航空发动机复杂结构零件加工技术探索
航空发动机钛合金筒体加工工艺研究
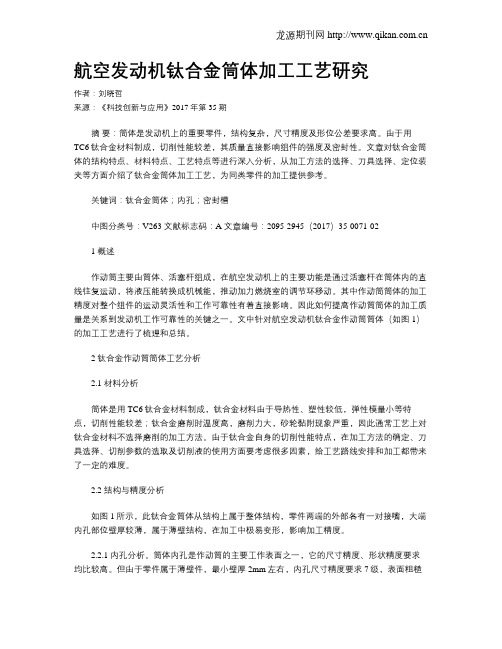
航空发动机钛合金筒体加工工艺研究作者:刘晓哲来源:《科技创新与应用》2017年第35期摘要:筒体是发动机上的重要零件,结构复杂,尺寸精度及形位公差要求高。
由于用TC6钛合金材料制成,切削性能较差,其质量直接影响组件的强度及密封性。
文章对钛合金筒体的结构特点、材料特点、工艺特点等进行深入分析,从加工方法的选择、刀具选择、定位装夹等方面介绍了钛合金筒体加工工艺,为同类零件的加工提供参考。
关键词:钛合金筒体;内孔;密封槽中图分类号:V263 文献标志码:A 文章编号:2095-2945(2017)35-0071-021 概述作动筒主要由筒体、活塞杆组成,在航空发动机上的主要功能是通过活塞杆在筒体内的直线往复运动,将液压能转换成机械能,推动加力燃烧室的调节环移动。
其中作动筒筒体的加工精度对整个组件的运动灵活性和工作可靠性有着直接影响。
因此如何提高作动筒筒体的加工质量是关系到发动机工作可靠性的关键之一。
文中针对航空发动机钛合金作动筒筒体(如图1)的加工工艺进行了梳理和总结。
2 钛合金作动筒筒体工艺分析2.1 材料分析筒体是用TC6钛合金材料制成,钛合金材料由于导热性、塑性较低,弹性模量小等特点,切削性能较差;钛合金磨削时温度高,磨削力大,砂轮黏附现象严重,因此通常工艺上对钛合金材料不选择磨削的加工方法。
由于钛合金自身的切削性能特点,在加工方法的确定、刀具选择、切削参数的选取及切削液的使用方面要考虑很多因素,给工艺路线安排和加工都带来了一定的难度。
2.2 结构与精度分析如图1所示,此钛合金筒体从结构上属于整体结构,零件两端的外部各有一对接嘴,大端内孔部位壁厚较薄,属于薄壁结构,在加工中极易变形,影响加工精度。
2.2.1 内孔分析。
筒体内孔是作动筒的主要工作表面之一,它的尺寸精度、形状精度要求均比较高。
但由于零件属于薄壁件,最小壁厚2mm左右,内孔尺寸精度要求7级,表面粗糙度要求Ra0.20μm,对基准的跳动要求为0.03mm;且零件外部带有接嘴(如图1),这种结构对加工时的定位装夹提出了更高的要求。
航空发动机涡轮叶片精密成型技术分析

航空发动机涡轮叶片精密成型技术分析摘要:航空发动机技术复杂且难以制造。
世界上只有几个国家可以完成航空发动机的设计和制造。
中国不断发展航空发动机的设计和制造,以提高自身的制造水平。
空心涡轮叶片是高性能航空发动机的主要部件之一,制造困难长期以来一直给中国的制造公司带来麻烦。
通过分析空心涡轮叶片的结构特性,分析和解释空心涡轮叶片的精密成型技术。
关键词:空心涡轮叶片;精密成型技术;精密铸造前言空心涡轮叶片是高性能航空发动机的关键组件,由于对精度的要求和制造困难,我们无法批量生产空心涡轮叶片。
为了提高空心涡轮叶片的制造合格率,我们将从叶片精密铸造的“形状控制”和“可控制性”两个方面出发分析空心涡轮叶片的精密铸造工艺,以提高叶片精密铸造的质量。
需要1空心涡轮叶片的精密铸造技术现代飞机发动机正朝着高推进力和低油耗的方向发展。
为了实现这一目标,当今世界上的主流方法是提高航空发动机涡轮的进气温度。
发动机涡轮的当前入口温度已经很高。
随着温度的不断升高,发动机涡轮叶片的温度达到1880℃±50℃,为了解决这个问题,目前的涡轮叶片主要用于复合膜冷却的单晶空心涡轮叶片(称为空心涡轮叶片)。
由于结构的复杂性和材料的特殊性,熔模铸造工艺主要用于制造空心涡轮叶片,但由于精度低,产量低,该工艺存在使空心涡轮叶片具有高性能的问题。
