橡胶硫化体系详解
硫化体系PPT课件

硫化体系的热力学原理
熵变效应
热稳定性
在硫化过程中,橡胶分子链由无序状 态转变为有序的网状结构,导致熵变 效应,影响硫化反应的平衡状态。
硫化体系在高温下的热稳定性取决于 橡胶分子的热分解温度和交联键的热 稳定性。
自由能变化
硫化过程中,橡胶分子链的自由能变 化与交联密度、交联键类型等因素有 关,自由能变化会影响硫化体系的稳 定性。
硫化体系的动力学原理
硫化速率
硫化体系的动力学原理主要研究 硫化速率与反应条件的关系,如 温度、压力、促进剂种类和浓度
等。
硫化动力学模型
通过建立硫化动力学模型,可以描 述硫化过程中各阶段的反应速率常 数、活化能等参数,有助于优化硫 化工艺和提高产品质量。
促进剂的作用
在硫化过程中,促进剂可以加速硫 化反应速率,缩短硫化时间,提高 生产效率。
03 硫化体系的应用
在橡胶工业中的应用
轮胎制造
硫化体系在轮胎制造过程中起到 至关重要的作用,能够提高轮胎 的耐磨性、抗疲劳性和抗湿滑性, 从而提高轮胎的性能和使用寿命。
橡胶管和密封件
硫化体系在橡胶管和密封件的生 产中也有广泛应用,能够改善橡 胶制品的弹性和耐久性,提高产
品的质量和可靠性。
橡胶鞋和手套
硫化体系与其他技术的结合
硫化技术与纳米技术的结合
利用纳米材料的特点,如高比表面积、高活性等,与硫化体系结合,制备出具有 优异性能的橡胶复合材料。
硫化技术与智能材料的结合
将硫化技术与智能材料技术相结合,制备出具有自感知、自适应、自修复等功能 的智能橡胶材料。
硫化体系在环保方面的应用
低VOC排放
通过优化硫化体系配方,降低生产过 程中VOC(挥发性有机化合物)的排 放,减少对环境的污染。
【详细】橡胶的各种硫化体系讲解!(收藏)
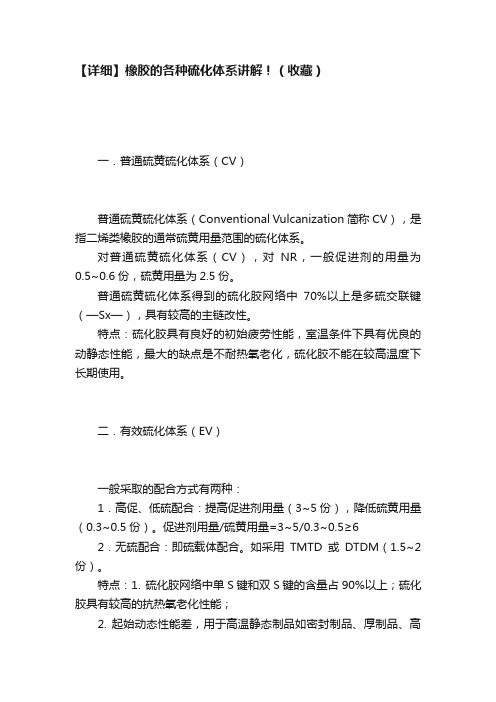
【详细】橡胶的各种硫化体系讲解!(收藏)一.普通硫黄硫化体系(CV)普通硫黄硫化体系(Conventional Vulcanization简称CV),是指二烯类橡胶的通常硫黄用量范围的硫化体系。
对普通硫黄硫化体系(CV),对NR,一般促进剂的用量为0.5~0.6份,硫黄用量为2.5份。
普通硫黄硫化体系得到的硫化胶网络中70%以上是多硫交联键(—Sx—),具有较高的主链改性。
特点:硫化胶具有良好的初始疲劳性能,室温条件下具有优良的动静态性能,最大的缺点是不耐热氧老化,硫化胶不能在较高温度下长期使用。
二.有效硫化体系(EV)一般采取的配合方式有两种:1.高促、低硫配合:提高促进剂用量(3~5份),降低硫黄用量(0.3~0.5份)。
促进剂用量/硫黄用量=3~5/0.3~0.5≥6 2.无硫配合:即硫载体配合。
如采用TMTD或DTDM(1.5~2份)。
特点:1. 硫化胶网络中单S键和双S键的含量占90%以上;硫化胶具有较高的抗热氧老化性能;2. 起始动态性能差,用于高温静态制品如密封制品、厚制品、高温快速硫化体系。
三.半有效硫化体系(SEV)为了改善硫化胶的抗热氧老化和动态疲劳性能,发展了一种促进剂和硫黄的用量介于CV和EV之间的硫化体系,所得到的硫化胶既具有适量的多硫键,又有适量的单、双硫交联键,使其既具有较好的动态性能,又有中等程度的耐热氧老化性能,这样的硫化体系称为半有效硫化体系(SEV)。
用于有一定的使用温度要求的动静态制品。
