隧道窑特点是
隧道窑知识及其工作原理

一、隧道窑的工作原理及其优点隧道窑一般是一条长的直线形通道,两侧及顶部有固定的窑墙及窑顶(顶部有平顶和拱顶之分),底部铺设的轨道上运行着窑车,窑车上装载着烧成产品,依次窑车进车,窑尾出车。
窑体构成了固定的预热带,冷却带,通常称为隧道窑的“三带”。
燃烧产生的高温烟气在隧道窑前端烟囱或在引风机的作用下,沿着隧道向窑头方向流动,同时逐步地预热进入窑内的制品,这一段构成了隧道窑的预热带。
隧道窑的中间为烧成带,在隧道窑的窑尾鼓入冷风,冷却隧道窑内后一段制品,鼓入的冷风经制品而被加热后,再抽出送入干燥窑作为干燥生坯的热源,这一段便构成了隧道窑的冷却带。
烧结砖隧道窑使用的燃料有固体、液体和气体3种不同的燃料。
目前我国大部分隧道窑使用的是固体燃料,也就是煤。
称作内燃烧结,有条件的地方也使用外烧结法,也就是油和气作为燃烧原料。
隧道窑是连续化生产,中间没有间断期,烧成周期短产量大,不受自然天气的影响,节约燃料。
它主要是利用逆流原理工作,因此热利用率较高,与常规轮窑相比热利用率高达50%左右。
隧道窑生产可节省劳力,能改善劳动环境,可减少环境污染,操作简便,装卸产品便于实现机械化。
减轻了工人的劳动强度。
在提高产品质量上,与轮窑相比,减少了工人二次倒运,烧成温度可控可调。
容易掌控其烧成规律,破碎率较低。
隧道窑和窑体内配套设备比较耐用,因为隧道窑与轮窑相比窑内不受急冷急热的影响,所以窑体使用寿命较长,一般在5年内不大修。
隧道窑在占地面积上与相同产量和规格的轮窑相比要少2|3。
隧道窑与轮窑所用砌筑材料和配备设备不一样。
因此,投资造价要高于轮窑,但后期生产成本低于轮窑。
二、隧道窑的种类与结构隧道窑可按内宽、产量、结构、运转自动化程度等各项指标进行分类。
(一)按隧道窑的断面宽度分类可分为3.0m,3.3m,3.6m,4.6m,4.8m,6.9m,7.3m,9,3m,10.3m等不同宽度的隧道窑。
(二)按窑炉结构分类(1)按窑顶结构可分成拱顶隧道窑,吊平顶隧道窑两大结构。
隧道窑特点是

隧道窑特点是:砖坯不动窑移动,窑体沿直径60m~80m的环形轨道运行,窑体从前到后分为干燥段、预热段、焙烧段、保温段、冷却段,总长约l00m~120m。
在未被窑体占用的环形轨道上,移动台车承载的制坯机与窑体同向运转,边制坯边码坯;在其后的移动式窑体以70m/d~l20m/d的速度前移,前端“纳入”砖坯,后端“吐出”成品砖,依次完成码坯一干燥一预热-焙烧-保温-冷却-出砖的全过程。
与传统的普通隧道窑相比,砖坯一次码在环形窑底上,由窑体移动来完成制砖工艺所需要的相对移动,故不需要窑车及其配套设施。
在普通隧道窑中,窑车的上部为焙烧空间,没有送风、排烟风机,为避免高温烟气窜入窑车烧坏车轮和轴承,还需设置车底送风风机。
在整个热供系统中,需保持车底、车面的送风压力平衡,既不让高温烟气下窜,也不许车底冷风上窜降低窑温。
移动式隧道窑没有窑车,故无需车底送风。
烧砖需要耗煤或有机质或油或蒸汽。
如何最大限度地提高热效率,是烧砖窑设计时的技术关键点。
