热处理工艺 内容摘要
金属材料热处理工艺与技术现状分析

金属材料热处理工艺与技术现状分析摘要:目前,我国尚不具备较为成熟的金属材料热处理技术,因而经常会出现工件脱碳等问题,造成所产出的产品质量不达标。
另外,从国内现有的金属材料的热处理工艺来看,由于等级偏低,使得产品自身很难形成较好的耐用。
所以,如果能够有效地提高金属材料的热处理技术,不仅能够保证最后的产品质量达标,也能够保证整个生产流程的绿色环保。
为此,有关人员应在实践中对这一技术进行进一步的研究与发展,从而形成一套较为完备的金属材料热处理工艺。
关键词:金属材料;热处理;技术应用1热处理工艺对金属材料性能的影响1.1金属材料的耐久性以及热处理应力如果是一种金属,长期经受着外界的巨大压力,又或者是处在一种极易被侵蚀的环境当中,就有可能会产生破损,甚至被侵蚀。
这个时候,就必须要考虑到这一点,因为这一块金属的高度,以及它的耐用性,以及热处理过程中所产生的应力。
在这类金属材料的高温热处理现场及工作中,所采用的不同用途尺寸应与其自身的高温耐久性能直接相关。
这也要求我们能将由于热处理而产生的应力所造成的消极影响降到最低,最后才能使产品的品质得到更好的提高。
1.2技术材料切割与热处理预热在对各种金属材料进行切削和施工的时候,也是要根据该金属材料自身的特性和特性,来对切割和加工工具进行合理的选择。
除此之外,在对各种金属材料进行切割的过程中,金属的颜色、变形状况、金属材料的光泽度也会直接地受到各种施工条件和环境的影响。
因此,在对各种金属材料进行预热和处理的时候,必须要提前对各种金属材料进行预热和处理,而且还可以为后续的各种金属材料的剪切、各种热处理步骤等提供一个更加健全、完善的技术保障。
通过对这类金属材料分别进行一次预热和高温加工后的处理,可以有效地降低切割工艺中的刀具粘连,并且可以有效地提高其切割效率和刀具切削精度,从而促进该种金属材料零件的性能和质量也得到显著地提高。
1.3金属材料的疲劳性与热处理温度在对各类金属材料进行加工和处理时,还会按照我们的要求进行一些低温热处理工艺和一个整体加工的流程,这样就可以更好地促进各类金属半导体产品的化学性能和质量都得到了较大程度的提高,在进行了一些相应的低温热处理后,通过简单的冷却和低温热处理就可以更好地促进各类金属材料的加工和处理,从而更好地使我们在一定环境下能够承受最大应力系数值而得到一定的临界值,并且极易造成材料断裂。
t10钢车刀热处理工艺

摘要T10钢车刀是用于车削加工的、具有一个切削部分的刀具。
车刀是切削加工中应用最广的刀具之一。
车刀的工作部分就是产生和处理切屑的部分,包括刀刃、使切屑断碎或卷拢的构造、排屑或容储切屑的空间、切削液的通道等构造要素。
在切削过程中,刀具的切削部分要承受很大的压力、摩擦、冲击和很高的温度。
因此,刀具材料必须具备高硬度、高耐磨性、足够的强度,韧性和抗氧化性,还需具有高的耐热性〔红硬性〕,即在高温下仍能保持足够硬度的性能。
[关键词] 切削耐磨高硬度红硬性技术要求高硬度,高耐磨性是刀具最重要的使用性能之一,假设没有足够的高的硬度是不能进展切削加工的。
否那么,在应力作用下,工具的形状和尺寸都要发生变化而失效。
高耐磨性那么是保证和进步工具寿命的必要性,除了以上要求红硬性及一定的强度和韧性。
在化学成分上,为了使工具钢尤其是刃具钢具有较高的硬度,通常都使其含有较高的的碳〔W〔C〕=0.65%~1.55%〕,以保证淬火后获得高碳马氏体,从而得到高的硬度和切断抗力,这对减少防止工具损坏是有利的。
大量的含碳质量分数又可进步耐磨性,碳素工具钢的理想淬火组织应该是细小的高碳马氏体和均匀细小的碳化物,工具钢在热处理前都应进展球化退火,以使碳化物呈细小的颗粒状且分布均匀。
工作条件及性能要求刃具在切削过程中,刀刃与工件外表金属互相作用,使切削产生变形与断裂,并从工件整体剥离下来。
故刀刃本身承受弯曲、改变、剪切应力和冲击、振动等负载荷作用。
由于切削层金属的变形及刃具与工件、切削的摩擦产生大量的摩擦热,均使刃具温度升高。
切屑速度越快,那么刃具的温度越高,有时刀刃温度可达600℃左右。
失效形式及使用性能刀刃是的失效形式有很多种,磨损是刀具失效的主要原因之一,如崩刃,折断和断裂等等。
〔1〕为了保证刃具的使用寿命,应要求有足够的耐磨性。
高的耐磨性不仅决定于高硬度,同时也取决于钢的组织。
在马氏体基体上分布着弥散的碳化物,尤其是各种合金碳化物能有效地进步刃具钢的耐磨才能。
真空热处理工艺.
