基于参数最优化的车架轻量化设计
基于参数化模型的小型电动车全铝框架车身结构轻量化设计
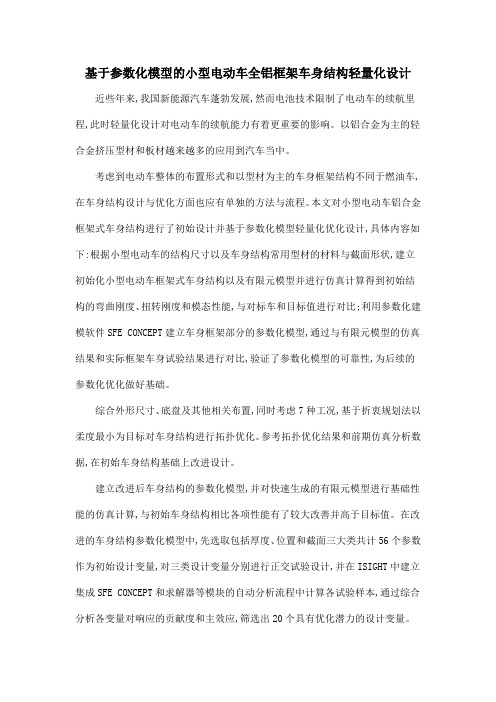
基于参数化模型的小型电动车全铝框架车身结构轻量化设计近些年来,我国新能源汽车蓬勃发展,然而电池技术限制了电动车的续航里程,此时轻量化设计对电动车的续航能力有着更重要的影响。
以铝合金为主的轻合金挤压型材和板材越来越多的应用到汽车当中。
考虑到电动车整体的布置形式和以型材为主的车身框架结构不同于燃油车,在车身结构设计与优化方面也应有单独的方法与流程。
本文对小型电动车铝合金框架式车身结构进行了初始设计并基于参数化模型轻量化优化设计,具体内容如下:根据小型电动车的结构尺寸以及车身结构常用型材的材料与截面形状,建立初始化小型电动车框架式车身结构以及有限元模型并进行仿真计算得到初始结构的弯曲刚度、扭转刚度和模态性能,与对标车和目标值进行对比;利用参数化建模软件SFE CONCEPT建立车身框架部分的参数化模型,通过与有限元模型的仿真结果和实际框架车身试验结果进行对比,验证了参数化模型的可靠性,为后续的参数化优化做好基础。
综合外形尺寸、底盘及其他相关布置,同时考虑7种工况,基于折衷规划法以柔度最小为目标对车身结构进行拓扑优化。
参考拓扑优化结果和前期仿真分析数据,在初始车身结构基础上改进设计。
建立改进后车身结构的参数化模型,并对快速生成的有限元模型进行基础性能的仿真计算,与初始车身结构相比各项性能有了较大改善并高于目标值。
在改进的车身结构参数化模型中,先选取包括厚度、位置和截面三大类共计56个参数作为初始设计变量,对三类设计变量分别进行正交试验设计,并在ISIGHT中建立集成SFE CONCEPT和求解器等模块的自动分析流程中计算各试验样本,通过综合分析各变量对响应的贡献度和主效应,筛选出20个具有优化潜力的设计变量。
利用优化拉丁方试验设计方法进行130次试验设计,根据样本点数据建立不同近似模型来表示变量与响应之间的关系。
最终通过精度对比,选用响应面近似模型代替仿真模型,采用NSGA-Ⅱ多目标优化算法,以质量最小和弯扭刚度最大为目标对车身结构进行多目标优化。
轿车悬架控制臂参数化建模及轻量化多目标优化设计

轿车悬架控制臂参数化建模及轻量化多目标优化设计车辆悬架是车辆重要的组成部分之一,直接关系到车辆的行驶性能和舒适性。
悬架控制臂作为悬架系统的重要部件,其参数设计对车辆的转向稳定性、抗疲劳能力、通过性等方面有着很大影响。
为了提高轿车的性能与可靠性,轿车悬架控制臂的参数化建模和轻量化多目标优化设计是必不可少的步骤。
首先,对于轿车悬架控制臂参数化建模,可以采用CAD建模软件进行完成。
具体的建模过程包括坐标系的设定、几何图形的建立及参数的提取等。
在建模时需考虑到悬架控制臂的结构特点以及设计要求,以确保建模结果准确可靠。
其次,针对轿车悬架控制臂的轻量化优化设计,可以采用拓扑优化技术。
具体做法是在前提满足轿车行驶稳定性的基础上,利用有限元分析软件对悬架控制臂进行力学仿真分析,获得载荷作用下的最大应力集中区域。
然后,设置拓扑域和拓扑分区,减少结构材料的使用量,同时保证结构刚度和强度要求。
最后再基于多目标优化理论,考虑在轿车悬架控制臂轻量化的基础上进一步优化转向稳定性和驾驶舒适性等方面的性能。
最后,轿车悬架控制臂参数化建模与轻量化多目标优化设计的实施,可以达到节省材料、减轻车重、提升性能和降低油耗等多重优势。
同时还可以有效控制车辆成本,提高车辆的市场竞争力。
因此,在轿车悬架系统的设计中,参数化建模与轻量化多目标优化设计的应用越来越受到车辆制造业和悬架系统制造公司的重视和推广。
