粉末冶金法在金属制备中的应用
金属基复合材料的制备及应用

金属基复合材料的制备及应用一、引言金属基复合材料,是指金属基体中添加其他高性能材料,形成的一种新型复合材料。
金属基复合材料具有高强度、高耐磨性、高温性能和导电性能好等优点。
本文将从制备及其应用两个方面分别进行阐述。
二、制备方法目前,金属基复合材料的制备方法主要分为机械法、粉末冶金法、热等静压法及热处理法等几种方法。
1.机械法机械法是把高性能材料加入到金属水泥(搪瓷)中,将其剪切和挤出,形成具有高强度和高导热性的复合材料。
这种方法操作简单,但是强度相对较低。
现在已经很少应用。
2.粉末冶金法粉末冶金法是将高性能材料的粉末与金属粉末混合,进而放入压制模具内进行压制,最后通过热处理得到金属基复合材料。
其精度高、性能稳定,但制备周期较长。
3.热等静压法热等静压法是将高性能陶瓷、纳米粒子及金属混合制粉末分布于金属粉末中,然后通过等静压加工形成复合材料。
其优点是即使是对一些易反应的材料也能热压成型,并且制品光整度好。
但采用这种方法制备的复合材料的强度与轻便型材相比还存在差距。
4.热处理法热处理法是指将高温稳定性好的有色金属及其合金经过热处理后,再经过冷加工以及添加高强度材料,如 SiC,WC 等制成复合材料。
这种方法制备出的复合材料强度较高,且成本较低。
三、应用领域金属基复合材料在工业生产中占有着重要的地位。
下面列举几个常见的应用领域:1.航空领域金属基复合材料在航空领域中应用最为广泛。
由于其高强度、高温性能以及耐腐蚀性,使得它不仅可以制造一个很轻的结构,还可以提高发动机的效率。
2.制造业金属基复合材料广泛应用于制造业生产中,例如汽车制造、机械制造等。
这是因为它可以提高产品的强度及抗性能,同时减少产品重量,节约原材料。
3.核能领域金属基复合材料在核反应堆内作为结构材料,成为了当前研究的重点方向之一。
它的高温性能以及良好的耐辐射性能为核能领域的发展提供了广阔的空间。
4.电子领域金属基复合材料电导率高,散热性能优良,因此广泛用于电子产品的外壳材料、散热片等方面的制造。
粉末冶金工艺在复杂零件制备中的应用

粉末冶金工艺在复杂零件制备中的应用粉末冶金工艺是一种重要的金属材料加工技术,通过将金属粉末压制成形,然后进行高温烧结,从而制造出各种复杂的零件。
粉末冶金工艺具有成本低、生产效率高、能耗低等优点,因此在复杂零件制备中有广泛的应用。
首先,粉末冶金工艺可以制备出具有复杂形状和内部结构的零件。
传统的加工方法可能会受到几何形状的限制,而粉末冶金工艺可以灵活地调整粉末的成型方式,从而制造出各种复杂形状的零件,如内孔、螺纹、齿轮等。
这些零件在一些特殊的工程领域中得到广泛应用,例如航空航天、汽车制造等。
其次,粉末冶金工艺可以制备出具有多种材料组成的零件。
在一些特殊的工程要求中,需要零件具有复合材料的特性,而传统的加工方法难以实现。
而粉末冶金工艺可以将不同材料的粉末混合在一起,并且可以通过控制烧结参数,使各种材料之间充分结合,从而制备出具有复合材料特性的零件。
再次,粉末冶金工艺可以制备出具有高精度和精细的表面特性的零件。
粉末冶金工艺可以通过控制粉末的尺寸和形状以及烧结参数等,使得零件的尺寸和形状精度高,表面粗糙度小,从而满足一些对零件的高精度要求。