有。
通常,当今的空心涡轮叶片精密铸造的产率约为10%,其中约90%的废叶片的形状和尺寸偏差约为50%,而重结晶缺陷约占25%。
主要原因是铸造缺陷。
为了提高空心涡轮叶片的制造成品率,有必要解决“形状控制”和“铸造控制”两个问题:精密铸造后的尺寸精度和复合材料性能。
空心涡轮叶片的工艺复杂且难以制造:粗略的制造过程如下:首先,使用模芯来完成空心涡轮叶片精密铸造所需的陶瓷芯,并且陶瓷芯是空心的填充零件。
用来。
随后,使用蜡模工艺在芯的外层上制备涡轮叶片蜡模,然后通过烧结注射成型和其他工艺来制造空心涡轮叶片粗糙毛坯。
航空发动机机匣加工工艺研究

航空发动机机匣加工工艺研究摘要:随着我国综合国力的增强,同时也在促进国产发动机的性能逐渐朝着优良的方向不断发展。
近年来航空发动机的性能及设计结构在不断改进和提高,发动机机匣零件的材料、结构也发生了很大的变化。
本文就航空发动机机匣加工工艺展开探讨。
关键词:航空发动机;机匣;加工工艺1加工工艺特点机匣加工表面主要分为内、外两部分。
由于其外部需要连接到许多如电气、冷却、油路及管路等附件系统,导致其表面形状结构复杂,对机加要求比较高,尤其是对位置和尺寸精度要求较高;另外发动机机匣的内部主要是承载其压气机的涡轮叶片,包括动、静力叶片,这些都是其关键的动力输出部分,所以也对制造精度要求较高。
综上所述,机匣制造加工工艺的难点主要体现在材料切除率高、薄壁易变形、材料难切削和对刀具切削性能要求高等多个方面。
2.1轴数控铣削机匣型面的成形,国内通常是通过在多轴数控铣削设备上加工完成的。
数控机床的出现以及带来的巨大利益,引起世界各国科技界和工业界的普遍重视。
在航空机闸机械加工中,发展数控机床是当前我国机械制造业技术改造的必由之路,是未来工厂自动化的基础。
数控机床的大量使用,需要大批熟练掌握现代数控技术的人员。
数控技术的应用不但给传统制造业带来了革命性的变化,使制造业成为工业化的象征,而且随着数控技术的不断发展和应用领域的扩大,它对国计民生的一些重要行业的发展起着越来越重要的作用。
机匣零件外环形面共分二级,分布有二条环形凸缘,下部有1个纵向小凸缘,两个纵向凸缘对称分布。
由于机匣毛坯是自锻件,加工余量很大,且零件材料难切削,为了保证尺寸加工精度和表面加工质量,防止加工后零件变形。
其外型面加工分层、分块进行,采取合理的走刀路径,采用对称的切削加工余量。
分几次走刀加工到最后尺寸的方法,以减少加工后的变形。
因此,该机匣加工划分三个主要阶段并附加特征工序热处理,以去除材料内应力,防止零件变形。
2.2磨粒流加工磨粒流加工就是用流体作为载体,将具有实际切削技术性能的末了悬浮于其中,形成一个流体磨料,依靠末了相对于被加工材料表面的流动提供能量进行加工分析的一种技术。
基于3D打印技术的复杂零件制造工艺研究

基于3D打印技术的复杂零件制造工艺研究近年来,随着3D打印技术的飞速发展,其在汽车、航空航天、医疗等领域的应用越来越广泛,并在一定程度上改变了传统的制造模式。
特别是在制造复杂零件方面,3D打印技术发挥着越来越重要的作用。
1. 3D打印技术在复杂零件制造中的应用复杂零件是指结构复杂、加工难度大的零部件。
传统制造方式需要借助多种加工工具,而且还需要与多个零件进行组合,其加工成本高、周期长,同时还存在着质量难以保证的问题。
而3D打印技术能够直接将设计文件转化为实体模型,无需进行拼接、组装等环节,可以大幅减少制造周期和成本。
同时,由于3D打印技术使用的是粉末烧结、激光烧结等非传统加工方式,可以实现更高的精度和更复杂的形态。
