[整理]C6140普通车床主轴变速箱设计.
(完整版)普通型车床C6140主轴课程设计说明书

目录1、前言 (2)1.1金属切削机床在国民经济中的地位 ........................................1.2机床课程设计的目的 ....................................................1.3设计内容和要求 ........................................................ 2 2 22、参数的拟定 (3)2.1车床的规格系列和用处 ..................................................2.2确定极限转速 . .........................................................2.3主电机选择 . .......................................................... 3 3 33.传动设计 (3)3.1主传动方案拟定 . ......................................................3.2传动结构式、结构网的选择 . ............................................3.2.1 确定传动组及各传动组中传动副的数目 . ...............................3.2.2 传动式的拟定 . .....................................................3.2.3 结构式的拟定 . .....................................................3.3转速图的拟定 .......................................................... 3 4 4 4 4 54.传动件的估算 (6)4.1 V带传动的计算 ........................................................4.2传动轴的估算 . ........................................................4.2.1确定各轴转速 . ......................................................4.2.2 传动轴直径的估算 . .................................................4.3齿轮齿数的确定和模数的计算 . .........................................4.3.1 齿轮齿数的确定 . ..................................................4.3.2 齿轮模数的计算 . ..................................................4.3.4齿宽确定 . .........................................................4.4带轮结构设计 . .......................................................6 8 8 9 10101113145.动力设计 (14)5.1主轴刚度验算 .........................................................5.1.1 选定前端悬伸量 C ................................................. 5.1.2 主轴支承跨距 L 的确定 . ............................................5.1.3计算 C点挠度 . .....................................141414 错误!未定义书签。
C6140普通车床主轴变速箱设计

无锡太湖学院
毕业设计(论文)
题目:
车床主轴传动系统设计 单主轴变速机构设计
信机
系
模具设计与制造 专 业
学
号:
学生姓名: 指导教师:
2013 年 5 月 25 日
I
无锡太湖学院本科毕业设计(论文)
诚 信 承 诺 书
本人郑重声明:所呈交的毕业设计(论文) 《车床主轴传动系统
设计-单主轴变速机构设计》 是本人在导师的指导下独立进行研究所取 得的成果,除了在毕业设计(论文)中特别加以标注引用、表示致谢的 内容外,本毕业设计(论文)不包含任何其他个人
级: 号:
作者姓名: 2013 年 5 月 22 日
II
无锡太湖学院
信 机 系 模具设计与制造 专业
一、 题目及专题
1、 2、
题目 专题
车床主轴传动系统设计 单主轴变速机构设计
二、 课题来源及选题依据 课题来源为无锡某机械有限公司。 通过毕业设计是为了培养学生开发和 创新机械产品的能力,要求学生能够针对实际使用过程中存在的机床选择问 题,综合所学的机械理论设计与方法、专用机床设计方法,在机床基础型系 的基础上,设计一个简单的主传动变速系统,从而达到解决实际工程问题的 能力。 在设计传动件时,在满足产品工作要求的情况下,应尽可能多的采用标 准件,提高其互换性要求,以减少产品的设计生产成本。 三、 本设计(论文或其他)应达到的要求 1、 2、 该部件工作时,能运转正常; 拟定工作机构和驱动系统的运动方案,并进行多方案对比分析;
III
3、