在进行轿车悬架控制臂参数化建模和轻量化多目标优化设计时,还需要考虑一些关键因素。
首先需要考虑的是材料选择与性能设计。
轿车悬架控制臂所使用的材料不仅需要满足强度、刚度等基本要求,同时还需考虑其重量、成本等因素。
因此,在进行参数化建模和轻量化多目标优化设计时,需要根据材料的特性和特点进行合理的材料选择。
其次,在选定适当的材料后,需要进一步考虑材料的加工工艺以及成本等方面的因素。
针对这些因素,需要通过多方面的分析,优化材料性能与成本,以达到最优的效果。
汽车车架的轻量化设计 (1)

V90680‘西华大学硕士学位(毕业)论文题目:汽车车架的轻量化设计研究生指导教师:专、№研究方向:培养单位:论文起止日期曲昌荣巢凯年f教授1车辆工程汽车陛能测试与分析西华大学2005年5月至2006年5月2。
6年5月西华人学硕十学位论文1.具有良好的图形用户接口(GuI)(如图2l所示)Fi醇.1GulofANSYS例2.1ANsYs软件图形用户界面通过GUI可方便的交互访问程序的各种功能、命令、用户手册和参考材料,并可一步一步完成整个分析,因而使ANSYs易于使用。
在用户接口中,ANSYS程序提供了四种通用方法输入命令:菜单、对话框、工具杆、直接输入命令。
菜单出运行ANSYS程序是相关的命令和功能组成,位于各自的窗口中,用户在任何时候均可用鼠标访问这些窗口,这些窗口也可用鼠标移动或隐去操作。
ANSYS命令根据其功能分组,保证了用户快速访问到合适的命令。
2全交互式图形它是ANSYs程序中不可分割的组成部分,图形对于校验前处理数据和在后处理中检查求解结果都是非常重要的。
西华人学硕十学位论文Fi醇.3Geome廿icmodeIofatnJck图2.3载货汽车车架的几何模型2.2.4模型的网格划分汽车的车架大多数是由薄壁型钢焊接和铆接而成,其中槽钢就是最常用的一种型钢,该货车也采用槽钢。
由于载荷常常不通过这些薄壁截面的弯曲中心,由材料力学可知,这些杆件不但要发生弯曲变形,而且还要发生扭转变型。
薄壁杆件抗扭的能力较差,当汽车在高低不平的路面上行驶时,必须考虑到杆件的扭转变型。
在建立板壳单元刚度矩阵时,板壳单元有三节点、四节点、六节点、八节点等几种类型的单元,由于货车车架纵梁和横梁均为平直的槽钢,故可以采用四节点和八节点单元,而八节点单元精度较高。
对于高次单元由于内部应力不是常量,可以较好的适应结构变化的应力场,用较少的单元可以得到较好的效果。
但是高次单元的刚度矩阵比较复杂,形成结构刚度矩阵要花很长的计算时间。
FSAE赛车车架结构优化和轻量化
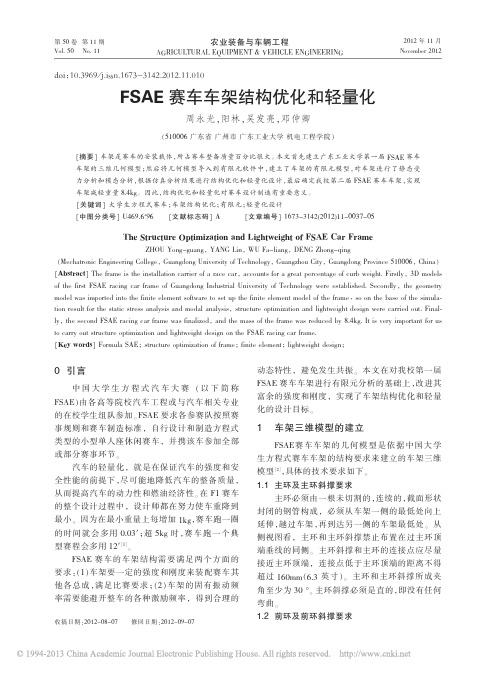
前隔板 前环斜撑 前环 侧防撞壁
主环 主环斜撑
图 l 第一届 FSAE 赛车车架三维模型 Fig.1 Three-dimensional model of The First FSAE Frame
2 车架有限元模型(包括网格的划分)
为了减少计算量, 需要对车架的网格大小进 行合理控制。 对于受力复杂的下层车架钢管划分 网 格 分 得 细 密 些 ,尺 寸 单 元 约 为 5mm,其 对 于 受 力较少的上层车架单元网格划分得粗些, 其尺寸 单元约为 25~45mm,对于与悬架硬点和发动机固 定点相连接的车架管件网格划分要更细些。
力分析和模态分析,根据仿真分析结果进行结构优化和轻量化设计,最后确定我校第二届 FSAE 赛车车架,实现
车架减轻重量 8.4kg。 因此,结构优化和轻量化对赛车设计制造有重要意义。
[关键词] 大学生方程式赛车;车架结构优化;有限元;轻量化设计
[中图分类号] U469.6+96 [文献标志码] A
