静电喷涂工艺参数
静电喷涂工艺要求
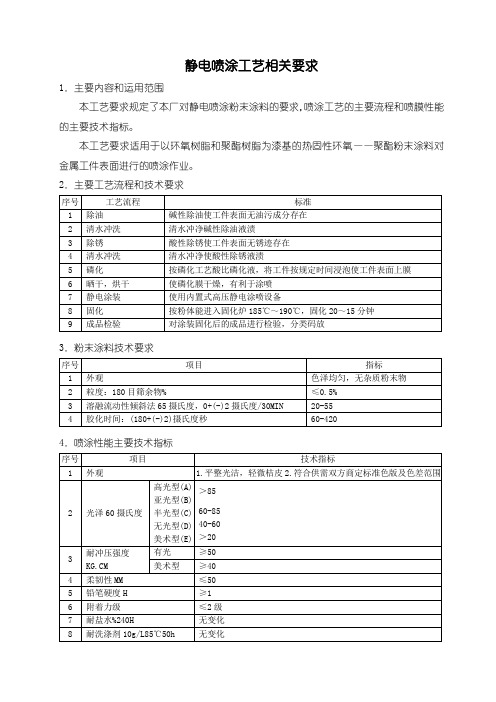
静电喷涂工艺相关要求
1.主要内容和运用范围
本工艺要求规定了本厂对静电喷涂粉末涂料的要求,喷涂工艺的主要流程和喷膜性能的主要技术指标。
本工艺要求适用于以环氧树脂和聚酯树脂为漆基的热固性环氧——聚酯粉末涂料对金属工件表面进行的喷涂作业。
2.主要工艺流程和技术要求
3.粉末涂料技术要求
4.喷涂性能主要技术指标
5.喷涂作业注意事项
1)粉末涂料严格按批次顺序使用,先生产的先使用。
2)工件在喷涂前应彻底清除其表面污染物,正确进行预处理。
3)压缩空气应无油、无水,经常检查油水分离器的工作状况。
4)工件夹持应适当,与接地传送部分要保持良好的连接。
工夹具应定期清洗,以保证良好地接地。
5)烘炉的性能要稳定,为了减少色差,烘箱内部温度的温差不得大于5℃,以达到正确固化涂层之条件。
6)供粉器、回收系统和喷柜应无污染,不与其他粉料混用,否则将影响最后涂层之外观。
7)经常检查预处理、固化炉的性能,检查所用粉末的物理性能。
8)回收粉末必须过筛,并按规定的比例与新粉混合使用。
9)在粉末涂料喷涂现场附近应避免出现灰尘等物,以免影响涂膜外观质量。
粉末静电喷涂工艺(3篇)

第1篇摘要:粉末静电喷涂是一种高效、环保、经济的涂装工艺,广泛应用于汽车、家具、建筑、电子等行业。
本文将从粉末静电喷涂的基本原理、设备组成、工艺流程、质量控制等方面进行详细介绍,以期为粉末静电喷涂技术的应用提供参考。
一、引言随着工业技术的不断发展,涂装工艺在提高产品质量、延长使用寿命、美化外观等方面发挥着重要作用。
粉末静电喷涂作为一种先进的涂装技术,具有诸多优点,如环保、节能、高效、质量稳定等。
本文将对粉末静电喷涂工艺进行详细介绍。
二、粉末静电喷涂基本原理粉末静电喷涂是利用静电吸附原理,将粉末涂料喷涂到工件表面的一种涂装方法。
其基本原理如下:1. 喷涂:粉末涂料通过静电喷枪喷出,形成带正电荷的粉末粒子。
2. 静电吸附:带正电荷的粉末粒子在静电场作用下,被工件表面带负电荷的部位吸附。
3. 热固化:吸附在工件表面的粉末涂料在高温下熔化、流平,形成均匀、致密的涂层。
三、设备组成粉末静电喷涂设备主要由以下几部分组成:1. 粉末涂料供应系统:包括粉末料斗、螺旋输送器、定量分配器等。
2. 静电喷枪:用于将粉末涂料喷出,形成带正电荷的粉末粒子。
3. 静电发生器:产生高压静电场,使粉末涂料带电。
4. 烘干固化设备:用于将吸附在工件表面的粉末涂料加热固化。
5. 辅助设备:包括输送装置、工件悬挂装置、冷却装置等。
四、工艺流程粉末静电喷涂工艺流程如下:1. 工件表面处理:对工件进行除油、除锈、磷化等表面处理,提高涂层的附着力。
2. 粉末涂料选择:根据工件材质、要求和使用环境选择合适的粉末涂料。
3. 设备调试:调整粉末涂料供应系统、静电喷枪、烘干固化设备等,确保喷涂质量。