根据车床的加工要求,设计出机床主传动系统的原理及绘制主传动 系 统的装配图;
4、 5、 6、 7、
对所设计的主传动系统进行必要的验算和推导; 绘制车床的主传动轴的零件图; 绘制车床主传动系转速图和变速传动系图; 编制设计说明书 1 份。
CA6140型车床进给箱设计(全套图纸)
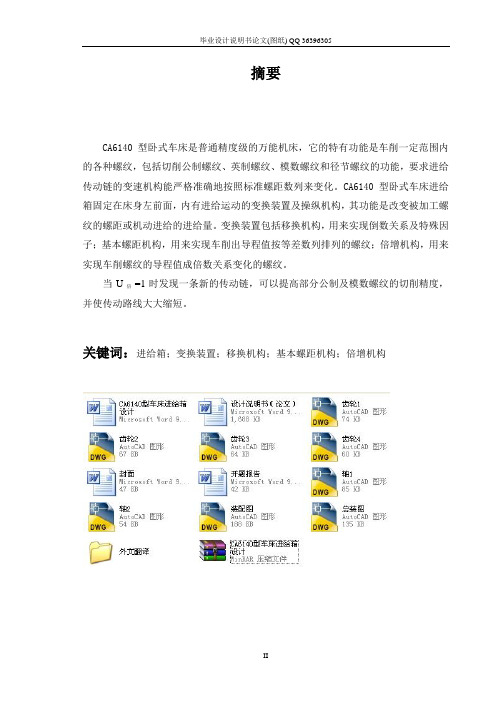
摘要CA6140型卧式车床是普通精度级的万能机床,它的特有功能是车削一定范围内的各种螺纹,包括切削公制螺纹、英制螺纹、模数螺纹和径节螺纹的功能,要求进给传动链的变速机构能严格准确地按照标准螺距数列来变化。
CA6140型卧式车床进给箱固定在床身左前面,内有进给运动的变换装置及操纵机构,其功能是改变被加工螺纹的螺距或机动进给的进给量。
变换装置包括移换机构,用来实现倒数关系及特殊因子;基本螺距机构,用来实现车削出导程值按等差数列排列的螺纹;倍增机构,用来实现车削螺纹的导程值成倍数关系变化的螺纹。
当U=1时发现一条新的传动链,可以提高部分公制及模数螺纹的切削精度,倍并使传动路线大大缩短。
关键词:进给箱;变换装置;移换机构;基本螺距机构;倍增机构目录1 绪论-----------------------------------------------------------------12 CA6140进给箱传动方案设计----------------------------------4 2.1 CA6140普通车床简介-------------------------------------------------------------------------4 2.2 进给箱的传动机构-----------------------------------------------------------------------------5 2.3 进给箱切螺纹机构设计----------------------------------------------------------------------8 2.4 切螺纹系统及齿数比的确定---------------------------------------------------------------9 2.5 增倍机构设计以及移换机构设计--------------------------------------------------------102.6 车制螺纹的工作过程-------------------------------------------------------------------------123 主要零件设计-----------------------------------------------------21 3.1 齿式离合器的设计-----------------------------------------------------------------------------21 3.2 各轴及轴上组件的设计验算---------------------------------------------------------------213.2.1 中心距a的确定----------------------------------------------------------------------------223.2.2 XII轴上齿轮的设计验算-----------------------------------------------------------------223.2.3 XIV轴上齿轮的验算----------------------------------------------------------------------253.2.4 XIV轴的设计验算-------------------------------------------------------------------------303.2.5 XV轴上齿轮的设计验算-----------------------------------------------------------------353.2.6 XV轴的设计验算--------------------------------------------------------------------------383.2.7 XVI轴齿轮的设计验算-------------------------------------------------------------------404 双联滑移齿轮进给箱传动系统的研究-----------------------44 4.1 新传动链车公制螺纹-------------------------------------------------------------------------44 4.2 新传动链车模数螺纹-------------------------------------------------------------------------45 4.3 新传动链的特点及适用范围---------------------------------------------------------------46 结论---------------------------------------------------------------------------48致谢---------------------------------------------------------------------------49参考文献---------------------------------------------------------------------501 绪论1、毕业设计的目的及意义毕业设计是本科生教学活动中最后的一个重要环节。