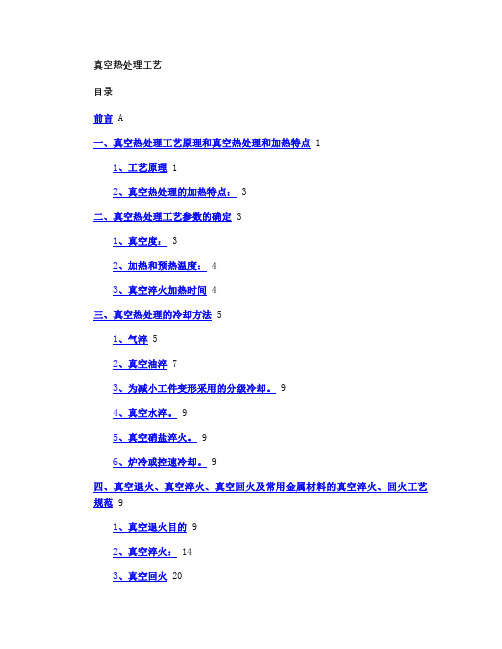
真空热处理工艺目录前言 A一、真空热处理工艺原理和真空热处理和加热特点 11、工艺原理 12、真空热处理的加热特点: 3二、真空热处理工艺参数的确定 31、真空度: 32、加热和预热温度: 43、真空淬火加热时间 4三、真空热处理的冷却方法 51、气淬 52、真空油淬 73、为减小工件变形采用的分级冷却。
94、真空水淬。
95、真空硝盐淬火。
96、炉冷或控速冷却。
9四、真空退火、真空淬火、真空回火及常用金属材料的真空淬火、回火工艺规范 91、真空退火目的 92、真空淬火: 143、真空回火 20四、常用金属材料的真空淬火、回火工艺规范。
20(1)合金结构钢和超高强度钢 20(2)弹簧钢 22(3)轴承钢 22(4)合金工具钢 23(5)高速钢 23(6)不锈耐热钢 24所谓真空热处理是工件在10-1~10-2Pa真空介质中进行加热到所需要的温度,然后在不同介质中以不同冷速进行冷却的热处理方法。
真空热处理被当代热处理界称为高效、节能和无污染的清洁热处理。
真空热处理的零件具有无氧化,无脱碳、脱气、脱脂,表面质量好,变形小,综合力学性能高,可靠性好(重复性好,寿命稳定)等一系列优点。
因此,真空热处理受到国内外广泛的重视和普遍的应用。
并把真空热处理普及程度作为衡量一个国家热处理技术水平的重要标志。
真空热处理技术是近四十年以来热处理工艺发展的热点,也是当今先进制造技术的重要领域。
一、真空热处理工艺原理和真空热处理和加热特点1、工艺原理(1)金属在真空状态下的相变特点。
在与大气压只差0.1MPa范围内的真空下,固态相变热力学、动力学不产生什么变化。
在制订真空热处理工艺规程时,完全可以依据在常压下固态相变的原理。
完全可以参考常压下各种类型组织转变的数据。
(2)真空脱气作用,提高金属材料的物理性能和力学性能。
(3)真空脱脂作用。
(4)金属的蒸发:在真空状态下加热,工件表面元素会发生蒸发现象。
表一各种金属的蒸气压-td金属达到下列蒸气压的平衡温度(℃)熔点(℃)10-2Pa10-1Pa1Pa10Pa133PaCu103511411273142216281038 Ag848936104711841353961 Be102911301246139515821284 Mg301331343515605651 Ca463528605700817851 Ba406546629730858717 Zn248292323405-419 Cd180220264321-321Hg-5.5134882126-38.9 Ae80888999611231179660Li377439514607725179Na19523829135643798K12316120726533864In74684095210881260157C22882471268129263214-Si111612231343148516701410Ti1249138415461742-1721Zr166018612001221225491830Sn9221042118913731609232Pb548625718832975328V158617261888207922071697 Nb23552539--2415 Ta25992820---2996Bi536609693802934271 Cr99210901205134215041890 Mo209522902533--2625 Mn791873980110312511244 Fe119513301447160217831535 W276730163309--3410 Ni125713711510167918841455 Pt174419042090231325821774 Au119013161465164618671063(5)表面净化作用,实现少无氧化和少无脱碳加热。