同时,粉末冶金工艺还可以制备出具有特殊功能表面的零件,例如具有疏水、疏油、耐磨等特性的表面。
最后,粉末冶金工艺可以实现批量生产,并且可以高效利用材料。
粉末冶金工艺可以将金属粉末高效压制成形,同时可以通过粉末的再利用,减少材料的浪费。
由于粉末冶金工艺的工艺稳定性好,生产效率高,因此可以实现批量生产,满足大规模生产的需求。
总之,粉末冶金工艺在复杂零件制备中具有重要的应用价值。
通过粉末冶金工艺,可以制备出具有复杂形状和内部结构的零件,具有多种材料组成的零件,具有高精度和精细的表面特性的零件,并且可以实现批量生产并高效利用材料。
粉末冶金工艺的应用在提高零件质量和生产效率,推动工业发展等方面发挥着重要的作用。
粉末冶金工艺在复杂零件制备中的应用已经广泛涉及到各个领域,包括航空航天、汽车制造、机械加工等等。
粉末冶金材料的应用
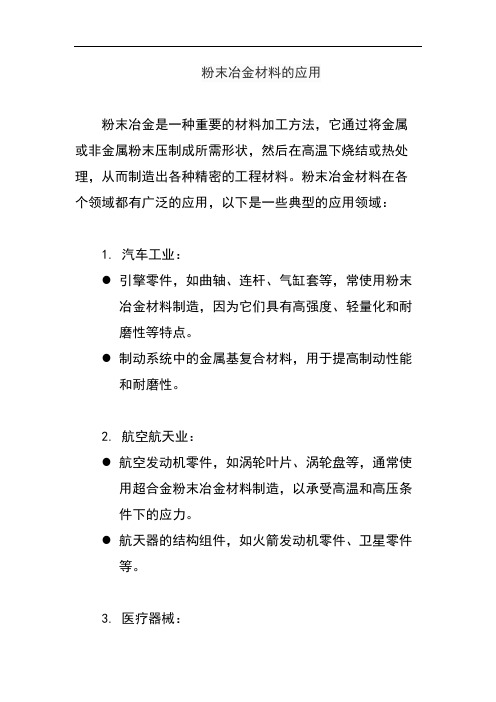
粉末冶金材料的应用粉末冶金是一种重要的材料加工方法,它通过将金属或非金属粉末压制成所需形状,然后在高温下烧结或热处理,从而制造出各种精密的工程材料。
粉末冶金材料在各个领域都有广泛的应用,以下是一些典型的应用领域:1. 汽车工业:●引擎零件,如曲轴、连杆、气缸套等,常使用粉末冶金材料制造,因为它们具有高强度、轻量化和耐磨性等特点。
●制动系统中的金属基复合材料,用于提高制动性能和耐磨性。
2. 航空航天业:●航空发动机零件,如涡轮叶片、涡轮盘等,通常使用超合金粉末冶金材料制造,以承受高温和高压条件下的应力。
●航天器的结构组件,如火箭发动机零件、卫星零件等。
3. 医疗器械:●人工关节、牙科植入物和医用工具等医疗器械中,粉末冶金材料常用于制造耐腐蚀、生物相容性好的部件。
4. 电子和电气工程:●电子电路板上的金属化连接器、封装材料和导电粘合剂中常使用粉末冶金材料。
●用于磁性元件、电感器和传感器的软磁材料,如铁氧体粉末。
5. 工具和刀具:●刀片、铣刀、钻头、齿轮和锯片等切削工具常使用粉末冶金材料制造,因为它们具有高硬度、耐磨性和耐热性。
●硬质合金(碳化钨等)用于制造切削刀具。
6. 磁性材料:●用于电机、变压器、传感器和磁盘驱动器的永磁体材料。
●电感线圈和电子元件的软磁材料。
7. 能源产业:●用于太阳能电池和燃料电池的材料。
●用于储能系统中的电池材料。
总的来说,粉末冶金材料在制造业中发挥着重要作用,因为它们具有高度可控性、高精度和多种定制化特性,可以满足各种应用的要求。
由于粉末冶金材料的广泛适用性和优越性能,它们在现代工程和科学领域中扮演着不可或缺的角色。
粉末冶金产品及应用
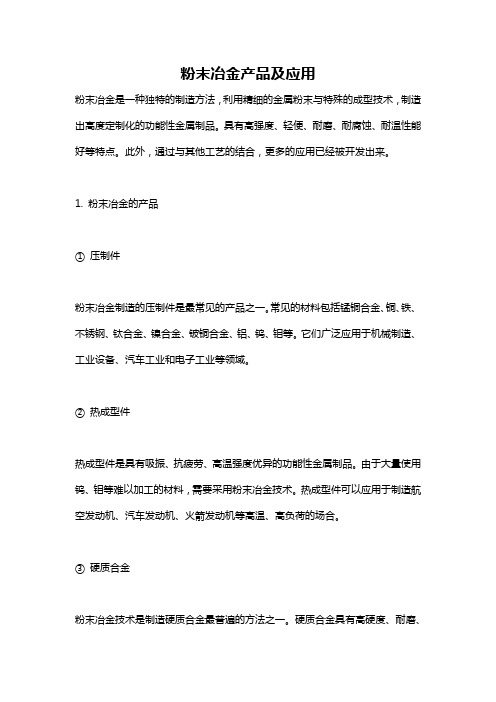
粉末冶金产品及应用粉末冶金是一种独特的制造方法,利用精细的金属粉末与特殊的成型技术,制造出高度定制化的功能性金属制品。
具有高强度、轻便、耐磨、耐腐蚀、耐温性能好等特点。
此外,通过与其他工艺的结合,更多的应用已经被开发出来。
1. 粉末冶金的产品①压制件粉末冶金制造的压制件是最常见的产品之一。
常见的材料包括锰铜合金、铜、铁、不锈钢、钛合金、镍合金、铍铜合金、铝、钨、钼等。
它们广泛应用于机械制造、工业设备、汽车工业和电子工业等领域。
②热成型件热成型件是具有吸振、抗疲劳、高温强度优异的功能性金属制品。