在航空航天领域,3D打印技术已经开始应用到发动机零件、燃油喷嘴等复杂零件的制造中。
在医疗领域,3D打印技术可以用于制造高精度假体,以及可塑性强的新型支架等复杂医疗器械。
2. 3D打印技术在复杂零件制造中的挑战虽然3D打印技术在复杂零件制造中具有很多优势,但是还存在一些挑战。
首先,3D打印技术目前还无法制造大型零件,而且制造周期往往比传统制造方式长。
其次,粉末烧结、激光烧结等加工方式会对材料性能造成一定影响,需要在材料选择和加工参数设置上做出相应调整。
此外,3D打印技术目前的材料范围还比较狭窄,无法满足所有复杂零件的制造需求。
3. 3D打印技术在复杂零件制造中的发展趋势尽管3D打印技术在复杂零件制造中还存在一些挑战,但是随着技术的不断发展,这些问题也将得到解决。
首先,未来的3D打印设备将应用到更多领域,包括大型零件制造。
从更广泛意义上看,随着人工智能、机器学习等技术的应用,3D打印技术还将更加智能化、可自适应调整。
其次,未来3D打印材料的种类也将更加丰富,覆盖越来越多的行业。
4. 基于3D打印技术的复杂零件制造工艺研究如何利用3D打印技术实现更好的复杂零件制造效果,是当前制造行业所关注的问题。
航空发动机机匣加工工艺探讨
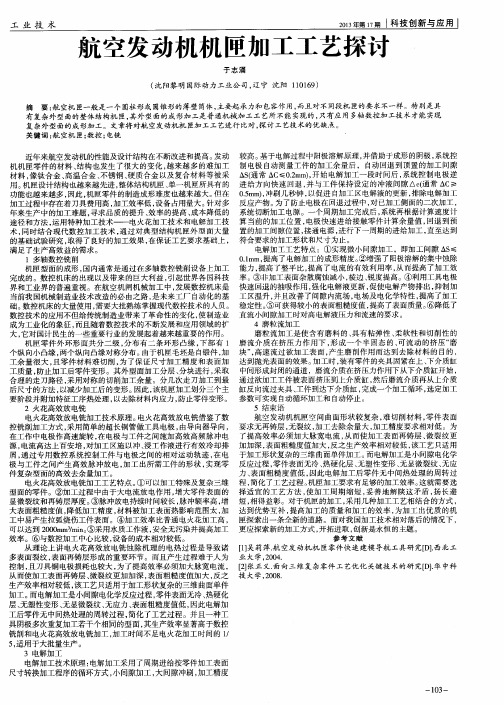
航 空发动机机 匣加工工艺探讨
于 志 涌
( 沈 阳黎 明 国 际动 力 工 业公 司 , 辽宁 沈 阳 1 1 0 1 6 9 )
摘 要: 航空机 匣一般是一 个圆柱形或 圆锥 形的薄壁筒体 , 主要起承力和包容作用, 而且对不同段机 匣的要求不一样。特别是具 有复 杂外型面的整体结构机 匣, 其外型面的成形加工是普通机械加工工艺所不能 实现 的, 只有应用 多轴数控加工技术才能实现 复杂外型面的成形加工。文章将对航空发动机机 匣加工工艺进行比对 , 探讨工艺技术的优缺点。
关键 词 : 航 空机 匣; 数控 ; 电铣
近年来航空发动机 的性能及设计结构在不断改进和提高 。 发动 机 机 匣零 件 的材 料 、 结 构 也发 生 了很 大 的变 化 , 越来 越 多 的难 加 工 材料 , 像钛合金 、 高温合金 、 不锈钢 、 硬质合金以及复合材料等被采 用。 机匣设计结构也越来越先进 , 整体结构机匣、 单一机匣所具有的 功能也越来越多 , 因此 , 机匣零件的制造成形难度也越来越大 。 但在 加工过程中存在着刀具费用高 , 加工效率低, 设备 占用量大。 针对多 年来生产 中的加工难题 , 寻求品质的提升 、 效率的提高 、 成本降低的 途径和方法 , 运用 特 种 加 工技 术 —— 电火 花 加 工 技术 和 电解 加 工技 术, 同时结合现代数控加工技术 , 通过对典型结构机 匣外 型面大量 的基础试 验研究 , 取得了 良好 的加工效果 , 在保证工艺要求基础上 , 满 足 了生 产高 效 益 的需 求 。 1多轴 数 控铣 削 机匣型面 的成形 , 国内通常是通 过在多轴数控铣 削设备上加工 完 成 的 。数 控 机床 的 出现 以及 带来 的 巨大 利 益 , 引起 世 界 各 国科技 界 和 工业 界 的普 遍 重视 。在航 空机 闸机 械 加 工 中 , 发展 数 控 机 床是 当前 我 国机 械 制 造业 技 术 改 造 的必 由之 路 , 是 未 来工 厂 自动 化 的基 础。 数控机床 的大量使用 , 需要大批熟练掌握现代数控技术的人员 。 