生产计划与物料控制PMC培训教材.pptx
合集下载
PMC培训资料生产计划与物料控制PPT文档共96页

61、奢侈是舒适的,否则就不是奢侈 。——CocoCha nel 62、少而好学,如日出之阳;壮而好学 ,如日 中之光 ;志而 好学, 如炳烛 之光。 ——刘 向 63、三军可夺帅也,匹夫不可夺志也。 ——孔 丘 64、人生就是学校。在那里,与其说好 的教师 是幸福 ,不如 说好的 教师是 不幸。 ——海 贝尔 65、接受挑战,就可以享受胜利的喜悦 。——杰纳勒 尔·乔治·S·巴顿人民应该为法律而战斗,就像为 了城墙 而战斗 一样。 ——赫 拉克利 特 17、人类对于不公正的行为加以指责 ,并非 因为他 们愿意 做出这 种行为 ,而是 惟恐自 己会成 为这种 行为的 牺牲者 。—— 柏拉图 18、制定法律法令,就是为了不让强 者做什 么事都 横行霸 道。— —奥维 德 19、法律是社会的习惯和思想的结晶 。—— 托·伍·威尔逊 20、人们嘴上挂着的法律,其真实含 义是财 富。— —爱献 生
谢谢!
生产计划与物料管理(PMC)培训教材
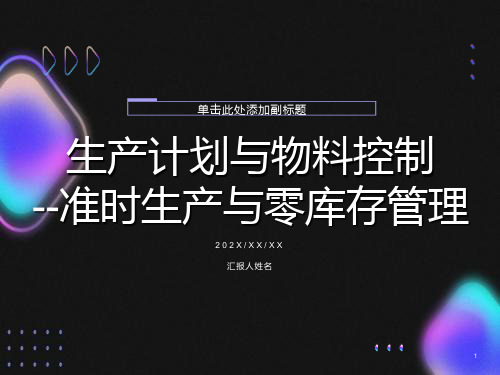
*
运行有效性
OEE - Overall Equipment Effectiveness TPM - Total Preventive Maintenance QCO - Quick Change Over 总的设备有效性 全员设备维护 快速换型
.…实际....657.…目标...700..........
减速 – 满负荷的80%
较小的停工 – 30 min
废品 – 2%
作业起动损失-15 min
总的设备有效性计算示例 - 切削设备
*
Benefits: 1. Reduced machine downtime 2. Flexibility in scheduling 3. Reduced cost of scrap 4. Reduced inventory holding costs 5. Increased capacity
看板挂板
Run /生产点
A
D
E
F
G
B
C
OD
D
产能力匹配与平衡(均衡化与匹配)
01
生产同期化
02
生产一个流
03
在制造过程中追求:
JIT的实施
8
A B C D E F G H I J
瓶 颈
不平衡时的库存、损耗
10
10
8
11
9
9
10
大批量生产
降低成本
刺激需求
批量的扩大
精益生产方式 精益生产方式是美国在全面研究以JIT生产方式为代表的日本式生产方式在西方发达国家以及发展中国家应用情况的基础上,于1990年提出的一种较完整的经营管理理论。
第三章、JIT的现场控制
PMC培训资料生产计划与物料控制2

PPT文档演模板
物料管理范围和意义 •物料管理的范围
•物料计划及物料控制
•Material Control
•采 购 •Purchasing
•仓库 •Warehouse
PMC培训资料生产计划与物料控制2
•第一室:物料控制管理概述
•凝 •聚 •真 •知 •, •协 •同 •共 •进
PPT文档演模板
•物料管理范围和意义 •物料管理的意义
差异率 盘点正确率 呆料率
废料处理
损耗控制PMC培训资料生产计划与物料控制2
物料管理执行流程
•业务
•生产管 制
•物料管理
•物料管理 •采购
•依照客 户订单发
出工厂订 单
•订单生 产计划
•新产品 •产品登记 分析
•寻找厂商报 价、送样品
•仓库
•工程
•厂部生 产
•物料规格确定验收标 准 •物料编制管理
编制/日期:
审批/日期: PMC培训资料生产计划与物料控制2
•第一室:物料控制管理概述
•凝 •聚 •真 •知 •, •协 •同 •共 •进
