悬置支架的优化设计与疲劳寿命分析
某车型发动机悬置后支架优化设计和疲劳分析

a d b t r sr s it b t n,a d t e s b t u e tra i a ay e o p o e t e r t n l y a iu n e t t s d sr u i e e i o n h u si td ma e l s n l z d t r v h a i ai ;f t e t i o t g
分布 比较 均 匀的 轻量化 设 计方案 , 分析 更替 材料 的合 理性 ; 原结 构和优 化后 的 结构进行 疲 劳分 并 对
析 , 现原 结构 侧 筋根 部 疲 劳寿命 最短 , 结构 的 疲 劳 区域 较 小. 化后 的悬 置后 支架 不仅 解 决 开 发 新 优
裂 问题 , 而且在 降 重的前 提 下确保 材料 替换 的合 理性 并得 到性 能提 升. 关 键词 :发动 机 ;悬置后 支 架 ;结构设 计 ; 扑优 化 ; 量化设 计 ; 劳分析 拓 轻 疲 中图分 类 号 :U 6 . 3 ; B 1 . 4 4 1 1 T 15 2 文献标 志码 :B
Op i ia i n d sg n a i u n l ss o n i e r a tm z to e i n a d f tg e a a y i n e g n e r
m 0 Unt br c t 0■ a - m o l ・- a Re・ l ut - ● o _- bie ’
S na U Xito,CHEN i Zh
( e h ooyC n r C a gh u mo i a ua t y e i o n Mo r o , t. C a gh 1 1 9 C i ) T c n l e t , h n s aA t bl M n fc r ,B i t t . Ld , h n s a 0 2 , hn g e o e o qF o oC 4 a
汽车发动机悬置支架结构优化与可靠性研究
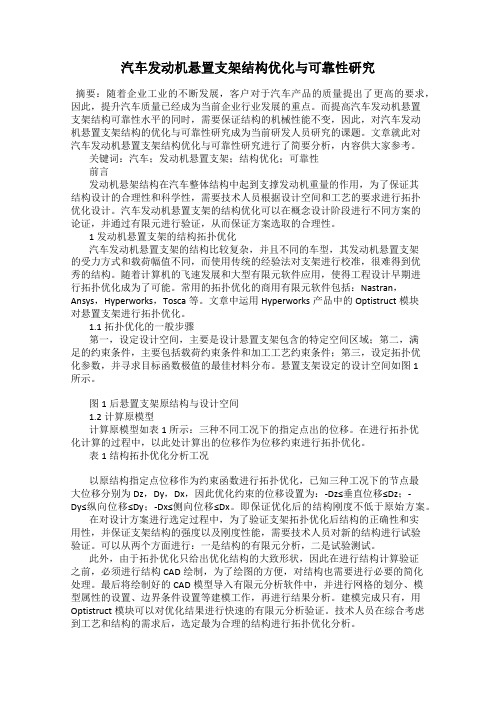
汽车发动机悬置支架结构优化与可靠性研究摘要:随着企业工业的不断发展,客户对于汽车产品的质量提出了更高的要求,因此,提升汽车质量已经成为当前企业行业发展的重点。
而提高汽车发动机悬置支架结构可靠性水平的同时,需要保证结构的机械性能不变,因此,对汽车发动机悬置支架结构的优化与可靠性研究成为当前研发人员研究的课题。
文章就此对汽车发动机悬置支架结构优化与可靠性研究进行了简要分析,内容供大家参考。
关键词:汽车;发动机悬置支架;结构优化;可靠性前言发动机悬架结构在汽车整体结构中起到支撑发动机重量的作用,为了保证其结构设计的合理性和科学性,需要技术人员根据设计空间和工艺的要求进行拓扑优化设计。
汽车发动机悬置支架的结构优化可以在概念设计阶段进行不同方案的论证,并通过有限元进行验证,从而保证方案选取的合理性。
1发动机悬置支架的结构拓扑优化汽车发动机悬置支架的结构比较复杂,并且不同的车型,其发动机悬置支架的受力方式和载荷幅值不同,而使用传统的经验法对支架进行校准,很难得到优秀的结构。