[文章编号] 1673-3142(2012)11-0037-05
1 车架三维模型的建立
FSAE赛 车 车 架 的 几 何 模 型 是 依 据 中 国 大 学 生方程式赛车车架的结构要求来建立的车架三维 模 型 [2],具 体 的 技 术 要 求 如 下 。 1.1 主环及主环斜撑要求
主环必须由一根未切割的,连续的,截面形状 封闭的钢管构成, 必须从车架一侧的最低处向上 延伸,越过车架,再到达另一侧的车架最低处。 从 侧视图看, 主环和主环斜撑禁止布置在过主环顶 端垂线的同侧。 主环斜撑和主环的连接点应尽量 接近主环顶端, 连接点低于主环顶端的距离不得 超过 160mm(6.3 英寸)。 主环和主环斜撑所成夹 角至少为 30 °。 主环斜撑必须是直的,即没有任何 弯曲。 1.2 前环及前环斜撑要求
基于拓扑与尺寸优化的电动环卫车车架轻量化设计
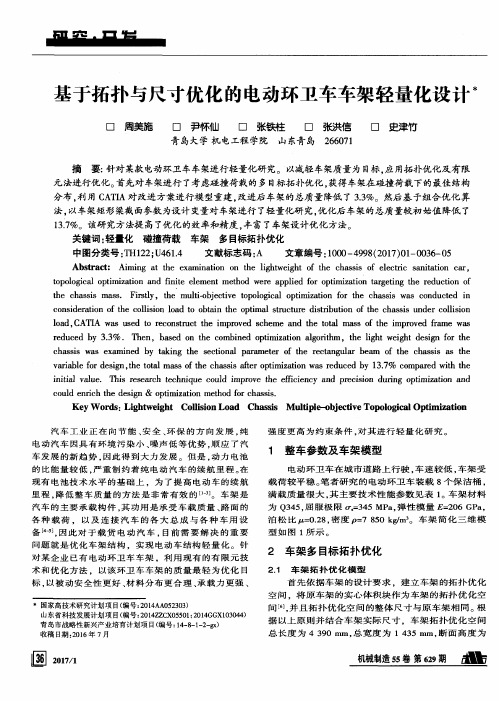
Ab s t r a c t : A i mi n g a t t h e e x a mi n a t i o n o n t h e l i g h t we i g h t o f t h e c h a s s i s o f e l e c t ic r s a n i t a t i o n c a r , t o p o l o g i c a l o p t i mi z a t i o n a n d f i n i t e e l e me n t me t h o d we r e a p p l i e d f o r o p t i mi z a t i o n t a r g e t i n g t h e r e d u c t i o n o f
t h e c h a s s i s m a s s .F i r s t l y ,t h e m u l t i - o b j e c t i v e t o p o l o g i c a l o p t i mi z a t i o n or f t h e c h a s s i s w a s c o n d u c t e d i n
c h a s s i s wa s e x a mi n e d b y t a k i n g t h e s e c t i o n l a p a r a me t e r o f t h e r e c t a n g u l r a b e m a o f t h e c h a s s i s s a t h e v a r i a b l e f o r d e s i g n. t h e t o t a l ma s s o f t h e c h ss a i s a f t e r o p t i mi z a t i o n wa s r e d u c e d b y 1 3 . 7 % c o mp a r e d w i t h t h e i n i t i l a v a l u e .T h i s r e s e a r c h t e c h n i q u e c o u l d i mp r o v e t h e e ic f i e n c y a n d p r e c i s i o n d u in r g o p t i mi z a t i o n a n d c o u l d e n ic r h t h e d e s i g n& o p t i mi z a t i o n me t h o d or f c h ss a i s .