钛合金及其热处理工艺简述

钛合金及其热处理工艺简述宝鸡钛业股份有限公司:杨新林摘要:本文对钛及其合金的基本信息进行了简要介绍,对钛的几类固溶体划分进行了简述,对钛合金固态相变也进行了概述。
重点概述了钛合金的热处理类型及工艺,为之后生产实习中对钛合金的热处理工艺认识提供指导。
关键词:钛合金,热处理1 引言钛在地壳中的蕴藏量位于结构金属的第四位,但其应用远比铜、铁、锡等金属滞后。
钛合金中溶解的少量氧、氮、碳、氢等杂质元素,使其产生脆性,从而妨碍了早期人们对钛合金的开发和利用。
直至二十世纪四五十年代,随着英、美及苏联等国钛合金熔炼技术的改进和提高,钛合金的应用才逐渐开展[5]。
纯钛的熔点为1668℃,高于铁的熔点。
钛在固态下具有同素异构转变,在882.5℃以上为体心立方晶格的β相,在882.5℃以下为密排六方晶格的α相。
钛合金根据其退火后的室温组织类型进行分类,退火组织为α相的钛合金记为TAX,也称为α型钛合金;退火组织为β相的钛合金记为TBX,也称为β型钛合金;退火组织为α+β两相的钛合金记为TCX,也称为α+β型钛合金,其中的“X”为顺序号。
我国目前的钛合金牌号已超过50个,其中TA型26个,TB型8个以上,TC 型15个以上[5]。
钛合金具有如下特点:(1)与其他的合金相比,钛合金的屈强比很高,屈服强度与抗拉强度极为接近;(2)钛合金的密度为4g/cm3,大约为钢的一半,因此,它具有较高的比强度;(3)钛合金的耐腐蚀性能优良,在海水中其耐蚀性甚至比不锈钢还要好;(4)钛合金的导热系数小,摩擦系数大,因而机械加工性不好;(5)在焊接时,钛合金焊缝金属和高热影响区容易被氧、氢、碳、氮等元素污染,使接头性能变坏。
在熔炼和各种加工过程完成之后,为了消除材料中的加工应力,达到使用要求的性能水平,稳定零件尺寸以及去除热加工或化学处理过程中增加的有害元素(例如氢)等,往往要通过热处理工艺来实现。
钛合金热处理工艺大体可分为退火、固溶处理和时效处理三个类型。
35crmnsia钢热处理工艺研究

35crmnsia钢热处理工艺研究摘要:35crmnsia钢作为一种高强度低合金结构钢,在航空、航天、军工等领域有着广泛的应用。
本文通过对35crmnsia钢的热处理工艺进行研究,探讨了不同热处理工艺对钢材性能的影响,为钢材的应用提供了参考依据。
关键词:35crmnsia钢、热处理工艺、性能影响、应用一、引言35crmnsia钢是一种高强度低合金结构钢,具有优异的力学性能和耐热性能,在航空、航天、军工等领域有着广泛的应用。
钢材的性能受到热处理工艺的影响较大,因此研究35crmnsia钢的热处理工艺对钢材性能的影响,对于提高钢材的性能和推广应用具有重要意义。
二、35crmnsia钢的热处理工艺35crmnsia钢的热处理工艺主要包括淬火、回火和正火三个阶段。
淬火是将钢材加热到一定温度并迅速冷却,使钢材的组织发生变化,从而提高钢材的硬度和强度。