随着计算机的飞速发展和大型有限元软件应用,使得工程设计早期进行拓扑优化成为了可能。
常用的拓扑优化的商用有限元软件包括:Nastran,Ansys,Hyperworks,Tosca等。
文章中运用Hyperworks产品中的Optistruct模块对悬置支架进行拓扑优化。
1.1拓扑优化的一般步骤第一,设定设计空间,主要是设计悬置支架包含的特定空间区域;第二,满足的约束条件,主要包括载荷约束条件和加工工艺约束条件;第三,设定拓扑优化参数,并寻求目标函数极值的最佳材料分布。
悬置支架设定的设计空间如图1所示。
图1后悬置支架原结构与设计空间1.2计算原模型计算原模型如表1所示:三种不同工况下的指定点出的位移。
在进行拓扑优化计算的过程中,以此处计算出的位移作为位移约束进行拓扑优化。
表1结构拓扑优化分析工况以原结构指定点位移作为约束函数进行拓扑优化,已知三种工况下的节点最大位移分别为Dz,Dy,Dx,因此优化约束的位移设置为:-Dz≤垂直位移≤Dz;-Dy≤纵向位移≤Dy;-Dx≤侧向位移≤Dx。
重型卡车悬挂系统疲劳寿命评估

重型卡车悬挂系统疲劳寿命评估概述重型卡车扮演着现代物流运输的重要角色,它们需要经受各种恶劣路况和载重条件的考验。
悬挂系统是重型卡车的关键组成部分,它不仅要保证车辆稳定性和操控性,还要经受长期使用过程中带来的疲劳损伤。
因此,对重型卡车悬挂系统的疲劳寿命进行评估,对于保证车辆的安全性和可靠性至关重要。
疲劳损伤及其影响因素疲劳损伤是指在长期交变载荷作用下,材料或结构产生的逐渐积累和扩展的损伤现象。
重型卡车悬挂系统在运营过程中,由于路况的不平坦、载重的变化以及不同方向上的受力,会受到复杂而变化的载荷作用。
这些载荷作用导致悬挂系统的疲劳损伤,最终影响其使用寿命。
对于重型卡车悬挂系统的疲劳寿命评估,关键的影响因素主要包括载荷、材料和结构设计。
载荷是指悬挂系统在运营过程中所受到的外部载荷作用。
车辆在行驶过程中会经历不同的道路条件,如起伏的山路、崎岖的乡间小路等。
此外,载重的变化也会对悬挂系统产生影响。
更重的载物会增加悬挂系统的受力程度,从而导致疲劳损伤。
材料的选择对悬挂系统的疲劳寿命有着直接的影响。
优质的材料可以提高悬挂系统的强度和韧性,从而延长其使用寿命。
同时,考虑到重型卡车运营环境的实际情况,还要考虑材料的耐腐蚀性和抗磨损性能。
悬挂系统的结构设计也是影响其疲劳寿命的重要因素。
科学合理的结构设计可以减小疲劳裂纹的发生和扩展的可能性,从而延长悬挂系统的使用寿命。
在设计过程中,要充分考虑到路况和载重的变化,通过合适的几何尺寸和设计方法来减小疲劳损伤。
疲劳寿命评估方法为了评估重型卡车悬挂系统的疲劳寿命,目前主要采用试验和数值计算两种方法。
试验是一种直接获取悬挂系统疲劳性能的方法。
通过在实际工况下对悬挂系统进行加速寿命试验,可以模拟实际的载荷作用,进而评估其疲劳寿命。
试验方法需要考虑到载荷的合理选择、试验台设计和试验过程中监测的参数等因素。
试验方法具有可靠性高、直观性强的特点,但耗时较长且成本较高。
数值计算是一种通过计算机模拟来预测悬挂系统疲劳寿命的方法。