C6140普通车床主轴箱传动设计说明书

设计题目:C6140普通车床主轴箱传动设计摘要目前机床主轴变速箱的设计还是以经验或类比为基础的传统(经验)设计方法。
本文探索科学理论的应用,科学地分析的处理经验,数据和资料,确定设计方案:1. 参数拟定根据机床类型,规格和其他特点,了解典型工艺的切削用量,结合实际条件和情况,并与同类机床对比分析后确定:极限转速m axn 和m in n ,公比 (或级数Z ),主传动电机功率N 。
2. 传动设计根据拟定的参数,通过结构网和转速图的分析,确定转动结构方案和转动系统图,计算各转动副的传动比及齿轮的齿数,并验算主轴的转速误差。
3. 动力计算和结构草图设计估算齿输模数m 和直径d ,选择和计算反向离合器,制动器。
将各传动件及其它零件在展开图和剖面图上做初步的安排,布置和设计。
4. V 带的设计在结构草图的基础上,进行V 带和带轮的设计和计算。
5. 主轴变速箱装配设计主轴变速箱装配图是以结构草图为“底稿”,进行设计和会制的。
图上各零件要表达清楚,并标注尺寸和配合。
这样既能提高机床设计和制造水平,也将促进设计方法的现代化。
关键词: 齿轮; 结构设计; 箱体AbstractThe machine tool spindle gear box design or to experience or analogy based on traditional design method ( experience ).This paper explores the application of scientific theory, scientific analysis of the processing experience, data and information, the determination of design scheme:According to the machine type, size and other characteristics, understanding the typical process of cutting parameters, with the world's terms and conditions, and with a similar machine after the comparative analysis to determine: speed and, common ratio ( or series Z ), the main drive motor power N.The 2transmission designAccording to the parameter drafted, through the structure of network and speed chart analysis, determine the rotational structure scheme and the rotation system diagram, calculation of the rotation pairs of transmission ratio and gear teeth, and checking the spindle speed error.3dynamic calculation and structure sketch designEstimation of gear modulus m and D diameter, selection and calculation of reverse clutch, brake.The transmission parts and other parts in the expansion plans and sections do preliminary arrangement, layout and design.4shaft and bearing calculationIn the structure of the draft on the basis, a transmission shaft stiffness and the shafting bearing life checking.5spindle gear box assembly designMain gearbox assembly drawing is the structure sketch for" papers", design and system. Map all parts to express clearly, and dimensioning and coordination.This can enhance the machine tool design and manufacturing level, also will promote the modernization design method.Key words: gear box; structure design;目录1.车床参数的拟定 (3)1.1概述 (3)1.2参数的拟定 (3)2.传动设计 (5)2.1传动结构式、结构网的选择确定 (5)2.2 转速图的拟定 (7)2.3齿轮齿数的确定及传动系统图的绘制 (9)3.动力计算和结构草图设计 (13)3.1计算转速 (13)3.2传动轴的估算和验算 (13)3.3齿轮模数的估算和计算 (18)3.4轴承的选择和校核 (23)3.5摩擦离合器的选择与校核 (26)4.V带的设计 (29)4.1V带的传动计算 (29)4.2传动轴的估算 (31)4.3齿轮模数的确定和模数的计算 (33)4.4带轮结构设计 (38)4.5片式摩擦离合器的选择和计算 (38)5.主轴变速箱装配设计 (41)5.1主轴刚度验算 (41)5.2齿轮校验 (43)5.3轴承的校验 (44)5.4轴轮块的设计 (45)5.5传动轴的设计 (46)5.6主轴组件的设计 (47)结束语 (52)致谢 (53)参考文献 (54)1.车床参数的拟定1.1概述普通机床的规格和类型有系列型谱作为设计时应该遵照的基础。