回火是将淬火后的钢材加热到一定温度并保温一段时间,使钢材的硬度和强度适当降低,同时提高钢材的韧性和塑性。
正火是将钢材加热到一定温度并保温一段时间,使钢材的组织稳定化,提高钢材的抗蠕变性能。
三、35crmnsia钢热处理工艺对钢材性能的影响1.淬火工艺对钢材性能的影响淬火是35crmnsia钢热处理工艺中最重要的一个环节,淬火工艺的不同会对钢材的性能产生较大影响。
淬火温度越高,钢材的硬度和强度越高,但韧性和塑性会相应降低。
淬火温度越低,钢材的韧性和塑性越高,但硬度和强度会相应降低。
淬火介质的选择也会对钢材的性能产生影响,一般情况下,水冷淬火可以获得更高的硬度和强度,但容易产生裂纹和变形;油冷淬火可以获得较高的硬度和强度,同时也能保证钢材的韧性和塑性。
2.回火工艺对钢材性能的影响回火是35crmnsia钢热处理工艺中的重要环节之一,回火温度和时间的不同会对钢材的性能产生较大影响。
回火温度越高,钢材的硬度和强度会降低,但韧性和塑性会相应提高。
回火温度越低,钢材的韧性和塑性会降低,但硬度和强度会相应提高。
热处理工艺报告
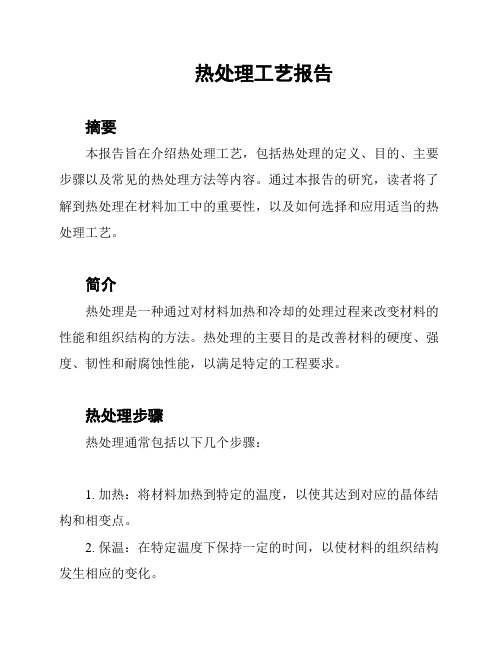
热处理工艺报告
摘要
本报告旨在介绍热处理工艺,包括热处理的定义、目的、主要步骤以及常见的热处理方法等内容。
通过本报告的研究,读者将了解到热处理在材料加工中的重要性,以及如何选择和应用适当的热处理工艺。
简介
热处理是一种通过对材料加热和冷却的处理过程来改变材料的性能和组织结构的方法。
热处理的主要目的是改善材料的硬度、强度、韧性和耐腐蚀性能,以满足特定的工程要求。
热处理步骤
热处理通常包括以下几个步骤:
1. 加热:将材料加热到特定的温度,以使其达到对应的晶体结构和相变点。
2. 保温:在特定温度下保持一定的时间,以使材料的组织结构发生相应的变化。
3. 冷却:将材料迅速冷却到室温,以稳定其组织结构和性能。
常见的热处理方法
以下是几种常见的热处理方法:
1. 固溶处理:将合金加热到固溶态,以溶解固溶体中的溶质元素,然后通过急冷或保温使其形成固溶体。
2. 淬火处理:将材料加热到临界温度以上,然后迅速冷却,以获得高硬度和高弹性的材料。
3. 微调退火:在固溶处理后,通过退火使合金中的溶质元素重新析出,从而产生所需的微观结构和性能。
4. 热拉伸处理:将材料加热到固溶态,然后通过拉伸和冷却来调整其组织结构和性能。
结论
热处理工艺在材料加工中起着重要的作用,可以改善材料的性能和组织结构。
选择合适的热处理方法对于满足特定的工程要求至关重要。
在实际应用中,需要综合考虑材料的成分、加工工艺和使用环境等因素,以确定最佳的热处理工艺方案。
6061合金在线热处理工艺研究

6061合金在线热处理工艺研究摘要:分析了6061合金在线热处理的工艺条件。
挤压出口温度510℃-540℃。
挤压速度3-12米/分,可以获得高的强度和硬度及组织均匀。
关键词:在线热处理、强度、硬度。
6061合金属于Al-Mg-Si系铝合金,其中强化相为Mg2Si,具有良好的塑性加工性能,属于中等强度的铝合金。
其耐蚀性良好,被广泛应用结构材料中。
随着科学技术的发展,各个领域对材料的内在质量要求越来越高,特别是机械性能和表面硬度指标的相对提高,对热处理工艺提出了更高的要求。
