新型的水泥联合粉磨工艺系统方案
联合粉磨系统介绍2010-3s-1

天津水泥工业设计研究院有限公司
9
V-
S联EP合AR粉AT磨O 系统流程B
R
天津水泥工业设计研究院有限公司
10
振兴联合粉磨系统
辊压机 TRP140/140
600t/h
V选 TPS160 160000m3/h
旋风筒 6DC1525 180000 m3/h
循环风机 M4-73-15 No.18F
180000 m3/h
26~28 18~22
200~240
200~300
~4000
~4000
天津水泥工业设计研究院有限公司
2
◆ 辊压机发展概况
1977年:Clausthal大学Schonert教授申请专利 1985年:第一台样机投产
●规格不断大型化,对粒度的适应性提高; ●耐磨性能不断改善,使用寿命延长; ●液压系统可靠性提高,故障率降低; ●系统不断改进,辊压机作用得到充分体现。
L/D 利弊
>1
① 边缘效应小; ② 辊宽方向受力好; ③ 辊子偏斜量大,但目前
从液压系统的调节上 已经解决。
<1
① 边缘效应大; ② 辊宽方向受力
差; ③ 辊子偏斜量小
。
天津水泥工业设计研究院有限公司
4
压力与辊压机的出力:
PR=2Sinβ×D×B ×V ×PT
(PR-需用功率, PT-挤压力)
辊压机的规格系数:
设计
实际
86
84
5
5
9
4
7
170
170
3300
3480
30.2
29.3
7.6
7.1
17.6
16.8
12
●系统运行指标先进,是比较满意的辊压机系统之一; ●半成品≥1800cm2/g,R80mm=20~30%, R45mm=50%,全部入磨影响粉磨效率; ●系统比较复杂,通风电耗较高;
水泥联合粉磨系统主机工艺选型计算

则 H厂 V型选 粉 机后循 环 风机 风量 为 :
Q= 0 x 6 3 1 + 6 ) . 2 1 8 m /。 1 0 ( 2 x . 10 / 5 0 8 O 2 4= 6 h
当采用 4 直径球磨 时 , .n 2l 直径修正系数A取 :
表 1 ; 为 粉磨 系 统修 正 系数 ; 为 不 同粉磨 细 度修 ) 正 系数 , (/0 0 ,为成 品 细度 。 A=s3 0 )。S
表 1 磨机 直径修 正系数A
c 水泥粉磨系统进料量 ,h 一 t; / 斗式 提 升机选 型 备用 系数 , 此处 选 1 。 . 2
Pr c s a c l t n o o b n d c me t i y t m n e lc o y e o e sc l u a i f m i e e n l s se a d t t t p o c m l h e
Z a gS ia,a u , i a fn (i0 aIt n t nl nin r g o,t. aj g, a n ,in s, 1 】0 h n hc i oY n L Y ne gSn m e a oa E gn ei . d( n n)N mi J gu 2 0 ) Y nr i nC L N i g a l
表 2 不同磨 径所需每米功率
磨径( )f 外径 D/ m
中4 3 中44) .( .
