内燃机铝活塞技术要求
活塞、活塞环标准
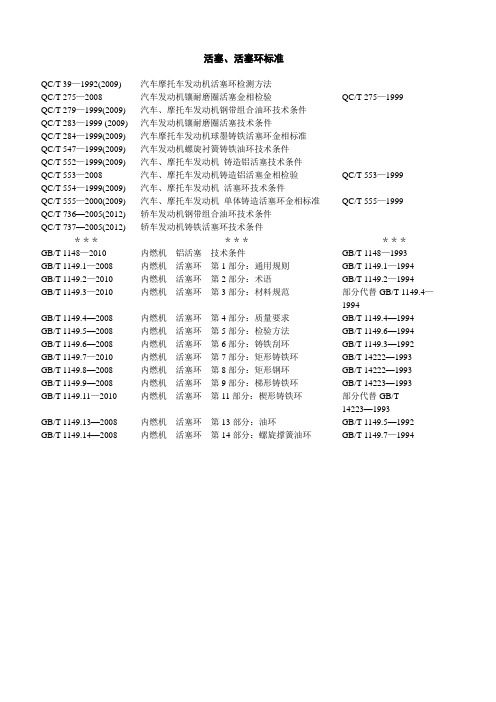
活塞、活塞环标准QC/T 39—1992(2009) 汽车摩托车发动机活塞环检测方法QC/T 275—2008 汽车发动机镶耐磨圈活塞金相检验QC/T 275—1999QC/T 279—1999(2009) 汽车、摩托车发动机钢带组合油环技术条件QC/T 283—1999 (2009) 汽车发动机镶耐磨圈活塞技术条件QC/T 284—1999(2009) 汽车摩托车发动机球墨铸铁活塞环金相标准QC/T 547—1999(2009) 汽车发动机螺旋衬簧铸铁油环技术条件QC/T 552—1999(2009) 汽车、摩托车发动机铸造铝活塞技术条件QC/T 553—2008 汽车、摩托车发动机铸造铝活塞金相检验QC/T 553—1999QC/T 554—1999(2009) 汽车、摩托车发动机活塞环技术条件QC/T 555—2000(2009) 汽车、摩托车发动机单体铸造活塞环金相标准QC/T 555—1999QC/T 736—2005(2012) 轿车发动机钢带组合油环技术条件QC/T 737—2005(2012) 轿车发动机铸铁活塞环技术条件*********GB/T 1148—2010 内燃机铝活塞技术条件GB/T 1148—1993GB/T 1149.1—2008 内燃机活塞环第1部分:通用规则GB/T 1149.1—1994GB/T 1149.2—2010 内燃机活塞环第2部分:术语GB/T 1149.2—1994GB/T 1149.3—2010 内燃机活塞环第3部分:材料规范部分代替GB/T 1149.4—1994GB/T 1149.4—2008 内燃机活塞环第4部分:质量要求GB/T 1149.4—1994GB/T 1149.5—2008 内燃机活塞环第5部分:检验方法GB/T 1149.6—1994GB/T 1149.6—2008 内燃机活塞环第6部分:铸铁刮环GB/T 1149.3—1992GB/T 1149.7—2010 内燃机活塞环第7部分:矩形铸铁环GB/T 14222—1993GB/T 1149.8—2008 内燃机活塞环第8部分:矩形钢环GB/T 14222—1993GB/T 1149.9—2008 内燃机活塞环第9部分:梯形铸铁环GB/T 14223—1993GB/T 1149.11—2010 内燃机活塞环第11部分:楔形铸铁环部分代替GB/T14223—1993GB/T 1149.13—2008 内燃机活塞环第13部分:油环GB/T 1149.5—1992GB/T 1149.14—2008 内燃机活塞环第14部分:螺旋撑簧油环GB/T 1149.7—1994。
活塞的加工工艺
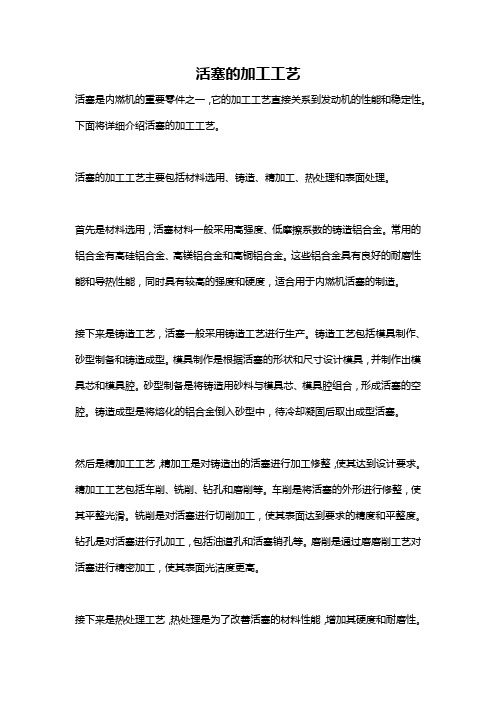
活塞的加工工艺活塞是内燃机的重要零件之一,它的加工工艺直接关系到发动机的性能和稳定性。
下面将详细介绍活塞的加工工艺。
活塞的加工工艺主要包括材料选用、铸造、精加工、热处理和表面处理。
首先是材料选用,活塞材料一般采用高强度、低摩擦系数的铸造铝合金。
常用的铝合金有高硅铝合金、高镁铝合金和高铜铝合金。
这些铝合金具有良好的耐磨性能和导热性能,同时具有较高的强度和硬度,适合用于内燃机活塞的制造。
接下来是铸造工艺,活塞一般采用铸造工艺进行生产。
铸造工艺包括模具制作、砂型制备和铸造成型。