数控技术 的应用不但给传统制造业带来 了革命性 的变化 , 使制造业 成 为 工业 化 的象 征 , 而 且 随着 数 控技 术 的不 断 发 展 和应 用 领 域 的扩 大, 它 对 国 计 民生 的一 些重 要 行业 的发 展起 着 越 来越 重 要 的作 用 。 机匣零件外环形面共分二级 , 分布有二条环形 凸缘 , 下部有 1 个 纵 向小 凸缘 , 两 个 纵 向 凸缘 对称 分 布 。 由 于机 匣 毛坯 是 自锻件 , 加 工余量很大 , 且零件材料难切削 , 为了保证 尺寸加工精度 和表 面加 工质量 , 防 止加 工 后 零件 变 形 。其外 型面 加 工 分 层 、 分 块进 行 , 采取 合理的走刀路径 , 采用对称 的切削加工余量 。分几次走刀加工到最 后尺寸的方法 , 以减少加工后的变形 。 因此 , 该机匣加工划分三个主 要 阶段 并 附加 特征 工 序 热 处理 , 以去 除 材料 内应 力 , 防止 零 件 变形 。
航空发动机精锻叶片数字化数控加工技术
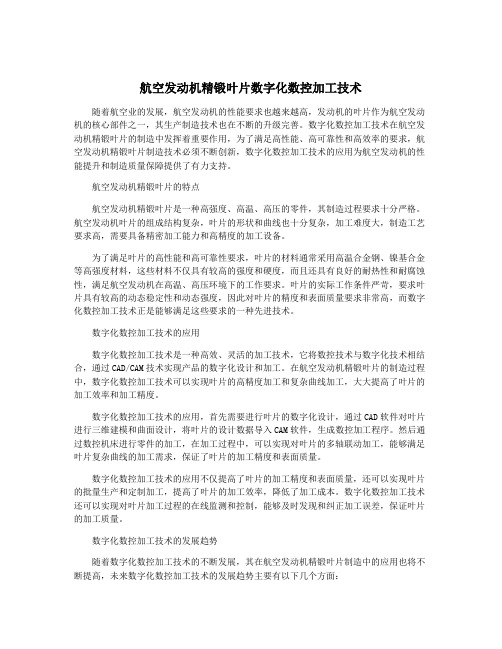
航空发动机精锻叶片数字化数控加工技术随着航空业的发展,航空发动机的性能要求也越来越高,发动机的叶片作为航空发动机的核心部件之一,其生产制造技术也在不断的升级完善。
数字化数控加工技术在航空发动机精锻叶片的制造中发挥着重要作用,为了满足高性能、高可靠性和高效率的要求,航空发动机精锻叶片制造技术必须不断创新,数字化数控加工技术的应用为航空发动机的性能提升和制造质量保障提供了有力支持。
航空发动机精锻叶片的特点航空发动机精锻叶片是一种高强度、高温、高压的零件,其制造过程要求十分严格。
航空发动机叶片的组成结构复杂,叶片的形状和曲线也十分复杂,加工难度大,制造工艺要求高,需要具备精密加工能力和高精度的加工设备。
为了满足叶片的高性能和高可靠性要求,叶片的材料通常采用高温合金钢、镍基合金等高强度材料,这些材料不仅具有较高的强度和硬度,而且还具有良好的耐热性和耐腐蚀性,满足航空发动机在高温、高压环境下的工作要求。
叶片的实际工作条件严苛,要求叶片具有较高的动态稳定性和动态强度,因此对叶片的精度和表面质量要求非常高,而数字化数控加工技术正是能够满足这些要求的一种先进技术。
数字化数控加工技术的应用数字化数控加工技术是一种高效、灵活的加工技术,它将数控技术与数字化技术相结合,通过CAD/CAM技术实现产品的数字化设计和加工。
在航空发动机精锻叶片的制造过程中,数字化数控加工技术可以实现叶片的高精度加工和复杂曲线加工,大大提高了叶片的加工效率和加工精度。
数字化数控加工技术的应用,首先需要进行叶片的数字化设计,通过CAD软件对叶片进行三维建模和曲面设计,将叶片的设计数据导入CAM软件,生成数控加工程序。
然后通过数控机床进行零件的加工,在加工过程中,可以实现对叶片的多轴联动加工,能够满足叶片复杂曲线的加工需求,保证了叶片的加工精度和表面质量。
数字化数控加工技术的应用不仅提高了叶片的加工精度和表面质量,还可以实现叶片的批量生产和定制加工,提高了叶片的加工效率,降低了加工成本。
航空发动机涡轮叶片精密成形技术分析
航空发动机涡轮叶片精密成形技术分析航空发动机作为飞机的动力系统,发挥着至关重要的作用。
而发动机的性能优劣直接影响着飞机的飞行性能和安全性。
在航空发动机中,涡轮叶片是发动机中最关键的部件之一,涡轮叶片的制作工艺与精度直接决定了发动机的性能。
涡轮叶片的精密成形技术显得尤为重要。
涡轮叶片是航空发动机中的一个重要零部件,它在发动机中扮演着承受高温高速气流的任务。
涡轮叶片需要具有极高的强度和耐热性。