4. 喷涂:将工件悬挂在输送装置上,通过静电喷枪将粉末涂料均匀喷涂在工件表面。
5. 烘干固化:将喷涂后的工件送入烘干固化设备,加热固化粉末涂料。
6. 后处理:检查涂层质量,进行必要的修补和装饰。
五、质量控制粉末静电喷涂质量控制主要包括以下方面:1. 工件表面处理:确保工件表面处理质量,提高涂层附着力。
阀门静电喷涂工艺及检验规程

静电喷涂工艺规程为有效控制喷涂产品的外观质量,结合我公司的时际情况,特制定本工艺规程。
(喷涂工艺流程:工件预处理→预热→喷涂→固化→冷却)。
一、预处理需要涂装的表面必须是干燥和干净的、且具有一定的粗糙度。
,铸铁涂装前采用喷丸和喷砂处理工艺,达到Sa2.5级。
工件处理后6h内需进入预热处理工序,并且注意零部件不得被雨淋,防止再次生锈。
搬运过程中必须防止油污污染,并佩戴帆布类手套,避免人工多次接触工件,防止工件二次污染。
喷丸用的耗材可以采用优质不锈钢丸(S¢1.5)与不锈钢切头(¢1.2)按1:1比例混合,根据消耗情况定期按比例补充。
二、预热铸件必须保证实体温度在160-180℃,不能以烘室空气温度作为判定工件温度的依据,空气温度只能作为参考。
由于阀门铸件厚重且组织疏松,存在热惰性现象,须有足够的预热时间保证工件的温度,同时将工件中的气体烘出,防止粉末喷涂后溢出,形成气泡缺陷。
具体时间根据工件规格尺寸设定(15-25分钟)。
三、喷涂主要采用静电喷涂。
涂层的厚度控制在250-300μm。
粉末遇到热的工件即在表面形成凝胶,喷涂应在尽可能短的时间内完成,最好是在粉磨机凝胶时间内。
对于不需要喷涂的螺纹、平面、孔等处,可以采用硅胶塞和高温胶带等器具遮蔽保护,待喷涂完成后取下即可,(工艺参数见附表一)。
四、固化固化温度在160-180℃,时间10~20min。
固化环节是涂层最终成型的环节,对最终涂层性能影响较大,应合理控制其温度和时间。
温度低、时间短,固化不完全。
温度高或时间长,会导致涂层变色。
喷涂完成后进入固化烘道的时间要尽可能短,2min以内为佳,否则会影响固化效果。
固化完成的工件,冷却至室温,建议采用自然冷却法(各类零件固化时间和温度见附表二)。
五、检验5.1 常规检验用于日常生产的阀门涂层常规检测项目有外观、附着力、厚度和交联性等。
①外观目测应光滑,颜色一致,无气孔、气泡、漏喷等缺陷。
②附着力依据EN ISO 4624的要求进行剥离测试,平均值≥8MPa,最小单值≥6MPa。
粉沫静电喷涂--基本工艺
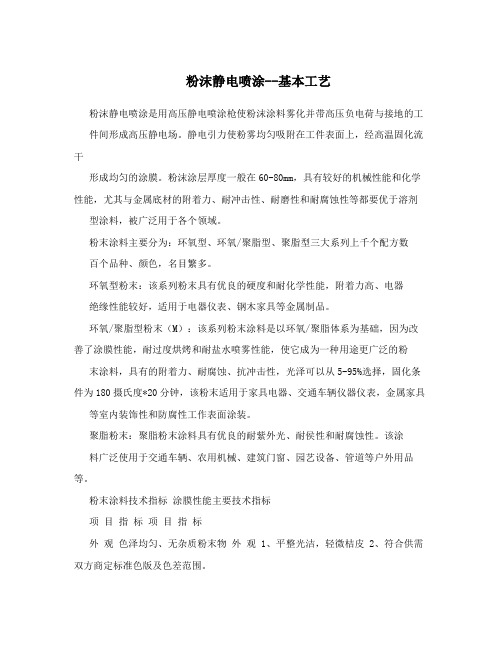
粉沫静电喷涂--基本工艺粉沫静电喷涂是用高压静电喷涂枪使粉沫涂料雾化并带高压负电荷与接地的工件间形成高压静电场。
静电引力使粉雾均匀吸附在工件表面上,经高温固化流干形成均匀的涂膜。
粉沫涂层厚度一般在60-80mm,具有较好的机械性能和化学性能,尤其与金属底材的附着力、耐冲击性、耐磨性和耐腐蚀性等都要优于溶剂型涂料,被广泛用于各个领域。
粉末涂料主要分为:环氧型、环氧/聚脂型、聚脂型三大系列上千个配方数百个品种、颜色,名目繁多。
