计书

合成氨工艺流程设计书一、 天然气脱硫:天然气又称油田气、石油气、石油伴生气。
开采石油时,只有气体称为天然气;石油和石油气,这个石油气称为油田气或称石油伴生气。
天然气的化学组成及其理化特性因地而异,主要成分是甲烷,还含有少量乙烷、丁烷、戊烷、二氧化碳、一氧化碳、硫化氢等。
无硫化氢时为无色无臭易燃易爆气体,密度多在0.6~0.8g/cm3,比空气轻。
通常将含甲烷高于90%的称为干气,含甲烷低于90%的称为湿气。
脱硫的方法有干法脱硫、湿法脱硫我们采用湿法脱硫——氨水催化法一般采用氨水浓度为8~22滴度,并加有0.2~0.3g/L 的对苯二酚作为催化剂。
相应的脱硫和再生反应: O H HS NH S H OH NH 2424+=+ O H NH S O HS NH 232421++=+氨水催化法有氨损失大、硫容量低的缺点,当煤气中硫含量高时,相应的应增加溶液循环量。
二、甲烷的转换甲烷蒸汽转化机理有两种说法;一种认为甲烷逐级分解成次甲基、乙烷、乙烯和碳,同时,这些分解产物于水蒸气反应生成氢气、一氧化碳和二氧化碳:另一种认为甲烷先裂解成碳和氢,然后碳再由水蒸气气化生成一氧化碳和氢气:其次认为镍催化剂的表面,甲烷转化的速度比甲烷分解的速度快得多,中间产物中不会有碳的生成。
镍催化剂表面甲烷和水蒸气解离成次甲基和原子态氧,并在催化剂表面互相作用,最后生成CO 、22H CO 和。
有5个步骤表示反应历程;2243)(H CO g O H CH +⇒+Z-镍催化剂表面的活性中心;)()()(2O Z CO Z CH Z 、、-分别为化学吸收为化学吸附态的次甲基、一氧化碳和氧原子。
1、在较低温度下,在外热式一段转化炉内进行烃类蒸汽转化反应,而后在较高温度下,于耐火砖衬里的钢制转化炉中加入空气,利用反应热将甲烷转化反应进行到底。
2、二段转化炉的反应中内也装有催化剂,加入空气来自一段转化气先与空气作用;mol kJ H g O H O H /99.483)(22298222-=∆=+O, mol kJ H CO O CO /95.565229822-=∆=+O ,其理论火焰温度为1203C O 。
合成氨生产工艺脱硫

第七章脱硫工段第一节工艺流程及主要设备一、本工段任务从造气工段来的半水煤气中,除氢和氮外,还含有27%左右的CO,8%左右的C02,以及少量的硫化物和氧等。
硫化物(主在是仏5,约占半水煤气中硫总量的90%左右,其次还有CS2,COS和RSH等)含量约为1.0〜4.Og/Nm3。
这些硫化物对合成氨生产是有害的。
它会腐蚀设备、管道;会引起变换、合成、甲醇等工段触媒中毒、降低活性或失去活性;会破坏铜液成份。
H2S与铜液中的Cu2+和CU+作用生成CuS和Cu2S沉淀,堵塞设备管道与阀门,使精炼操作条件恶化。
生产过程中,h2s从溶液中解吸出来,或从设备管道中泄漏出来,会污染环境,影响人体健康。
本工段的主要任务,就是用脱硫液将半水煤气中的硫化物脱除至0.07g/Nr^以下,使半水煤气得到净化,以满足后工段生产工艺的要求。
吸收硫化氢的脱硫液经再生后循环使用,再生析出的硫回收成硫磺。
本工段要根据全厂生产情况,调节罗茨风机气垴。
脱硫的方法很多,根据脱硫剂的形态可分为湿法和干法两大类。
干法以固体为吸收剂,如活性碳法、分子筛法等。
湿法以液体为吸收剂,如氨水液相催化法、氨水中和法、ADA法,近年来还发展了拷胶法、PDS 法等。