模具制作是根据活塞的形状和尺寸设计模具,并制作出模具芯和模具腔。
砂型制备是将铸造用砂料与模具芯、模具腔组合,形成活塞的空腔。
铸造成型是将熔化的铝合金倒入砂型中,待冷却凝固后取出成型活塞。
然后是精加工工艺,精加工是对铸造出的活塞进行加工修整,使其达到设计要求。
精加工工艺包括车削、铣削、钻孔和磨削等。
车削是将活塞的外形进行修整,使其平整光滑。
铣削是对活塞进行切削加工,使其表面达到要求的精度和平整度。
钻孔是对活塞进行孔加工,包括油道孔和活塞销孔等。
磨削是通过磨磨削工艺对活塞进行精密加工,使其表面光洁度更高。
接下来是热处理工艺,热处理是为了改善活塞的材料性能,增加其硬度和耐磨性。
常用的热处理方法包括退火、固溶处理和人工时效处理等。
退火是将活塞加热至一定温度后缓慢冷却,以消除内部应力,增加其韧性。
固溶处理是将活塞加热至一定温度后迅速冷却,使其硬化。
人工时效处理是在固溶处理后对活塞进行再加热,以进一步提高其硬度和强度。
最后是表面处理工艺,表面处理是为了增加活塞的表面硬度和耐磨性。
常用的表面处理方法包括喷涂、电镀和气体渗碳等。
喷涂是将特殊材料喷涂在活塞表面,形成一层保护层。
电镀是将金属镀层沉积在活塞表面,使其增加硬度和耐磨性。
气体渗碳是将活塞加热至一定温度后,使碳原子渗透到活塞表面,形成碳化层。
综上所述,活塞的加工工艺包括材料选用、铸造、精加工、热处理和表面处理。
活塞工艺技术要求

活塞工艺技术要求
活塞是一种常用于内燃机和压缩机等设备中的零件,它的质量和加工精度直接影响着设备的性能和使用寿命。
为了保证活塞的质量,需要严格遵循一系列活塞工艺技术要求。
首先,活塞的材料应选择高强度、高耐磨性和高导热性的材料,例如铝合金材料、铸钢材料等。
材料的选择应根据活塞的工作条件和负荷情况进行合理选择,以提高活塞的强度和耐磨性。
其次,活塞的制造要保持较高的加工精度。
活塞的外形尺寸、轴向度和表面粗糙度等都需要符合相关的技术要求。
特别是活塞的直径、圆度和圆柱度等尺寸误差应控制在规定范围内,以确保活塞与气缸之间的密封性能。
第三,活塞的表面质量要求高。
活塞的表面应经过精细研磨和处理,以提高活塞的光洁度和硬度。
一般情况下,活塞的表面粗糙度应控制在0.2-0.8μm范围内,硬度应达到45-70HRC,
以提高活塞的磨损性能和耐腐蚀性能。
此外,在活塞的制造过程中,还需要注意以下几点:一是活塞的冷热处理要适当。
活塞的冷热处理对活塞的强度和硬度有重要影响,应根据材料和工艺要求进行合理选择,以提高活塞的力学性能。
二是活塞的研磨过程要规范。
活塞的研磨过程中应注意保持适当的切削速度和切削量,避免产生过量的热量,以防止活塞表面产生裂纹。
三是活塞的装配要精确。
活塞和气缸的配合间隙应适当,既要保证活塞的自由度,又要保证活塞与气缸之间的密封性。
总之,活塞工艺技术要求是保证活塞质量的重要保证。
只有严格遵循工艺要求,合理选择材料、控制加工精度和提高表面质量,才能制造出质量可靠、性能优越的活塞,有效提高设备的使用寿命和性能。
活塞机械加工工艺及其夹具设计

活塞机械加工工艺及其夹具设计活塞是内燃机中重要的零件之一,其精度和质量直接影响到整个内燃机的稳定性和性能。
活塞机械加工工艺及其夹具设计是影响活塞质量的关键因素,在内燃机制造领域有着重要的地位。
1.活塞机械加工工艺活塞加工包括材料选择、毛坯制备、粗加工、精加工、表面处理等多个环节,其中材料选择和表面处理对于活塞质量影响比较大。