PPT文档演模板
•案例分析和分组 发表
• 某印刷厂印前部在2004年2月1号印刷OP唛24双耳有盖 盒过程中发现:
生产单编码:124824的订单在完成后需要500PCS(交 货数6464石)
•物料管理与生产体系的九方面关系连接图
•人
材料
产能计划
•需求量计算
• 产能计划
内个制区分
采购
内个制区分
日程计划
交货期管理
日程计划
插卡箱
•凝
进度管理
入库验收 仓储管理
插卡箱 进度管理
•聚 •真
物料管理范围和意义 •物料管理的范围
•物料计划及物料控制
•Material Control
•采 购 •Purchasing
•仓库 •Warehouse
PMC培训资料生产计划与物料控制2
•第一室:物料控制管理概述
•凝 •聚 •真 •知 •, •协 •同 •共 •进
PPT文档演模板
•物料管理范围和意义 •物料管理的意义
差异率 盘点正确率 呆料率
废料处理
损耗控制PMC培训资料生产计划与物料控制2
物料管理执行流程
•业务
•生产管 制
•物料管理
•物料管理 •采购
•依照客 户订单发
出工厂订 单
•订单生 产计划
•新产品 •产品登记 分析
•寻找厂商报 价、送样品
•仓库
•工程
•厂部生 产
•物料规格确定验收标 准 •物料编制管理
编制/日期:
审批/日期: PMC培训资料生产计划与物料控制2
•第一室:物料控制管理概述
•凝 •聚 •真 •知 •, •协 •同 •共 •进
PPT文档演模板
•案例分析和分组 发表
• 某印刷厂印前部在2004年2月1号印刷OP唛24双耳有盖 盒过程中发现:
生产单编码:124824的订单在完成后需要500PCS(交 货数6464石)
•物料管理与生产体系的九方面关系连接图
•人
材料
产能计划
•需求量计算
• 产能计划
内个制区分
采购
内个制区分
日程计划
交货期管理
日程计划
插卡箱
•凝
进度管理
入库验收 仓储管理
插卡箱 进度管理
•聚 •真
生产计划与物料控制(PMC)PPT课件81页PPT

生产计划与物料控制(PMቤተ መጻሕፍቲ ባይዱ)PPT课件
46、法律有权打破平静。——马·格林 47、在一千磅法律里,没有一盎司仁 爱。— —英国
48、法律一多,公正就少。——托·富 勒 49、犯罪总是以惩罚相补偿;只有处 罚才能 使犯罪 得到偿 还。— —达雷 尔
50、弱者比强者更能得到法律的保护 。—— 威·厄尔
66、节制使快乐增加并使享受加强。 ——德 谟克利 特 67、今天应做的事没有做,明天再早也 是耽误 了。——裴斯 泰洛齐 68、决定一个人的一生,以及整个命运 的,只 是一瞬 之间。 ——歌 德 69、懒人无法享受休息之乐。——拉布 克 70、浪费时间是一桩大罪过。——卢梭
46、法律有权打破平静。——马·格林 47、在一千磅法律里,没有一盎司仁 爱。— —英国
48、法律一多,公正就少。——托·富 勒 49、犯罪总是以惩罚相补偿;只有处 罚才能 使犯罪 得到偿 还。— —达雷 尔
50、弱者比强者更能得到法律的保护 。—— 威·厄尔
66、节制使快乐增加并使享受加强。 ——德 谟克利 特 67、今天应做的事没有做,明天再早也 是耽误 了。——裴斯 泰洛齐 68、决定一个人的一生,以及整个命运 的,只 是一瞬 之间。 ——歌 德 69、懒人无法享受休息之乐。——拉布 克 70、浪费时间是一桩大罪过。——卢梭
PMC生产计划与物料控制ppt课件

要维持事宜的库存必须由结果库存转向计划库存。
制定库存计划必须要有信息。因而,销售部门必须就产品类别对各种产品的 销路作预测。说起产品类别,因现在是多品种时代,品种数量之多,令人惊讶。不 过,按产品类别的销售预测是库存管理的开端,因此,即使麻烦也不能马虎。