(完整版)CA6140车床主轴箱的含图毕业设计
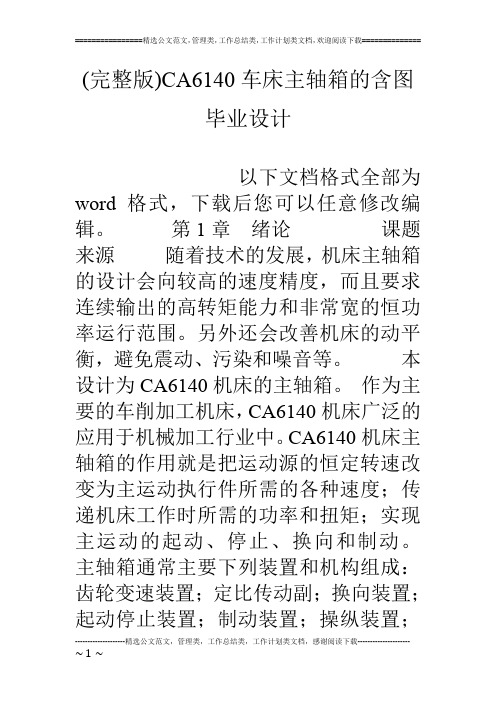
(完整版)CA6140车床主轴箱的含图毕业设计以下文档格式全部为word格式,下载后您可以任意修改编辑。
第1章绪论课题来源随着技术的发展,机床主轴箱的设计会向较高的速度精度,而且要求连续输出的高转矩能力和非常宽的恒功率运行范围。
另外还会改善机床的动平衡,避免震动、污染和噪音等。
本设计为CA6140机床的主轴箱。
作为主要的车削加工机床,CA6140机床广泛的应用于机械加工行业中。
CA6140机床主轴箱的作用就是把运动源的恒定转速改变为主运动执行件所需的各种速度;传递机床工作时所需的功率和扭矩;实现主运动的起动、停止、换向和制动。
主轴箱通常主要下列装置和机构组成:齿轮变速装置;定比传动副;换向装置;起动停止装置;制动装置;操纵装置;密封装置;主轴部件和箱体。
根据机床的用途和性能不同,有的机床主轴箱可以只包括其中的部分装置和部件。
主轴箱是支承主轴并安装主轴的传动变速装置,使主轴获得各种不同转速,以实现主切削运动。
该机床主轴箱刚性好、功率大、操作方便。
CA6140机床可进行各种车削工作,并可加工公制、英制、模数和径节螺纹。
主轴三支撑均采用滚动轴承;进给系统用双轴滑移共用齿轮机构;纵向与横向进给十字手柄操纵,并附有快速电机。
该机床刚性好、功率大、操作方便。
研究动态及发展趋势机床设计和制造的发展速度是很快的。
原先的只为满足加工成形而要求刀具与工件间的某些相对运动关系和零件的一定强度和刚度,发展至今日的高度科学技术成果综合应用的现代机床的设计,也包括计算机辅助设计的应用。
但目前机床主轴变速箱的设计还是以经验或类比为基础的传统设计方法。
因此,探索科学理论的应用,科学地分析的处理经验,数据和资料,既能提高机床设计和制造水平,也将促进设计方法的现代化。
随着科学技术的不断发展,机械产品日趋精密、复杂,改型也日益频繁,对机床的性能、精度、自动化程度等提出了越来越高的要求。
机械加工工艺过程自动化是实现上述要求的重要技术措施之一,不仅能提高产品质量和生产率,降低生产成本,还能改善工人的劳动条件。
CA6140车床主轴箱的设计说明书

CA6140车床主轴箱的设计摘要在工业生产的很多时候都要用到CA6140车床,然而,这种车床的自动化程度不高,结构又相对复杂,如果要加工一些相对复杂的工件,就需要不断换刀,给实际操作带来很多麻烦,再加上这种车床的加工过程较慢,造成效率不高,所以,只能在单件或者小批量生产中广泛应用。
本文主要对该机床的主轴箱进行了设计,采用三轴支撑的滚动轴承,加上双轴滑移的共用齿轮作为进给体系;加上快速电机和十字手柄,极大改善了机床的性能,提高了操作性。
本文从CA6140机床的参数设定、传动体系图制定、传动方案制定,主要零部件的校荷,对该机床的主轴箱设计进行了说明,并附有机床了零部件整体装配详图。
关键词:CA6140机床;主轴箱;零件;传动;AbstractThe scope of application of CA6140 lathe is very extensive, but the complex structure and low degree of automation, the workpiece processing is more complicated in shape, change the knife trouble, in the process of auxiliary time is relatively long, low productivity, suitable for single or small batch production. The main shaft three support adopts the rolling bearing; the feed system uses the two axle sliding common gear mechanism; the longitudinal and transverse feed is controlled by the cross handle. The machine has good rigidity, large power and convenient operation.As a major turning processing machine, CA6140 machine is widely used in mechanical processing industry, the design of the main spindle box for CA6140 machine design, design is the main content of the main parameters of the machine, drawing up the transmission plan and the transmission scheme, the main parts of the calculation and checking, the use of CAD drawing software design and processing of parts.Keywords: CA6140 machine tool ;spindle box ;parts ;transmission目录第1章引言 (5)第2章主要技术参数 (6)第3章传动方案和传动系统图的拟定 (8)3.1. 