一般采取的配合方式有两种:1.促进剂用量/硫用量=1.0/1.0=1(或稍大于1);2.硫与硫载体并用,促进剂用量与SEV中一致。
NR的三种硫化体系配合如下表所示:配方成分C V EV高促低硫无硫配合Semi—EV高促低硫硫\硫载体并用SNOB STMT DDMD T 2.50.60.53.0 1.10.6 1.11.11.5 1.51.5 0.60.6四.高温快速硫化体系随着橡胶工业生产的自动化、联动化,高温快速硫化体系被广泛采用,如注射硫化、电缆的硫化等。
橡胶硫化的资料
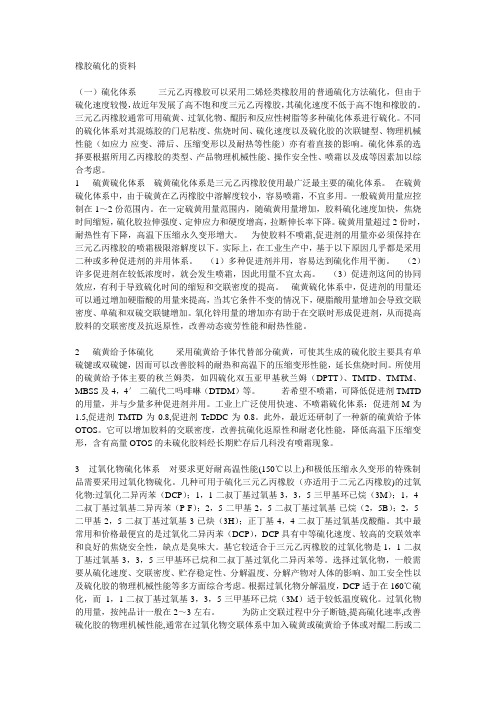
橡胶硫化的资料-(一)硫化体系三元乙丙橡胶可以采用二烯烃类橡胶用的普通硫化方法硫化,但由于硫化速度较慢,故近年发展了高不饱和度三元乙丙橡胶,其硫化速度不低于高不饱和橡胶的。
三元乙丙橡胶通常可用硫黄、过氧化物、醌肟和反应性树脂等多种硫化体系进行硫化。
不同的硫化体系对其混炼胶的门尼粘度、焦烧时间、硫化速度以及硫化胶的次联键型、物理机械性能(如应力-应变、滞后、压缩变形以及耐热等性能)亦有着直接的影响。
硫化体系的选择要根据所用乙丙橡胶的类型、产品物理机械性能、操作安全性、喷霜以及成等因素加以综合考虑。
1 硫黄硫化体系硫黄硫化体系是三元乙丙橡胶使用最广泛最主要的硫化体系。
在硫黄硫化体系中,由于硫黄在乙丙橡胶中溶解度较小,容易喷霜,不宜多用。
一般硫黄用量应控制在1~2份范围内。
在一定硫黄用量范围内,随硫黄用量增加,胶料硫化速度加快,焦烧时间缩短,硫化胶拉伸强度、定伸应力和硬度增高,拉断伸长率下降。
硫黄用量超过2份时,耐热性有下降,高温下压缩永久变形增大。
为使胶料不喷霜,促进剂的用量亦必须保持在三元乙丙橡胶的喷霜极限溶解度以下。
实际上,在工业生产中,基于以下原因几乎都是采用二种或多种促进剂的并用体系。
(1)多种促进剂并用,容易达到硫化作用平衡。
(2)许多促进剂在较低浓度时,就会发生喷霜,因此用量不宜太高。
(3)促进剂这间的协同效应,有利于导致硫化时间的缩短和交联密度的提高。
硫黄硫化体系中,促进剂的用量还可以通过增加硬脂酸的用量来提高,当其它条件不变的情况下,硬脂酸用量增加会导致交联密度、单硫和双硫交联键增加。
氧化锌用量的增加亦有助于在交联时形成促进剂,从而提高胶料的交联密度及抗返原性,改善动态疲劳性能和耐热性能。
2 硫黄给予体硫化采用硫黄给予体代替部分硫黄,可使其生成的硫化胶主要具有单硫键或双硫键,因而可以改善胶料的耐热和高温下的压缩变形性能,延长焦烧时间。
所使用的硫黄给予体主要的秋兰姆类,如四硫化双五亚甲基秋兰姆(DPTT)、TMTD、TMTM、MBSS及4,4′-二硫代二吗啡啉(DTDM)等。
橡胶的硫化体系

橡胶的硫化体系橡胶是一种高分子化合物,通常由天然橡胶或合成橡胶组成,其应用范围非常广泛。
但是,橡胶具有高度的粘性和变形性,在高温下易于熔化,这些特性使得橡胶在运输和储存过程中变得非常困难。
为了克服这些问题,橡胶制造业采用了许多方法,其中最常见的方法是橡胶的硫化。
橡胶的硫化历史可以追溯到19世纪末,当时化学家发现橡胶可以通过将其与硫或硫化物混合,然后在高温下进行处理,从而获得一种经过硫化的新材料。
这种新材料具有更高的强度、耐磨性和化学稳定性,逐渐取代了纯天然橡胶。
然而,它仍然存在着一些局限性,例如:硫化时间长,生产效率低;活化空间小,不利于大规模生产等等问题。