B前,小氮肥厂脱硫采用较多的是氨水液相催化法。
现以本法为例,简述脱硫过程。
二、工艺流程简述氨水液相催化法脱硫是用脱硫液(贫液)吸收半水煤气中的硫化氢。
吸收硫化氢后的脱硫液(富液),在对苯二酚载氧体的催化作用下,经氧化再生后循环使用。
再生析出的硫泡沫经分离,熔融精制成硫锭。
主要反应方程式如下:NH4OH+H2S==MH4HS+H2O(脱硫反应)2NH4OH+CO2==(NH4)2CO3+H2O2NH4HS+Oz==2NH4OH+2S| (再生反应)2NH4HS+202=(NH4)2S203+H20来自造气工段的半水煤气,经除尘器除去所含的部份粉尘,煤焦油等杂质后,由罗茨鼓风机增压送入气体冷却器冷却,然后在喷旋脱硫塔的喷射器中与贫液并流接触而下,从喷旋塔底部进入,在旋流板中气液转为逆流接触,半水煤气中的硫化氢被贫液吸收。
合成氨脱硫工艺设计

合成氨脱硫工艺设计
1.工艺原理
合成氨脱硫使用了一种称为氧化剂的物质,通常是氧气和氯气的混合物,加之于废气中。
氧化剂与硫化物反应生成硫酸盐。
该反应需要一定的温度和压力条件下才能进行。
通常情况下,反应温度为120-200摄氏度,压力为1-3兆帕。
2.工艺流程
在吸收器中,还需要添加一种促进剂,以提高硫酸盐的转化率。
常用的促进剂包括硫酸铵和硝酸铵。
这些促进剂能增加硫酸盐的反应速率,并且防止硫酸盐结晶。
硫酸盐溶液在吸收废气中的过程中,会逐渐饱和。
当饱和度达到一定的程度时,需要对硫酸盐溶液进行再生。
再生通常通过加热溶液,释放出硫化物,并将其氧化成硫化氢。
然后将硫化氢处理成为硫酸盐。
3.设备设计
在工艺设计中,需要考虑各个设备的容量和尺寸,以满足处理废气的要求。
此外,还需考虑设备的材料选择,以保证其在高温、高压、腐蚀等恶劣条件下的使用寿命。
4.运行与控制
合成氨脱硫工艺需要建立一个完善的运行与控制系统,以保证整个工艺的稳定和高效运行。
应根据实际情况采用合适的控制策略,监测和调节各个参数,如废气流量、温度、压力、硫酸盐浓度等。
此外,还需建立一个规范的维护和保养计划,定期检查设备的状况,及时进行修复和更换。
总之,合成氨脱硫工艺设计需要考虑多个方面,包括工艺原理、工艺流程、设备设计和运行控制。
通过科学合理的设计和操作,可以有效降低硫化物的排放,减少环境污染。
合成氨脱硫工段工艺设计
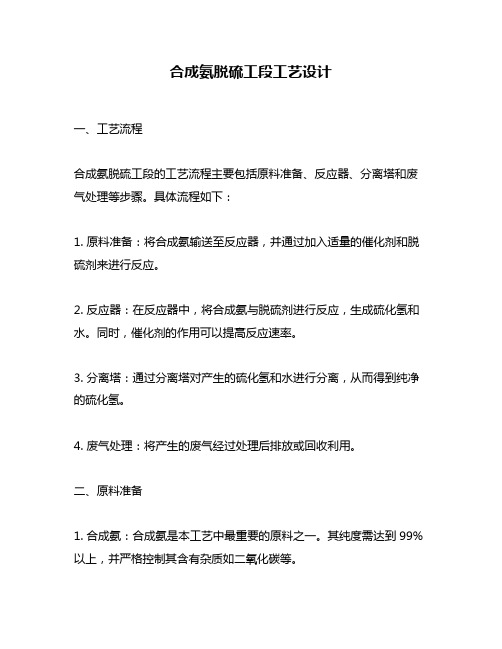
合成氨脱硫工段工艺设计一、工艺流程合成氨脱硫工段的工艺流程主要包括原料准备、反应器、分离塔和废气处理等步骤。
具体流程如下:1. 原料准备:将合成氨输送至反应器,并通过加入适量的催化剂和脱硫剂来进行反应。
2. 反应器:在反应器中,将合成氨与脱硫剂进行反应,生成硫化氢和水。
同时,催化剂的作用可以提高反应速率。
3. 分离塔:通过分离塔对产生的硫化氢和水进行分离,从而得到纯净的硫化氢。
4. 废气处理:将产生的废气经过处理后排放或回收利用。
二、原料准备1. 合成氨:合成氨是本工艺中最重要的原料之一。
其纯度需达到99%以上,并严格控制其含有杂质如二氧化碳等。
2. 催化剂:催化剂是本工艺中必不可少的组成部分。
常用的催化剂包括铝酸盐、钼酸盐等。
其作用是加速反应速率,提高产物纯度。
3. 脱硫剂:脱硫剂是用于吸收反应中生成的硫化氢的物质。
常用的脱硫剂包括三乙醇胺、二乙醇胺等。