重型载重汽车车架轻量化设计研究
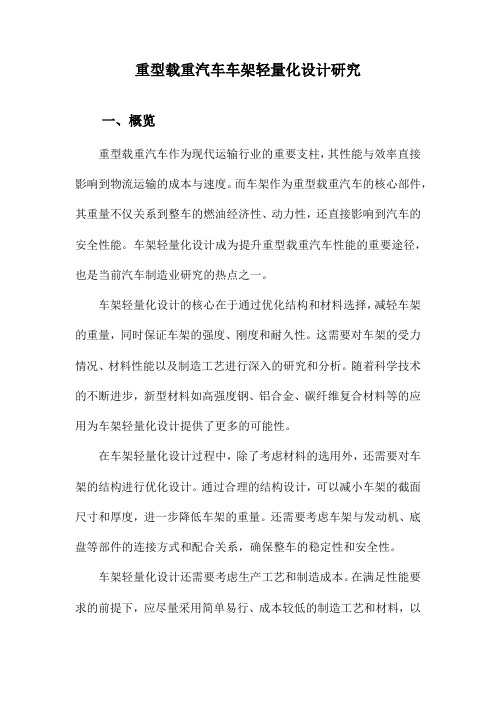
重型载重汽车车架轻量化设计研究一、概览重型载重汽车作为现代运输行业的重要支柱,其性能与效率直接影响到物流运输的成本与速度。
而车架作为重型载重汽车的核心部件,其重量不仅关系到整车的燃油经济性、动力性,还直接影响到汽车的安全性能。
车架轻量化设计成为提升重型载重汽车性能的重要途径,也是当前汽车制造业研究的热点之一。
车架轻量化设计的核心在于通过优化结构和材料选择,减轻车架的重量,同时保证车架的强度、刚度和耐久性。
这需要对车架的受力情况、材料性能以及制造工艺进行深入的研究和分析。
随着科学技术的不断进步,新型材料如高强度钢、铝合金、碳纤维复合材料等的应用为车架轻量化设计提供了更多的可能性。
在车架轻量化设计过程中,除了考虑材料的选用外,还需要对车架的结构进行优化设计。
通过合理的结构设计,可以减小车架的截面尺寸和厚度,进一步降低车架的重量。
还需要考虑车架与发动机、底盘等部件的连接方式和配合关系,确保整车的稳定性和安全性。
车架轻量化设计还需要考虑生产工艺和制造成本。
在满足性能要求的前提下,应尽量采用简单易行、成本较低的制造工艺和材料,以降低整车的生产成本,提高市场竞争力。
重型载重汽车车架轻量化设计是一个涉及材料、结构、工艺等多方面的复杂问题。
通过深入研究和分析,采用合理的设计方法和手段,可以实现车架的轻量化,提高重型载重汽车的性能和效率,为物流运输行业的发展做出贡献。
1. 重型载重汽车在社会经济中的地位与作用重型载重汽车作为道路交通的重要载体,在社会经济发展中占据着举足轻重的地位。
它们不仅是货物运输的主要工具,还是基础设施建设、物流运输、农业生产等领域不可或缺的力量。
随着全球经济一体化的加速推进,重型载重汽车的需求日益增长,对社会经济的发展起着重要的支撑作用。
重型载重汽车在货物运输中发挥着关键作用。
无论是长途运输还是短途配送,重型载重汽车都能以其强大的承载能力和稳定的性能,确保货物安全、高效地到达目的地。
在国际贸易中,重型载重汽车更是扮演着重要角色,它们穿梭于世界各地的港口、仓库和物流中心,将货物运送到各个角落,为国际贸易的繁荣做出了巨大贡献。
利用有限元分析优化摩托车车架设计
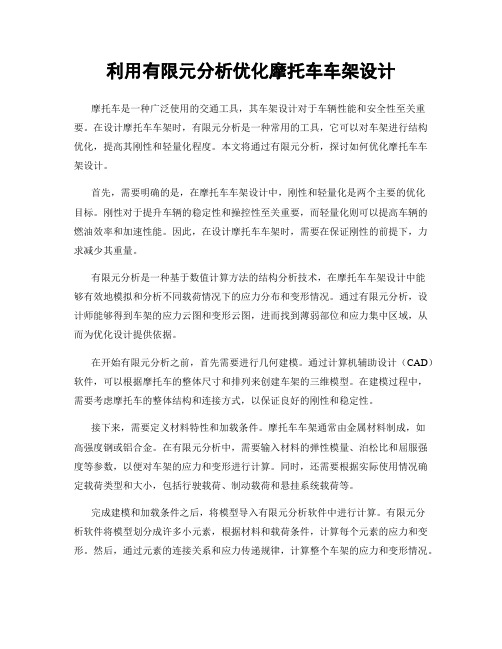
利用有限元分析优化摩托车车架设计摩托车是一种广泛使用的交通工具,其车架设计对于车辆性能和安全性至关重要。
在设计摩托车车架时,有限元分析是一种常用的工具,它可以对车架进行结构优化,提高其刚性和轻量化程度。
本文将通过有限元分析,探讨如何优化摩托车车架设计。
首先,需要明确的是,在摩托车车架设计中,刚性和轻量化是两个主要的优化目标。
刚性对于提升车辆的稳定性和操控性至关重要,而轻量化则可以提高车辆的燃油效率和加速性能。
因此,在设计摩托车车架时,需要在保证刚性的前提下,力求减少其重量。
有限元分析是一种基于数值计算方法的结构分析技术,在摩托车车架设计中能够有效地模拟和分析不同载荷情况下的应力分布和变形情况。