环氧型粉末:该系列粉末具有优良的硬度和耐化学性能,附着力高、电器绝缘性能较好,适用于电器仪表、钢木家具等金属制品。
环氧/聚脂型粉末(M):该系列粉末涂料是以环氧/聚脂体系为基础,因为改善了涂膜性能,耐过度烘烤和耐盐水喷雾性能,使它成为一种用途更广泛的粉末涂料,具有的附着力、耐腐蚀、抗冲击性,光泽可以从5-95%选择,固化条件为180摄氏度*20分钟,该粉末适用于家具电器、交通车辆仪器仪表,金属家具等室内装饰性和防腐性工作表面涂装。
聚脂粉末:聚脂粉末涂料具有优良的耐紫外光、耐侯性和耐腐蚀性。
该涂料广泛使用于交通车辆、农用机械、建筑门窗、园艺设备、管道等户外用品等。
粉末涂料技术指标涂膜性能主要技术指标项目指标项目指标外观色泽均匀、无杂质粉末物外观 1、平整光洁,轻微桔皮 2、符合供需双方商定标准色版及色差范围。
粒度:180目筛余物% 《=0.5% 光泽60摄氏度高光型(A)亚光型(A)半光型(B)无光型(C)美术型(D) >8560-8540-60>20符合供需双方商定色熔融流动性倾斜法65摄氏度、0+(-)2摄氏度/30min 20-55 耐冲击强度KG.CM有光 >=50美术型 >=40柔韧性MM <=50铅笔硬度H >=1胶化时间:(180+(-)2)摄氏度秒 60-420 附着力级 <=2级耐盐水%240h 无变化耐洗涤剂10g/L85摄氏度50h 无变化工艺技术指标工艺流程标准除油碱性除油使工件表面干净无油污成份存在清水冲洗清水冲净碱性除油液渍除锈酸性除锈使工件表面无锈迹存在清水冲洗清水冲净酸性除锈液渍磷化按磷化工艺酸比磷化液,将工件按规定时间浸泡使工件表面上膜晒干、烘干使磷化膜干燥,有利于涂装静电涂装使用内置式高压静电涂装设备固化按粉体性能进入固化炉185摄氏度-190摄氏度固化20-15分钟成品检验对涂装固化后的成品进行检验,分类码放。
静电塑粉喷涂工艺操作规程
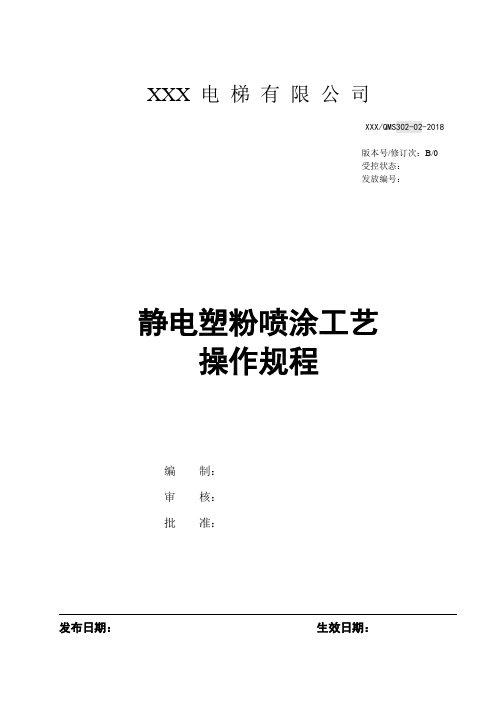
XXX 电梯有限公司XXX/QMS302-02-2018 ----------------------------------------------------------------------------------------------------------------------------------------版本号/修订次:B/0受控状态:发放编号:静电塑粉喷涂工艺操作规程编制:审核:批准:发布日期:生效日期:1.总则根据《NJPC-2003A静电粉末喷涂机使用说明书》、《OMTC喷涂设备用户手册》、《自动升降机用户手册》,本公司喷涂产品,结合塑粉供应商提供参数,以及GB15067-1995《涂装作业规程粉末静电喷涂工艺安全》,编制本文件。
本文件仅适用于本公司静电塑粉喷涂生产线。
2. 工艺流程:挂件→喷涂→烘干固化→摘件→检查2.工艺参数2.1 静电塑粉本公司静电塑粉使用“纯聚酯粉末”(PURE POLYESTER)。