该合金热处理温度范围宽,但淬火敏感性比6063合金的高,挤压后不能实现风冷淬火,需重新固溶处理和淬火时效,才能获得较高的强度和硬度。
生产中一般采用空气循环淬火炉淬火和在线水冷淬火两种热处理方式进行。
实现在线水冷淬火热处理需要满足三个基本条件:一是要在制品水冷前达到固溶处理的温度范围;二是要有充分冷却速度;三是制品从模孔中流出来进行淬火水槽的过程(又称转移过程)中对材料的综合性能没有大的影响。
本文就在线水冷的工艺制度做一分析,以确定适宜的工艺参数。
1、试验材料之工艺研制1.1挤压铸锭的制备试验中使用的6061合金铸锭其化学成分见表1所示。
采用φ152㎜铸棒,熔体经气体精炼、过滤及晶粒细化处理。
铸棒在均匀化温度为550℃,保温6小时的制度下均匀化处理表1 化学成分质量分数(%)1.2 挤压工艺试验中采用制品挤压直接在线淬火后再进行人工时效的生产工艺。
其挤压工艺流程图如图1所示:铸锭装入加热炉内进行加热,其加热温度500-540℃,挤压筒定温440℃。
在铝材三厂1350T挤压机上采用φ156.8㎜挤压筒进行挤压。
在冷却时调整好水的流量,使之有足够的冷却强度,并根据挤压机所具有的特点,选择了不同的挤压速度来改变冷却效果。
试验中采用3-8m/min的不同挤压速度,主要挤压工艺参数见表2所示表2 挤压工艺参数2.3 热处理及精整工艺在线淬火采用冷却方式为水冷却.调整好水管喷头流量,保证制品通过淬火区域有足够的冷却强度.使冷却速度够快.试验中制品流出出料口的温度为510-530℃,经过水冷淬火后的制品温度从50℃逐渐回升到98℃。
热处理工艺
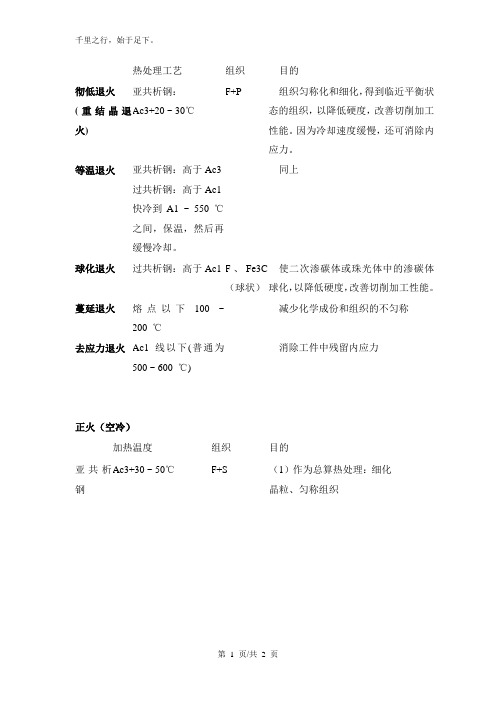
使二次渗碳体或珠光体中的渗碳体球化,以降低硬度,改善切削加工性能。
蔓延退火
熔点以下100~200℃
减少化学成份和组织的不匀称
去应力退火
Ac1线以下(普通为500~600℃)
消除工件中残留内应力
正火(空冷)
加热温度
组织
目的
亚共析钢
Ac3+30~50℃
F+S
(1)作为总算热处理:细化晶粒、匀称组织
(2)作为预先热处理:对结构较大的合金结构钢前,淬火或调质前常举行正火,消除魏氏组织和带状组织,并获得细小而匀称的组织。
(3)改善切削加工性能:调节硬度
过共析钢
Accm+30~50℃
S+ Fe3CⅡ
热处理工艺
组织
目的
彻低退火
(重结晶退火)
亚共析钢:Ac3+20 Nhomakorabea30℃F+P
组织匀称化和细化,得到临近平衡状态的组织,以降低硬度,改善切削加工性能。因为冷却速度缓慢,还可消除内应力。
等温退火
亚共析钢:高于Ac3
过共析钢:高于Ac1
快冷到A1~550℃之间,保温,然后再缓慢冷却。
同上
球化退火
过共析钢:高于Ac1
- 1、下载文档前请自行甄别文档内容的完整性,平台不提供额外的编辑、内容补充、找答案等附加服务。
- 2、"仅部分预览"的文档,不可在线预览部分如存在完整性等问题,可反馈申请退款(可完整预览的文档不适用该条件!)。
- 3、如文档侵犯您的权益,请联系客服反馈,我们会尽快为您处理(人工客服工作时间:9:00-18:30)。
正火时的Ac3(也称Acm)温度是铁碳合金的AC3线,一般是从727到912摄氏度之间正火温度一般在AC3线上30-50摄氏度,即对应为757到962摄氏度.热处理工艺正火,又称常化,是将工件加热至Ac3或Accm以上30~50℃,保温一段时间后,从炉中取出在空气中或喷水、喷雾或吹风冷却的金属热处理工艺。