式中 : Q一 联合粉磨系统的台时产量 ,h t; / z 一 辊 压 机 表 面 功 指 数 ,wh(・r ・ , 。 k /1Cl g ) r
水 泥 联 合 粉 磨 系 统 的 初 取 00 4 00 5k / .0~ . Wh 0
I
主 袋 收 尘 器
水泥粉磨系统优化设计方案

水泥粉磨系统优化设计方案水泥粉磨系统是水泥生产过程中非常重要的环节,它直接影响着水泥产品的质量和生产效率。
对水泥粉磨系统进行优化设计,提高其工作效率和产品质量,对水泥生产企业来说具有重要意义。
本文将针对水泥粉磨系统进行优化设计方案的制定,进行详细的介绍和分析。
一、水泥粉磨系统的工作原理在水泥生产过程中,水泥生产企业主要采用球磨机或立磨机进行水泥熟料的粉磨工作。
而水泥磨矿机在磨矿过程中,主要是通过水泥磨机的回转部件和磨辊、磨盘、磨头的自转,传动装置使磨辊向外侧翻滚,并等速自转,使熟料通过分散装置均匀的进入磨辊和磨盘之间,形成前磨层。
在冲击,挤压和摩擦作用下,将熟料磨矿成水泥熟料粉,颗粒逐渐减小,颗粒细化,缩小了分散液相间的界面,提高了水泥的水化速度。
水泥粉磨系统的主要工作原理可以总结为:通过磨机的机械作用,将水泥熟料磨成水泥产品所需的细度和颗粒大小,从而保证水泥的质量和水泥产品的性能。
传统的水泥粉磨系统存在一些问题,主要表现在以下几个方面:1. 能耗较高:传统水泥粉磨系统的能耗较高,不利于节能减排。
2. 生产效率低:传统水泥粉磨系统的生产效率较低,无法满足企业的生产需求。
3. 产品质量不稳定:由于水泥粉磨系统的工艺不够完善,导致水泥产品的质量不稳定,影响产品的市场竞争力。
4. 设备磨损大:传统水泥粉磨系统的设备磨损较大,需要经常进行维护和更换。
针对以上问题,需要对水泥粉磨系统进行优化设计,从而提高其工作效率和产品质量,降低能耗和设备磨损,实现水泥生产的可持续发展。
1. 提高设备的自动化水平通过提高水泥粉磨系统设备的自动化水平,实现设备的智能化控制和运行,从而减少人为操作的干扰,提高生产效率和产品质量。
可以采用先进的自动化控制系统,实现设备的远程监控和智能化运行,实时监测设备的运行状态和生产数据,做到及时发现问题并进行处理,提高设备的可靠性和稳定性。
2. 优化磨矿工艺通过优化水泥粉磨系统的磨矿工艺,实现水泥熟料的高效粉磨,提高产品的细度和颗粒大小,从而提高产品的质量和性能。
水泥联合粉磨系统的工艺改进

图 1 水 泥磨 改 造前 工艺 布 置 图
为了确保金属等硬物不至于进入辊压机系统而 对辊面造成损坏 , 系统设置了金属除出与旁路系统。
一
般 的金属 可 由安装 在 喂料 胶带 输送 机 上 的 自卸 式
电磁 除铁器 直接 排 除 ; 于仍 未被 排 出 的金属 , 经 对 再
金属探测仪 、气动三通阀组成的辊压机旁路系统直 接喂入水泥磨机 , 从而实现保护辊压机 的目的。 调试 期 间磨机 喂料 不久 就 出现 一仓 饱磨 ,磨 机
机 的 圈流水 泥粉磨 系 统 。设 计 入磨 粒 度< m, 2 m 台时
料能力及通风能力大大降低。 严重时被迫停机 , 必须 人工 进磨 清理 。直接影 响 了水 泥粉 磨 系统 的调 试及 运行 工作 。分 析 由以下原 因引起 : () 1 部分粗筛板加工尺寸误差过大导致 间隙偏 大, 同时排列布置不合理 , 主要表现在四块粗筛板之 间缝隙未错开造成局部间隙过大 ,从而使部分钢球
求j 程 7 6 工
图 水磨造工布 图 2 泥改后 艺置
一
3 — 7
维普资讯
通风极 差 , 头正 压甚 至吐 料 ; 磨 而二 仓磨 音 高呈 空磨