主运动传动链 (8)3.2. 进给传动链 (11)第4章主要设计零件的计算和验算 (15)4.1主轴箱的箱体 (15)4.2.传动系统的I轴及轴上零件设计 (17)4.2.1普通V带传动的计算 (17)4.2.2多片式摩擦离合器的计算 (19)4.2.3齿轮的验算 (21)4.2.4传动轴的验算 (24)4.2.5轴承疲劳强度校核 (26)4.3.传动系统的Ⅱ轴及轴上零件设计 (27)4.3.1齿轮的验算 (27)4.3.2传动轴的验算 (31)4.3.3轴组件的刚度验算 (32)4.4 传动系统的Ⅲ轴及轴上零件设计 (34)4.4.1齿轮的验算 (34)4.4.2 传动轴的验算 (38)4.4.3 轴组件的刚度验算 (40)4.5传动系统的Ⅳ轴及轴上零件设计 (42)4.5.1齿轮的验算 (42)4.5.2传动轴的验算 (45)4.5.3轴组件的刚度验算 (48)4.6. 传动系统的Ⅴ轴及轴上零件设计 (50)4.6.1齿轮的验算 (50)4.6.2传动轴的验算 (54)4.6.3轴组件的刚度验算 (56)结论 (59)毕业设计小结 (59)参考文献 (64)致谢 (65)第1章引言在车床类中。
CA6140型车床主轴箱操纵机构及轴的毕业设计(可编辑)

摘要此次毕业设计要求综合的运用机械制图、机械设计、机械原理、机械制造技术、金属切削机床设计等相关知识对CA6140型卧式车床进行了传动设计,主要对其主轴箱的结构和传动原理进行深入的了解。
CA6140车床是我国设计制造的典型的卧式车床,在我国机械制造类行业中使用极为广泛。
近些年,虽然随着电子计算机的发展,数控技术和数控机床得到的较大的发展,但通过对普通车床的研究和设计,可以开阔我们的视野,增强我们的实践经验,加强我们自己动手的工作能力,巩固所学知识,在我们马上要走上工作岗位之际,对提高我们的专业素质有很大的帮助。
本次毕业设计的研究内容、方法、成果:1、通过绘制车床主轴箱操纵机构的装配图,进一步深入的了解了主轴箱的结构和其传动原理;2、通过运用机械原理和机械设计等知识对车床进给箱中的轴进行设计和校核;3、最后运用机械制图知识绘出CA6140型卧式车床主轴箱操纵机构,并运用AutoCAD制图软件绘制进给箱中的014轴,进一步熟练了CAD的使用。
关键词:CA6140型车床;主轴箱;传动系统;轴的设计;轴的绘制;ABSTRACTThe integrated design uses a mechanical drawing,mechanical design, mechanical principles, machinery manufacturing technology, Metal Cutting Machine design knowledge to CA6140 horizontal lathe design of the drive, Headstock mainly on the structure and box drive principle in-depth understanding. CA6140 lathe is the design and manufacture of a typical horizontal lathe. China's machinery manufacturing industries, is widely used. In recent years, although the development of electronic computers, technology and CNC machine tool CNC is the larger development, But through Lathe of research and design, broadening our horizons, enhance our practical experience, strengthen our own hands the ability to consolidate knowledge, we all got to go to work when to improve the professional quality of our great helpThe graduation of the study design, methods, results :1. Drawing spindle lathes me through manipulation of the assembly, further in-depth understanding of the structure of the spindle box and its drive principle2. Through the use of mechanical principles and mechanical design knowledge to design and check the shaft in lathe3. Finally the use of AutoCAD software rendering the machine spindle and operating mechanism , and the use of CAD to render the 014 shaft in lathe;Further skilled in the use ofCADKeywords : CA6140 lathe; Headstock; Transmission; Axis designs; Axis drawing.