由于大量使用钨、钼等难以加工的材料,需要采用粉末冶金技术。
热成型件可以应用于制造航空发动机、汽车发动机、火箭发动机等高温、高负荷的场合。
③硬质合金粉末冶金技术是制造硬质合金最普遍的方法之一。
硬质合金具有高硬度、耐磨、耐腐蚀、高温强度优异等特点。
硬质合金主要应用于机械制造、采矿、化工等行业。
④金属陶瓷合成材料另一种重要的粉末冶金产品是金属陶瓷合成材料。
金属陶瓷具有低密度、高强度、抗磨损、抗腐蚀、高温抗氧化性等优点。
金属陶瓷主要应用于制造刀片、钻头、飞机发动机涡轮叶片等领域。
2. 粉末冶金的应用①汽车领域粉末冶金技术已经广泛应用于汽车制造。
其中最重要的应用是用于制造发动机和自动变速器零件,如齿轮、轴承、凸轮、气门座圈,它们具有高精密、高强度、低摩擦、低噪音等优点。
②医疗领域粉末冶金技术应用于医疗领域已成为一种趋势。
粉末冶金技术在制造人造关节和骨骼修复材料方面表现出色。
利用粉末冶金技术,可以制造出性能优良的不锈钢、钛合金、铬钼合金等医疗用材料。
③食品加工及包装粉末冶金技术在食品加工和包装领域也有广泛的应用。
粉末冶金可以制造高度纯净的食品加工设备,如研磨器和切割机。
此外,粉末冶金也可以制造出具有自我润滑、抗腐蚀性能的包装材料。
总之,随着技术的发展,粉末冶金正变得更加成熟和广泛应用。
粉末冶金的产品不仅可以应用于传统制造企业,还可以应用于新兴领域,如能源、环保等领域。
粉末冶金的名词解释

粉末冶金的名词解释粉末冶金是一种先进的金属加工技术,它是通过将金属或非金属材料粉末进行成型和烧结而制造出零件或产品的过程。
相较于传统的金属加工方法,粉末冶金具有独特的优势和应用领域。
本文将对粉末冶金进行解释,并讨论其在不同领域的应用。
一、粉末冶金的工艺过程粉末冶金的工艺过程主要包括粉末制备、成型和烧结三个阶段。
粉末制备是将金属或非金属材料通过不同的方法制备成粉末。
常见的方法包括机械破碎、球磨、水热法和煅烧等。
通过这些方法可以控制粉末的颗粒大小和形状,以满足不同材料和应用的需求。
成型是将制备好的粉末放入模具中,通过力的作用进行成型。
成型方法常见的有压力成型、注射成型和挤压成型等。
通过成型,粉末可以被固化成具有初步形状的零件。
烧结是将成型后的零件进行高温处理,使粉末颗粒之间发生结合并形成固体。
这个过程中,粉末颗粒会扩散,表面能降低,从而使其相互连接,形成具有一定强度和密度的零件。
二、粉末冶金的优势粉末冶金相较于传统的金属加工方法,具有以下优势:1. 原材料利用率高。
粉末冶金可以直接利用原材料制备成粉末,大大减少了废料的产生。
同时,可以使用廉价原材料和废料来制备粉末,降低成本。
2. 零件成型精度高。
粉末冶金可以通过模具成型,在模具的作用下零件形状和尺寸可以精确控制,成型精度高。
3. 可以制造复杂形状和孔隙材料。
由于粉末可以在模具中充分填充,而且可以通过加工制造出复杂形状和孔隙材料。
4. 可以制造具有特殊性能的材料。
通过控制粉末的成分和制备过程,可以制造出具有特殊性能的材料,如陶瓷材料、合金材料等。
三、粉末冶金的应用领域粉末冶金广泛应用于各个领域,以下是几个常见的应用领域:1. 汽车工业。
粉末冶金用于制造汽车零部件,如发动机活塞、齿轮和制动系统等。
由于粉末冶金可以制造出高强度、低摩擦系数和高耐磨性的材料,适用于汽车工业的要求。
2. 电子工业。