三、反应器1. 反应器设计:反应器主要由反应釜、搅拌器、加热系统和控制系统等部分组成。
反应釜材质一般为不锈钢或碳钢,且内壁需进行防腐处理。
2. 反应条件:合成氨脱硫反应需要在一定的温度和压力下进行。
通常情况下,温度控制在150℃-250℃之间,压力控制在1MPa-3MPa之间。
四、分离塔1. 分离塔设计:分离塔主要由进料口、出料口、填料层和塔板层等部分组成。
填料层材质一般为陶瓷或金属,其作用是增加接触面积,提高分离效率。
2. 分离条件:分离塔需要在一定的温度和压力下进行。
通常情况下,温度控制在50℃-100℃之间,压力控制在0.1MPa-0.5MPa之间。
五、废气处理1. 废气处理方法:废气处理一般采用吸收法或燃烧法。
吸收法是将废气通过吸收剂中,使其中的有害物质被吸收,从而达到净化的目的。
燃烧法则是将废气进行高温燃烧,使其中的有害物质被分解,从而达到净化的目的。
2. 废气处理设备:废气处理设备包括吸收器、除尘器、脱臭器和排放管道等部分。
其中,吸收器和脱臭器材质一般为玻璃钢或不锈钢。
合成氨生产工艺脱硫
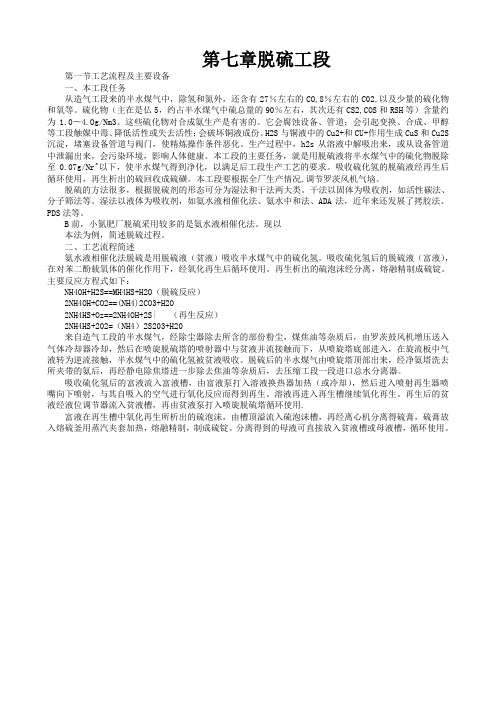
第七章脱硫工段第一节工艺流程及主要设备一、本工段任务从造气工段来的半水煤气中,除氢和氮外,还含有27%左右的CO,8%左右的C02,以及少量的硫化物和氧等。
硫化物(主在是仏5,约占半水煤气中硫总量的90%左右,其次还有CS2,COS和RSH等)含量约为1.0〜4.Og/Nm3。
这些硫化物对合成氨生产是有害的。
它会腐蚀设备、管道;会引起变换、合成、甲醇等工段触媒中毒、降低活性或失去活性;会破坏铜液成份。
H2S与铜液中的Cu2+和CU+作用生成CuS和Cu2S 沉淀,堵塞设备管道与阀门,使精炼操作条件恶化。
生产过程中,h2s从溶液中解吸出来,或从设备管道中泄漏出来,会污染环境,影响人体健康。
本工段的主要任务,就是用脱硫液将半水煤气中的硫化物脱除至0.07g/Nr^以下,使半水煤气得到净化,以满足后工段生产工艺的要求。
吸收硫化氢的脱硫液经再生后循环使用,再生析出的硫回收成硫磺。
本工段要根据全厂生产情况,调节罗茨风机气垴。
脱硫的方法很多,根据脱硫剂的形态可分为湿法和干法两大类。
干法以固体为吸收剂,如活性碳法、分子筛法等。
湿法以液体为吸收剂,如氨水液相催化法、氨水中和法、ADA法,近年来还发展了拷胶法、PDS法等。
B前,小氮肥厂脱硫采用较多的是氨水液相催化法。
现以本法为例,简述脱硫过程。
二、工艺流程简述氨水液相催化法脱硫是用脱硫液(贫液)吸收半水煤气中的硫化氢。
吸收硫化氢后的脱硫液(富液),在对苯二酚载氧体的催化作用下,经氧化再生后循环使用。
再生析出的硫泡沫经分离,熔融精制成硫锭。
主要反应方程式如下:NH4OH+H2S==MH4HS+H2O(脱硫反应)2NH4OH+CO2==(NH4)2CO3+H2O2NH4HS+Oz==2NH4OH+2S| (再生反应)2NH4HS+202=(NH4)2S203+H20来自造气工段的半水煤气,经除尘器除去所含的部份粉尘,煤焦油等杂质后,由罗茨鼓风机增压送入气体冷却器冷却,然后在喷旋脱硫塔的喷射器中与贫液并流接触而下,从喷旋塔底部进入,在旋流板中气液转为逆流接触,半水煤气中的硫化氢被贫液吸收。
C10255年产40万吨合成氨脱硫工段的设计