目录第一章绪论 11.1 毕业设计的目的及意义 11.2毕业设计的内容 11.3设计步骤 21.4设计时应注意的事项3第二章 CA6140型卧式车床的简介 42.1 CA6140车床的用途 42.2 CA6140车床的分类 52.3 CA6140工艺范围52.4 CA6140车床的布局 5第三章 CA6140型车床传动系统83.1车床传动路线及传动分析83.2 主轴箱的传动链 103.3 主轴箱的主要构造12第四章 CA6140型车床齿轮传动设计184.1分级变速传动链设计184.2动力计算224.3计算转速244.4机床的功率转矩特性24第五章 CA6140型卧式车床主轴箱结构设计265.1轴的设计及轴上零件的定位265.2 轴承、密封、润滑285.3齿轮305.4操纵机构315.5箱体34第六章 014轴(ⅩⅢ轴)的设计计算及校核396.1轴的结构设计原则396.2轴的强度计算406.3轴的材料及选择416.4 014轴(ⅩⅢ轴)的设计计算及校核45参考文献50致谢 51第一章绪论1.1 毕业设计的目的及意义毕业课题(论文)教学过程是实现本科培养目标要求的重要阶段,是基础理论学习深化与升华的重要环节,是全面检验学生综合素质与实践能力培养效果的主要手段,是学生毕业及学位资格认证的重要依据,是衡量高等学校教育质量和办学效益的重要评价内容。
CA6140车床主轴箱的传动系统设计另外有完整图纸解析

CA6140车床主轴箱的传动系统设计另外有完整图纸解析A6140车床主轴箱传动系统设计及仿真摘要:CA6140卧室车床属于通⽤的中型机床,其主要组成部分可概括为“三箱⼑架尾座床⾝”。
此毕业设计是对CA6140车床主轴箱的传动系统及仿真进⾏设计,设计的内容包括:主传动系统总体设计、机床主轴箱设计传动设计、动⼒计算。
主传动系统总体设计包括主传动形式选择、主轴电机选择及功率计算;机床主轴箱设计传动设计:拟定主传动参数、结构⽹、转速图、确定齿轮齿数和带轮直径,主传动的转向与制动⽅式,画出主运动的传动系统图;动⼒计算,其中包括确定齿轮模数,轴的尺、轴承的形式和型号,以及其他有关的计算。
我运⽤CAD完成了主轴箱的⼆维总装配图和⼏个轴上零件的装配图,运⽤Pro-E软件完成零件设计(轴、齿轮、箱体、轴承等并进⾏了虚拟装配和仿真,保存了仿真的视频格式并且在Pro-E5.0界⾯中让它运⾏起来。
关键词:CA6140机床;主轴箱;零件传动Design and Simulation of CA6140 lathe main spindle boxdrive systemAbstract:CA6140 lathe is a versatile medium-sized bedrooms machine, the main components can be summarized as "three-box turret tailstock bed." This graduation project is a drive system and simulation CA6140 lathe headstock design, the design includes: overall design of the main drive system, the spindle box design transmission design, dynamic calculation. The overall design of main drive system includes a main form of transmission choice, selection and spindle motor power calculation; spindle box design transmission design: Preparation of the main transmission parameters, network structure, speed diagram, determine the diameter of the pulley and gear, main drive and steering system dynamic way, to draw the main motion drive system diagram; dynamic calculation, including the identification of the gear module, feet, bearing forms and models, as well as other relevant calculation axis. I use CAD finished headstock assembly drawing two-dimensional assembly drawing and parts of several axes, the use of Pro-E design software to complete parts (shafts, gears, box, bearings and virtual assembly simulation and save simulation video formats and let the Pro-E5.0 interface up and running. Keywords: CA6140 machine; headstock; transmission parts1、绪论1简介主题1.1⾦属切削机床国内外研究现状⾦属切削机床是采⽤切削⼯具,去除⼯件上多余的⾦属它是制造机器的机器,通常称之为“机床”。
