离心浇铸
苏锡常离心浇铸工艺流程
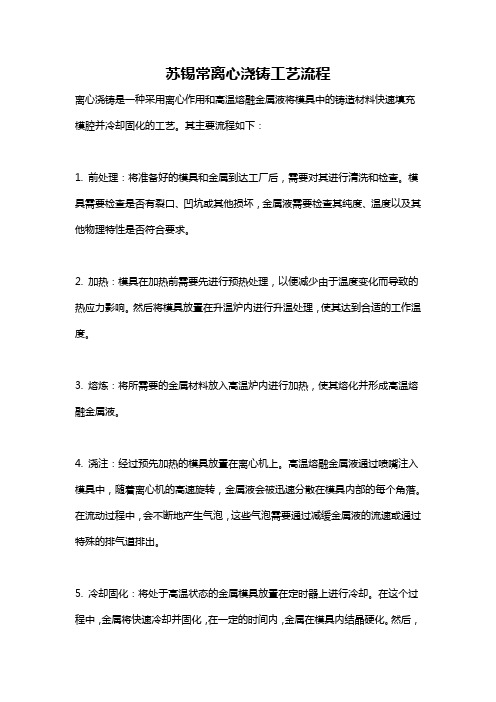
苏锡常离心浇铸工艺流程
离心浇铸是一种采用离心作用和高温熔融金属液将模具中的铸造材料快速填充模腔并冷却固化的工艺。
其主要流程如下:
1. 前处理:将准备好的模具和金属到达工厂后,需要对其进行清洗和检查。
模具需要检查是否有裂口、凹坑或其他损坏,金属液需要检查其纯度、温度以及其他物理特性是否符合要求。
2. 加热:模具在加热前需要先进行预热处理,以便减少由于温度变化而导致的热应力影响。
然后将模具放置在升温炉内进行升温处理,使其达到合适的工作温度。
3. 熔炼:将所需要的金属材料放入高温炉内进行加热,使其熔化并形成高温熔融金属液。
4. 浇注:经过预先加热的模具放置在离心机上。
高温熔融金属液通过喷嘴注入模具中,随着离心机的高速旋转,金属液会被迅速分散在模具内部的每个角落。
在流动过程中,会不断地产生气泡,这些气泡需要通过减缓金属液的流速或通过特殊的排气道排出。
5. 冷却固化:将处于高温状态的金属模具放置在定时器上进行冷却。
在这个过程中,金属将快速冷却并固化,在一定的时间内,金属在模具内结晶硬化。
然后,
模具从离心机中取出,并进行后处理:
6. 后处理:将已经固化的铸件取出并清理表面。
移除挂件和毛刺(连接于零件上的铸造余料),并尽可能地使零件表面平整。
以上是苏锡常离心浇铸工艺的基本流程,这种工艺在制造铸件时经常被采用,其优点是能制造出更加均匀、质量更好的铸件。
铜丝母离心机浇铸工艺流程

铜丝母离心机浇铸工艺流程
铜丝母离心机浇铸工艺流程:
一、准备工序
1、检查熔铸机、合金、模具和要求的参数(因外观要求而可能用到的涂漆)。
2、准备浇铸沙(或沥青)和涂料。
3、清洗和湿润模具表面。
二、浇铸工序
1、将合金块放入熔铸机,加热至熔点(例如铜合金为1100℃),按预定时间保持熔点,以保证纯度和材料的细致性能。
2、铜丝母离心机浇铸模具准备好,将铜丝母、螺丝和螺母组装到模具中,并加入浇铸沙支撑和铸造用的油脂。
3、把熔铸后的铜合金铸件从熔铸机龙头转移到铸造机上,并将合金撒在模具中,确保铸件的填充质量。
4、待铸件冷却后,手动或自动气动移动离心机机械手,按照螺丝、螺母图案打满。
5、安装螺母、螺丝到铸件上,确保打排整齐。
6、涂漆装饰,如果要求完成后的外观外形要求。
三、完成工序
1、拆下模具、将熔铸铜合金从模具中取出,然后用清水清洗,表面干净无污渍。
2、检查浇铸件的外观,形状,精度和尺寸,以确保完成品的质
量。
3、完成所有浇铸过程,清洗和清理铸造机和模具,准备下次使用或存放。
离心浇铸个人工作总结
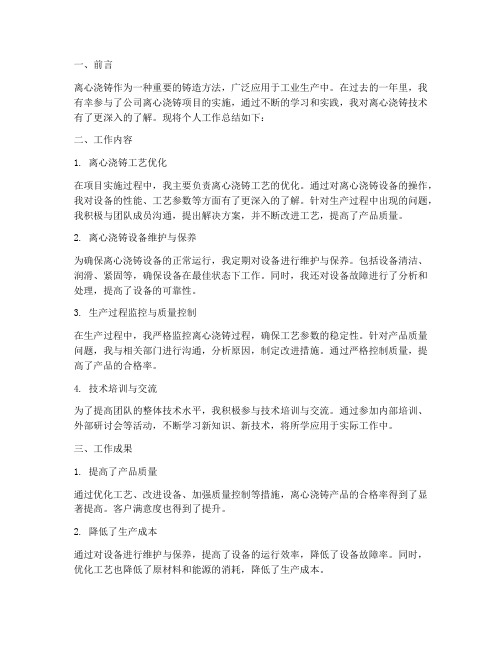
一、前言离心浇铸作为一种重要的铸造方法,广泛应用于工业生产中。
在过去的一年里,我有幸参与了公司离心浇铸项目的实施,通过不断的学习和实践,我对离心浇铸技术有了更深入的了解。
现将个人工作总结如下:二、工作内容1. 离心浇铸工艺优化在项目实施过程中,我主要负责离心浇铸工艺的优化。
通过对离心浇铸设备的操作,我对设备的性能、工艺参数等方面有了更深入的了解。
针对生产过程中出现的问题,我积极与团队成员沟通,提出解决方案,并不断改进工艺,提高了产品质量。
2. 离心浇铸设备维护与保养为确保离心浇铸设备的正常运行,我定期对设备进行维护与保养。