砖的烧结温度在950°C~1080°C之间,要节煤就得提高窑炉的保温隔热效果。
移动式隧道窑采用硅酸铝耐火纤维砖叠砌,不但能减少窑体重量和窑体热胀冷缩应力,更能提高其绝热性,窑温保持时间长。
在生产实际中停止投煤、供风48小时后,重新投煤、供风仍能正常焙烧,这在普通隧道窑的运行中是不可能达到的。
移动式隧道窑中,砖坯从烧成温度降至室温,其散发的热量足以烘干同体积的湿砖坯,这可免建热风炉,也不必采取超热焙烧工艺来多耗煤以供烘干用热。
移动式隧道窑简析移动隧道窑特点是:砖坯不动窑移动,窑体沿直径60m~80m的环形轨道运行,窑体从前到后分为干燥段、预热段、焙烧段、保温段、冷却段,总长约l00m~120m.在未被窑体占用的环形轨道上,移动台车承载的制坯机与窑体同向运转,边制坯边码坯;在其后的移动式窑体以70m/d~l20m/d的速度前移,前端“纳入”砖坯,后端“吐出”成品砖,依次完成码坯一干燥一预热-焙烧-保温-冷却-出砖的全过程。
隧道窑的自问自答

隧道窑技术自问自答一.隧道窑的由来,以及优缺点因为窑的内腔象一条隧道,故而得名,隧道窑。
优点:1、生产连续化,周期短,产量大,质量高。
2、利用逆流原理工作3、烧成时间减短。
4、节省劳力。
5、提高质量,预热带、烧成带、冷却带三部分的温度,常常保持一定的范围,容易掌握其烧成规律,因此质量也较好,破损率也少。
缺点:因是连续烧成窑,所以烧成制度不宜随意变动,一般只适用大批量的生产和对烧成制度要求基本相同的制品,灵活性较差。
二.隧道窑的工艺流程隧道窑的工艺流程大体分为3个带:1.预热带:预热带的用是给窑车砖坯进行初期的预热,将砖坯中的水分,杂质排出砖坯进行第二次的干燥,保证砖坯不至于水份含量过高急剧加热产生炸裂。
一般来说预热带的操作对整个烧成工艺的成品率起着关键性的作用,若操作不当就会导致砖坯排水不充分造成了砖的压花(砖垛搭接处产生一圈黑纹)、黑心(砖中结构水没有排出就进行了烧结致使氧气进入不到砖的内部而使砖坯内燃掺料燃烧不充分)、网状裂纹。
2.培烧带:培烧带的作用是将窑车砖坯进行高温培烧,将砖坯中的内燃掺料作为燃料进行砖的高温烧结。
培烧带的操作是整个烧成工艺的核心,对砖的成品质量起着决定性的作用,若操作不当直接影响着成品的产质量,所以说应该针对本厂的工艺参数制定一套合理的烧成制度并且不宜随意改动。
3.冷却带:冷却带的作用是将烧好的高温砖坯进行冷却降温成为成品。
冷却带的操作对于整个烧成工艺起着改善作业环境提高能源利用的优化作用。
三.隧道窑的原理利用气流走向的原理来对制品进行预热、烧成、冷却。
总的来说培烧带燃烧产生的高温烟气在隧道窑前端烟囱或引风机的作用下,沿着隧道向窑头方向流动,同时逐步地预热进入窑内的制品,这一段构成了隧道窑的预热带。
在隧道窑的窑尾鼓入冷风,冷却隧道窑内后一段的制品,鼓入的冷风流经制品而被加热后,再抽出送入干燥窑作为干燥生坯的热源,这一段便构成了隧道窑的冷却带。
四.本厂隧道窑工艺的设备及其作用:1.牵引机:起到窑车运动的作用,操作时一定要按操作规程操作。