年产40万吨合成氨脱硫工段工艺设计是结合文献中提供的生产中收集到的各类生产技术指标而设计的。
本设计所采用栲胶脱硫法对合成氨生产进行脱硫,其主要原料是半水煤气和脱硫液,详细介绍了合成氨脱硫工段的生产原理、工艺流程、工艺参数、物料衡算、热量衡算,以及设备选型、厂房布置和三废处理。
本设计的特点是在脱硫效率和再生率方面的研究有所突破。
关键词:栲胶脱硫法合成氨脱硫塔Annual output of 400000 tons of ammonia desulfurization section of process design is to provide production, combined with literature collected all kinds of production technology index. This design adopts the extract desulfurization method for desulfurization, the production of synthetic ammonia, its main raw material is semi water gas and fluid of desulfurization. Ammonia desulfurization section was introduced in detail the principle, process flow, process parameters, material balance, heat balance, as well as the equipment selection, building layout, and three wastes disposal. The characteristic of this design is in the desulfurization efficiency and breakthrough in the study of regeneration rate.Key words:method of desulfurization by tannin extract synthesis ammonia Desulfurization tower目录1. 总论 (5)1.1.1栲胶的组成及性质 ............................................................ 错误!未定义书签。
- 1、下载文档前请自行甄别文档内容的完整性,平台不提供额外的编辑、内容补充、找答案等附加服务。
- 2、"仅部分预览"的文档,不可在线预览部分如存在完整性等问题,可反馈申请退款(可完整预览的文档不适用该条件!)。
- 3、如文档侵犯您的权益,请联系客服反馈,我们会尽快为您处理(人工客服工作时间:9:00-18:30)。
目录1.设计任务 (3)2.脱硫方法的选择 (4)3.工艺流程 (5)4.物料衡算 (8)5.热量衡算 (12)6.设备尺寸计算 (15)7.主要设备及其工艺参数 (20)8.致谢 (24)合成氨脱硫工艺设计说明书第一节设计任务1.设计项目:合成氨脱硫工艺设计2.年生产能力:4000吨3.设计依据:合成氨原料气中,一般总含有不同数量的无机硫化物和有机硫化物,这些硫化物的成分和含量取决于气化所用燃料的性质及其加工的方法。