2.1.1 粉末的颗粒级配2.1.2 粉末的电阻率粉末电阻率为109--1013Ω.cm。
2.1.3 粉末的含水率粉末的含水率小于等于0.5%。
2.1.4 保存期超过6个月的和回收的粉末1)保存期超过6个月的粉末:必须过筛,要求用双层钢丝筛网180目;2)受潮的粉末:可在40-50℃下长时间干燥;3)回收的粉末过筛后,必须按30%的比例与新粉搭配。
喷涂用粉末必须严格按上述要求执行,否则达不到预期的喷涂产品质量要求。
2.2 喷涂电压2.2.1 一般喷涂电压:50—70KV。
2.2.2 死角、内角喷涂电压:40--50KV。
2.3 喷涂相关的气压2.3.1 集粉桶流化气压:0.05—0.10Mpa(0.50—1.00bar)2.3.2 一次气压(浓度气压):0.20—0.35Mpa(2.00—3.50bar)2.3.3 二次气压(雾化气压):0.08—0.15Mpa(0.80—1.50bar)2.3.4 三次气压(冷却倍压块、清洁放电针用气压):0.02—0.04Mpa(0.20—0.40bar)2.4 喷粉量2.4.1 喷粉量:是指单位时间内喷枪的出粉量,一般喷涂施工中喷粉量控制在100—200g/min。
静电喷塑技术要求及参考工艺

静电喷塑技术要求及参考工艺标准化管理处编码[BBX968T-XBB8968-NNJ668-MM9N]技术要求外观:无发蓝、麻点、黑点、针空、脱皮、粉团、桔皮、露底、碰伤、变形。
厚度:40-200μm。
在同一平面内距边缘10mm以内测量,测量时将测厚仪探头垂直接触待测面,每次测量上、中、下、左、右五点,取五点的平均值为厚度结果(五点中的最小值不能低于标准值)。
附着力:在厚度合格的零件表面上用刀片纵横刻划出11条间隔1 mm的线,使之形成100个小方格。
刀刃要垂直于表面,用力要均匀,深度划至钣金件。
用氧化锌(医用)胶布粘贴划格处,再以垂直方向揭起胶布,肉眼(或放大镜)检查涂层脱落情况。
光泽度:在同一平面内距边缘10mm以内测量,测量时将光泽仪探头垂直接触待测面,每次测量上、中、下、左、右五点,取五点的平均值为光泽度结果(五点中的最小值不能低于标准值)。
色差:ΔE≤。
用色差计测量。
参考工艺1. 除锈工序:1)工件打磨(手工消除工件锈斑、锈块)2)盐酸除锈(常温,浓度30%)15分钟3)清水清洗2分钟2. 除油工序:1)脱脂剂、除油粉(包括预脱脂和主脱脂)2)清水清洗2分钟3. 表面调整工序:1)胶汰表调剂(常温,PH8--10,浓度%)3--5分钟4. 磷化工序:1)磷化液+促进剂%(20--35℃,PH2--4)15--25分钟2)纯水清洗2分钟3)烘干,5-10分钟,须在8小时内喷塑5. 喷塑工序:1)清件(工件吹风,清渣,刷掉工件污垢)2)工件喷塑,厚度符合客户需求。
静电电压60—70KV,气压适当3)烘烤185--190℃,恒温保持15—20分钟6. 出件:工件出炉后,小心轻放,软性包装。