汽车动力总成悬置支架的优化设计

汽车科技第3期2007年5月汽车动力总成悬置支架的优化设计汽车动力总成悬置支架是动力总成悬置系统的安全件和功能件。
一方面,悬置支架连接发动机与车身(或车架、副车架),在汽车的各种行驶工况下,传递作用在动力总成上的一切力和力矩;另一方面,悬置支架的一阶固有频率对车内噪声的影响很大。
因此,在进行动力总成的悬置系统设计时,应对支架的强度和固有频率进行优化设计和试验验证。
在对悬置支架进行设计时,常常将其设计的较重,虽然提高了其强度,但浪费材料,并且由于设计得不合理,可能会导致其一阶固有频率太低,在发动机的工作转速范围内,使悬置支架产生共振,从而增大车内噪声;相反的情况是:支架设计得较薄,在汽车行驶或者进行试验时,造成支架断裂,严重影响汽车的安全性。
因此,悬置支架设计是动力总成悬置系统设计的重要内容之一。
本文以某轿车动力总成发动机悬置支架为例,阐述了悬置支架设计和试验时载荷工况的确定、悬置支架的拓扑优化与形状优化方法,并与试验结果进行了对比分析,证明了本文所述方法的有效性。
1存在的问题在开发某新款轿车时,新车型的动力总成与原车型不一样,因此要对其悬置系统进行重新设计。
按照新车型悬置系统的载荷工况,对原车型动力总成的发动机支架进行疲劳试验时,支架出现了开裂的现象,如图1所示。
因此,在新车型的悬置系统中,不可以借用原车型的支架,应重新进行支架的设计。
为了从理论上解释原支架在新车型的动力总成悬置系统中被破坏的原因,按照新车型的载荷工况,对原支架进行了应力分析。
计算结果表明,在新车型的悬置系统中,如果仍然借用原车型的动力总成的支架,在汽车的极限行驶工况下,原支架的应力会大于支架材料的屈服强度,从而导致支架的疲劳破坏。
图2为原支架的几何模型及有限元模型,该支架为铸钢件,具体材料参数如表1所示。
支架与发动机的连接面为固定约束,与悬置的连接点为加载点,作用在支架上的计算载荷如表2所示,共有四种载荷工况。
(a)几何模型(b)有限元模型图2原支架表1支架材料参数表2悬置支架的计算载荷工况N载荷工况x方向y方向z方向11874.8-564.27023.92-3693.1-1239.2-2485.83153.5-17093217.34-179.41721.7-1870材料杨氏模量/MPa泊松比密度/kg・m-3屈服强度/MPa抗拉强度/MPaZG270-5002.1E+050.37800270500赵艳青1,刘本元2,上官文斌1(1.华南理工大学汽车工程学院,广州510640;2.宁波拓减震系统有限公司,宁波315800)摘要:汽车动力总成悬置支架是动力总成悬置系统的安全件和功能件,它的结构强度影响汽车的安全性,其一阶固有频率对车内噪声有较大的影响。
某车型悬置支架模态优化设计

图1 3挡WOT车内前排噪声响度
在噪声彩图中发现车辆中高频共振情况严重,500~600 Hz 尤其严重(图2)。
悬置支架一般模态范围在500~1 000 Hz区间内,因此决定测量悬置车身端与动力总成端加速度,以判断悬置振
【参考文献】
[1]潘孝勇,柴国忠.悬置支架的优化设计与疲劳寿命分析.汽车工程,2007(4).