以下是活塞机械加工的工艺流程和注意事项:1.1 材料选择活塞最常用的材料是铝合金和铸铁,其中铝合金的比重小、导热性好、强度高、耐腐蚀性强等特点使其成为首选材料。
但铝合金的切削性差,易产生毛刺和毛边,加工时需要合适的切削速度和切削液。
1.2 毛坯制备毛坯制备是活塞加工的基础工艺,其精度和表面质量对于后续的加工和质量影响非常大。
毛坯制备包括铸造、锻造、挤压等多种方法,其中铸造最常用。
为保证毛坯质量,需要进行毛坯检测和分类,分类标准为长度、材质、直径、表面质量等。
1.3 粗加工粗加工是将毛坯切削成近似形状的加工,主要包括车削、镗削、铣削等。
粗加工要求高速度、大进刀量、高转速等,以提高加工效率和降低成本。
1.4 精加工精加工是将粗加工的活塞进行进一步的修整和加工,主要包括磨削、车削、铣削、划线等。
精加工需要较高的加工精度和表面质量,以保证活塞的质量和稳定性。
1.5 表面处理表面处理主要是对活塞表面进行喷砂、酸洗、阳极氧化等处理,以提高表面质量和耐磨性。
表面处理是活塞加工的最后一个环节,也是影响活塞使用寿命和质量的关键因素。
2.夹具设计夹具是活塞加工的必要辅助工具,其设计和选择直接关系到活塞的加工质量和效率。
以下是活塞加工中常用的夹具类型:2.1 三爪卡盘三爪卡盘是最常用的夹具之一,其优点是结构简单、使用方便、维护成本低等。
三爪卡盘能够适应不同直径和长度的毛坯,但对于形状较为复杂的毛坯夹紧效果不够理想。
2.2 四爪卡盘四爪卡盘是一种比较精度高的夹具,其优点是能够适应不同形状和大小的毛坯,夹紧力度均匀。
活塞制造工艺

活塞制造工艺活塞制造是机械制造领域中的重要工艺之一。
活塞作为内燃机的关键部件,其制造质量直接影响着发动机的性能和可靠性。
本文将从活塞制造的材料选择、工艺流程和质量控制等方面进行介绍。
一、材料选择活塞通常采用铝合金材料制造,因为铝合金具有良好的热膨胀性能、轻质高强度、导热性能好等优点。
常用的铝合金材料有铝硅合金、铝铜合金和铝镁合金等。
根据发动机的使用条件和要求,选择合适的铝合金材料可以提高活塞的耐磨性、耐热性和抗疲劳性能。
二、工艺流程活塞的制造工艺主要包括锻造、精整、热处理和表面处理等环节。
1. 锻造:活塞的锻造一般采用冷挤压工艺。
首先将铝合金材料加热至一定温度,然后放入锻压机中进行挤压成型。
挤压过程中要控制好挤压速度和力度,以保证活塞的形状和尺寸精度。
2. 精整:锻造后的活塞需要进行精整加工,包括车削、铣削和钻孔等工序。
通过精细加工,可以使活塞的表面光滑度和尺寸精度达到要求,为后续的热处理和表面处理做好准备。
3. 热处理:活塞的热处理是提高其硬度和耐磨性的关键步骤。
常用的热处理方法有淬火和时效处理。
淬火可以使活塞表面形成一层硬度高的硬化层,提高耐磨性;时效处理则可以进一步提高活塞的强度和硬度。
4. 表面处理:为了提高活塞的润滑性能和耐腐蚀性能,常常对活塞进行表面处理。
常用的表面处理方法有氧化、硬质阳极氧化和涂层等。
氧化处理可以形成一层致密的氧化层,提高活塞的耐腐蚀性;硬质阳极氧化可以形成一层硬度高的氧化层,进一步提高活塞的耐磨性;涂层可以在活塞表面形成一层保护膜,提高润滑性能和耐腐蚀性能。
三、质量控制活塞的制造过程中需要进行严格的质量控制,以确保活塞的质量符合要求。
1. 原材料检验:对铝合金材料进行化学成分分析和力学性能测试,确保材料的质量稳定。