粉末冶金用于制造电子器件和元器件,如继电器、电容器和磁体等。
粉末冶金可以制造出具有特殊性能的材料,满足微电子技术的要求。
制备金属材料的技术和应用

制备金属材料的技术和应用金属材料是现代工业的基础材料之一,广泛应用于各种制造和加工过程中。
金属材料的制备技术不断发展,各种新型材料不断涌现,这些材料的应用范围也越来越广泛。
一、传统金属材料的制备技术1. 熔铸法熔铸法是最传统的金属材料制备技术之一,也是应用最广泛的方法。
熔铸法适用于制备各种合金和纯金属材料。
熔铸法的基本原理是将金属或金属合金加热到熔点,在熔化状态下通过特定的操作方式,将其倒入模具中或在特定的工艺条件下制成棒材、板材等形状。
2. 粉末冶金法粉末冶金法是一种金属材料制备的重要技术,它采用微米尺度的金属粉末作为原料,并通过压制、烧结或热等方法将其加工成材料。
粉末冶金法可以制备复杂的形状和结构,还可以制备高强度、高硬度、高耐磨等特殊性能的材料。
3. 拉伸法拉伸法是一种金属材料制备的传统方式。
拉伸法的原理是将金属材料加热到一定温度,然后通过拉伸外力将其变形,使其达到一定的形状和尺寸。
二、新型金属材料的制备技术1. 3D打印技术3D打印技术是目前最为热门的金属材料制备技术之一。
利用3D打印技术,可以在计算机辅助下将金属材料精细地制成各种三维形状。
这种技术不仅可以制备各种形状的金属制品,还可以制备各种复杂的内部结构和空洞结构。
2. 等离子喷涂技术等离子喷涂技术是一种新型的金属材料制备技术,利用等离子体技术将金属粉末制成涂层。
这种技术具有制作高性能、高应力、耐热、耐化学腐蚀的薄膜等特点,适用于高温、高压、腐蚀性环境下的应用。
3. 碳化物浸渍技术碳化物浸渍技术是一种新型的金属材料制备技术,利用气相物理或化学方法将碳化物材料浸渍到金属基底中。
这种技术具有制备高性能的复合材料、高强度、耐磨、耐腐蚀等特点,可以广泛应用于工业生产中。
三、金属材料的应用金属材料应用范围广泛,涉及到各个领域和行业。
以下是几个典型的应用领域:1. 机械制造金属材料在机械制造领域中发挥着重要的作用,可以制造车辆、机器人、船舶等各种机械装备。
粉末冶金工艺在生产中的应用

粉末冶金工艺在生产中的应用
粉末冶金工艺是一种利用金属或非金属粉末作为原料,通过成型和烧结等工艺制造零部件的方法。
在工业生产中,粉末冶金工艺被广泛应用于制造各种金属零部件,具有许多独特的优势和特点。
粉末冶金工艺可以实现材料的高效利用。
在传统的加工方法中,通常需要大量的原材料来制造零部件,而粉末冶金工艺可以将原材料直接制成粉末,避免了材料的浪费。
此外,粉末冶金工艺还可以实现材料的高纯度和均匀性,提高了零部件的质量和性能。
粉末冶金工艺可以制造复杂形状的零部件。
由于粉末可以在成型过程中填充到任何形状的模具中,并且可以在高温下烧结成固体,因此粉末冶金工艺可以制造出各种复杂形状的零部件,包括内部结构复杂的零部件,这是传统加工方法无法实现的。
粉末冶金工艺还可以实现批量生产,提高生产效率。
在粉末冶金工艺中,可以通过一次成型和一次烧结来制造大量相同或类似的零部件,避免了传统加工方法中需要逐个加工的繁琐过程,大大提高了生产效率。
粉末冶金工艺还可以制造具有特殊性能的材料。
通过粉末冶金工艺可以制备出各种合金材料,包括高强度、耐磨、耐腐蚀等特殊性能的材料,满足了不同领域对材料性能的需求。