喷涂线流程图13-7-16

喷涂线工艺流程及工艺参数工艺流程图工艺列表该生产线由槽浸式前处理机、输送机电气控制系统等部分组成。
上件冷却 下件转挂·脱脂静电喷涂工艺流程为:工件前处理除锈→上件→水洗→烘干→喷漆→补漆→流平→冷却→检查→成品。
一、前处理:工件经过前处理除掉托辊表面的油污和灰尘后才能喷涂作业,同时在工件表面形成一层锌系磷化膜以增强喷漆后的附着力。
前处理后的工件必须完全烘干水分并且充分冷却到35℃以下才能保证喷漆后工件的理化性能和外观质量。
二、静电喷涂:静电喷漆的基本原理:工件通过输送链进入喷漆房的喷枪位置准备喷涂作业。
静电发生器通过喷枪枪口的电极针向工件方向的空间释放高压静电(负极),该高压静电使从喷枪口喷出的油漆和压缩空气的混合物以及电极周围空气电离(带负电荷)。
工件经过挂具通过输送链接地(接地极),这样就在喷枪和工件之间形成一个电场.油漆在电场力和压缩空气压力的双重推动下到达工件表面,依靠静电吸引在工件表面形成一层均匀的涂层三、固化固化过程分为流平、固化、冷却油漆在工件表面形成薄而平整的一层,此阶段称流平。
托辊经输送链条在烘房内油漆逐渐表干,经过热循环风、电加热油漆达到固化程度。
.四、检查固化后的工件,日常主要检查外观(是否平整光亮、有无颗粒、缩孔等缺陷)和厚度(控在30~60μm)。
如果首次调试或需要更换油漆时则要求使用相应的检测仪器检测如下项目:外观、光泽、色差、涂层厚度、附着力(划格法)、硬度(铅笔法)、冲击强度、耐盐雾(400h)、耐候性(人工加速老化)、耐湿热性(1 000h)五、成品检查后的成品分类摆放在成品对方区,出口项目按客户要求包装。
防止划伤并做好标识待用。
静电喷涂工艺参数

静电喷涂工艺参数静电喷涂是利用高压静电电场使带负电的涂料微粒沿着电场相反的方向定向运动,并将涂料微粒吸附在工件表面的一种喷涂方法。
其工艺参数主要包括以下几个方面:1. 喷涂电压:喷涂电压是静电喷涂的重要参数之一,它直接影响到涂料的荷电量和喷涂效果。
一般来说,喷涂电压越高,涂料的荷电量越大,喷涂效果也越好。
但过高的电压会导致涂料反弹和飞溅,因此需要根据涂料的性质和工件的形状来选择合适的喷涂电压。
2. 喷涂距离:喷涂距离是指喷枪与工件之间的距离,它也会影响到涂料的荷电量和喷涂效果。
一般来说,喷涂距离越近,涂料的荷电量越大,喷涂效果也越好。
但过近的距离会导致涂料聚集和流淌,因此需要根据涂料的性质和工件的形状来选择合适的喷涂距离。
3. 喷涂气压:喷涂气压是指喷枪内部的气压,它会影响到涂料的雾化效果和喷涂速度。
一般来说,喷涂气压越高,涂料的雾化效果越好,喷涂速度也越快。
但过高的气压会导致涂料反弹和飞溅,因此需要根据涂料的性质和工件的形状来选择合适的喷涂气压。
4. 涂料流量:涂料流量是指单位时间内喷枪喷出的涂料量,它会影响到涂料的覆盖面积和涂层厚度。
一般来说,涂料流量越大,涂料的覆盖面积越大,涂层厚度也越厚。
但过大的涂料流量会导致涂料流淌和浪费,因此需要根据涂料的性质和工件的形状来选择合适的涂料流量。