随着科技的不断发展,人们对橡胶的硫化体系进行了不断探索和研究,并提出了许多新的改进方案和方法。
橡胶硫化的过程可以通过化学反应方程式来表示:硫化前橡胶+ Caucas 橡胶+ Caucas硫化后橡胶+ Caucas 橡胶- Caucas - 橡胶(其中,Caucas 是用于促进反应的硫化促进剂。
)橡胶的硫化分为自然硫化和人工硫化。
自然硫化是指橡胶在自然条件下,如阳光、温度和湿度等影响下,慢慢发生硫化反应。
人工硫化则是将促进剂和硫化剂添加到橡胶中,然后进行加热处理,从而更快地发生化学反应,使橡胶硫化。
橡胶硫化的体系可以分为多种,其中经典的体系是硫氧化物体系。
这种体系基于硫和氧的反应,利用硫化促进剂、硫化剂和杂原料等组成。
在这种体系中,硫化剂与促进剂的比例非常重要,控制好比例可以在橡胶硫化的过程中获得更好的效果。
当然,还有许多其他的硫化体系,如酚酞氧化物的硫化体系、过氧化氢的硫化体系等等。
在橡胶的硫化过程中,促进剂的作用非常关键,它可以加速反应速度,降低硫化温度,并提高硫化效率。
在经典的硫氧化物体系中,常用的促进剂有苯胺类促进剂、吡啶类促进剂、咪唑类促进剂等。
不同种类的促进剂具有不同的作用机理和反应速率,因此在橡胶硫化过程中的选择和使用非常重要。
另一个重要的组分是杂原料。
橡胶硫化体系详解

硫化是胶料通过生胶分子间交联,形成三维网络结构,制备硫化胶的基本过程。
不同的硫化体系适用于不同的生胶。
橡胶硫化的研究一直在深入持久地进行,研究的目的主要是改进硫化胶的力学性能及其它性能,简化及完善工艺过程,降低硫化时有害物质的释放等等。
下面有针对性地简述当前使用的硫化体系。
不饱和橡胶通常使用如下几类硫化体系。
1.以硫黄,有机二硫化物及多硫化物、噻唑类、二苯胍类,氧化锌及硬脂酸为主的硫化剂。
这是最通用的硫化体系。
但所制得的硫化胶的耐热氧老化性能不高。
2.烷基酚醛树脂。
3.多卤化物(如用于聚丁二烯橡胶、丁苯橡胶及丁腈橡胶的六氯乙烷)、六氯-对二甲苯。
4.双官能试剂[如醌类、二胺类、偶氮及苯基偶氮衍生物(用于丁基橡胶及乙丙橡胶)等。
5.双马来酰亚胺,双丙烯酸酯。
两价金属的丙烯酸酯(甲基丙烯酸酯)、预聚醚丙烯酸酯。
6.用于硫化饱和橡胶的有机过氧化物。
饱和橡胶硫化不同种类的饱和橡胶时,可使用不同的硫化体系。
例如,硫化三元乙丙橡胶时,使用有机过氧化物与不饱和交联试剂,如三烯丙基异氰脲酸酯(硫化剂TAIC)。
硫化硅橡胶时也可使用有机过氧化物。
乙烯基硅橡胶硫化时可在催化剂(Pt)参与条件下进行。
含卤原子橡胶或含功能性基团的橡胶。
聚氯丁二烯橡胶、氯磺化聚乙烯及氯化丁基橡胶等是最常用的含氯橡胶。
硫化氯丁橡胶通常采用ZnO与MgO的并用物,以乙撑硫脲(NA-22)、二硫化秋兰姆、二-邻-甲苯基二胍(促进剂BG)及硫黄作硫化促进剂。
硫化氯磺化聚乙烯时可使用如下硫化体系。
1.氧化铝、氧化铅和氧化镁的并用物,以及氧化镁和季戊四醇酯,以四硫化双五甲撑秋兰姆(促进剂TRA)及促进剂DM作硫化促进剂。
2.六次甲基四胺与己二酸及癸二酸盐及氧化镁。
3.有机胺与环氧化物作用的产物。
以下体系可用于氯化丁基橡胶硫化:1.氧化锌与硬脂酸、氧化镁、秋兰姆及苯并噻唑二硫化物等的并用物;2.乙烯基二硫脲与氧化锌及氧化镁的并用物。
3.多羟基甲基酚醛树脂与氧化锌的并用物。