通常,预测是在月初或每旬,以按一定周期的循环方式进行的。预测面临的 首要题目是预测期间,既要解决预测的提前量。作为结论,它应该是产品的最长工 作日程加上预测周期后的天数。例如,最长工作日程是3个月,预测周期1个月,预 测期间就是4个月。
过程流程图
①不同零部件的加工顺序; ②标准时间 ③标准批量; ④工作日程
零件明细
12 2024/2/10
2.2 计划的形态——日程计划
X工序 基准日程5天
连续型的工作日程
Y工序
Z工序
基准日程8天
基准日程9天
Y工序的开工工作日程17天
加工零部件索要的总工作日程22天
并行型的工作日程
2024/2/10
外加工品日程计划的制订 方法,同工厂内工序的日程计 划完全相同。基准日程也与工 厂内工序一样。
①铸造工序
10月2日
外加工订货的日程计划
②车床工序
10月4日
交货期10月10日
③外加工工序
10月6日
④完成 工序
10月9日
天
1
若有外加工品所需要的标 准时间资料,那么也能制定与 其关联的复合计划。
有关外加工品的开工日与 完工日的日程计划,图中使用 的是倒计时的方式,具有连续
2024/2/10
从大日程计划到中日程计划
6月
7月
123
29 30 1 2 3
日日日
日 日 日日日
制定库存计划必须要有信息。因而,销售部门必须就产品类别对各种产品的 销路作预测。说起产品类别,因现在是多品种时代,品种数量之多,令人惊讶。不 过,按产品类别的销售预测是库存管理的开端,因此,即使麻烦也不能马虎。
通常,预测是在月初或每旬,以按一定周期的循环方式进行的。预测面临的 首要题目是预测期间,既要解决预测的提前量。作为结论,它应该是产品的最长工 作日程加上预测周期后的天数。例如,最长工作日程是3个月,预测周期1个月,预 测期间就是4个月。
过程流程图
①不同零部件的加工顺序; ②标准时间 ③标准批量; ④工作日程
零件明细
12 2024/2/10
2.2 计划的形态——日程计划
X工序 基准日程5天
连续型的工作日程
Y工序
Z工序
基准日程8天
基准日程9天
Y工序的开工工作日程17天
加工零部件索要的总工作日程22天
并行型的工作日程
2024/2/10
外加工品日程计划的制订 方法,同工厂内工序的日程计 划完全相同。基准日程也与工 厂内工序一样。
①铸造工序
10月2日
外加工订货的日程计划
②车床工序
10月4日
交货期10月10日
③外加工工序
10月6日
④完成 工序
10月9日
天
1
若有外加工品所需要的标 准时间资料,那么也能制定与 其关联的复合计划。
有关外加工品的开工日与 完工日的日程计划,图中使用 的是倒计时的方式,具有连续
2024/2/10
从大日程计划到中日程计划
6月
7月
123
29 30 1 2 3
日日日
日 日 日日日
生产计划和物料控制(PMC) ppt课件

物料备料与催料流程 备料检验及品质异常处理流程 物料收发制度及执行 制定库存量考核方案
仓库呆料处理制度
帐物一致相关制度
ppt课件 9
第三室:材料计划和存量控制
采购必备的条件和依据
1、条件
• • • • • • • • • • 根据不同的物料、供应商使用不同的采购方式 信息共享 采购要懂生产计划,供应链(SCM)管理 针对核心物料进行供应商生产计划库存监控 仓库库存管理 库存 采购周期 在途量扣除 采购周期 本次订货量
ppt课件 16
第三室:材料计划和存量控制
库存管理九大指标
• 库存周转率
• • • • • • • • 及时发货率 帐物相符率 月均库存量 年均库存量 库存物料数量准确率 库存物料质量完好率 仓库面积容积利用率 运输质量保证率
ppt课件
17
第四室:生产计划控制管理
一般控制流程