图3 左悬置方案图
图4 右悬置方案图
图5 3挡WOT更改前后噪声对比图
表3 支架方案模态对比表
原方案最终方案
原方案最终方案
方案一阶模态二阶模态左悬置车身端
原方案431 Hz 687 Hz 最终方案
705 Hz 1 066 Hz 653 Hz 820 Hz 4 结束语
针对某车型噪声比较大的现象,通过路径查找,明确原因为悬
置支架模态低。
利用有限元分析工具,提出支架优化方案,并利用拓扑优化对其进行减重。
通过整车验证,方案有效,该方法对解决支架模态低的问题具有参考意义。
重卡前翻转支架疲劳寿命的试验方法研究

北汽福田 技术研究院 中试厂 试验所 杨丽洁【摘要】载货汽车驾驶室悬置是决定汽车舒适性的重要装置。
随着高速货物运输的快速发展及对汽车舒适性能要求的提高,对载货汽车驾驶室悬置提出了愈来愈高的要求,同时也对其疲劳强度提出了更高的要求。
本文就重型载货汽车可翻式驾驶室全浮式悬置装置的疲劳寿命台架试验方法,从建立方案过程、方案实施过程、检验结果分析等方面进行综述。
叙词: 驾驶室悬置 舒适性 前翻转支架 台架试验 前言驾驶室悬置是影响汽车舒适性的重要装置。
随着对汽车乘座舒适性要求的提高,中、重型载货汽车采用“全浮式驾驶室悬置”,全浮式悬置是在半浮式悬置基础上的发展,驾驶室悬置得到了不断改进和完善。
在全浮式悬置结构中,前悬置和后悬置都采用了与汽车悬架结构相似的钢板弹簧或螺旋弹簧做为弹性元件,都配置筒式减振器,弹簧的变形量要比橡胶垫大许多倍。
采用全浮式悬置的汽车,在车架受扭变形时,弹簧的变形可抵消车架变形量的大部分,从而改善了驾驶室的受力状况,对驾驶室起到保护作用。
然而,前悬置连接在驾驶室和车架之间,受力情况非常复杂,正常行驶的情况下,主要受垂直载荷的作用,在转弯和颠簸路面时会受侧倾力矩的作用,在交变力的作用下如何确定前翻转支架的疲劳强度,本文就实现这一目的的台架试验方法的选定及实施,最终确定符合实际情况的试验方法进行论述。
筒式减振器 螺旋弹簧 翻转轴 螺旋弹簧 筒式减振器前悬置支座1 后悬置装置图1 全浮式悬置装置示意图1、 试验设备根据试验的实际情况,为保证试验过程的准确性和一致性,试验设备选用襄樊达安检测中心的申克多通道疲劳试验机,此试验机带360°可旋转激振头,可根据需要在任意方向加载。
2、受力分析汽车在直路行驶时,由于路面的不平导致驾驶室上下颠簸振动,反复变化的重力作用于驾驶室支座,螺旋弹簧及减振器又将此力传递于支架上,支架的受力有以下几种交变力组成: a 垂直向下或向上的压力或拉力;b 以螺旋弹簧支架或前悬置支座1为支点的向前或向后的扭转力;c 汽车在转弯时或左右轮处于不同平面时,支架的一侧受到拉力而另一侧受到压力;d 在任何情况下都会有扭杆弹簧的扭转力的作用。
重型载货汽车复合空气悬架导向臂支架优化设计

重型载货汽车复合空气悬架导向臂支架优化设计重型载货汽车的复合空气悬架导向臂支架是该车型悬架系统的重要组成部分,其负责连接车轮与车身,支撑车轮承受路面不平所产生的负荷。
本文旨在探究如何优化该部件的设计以提高汽车的悬架系统性能和安全性。
1.材料选用复合空气悬架导向臂支架的材料选择对其性能和寿命有着极大的影响。
合适的材料应该既具有足够的强度和刚度,又要满足重量控制的要求,降低车辆的整车重量,同时还要具有较高的耐腐蚀性。
通过对不同材料的比较,最终选择了钛合金材料作为导向臂支架的主体材料,该材料具有较高的比强度和比刚度,同时具有优异的耐腐蚀性,可以有效延长导向臂支架的寿命。