橡胶的硫化体系介绍

橡胶的硫化体系介绍橡胶是一种天然或合成的高分子化合物,具有特殊的弹性和可塑性。
它广泛应用于轮胎、橡胶鞋、管道、密封件等领域。
然而,未经处理的橡胶易老化、自然硬化、热塑性差等缺陷,限制了其使用寿命和性能。
为了克服这些缺陷,橡胶必须进行硫化处理,即向其中引入硫化剂将橡胶分子交联成网状结构,从而增强其硬度、强度、耐磨性和耐化学性等方面的性能。
本文将介绍橡胶硫化体系的基本知识和应用。
1.橡胶的硫化橡胶的硫化是指在适当的温度和压力下,将橡胶与硫化剂反应生成交联链的过程。
硫化剂的作用是将橡胶分子链上的双键和硫醇基之间形成新的硫化键,使其形成硫化链。
随着硫化时间的延长,硫化链交联成网状结构,从而增强了橡胶的强度和硬度。
常见的硫化剂有硫化石灰、含硫羟化合物、代硫酰化合物等。
2.硫化剂的选择选择合适的硫化剂是橡胶硫化体系设计的重要环节。
硫化剂的性质影响着硫化过程的速率和特性。
一般来说,硫化剂的选择应该考虑以下因素:(1) 橡胶的种类和用途。
不同类型的橡胶对硫化剂的适应性不同,在选择硫化剂时应该考虑橡胶本身的特性和使用要求。
(2) 硬度和硫化速率。
硫化剂的种类、含量和硫化条件等因素都会影响硬度和硫化速率,因此选择硫化剂时应该考虑硬度和硫化速率的平衡。
(3) 压力和温度。
硫化剂的选择还应该考虑硫化过程的温度和压力等因素。
(4) 环保和成本。
在选择硫化剂时,还应考虑其环保性和成本因素。
3.橡胶硫化体系的分类橡胶硫化体系主要分为硫磺法和非硫磺法两种。
硫磺法是指使用硫磺作为硫化剂,形成交联链的过程。
硫磺硫化可以在常温下进行,对环境污染小,但硫化速率慢,需要使用促进剂和加热加压等条件来促进硫化。
非硫磺法是指使用非硫磺硫化剂来进行橡胶硫化,如含硫异氰酸酯、含硫醚化合物、含硫羟化合物、代硫酰化合物等。
这些硫化剂可在温和条件下发生反应,硫化速率快,不需要特殊的加热和加压条件,且可降低环境污染。
4.硫化介质的种类硫化介质是指用来促进硫化反应的介质,可以提高反应速率和控制反应条件。
橡胶硫化体系

橡胶硫化体系介绍橡胶硫化体系是指通过加入硫化剂、促进剂和助磺剂等物质,使橡胶分子间发生化学交联反应,形成弹性体的过程。
这个体系在橡胶制品的生产过程中起到了至关重要的作用。
本文将对橡胶硫化体系进行全面、详细、完整且深入地探讨。
硫化剂的作用硫化剂是橡胶硫化体系的核心组成部分,它能够引发橡胶分子间的交联反应。
硫化剂的主要作用有: 1. 引发剂作用:硫化剂能够分解,产生自由基或电离态硫,进而引发橡胶分子的交联反应。
2. 网络形成:硫化剂引发的交联反应使橡胶分子间形成网络结构,增加了橡胶的物理性能,如弹性、耐磨性等。
3. 促进界面反应:硫化剂可以提高橡胶与填料、助剂等其他物质之间的反应活性,增强它们之间的相互作用。
促进剂的作用促进剂常与硫化剂一同使用,它对硫化系统有着重要的调节作用。
促进剂的主要作用有: 1. 提高硫化速度:促进剂能够加快硫化反应的进行,缩短橡胶制品的硫化时间。
2. 改善硫化性能:促进剂能够改善橡胶硫化后的物理性能,如强度、硬度、耐磨性等,使制品具有更好的综合性能。
3. 调节硫化体系:促进剂能够调节硫化体系的活性、稳定性和选择性,提高其适应性和可控性。
助磺剂的作用助磺剂是橡胶硫化体系中的辅助物质,它对硫化反应起到协助作用。