四、隧道窑的原理与结构

层号
厚度mm
材料名称
体积密度kg/m3
1
2 3 4 5
126
126 126 116 75
硅线石质砖
轻质高铝砖 轻质粘土砖 硅藻土砖 隔热板
2400
1050 800 450 375
6 126 800 轻质粘土砖 传统型隧道窑的窑体材料及厚度(烧成带,内壁温度1250℃)
现代陶瓷隧道窑由于窑墙不承受荷重,可以 彩优质耐火隔热材料取代传统窑墙耐火砖层 和保温砖层,在同样热阻的条件下,使窑墙 厚度和每平方米窑墙的质量均大大下降。目 前有组合型和全耐火纤维型两种结构形式。 应当指出,隧道窑内壁温度沿长度变化很大, 组合型和全耐火纤维型窑墙,在使用温度不 同的各区段内,各种材质及其衬砌厚度,均 应根据使用温度和传热利算确定。
(2)窑体密封构造 隧道窑的窑体是不动的,而窑底一窑车的台 面,则是随窑车而运动的。为了维持窑内的 烧成制度,隧道窑是通过设置砂封槽和曲折 密封来将窑内外隔开的。 生产中应注意保持砂封槽内有砂,并能埋住 窑车的沙封板,每辆窑车的砂封板应接触良 好,不能有变形。 窑车前后的曲折密封应互相对住,两侧与窑 墙之间的间隙应均匀,不能过大。
一)窑体主要尺寸 窑体主要尺寸包括窑体长度(有效长度),内宽,内高(有效高 度)等。 目前建筑卫生陶瓷隧道窑的长度在40~120m之间, 一般来说,当断面宽、高尺寸一定,码窑方式和烧成周期不变时, 增大窑长,则单窑产量扩大。 但窑长增加后,窑内阻力成正比增大,要维持烧成带微正压则预 热带负压也将随之成正比增大,漏风量和窑内上下温差都将增大, 不仅电耗增加,而且产品质量变差,反过来又限制了产量的增大, 同时长窑投资大,窑内气流阻力减少,投资减少,这是有利的, 但产量也会有所下降,而且窑过短时,窑内温度曲线和气氛都不 易调节,不易稳定。 因此,一般认为隧道窑适宜的长度为70~80米左右。
隧道窑的工作原理及特点
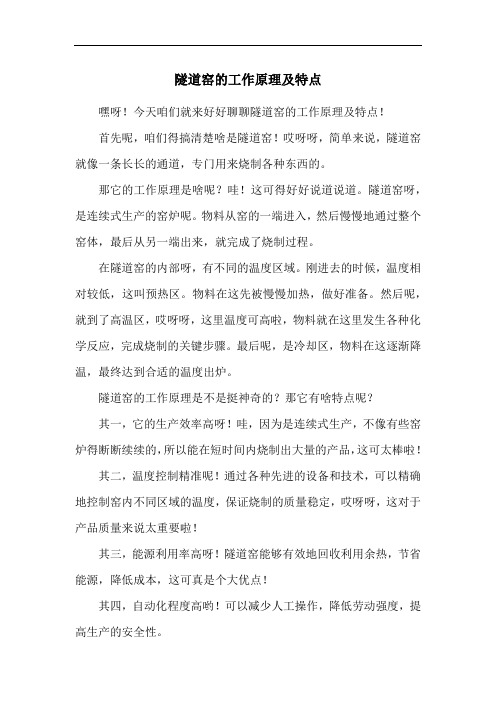
隧道窑的工作原理及特点嘿呀!今天咱们就来好好聊聊隧道窑的工作原理及特点!首先呢,咱们得搞清楚啥是隧道窑!哎呀呀,简单来说,隧道窑就像一条长长的通道,专门用来烧制各种东西的。
那它的工作原理是啥呢?哇!这可得好好说道说道。
隧道窑呀,是连续式生产的窑炉呢。
物料从窑的一端进入,然后慢慢地通过整个窑体,最后从另一端出来,就完成了烧制过程。
在隧道窑的内部呀,有不同的温度区域。
刚进去的时候,温度相对较低,这叫预热区。
物料在这先被慢慢加热,做好准备。
然后呢,就到了高温区,哎呀呀,这里温度可高啦,物料就在这里发生各种化学反应,完成烧制的关键步骤。
最后呢,是冷却区,物料在这逐渐降温,最终达到合适的温度出炉。
隧道窑的工作原理是不是挺神奇的?那它有啥特点呢?其一,它的生产效率高呀!哇,因为是连续式生产,不像有些窑炉得断断续续的,所以能在短时间内烧制出大量的产品,这可太棒啦!其二,温度控制精准呢!通过各种先进的设备和技术,可以精确地控制窑内不同区域的温度,保证烧制的质量稳定,哎呀呀,这对于产品质量来说太重要啦!其三,能源利用率高呀!隧道窑能够有效地回收利用余热,节省能源,降低成本,这可真是个大优点!其四,自动化程度高哟!可以减少人工操作,降低劳动强度,提高生产的安全性。