总的来说,粉末冶金工艺在工业生产中具有广泛的应用前景。
随着
科技的不断进步和工艺的不断完善,粉末冶金工艺将更好地满足各种行业对高质量、高效率、特殊性能材料的需求,推动着工业制造的发展。
粉末冶金工艺在生产中的应用具有独特优势,为各行业提供了更多可能性。
随着工艺的不断创新和完善,相信粉末冶金工艺将在未来得到更广泛的应用,并为工业生产带来更多的发展机遇。
金属粉末冶金在模具制造中的应用研究

金属粉末冶金在模具制造中的应用研究现代制造业的发展离不开高精度模具的应用,而金属粉末冶金技术作为一种先进的制造工艺,已经在模具制造领域发挥了重要作用。
本文将探讨金属粉末冶金在模具制造中的应用研究,包括其原理、优势以及面临的挑战。
一、金属粉末冶金的原理金属粉末冶金是利用金属粉末通过成型、烧结等工艺制备零件的技术。
其基本原理是将金属粉末与其他添加剂按一定比例混合,然后通过压制成型和烧结工艺,使金属粉末颗粒之间发生冶金结合,形成致密的金属零件。
金属粉末冶金技术具有灵活性强、材料利用率高、生产过程环保等优势。
通过调节金属粉末成分和粒度,可以实现不同材料性能的调控和优化。
因此,在模具制造中应用金属粉末冶金技术,可以有效提高模具的材料性能和使用寿命。
二、金属粉末冶金在模具制造中的应用1. 陶瓷模具制造金属粉末冶金技术在陶瓷模具制造中有广泛应用。
传统的陶瓷模具制造过程需要使用粘土等材料,且成本高、制作周期长。
而采用金属粉末冶金技术制造陶瓷模具,不仅可以提高模具的耐磨性和耐腐蚀性,还能够减少生产周期和成本。
2. 超硬模具制造超硬材料如金刚石、立方氮化硼等具有极高的硬度和耐磨性,常用于制造需要高度精密加工的工具。
金属粉末冶金技术可以制备具有高硬度的超硬合金材料,用于制造高效的模具。
这些模具不仅可以提高工具的寿命和加工效率,还可以降低加工过程中的能耗和废料产生。
3. 复合材料模具制造复合材料在航天航空、汽车、电子等行业得到了广泛应用。
而金属粉末冶金技术可以制备具有优良综合性能的复合材料模具,用于制造复杂的复合材料产品。
这些模具可以提供更高的加工精度和复杂度,满足现代工业对产品的多样化需求。
三、金属粉末冶金在模具制造中面临的挑战虽然金属粉末冶金技术在模具制造中具有广泛应用前景,但目前仍面临一些挑战。
首先,金属粉末的成本较高,制造成本较传统工艺高。
随着技术的进步和规模效应的发挥,相信金属粉末冶金技术的成本将会逐渐降低。
- 1、下载文档前请自行甄别文档内容的完整性,平台不提供额外的编辑、内容补充、找答案等附加服务。
- 2、"仅部分预览"的文档,不可在线预览部分如存在完整性等问题,可反馈申请退款(可完整预览的文档不适用该条件!)。
- 3、如文档侵犯您的权益,请联系客服反馈,我们会尽快为您处理(人工客服工作时间:9:00-18:30)。