状态 , 同时引起磨尾滑履瓦温度过高的现象。 有时采 取止料摇磨措施 , 一仓饱磨情况会有所好转 , 但只要 恢复喂料 , 同样 的现象很快再次出现 。 停机进磨检查 发现磨 内一 、 二仓之间隔仓板的粗筛板 、 细筛板篦缝 大部分被排列有序 的熟料颗粒 、 钢球等堵塞 , 、 粗 细 筛板之问也被钢球堵满 , 情况相当严重 , 使磨机的过
进入 粗 、 细筛 板之 间 : ()由于 入 磨 熟 料 颗 粒 过 大 , 仓 破 碎 粉磨 能 2 一
水泥生料粉磨系统安装方案
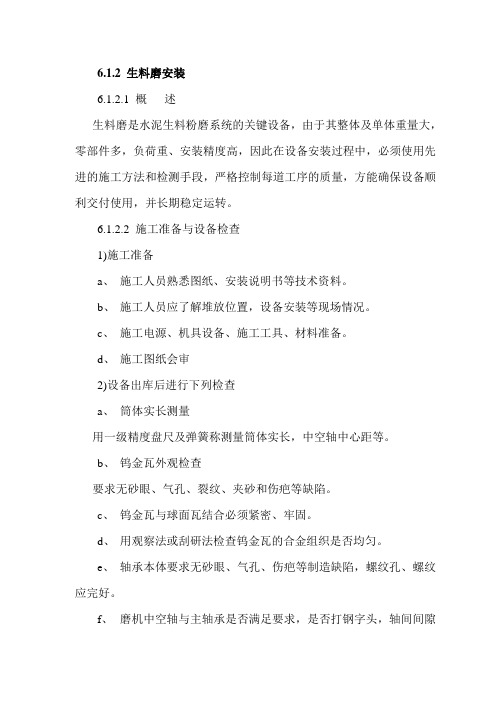
6.1.2 生料磨安装6.1.2.1 概述生料磨是水泥生料粉磨系统的关键设备,由于其整体及单体重量大,零部件多,负荷重、安装精度高,因此在设备安装过程中,必须使用先进的施工方法和检测手段,严格控制每道工序的质量,方能确保设备顺利交付使用,并长期稳定运转。
6.1.2.2 施工准备与设备检查1)施工准备a、施工人员熟悉图纸、安装说明书等技术资料。
b、施工人员应了解堆放位置,设备安装等现场情况。
c、施工电源、机具设备、施工工具、材料准备。
d、施工图纸会审2)设备出库后进行下列检查a、筒体实长测量用一级精度盘尺及弹簧称测量筒体实长,中空轴中心距等。
b、钨金瓦外观检查要求无砂眼、气孔、裂纹、夹砂和伤疤等缺陷。
c、钨金瓦与球面瓦结合必须紧密、牢固。
d、用观察法或刮研法检查钨金瓦的合金组织是否均匀。
e、轴承本体要求无砂眼、气孔、伤疤等制造缺陷,螺纹孔、螺纹应完好。
f、磨机中空轴与主轴承是否满足要求,是否打钢字头,轴间间隙量是否达到设计要求。
g、轴颈表面有无砂眼,毛刺、腐蚀,碰伤等缺陷。
h、钢底座的厚度等几何尺寸和主瓦座标高的测定。
以上各项检查应做好详细记录,若有与图纸要求不符等问题,应及时通报监理单位和业主,并积极配合处理。
6.1.2.3 基础验收1)土建完成±0.000平面工程及磨机基础后,可将生料磨基础先行交付安装。
2)基础外形尺寸、中心线、标高、地脚螺栓孔相互位置尺寸,应符合施工图纸和验收规程的要求,其允许偏差如下:基础外形尺寸:±3mm基础标高:±3mm中心线间的距离:±1mm地脚孔中心位置:±10mm地脚孔深度:±20mm地脚孔垂直度:±1000mm6.1.2.4 标板埋设与基础划线1) 标板埋设:a、每条主要中心线至少埋设两块中心标板,每个基础设置一个基准标高点;b、中心标板采用100×50×10钢板制作;基准标高点采用φ25园钢制作,表面制作;2)基础划线:a、根据土建或业主给定的基准点和基准线,按施工图的要求,用高精度经纬仪、盘尺、角尺、钢板尺、弹簧称、地规、墨斗等一次划出磨机、减速器、电机的纵横中心线,并以对角线复核放线的精度;b、基础划线应符合下列要求:同一中心线各中心标板的中心点,允许偏差0.5mm;两基础上横向中心线距离偏差不得大于±1mm;基准点标高允许偏差0.5mm;c、划线完毕后,在预埋的标板上,打上洋冲眼。
日产6000吨新型干法水泥熟料生产线水泥粉磨车间工艺设计

日产6000吨新型干法水泥熟料生产线水泥粉磨车间工艺设计一、前置工序1. 原材料处理2. 破碎、混合及研磨3. 烧成及制粉二、水泥生产工艺1. 干法水泥熟料生产线工艺流程1.1 原材料预处理1.2 破碎、混合及研磨1.3 熟料生产2. 水泥粉磨车间工艺流程2.1 水泥粉磨系统概述2.2 储存与输送系统概述2.3 粉磨系统概述三、干法水泥熟料生产线工艺流程1. 原材料预处理原材料预处理主要包括:原材料的贮存、输送和称量。