原料气中的硫含量,可以认为于燃料只能跟硫含量成正比。
一般说来,以焦碳或无烟煤制的的水煤气或半水煤气中,较高者,硫化氢达4-6克/标准米3,有机硫0.5-0.8克/标准米3(主要为硫氧化碳;其次为二氧化碳,约占百分之十几);较低者,硫化氢1-2克/标准米3,有机硫0.05-0.2克/标准米3。
但是近来有些小合成氨厂用当地高硫煤作原料,制得的煤气中硫化氢含量也有高达20-30克/标准米3,有机硫1-2克/标准米3(主要为二氧化碳。
其次为硫氧化碳.硫醇和噻吩)。
天然气中硫化氢的含量,则因地区不同有极大的差异,约在0.5-15克/标准米3的范围内变动,有机硫则以硫醇为主。
重油.轻油中的硫含量亦因不同的石油产地而有极大的差异。
重油部分氧化法的制气过程中,重油只能感的硫分有95%以上转化成硫化氢,只有小部分变成有机硫,其主要组分为硫氧化碳。
例如,含硫分0.3-5.5%的重油,气体得到的气体中含硫化氢1.1-2.0克/标准米3和硫氧化碳0.03-0.4克/标准米3。
原料气中碳化物的存在,会增加气体对金属的腐蚀并使催化剂中毒。
此外,硫本身也是一种重要的资源,应当予以回收。
为此。
必须对原料气进行脱硫4.其它:由于本设计为假定的设计,因此有关设计任务书的其它项目,如进行设计的依据、厂区或厂址、主要经济技术指标、原料的供应、技术规格以及燃料种类、水电汽的主要来源、与其它工业企业的关系、建厂期限、设计单位、设计进度及设计阶段的规定等均从略。
第二节脱硫方法的选择脱硫气体中硫化氢的方法很多,一般可分为湿法与干法两大类。
湿法脱硫按溶液的吸收于再生性质,又可分为氧化法,化学吸收法,物理吸收法三类。
氧化法是借溶液中载氧体的催化作用,把被吸收的硫化氢氧化成硫磺,使溶液获得再生。
主要有葱醌二磺酸纳法.氨水催化法.砷碱法和砷碱法(G-V法)等。
化学吸收法系以弱碱性溶液为吸收剂,与硫化氢进行化学反应而形成化合物,当富液温度升高.压力减低时,该化合物即能分解,使硫化氢放出,这类方法中有烷基醇胺法,碱性盐溶液法等。
物理吸收法常用有机溶液为吸收剂,其吸收完全是物理过程,当富液降低压力时,硫化氢能放出,如聚乙二醇二甲醚法(Selexol法)和冷甲醇法等,而今年来发展的环丁砜法是属于物理与化学吸收相结合的方法。
干法脱硫中最早使用的是氢氧化铁法和活性炭。
但今年合成氨工业常用干法脱硫作为脱除有机硫和精细脱硫的手段,如氧化锌脱硫.分子筛脱硫。
钴钼催化剂加氢脱硫等。
以煤(焦)为原料的合成氨变换气中,H2S含量通常在80~200mg/m3之间,为使后继工序稳定、经济地运行,需将其脱除。
过去推荐采用干法(氧化铁、活性炭等)脱除变换气中H2S,但多年的生产实践表明,干法变脱存在硫容低、更换频繁和净化度不高等缺点,故越来越多的厂家采用湿法(如栲胶法)脱除变换气中的H2S并取得了较好的经济效益。
随着气源中分压升高,H2S在脱硫液中传质率下降,脱硫效率降低。
变换气CO2分压较高(变换气中CO2含量近28%,变换气脱硫压力多数厂为0.8MPa,少数为1.6MPa因此,从变换气中脱除H2S有其自身的难度和特点,现有湿法变换气脱硫效率仅60%-80%。
国外以天然气(轻油)为原料的醇氨厂,通常在钴钼加氢后用氧化锌脱硫,而以煤(重油)为原料的厂家,则采用低温甲醇洗脱硫,可脱至总硫小于0.1*10-6。