其五,产品质量稳定哟!由于温度控制精准,生产过程连续稳定,所以生产出来的产品质量都差不多,不会出现太大的差异。
哎呀呀,隧道窑的工作原理和特点是不是很有意思?它在陶瓷、耐火材料、砖瓦等行业都发挥着重要的作用呢!总之呀,隧道窑凭借着它独特的工作原理和显著的特点,成为了现代工业生产中不可或缺的一部分!哇!相信在未来,随着技术的不断进步,隧道窑还会不断地改进和完善,为我们的生产生活带来更多的便利和惊喜呢!。
隧道窑简介

隧道窑简介隧道窑简介隧道窑属于连续性火焰加热窑炉,一般是一条长直线形隧道,其两侧及顶部有固定的墙壁及拱顶,底部铺设轨道上运行着窑车,主要用于耐火材料,陶瓷,建筑用砖的烧成。
隧道窑与间歇式的旧式倒焰窑相比较,具有一系列的优点。
1、生产连续化,周期短,产量大,质量高。
2、利用逆流原理工作,因此热利用率高,燃料经济,因为热量的保持和余热的利用都很良好,所以燃料很节省,较倒焰窑可以节省燃料50-60%左右。
3、采用气幕、搅动循环装置,保证窑内温度上下均匀及烧成气氛,减少废品。
4、烧成时间减短,比较普通大窑由装窑到出窑需要3-5天,而隧道窑连续生产,节约装出窑升温及冷却时间。
5、节省劳力。
不但烧火操作简便,而且装窑和出窑的操作都在窑外进行,也很便利,改善了操作人员的劳动条件,减轻了劳动强度6、提高质量。
预热带、烧成带、冷却带三部分的温度,常常保持一定的范围,容易掌握其烧成规律,因此质量也较好,破损率也少。
7、窑和窑具都耐用。
因为窑内不受急冷急热的影响,所以窑体使用寿命长。
但是,隧道窑建造所需材料和设备较多,因此一次投资较大。
因是连续烧成窑,所以烧成制度不宜随意变动,一般只适用大批量的生产和对烧成制度要求基本相同的制品,灵活性较差。
隧道窑工作原理隧道可分为三带:预热带,烧成带,冷却带。
坯体(未烧半成品)干燥至一定水分装载在窑车上入窑,首先经预热带,受到来自烧成带的燃烧产物(烟气)预热,然后进入烧成带,燃料燃烧的火焰及生成的燃烧产物加热坯体,使达到一定的温度而烧成。
烧成的产品最后进入冷却带,将热量传给入窑的冷空气,产品本身冷却后出窑。
隧道窑结构概括的说隧道窑包括四部分:1)窑体2)窑内输送设备3)燃烧系统4)通风系统。
1.窑体是由窑墙、窑顶所组成。
窑体设置检查坑道,便于清扫落下的碎屑和砂粒,冷却窑车,检查窑车,以及在发生倒剁事故时,便于拖出窑车进行事故处理。
窑在进出车端设计有窑门,保证窑内操作稳定,防止冷空气漏人以减小气体分层,减少上下温差。
隧道窑知识及其工作原理
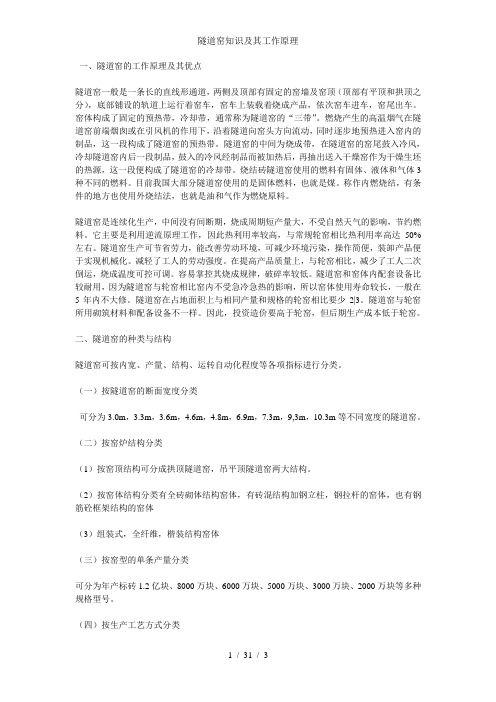
一、隧道窑的工作原理及其优点隧道窑一般是一条长的直线形通道,两侧及顶部有固定的窑墙及窑顶(顶部有平顶和拱顶之分),底部铺设的轨道上运行着窑车,窑车上装载着烧成产品,依次窑车进车,窑尾出车。