2. 在制品检验:对锻造后的活塞进行尺寸检测、表面质量检查和力学性能测试,排除不合格品。
3. 热处理过程控制:严格控制热处理的温度、时间和冷却速度,以确保活塞的热处理效果符合要求。
内燃机车基本技术规定

内燃机车基本技术规定柴油机第12条机体及机座检修要求:一、检查机体、机座状态,并清扫干净。
主轴承盖、稳压箱及齿轮箱不许有裂纹。
二、气缸盖栽丝无裂纹及松缓,其螺纹不得损坏或严重磨损。
三、主轴承螺栓及螺母不许有裂纹,其螺纹不得损坏或严重磨损,螺母与主轴承盖及机体的接触面须平整。
螺母紧固力矩标准为180~185公斤/米,或相应的螺栓伸长量为0.35~0.40毫米。
四、主机油道、活塞冷却油道架修时应冲洗干净。
焊修后须进行10公斤/平方厘米的水压试验,保持5分钟无泄漏。
活塞冷却油喷嘴不得有裂纹和松动。
五、机体与机座应配对组装,更换其中任一个时,组装后与齿轮箱结合面的不平齐度不大于0.05毫米。
六、机座的弹性支座橡胶元件不得有老化、龟裂和破损。
七、油底壳经焊修后应灌水作密封性能试验,保持30分钟无渗漏。
第13条曲轴及其附件检修要求:一、曲轴不许有裂纹存在。
若用磁力探伤检查,探伤后须作退磁处理。
二、曲轴均衡块螺栓不得松缓,紧固力矩标准为65~70公斤/米。
三、曲轴油道须清洗干净,油封杯、油封垫及螺栓必须按原位组装,更换油封垫时要严格按图纸加工。
组装后曲轴油道应进行10公斤/平方厘米的油压试验,保持5分钟无泄漏。
四、减振器各部不许有裂纹、渗油。
惯性体、摩擦环不许有严重拉伤,更换摩擦环时,两侧摩擦环对惯性体端面凸出量之差应不大于0.05毫米。
减振器装机后应作用良好。
五、分解时,曲轴输出法兰、正时齿轮与曲轴锥度配合面的接触面积应不小于75%,其轴向压入量应分别为18±0.5毫米和8—1毫米。
六、弹性联轴节橡胶应无老化、破损,允许有不超过3处的开裂,但总长不大于100毫米,深度不大于10毫米,开裂超过上述规定时应作扭转试验,扭矩2000公斤·米时扭转角为7.5°~9.5°,裂纹不得扩大,扭转试验合格者可继续使用。
架修时应更换弹性联轴节内的润滑脂、检查轴承状态。
更换弹性联轴节内的零件后应作动平衡试验,不平衡度不大于100克厘米。
CA型铝活塞的机械加工工艺设计及夹具设计
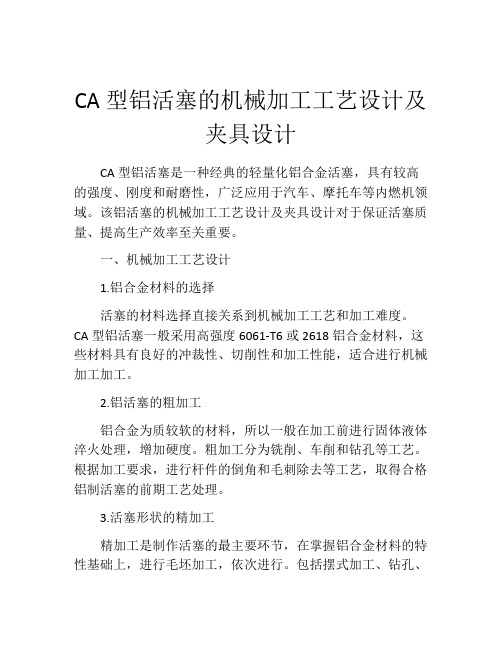
CA型铝活塞的机械加工工艺设计及夹具设计CA型铝活塞是一种经典的轻量化铝合金活塞,具有较高的强度、刚度和耐磨性,广泛应用于汽车、摩托车等内燃机领域。
该铝活塞的机械加工工艺设计及夹具设计对于保证活塞质量、提高生产效率至关重要。
一、机械加工工艺设计1.铝合金材料的选择活塞的材料选择直接关系到机械加工工艺和加工难度。
CA型铝活塞一般采用高强度6061-T6或2618铝合金材料,这些材料具有良好的冲裁性、切削性和加工性能,适合进行机械加工加工。
2.铝活塞的粗加工铝合金为质较软的材料,所以一般在加工前进行固体液体淬火处理,增加硬度。
粗加工分为铣削、车削和钻孔等工艺。
根据加工要求,进行杆件的倒角和毛刺除去等工艺,取得合格铝制活塞的前期工艺处理。
3.活塞形状的精加工精加工是制作活塞的最主要环节,在掌握铝合金材料的特性基础上,进行毛坯加工,依次进行。
包括摆式加工、钻孔、铰孔、铣削、车削等一系列工艺,即依靠转子刀、基轴刀、下铰刀、电极等工具加工出不同形状的特殊要求铝活塞。