涡轮叶片的表面粗糙度、气动性能也对发动机的性能有着直接的影响。
在涡轮叶片的制作工艺中,精密成形技术是至关重要的一环。
精密成形技术是一种应用于金属材料制造加工的高新技术,它包括了压铸、注塑、锻造、精密锻造等多种工艺。
而在航空发动机涡轮叶片的制作中,常用的精密成形技术主要有精密铸造和精密锻造两种。
下面将从这两种技术进行详细的分析。
一、精密铸造技术精密铸造技术是将金属材料通过在低温状态下的液态状态注入模具中,利用模具的结构将熔融金属冷却后形成所需形状的一种成形技术。
精密铸造技术制造的零件表面光洁度高,尺寸精度高,重量轻,成本低。
精密铸造技术在航空发动机涡轮叶片的制作中应用广泛。
在精密铸造技术中,铸造模具的结构设计和制造对于涡轮叶片的成型至关重要。
一方面,铸造模具的结构设计需要考虑到叶片的复杂形状和内部空腔,保证叶片的内部结构完整性;铸造模具的制造需要具备高精度加工和表面处理技术,以确保叶片的表面粗糙度和尺寸精度。
精密铸造技术制造的涡轮叶片表面光洁度高,可以减小叶片表面的阻力,提高叶片的气动性能;精密铸造技术还能够制造出形状复杂的内部空腔结构,提高叶片的强度和耐热性。
精密铸造技术在航空发动机涡轮叶片制作中有着重要的应用价值。
在不断发展的航空发动机领域,涡轮叶片的制作技术也在不断地进行创新与提升。
未来,随着材料工艺技术的不断进步,精密成形技术在涡轮叶片制作中将会有更加广泛和深入的应用,为航空发动机的性能提升和安全保障提供更加可靠的技术支持。
航空发动机涡轮叶片精密成形技术分析
航空发动机涡轮叶片精密成形技术分析【摘要】航空发动机涡轮叶片是航空发动机中至关重要的部件,对发动机的性能和效率起着关键作用。
涡轮叶片精密成形技术是一项关键技术,经历了多年的发展历程,逐步完善并应用于实际生产中。
本文从涡轮叶片的重要性入手,阐述了涡轮叶片精密成形技术的发展历程及关键步骤,探讨了该技术在航空领域的应用,并展望了未来的发展趋势。
通过本文的研究,有助于更深入地了解航空发动机涡轮叶片精密成形技术的重要性和发展现状,为相关领域的研究和应用提供参考和借鉴。
【关键词】航空发动机、涡轮叶片、精密成形技术、研究背景、研究意义、发展历程、关键步骤、应用、发展趋势、未来展望、总结1. 引言1.1 研究背景航空发动机涡轮叶片是航空发动机中的重要部件,直接影响着发动机的性能和效率。
随着航空业的发展和需求的提高,对于发动机的要求也越来越高,涡轮叶片的精密成形技术显得尤为重要。
在过去的几十年里,涡轮叶片的制造技术已经取得了长足的进步,包括材料的优化和加工工艺的改进。
随着飞行速度的提高和环保要求的增加,传统的涡轮叶片制造技术已经难以满足对高性能和高精度的要求。
研究涡轮叶片精密成形技术成为当前航空发动机领域的热点之一。
通过精密成形技术,可以实现涡轮叶片的高精度、高效率的制造,提高发动机的性能和可靠性。
涡轮叶片精密成形技术还可以减少材料浪费和能耗,降低制造成本,符合航空工业的可持续发展要求。
深入研究航空发动机涡轮叶片精密成形技术的背景意义重大,能够为航空领域的技术进步和发展提供重要支持和保障。
1.2 研究意义航空发动机涡轮叶片精密成形技术的研究意义在于提高航空发动机的性能和效率,进一步推动航空工业的发展。
随着航空业的快速发展,对涡轮叶片精密成形技术的要求也越来越高。
研究该技术能够提高航空发动机的性能和可靠性,减少能源消耗和碳排放,从而符合节能减排的国际趋势。
涡轮叶片是航空发动机的关键部件之一,其质量和制造工艺直接影响整个发动机的工作效率和安全性。
航空发动机加工难在哪?到底需要怎样的机床工具?