市场部销售 供货信息 生产计 划 物料需 求计划 协商交 货期 产出计 划
ppt课件
15
第三室:材料计划和存量控制
如何加快库存周转
1、库存周转率的概念 在已定的周期中(生产周期为6个月者,就以6个月计 ,销售业着如进货周期为1个月,以1个月计)原材料 或商品经过了若干次周转的比率。 2、库存周转率的计算 库存周转率=出库数量(销售量)/库存数量 库存周转率(金额)=该期出库金额(销售额)/该期 平均库存金额 库存计划=次月销售计划/库存周转
ppt课件
6
第一室:物料控制/生产计划/销售计划管理
(三)单品型:
必须从产品设计开始,包含设计期限在内的全部门的计划。 由于这时的计划只针对设计,资财准备、加工等部门,因而交货 期很粗略,通常称其为“订单大日程计划” 由于交货期是规定了的,设计部门必须按大日程完成设计, 任何部门发生拖延,最坏的结局就是交货误期。 通常,接受个别订单生产时,延误交货期的最大原因是设计 图出图不及时。
仓库呆料处理制度
帐物一致相关制度
ppt课件 9
第三室:材料计划和存量控制
采购必备的条件和依据
1、条件
• • • • • • • • • • 根据不同的物料、供应商使用不同的采购方式 信息共享 采购要懂生产计划,供应链(SCM)管理 针对核心物料进行供应商生产计划库存监控 仓库库存管理 库存 采购周期 在途量扣除 采购周期 本次订货量
ppt课件 16
第三室:材料计划和存量控制
库存管理九大指标
• 库存周转率
• • • • • • • • 及时发货率 帐物相符率 月均库存量 年均库存量 库存物料数量准确率 库存物料质量完好率 仓库面积容积利用率 运输质量保证率
ppt课件
17
第四室:生产计划控制管理
一般控制流程
市场部销售 供货信息 生产计 划 物料需 求计划 协商交 货期 产出计 划
ppt课件
15
第三室:材料计划和存量控制
如何加快库存周转
1、库存周转率的概念 在已定的周期中(生产周期为6个月者,就以6个月计 ,销售业着如进货周期为1个月,以1个月计)原材料 或商品经过了若干次周转的比率。 2、库存周转率的计算 库存周转率=出库数量(销售量)/库存数量 库存周转率(金额)=该期出库金额(销售额)/该期 平均库存金额 库存计划=次月销售计划/库存周转
ppt课件
6
第一室:物料控制/生产计划/销售计划管理
(三)单品型:
必须从产品设计开始,包含设计期限在内的全部门的计划。 由于这时的计划只针对设计,资财准备、加工等部门,因而交货 期很粗略,通常称其为“订单大日程计划” 由于交货期是规定了的,设计部门必须按大日程完成设计, 任何部门发生拖延,最坏的结局就是交货误期。 通常,接受个别订单生产时,延误交货期的最大原因是设计 图出图不及时。
- 1、下载文档前请自行甄别文档内容的完整性,平台不提供额外的编辑、内容补充、找答案等附加服务。
- 2、"仅部分预览"的文档,不可在线预览部分如存在完整性等问题,可反馈申请退款(可完整预览的文档不适用该条件!)。
- 3、如文档侵犯您的权益,请联系客服反馈,我们会尽快为您处理(人工客服工作时间:9:00-18:30)。
销售预测准确率 销售计划准确率 主生产计划准确率 缺料计划准确率 采购计划准确率 余力计划准确率 作业计划准确率
演练
请设计一张六大计划准确率考核表格。
2、信息同步
目视化 一小时通话
3、协调解决
问题解决在发生之前 FMEA运用
第二讲:主生产计划如何精确 的分解为作业计划
1、余力、工艺掌握 2、分解方法 3、排程原则 4、管理项目
判断:A>B余力管理/A<B外包管理
5、生产线平衡率
作业所需时间
(秒)
22
尖峰时间20秒
20
18
损失时间
16
(斜线部份)
14
求 E%?
12
10
L% ?