原材料主要有:石灰岩、黏土、铁粉等。
这些原材料需经过称量后,按比例混合,形成均匀的混合物。
2. 破碎、混合及研磨经过预处理的原材料进入制备系统,进行初步的粉碎和混合。
然后将初步制备好的物料送入球磨机中进行细磨,形成粉末状的原料。
3. 熟料生产将细磨后的原料送入旋转窑中进行烧成,形成熟料。
在旋转窑中,原料经过高温下的化学反应,形成新的化合物。
经过冷却后,得到烧成好的熟料。
四、水泥粉磨车间工艺流程1. 水泥粉磨系统概述水泥粉磨系统主要由一台立式辊压机、一台球磨机、一台高效分级器和相关输送设备组成。
立式辊压机用于初步粉碎和干式分类,球磨机用于细碎和混合。
2. 储存与输送系统概述水泥生产完成后,需要进行储存和输送。
储存设备包括水泥仓、自动配料仓等。
输送设备包括皮带输送机、斗式提升机等。
3. 粉磨系统概述经过储存和输送后的水泥进入球磨机中进行细碎和混合。
然后通过高效分级器进行分类,并将符合要求的产品送入储存设备中。
五、工艺优点1. 干法水泥熟料生产线采用先进的工艺,能够提高生产效率和产品质量。
2. 水泥粉磨车间采用立式辊压机和球磨机相结合的工艺,能够提高水泥的细度和均匀度。
3. 储存与输送系统采用自动化控制,能够提高生产效率和产品质量。
六、总结以上是日产6000吨新型干法水泥熟料生产线水泥粉磨车间的工艺设计。
该工艺采用先进的设备和自动化控制技术,能够提高生产效率和产品质量,满足市场需求。
辊压机联合粉磨工艺系统分析

辊压机联合粉磨工艺系统分析辊压机联合粉磨(或半终粉磨)工艺系统,其技术核心在本质上属于“分段粉磨”。
目前,国内水泥制成工序广泛应用由辊压机+打散分级机(动态分级设备)或V型选粉机(静态分级设备)+管磨机开路(或配用高效选粉机组成双闭路)组成的联合粉磨工艺系统(或由辊压机+V型选粉机(静态分级设备)+高效选粉机+管磨机组成的半终粉磨工艺系统),在实际运行过程中,由于各线生产工艺流程及设备配置、物料粉磨特性、水份等方面因素不尽相同,导致系统产量、质量及粉磨电耗等技术经济指标也参差不齐,本文拟对水泥联合粉磨单闭路(管磨机为开路)及双闭路系统(或半终粉磨系统)中各段常出现的工艺技术与设备故障模式进行探讨分析,并提出了相应的解决办法,仅供粉磨工程技术人员在日常工作中参考,文章中谬误之处恳望予以批评指正:一、辊压机系统故障模式:辊压机挤压效果差故障原因1:1. 被挤压物料中的细粉过多,辊压机运行辊缝小,工作压力低影响分析:辊压机作为高压料床(流动料床)粉磨设备,其最大特点是挤压力高(>150Mpa),粉磨效率高,是管磨机的3-4倍,预处理物料通过量大,能够与分级和选粉设备配置用于生料终粉磨系统。
但由于产品粒度分布窄、颗粒形貌不合理及凝结时间过快、标准稠度需水量大与混凝土外加剂相容性差等工作性能参数方面的原因,国内水泥制备工艺未采用辊压机终粉磨系统,辊压机只在水泥联合粉磨系统中承担半终粉磨(预粉磨)的任务,经施以双辊之间的高压力挤压后的物料,其内部结构产生大量的晶格裂纹及微观缺陷、<2.0mm及以下颗粒与<80um细粉含量增多(颗粒裂纹与粒度效应),分级后的入磨物料粉磨功指数显著下降(15-25%),易磨性明显改善;因后续管磨机一仓破碎功能被移至磨前,相当于延长了管磨机细磨仓,从而大幅度提高了系统产量,降低粉磨电耗。
但辊压机作业过程中对入机物料粒度及均匀性非常敏感,粒状料挤压效果好、粉状料挤压效果差,即有“挤粗不挤细”的料床粉磨特性;当入机物料中细粉料量多时会造成辊压机实际运行辊缝小,主电机出力少,工作压力低,若不及时调整,则挤压效果会变差、系统电耗增加。