包括设备清洁、润滑、紧固等,确保设备在最佳状态下工作。
同时,我还对设备故障进行了分析和处理,提高了设备的可靠性。
3. 生产过程监控与质量控制在生产过程中,我严格监控离心浇铸过程,确保工艺参数的稳定性。
针对产品质量问题,我与相关部门进行沟通,分析原因,制定改进措施。
通过严格控制质量,提高了产品的合格率。
4. 技术培训与交流为了提高团队的整体技术水平,我积极参与技术培训与交流。
通过参加内部培训、外部研讨会等活动,不断学习新知识、新技术,将所学应用于实际工作中。
三、工作成果1. 提高了产品质量通过优化工艺、改进设备、加强质量控制等措施,离心浇铸产品的合格率得到了显著提高。
客户满意度也得到了提升。
2. 降低了生产成本通过对设备进行维护与保养,提高了设备的运行效率,降低了设备故障率。
同时,优化工艺也降低了原材料和能源的消耗,降低了生产成本。
3. 丰富了团队技术实力通过技术培训与交流,团队成员的技术水平得到了提升,为公司的技术创新和持续发展奠定了基础。
四、不足与改进1. 理论知识储备不足虽然在实际工作中取得了一定的成绩,但我在理论知识方面还有待提高。
在今后的工作中,我将加强学习,提高自己的理论水平。
2. 沟通协调能力有待提高在项目实施过程中,我发现自己在沟通协调方面还存在不足。
为了更好地完成工作,我将努力提高自己的沟通协调能力。
9-离心和浇铸成型工艺
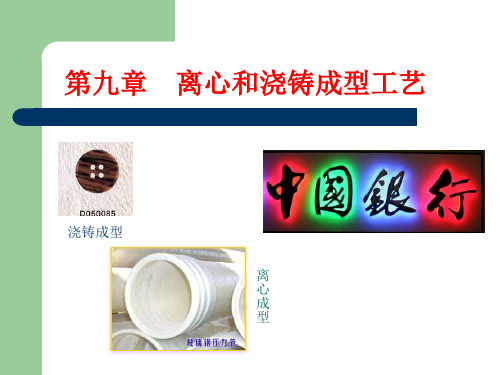
2 人造石材生产工艺
生产人造石材的原材料是不饱和聚酯树脂,填 料和颜料。
①树脂
生产人造石材的树脂分面层和结构层两种, 表面装饰层树脂要求收缩性小,有韧性、硬度好, 耐热、耐磨、耐水等,同时要求易调色。 例:辛戌二醇邻苯型树脂用于人造石材,辛戌 二醇间苯型树脂用于生产卫生洁具。
②填料 生产人造石材的填料有很多。 生产人造大理石的填料是大理石粉,石英粉、 白云石粉、碳酸钙粉等。
(2)模具
离心法生产玻璃钢管的模具,主要是钢模, 模具分整体式和拼装式两种:小于φ800mm管的模 具,用整体式,大于φ800mm管的模具,可以用拼 装式。
模具
模具设计要保证有足够的强度和刚度,防止 旋转、震动过程中变形。
模具
模具由管身、封头、托轮箍组成。 管身由钢板卷焊而成,小直径管身可用无缝钢管。模 具的管身内表面必须平整,光滑,一般都要精加工和抛光, 保证顺利脱模。 封头的作用是增加管模端头的强度和防止物料外流。
1 钮扣生产工艺
用聚酯树脂浇铸的钮扣,具有硬度高,光泽 好,耐磨、耐烫、耐干洗、花色品种多及价格低 等优点,目前在国内外已基本取代了有机玻璃钮 扣,占钮扣市场80%以上。
1 钮扣生产工艺
生产钮扣的原料主要是不饱和聚酯树脂、固化 剂(引发剂采用过氧化甲乙酮)和辅助材料(包 括色浆、珠光粉、触变剂等)。
不饱和聚酯树脂
增强材料
主要是玻璃纤维及其制品。玻纤制品有连续 纤维毡、网格布及单向布等,制造异形断面制品时, 可先将玻纤制成预制件,然后放入模内。
网格布
填料
增加制品的刚度、厚度、降低成本。 填料的种类要根据使用要求选择,一般为石英 砂、石英粉、辉绿岩粉等。
石英粉
离心制管的加料方法与缠绕成型工艺不同, 加料系统是把树脂、纤维和填料的供料装置,统 一安装在可往复运动的小车上。
离心浇铸工艺流程

离心浇铸工艺流程
《离心浇铸工艺流程》
离心浇铸是一种常见的金属加工工艺,它以其高精度、高质量和高效率而广泛应用于航空航天、汽车制造、船舶建造等领域。