8
6
损失时间 ?
4
2
0 1
2
3
4
5
制 程(每制程为乙名作业员)
平衡安排生产
一周工作5天,一天8小时,A、B、C、D
4台设备,专人操作,一周运营成本6000元。
1、实时余力掌握
现有的ERP是如何掌握余力的?
余力
月份工作天
制程名称 (机器代号)
产能 工时 A
负荷
余力
比率 %
工时
100
B
比 率 工时 %
B/A
C
比率 %
1.工时单位:人天、人时、人分 工时:(a)产能(A)=每日可用工时×工作天数 (b)负荷(B)=标准工时×计划数量 (C)余力(C)=产能(A)-负荷(B)
我们应当如何考虑?
客户要求交货日期 生产时间:标准工时、生产综合效率、
实际产能、 余力、 平衡率 采购时间:下采购单时间、供应商制备
时间、交运时间、验收时间 交运客户时间
1、标准工时
2、实际产能
工序工时效率计算:
某工序出勤体制为两班两倒,每班出勤8小时,一天出勤16小时.2008年6月 12日,该工序工时运用的实际情况如下:
该工序有效运转率为: 有效运转率=807÷960×100%=84.06% 该工序主要生产u,v两大系列产品.2007年6月生产26天,机型
切换52次,机型切换消耗的总工时为1254分钟. 则该工序切换率为: 切换率=1254÷(16×26×60) ×100%=5.02% 切换效率为:切换效率=1- 5.02%=94.98%
生产计划与物料控制 (PMC)
课程大纲
第一讲:销售计划、主生产计划、采购计划同步 第二讲:主生产计划如何精确的分解为作业计划 第三讲:采购计划如何编制、跟踪 第四讲:生产进度管制 第五讲:如何进行插单管理 第六讲:减少库存,加速周转
第一讲:销售计划、主生产计 划、采购计划同步
1、计划编制流程 2、如何识别同步 3、如何实现同步
P产品
Q产品
90元 100个
100元 50个
D原材料5元
D工序15分钟 C工序10分钟
C工序5分钟 B工序15分钟
D工序20分钟 C工序10分钟 B工序15分钟
A工序15分钟 A原材料20元
B原材料20元
A工序15分钟 C原材料20元
3、如何实现同步
1、同步管理项目 2、信息同步 3、协调解决
1、同步管理项目
品 名 J480 D673 A385 B458 C550
数量 1 2 3 4
6000 5300 4700 3000 1800
567891111111 0123456
×100
③故
障
④ 准备、交换、调整
⑤速 度 低 下
性能运转率=
标准 时间 ×加工数量 实际时间×加工数量
×100
⑥ 空 转、 暂 停 ⑦ 修 理·再 加 工
加工数量 - ⑦⑧
良品率 =
数量
⑧废 弃
生产综合效率 = 时间运转率×性能运转率×良品率
×100
生产综合效率的计算
计算题:
三班倒的企业,每班一天工作8小时,其中生产计 划休息时间20分,设备故障停止20分,准备作业花去20 分,调整10分,一个班可以生产400个产品,标准为半 分钟生产一个,因为设备性能下降实际每个产品平均 需要0 .8分钟,不良率为2%。
综合有效运转率= 84.06% × 94.98%=79.84%
工序生产能力
如前面工序的标准工时为:U系列12.6秒/件,V系列14.0秒/件, 则该工序生产能力为:
(1)单时生产能力:
单时U系列生产能力=3600×84%÷12.6=240件/小时 单时V系列生产能力=3600×84%÷14.0=216件/小时 (2)单日生产能力: 单日U系列单型号生产能力=240×16=3840件/日 单日U系列生产能力=240×16×(1-U系列切换率) 单日V系列单型号生产能力=216×16=3456件/日 单日V系列生产能力=216×16×(1-U系列切换率) (3)单月生产能力: 6月U占60%,V占40% 月度生产能力=(3840×26×60%+3456×26×40%) ×(1-5%)=91054件/月
1. 比率:1产能以100%表示 2负荷以B/A表示 3余力以(100-B/A)%表示
判断:A>B余力管理/A<B外包管理
演练
请设计一张余力报表。
2、分解方法
主生产计划 月计划 周计划 日计划
生产排程常见的月生产日程表
序 品名 批号 批量 累计完成 未完成量 计划 交期
号
量
量
生产排程常见的月生产进度计划
销售预测
1、计划编制流程 销售计划
产品设计图
1SOP(标准途程) 2SIP(标准检验程序) 3BOM(标准料表) 4ST(标准时间表) 5LT(前置时间) 6LOT SIZE(批量)
基准日程
订单 主生产计划
缺料计划 采购计划
交期
数量
物料到位 人机负荷
产能负荷调整
日程编订
进度跟催
2、如何识别同步
现有的ERP是如何设计来实现同步的?