窑体构成了固定的预热带,冷却带,通常称为隧道窑的“三带”。
燃烧产生的高温烟气在隧道窑前端烟囱或在引风机的作用下,沿着隧道向窑头方向流动,同时逐步地预热进入窑内的制品,这一段构成了隧道窑的预热带。
隧道窑的中间为烧成带,在隧道窑的窑尾鼓入冷风,冷却隧道窑内后一段制品,鼓入的冷风经制品而被加热后,再抽出送入干燥窑作为干燥生坯的热源,这一段便构成了隧道窑的冷却带。
烧结砖隧道窑使用的燃料有固体、液体和气体3种不同的燃料。
目前我国大部分隧道窑使用的是固体燃料,也就是煤。
称作内燃烧结,有条件的地方也使用外烧结法,也就是油和气作为燃烧原料。
隧道窑是连续化生产,中间没有间断期,烧成周期短产量大,不受自然天气的影响,节约燃料。
它主要是利用逆流原理工作,因此热利用率较高,与常规轮窑相比热利用率高达50%左右。
隧道窑生产可节省劳力,能改善劳动环境,可减少环境污染,操作简便,装卸产品便于实现机械化。
减轻了工人的劳动强度。
在提高产品质量上,与轮窑相比,减少了工人二次倒运,烧成温度可控可调。
容易掌控其烧成规律,破碎率较低。
隧道窑和窑体内配套设备比较耐用,因为隧道窑与轮窑相比窑内不受急冷急热的影响,所以窑体使用寿命较长,一般在5年内不大修。
隧道窑在占地面积上与相同产量和规格的轮窑相比要少2|3。
隧道窑与轮窑所用砌筑材料和配备设备不一样。
因此,投资造价要高于轮窑,但后期生产成本低于轮窑。
二、隧道窑的种类与结构隧道窑可按内宽、产量、结构、运转自动化程度等各项指标进行分类。
(一)按隧道窑的断面宽度分类可分为3.0m,3.3m,3.6m,4.6m,4.8m,6.9m,7.3m,9,3m,10.3m等不同宽度的隧道窑。
(二)按窑炉结构分类(1)按窑顶结构可分成拱顶隧道窑,吊平顶隧道窑两大结构。
隧道窑
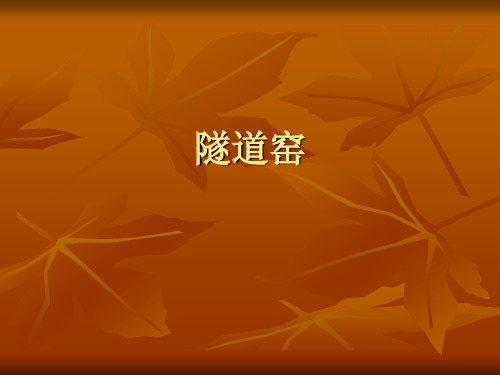
日用瓷(7 x 106 吨/年): 预热带/烧成带/冷却带 = 29.86/26.47/35.67(米)
电瓷(还原焰)(562 万吨/年): 预热带/烧成带/冷却带 = 38.52/28.0/50.07(米)
卫生瓷(隔 焰)(2 x 105 件/年): 预热带/烧成带/冷却带 = 30/22/40(米)
空
一 次 空 气
送 煤 气
风
气
图1-1 隧道窑工作原理图
隧道窑系统图
图1-2
三.隧道窑的规格
不同制品的隧道窑常见的规格为:
粘土砖(3~3.5 万吨/年): 预热带/烧成带/冷却带 = 41.8/22.0/37.4(米)
高铝砖(3.5 万吨/年): 预热带/烧成带/冷却带 = 72/24/60.6(米)
隧道窑
1.概述 2.隧道窑的结构 3.隧道窑的温度制度
概述
在耐火材料、陶瓷等制品的生产过程中, 烧成是一道重要工序,对产品的产量和质 量影响较大。 烧成设备主要有两大类,一类是连续式窑, 如隧道窑;另一种为间歇式窑,如倒焰窑 等。
★隧道窑的特点: 优点:生产能力大、燃耗低、使用寿命长、
机械化、自动化程度高、劳动条件好。