题目:粉末冶金法在金属制备中的应用*名:***学号: ************ 年级: 2012级专业:化学学院:理学院成绩:目录1粉末冶金的定义 (1)2粉末冶金工艺 (2)3粉末冶金技术的特点 (2)3.1低的生产成本 (2)3.2高的性能 (2)4粉末冶金材料的应用 (3)4.1应用于机械零件的制造 (3)4.2应用于合金性能的改进 (3)4.2.1铝合金 (3)4.2.2高合金材料 (3)4.2.3高温合金 (4)4.2.4磁性材料 (4)4.3应用于新型材料的研制 (4)4.3.1金属基复合材料 (4)4.3.2弥散强化高温材料 (4)4.4梯度功能材料 (4)4.5其他方法的应用 (4)4.5.1超塑性材料 (4)4.5.2高抗蚀性材料 (4)4.6粉末冶金材料在国民经济各部门的应用 (4)5.主要不足之处 (6)6.粉末冶金的发展前景 (6)6.1向全致密化发展 (6)6.2向高性能化、集成化和低成木等方向发展 (7)6.3粉木治金产业化发展 (7)7.展望 (7)8.参考文献 (7)粉末冶金法在金属制备中的应用摘要:从机械零件的制造、合金性能的改进及新型材料的研制及制备工艺等方面综述了粉末冶金技术的应用与发展。
粉末冶金作为一种独特的零件制造技术,向高致密化、高性能化、集成化和低成木等方向发展,木文分析了粉末冶金的定义涵和该技术的主要功能,重点对粉末冶金技术的应用进行慨括。
关键词:粉末冶金、制备工艺、应用、发展近30 年来,粉末冶金技术获得了飞速的发展,许多“后致密化”技术(即在传统的粉末冶金方法的烧结工序之后增加一些致密化工序,如复压、复烧、锻造、拉制、挤压等) 、热等静压、注射成型以及机械合金化等工艺的研制成功,克服了传统粉末冶金制品由于致密性低而导致使用上的技术障碍,使粉末冶金技术得以推广应用。
到目前为止,粉末冶金技术既是高强度、高密度、形状复杂、无切削、少切削零件的制造工艺,又是生产新型材料的加工方1.粉末冶金的定义:末冶金是制取金属粉末或用金属粉末(或金属粉末与非金属粉末的混合物)作为原料,经过成形和烧结,制取金属材料、复合材料以及各种类型制品的工业技术。
目前,粉末冶金技术已被广泛应用于交通、机械、电子、航空航天、兵器、生物、新能源、信息和核工业等领域,成为新材料科学中最具发展活力的分支之一。
粉末冶金技术具备显著节能、省材、性能优异、产品精度高且稳定性好等一系列优点,非常适合于大批量生产。
2..2 粉末冶金工艺粉末冶金技术的大致工艺过程如下原料粉末+添加剂合金元素粉末、润滑剂、成形剂↓成形模压、CIP、粉浆浇注、轧制、挤压、温压、注射成形等↓烧结加压烧结、热压、HIP等↓粉末冶金材料或粉末冶金零部件—后续处理3 粉末冶金技术的特点3.1低的生产成本低的生产成本能耗小生产率高材料利用率高设备投资少。
↑↑↑工艺流程短和加工温度低加工工序少少切削、无切削粉末冶金原理补充完整版材料成分设计灵活、微观结构可控由工艺特征决定能制造普通熔练法不可能生产的材料如W-Cu、SnO2-Ag、WC-Co、Cu-石墨、金属陶瓷TiC-NiCr,Al2O3-Ni或Cu,TiB2-Cu等、弥散强化材料Al2O3-Cu Al2O3-Al Y2O3-Fe基合金、粉末超合金非相图成分、难熔金属及其合金如钨钼、含油轴承、过滤材料等。
.3.2高的性能粉末高速钢、粉末超合金因无成分偏析和稳定的组织细的晶粒而性能优于熔炼法制备的合金纳米材料金属陶瓷梯度复合材料梯度硬质合金。
4 粉末冶金材料的应用4.1应用于机械零件的制造现代粉末冶金技术在机械零件制造中的应用范围正沿两个方向扩展:一是制取承受高负荷的零件;二是制取几何尺寸复杂、尺寸精度高的零件,并使最终机械加工量减至最小限度。
在承受高负荷零件的制造中,后致密化技术中的锻造(以下简称粉末锻造) 和热等静压起到了非常重要的作用。