3、生产综合效率
设备
日历时间 (年 月 日) (A )
管
负荷时间 (B)
理 浪
费
停
运转时间 ( C )
止 浪
费
性 实 际(D) 能 运转时间 浪
费
不 价 值(E) 良 运转时间 浪
费
8大浪费
生 产 综 合 效 率的 计 算
①计 划 保 全 ②生 产 调 整
时间运转率=
日.历 时间-①②③④ 日.历 时间
4、产能负荷分析表(范例)
月份工作天
制程名称 (机器代号)
产能 工时 A
负荷
余力
比率 %
工时
100
B
比 率 工时 %
Hale Waihona Puke B/AC比率 %
1.工时单位:人天、人时、人分 工时:(a)产能(A)=每日可用工时×工作天数 (b)负荷(B)=标准工时×计划数量 (C)余力(C)=产能(A)-负荷(B)
1. 比率:1产能以100%表示 2负荷以B/A表示 3余力以(100-B/A)%表示
演练
请设计一张六大计划准确率考核表格。
2、信息同步
目视化 一小时通话
3、协调解决
问题解决在发生之前 FMEA运用
第二讲:主生产计划如何精确 的分解为作业计划
1、余力、工艺掌握 2、分解方法 3、排程原则 4、管理项目
判断:A>B余力管理/A<B外包管理
5、生产线平衡率
作业所需时间
(秒)
22
尖峰时间20秒
20
18
损失时间
16
(斜线部份)
14
求 E%?
12
10
L% ?
8
6
损失时间 ?
4
2
0 1
2
3
4
5
制 程(每制程为乙名作业员)
平衡安排生产
一周工作5天,一天8小时,A、B、C、D
4台设备,专人操作,一周运营成本6000元。
1、实时余力掌握
现有的ERP是如何掌握余力的?
余力
月份工作天
制程名称 (机器代号)
产能 工时 A
负荷
余力
比率 %
工时
100
B
比 率 工时 %
B/A
C
比率 %
1.工时单位:人天、人时、人分 工时:(a)产能(A)=每日可用工时×工作天数 (b)负荷(B)=标准工时×计划数量 (C)余力(C)=产能(A)-负荷(B)
我们应当如何考虑?