第三节工艺流程3.1工艺流程(1)半水煤气脱硫从造气车间送出来的半水煤气经气柜通过静电除焦器和罗茨鼓风,经冷却后进入脱硫塔,脱硫后的半水煤气再机进入冷却清洗塔的下段净化后的半水煤气送氮氢气压缩机一段入口。
半水煤气脱硫流程如图3-1所示。
图3-1半水煤气脱硫流程图3.2变换气脱硫从变换送出来的变换气(变换气压力 2.1PMa),经二次脱硫清洗塔后进入二次脱硫塔,脱硫后送压缩工段。
变换气脱硫流程如图3-2所示。
图3-2变换气脱硫流程图从图3-1中可以看出:采样管分别取自3台电动给水泵入口门前,最后汇至一根总管去化学采样架,正常时采样门全部处于开启状态,华泽铝电机组运行时保持2台电动给水泵运行,,1台电动给水泵备用。
从运行中观察发现备用电动给水泵入口管道处温度低于运行泵入口温度10度-15度,这是由于备用电动给水泵内水不流动,造成入口管道给水被冷却温度逐渐降低。
大家知道,热力除氧的原理为:根据道尔顿分压定律, 溶于水中的气体量与气体种类、气体在水面上的分压力以及水的温度有,水温越高,水面上的气体分压力越低,气体的溶解度越小。
当水处于关沸腾状态时,水中含氧量约等于零。
图3-2说明了在压力不变的情况下, 水中的溶氧随温度的升高而降低。
备用电动给水泵入口管道温度低,就可能造成备用电动给水泵入口溶氧局部增大。
经过分析,决定关闭备用电动给水泵入口门化学采样手动,进行观察。
表2是关闭备用电动给水泵入口采样手动门后的数据。
从表2中可以看出锅炉给水溶氧明显达到小于7ug/l的国家标准。
说明在除氧器底部靠近备用电动给水入口管道处存在局部溶氧超标现象。
防腐措施(1)在电动给水泵停运备用时,及时关闭备用电动给水泵采样手动门,开启运行泵采样手动门,保证采样数据的真实性。
(2)加强化学采样流量的监视,保证采样数据真实性。
(3)从数据可以看出,除氧器局部溶氧大,与空冷机组凝结水溶氧大,加强凝结水溶氧的分析,在没有具体标准的情况下,参考湿冷机组凝结水溶氧标准和同类型机组比较,使凝结水溶氧保持在较低的水平。
(4)在保证给水溶氧合格的情况下,适当关小除氧器排氧门,减少工质损失,提高机组经济性。
3.3脱硫液流程在再生槽再生的脱硫液分别经贫液泵及二次脱硫泵从脱硫塔及二次脱硫塔顶部喷淋而下。
从脱硫塔底排出的溶液经富液泵压至喷射再生器吸入空气在再生槽再生,析出硫磺后的溶液再循环使用,从二次脱硫塔底的2.1MPa送至脱硫塔进行第二次脱硫,这样既减少贫液量,又能使溶液中吸收的少量CO2在常压下解吸,减少CO2损失。
脱硫液流程如图3-3所示:脱硫液图3-3脱硫液流程图3.4回收流程硫磺泡沫在再生槽顶部溢流至硫泡沫混合槽,以硫泡沫泵压至硫泡,分离出硫膏,进入熔硫釜,加热熔融后,硫磺呈液态流出冷却成形后作为副产品出售。
回收流程如图3-4所示:图3-4回收流程图采用变换气脱硫溶液减压到脱硫塔进行第二次脱硫的生产工艺,既,又能使溶液中吸收的少量减轻了贫液泵负荷CO 2在常压中解吸,减少CO 2损失。
第四节 物料衡算下面介绍氨水脱硫塔的物料衡算。
1.计算说明(1)原料为炭化煤球,采用铜洗流程,产品为碳酸氢铵。
设备能力按年产4000吨合成氨来计算,即每小时氨产量为0.91吨。
(2)半水煤气中H2S ,2g/m 3,用精炼工段来的新鲜氨水进行一次脱硫。
稀氨水直接排放,可供工厂附近农田施肥用。
(3)为了简化计算起见,不考虑再生气回收氨后其余成分的变化,以 及一次脱硫后CO 2成分的变化。