助磺剂的作用主要有: 1. 促进硫化反应:助磺剂与硫化剂共同作用,加速硫化反应的进行,提高交联密度,增强橡胶硫化的效果。
2. 改善反应性能:助磺剂能够调节硫化体系的反应速度、温度敏感性和耐老化性,改善橡胶硫化的性能和稳定性。
硫化体系的选择在实际应用中,选择合适的硫化体系对于橡胶制品的质量和性能至关重要。
硫化体系的选择需要考虑以下几个因素: 1. 橡胶种类:不同种类的橡胶对硫化剂的反应性和选择性有所差异,需要根据橡胶材料的特点进行选择。
2. 硬度要求:不同硫化体系对制品硬度的影响不同,根据制品要求选择合适的硫化体系。
3. 工艺条件:硫化体系的选择还需考虑工艺条件,如硫化温度、硫化时间等。
3橡胶工艺学第二章橡胶的硫化体系
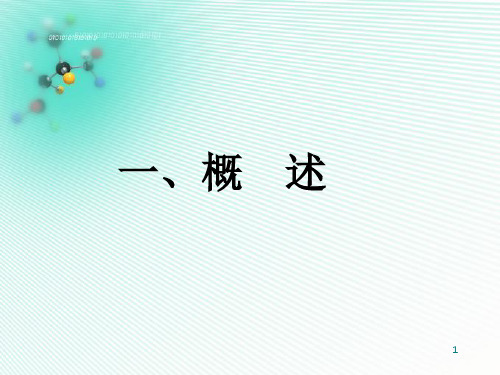
特点:
焦烧时间长,硫化速度快。 适用于合成橡胶的高温快速硫化和厚制
品的硫化。该类促进剂诱导期的长短与 和氨基相连基团的大小数量有关,基团 越大,数量越多,诱导期越长,防焦效 果越好。如DZ>NOBS>CZ。
31
Ⅲ.秋兰姆类:
ห้องสมุดไป่ตู้
结构通式为:
R' S
S
R'
N C Sx C N
R
R
R,R’为烷基,芳基或其它基团
双键 自由基 Or 离子型加成
∵硫化前后双键数目变化不大。
∴反应主要在α-H上反应,以自由基 机理为主。
7
㈡、硫化历程
第一阶段:诱导期,活性剂,促进剂,硫 黄之间相互作用,生成带有多硫促进剂侧 基的橡胶大分子。线型分子,能流动。
第二阶段:交联反应,带有多硫促进剂侧 基的橡胶大分子与橡胶大分子之间发生交 联反应,生成交联键。初期网状分子,已 不能流动。
H, D
NA-22,
CZ
NOBS,
DZ
18
按促进速度分类:
国际上习惯以促进剂M对NR的硫化速度 为标准,以比较促进剂的硫化速度。
慢速级促进剂:H,NA-22 中速级促进剂:D 准速级促进剂:M,DM,CZ,DZ,NOBS 超速级促进剂:TMTD,TMTM 超超速级促进剂:ZDMC,ZDC
英文 简称 ZDM
C ZDC
BZ
PX
基团
R,R’为甲基,M为 锌
R,R’为乙基,M为 锌
R,R’为丁基,M为 锌
R为乙基,R’为苯 基,M为锌
36
特点:
此类促进剂比秋兰姆更活泼。 过渡金属离子使橡胶的不饱和键更易
极化,硫化速度更快,属超超速级酸 性促进剂。 诱导期极短,适用于室温硫化和胶乳 制品的硫化。
- 1、下载文档前请自行甄别文档内容的完整性,平台不提供额外的编辑、内容补充、找答案等附加服务。
- 2、"仅部分预览"的文档,不可在线预览部分如存在完整性等问题,可反馈申请退款(可完整预览的文档不适用该条件!)。
- 3、如文档侵犯您的权益,请联系客服反馈,我们会尽快为您处理(人工客服工作时间:9:00-18:30)。
硫化是胶料通过生胶分子间交联,形成三维网络结构,制备硫化胶的基本过程。
不同的硫化体系适用于不同的生胶。
橡胶硫化的研究一直在深入持久地进行,研究的目的主要是改进硫化胶的力学性能及其它性能,简化及完善工艺过程,降低硫化时有害物质的释放等等。
下面有针对性地简述当前使用的硫化体系。
不饱和橡胶通常使用如下几类硫化体系。
1.以硫黄,有机二硫化物及多硫化物、噻唑类、二苯胍类,氧化锌及硬脂酸为主的硫化剂。
这是最通用的硫化体系。
但所制得的硫化胶的耐热氧老化性能不高。
2.烷基酚醛树脂。