正火与退火的不同点是正火冷却速度比退火冷却速度稍快,因而正火组织要比退火组织更细一些,其机械性能也有所提高。
另外,正火炉外冷却不占用设备,生产率较高,因此生产中尽可能采用正火来代替退火。
正火的主要应用范围有:①用于低碳钢,正火后硬度略高于退火,韧性也较好,可作为切削加工的预处理。
②用于中碳钢,可代替调质处理作为最后热处理,也可作为用感应加热方法进行表面淬火前的预备处理。
③用于工具钢、轴承钢、渗碳钢等,可以消降或抑制网状碳化物的形成,从而得到球化退火所需的良好组织。
④用于铸钢件,可以细化铸态组织,改善切削加工性能。
⑤用于大型锻件,可作为最后热处理,从而避免淬火时较大的开裂倾向。
⑥用于球墨铸铁,使硬度、强度、耐磨性得到提高,如用于制造汽车、拖拉机、柴油机的曲轴、连杆等重要零件。
⑦过共析钢球化退火前进行一次正火,可消除网状二次渗碳体,以保证球化退火时渗碳体全部球粒化。
退火annealing将金属缓慢加热到一定温度,保持足够时间,然后以适宜速度冷却(通常是缓慢冷却,有时是控制冷却)的一种金属热处理工艺。
目的是使经过铸造、锻轧、焊接或切削加工的材料或工件软化,改善塑性和韧性,使化学成分均匀化,去除残余应力,或得到预期的物理性能。
退火工艺随目的之不同而有多种,如重结晶退火、等温退火、均匀化退火、球化退火、去除应力退火、再结晶退火,以及稳定化退火、磁场退火等等。
退火的一个最主要工艺参数是最高加热温度(退火温度),大多数合金的退火加热温度的选择是以该合金系的相图为基础的,如碳素钢以铁碳平衡图为基础(图1)。
各种钢(包括碳素钢及合金钢)的退火温度,视具体退火目的的不同而在各该钢种的Ac3以上、Ac1以上或以下的某一温度。
各种非铁合金的退火温度则在各该合金的固相线温度以下、固溶度线温度以上或以下的某一温度。
重结晶退火应用于平衡加热和冷却时有固态相变(重结晶)发生的合金。
其退火温度为各该合金的相变温度区间以上或以内的某一温度。
加热和冷却都是缓慢的。
合金于加热和冷却过程中各发生一次相变重结晶,故称为重结晶退火,常被简称为退火。
这种退火方法,相当普遍地应用于钢。
钢的重结晶退火工艺是:缓慢加热到Ac3(亚共析钢)或Ac1(共析钢或过共析钢)以上30~50℃,保持适当时间,然后缓慢冷却下来。
通过加热过程中发生的珠光体(或者还有先共析的铁素体或渗碳体)转变为奥氏体(第一回相变重结晶)以及冷却过程中发生的与此相反的第二回相变重结晶,形成晶粒较细、片层较厚、组织均匀的珠光体(或者还有先共析铁素体或渗碳体)。
退火温度在Ac3以上(亚共析钢)使钢发生完全的重结晶者,称为完全退火,退火温度在Ac1与Ac3之间(亚共析钢)或Ac1与Acm之间(过共析钢),使钢发生部分的重结晶者,称为不完全退火。
前者主要用于亚共析钢的铸件、锻轧件、焊件,以消除组织缺陷(如魏氏组织、带状组织等),使组织变细和变均匀,以提高钢件的塑性和韧性。
后者主要用于中碳和高碳钢及低合金结构钢的锻轧件。
此种锻、轧件若锻、轧后的冷却速度较大时,形成的珠光体较细、硬度较高;若停锻、停轧温度过低,钢件中还有大的内应力。
此时可用不完全退火代替完全退火,使珠光体发生重结晶,晶粒变细,同时也降低硬度,消除内应力,改善被切削性。
此外,退火温度在Ac1与Acm之间的过共析钢球化退火,也是不完全退火。