通过有限元分析,设计师能够得到车架的应力云图和变形云图,进而找到薄弱部位和应力集中区域,从而为优化设计提供依据。
在开始有限元分析之前,首先需要进行几何建模。
通过计算机辅助设计(CAD)软件,可以根据摩托车的整体尺寸和排列来创建车架的三维模型。
在建模过程中,需要考虑摩托车的整体结构和连接方式,以保证良好的刚性和稳定性。
接下来,需要定义材料特性和加载条件。
摩托车车架通常由金属材料制成,如高强度钢或铝合金。
在有限元分析中,需要输入材料的弹性模量、泊松比和屈服强度等参数,以便对车架的应力和变形进行计算。
同时,还需要根据实际使用情况确定载荷类型和大小,包括行驶载荷、制动载荷和悬挂系统载荷等。
完成建模和加载条件之后,将模型导入有限元分析软件中进行计算。
有限元分析软件将模型划分成许多小元素,根据材料和载荷条件,计算每个元素的应力和变形。
然后,通过元素的连接关系和应力传递规律,计算整个车架的应力和变形情况。
通过有限元分析,可以得到车架的应力云图和变形云图。
应力云图用彩色表示不同部位的应力大小,通过对比云图,可以找到应力集中区域和薄弱部位。
变形云图则用于确定车架在各个载荷下的变形情况,从而评估其刚性和稳定性。
在了解了车架的应力和变形情况之后,可以根据实际需求进行优化设计。
某型货车车架轻量化优化设计
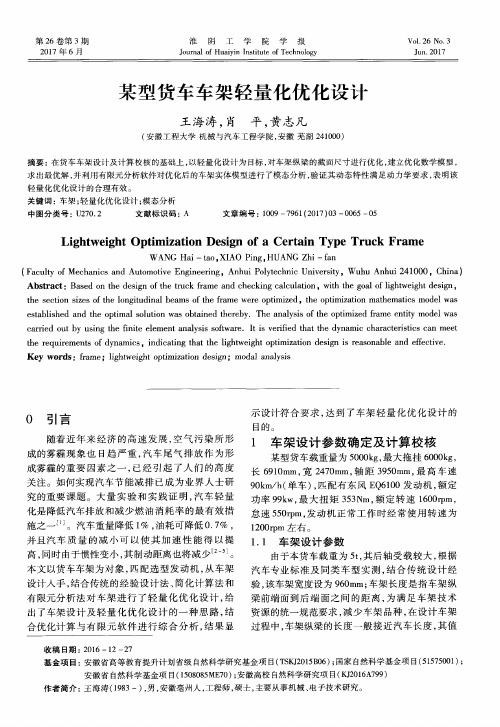
示设 计符 合 要 求 , 达 到 了车 架 轻 量 化 优 化 设 计 的
目的 。
1 车架设计参数确定及计算校核
某 型货 车载 重量 为 5 0 0 0 k g , 最 大拖 挂 6 0 0 0 k g , 成 雾 霾 的重 要 因 素 之 一 , 已 经 引 起 了人 们 的 高 度 长 6 9 1 0 m m, 宽 2 4 7 0 m m, 轴距 3 9 5 0 m m, 最 高 车 速 关 注 。如 何 实现 汽车 节 能 减 排 已成 为业 界 人 士 研 9 0 k m / h ( 单车) , 匹配 有 东 风 E Q 6 1 0 0发 动 机 , 额 定 究 的重要 课 题 。大 量 实 验 和 实 践 证 明 , 汽 车 轻 量 功率 9 9 k w, 最大扭 矩 3 5 3 N m, 额定 转速 1 6 0 0 r p m, 化是 降低 汽 车排 放 和减 少 燃 油 消 耗 率 的 最有 效 措 怠 速 5 5 0 r p m, 发 动机 正 常 工 作 时经 常 使 用 转 速 为 施之一¨ J 。汽 车重 量 降低 I %, 油 耗 可 降低 0 . 7 %, 1 2 0 0 r p m左 右 。 并 且 汽 车 质 量 的 减 小 可 以使 其 加 速 性 能 得 以 提 1 . 1 车 架 设 计 参 数 高, 同时 由于惯性 变小 , 其 制动 距离 也将 减 少 。 由于本货 车 载 重为 5 t , 其 后 轴 受 载较 大 , 根据