下面将介绍离心浇铸的工艺流程。
首先,准备模具。
模具一般由两部分组成,上模和下模。
上模用于形成铸件的外形,下模用于支撑上模和固定浇口。
在准备模具的过程中,需要注意模具的表面光洁度和精度,以确保最终铸件的质量。
然后,准备熔炼金属。
通常情况下,铸件的材料是金属,需要将金属熔化并倒入模具中。
在这一步骤中,需要控制熔炼金属的温度和化学成分,以确保最终铸件的机械性能和化学性能符合要求。
接下来,进行离心浇铸。
在离心浇铸过程中,模具被放置在旋转的离心机上,并且铸件在离心力的作用下,熔化金属被迫填充模具中,这样可以确保铸件内部没有气泡并且表面光滑。
最后,冷却和处理。
待熔炼金属填满整个模具后,需要等待一段时间让金属冷却凝固。
然后,可以将铸件从模具中取出,并进行后续的热处理或机械加工。
总的来说,离心浇铸工艺流程具有简单、高效的特点,并且可
以生产出高精度、高质量的铸件。
随着现代制造技术的不断发展,离心浇铸工艺将在未来得到更广泛的应用。
离心浇铸工艺
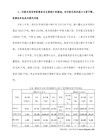
离心铸造时,浇注工艺有其本身的特点,首先由于铸件的内表面是自由表面,而铸件厚度的控制全由所浇注液体金属的数量决定,故离心铸造浇注时,对所浇注金属的定量要求较高。此外由于浇注是在铸型旋转情况下进行的为了尽可能地消除金属飞溅的现象,要很好控制金属进入铸型时的方向。
液体金属的定量有重量法、容积法和定自由表面高度(液体金属厚度)法等。容积法用一定体积的浇包控制所浇注液体金属的数量,此法较简便,但受金属的温度,熔渣等影响,定量不太准确,在生产中用的较多。
5)铸件易产生偏析,铸件内表面较粗糙。内表面尺寸不易控制。
离心铸造的第一个专利是在1809年由英国人爱尔恰尔特(Erchardt)提出的,直到二十世纪初期这一方法在生产方面才逐步地被采用。我国在三十年代也开始利用离心管、筒类铸件如铁管、铜套、缸套、双金属钢背铜套等方面,离心铸造几乎是一种主要的方法;此外在耐热钢辊道、一些特殊钢无缝纲管的毛坯,造纸机干燥滚筒等生产方面,离心铸造法也用得很有成效。目前已制出高度机械化、自动化的离心铸造机,已建起大量生产的机械化离心铸管车间。
离心浇铸
1 概述
离心铸造是将液体金属浇入旋转的铸型中,使液体金属在离心力的作用下充填铸型和凝固形成的一种铸造方法。
为实现上述工艺过程,必须采用离心铸造机创造使铸旋转的条件。根据铸型旋转轴在空间位置的不同,常用的有立式离心铸造机和卧式离心铸造机两种类型。
立式离心铸造机上的铸型是绕垂直轴旋转的(图1),它主要用来生产高度小于直径的圆环类铸件,有时也可用此种离心铸造机浇注异形铸件。
几乎一切铸造合金都可用于离心铸造法生产,离心铸件的最小内径可达8毫米,最大直径可达3m,铸件的最大长度可达8m,离心铸件的重量范围为几牛至几万牛(零点几公斤至十多吨)。
玻璃钢离心浇铸工艺流程
玻璃钢离心浇铸工艺流程玻璃钢离心浇铸可是个很有趣的工艺呢!今天就来给大家好好唠唠这个工艺流程。
一、准备工作。
这就像是做饭之前得把食材都准备好一样。
我们得先有个模具,这个模具得符合我们要做的玻璃钢制品的形状。
模具的质量可不能马虎,要是它歪歪扭扭的,那做出来的产品肯定也不好看。
然后呢,还得准备好玻璃纤维和树脂。
玻璃纤维就像是盖房子的钢筋,是起到增强作用的。