重结晶退火也用于非铁合金,例如钛合金于加热和冷却时发生同素异构转变,低温为α相(密排六方结构),高温为β相(体心立方结构),其中间是“α+β”两相区,即相变温度区间。
为了得到接近平衡的室温稳定组织和细化晶粒,也进行重结晶退火,即缓慢加热到高于相变温度区间不多的温度,保温适当时间,使合金转变为β相的细小晶粒;然后缓慢冷却下来,使β相再转变为α相或α+β两相的细小晶粒。
等温退火应用于钢和某些非铁合金如钛合金的一种控制冷却的退火方法。
对钢来说,是缓慢加热到Ac3(亚共析钢)或Ac1(共析钢和过共析钢)以上不多的温度,保温一段时间,使钢奥氏体化,然后迅速移入温度在A1以下不多的另一炉内,等温保持直到奥氏体全部转变为片层状珠光体(亚共析钢还有先共析铁素体;过共析钢还有先共析渗碳体)为止,最后以任意速度冷却下来(通常是出炉在空气中冷却)。
等温保持的大致温度范围在所处理钢种的等温转变图上A1至珠光体转变鼻尖温度这一区间之内(见过冷奥氏体转变图);具体温度和时间,主要根据退火后所要求的硬度来确定(图2)。
等温温度不可过低或过高,过低则退火后硬度偏高;过高则等温保持时间需要延长。
钢的等温退火的目的,与重结晶退火基本相同,但工艺操作和所需设备都比较复杂,所以通常主要是应用于过冷奥氏体在珠光体型相变温度区间转变相当缓慢的合金钢。
后者若采用重结晶退火方法,往往需要数十小时,很不经济;采用等温退火则能大大缩短生产周期,并能使整个工件获得更为均匀的组织和性能。
等温退火也可在钢的热加工的不同阶段来用。
例如,若让空冷淬硬性合金钢由高温空冷到室温时,当心部转变为马氏体之时,在已发生了马氏体相变的外层就会出现裂纹;若将该类钢的热钢锭或钢坯在冷却过程中放入700℃左右的等温炉内,保持等温直到珠光体相变完成后,再出炉空冷,则可免生裂纹。
含β相稳定化元素较高的钛合金,其β相相当稳定,容易被过冷。
过冷的β相,其等温转变动力学曲线(图3)与钢的过冷奥氏体等温转变图相似。
为了缩短重结晶退火的生产周期并获得更细、更均匀的组织,亦可采用等温退火。
均匀化退火亦称扩散退火。
应用于钢及非铁合金(如锡青铜、硅青铜、白铜、镁合金等)的铸锭或铸件的一种退火方法。
将铸锭或铸件加热到各该合金的固相线温度以下的某一较高温度,长时间保温,然后缓慢冷却下来。
均匀化退火是使合金中的元素发生固态扩散,来减轻化学成分不均匀性(偏析),主要是减轻晶粒尺度内的化学成分不均匀性(晶内偏析或称枝晶偏析)。
均匀化退火温度所以如此之高,是为了加快合金元素扩散,尽可能缩短保温时间。
合金钢的均匀化退火温度远高于Ac3,通常是1050~1200℃。
非铁合金锭进行均匀化退火的温度一般是“0.95×固相线温度(K)”,均匀化退火因加热温度高,保温时间长,所以热能消耗量大。
球化退火只应用于钢的一种退火方法。
将钢加热到稍低于或稍高于Ac1的温度或者使温度在A1上下周期变化,然后缓冷下来。
目的在于使珠光体内的片状渗碳体以及先共析渗碳体都变为球粒状,均匀分布于铁素体基体中(这种组织称为球化珠光体)。
具有这种组织的中碳钢和高碳钢硬度低、被切削性好、冷形变能力大。
对工具钢来说,这种组织是淬火前最好的原始组织。