航空发动机加工难在哪?到底需要怎样的机床工具?航空发动机是飞机的心脏,是决定飞机性能的重要因素之一。
发动机中盘、轴、鼓筒、轴颈等零件均是发动机的核心转动部件和关键件,在高温、高压、高转速的恶劣环境下工作。
这类零件材料大多采用高温合金、粉末高温合金、钛合金等难加工材料制造,尺寸精度要求高,技术条件严格,对零件表面质量、表面完整性要求高,其加工质量的高低直接影响到发动机的使用寿命和安全可靠性。
近年来,随着航空发动机技术的不断进步和发展,这些关键部件的加工技术有了大幅度的提升,从传统的加工方式、过多依赖操作者的经验和水平完成加工,转向车铣复合加工、全程序无干预数控加工、各类边缘自动成型加工和自动光整加工等自动化、集成化、精准化及抗疲劳制造的方向推进和发展。
航空发动机关键部件加工技术的进步对提高航空发动机的可靠性,在全寿命使用周期内安全可靠的工作起到了至关重要的作用。
今天金属加工小编为金粉们介绍几个航空关键部件加工的典型案例。
1航空发动机制造对机床工具需求航空制造业对零件加工精度和效率日益提高的需求不断推动机床技术的发展,是机床产品创新的源源动力。
高速高精度加工中心、复合加工和多轴联动数控机床的出现,都与客户需求密切相关。
3 ~5轴加工中心、数控车床加工中心、各种磨削设备、各种精锻设备、各种铸造设备、特种电加工设备、复合加工中心(车铣、铣车)、叶片加工中心及磨削中心、特种电加工设备、激光加工及强化设备和零件表面处理设备是航空制造中必需的设备。
(1)盘类零件加工设备的基本要求。
数控立车:在工作台直径、定位精度、重复定位精度、工作台转速和工作台承重等方面应与所加工零件相适应。
具有自动换刀功能,刀库容量足够大;控制系统,具备刀具轨迹图形显示功能;具备USB 端口、DNC网络接收数据端口;配置高压内冷,机载自动对刀功能、机载工件测量功能、温度自动补偿功能;机床具有足够的刚性和可靠性。
(2)机匣加工设备的基本要求。
航空发动机零部件精密制造技术
航空发动机零部件精密制造技术作者:贾丽郝军涛杜改梅来源:《科技创新与应用》2018年第30期摘要:航空发动机关键零部件的精密制造技术一直是我国高性能航空发动机研制的瓶颈。
文章深入分析了航空发动机关键零部件的典型制造技术,对精密制坯、高效切削、抗疲劳制造、特种加工以及复合材料构件加工技术进行了总结,并给出了其发展方向。
关键词:航空发动机;精密制坯;高效切削;抗疲劳制造中图分类号:V262.3 文献标志码:A 文章编号:2095-2945(2018)30-0157-04Abstract: The precision manufacturing technology of the key components of aero-engine has been the bottleneck of the development of high-performance aero-engine in our country. This paper analyzes the typical manufacturing technology of the key components of aero-engine, summarizes the technologies of precision billet making, high-efficiency cutting, anti-fatigue manufacturing,special machining and processing of composite components, and gives the development direction of these technologies.Keywords: aero-engine; precision blanking; high efficiency cutting; anti-fatigue manufacturing航空制造集聚了大量的高新制造技术,其制造过程对制造设备、工艺、执业人员素质等要求极高;航空发动机被誉为飞机的“心脏”,是研发制造难度最大最顶级的现代工业造物,其制造技术的进步对航空制造乃至整个制造业的发展起着决定性的作用。