联合粉磨系统技术交流

联合粉磨系统技术交流联合粉磨系统是一种重要的水泥生产技术,它通过多种磨机共同工作,使原始材料尽可能地细磨,提高水泥品质以及生产效率。
在联合粉磨系统技术中,各工序之间需要进行紧密配合和有效沟通,以确保系统的正常运行和优化效果。
首先,联合粉磨系统需要确保各磨机之间的平衡。
不同的磨机在磨矿物颗粒过程中具有不同的特点和磨矿能力。
为了避免某一台磨机因为工作负荷过重而导致故障,需要精确地控制各磨机之间的进料量和出料量,以保持系统的平衡状态。
其次,联合粉磨系统需要进行材料的合理混合和流通。
原始材料在不同工序中需要经过多次磨矿和混合,以提高水泥的品质和性能。
因此,磨机之间的材料流动需要根据生产工艺和产品要求进行精确控制,确保原材料在系统内的均匀分布和合理流通,从而提高磨矿效率和水泥品质。
另外,联合粉磨系统需要进行精确的控制和调节。
通过对磨机的磨矿参数、进出料口的调节以及系统的温度、压力、流量等参数的监控和调整,可以实现对整个系统的精确控制和优化。
同时,通过对系统运行过程中的数据进行实时监测和分析,可以及时发现问题并采取措施,以确保系统的稳定运行和优化效果。
在实际的生产中,联合粉磨系统技术交流是非常重要的。
不同的生产企业和磨机供应商之间需要进行经验、技术和数据的交流,共同解决生产过程中的问题和挑战。
通过经验交流和技术合作,可以不断改进和提高联合粉磨系统的性能和效益。
总之,联合粉磨系统技术交流对于水泥生产企业和磨机供应商来说具有重要意义。
只有通过有效地沟通和合作,才能共同解决生产过程中的问题,优化系统性能,提高产品质量和生产效率。
联合粉磨系统技术交流是水泥生产企业和磨机供应商之间的一种重要合作方式,通过互相学习、分享经验和技术,共同提高联合粉磨系统的效率和性能。
在技术交流中,需要重视以下几个方面。
首先,技术交流应该着重于磨机的性能和参数。
不同的磨机具有不同的特点和磨矿能力,因此在技术交流中,要重点关注各磨机的磨矿效率、能耗、产能等参数,并根据实际生产情况进行比较和分析。
- 1、下载文档前请自行甄别文档内容的完整性,平台不提供额外的编辑、内容补充、找答案等附加服务。
- 2、"仅部分预览"的文档,不可在线预览部分如存在完整性等问题,可反馈申请退款(可完整预览的文档不适用该条件!)。
- 3、如文档侵犯您的权益,请联系客服反馈,我们会尽快为您处理(人工客服工作时间:9:00-18:30)。
新型的水泥联合粉磨工艺系统
本文介绍的辊压机半终粉磨系统属于优化的联合粉磨系统,开发目的是提高系统运转率和粉磨效率,解决循环风机的磨损问题,从已投产系统的运行情况看,我们实现了这一目的。
当然,因为推出时间较短,实际投产的新系统还不多,我们期待更多的半终粉磨系统尽快投入运行,通过实践进一步促进辊压机粉磨系统技术的进步和发展。
联合粉磨和半终粉磨二者的区别在于联合粉磨系统中的半成品直接进入到球磨机再粉磨,而半终粉磨系统中的半成品先经过分选,细粉入成品,粗粉入球磨。
联合粉磨和半终粉磨的优点是辊压机负担的粉磨任务多,单位吸收功率多,半成品比较细,故增产节能幅度较大;出辊压机的物料粒度得到控制,球磨机配球容易,粉磨效率有保证。
(有的文献中对联合粉磨和半终粉磨也没有严格的区分,统称为联合粉磨,泛指出辊压机的物料经过分选的各种系统。
)表1对通过式预粉磨和联合粉磨系统的具体情况进行了比较。
表1 通过式预粉磨和联合粉磨系统比较
2)联合粉磨系统情况分析
典型的联合粉磨系统如图1所示,新料与出辊压机的物料一起经提升机喂入V型选粉机进行分选,粗料落入小仓再进辊压机挤压,细料被气体带入旋风收尘器被收集作为半成品喂入球磨机再细磨。