球化退火的具体工艺(图4)有:①普通(缓冷)球化退火(图4a),缓冷适用于多数钢种,尤其是装炉量大时,操作比较方便,但生产周期长;②等温球化退火(图4b),适用于多数钢种,特别是难于球化的钢以及球化质量要求高的钢(如滚动轴承钢);其生产周期比普通球化退火短,不过需要有能够控制共析转变前冷却速率的炉子;③周期球化退火(图4c),适用于原始组织为片层状珠光体组织的钢,其生产周期也比普通球化退火短,不过在设备装炉量大的条件下,很难按控制要求改变温度,故在生产中未广泛采用;④低温球化退火(图4d),适用于经过冷形变加工的钢以及淬火硬化过的钢(后者通常称为高温软化回火);⑤形变球化退火,形变加工对球化有加速作用,将形变加工与球化结合起来,可缩短球化时间。
它适用于冷、热形变成形的钢件和钢材(如带材)(图4e是在Acm或Ac3与Ac1之间进行短时间、大形变量的热形变加工者;图4f是在常温先予以形变加工者;图4g是利用锻造余热进行球化者)。
再结晶退火应用于经过冷变形加工的金属及合金的一种退火方法。
目的为使金属内部组织变为细小的等轴晶粒,消除形变硬化,恢复金属或合金的塑性和形变能力(回复和再结晶)。
若欲保持金属或合金表面光亮,则可在可控气氛的炉中或真空炉中进行再结晶退火。
去除应力退火铸、锻、焊件在冷却时由于各部位冷却速度不同而产生内应力,金属及合金在冷变形加工中以及工件在切削加工过程中也产生内应力。
若内应力较大而未及时予以去除,常导致工件变形甚至形成裂纹。
去除应力退火是将工件缓慢加热到较低温度(例如,灰口铸铁是500~550℃,钢是500~650℃),保温一段时间,使金属内部发生弛豫,然后缓冷下来。
应该指出,去除应力退火并不能将内应力完全去除,而只是部分去除,从而消除它的有害作用。
回火tempering;temper又称配火。
金属热处理工艺的一种。
将经过淬火的工件重新加热到低于下临界温度的适当温度,保温一段时间后在空气或水、油等介质中冷却的金属热处理。
或将淬火后的合金工件加热到适当温度,保温若干时间,然后缓慢或快速冷却。
一般用以减低或消除淬火钢件中的内应力,或降低其硬度和强度,以提高其延性或韧性。
根据不同的要求可采用低温回火、中温回火或高温回火。
通常随着回火温度的升高,硬度和强度降低,延性或韧性逐渐增高。
钢铁工件在淬火后具有以下特点:①得到了马氏体、贝氏体、残余奥氏体等不平衡(即不稳定)组织。
②存在较大内应力。
③力学性能不能满足要求。
因此,钢铁工件淬火后一般都要经过回火。
作用回火的作用在于:①提高组织稳定性,使工件在使用过程中不再发生组织转变,从而使工件几何尺寸和性能保持稳定。
②消除内应力,以便改善工件的使用性能并稳定工件几何尺寸。
③调整钢铁的力学性能以满足使用要求。
回火之所以具有这些作用,是因为温度升高时,原子活动能力增强,钢铁中的铁、碳和其他合金元素的原子可以较快地进行扩散,实现原子的重新排列组合,从而使不稳定的不平衡组织逐步转变为稳定的平衡组织。
内应力的消除还与温度升高时金属强度降低有关。
一般钢铁回火时,硬度和强度下降,塑性提高。
回火温度越高,这些力学性能的变化越大。
有些合金元素含量较高的合金钢,在某一温度范围回火时,会析出一些颗粒细小的金属化合物,使强度和硬度上升。
这种现象称为二次硬化。
要求用途不同的工件应在不同温度下回火,以满足使用中的要求。
①刀具、轴承、渗碳淬火零件、表面淬火零件通常在250℃以下进行低温回火。
低温回火后硬度变化不大,内应力减小,韧性稍有提高。
②弹簧在350~500℃下中温回火,可获得较高的弹性和必要的韧性。
③中碳结构钢制作的零件通常在500~600℃进行高温回火,以获得适宜的强度与韧性的良好配合。
淬火加高温回火的热处理工艺总称为调质。