4.活塞最终加工最终加工是把铝活塞的形状和尺寸处理到最终要求的环节。
活塞的表面光洁度、平直度、孔壁平行度等一系列尺寸工艺要求及表面质量,需采用很高的精度加工工艺。
最终加工工艺包括打磨、车削、铣削、锥度切削、精加工对称度等一系列工艺。
二、夹具设计1.夹具类型夹具是在机械加工过程中固定工件,以保证被加工工件的稳定度和精度度。
针对要求高精度度的铝活塞,一般采用独立式和多点式制作夹具,以供活塞的形状稳定和安全过程中不得变化的要求。
2.夹具结构铝活塞在机械加工过程中,其形状是从上向下的,进而须考虑在夹具上的稳定性及安全。
夹具上选用铝合金材料制作,其对铝活塞材质影响很小。
夹具上采用行星伺服电机及单元控制系统可满足大批量加工的自动化加工工艺的要求。
三、总结CA型铝活塞的机械加工工艺设计及夹具设计需要全面考虑加工工艺与夹具工艺,同时,加工工具及设备的选择,还需要考虑成本与效益问题。
发动机活塞的设计讲解
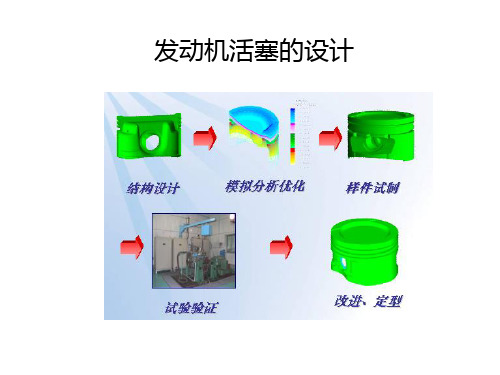
3、减压腔的设计 把油环紧邻气环间的环岸设计成直径小于1mm左右,形成“减压腔”, 使刮下的机油减压并形成泄油分配腔,降低机油消耗。如372发动机图 中71尺寸
4、活塞环槽增强方法 活塞环槽的磨损常常是限制活塞使用寿命的一个重要因素,为了保护 和加强活塞环槽,可在铝合金活塞环槽部位注入由耐热合金钢制造的环 槽护圈。
发动机活塞的设计
一、活塞的工作条件和基本要求
(一)、工作条件 1、活塞的机械负荷 P=πD2(Pz-1)x10-1/4 (N) 往复惯性应力:Pjmax=Grω 2(1+λ ) (N) 2、活塞的热负荷 A、传导产生的热负荷:在内燃机工作过程中,活塞顶直接 与燃气接触,燃气的最高温度一般达到2000℃左右。 B、能量转换:活塞与缸孔摩擦生成的热。 (二)、基本要求 1、结构要求 合适的壁厚和合理的形状,保证足够的强度和刚度前提下, 结构简单、轻巧,截面变化要圆滑,减少应力集中,采用强 度好、比重小的材料,头部和裙部采用适当的处理方式。
5、裙部表面处理和加工要求 A、表面处理方式: 在我们国内常见的处理方式是:磷化、镀锡、印刷石墨,在国 外还用了许多先进的处理方式
B、表面加工要求 裙部一般加工对粗糙度和表面波纹进行控制
6、裙部的膨胀控制 横向隔热槽和纵向补偿槽、椭圆裙、镶钢片
为了减少铝活塞裙部的热膨胀量,有的汽油机活塞在活塞销座中 镶有热膨胀系数低的“恒范钢片”(含镍33%~36%,线膨胀系数 约为铸铝合金的1/10)以牵制裙部的热膨胀
ห้องสมุดไป่ตู้
4、顶部最小厚度: 汽油机δ=(0.06~0.1)D, 柴油机δ=(0.1~0.2)D 为了提高活塞顶部的刚度和强度,增大散热面积,常常增 加各种形状的肋条(在活塞背面增加方格形、横形和直肋条)
- 1、下载文档前请自行甄别文档内容的完整性,平台不提供额外的编辑、内容补充、找答案等附加服务。
- 2、"仅部分预览"的文档,不可在线预览部分如存在完整性等问题,可反馈申请退款(可完整预览的文档不适用该条件!)。
- 3、如文档侵犯您的权益,请联系客服反馈,我们会尽快为您处理(人工客服工作时间:9:00-18:30)。
GB/T 1148—2010(2010-11-10发布2011-03-01实施)代替GB/T 1148—1993前言本标准是对GB/T 1148—1993《内燃机铝活塞技术条件》的修订。