4.2应用于合金性能的改进随着对材料要求的不断提高,传统的铸锭冶金( IM) 方法对合金的性能改进已趋于顶峰,粉末冶金(PM) 技术成为改进和研制合金的一种手段4.2.1 铝合金到目前为止,用PM 方法改进或研制的铝合金按性能可分为4 类:高强度,高弹性模量,低密度,热强和功能铝合金。
7090 , 7091 , MR61 , MR64 , CW67 , IN9021 和IN9052 属PM 高强度铝合金。
前5 种是RSP(快冷合金粉末) 合金,是在7 ×××系合金的基础上添加少量的Co ,Zr 或Cr 作为附加剂和稳定剂而制得的;后两种是用机械合金化方法制得的,它们在抗拉强度、抗蚀性、断裂韧性等方面具有良好的综合性能。
PM 高弹性模量、低密度铝合金大多数是在IN2024 合金的基础上(也有降低Cu ,Mg 含量及用Zr取代Cr 的) 添加1 %~3 %Li 的铝锂合金。
Al - Cu -Li - Zr ,Al - Li - Zr 及Al - Cu - Mg - Li - Zr 是发展高弹性模量、低密度铝合金的主要方向4.2.2 高合金材料高合金材料如高速钢采用PM 方法生产,可得到碳化分布均匀的细晶粒组织,具有较高的抗弯强度和冲击强度,韧性可提高50 % ,热处理变形约为IM 高速钢的1/ 10 。
还大大提高了耐磨削性能,用它制造的刀具寿命可提高3~5 倍。
此外,粉末冶金制品的工序较少,材料利用率可由50 %~60 %提高到95 %。
4.2.3 高温合金采用先进的粉末冶金技术可以制得纯净的合金粉末,并且合金组织均匀,无偏析。
采用PM 技术,可使现有的高温合金的工作温度提高100 ℃,疲劳寿命提高100 倍,蠕变强度大约提高20%4.2.4 磁性材料与熔铸方法相比,PM 磁性材料有如下优点:可以生产出具有特殊性能的磁性材料,如铁氧体、磁介质等;能用单畴粉末制造出优质永磁材料;材料晶粒细、强度大、无缩孔及偏析等弊病。
用PM 方法制造体积小、形状复杂的小型磁体具有极大的竞争力。
采用PM 方法生产材料最显著的一个特点是材料设计的自由度高,通过改变材料的成分或工艺方法以改变材料的晶体结构,可获得不同功能的材料。
4.3应用于新型材料的研制4.3.1 金属基复合材料用于制造金属基复合材料的工艺方法有: PM 法、压铸法和搅拌铸造法。
与搅拌铸造法相比, PM 法制取复合材料的温度低,减轻了基体与增强体之间的界面反应,减少了界面上硬质化合物的生成,从而得到较好力学性能的材料; PM 法可以制造用搅拌铸造法不能制取的材料,如用搅拌铸造法制造碳化硅钛基复合材料时,碳化硅晶须溶于钛合金基体,采用PM 法可避免这一现象发生。
4.3.2 弥散强化高温材料近年来弥散强化铝合金研究的有:Al - C ,Al - TiC ,Al - ZrC ,Al - NbC ,Al - Cr2O3 ,Al - MoC ,Al WC 等,其中Al - C 材料已用于内燃机活塞,它的强化相是Al4C。
属间化合物的研究主要采用机械合金化方法,4.4梯度功能材料目前,梯度功能材料的开发仅有热功能梯度材料。
它是基于航宇结构、核聚变反应堆和未来高速飞行的需要而研制的。
它的一面是高强度的金属材料,另一面为耐高温粉末材料(如高温结构陶瓷、金属间化合物) ,中间层为高强度的纤维(如氧化锆、碳化硅纤维等) 和微粒(如陶瓷或金属间化合物粉末,碳粒或玻璃微粒等) 。