Abs t r a c t :Ba s e d o n t h e d e s i g n o f t he t r u c k f r a me a n d c he c k i n g c a l c u l a t i o n,wi t h t h e g o a l o f l i g h t we i g ht d e s i g n,
- 1、下载文档前请自行甄别文档内容的完整性,平台不提供额外的编辑、内容补充、找答案等附加服务。
- 2、"仅部分预览"的文档,不可在线预览部分如存在完整性等问题,可反馈申请退款(可完整预览的文档不适用该条件!)。
- 3、如文档侵犯您的权益,请联系客服反馈,我们会尽快为您处理(人工客服工作时间:9:00-18:30)。
( 1 )
( 2)
电 瓶
4 0
2 I 0 0 0 1 O O 0 o 4 8 0
mi n V=Vo + A £
i= 1
表 2 边 界条 件
£ ≤ ≤ 一 =1, 2, … , n
部 位
左 前 轮
弯 曲工 况 约 束 自 由度 扭 转 工 况 约 束 自由 度
车架 通过 悬架 系 统 、 车 桥 和车轮 支 承在地 面 上 , 为
和 目标 函 数 在 优 化 设 计 模 型 中 加 以 确 定 ,在 优 化 迭 代 时 对 目标 函 数 和 约 束 函 数 进 行 计 算 , 以 保 证 目 标 函 数 在 满 足 约 束 条 件 的 情 况 下 不 断 下 降 。 约 束 函 数 在
ANS YS 中 是 通 过 定 义 状 态 变 量 及 状 态 变 量 的 上 下 限
更 准 确 地 模 拟 实 际 使 用 工 况 。以 弹 簧 实 际 支 撑 点 为 弹 性 体 的着 力 点 , 以 弹 簧 的 实 际 刚 度 为 弹 性 体 刚 度 建 立 模拟 弹簧 ] 。
1 . 2 车 架 载 荷 及 边 界 条 件
X z X. Y. z
S , ≤J s . =1 , 2, …, m
( 3 )
式中: 。 为主 副车架 结 构不 参与 优化 部分 的 总体 积 ; A 为 第 个 构 件 的 横 截 面 积 ; 式 ( 2 ) 为 板厚 尺 寸 约 束 ; t … 和 t i 一 分别 为第 i 个 构 件壁 厚参 数 的下 限值 和上 限值 ; 式( 3 ) 为应 力 约束 ; m 为 主 副 车 架 有 限 元 模 型 中 的 单 元
分 布 到 车 架 纵 梁 上 ] , 车 架 的重 力取 为 惯 性载 荷 , 重 力
3 数 学 模 型 建 立
优 化 问 题 的 数 学 模 型 是 实 际优 化 设 计 问 题 的 数 学
抽象 , 在 明确设计 变 量 、 状 态 变量 、 约束 条件 、 目标 函数
之后 , 优 化 设 计 问 题 就 可 以变 为 一 般 数 学 形 式 :
[ 6 ]
。
日 为纵 梁宽 、 高, B1 、 日 一, 曰7 、 H7 为 第 1至 第 7 横 梁 的 宽 、 高 。设计 变 量初 始值 及取 值 空间见 表 3 。
4. 2 状 态 变 量 选 取
整个 优化 流程 如 图 2
来 实 现 的 。 目标 函 数 是 根 据 具 体 的 研 究 对 象 和 研 究 目