3.多卤化物(如用于聚丁二烯橡胶、丁苯橡胶及丁腈橡胶的六氯乙烷)、六氯-对二甲苯。
4.双官能试剂[如醌类、二胺类、偶氮及苯基偶氮衍生物(用于丁基橡胶及乙丙橡胶)等。
5.双马来酰亚胺,双丙烯酸酯。
两价金属的丙烯酸酯(甲基丙烯酸酯)、预聚醚丙烯酸酯。
6.用于硫化饱和橡胶的有机过氧化物。
饱和橡胶硫化不同种类的饱和橡胶时,可使用不同的硫化体系。
例如,硫化三元乙丙橡胶时,使用有机过氧化物与不饱和交联试剂,如三烯丙基异氰脲酸酯(硫化剂TAIC)。
硫化硅橡胶时也可使用有机过氧化物。
乙烯基硅橡胶硫化时可在催化剂(Pt)参与条件下进行。
含卤原子橡胶或含功能性基团的橡胶。
聚氯丁二烯橡胶、氯磺化聚乙烯及氯化丁基橡胶等是最常用的含氯橡胶。
硫化氯丁橡胶通常采用ZnO与MgO的并用物,以乙撑硫脲(NA-22)、二硫化秋兰姆、二-邻-甲苯基二胍(促进剂BG)及硫黄作硫化促进剂。
硫化氯磺化聚乙烯时可使用如下硫化体系。
1.氧化铝、氧化铅和氧化镁的并用物,以及氧化镁和季戊四醇酯,以四硫化双五甲撑秋兰姆(促进剂TRA)及促进剂DM作硫化促进剂。
2.六次甲基四胺与己二酸及癸二酸盐及氧化镁。
3.有机胺与环氧化物作用的产物。
以下体系可用于氯化丁基橡胶硫化:1.氧化锌与硬脂酸、氧化镁、秋兰姆及苯并噻唑二硫化物等的并用物;2.乙烯基二硫脲与氧化锌及氧化镁的并用物。
3.多羟基甲基酚醛树脂与氧化锌的并用物。
4.二烷基二硫代氨基甲酸锌。
5.羟基芳香化物(间苯二酚、氢醌等)(在室温下)。
硫化羧基橡胶时常使用金属氧化物及过氧化物、多元醇、二元胺及多胺,环氧化物、二异氰酸酯及聚异氰酸酯等。
硫化含胺基的橡胶时常用添加氧化锌的硫黄硫化体系、含卤有机物及环氧树脂等。
硫化含腈基的橡胶时常用氧化物(如MnO2、Sb2O5)硫化物(如CuS)以及添加硫黄的多胺(对于丙烯酸酯橡胶)。
在无硫化剂时,由于聚合物中具有反应能力的官能团之间发生反应。
在弹性体中也有可能生成化学交联键网络。
例如,在高温下,聚氯乙烯及丁腈橡胶并用胶中即有此种情况发生。
非传统硫化体系,近十年来,主要研究内容是硫化过程本身及硫化胶制品在使用过程中的生态问题以及完善硫化工艺、降低焦烧和返原倾向、推广冷硫化等等。
对防止硫化剂特别是硫黄在成品中的喷霜也给予了一定的关注。
通过选择适宜的硫化体系及硫化条件在改进硫化胶及制品性能方面也取得了一些成就。
降低使用硫化体系时的生态危害。
不饱和橡胶的硫化体系中通常都含有硫黄,故目前正在采取一系列措施,以防止硫黄在称量等过程中的飞扬,如可采用造粒工艺。
通常采用硫黄与二环戊二烯、苯乙烯及其低聚物的共聚物来消除硫黄喷霜。
也有人曾建议过用硫黄与高分子树脂的并用物、硫黄在环烃油中的溶解液、含硫低聚丁二烯、硫黄与5-乙烯-双环[9.2.1]庚-2-烯及四氢化茚等的反应产物。
向硫黄硫化胶中添加N-三氯甲基次磺基对氨基苯磺酸盐可减少喷霜。
乙烯与α-烯烃的共聚物、α-烯烃橡胶以及乙丙橡胶可用含Cl、S或SO2基的双马来酰亚胺衍生物硫化,而不用硫黄硫化。
亚硝基胺的生态危害性是众所周知的。
因此,以二胺为基础的促进剂因会生成挥发性亚硝基胺而具有危险性。
危险性最小的是二苄基二硫代氨基甲酸锌及二硫化二苄基秋兰姆。
次磺酰胺类以及二硫化四甲基秋兰姆及其它低烷基秋兰姆类促进剂可限量(0.4-0.5%)使用。