(4)计算基准:1吨氨 2.已知条件(1)半水煤气的组成(干)H 2S 含量=0.002×3460.394=6.921kg ≈0.204kmol (2)再生气组成(干)(3)混合煤气组成(干)=半水煤气(干)+再生气(干)(4)混合煤气进口温度35℃ (5)混合煤气出脱硫塔温度35℃(6)冷水温度32℃进脱硫塔氨水温度33℃ (7)混合煤气进脱硫系统压力250mmH 2O (8)混合煤气经罗茨风机后压力3500mmH 2O (9)混合煤气出脱硫塔压力3100mmH 2O (10)混合煤气去压缩机一段压力3000mmH 2O (11)大气压力753mmHg(12)一次脱硫后硫化氢含量0.1g/标准立方米 3.物料衡算(1)脱硫液的用量取液气比为4.51/标准m 3 脱硫液的用量=3592.382×4.5=16.2 m 3 出脱硫塔稀氨水中硫化氢含量:按硫平衡计算 塔顶进液H 2S 含量=0出脱硫塔稀氨水中H 2S 含量= 3(2.00.1)3592.3821016.2--⨯⨯=0.4231kg/m 3≈0.01236kmol/m 3出脱硫塔气体中H 2S 、NH 3平衡含量 出口气相中H 2S 的平衡分压22*1()H SS P A S K =- 式中A ,S ——分别为溶液中总氨、总H 2S 的含量, K ——平衡常数1log 0.089K S α=+α——常数;t=20℃, α=-1.1;t=40℃, α=-1.7进塔溶液温度33℃,α=-1.491log 1.490.0890.01236 1.4889K =-+⨯=-212*0.03240.012360.01984(0.250.01239)0.0324H SK P ===-⨯ 出塔气相中H 2S 的平衡含量0.0198413.61100%0.00202%3100102410.002023410000.030722.4100⨯⨯==+⨯⨯≈=⨯出塔气相中H 2S 的平衡含量31mg/标准m 3,小于要求出脱硫塔的H 2S100mg/标准m 3,净化率可以达到。
出塔气相氨平衡分压[]*333NH NH NH P H=式中3NH H——氨的亨利系数,kmol/m 3·mmHg 查氨在纯水中的亨利系数表,33℃时,H 0=0.0608kmol/m 3·mmHg[]3NH =A-S=0.25-0.01236-0.2376 kmol/m 333*3log0.0250.23760.06030.0595kmol/m3?mmHg 0.23763.99mmHg0.0595NH NH NH HH P -=⨯=== 出塔气相氨的平衡含量= 33.9913.61100%0.407%3100+102410.407100017 3.09/22.4100g m ⨯⨯=⨯⨯≈=⨯标准以上计算是将整个塔内溶液成分看成不变,实际上塔顶溶液中NH 3与H 2S 浓度都为低,所以计算得出的气相平衡NH 3与H 2S 含量偏高些。
(3)氨平衡 进项① 精炼再生气中含有氨量14.8811711.3022.4⨯= ② 合成贮槽放空补充氨 x kg 合计 11.30+ x kg 出项① 脱硫塔排出稀氨水中含氨0.251716.268.85⨯⨯=Kg ② 出脱硫塔气体中带出氨:已出塔气相平衡氨含量计算3592.382 3.0911.10⨯=kg合计79.95kg 平衡11.30+x=79.95 x=68.65kg即没生产一吨氨,脱硫消耗用氨79.95kg ,除精炼回收外。