2.结构优化导向臂支架的结构优化是提高其性能和安全性的关键。
通过对导向臂支架的结构进行优化,可以提高其强度和刚度,并在保证结构轻量化的基础上满足导向臂支架在不同工作条件下的要求。
本文选用有限元分析方法对导向臂支架进行分析,通过模拟不同载荷条件下的应力分布情况,确定了导向臂支架的最优结构。
该结构采用了双肋型结构设计,肋骨沿着载荷传导方向布置以提高其刚度,同时减少其重量,具有较高的抗弯强度和扭转刚度。
3.加工工艺控制复合空气悬架导向臂支架的加工工艺控制也是关键的一环,其正确的加工和焊接过程可以保证导向臂支架的质量和性能。
在选择材料和结构设计之后,必须按照规范制定加工工艺流程和标准,以确保导向臂支架的制造过程稳定可靠。
本文采用了先进的焊接工艺,通过TIG焊接和PLS(激光点焊)技术,确保了导向臂支架焊接过程中的稳定性和焊缝质量的高度一致性。
综上所述,对于重型载货汽车的复合空气悬架导向臂支架,材料、结构和加工工艺都是优化设计的关键。
本文通过材料选择、结构优化和加工工艺控制,有效提高了导向臂支架的性能和寿命,同时减轻了车辆的整车重量,提升了汽车悬架系统的安全性和稳定性,为行业的进一步发展提供了重要的技术支持。
除了材料、结构和加工工艺的优化,复合空气悬架导向臂支架的设计还需要考虑其他方面,以确保其可靠性和安全性。
随机振动疲劳分析的某商用车悬挂件改进设计

随机振动疲劳分析的某商用车悬挂件改进设计随机振动疲劳分析的某商用车悬挂件改进设计摘要:本文通过对某商用车悬挂件进行随机振动疲劳分析,发现其存在易损零部件的问题。
为此,对其进行改进设计,采用新材料和复合结构的方式,提高了悬挂件整体的稳定性和耐久性。
经过实际测试和使用验证,改进后的悬挂件性能得到了显著提升。
关键词:随机振动疲劳、悬挂件、改进设计、材料、复合结构1.引言商用车的悬挂件是保障车辆正常行驶和提高乘坐舒适度的重要部件之一。
在长时间使用过程中,其中易损的零部件容易发生疲劳断裂,导致车辆出现故障。
因此,对悬挂件的随机振动疲劳进行分析,并进行改进设计,对提高商用车的可靠性和安全性具有重要意义。
2.分析对某商用车悬挂件进行随机振动疲劳分析,得到如下结论:(1)悬挂件整体刚度不够,容易发生弯曲和变形;(2)悬挂件易损零部件存在疲劳断裂的风险;(3)过度磨损和冲击会损坏悬挂件和密封件。
根据分析结果,对悬挂件进行改进设计,主要如下:(1)采用新材料,提高整体刚度,避免弯曲和变形;(2)采用复合结构,增强悬挂件的强度;(3)重新设计关键部位,减少易损零部件的使用。
3.实施经过改进设计,新悬挂件在新材料和复合结构的支持下,具有更好的耐久性和稳定性。
此外,为了验证改进后的悬挂件的性能,进行了实际测试和使用验证。
测试结果表明,在相同的工况下,改进后的悬挂件相比原悬挂件具有更好的抗疲劳和抗震性能,而易损零部件的使用也得到了有效的控制。
在商用车长期使用中,改进后的悬挂件稳定可靠,有效延长了商用车的使用寿命。
4.总结通过对某商用车悬挂件的随机振动疲劳分析,本文得出了改进设计的方案,并通过实施验证证明了改进后的悬挂件性能得到了明显提升。
改进后的悬挂件可在商用车使用中具有更好的可靠性和安全性,有利于商用车的长期稳定运行。
5.改进设计的意义针对商用车悬挂件易损零部件的问题,本文设计了一种新型悬挂件。
通过采用新材料和复合结构的方式,大大提高了悬挂件整体的稳定性和耐久性。