釉面砖釉烧(1.8 x 105 m2/年): 预热带/烧成带/冷却带 = 13.47/6.9/13.51(米)
1.概述 2.隧道窑的结构 3.隧道窑的温度制度
隧道窑的结构
规格:长×内宽×有效高度
有效高度:从车台平面至拱顶内衬的最大高度
1.断面尺寸与长度
图1-5
2.窑顶结构
3.窑墙结构 4.隧道窑预热带结构
冷却带:中间高两边低
- 1、下载文档前请自行甄别文档内容的完整性,平台不提供额外的编辑、内容补充、找答案等附加服务。
- 2、"仅部分预览"的文档,不可在线预览部分如存在完整性等问题,可反馈申请退款(可完整预览的文档不适用该条件!)。
- 3、如文档侵犯您的权益,请联系客服反馈,我们会尽快为您处理(人工客服工作时间:9:00-18:30)。
隧道窑特点是:砖坯不动窑移动,窑体沿直径60m~80m的环形轨道运行,窑体从前到后分为干燥段、预热段、焙烧段、保温段、冷却段,总长约
l00m~120m。
在未被窑体占用的环形轨道上,移动台车承载的制坯机与窑体同向运转,边制坯边码坯;在其后的移动式窑体以70m/d~l20m/d的速度前移,前端纳入”砖坯,后端吐出”成品砖, 依次完成码坯一干燥一预热-焙烧-保温-冷却-出砖的全过程。
与传统的普通隧道窑相比,砖坯一次码在环形窑底上,由窑体移动来完成制砖工艺所需要的相对移动,故不需要窑车及其配套设施。
在普通隧道窑中,窑车的上部为焙烧空间,没有送风、排烟风机,为避免高温烟气窜入窑车烧坏车轮和轴承,还需设置车底送风风机。
在整个热供系统中,需保持车底、车面的送风压力平衡,既不让高温烟气下窜,也不许车底冷风上窜降低窑温。
移动式隧道窑没有窑车,故无需车底送风。
烧砖需要耗煤或有机质或油或蒸汽。
如何最大限度地提高热效率,是烧砖窑设计时的技术关键点。
砖的烧结温度在950°C~1080°C 之间,要节煤就得提高窑炉的保温隔热效果。
移动式隧道窑采用硅酸铝耐火纤维砖叠砌,不但能减少窑体重量和窑体热胀冷缩应力,更能提高其绝热性,窑温保持时间长。
在生产实际中停止投煤、供风48 小时后,重新投煤、供风仍能正常焙烧,这在普通隧道窑的运行中是不可能达到的。
移动式隧道窑简析
形轨道运行,窑体从前到后分为干燥段、预热段、焙烧段、 却段,总长约loom 〜120m.在未被窑体占用的环形轨道上, 的制
坯机与窑体同向运转,边制坯边码坯;在其后的移动式窑体以 70m/d 〜l20m/d 的速度前移,前端“纳入”砖坯,后端“吐出”成品砖, 依次完成码坯一干燥一预热 -焙烧-保温-冷却-出砖的全过程。
与传统的 普通隧道窑相比, 砖坯一次码在环形窑底上, 由窑体移动来完成制砖工 艺所需要的相对移动,故不需要窑车及其配套设施。
在普通隧道窑中,窑车的上部为焙烧空间,没有送风、排烟风机, 为避免高温烟气窜入窑车烧坏车轮和轴承,还需设置车底送风风机。
在 整个热供系统中,需保持车底、车面的送风压力平衡,既不让高温烟气 下窜,也不许车底冷风上窜降低窑温。
移动式隧道窑没有窑车,故无需 车底送风。
烧砖需要耗煤或有机质或油或蒸汽。
如何最大限度地提高热效率, 是烧砖窑设计时的技术关键点。