这种结构既保证了高强度和高耐热性,又保证了材料的组织与工作的温度梯度相适应,减小了在高温下受热表面和金属材料层间的热膨胀失配而引起的应力4.5.其他方法的应用4.5.1 超塑性材料采用PM 法可获得极细的晶粒,合金界面上的氧化物质点和析出相均能起钉扎晶界的作用,使材料具有高的组织稳定性。
另外, PM 法制备的超塑性材料还可实现高应变速率的超塑性,高的应变速率能提高超塑性成形效率。
因此,在材料的超塑性研究中, PM技术受到了极大的关注并取得了可喜的成果。
4.5.2 高抗蚀性材料高的抗腐蚀和抗应力腐蚀能力是粉末冶金的主要特性,洛克希德- 乔治亚公司已用PM 铝合金设计和制造了3 个试验性飞机零件,其中两个是挤压梁,一个是锻造襟翼滑轨加强缘条。
这些零件安装在3 架洛克希德C - 141 运输机上进行试验。
它的寿命比用IM法加工的零件长得多,使更换费用大大减少。
4.6粉末冶金材料在国民经济各部门的应用由于粉末冶金材料及其零部件较其它加工方法制造的零部件的成本低以及其性能能满足特种要求因而粉末冶金零部件和材料在国民经济各部门的应用十分广泛:汽车制造业的各种粉末冶金零部件、机加工工业中的切削用硬质合金和粉末高速钢刀具、电子工业用粉末冶金磁性材料和电触头、计算机的原器件用电子封装材料、机械制造业的减磨零件和结构部零件、航天航空业中的耐热材料及结构零部件、家用电器中的微型轴承、原子能材料、武器系统和作战平台高效、低成本、建材工业用金刚石工具材料等、环保与化工用催化剂及过滤器件等。
总之粉末冶金材料与人们的生活密不可分在国民经济和国防建设中发挥重大作用。
而且随着粉末冶金新技术和新工艺的开发与应用粉末冶金的技术上的优越性也更加显著应用领域不断扩大。
如温压成形技术的出现使粉末冶金零部件在轿车上的应用水平由原来的13.2Kg/辆增加到22Kg/辆大大扩大了粉末冶金零部件的应用范围。
5.主要不足之处.由于受设备容量的限制传统粉末冶金工艺制造的粉末冶金零部件的尺寸较其它加工方法铸造机加工等材料韧性不高零部件的形状复杂程度和综合力学性能有限等。
正被新型成形技术如无模成形技术温压成形注射成形逐步克服。
6.粉末冶金的发展前景6. 1、向全致密化发展粉末冶金的重点是超细粉末和纳米粉的制备技术,快速冷凝制备非晶、准晶和微晶粉末技术,机械合金化技术,自蔓延高温合成技术,粉末粒度、结构、形貌、成分控制技术。
总的趋势是向超细、超纯、粉末特性可控方向发展。
建立以“净近形成形”技术为中心的各种新型固结技术及其过程模过程理论,如粉末注射成形、挤压成形、喷射成形、温压成形、粉末锻造等。
建立以“全致密化”为主要目标的新型固结技术及其过程模拟技术6.2向高性能化、集成化和低成木等方向发展粉末冶金新的成形技术层出不穷,如:粉末注射成形、温压成形、流动温压成形、喷射成形、高速压制成形等新技术不断涌现。
近目前,粉末冶金技术正向着高致密化、高性能化、集成化和低成木等方向发展。
有代表性的铁基合金,将向大体积的精密制品,高质量的结构零部件发展;制造具有均匀显微组织结构的、加工困难而完全致密的高性能合金;用增强致密化过程来制造一般含有混合相组成的特殊合金;制造非均匀材料、非晶态、微晶或者亚稳合金;加工独特的和非一般形态或成分的复合零部件。