- 1、下载文档前请自行甄别文档内容的完整性,平台不提供额外的编辑、内容补充、找答案等附加服务。
- 2、"仅部分预览"的文档,不可在线预览部分如存在完整性等问题,可反馈申请退款(可完整预览的文档不适用该条件!)。
- 3、如文档侵犯您的权益,请联系客服反馈,我们会尽快为您处理(人工客服工作时间:9:00-18:30)。
航空发动机复杂结构零件加工技术探索
摘要:现阶段,科学技术的发展迅速,航空事业的发展也有了很大的改善。
航
空发动机作为飞机的动力装置,是飞机的心脏,其设计与制造技术对于航空工业
的发展起着关键性的作用,是体现一个国家科技水平、军事实力和综合国力的重
要标志之一。
航空发动机零件结构复杂、制造难度大、技术含量高,代表制造业
发展的方向,被称为制造业一颗璀璨的明珠。
数控加工技术和设备起源于满足航
空航天制造的需求,并在不断满足高、精、尖加工要求的过程中发展提高,成为
现代航空航天制造业的基础性关键技术。
国内外航空航天制造业一直是数控技术
与数控机床的最大用户,在航空航天制造企业中,数控机床制造企业的比例高达80%以上。
关键词:航空发动机;复杂结构;零件加工技术探索
引言
航空发动机零件的制造具有材料难加工、形状结构复杂、容易变形振动、加
工精度高等特点,代表着一个国家制造技术的实力和国防现代化的发展水平。
以
航空发动机叶片、叶轮、机匣、盘轴类零件为研究对象,分析了这些典型零部件
的材料和结构特性、加工工艺方法与特点、加工装备等,总结了航空发动机零件
加工对数控机床性能与功能的要求,并展望了航空发动机制造技术的发展趋势。
1加工复杂结构零件的机床工具特征
刀具在解决航空难加工材料复杂结构零件的加工中起着至关重要的作用。
先
进的航空产品要求航空零件具有更优异的性能、更低的成本和更高的环保性。
加
工工艺要求具有更快的加工速度、更高的可靠性、高重复精度和可再现性。
航空
钛合金、高温合金零件难切削的工件材料、复杂而薄壁的形状、高精度的尺寸和
表面粗糙度要求及大的金属去除量等特点,对刀具质量一致性提出了更高的要求。
现代高效精准加工要求刀具具有高精度、高耐磨性、高抗冲击性和高可靠性的特点,即具有高性能刀具的全部特征。
高质量的刀具方案明显标志是刀具结构形式、刀具材料与被加工零件的材料、结构相适应。
国外各著名数控机床制造商不遗余
力的开发高性能数控机床,进一步针对高动态响应、高精度和高刚性等展开研发。
高刚性以及高承载性能的线性导轨确保了全行程内光滑连续地移动,获得了工件
的高几何精度和表面质量,也保证了高加工效率。
机床的高刚性减小了加工系统
的振动,延长了刀具使用寿命。
高性能刀具涉及刀具材料、刀具涂层技术、刀具
结构设计与优化、刀具配套技术及刀具的应用等很多方面。
刀具结构的创新体现
在刀具结构的优化、切削负荷的合理分布、断屑槽型以及各种新型可转位刀片结构。
零件的精准加工对刀具的装夹提出了新的要求,它要求装夹精度高、径向圆
跳动小、夹持刚性好、结构紧凑且操作简单等。
2典型零件加工
2.1叶片加工
航空发动机叶片多采用钛合金、高温合金等材料,材料切削性能差,尺寸精
度要求严格,表面质量要求高。
叶片的加工部位主要包括叶身型面加工、叶片榫
头和榫齿加工、阻尼台加工、安装板及叶冠加工。
叶片加工的复杂性在于叶身部
分由复杂曲面组成,曲面按成形原理可分为直纹面和非直纹面,直纹面分为可展
和不可展。
对于可展直纹面,可以采用常规机械加工技术加工。
对于不可展直纹