本标准与GB/T 1148—1993相比,技术内容的主要变化如下:——更换了第3部分的图片,新增了一些部位名称;——技术要求中增加了环岸外圆直径、环槽底圆直径、环槽宽度的尺寸公差,对燃烧室容积、挡圈槽尺寸以及定位销的尺寸作了规定,并对质量小于400g的活塞质量差作了细化规定;技术要求中新增了对内冷油腔、清洁度、表面处理的规定;对部分检验方法作了必要的修改和增加。
本标准自实施之日起代替GB/T 1148—1993。
本标准由中国机械工业联合会提出。
本标准由全同内燃机标准化技术委员会(SAC/TC 177)归口。
本标准起草单位:上海内燃机研究所、山东滨州渤海活塞股份有限公司、成都银河动力股份有限公司、石家庄金刚内燃机零部件集团有限公司。
本标准主要起草人:苏晴华、林风华、马学军、文均、刘津东、姜殿昌、任德忠。
本标准所代替标准的历次版本发布情况为:——GB 1148—1982、GB/T 1148—1993。
内燃机铝活塞技术条件Internal combustion engines—Aluminium pistons—Specifications1范围本标准规定了内燃机铸造铝活塞的各部位名称、技术要求、检验方法、检验规则及标识、包装、运输和贮存。
本标准适用于气缸直径不大于200mm的往复活塞式内燃机铸造铝活塞(以下简称活塞)。
2规范性引用文件下列文件中的条款通过本标准的引用而成为本标准的条款。
凡是注日期的引用文件,其随后所有的修改单(不包括勘误的内容)或修订版均不适用于本标准,然而,鼓励根据本标准达成协议的各方研究是否可使用这些文件的最新版本。
凡是不注日期的引用文件,其最新版本适用于本标准。
GB/T 228金属材料室温拉伸试验方法(GB/T 228—2002,eqv ISO 6892:1998)GB/T 893.1孔用弹性挡圈——A型GB/T 893.2孔用弹性挡圈——B型GB/T 1149.1内燃机活塞环第1部分:通用规则(GB/T 1149.12008,ISO 6621—4:2003)GB/T 1800.1—2009产品几何技术规范(GPS)极限与配合第1部分:公差、偏差和配合的基础(ISO 286—1:1988,MOD)GB/T 19582004产品几何量技术规范(GPS)形状和位置公差检测规定GB/T 2828.1计数抽样检验程序第1部分:按接收质量限(AQL)检索的逐批检验抽样计划(GB/T 2828.1——2003,ISO 2859—1:1999,IDT)GB/T 3821中小功率内燃机清洁度测量方法GB/T 4957非磁性基体金属上非导电覆盖层覆盖层厚度测量涡流法(GB/T 4957—2003,ISO 2360:1982,IDT)JB/T 6289内燃机铸造铝活塞金相检验GJB 1580A变形金属超声检验方法3活塞各部位名称见表1、图1。
4技术要求4.1总则产品应按经规定程序批准的产品图样及技术文件制造。
4.2材料本体材料:铸造铝合金。
4.3力学性能和体积稳定性活塞应经热处理,其抗拉强度、硬度及体积稳定性(活塞直径D的残余胀大量)应符合表2规定。
但同批活塞,其硬度差应不大于30个布氏硬度单位,同—只活塞硬度差不大于10个布氏硬度单位。
4.4金相组织活塞的金相组织应符合JB/T 6289或其他有关标准的规定。
4.5尺寸公差4.5.1活塞环岸外圆直径、裙部外圆(控制点)直径、环槽底圆直径公差应符合表3规定。
4.5.2活塞裙部外圆直径应按最大尺十分组,分组十七号用I、Ⅱ、Ⅲ……表示,其顺序由最小尺寸组至最大尺寸组。