树脂就像是水泥,能把这些“钢筋”粘在一起。
这两种材料的质量也得把关好,就像挑水果得挑新鲜的一样。
二、玻璃纤维的铺放。
把模具准备好之后,就开始铺玻璃纤维啦。
这可不能乱铺哦,得按照一定的方向和层数来铺。
就像给娃娃做衣服,布料得裁剪好、铺平整才能好看。
玻璃纤维要铺得均匀,不能这儿厚那儿薄的。
要是有的地方玻璃纤维太多,那这个地方就会太硬;要是太少呢,又会不结实。
铺玻璃纤维的时候,感觉就像是在给模具穿上一件特制的衣服,一层一层地,慢慢地把它包裹起来。
三、树脂的灌注。
玻璃纤维铺好之后,就轮到树脂登场啦。
树脂要缓缓地灌注到铺好玻璃纤维的模具里。
这时候得小心点,就像给花瓶里插花一样,不能太粗鲁,不然树脂到处流,就会搞得一团糟。
灌注的时候要看着树脂慢慢地填满那些缝隙,让玻璃纤维都能被树脂充分地浸润。
这就像是给玻璃纤维洗个树脂澡,让它们都舒舒服服地粘在一起。
四、离心浇铸。
这可是个关键的步骤呢。
把灌注好树脂的模具放到离心机上。
一开机,模具就开始高速旋转起来。
这时候,树脂在离心力的作用下,就会均匀地分布在模具的内壁上。
感觉就像坐过山车一样,树脂和玻璃纤维在模具里转啊转。
这个过程中,树脂里的气泡也会被挤出来,这样做出来的玻璃钢制品就会很密实,不会有那种坑坑洼洼的小气泡,就像皮肤光滑的小宝宝一样。
五、固化。
转完之后,就等着它固化啦。
这个过程就像是面包在烤箱里慢慢烤熟一样。
树脂在一定的温度和时间下会变硬,和玻璃纤维牢牢地结合在一起。
这个时候可不能着急,得给它足够的时间来完成这个转变。
离心铸造工艺流程
离心铸造工艺流程离心铸造是常见的一种金属件制造工艺,适用于生产外形复杂、尺寸精度要求较高的零件。
下面将介绍离心铸造的工艺流程。
离心铸造工艺流程主要包括模具制备、熔炼金属、浇注、冷却、脱模和后处理等步骤。
首先是模具制备。
根据所需铸造零件的形状和尺寸,制作相应的模具。
一般情况下,模具制备需要非常精细的加工和装配,确保模具能够精确地复制原型零件的形状。
接着是熔炼金属。
将金属原料放入熔炉中进行加热,使其达到熔点并保持在液态。
熔炼金属的温度和成分要根据具体材料要求进行控制,以确保最终产品的质量。
然后是浇注。
将熔化的金属倒入模具中,通常是通过一个喷嘴或者浇口进行浇注。
在浇注过程中,金属液体会受到离心力的作用,沿着模具的壁厚分布均匀,确保铸件的尺寸一致性和形状精度。
接着是冷却。
浇注完成后,模具会慢慢冷却。
冷却过程中,金属液体会逐渐凝固并形成固态金属零件。
冷却时间会根据不同材料的性质和零件尺寸来确定,以确保零件能够充分凝固而不产生缺陷。
然后是脱模。
当金属零件完全冷却后,可以将模具打开,取出铸件。
脱模时需要小心操作,以防止损坏铸件表面和内部结构。
最后是后处理。
脱模后的铸件通常会有一些表面缺陷,如凸起、毛刺等。
这时需要进行清理和修整,使零件表面光滑。
另外,还需要进行热处理、机加工等后续工艺,以满足零件的使用要求。
总的来说,离心铸造工艺流程相对复杂,包含多个关键步骤。
每个步骤都需要严格控制和合理操作,以确保最终产品的质量。
离心铸造作为一种重要的金属件制造工艺,广泛应用于汽车、航空航天、能源等领域,为现代工业的发展做出了重要贡献。
离心铸造原理
离心铸造原理
离心铸造是一种利用离心力将金属液体注入模具进行凝固成型的铸造工艺。
它是一种高效、高精度的铸造方法,被广泛应用于航空航天、汽车、船舶等领域。