5. 喷枪移动速度:喷枪移动速度是指喷枪在工件表面移动的速度,它会影响到涂料的覆盖面积和涂层厚度。
一般来说,喷枪移动速度越快,涂料的覆盖面积越大,涂层厚度也越薄。
但过快的移动速度会导致涂料喷涂不均匀,因此需要根据涂料的性质和工件的形状来选择合适的喷枪移动速度。
总之,静电喷涂的工艺参数需要根据涂料的性质、工件的形状和要求来选择,以达到最佳的喷涂效果。
- 1、下载文档前请自行甄别文档内容的完整性,平台不提供额外的编辑、内容补充、找答案等附加服务。
- 2、"仅部分预览"的文档,不可在线预览部分如存在完整性等问题,可反馈申请退款(可完整预览的文档不适用该条件!)。
- 3、如文档侵犯您的权益,请联系客服反馈,我们会尽快为您处理(人工客服工作时间:9:00-18:30)。
静电喷涂的基本原理及技术参数
工件通过输送链进入喷粉房的喷枪位置准备喷涂作业。
静电发生器通过喷枪枪口的电极针向工件方向的空间释放高压静电(负极),该高压静电使从.喷枪口喷出的粉末和压缩空气的混合物以及电极周围空气电离(带负电荷)。
工件经过挂具通过输送链接地(接地极),这样就在
喷枪和工件之间形成一个电场占粉末在电场力和压缩空气压力的双重推动下到达工件表面,依靠静电吸引在工件表面形成一层均匀的涂层。
1.2.2 粉末静电喷涂的基本原料
用室内型环氧聚酯粉末涂料。
它的主要成分是环氧树脂、聚酯树脂、固化剂、颜料、填料、各种助剂(例如流平剂、防潮剂、边角改性剂等).粉末加热固化后在工件表面形成所需涂层。
辅助材料是压缩空气,要求清洁干燥、无油无水[含水量小于1.3g/m3、含油量小于1.0×10-5%(质量分数)]
1.2.3 粉末静电喷涂的施工工艺
●静电高压60-90kV。
电压过高容易造成粉末反弹和边缘麻点;电压过低上粉率低。
●静电电流10~20μA。
电流过高容易产生放电击穿粉末涂层;电流过低上粉率低
●流速压力0.30-0.55MPa.流速压力越.高则粉末的沉积速度越快,有利于快速获得预定
厚度的涂层,但过高就会增加粉末用量和喷枪的磨损速度。
●雾化压力0.30~0.45MPa。
适当增大雾化压力能够保持粉末涂层的厚度均匀,但过高会使送粉部件快速磨损。
适当降低雾化压力能够提高粉末的覆盖能力,但过低容易使送粉部件堵塞。
●清枪压力0.5MPa。
清枪压力过高会加速枪头磨损,过低容易造成枪头堵塞。
●供粉桶流化压力0.04~0.10MPa。
供粉桶流化压力过高会降低粉末密度使生产效率下降,过低容易出现供粉不足或者粉末结团。
●喷枪口至工件的距离150~300mm。
喷枪口至工件的距离过近容易产生放电击穿粉末涂层,过远会增加粉末用量和降低生产效率。
●输送链速度4.5~5.5m/min。
输送链速度过快会引起粉末涂层厚度不够,过慢则降低生产效率。
1.2.4 粉末静电喷涂的主要设备
●喷枪和静电控制器
喷枪除了传统的内藏式电极针,外部还设置了环形电晕而使静电场更加均匀以保持粉末