V型选粉机属于静态气力粗分选设备,具有打散和分级功能,无运动部件,抗磨性能好,选粉空气由循环风机提供。
图1 联合粉磨系统流程
振兴水泥二线(2400t/d)配套的水泥粉磨系统是投产最早的国产辊压机联合粉磨系统,水泥工业设计研究院提供了辊压机(TRP140/140、2×800kW)和球磨机(φ4.2×13、3150kW)等主机设备,并承担工程设计。
2004年投产至今,运行情况良好,与一线φ3.8×13圈流磨系统相比,单位水泥节电近7.0kWh/t,按年产水泥90万吨计,年节电达630万度,节电费用300多万元。
图2 循环风机的磨损
辊压机挤压后的物料颗粒多呈不规则体状,棱角多,对风管、旋风收尘器、循环风机具有很强的磨蚀性,特别是循环风机,一旦发生磨损,风量降低,选粉效率下降,从而影响系统产量,这在很大程度上影响了系统的运转率。
另外,旋风收尘器收集的半成品比表面积在1500cm2/g以上,<80μm的颗粒占70%~80%,<45μm的颗粒占50%~60%,将这种半成品喂入球磨机,势必影响粉磨效率。
因此,消除循环风机的磨损,提高系统的运转率,并进一步提高粉磨效率,是辊压机联合粉磨系统必须解决的问题。
3、半终粉磨系统的开发研究
联合粉磨系统中,物料的分选是个关键问题,如同圈流球磨系统的物料分选一样,将影响整个系统产能的发挥和运转的稳定性。
V型选粉机非常适合辊压机物料的粗分级,但是风量风速是前提,即要求供风系统稳定。
循环风机的磨损主要由气体中的含尘引起,而根据旋风收尘器的工作原理可知,其收尘效率只有90%左右,如果要彻底消除风机的磨损,只有最大限度的降低进入风机气体的含尘浓度。
为此,取消旋风收尘器,设计一台组合式高效选粉机对出V选的物料进行二次分选,含有合格成品的气体进入袋收尘器处理,最后由系统风机排出;同时,出球磨机的物料从上部喂入同一台高效选粉机分选,形成如图3的半终粉磨系统。
入球磨机的物料是选粉机的粗粉部分,这样同时解决了大量成品再入磨影响粉磨效率的问题。
图3 辊压机半终粉磨系统
但是,该系统有两个问题需要认真研究:一是选粉机的可靠性,二是产品质量问题。
⑴TESu型高效涡流选粉机
根据半终粉磨系统的特点,对配套的动态选粉机提出了多方面的
要求。
首先是结构方面,出球磨机的物料从顶部用斜槽喂入,出V选的物料靠气力提升从底部喂入;其次是要克服传统选粉机的缺陷,做到高效、节能,水泥产品性能好;再者是耐磨性能好,运转率高,因为出辊压机物料磨蚀性大,容易对设备产生磨损损坏。
图4 TESu型高效涡流选粉机
针对新系统的特点,在院选粉机技术的基础上,并吸收国外最新选粉机的优点,对其关键结构进行技术创新,从提高选粉机的运转率、选粉效率和选粉精度,降低空气阻力,节省动力消耗的角度出发,开发了半终粉磨系统专用的TESu型高效涡流式选粉机。
粉磨后的待选物料由上部的四个喂料管(进料口)喂入选粉机,通过转子撒料盘、缓冲板充分分散,而后落入选粉区。
选粉气流来自V选的含尘气体,通过下壳体进风口从底部进入
选粉机,冲击折流锥的部分粗粉落入下料管,经初分级的上升气体通过导流装置进入选粉区,颗粒在转子的离心力和空气的携带力作用下得到分选。
在选粉机由垂直叶片组成的笼式转子回转时,使得转子外压差在整个选粉区上下维持一个定值,从而使气流稳定均匀,为精确选粉创造了良好的条件。
物料每一个颗粒自上而下得到了多次重复分选的机会,最后落入下料锥管(下料灰斗)的粗颗粒经出料口排出机外返回球磨机。
细粉由转子中心与气流一起由大弯管排出,经收尘器收集作为成品。