裙部直径公差小于0.02 mm的可不分组。
4.5.3销孔直径公差应符合以下规定:a)销孔直径大于18 mm时:其直径公差应符合GB/T 1800.1规定的IT5;销孔直径不大于18mm时,其直径公差为IT6。
b)活塞销孔直径应按最小尺寸分组,分组代号用l、2、3……表示,其顺序由最小尺寸组至最大尺寸组。
销孔直径公差小于0.01 mm的可不分组。
4.5.4压缩高度公差:顶部表面机加工的汽油机用活塞为0.2mm,柴油机用活塞为0.1mm;顶部表面不机加工的活塞为0.4 mm。
4.5.5环槽宽度公差:平行环槽的宽度公差为0.03mm;梯形环槽的宽度公差为0.02 mm。
4.6形状和位置公差4.6.1环槽上、下两侧面各素线对裙部轴线的垂直度为25:0.07。
4.6.2环槽上、下两侧面各素线对裙部轴线的端面圆跳动为0.05mm。
4.6.3环槽厂侧面的平面度应符合表4规定。
4.6.4头部外圆、环岸外圆对裙部轴线的同轴度为φ0.06 mm。
4.6.5环槽底圆对裙部轴线的径向圆跳动为0.20 mm。
4.6.6裙部内表面轴线对裙部轴线的同轴度应符合表5规定。
4.6.7销孔轴线对裙部轴线且垂直于裙部轴线方向的位置度为0.20 mm。
4.6.8销孔轴线对裙部轴线的垂直度为100:0.035。
4.6.9销孔圆柱度应符合表6规定。
4.6.10销孔轴线的直线度为φ0.06 mm。
4.6.11挡圈槽底圆对销孔轴线的圆跳动为0.30 mm。
4.6.12裙部为椭圆时,椭圆长轴应与销孔轴线乘直,其最大偏移应符合表7规定。
4.7加工表面粗糙度参数值4.7.1外圆表面:R a为1μm~5μm。
4.7.2销孔表面:R a应不大于0.63μm。
4.7.3环槽上、下两侧面:R a应不大于0.63μm;耐磨镶圈环槽上、下两侧面:R a应不大于1.25μm。
4.7.4环槽底圆表面:R a应不大于6.3μm。
4.7.5其他加工表面:按产品图样规定。
4.8外观质量4.8.1活塞铸造表面应光洁,不允许有裂纹、飞边及高于1mm的分模界线。
4.8.2加工表面缺陷应符合以下规定:a)活塞所有加工表面不允许有裂纹和毛刺。
b)两段销孔表面,每段自内端至本段全长的1/4范围内和挡圈槽部位不允许有任何肉眼可见的孔眼。
每段销孔其余部位的孔眼应符合表8规定,同时允许在lcm2面积内存在不超过10个直径≤0.3 mm的微小缩松。
c)裙部外圆表面允许存在的孔眼,应符合表9的规定,孔眼间距必须不小于15 mm,距边缘不小5 mm,同时允许在1 cm2面积内存在不超过10个直径≤0.3 mm的微小缩松。
d)活塞止口端面和止口内圆表面允许各有一个孔眼。
其最大直径应不大于1.5mm,深度应不大于1.0mm。
e)活塞顶面和环槽上、下两平面不允许有肉眼可见的孔眼。
f)头部外圆、环岸外圆、环槽底圆表面上,允许有肉眼可见的最大直径应不大于0.4mm 的孔眼,在1cm2面积内应不大于5个,其分布面积应不大于所在部位面积的5%。
4.9成品活塞的质量差4.9.1单个成品活塞的实际质量与公称质量之差应符合表10规定。
4.9.2同一台内燃机所用同一质量组活塞的质量差应符合表11规定。
4.10燃烧室容积除非另有规定,燃烧室容积的允许偏差见表12。
4.11档圈槽4.11.1挡圈槽的横截面可以是圆形或矩形,圆形截面挡圈槽尺寸见图2和表13,矩形截面档卷槽尺寸按GB/T 893.1、GB 893.2执行。