对于轮胎胶料则常使用促进剂DZ(N,N’-二环已基-2-苯并噻唑次磺酰胺),也可采用二硫化与四苄基秋兰姆双马来酰亚胺的并用物。
不含氮原子的黄原酸衍生物与少量常用促进剂的并用物不会生成亚硝基胺。
以二烷基(C1-5)氧硫磷酰基三硫化物与N-三氯甲基次磺酰基苯基次磺酰胺和二硫化苯并噻唑(促进剂DM)以及二苄基二硫代氨基甲酸锌等的并用物作促进剂也不会生成亚硝基胺。
使用维生素C及维生素E添加剂可降低通用硫化体系中亚硝基胺的生成量。
从生态观点来看,用以1,1’-二硫代双(4-甲基哌嗪)及其它哌嗪的衍生物为主的促进剂取代胺类促进剂是适宜的,将秋兰姆和脲类并用,以及使用含2-15%多噻唑、15-50%双马来酰亚胺,15-45%次磺酰胺及20-55%硫黄的混合物均可减少亚硝基胺的生成。
建议用烷基二硫代磷酸盐作为三元乙丙橡胶的硫化促进剂,此时不会生成亚硝基胺。
用氨或正胺对填料与ZnO进行预处理可阻止生成亚硝基胺。
往聚丁二烯导丁苯橡胶的硫黄硫化并用胶料中加入少量CaO、Ca(OH)2及Ba(OH)2也能阻止生成亚硝基胺。
改进硫化胶的工艺及使用性能,近年来,用以改进硫化胶,特别是不饱和橡胶性能的硫化体系的品种显着增加。
不饱和橡胶新型硫化剂建议用邻苯二甲酸及偏苯三酸的Ca、Mg、Zn及其它两价金属盐来硫化羧基橡胶。
含此类金属盐的胶料抗焦烧,其硫化胶的强度可达18MPa。
以Fe(OH)3作促进剂用三乙醇胺可硫化丁二烯、丙烯腈及异丙氧基羰基甲基丙烯酸甲酯的共聚物。
所得硫化胶用于制备耐油和耐苯的制品。
用多功能乙烯酯可使丁腈橡胶交联。
用过氧化物硫化这些橡胶时,常用丙烯酸或二甲基丙烯酸苯酯和萘酯作共硫化剂,所得硫化胶具有耐热性及高耐磨性。
常用季戊四醇四乙烯酯来降低硫化温度。
建议将以乙烯硫脲为基础的新型硫化剂用于硫化丁腈橡胶、丁基橡胶、氯丁橡胶及三元乙丙橡胶。
使用低分子量的酚醛树脂硫化丁腈橡胶可生成互穿网络,从而起到增强作用。
醌单肟(Na、Zn、Al)盐及对醌二肟(Na、Zn)盐可用于硫化顺丁橡胶。
常用乙烯基三甲氧基硅烷来硫化二元乙丙橡胶及三元乙丙橡胶。
在过氧化酚醛低聚物存在下的过氧化物硫化可改进三元乙丙胶的高温性能及物理机械性能。
也可用含过氧基的环氧齐聚物硫化三元乙丙橡胶;此时,炭黑胶料的粘度下降,硫化胶的强度性能得到改善。
烷氧端基聚硅氧烷常用于聚丙烯与三元乙丙共混胶的动态硫化,所得热塑性弹性体具有高耐热性。
新型硫化促进剂羧基丁腈橡胶的硫化是采用硫代磷酸二硫化物与促进剂DM或N-氧化二乙烯-2-苯并噻唑次磺胺并用物。
二甲苯与蒽的二硝基氧化衍生物可将硫化速率提高1-3倍,而硫化温度仅为60-80℃。
(原需140-160℃)所得硫化胶可耐热氧老化。
为了加速羟基丁腈橡胶的硫化,也有使用双(二异丙基)硫代磷酸三硫化物的,可制得增高网络密度的硫化胶。
使用含芳香取代基或双键的苯并咪唑衍生物不仅可以提高丁腈橡胶的耐、热氧老化性能,而且可提高强度及耐动态疲劳性能。
此外还常往丁腈胶料中加入与杂环有共轭双键的苯并咪唑衍生物,从而使橡胶的强度及耐热氧老化性能提高,动态性能得到改善。
往丁腈橡胶CKH-26中加入二磷或多磷酰氢化物,往丁腈橡胶CKH-18中加入有机二硫代磷酸酐可加速硫化并使硫化胶保持稳定。
由六次甲基二胺与硫黄缩聚可制得用于异戊橡胶及丁二烯橡胶的新型聚合物硫化促进剂。
此种硫化促进剂具有宽域的硫化平坦区,可使硫化胶的物理机械性能得到改善。