客户要求交货日期 生产时间:标准工时、生产综合效率、
实际产能、 余力、 平衡率 采购时间:下采购单时间、供应商制备
时间、交运时间、验收时间 交运客户时间
1、标准工时
2、实际产能
工序工时效率计算:
某工序出勤体制为两班两倒,每班出勤8小时,一天出勤16小时.2008年6月 12日,该工序工时运用的实际情况如下:
该工序有效运转率为: 有效运转率=807÷960×100%=84.06% 该工序主要生产u,v两大系列产品.2007年6月生产26天,机型
切换52次,机型切换消耗的总工时为1254分钟. 则该工序切换率为: 切换率=1254÷(16×26×60) ×100%=5.02% 切换效率为:切换效率=1- 5.02%=94.98%
生产计划与物料控制 (PMC)
课程大纲
第一讲:销售计划、主生产计划、采购计划同步 第二讲:主生产计划如何精确的分解为作业计划 第三讲:采购计划如何编制、跟踪 第四讲:生产进度管制 第五讲:如何进行插单管理 第六讲:减少库存,加速周转
第一讲:销售计划、主生产计 划、采购计划同步
1、计划编制流程 2、如何识别同步 3、如何实现同步
P产品
Q产品
90元 100个
100元 50个
D原材料5元
D工序15分钟 C工序10分钟
C工序5分钟 B工序15分钟
D工序20分钟 C工序10分钟 B工序15分钟
A工序15分钟 A原材料20元
B原材料20元
A工序15分钟 C原材料20元
3、如何实现同步
1、同步管理项目 2、信息同步 3、协调解决
1、同步管理项目
品 名 J480 D673 A385 B458 C550
数量 1 2 3 4
6000 5300 4700 3000 1800
567891111111 0123456
×100
③故
障
④ 准备、交换、调整
⑤速 度 低 下
性能运转率=
标准 时间 ×加工数量 实际时间×加工数量
×100
⑥ 空 转、 暂 停 ⑦ 修 理·再 加 工
加工数量 - ⑦⑧
良品率 =
数量
⑧废 弃
生产综合效率 = 时间运转率×性能运转率×良品率
×100
生产综合效率的计算
计算题:
三班倒的企业,每班一天工作8小时,其中生产计 划休息时间20分,设备故障停止20分,准备作业花去20 分,调整10分,一个班可以生产400个产品,标准为半 分钟生产一个,因为设备性能下降实际每个产品平均 需要0 .8分钟,不良率为2%。
综合有效运转率= 84.06% × 94.98%=79.84%
工序生产能力
如前面工序的标准工时为:U系列12.6秒/件,V系列14.0秒/件, 则该工序生产能力为:
(1)单时生产能力:
单时U系列生产能力=3600×84%÷12.6=240件/小时 单时V系列生产能力=3600×84%÷14.0=216件/小时 (2)单日生产能力: 单日U系列单型号生产能力=240×16=3840件/日 单日U系列生产能力=240×16×(1-U系列切换率) 单日V系列单型号生产能力=216×16=3456件/日 单日V系列生产能力=216×16×(1-U系列切换率) (3)单月生产能力: 6月U占60%,V占40% 月度生产能力=(3840×26×60%+3456×26×40%) ×(1-5%)=91054件/月
1. 比率:1产能以100%表示 2负荷以B/A表示 3余力以(100-B/A)%表示
判断:A>B余力管理/A<B外包管理
演练
请设计一张余力报表。
2、分解方法
主生产计划 月计划 周计划 日计划
生产排程常见的月生产日程表
序 品名 批号 批量 累计完成 未完成量 计划 交期
号
量
量
生产排程常见的月生产进度计划
销售预测
1、计划编制流程 销售计划
产品设计图
1SOP(标准途程) 2SIP(标准检验程序) 3BOM(标准料表) 4ST(标准时间表) 5LT(前置时间) 6LOT SIZE(批量)
基准日程
订单 主生产计划
缺料计划 采购计划
交期
数量
物料到位 人机负荷
产能负荷调整
日程编订
进度跟催
2、如何识别同步
现有的ERP是如何设计来实现同步的?
3、生产综合效率
设备
日历时间 (年 月 日) (A )
管
负荷时间 (B)
理 浪
费
停
运转时间 ( C )
止 浪
费
性 实 际(D) 能 运转时间 浪
费
不 价 值(E) 良 运转时间 浪
费
8大浪费
生 产 综 合 效 率的 计 算
①计 划 保 全 ②生 产 调 整
时间运转率=
日.历 时间-①②③④ 日.历 时间
4、产能负荷分析表(范例)
月份工作天
制程名称 (机器代号)
产能 工时 A
负荷
余力
比率 %
工时
100
B
比 率 工时 %
Hale Waihona Puke B/AC比率 %
1.工时单位:人天、人时、人分 工时:(a)产能(A)=每日可用工时×工作天数 (b)负荷(B)=标准工时×计划数量 (C)余力(C)=产能(A)-负荷(B)
1. 比率:1产能以100%表示 2负荷以B/A表示 3余力以(100-B/A)%表示