砖的烧结温度在950° C 〜1080°C 之间,
要节煤就得提高窑炉的保温隔热效果。
移动式隧道窑采用硅酸铝耐火纤 维砖叠砌,不但能减少窑体重量和窑体热胀冷缩应力, 更能提高其绝热
性,窑温保持时间长。
在生产实际中停止投煤、供风 48小时后,重新 投煤、供风仍能正常焙烧,这在普通隧道窑的运行中是不可能达到的。
移动式隧道窑中,砖坯从烧成温度降至室温, 其散发的热量足以烘 干同体积的湿砖坯, 这可免建热风炉, 也不必采取超热焙烧工艺来多耗 煤以供烘干用热。
移动式隧道窑中, 砖坯从烧成温度降至室温, 其散发的热量足以
烘干同体积的湿砖坯,
这可免建热风炉, 也不必采取超热焙烧工艺来
多耗煤以供烘干用热。
移动隧道窑特点是:砖坯不动窑移动,窑体沿直径
60m~80m 勺环
保温段、冷 移动台车承载
在移动式隧道窑的热供系统中,干燥用风皆从窑尾进入,经过冷却段冷却烧成砖,使烧成砖在窑尾出口处降至室温,也就是说烧成砖散发的热量已全部被进入窑炉中的风带至焙烧段和干燥段,以供助燃和烘干。
移动式隧道窑的节能是其一个显著特点,而其合理的工艺流程设计、布局和简捷的物流路线也使整个制砖厂的能耗大幅度地降低。
在制砖厂生产中,每万块标砖需原料约20m3.若以每年生产3000 万块标砖、每年300 个工作日计,则每天生产10万块。
这样,原料制
备、运输、陈化、制坯、干燥、码烧等各工序间每日物流总量约250t X
(7次〜10次)以上。
普通隧道窑大部分人力消耗于此,因此,劳动强度大、工作环境恶劣。
在采用移动式隧道窑及其工艺布局的制砖企业,相对繁重的劳动是码坯,其动作简单而不费力,人力搬取(1〜 2 块/次)一转身(90°〜150 °)—码放。
这与传统制砖厂的装、出窑工作相比就相当轻松了,特别是工作环境不脏不热。
移动式隧道窑的工艺布局为:圆筒形陈化仓置于隧道窑环形轨道内场地的中央,仓墙与仓顶下檐之间设有密封件;跨越窑体上方的高架输送机将原料从窑的环轨外的细碎设备处输送至陈化仓,输送陈化料的旋转式输送饥一端铰接在仓内中央立柱中,另一端与移动台车上的制坯机料斗铰接;该旋转式的输送机的机架与陈化仓仓顶固接,制坯机移动时带动旋转式输送机使中央立柱旋转,仓顶也随之旋转;旋转式输送机伸入仓顶内的一段,其上布置的斗式提升机将陈化处理后的原料送至旋转式输送机,然后再送到制坯机,边制坯、边码坯。
制坯机按码坯需要逐渐前移。
这一工艺装备布局,圆筒中央陈化仓较之于分仓分时段入料、取料的传统矩形陈化仓有许多优点:占地少,建筑投资少;陈化循环合理,先入先取,循环渐进;物流路线简捷,提高了生产效率,降低了运营成本。
来源:作者: 何劲波徐惠彬
环形轨道上还设置有移动式护坯棚,包括位于环行隧道窑窑底上方的圆弧形棚顶和支撑棚顶的多个立柱。
该棚顶的两端分别与环形隧道窑窑体的首、尾端连为一体,棚顶架的两侧下沿设有导轨,棚顶立柱的上、下端均设有滚
轮,其中立柱下端滚轮置于环形隧道窑的轨道上,立柱上
端滚轮顶着棚顶下沿的导轨。
当窑体转动时棚顶将同步移动,而立柱也独立移动,以便调整柱的间距。