异戊二烯橡胶CKH-3及丁腈橡胶CKH-26常采用烷基三乙基氨溴化物作共硫化剂,此时,CKH-26硫化胶的强度可从4.5MPa提高到6.8MPa。
建议采用以脂肪芳香酸和脂肪族酸或醇为基础的酯类和2-(2’,4’-二硝基苯基)硫代苯并噻唑新型硫化剂,其分解诱导期在160℃时为140-165min。
为了提高不饱和橡胶的硫化速率,常常添加第二促进剂,如丁醛与苯胺的缩合物等。
硫化天然橡胶与丁苯橡胶的并用胶时,在使用秋兰姆的同时,还并用1-苯基-2,4-二缩二脲。
可用2-(2,4-二硝基苯基)硫醇基苯并噻唑与第二促进剂硫化天然橡胶。
所得硫化胶的性能与用2-苯并噻唑-N-硫代码啉硫化的相似为了提高天然橡胶的耐疲劳寿命常往该促进剂中加入酰胺基磷酸酯低聚物。
在1,3-丁二烯和2-乙烯吡啶共聚物存在条件下,天然橡胶的硫化速率加快,同时,硫化胶的强度增高。
丁二烯橡胶和丁腈橡胶的硫化速率也可用此种方法提高,且焦烧倾向降低。
往三元乙丙橡胶中加入水杨基亚胺铜及苯胺的衍生物可使硫化速率提高0.2-0.5倍。
同时,硫化胶强度提高,耐多次形变疲劳性能及耐热性改善。
使用脂肪酸的磷酸盐化烷基酰胺可提高丁苯硫化胶的强度(1倍)。
如在硫黄中加入二烷基二硫代磷酸钠及多季铵盐,则在硫化异戊橡胶时有协同效应,硫化胶强度达23.6MPa。
天然橡胶和丁苯橡胶的新型硫化剂是2-间二氮苯次磺酰胺。
与一般次磷酰胺促进剂相比,它们可使硫化速率提高得更快、硫化程度更高及诱导期更长。
丁基橡胶在热水中的“冷”硫化除使用二枯基过氧化物外,还可添加醌醚。
在60℃时硫化时间为9d,在95℃下则分别为12h和3h。
降低焦烧速率的新方法近十年来,为了降低焦烧速率,使用了许多新型化合物。
四苄基二硫化秋兰姆与次磺酰胺的并用物以及2-吡嗪次磺酰胺对大多数用硫黄硫化的橡胶有效。
对于丁苯橡胶与丁二烯橡胶的并用胶,建议使用四甲基异丁基一硫化秋兰姆。
对丁腈橡胶与一元乙丙橡胶的并用胶建议使用二甲基丙烯酸锌。
丁腈橡胶和异戊橡胶用过氧化物硫化时使用酚噻嗪极其有效,而硫化三元乙丙橡胶时有效的是酚噻嗪及2,6-二-特丁基-甲酚。
降低返原性建议使用二乙基磷酸的衍生物来降低返原性。
此外,还可使用六次甲基双(硫代硫酸)钠、五氯-β-羟基乙基二硫化物、双(柠檬酰胺)与三十碳六烯的并用物、二苯基二硫代磷酸盐(Ni、Sn、Zn)、1-苯基-及1,5-二苯基-2,4-二硫脲与N-环己基苯并噻唑次磺酰胺的并用物等。
使用含0.1%至0.25%的双(2,5-多硫代-1,3,4-噻二嗪、0.5%至0.3%双(马来酰亚胺)及0.5%至3%次磺酸胺的并用物也很有效。
使用含硫黄及烯烃基的烷氧端基硅烷硫化剂则没有返原现象。
使用脂肪酸锌和芳香酸锌盐的并用物不仅可以减轻返原,而且还可以改进硫化胶的动态性能。
加入1,3双(柠檬亚氨甲基)苯不仅可以减轻返原,同时还可提高硫化胶的抗撕裂性及强度。
使用硫黄硫化活性剂的新途径通常将ZnO(3-5质量份)与硬脂酸(1份)加以组合作为硫黄硫化的活性剂。
目前使用各种方法来降低氧化锌的用量,甚至取代氧化锌。
例如,将促进剂M与促进剂TT和ZnO、硬脂酸的并用物加热至100-105℃可使橡胶中ZnO含量降低至2质量份。
有时,也使用经聚合物表面活性剂溶液处理后的SiO2和ZnO并用物,这样,可降低ZnO用量,也曾采用过以ZnO“包覆”的无机填料。