面和自由曲面,则必须采用多轴数控机床加工,如五轴联动加工中心和五轴高速
龙门铣床。
叶根榫头采用拉床和缓进给强力磨床加工,缓进给强力磨床具有换砂
轮功能,配备滚轮修砂轮装置,在加工中还有在线测量、程序调整和自动补偿功能。
叶片机械加工以铣削和磨削为主,通常采用叶片高速铣等专用加工设备,由
专用叶片加工的计算机辅助设计(CAD)/计算机辅助制造(CAM)软件生成叶片
加工程序。
叶片的型面一般为大余量锻造,经数控加工后抛光而成。
切削加工主
要以锻造毛坯为基础,经过粗、半精、精加工等加工工序,以铣削方式将毛坯加
工至最终尺寸。
叶片加工一直是数控加工领域具有挑战性的课题,需要解决的问
题复杂繁多,如叶片造型、加工方式选择、刀具路径规划、叶片变形控制等。
根
据刀具与叶片的接触方式,叶片加工可以采用点铣法和侧铣法。
点铣法能较精确
加工叶片的设计型面,而且走刀方向与流线方向基本一致,有利于保护叶片的气
动性能,适用于自由曲面的叶片加工,不足之处是加工效率低下,刀具磨损严重,增加了产品的生产成本。
侧铣法避免刀具与工件接触区集中于一点,从而减缓刀
具磨损,显著改善了叶片的表面粗糙度,提高了叶片的加工效率。
现在国内应用
较多的是分片侧铣法,把叶片按加工特征和工艺要求分成若干片,用侧铣的方法
加工。
首先用刀具侧刃加工最外边的一片,然后不断地进退刀,加工相邻的分片。
理论上分片越多,叶片与刀具的接触线越短,加工精度就越高,但频繁的进退刀
和更换装夹方式又限制了加工效率。
2.2整体叶轮加工
其中,开式整体叶轮一次装夹可以完成所有数控铣削加工。
而对于闭式整体
叶轮而言,由于轮箍的存在,一般采用两次装夹、分区域铣削的加工方式。
整体
叶轮主要采用车削和铣削加工,特别是采用数控点铣和侧铣来加工叶片、轮毂及
叶根圆角等曲面。
整体叶轮也分为粗、半精和精加工3个阶段。
粗加工多选择平
底立铣刀或带有圆角的铣刀,刀具有效切削面积大,切除材料效率高。
精加工多
采用球头铣刀或高刚性的锥柄球头铣刀。
刀具尺寸根据叶轮几何尺寸进行选择:
粗加工尽量选择大直径刀具,以提高材料去除效率;精加工刀具球头半径则与曲
面曲率半径有关。
整体叶轮最容易发生干涉的部分是叶片与轮毂之间的叶根圆角,刀具球头半径应不大于叶根圆角曲面的最小曲率半径。
加工叶根圆角和加工叶片
部分可以选择不同直径的刀具,以提高效率。
精加工主要加工叶片、轮毂和叶根
圆角。
2.3盘轴类零件加工
航空发动机盘类零件包括高低压涡轮盘、高低压压气机盘。
盘类零件结构一
般由轮缘、腹板、轮毂、封严篦齿等组成,在轮缘上有安装叶片的榫槽,腹板上
有起平衡作用的小孔。
盘类零件通常采用高温合金、钛合金材料,材料难加工,
尺寸精度高,表面质量要求严格,壁薄易变形,对加工设备、加工刀具和测量工
具的要求较高。
航空发动机盘类零件机械加工包括车加工、钻镗、拉削和磨削等,主要加工部位包括内外圆、前后端面、腹板、篦齿和榫槽等。
一般选用整体锻造
或焊接毛坯,再经加工而成。
数控铣削加工灵活快速、可靠性高,因此发达国家
多采用五坐标加工中心铣削加工整体叶盘。
整体叶盘数控加工关键是叶片的数控
铣削。
轴类件主要指风扇轴、压气机轴、涡轮轴等,是航空发动机转子的重要组
成部分,对航空发动机的可靠性起着至关重要的作用。
轴类零件通常采用高性能
的耐热合金材料。
航空发动机轴类件工作时以每分钟上万转的高速旋转,负荷状
态复杂,工作时要求平稳、振动小,抗疲劳强度要求高,因此轴配合尺寸精度、
形位公差、表面质量和表面完整性也要求高。
轴类件加工包括内外表面车削、磨
削和深孔镗加工。
结语
航空发动机复杂结构零件的加工依赖于工艺方法的创新。
其制造水平直接决定了航空发动机的性能。
我们必须建立在可靠的研制基础之上,促进航空制造技术的不断提升。
参考文献:
[1]王聪梅.航空发动机典型零件机械加工[M].北京:航空工业出版社,2014.。