4.11.2挡圈槽间距公差为0.3mm。
4.12防转定位销二冲程内燃机活塞环的防转定位销分为侧面防转定位销和内圆面防转定位销。
它们的形状和尺寸见图3和表14。
4.13耐磨镶圈4.13.1耐磨镶圈与铝活塞本体的粘结面积率:非增压发动机应不小于85%,增压发动机应不小于93%。
4.13.2耐磨镶圈与铝活塞本体粘结界面单个缺陷长度:非增压发动机应不大于圆周长的10%,增压发动机应不大于圆周长的5%。
4.13.3耐磨镶圈与铝活塞本体粘结处两个缺陷之间的间距:必须不小于圆周长的9%。
4.13.4耐磨镶圈与铝活塞本体粘结处上下侧面缺陷的重叠度:非增压发动机应不大于圆周长的4%,增压发动机应不大于圆周长的1%。
4.13.5镶圈活塞加工完毕后,耐磨镶圈环岸的实际宽度应不小于基本宽度的0.6倍,且最小不得小于0.8mm。
注:耐磨镶圈环岸的基本宽度等于耐磨镶圈的全宽减去环槽宽度,再除以2。
4.13.6耐磨镶圈在镶圈活塞上相对于活塞中心线的倾斜度不大于0.38 mm。
4.14内冷油腔4.14.1内冷油腔中心线相对于活塞中心线的位置度要求:D≤150mm,不大于φ1.2mm;D>150mm,不大于φ2.5 mm。
4.14.2内冷油腔上下位置的偏移要求:D≤150 mm,不大于±1mm;D>150mm,不大于±1.2 mm。
4.15清洁度活塞清洁度包括杂质总量和颗粒度。
颗粒度值取颗粒任一投影形状的最大对角长度。
4.15.1汽油机用活塞清洁度见表15。
4.15.2柴油机用活塞清洁度见表16。
4.16表面处理4.16.1采用硬质阳极氧化处理的活塞,顶面氧化膜厚度为0.04mm~0.08mm,环槽氧化膜厚度为0.01mm±0.003 mm。
4.16.2活塞裙部采用石墨化处理时,石墨层厚度为0.0015mm±0.005mm。
4.16.3活塞采用镀锡处理时,镀锡层厚度为0.001mm~0.002 mm。
4.17维修用活塞维修用配件活塞外圆尺寸应加大,规格为:+0.25 mm、+0.50mm、+0.75mm、+1.00 mm、+1.25 mm五种。
5检验方法5.1抗拉强度供检验活塞高温、常温抗拉强度的试样,应在销孔至顶面之间截取,若尺寸不够,允许在头部横向截取。
如头部尺寸不够,可以用与活塞同样材料、同样铸造工艺及同样热处理的金属试棒,取所测得值的0.8倍,应符合本标准表2规定。
试样按GB/T 228制备,高温抗拉强度必须加热至300℃±5℃后保温0.5h测定。
5.2硬度硬度的测定部位应在活塞顶面上环槽底圆与内壁之间的实心部位测定。
测定点应沿销孔轴线方向测两点,垂直于销孔轴线方向测一点,共测三点,并算出硬度差。
5.3体积稳定性在活塞环岸部选择一横截面,在销孔轴线方向和垂直销孔轴线方向测量其外径尺寸。
再将活塞加热到250℃±5℃,保温5h,自然冷却到室温后,在加热前相同的测量点上重新测出二个方向直径各自的变化量,并算出百分比。
5.4金相组织金相组织按JB/T 6289或其他有关标准规定的方法进行检验。
5.5销孔直径销孔直径测量见图4。
5.6形位公差5.6.1测量环槽上、下两侧面各素线对裙部轴线的垂直度,以精加工裙部外圆的定位基准作测量基准,见图5,在对称方向测两处,取其平均值。
5.6.2测量环槽上、下两侧面对裙部轴线的端面圆跳动,以精加工裙部外圆的定位基准作测量基准,被测活塞应旋转一周,见图6。