涂层的厚度均匀。
静电控制器产生需要的静电高压并维持其稳定,波动范围小于10%。
●供粉系统
供粉系统由新粉桶、旋转筛和供粉桶组成。
粉末涂料先加入到新粉桶,压缩空气通过新
粉桶底部的流化板上的微孔使粉末预流化,再经过粉泵输送到旋转筛。
旋转筛分离出粒径过大的粉末粒子(100μm以上),剩余粉末下落到供粉桶。
供粉桶将粉末流化到规定程度后通过粉泵和送粉管供给喷枪喷涂工件。
●回收系统
喷枪喷出的粉末除一部分吸附到工件表面上(一般为50%~70%,本公司为70%)外,其
余部分自然沉降。
沉降过程中的粉末一部分被喷粉棚侧壁的旋风回收器收集,利用离心分离原理使粒径较大的粉末粒子(12μm以上)分离出来并送回旋转筛重新利用。
12pom以下的粉
末粒子被送到滤芯回收器内,其中粉末被脉冲压缩空气振落到滤芯底部收集斗内,这部分粉末定期清理装箱等待出售。
分离出粉末的洁净空气(含有的粉末粒径小于1 μm、浓度小于
5g/m3)排放到喷粉室内以维持喷粉室内的微负压。
负压过大容易吸入喷粉室外的灰尘和杂质,负压过小或正压容易造成粉末外溢。
沉降到喷粉棚底部的粉末收集后通过粉泵进入旋转筛重新利用。
回收粉末与新粉末的混合比例为(1:3)~(1:1)。
使用该回收系统,本公司的总体粉末利用率平均达到95%。
●喷粉室体
顶板和壁板采用透光聚丙烯塑料材质,以最大限度减少粉末黏附量,防止静电荷累积干扰静电场。
底板和基座采用不锈钢材质,既便于清洁又具有足够的机械强度。
●辅助系统
包括空调器、除湿机。
空调器的作用一是保持喷粉温度在35℃以下以防止粉末结块;二是通过空气循环(风速小于0.3m/s)保持喷粉室的微负压。
除湿机的作用是保持喷粉室相对湿度为45%~55%,湿度过大空气容易产生放电击穿粉末涂层,过小导电性差不易电离。
1.3 固化
1.3.1 粉末固化的基本原理
环氧树脂中的环氧基、聚酯树脂中的羧基与固化剂中的胺基发生缩聚、加成反应交联成大分子网状体,同时释放出小分子气体(副产物)。
固化过程分为熔融、流平、胶化和固化4个阶段。
温度升高到熔点后工件上的表层粉末开始融化,并逐渐与内部粉末形成漩涡直至全部融化。
粉末全部融化后开始缓慢流动,在工件表面形成薄而平整的一层,此阶段称流平。
温度继续升高到达胶点后有几分短暂的胶化状态(温度保持不变),之后温度继续升高粉末发生化学反应而固化。
1.3.2 粉末固化的基本工艺
采用的粉末固化工艺为180℃,烘15min,属正常固化。
其中的温度和时间是指工件的实际温度和维持不低于这一温度的累积时间,而不是固化炉的设定温度和工件在炉内的行走时间。
但两者之间相互关联,设备最初调试时需要使用炉温跟踪仪测量最大工件的上、中、下3点表面温度及累积时间,并根据测量结果调整固化炉设定温度和输送链速度(它决定工件在炉内的行走时间),直至符合上述固化工艺要求。
这样就可以得出两者之间的对应关系,因此在一段时间内(一般为2个月)只需要控制速度即可保证固化工艺。
1.3.3 粉末固化的主要设备。