标 来进 行定 义 的 。
本计 算 中 , 将 发 动机 、 变速 箱 、 电池 、 油 箱 等 作 为 集
中载荷 , 根 据 其 质 心 位 置 以及 与 车 架 之 间 的 连 接 部 位 ,
分 摊 到 相 应 的 节 点 上 ;驾 驶 室 和 乘 客 的 质 量 按 均 布 载 荷 分 布 到 车 架 纵 梁 上 。货 物 和 车 厢 的质 量 按 均 布 载 荷
:
加 速度为 1 。该 车 各 部 分 质 量 见 表 1 , 边界条件 见表 2 。
表 1 车 架 上 各 部 分 质 量, k g 厢 重 载 重 驾 驶 室 乘 员 发 动 机 变 速 箱 油 箱
2 0 o 6 4 8 2 3 2 1 8 4
{ t 1 , t 2 , … , }
4. 1 设 计 变 量 选 定
在 AN S YS 中 欲 建 立 参 数 化 有 限 元 模 型 . 首 先 要 选 取设 计变 量 , 并将其 参 数化 。 通 过 AP DL 语 言 可 实 现 参
数化 过程 , 主 要包 括三个 方 面工 作 : ① 定 义 变 量 并 为 变 量 赋 值 ;② 用 所 定 义 的 设 计 变 量 将 原 有 限 元 模 型 参 数
情 况 指 定 合 适 的 状 态 变 量 和 目标 函 数 , 以 建 立
总数 ; S 为 第 个 单 元 的 Vo n Mi s s应 力 值 ; S。 为该 单 元
的许用 应力 值 。
4 车 架 参 数 优 化
由 于 车 架 板 材 为 企 业 已选 定 型 号 .故 该 设 计 只 对 车 架横 梁 、 纵梁 、 截 面 的长和 宽进 行优 化 。
化 ; ③ 从 第 一 步 定 义 的 变 量 中选 取 若 干 变 量 , 并 将 其 定
义 为优化 设计 变 量 。故本 文选 定 的变量 为梁 的宽 、 高 , 分 别 为 设 计 变 量 B、 H, Bl 、 Hl , 2 、 2 , … , B 7 , 其 中 B、
合 理 的 优 化 模 型 ,然 后 选 择 合 适 的 优 化 方 法 和 设 置 合 适 的 循 环 次 数 后 即 可 进 行 轻 量 化 计 算
左 后 轮
右 前 轮 右 后 轮
Z
X. Y. z Y, Z
y. Z
X. z
2 参数 优 化 的 过 程
优 化 设 计 计 算 的 主 要 任 务 是 选 择 一 定 的 优 化 方 法 ,按 照 所 选 择 的 优 化 方 法 对 所 创 建 的 分 析 文 件 及 其 相 应 的 模 型 进 行 分 析 计算 , 然 后将 计 算结 果 与 较优 结 果 进 行 对 比 、 判断 。 得 出新 的较优 结果 , 如 此反 复循 环 , 直 到 最 终 得 到 符 合 条 件 的 最 优 结 果 ] 。因 此 , 通 常为 求得 最优 方案 , 一 般 需 要 进行 多轮 次 的计算 分 析 , 因而通 常所 需 时 间较长 。 根 据 不 同 的 研 究 目 标 ,选 取 不 同 的 设 计 参 数 作 为 设 计 变 量 , 并 根 据 实 际