- 1、下载文档前请自行甄别文档内容的完整性,平台不提供额外的编辑、内容补充、找答案等附加服务。
- 2、"仅部分预览"的文档,不可在线预览部分如存在完整性等问题,可反馈申请退款(可完整预览的文档不适用该条件!)。
- 3、如文档侵犯您的权益,请联系客服反馈,我们会尽快为您处理(人工客服工作时间:9:00-18:30)。
最大加工直径为Ф400mm普通车床主轴变速箱设计院(系) 部:机械工程系学生姓名:指导教师:刘吉兆(教授)专业:机械设计制造及其自动化班级:完成时间:2007年1月目录1.车床参数的拟定- ------------------------------------------------------2 1.1车床主参数和基本参数------------------------------------------------21.1.1拟定参数的步骤和方法----------------------------------------------22.运动设计- ------------------------------------------------------------4 2.1传动结构式、结构网的选择确定-----------------------------------------4 2.1.1传动组及各传动组中传动副的数目------------------------------------4 2.1.2传动系统扩大顺序的安排 -------------------------------------------4 2.1.3绘制结构网--------------------------------------------------------4 2.1.4传动组的变速范围的极限值------------------------------------------5 2.1.5最大扩大组的选择--------------------------------------------------5 2.2转速图的拟定--------------------------------------------------------6 2.2.1主电机的选定------------------------------------------------------6 2.3齿轮齿数的确定及传动系统图的绘制------------------------------------7 2.3.1齿轮齿数的确定的要求----------------------------------------------72.3.2变速传动组中齿轮齿数的确定----------------------------------------83.强度计算和结构草图设计-- --------------------------------------------11 3.1确定计算转速-------------------------------------------------------11 3.1.1主轴的计算转速---------------------------------------------------11 3.1.2中间传动件的计算转速---------------------------------------------11 3.1.3齿轮的计算转速---------------------------------------------------12 3.2传动轴的估算和验算-------------------------------------------------12 3.2.1传动轴直径的估算-------------------------------------------------12 3.2.2主轴的设计与计算-------------------------------------------------13 3.2.3主轴材料与热处理-------------------------------------------------16 3.3齿轮模数的估算和计算-----------------------------------------------16 3.3.1齿轮模数的估算---------------------------------------------------16 3.3.2齿轮模数的验算---------------------------------------------------19 3.4轴承的选择与校核---------------------------------------------------21 3.4.1一般传动轴上的轴承选择-------------------------------------------21 3.4.2主轴轴承的类型---------------------------------------------------22 3.4.3轴承间隙调整-----------------------------------------------------22 