该选粉机关键部件如分级叶片、翼型导流板和缓冲板均采用UP复合式耐磨钢板制作,壳体的蜗壳衬、转子主轴套的外壁和出风管采用互压式防脱落耐磨瓷片,确保了设备的抗磨损性能。
⑵产品性能研究
众所周知,辊压机产生的细粉特点是微细粉含量少、颗粒级配窄、球形度小,水泥需水量大。
半终粉磨系统的最终产品也有一部分直接来自辊压机,对需水量等性能有无不良影响?为此我们也进行了专项研究,研究方法是从辊压机联合粉磨系统采取半成品试样和出磨试样,然后分别分离出合格成品,再按不同比例配置水泥,测定各项性能。
试验结果如下:
a) 随着VS细样掺量的增加,试样的比表面积降低,但特征粒径却减小。
试样的均匀性系数n增加,说明颗粒分布变窄。
b) SO3含量随着VS细样掺量的增加而增加,系统平衡以后应为定值。
c) 需水量随着VS细样掺量的增加而增加,掺量25%左右时变化不大,超过50%时增加明显。
d) 3d、7d抗压强度在25%的VS细样掺量时最好,28d抗压强度在50%以上的VS细样掺量时最好。
3d抗折强度在25%的VS细样掺量时最好,7d抗折强度在50%的VS细样掺量时最好,28d抗折强度则在75%以上的VS细样掺量时最好。
c) VS细样掺量在25~50%之间时,只对3d抗压强度产生负面影响,但影响很小,在50%围以,对其它强度都产生促进作用。
e) VS半成品中<45μm的含量为50%~60%,考虑到45μm的选粉效率,进入成品中由辊压机直接挤压的细粉量<40%,即1/3左右。
f) 结论:与联合粉磨系统产品性能相比,半终粉磨系统产品性能无不良表现。
4、应用效果
新的联合粉磨系统既半终粉磨系统是在传统联合粉磨系统的基础上,通过系统流程优化,采用新的技术装备,以提高系统运转率、降低单位产品电耗为宗旨而开发的节能粉磨系统。
一经推出即得到市场的高度认可,仅2007年到现在就销售40台套。
首套辊压机半终粉磨既亚泰集团水泥6#水泥磨系统于2007年8月成功投产,系统运行稳定,运转率高,运行指标达到了预期值,得到了业主的肯定。
φ1400×1100、2×800kW辊压机与φ4.2×13、3150kW球磨机配置的系统产量可以达到160t/h左右,电耗31 kwh/t•cement,现在该厂生产32.5水泥,产量190~200t/d, 电耗29 kwh/t•cement左右。
半终粉磨系统的主要特点可以归纳为以下几点:
⑴系统流程简化
将双闭路合二为一,即由一台系统风机给两台选粉机供风,减少了设备数量,流程得到简化,操作更加容易,关键设备是高效涡流选粉机。
⑵粉磨效率提高
出辊压机的半成品首先要经过高效选粉机分选,细粉进入到成品,粗粉再入磨,降低了球磨机的过粉磨现象,从而提高了粉磨效率。
⑶消除风机磨损
新系统取消旋风收尘器和循环风机,出V选的含有半成品的气体经高效选粉机、袋收尘器入系统风机,消除了辅机设备的磨损问题,提高了系统运转率。
⑷系统可调性好
球磨圈流操作,粉磨效率高,成品细度易于控制,适合生产多品种水泥;产品温度可以有效控制,避免石膏过度脱水,保证产品质量。
球磨机单独设置收尘系统,便于调节磨机风速。
系统风机至V选入口设置循环风管,便于调节系统温度,夏季或水分高时少循环风,以降低温度,避免结皮,冬季多循环风以提高系统温度,避免结露。
⑸系统流程可变
该系统可实现多种操作模式:常规的辊压机和球磨机圈流联合操作、球磨机单独圈流操作、辊压机单独圈流操作、辊压机圈流与球磨机开流联合操作,可适应不同状态的要求。
图5 联合粉磨系统TL-1流程
图6 联合粉磨系统TL-Ⅱ流程
图7 TL-2粉磨系统开流球磨方案。