3.4.4轴承的校核-------------------------------------------------------23 3.5摩擦离合器的选择与验算---------------------------------------------23 3.5.1按扭矩选择-------------------------------------------------------24 3.5摩擦离合器的选择与验算---------------------------------------------24 3.5.1按扭矩选择-------------------------------------------------------24 3.5.2外摩擦片的内径d- ------------------------------------------------25 3.5.3选择摩擦片尺寸(自行设计)-----------------------------------------25 3.5.4计算摩擦面的对数Z------------------------------------------------25 3.5.5摩擦片片数 ------------------------------------------------------25参考文献- -------------------------------------------------------------261.车床参数的拟定1.1车床主参数和基本参数1.1.1拟定参数的步骤和方法1)极限切削速度Vmax 、Vmin根据典型的和可能的工艺选取极限切削速度要考虑: 允许的切速极限参考值如下:根据给出条件,取Vmax=150 m/min 螺纹加工和铰孔时取 Vmin=4 m/min2)主轴的极限转速计算车床主轴极限转速时的加工直径,按经验分别取K=0.5,Rn=0.25。
则主轴极限转速应为:取标准数列数值,即m ax n =1250r/min在min n 中考虑车螺纹和铰孔时,其加工的最大直径应根据实际加工情况选取50mm 左右。
min n =8.314014.3410001000max min =⨯⨯=d v πr/min取标准数列数值,即min n =28r/min转速范围Rn=minmaxn n 转速范围Rn=min max n n =281250=44.64r/min取41.1=ϕ Z=41.1lg 64.44lg 1lg lg 1+=+ϕn R =12 min/114625.05.04001415.3180100010001000min max r DkRn v d v n maz maz =⨯⨯⨯⨯===ππ考虑到设计的结构复杂程度要适中,故采用常规的扩大传动。
并选级数Z=12,各级转速数列可直接从标准的数列表中查出,按标准转速数列为:28,40,56,80,112,160,224,315,450,630,900,1250 3)主轴转速级数Z 和公比Φ 已知Rn=minmax n nRn=ΦZ-1且Z=2a x3ba 、b 为正整数,即Z 应可以分解为2和3的因子,以便用2、3联滑移齿轮实现变速。
取Z=12级 则Z=223⨯minmax1n n R Z n =Φ=- 11241.1-8.43==Rn m ax n =1250 m in n =28 Rn=minmaxn n =44.64 综合上述可得:主传动部件的运动参数1250max =n m in n =28 Z=12 Φ=1.414)主电机功率——动力参数的确定合理地确定电机功率N ,使机床既能充分发挥其性能,满足生产需要,又不致使电机经常轻载而降低功率因素。
中型普通车床典型重切削条件下的用量 刀具材料:YT15工件材料45号钢,切削方式:车削外圆 查表可知:切深a p =3.5mm 进给量f(s)=0.35mm/r 切削速度V=90m/min 功率估算法用的计算公式 a 主切削力:Fz=1900apf 0.75=190035.05.3⨯⨯0.75=3026Nb 切削功率:N 切=61200V F Z KW=61200903026⨯KW=4.45KWc 估算主电机功率:N=总切ηN =8.045.4=5.5KW 可选取电机为:Y132S-4额定功率为5.5KW ,满载转速为1440r/min.2.运动设计2.1传动结构式、结构网的选择确定2.1.1传动组及各传动组中传动副的数目级数为Z 的传动系统由若干个顺序的传递组组成,各传动组分别有Z1、Z2、Z3、…个传动副.即Z=Z 1Z 2Z 3…传动副数由于结构的限制以2或3为适合,即变速级数Z 应为2和3的因子: 即Z=2a 3b实现12级主轴转速变化的传动系统可以写成多种传动副的组合: 1) 12=3×4 2) 12=4×3 3) 12=3×2×2 4) 12=2×3×25) 12=2×2×3按照传动副“前多后少”的原则选择Z=3×2×2这一方案,但主轴换向采用双向片式摩擦离合器结构,致使Ⅰ轴的轴向尺寸过大,所以此方案不宜采用,而应先择12=2×3×2。
方案4)是比较合理的 12=2×3×22.1.2 传动系统扩大顺序的安排12=2×3×2的传动副组合,其传动组的扩大顺序又可以有6种形式: 1) 12=21×32×26 2) 12=21×34×22 3) 12=23×31×26 4) 12=26×31×23 5) 12=22×34×21 6) 12=26×32×21根据级比指数分配要“前密后疏”的原则,应选用Z=12×23×62这一方案,然而对于我们所设计的结构将会出现两个问题:第一变速组采用降速传动时,由于摩擦离合器径向结构尺寸限制,使得Ⅰ轴上的齿轮直径不能太小,Ⅱ轴上的齿轮则会成倍增大。