离心铸造原理是指利用离心力将金属液体从中心向外辐射,使金属液体在模具内壁上形成均匀的凝固层,从而获得高质量的铸件。
在离心铸造过程中,首先需要准备好模具和金属液体。
模具通常由耐高温材料制成,能够承受金属液体的高温。
金属液体则需要经过熔炼和脱气处理,以确保其纯净度和流动性。
一旦准备就绪,金属液体就会被注入到旋转的模具中。
当金属液体被注入到旋转的模具中时,离心力会使金属液体向外辐射,形成一个旋转的液体层。
由于离心力的作用,金属液体在模具内壁上形成了一个均匀的凝固层。
这种均匀的凝固层能够确保铸件的密度和结构均匀,从而提高了铸件的质量和机械性能。
除了提高铸件的质量外,离心铸造还可以实现一次成型,减少了后续加工的工序。
这不仅提高了生产效率,还降低了生产成本。
因此,离心铸造在现代工业生产中具有重要的地位和作用。
总的来说,离心铸造原理是利用离心力将金属液体注入模具进行凝固成型的铸造工艺。
它能够提高铸件的质量和机械性能,同时也能够提高生产效率和降低生产成本。
因此,离心铸造在现代工业生产中具有广阔的应用前景。
锌合金离心浇铸转速和离心力
锌合金离心浇铸转速和离心力一、引言离心浇铸是一种常见的金属成型工艺,其中锌合金离心浇铸是一种重要的应用。
在锌合金离心浇铸过程中,转速和离心力是影响产品质量的关键因素之一。
二、锌合金离心浇铸工艺1. 工艺流程锌合金离心浇铸工艺流程包括模具制作、熔炼、浇注、冷却、脱模和后处理。
其中,模具制作和后处理是关键环节。
2. 工艺参数在锌合金离心浇铸过程中,影响产品质量的主要参数包括转速、离心力、温度和压力等。
其中,转速和离心力是最为重要的两个参数。
三、转速对产品质量的影响1. 转速与产品密度的关系转速对于锌合金离心浇铸产品密度有着直接影响。
当转速增加时,由于惯性力增大,液态合金中央部分向外迁移,从而导致外围部分凝固更快,使得产品密度增加。
2. 转速与表面质量的关系转速对于锌合金离心浇铸表面质量也有着重要影响。
当转速过高时,液态合金在模具内部形成的压力会增大,从而导致表面出现疏松和缺陷。
因此,在锌合金离心浇铸过程中,需要根据具体工艺要求选择适当的转速。
四、离心力对产品质量的影响1. 离心力与产品密度的关系离心力对于锌合金离心浇铸产品密度同样有着直接影响。
当离心力增加时,液态合金中央部分向外迁移的速度也会增加,从而导致外围部分凝固更快,使得产品密度增加。
2. 离心力与表面质量的关系离心力对于锌合金离心浇铸表面质量同样有着重要影响。
当离心力过高时,液态合金在模具内部形成的压力会增大,从而导致表面出现疏松和缺陷。
因此,在锌合金离心浇铸过程中,需要根据具体工艺要求选择适当的离心力。
五、结论在锌合金离心浇铸过程中,转速和离心力是影响产品质量的关键因素之一。
合理选择适当的转速和离心力可以保证产品密度和表面质量,提高产品的质量和性能。
- 1、下载文档前请自行甄别文档内容的完整性,平台不提供额外的编辑、内容补充、找答案等附加服务。
- 2、"仅部分预览"的文档,不可在线预览部分如存在完整性等问题,可反馈申请退款(可完整预览的文档不适用该条件!)。
- 3、如文档侵犯您的权益,请联系客服反馈,我们会尽快为您处理(人工客服工作时间:9:00-18:30)。
离心铸造是将液体金属浇入旋转的铸型中,使液体金属在离心力的作用下充填铸型和凝固形成的一种铸造方法。
为实现上述工艺过程,必须采用离心铸造机创造使铸旋转的条件。
根据铸型旋转轴在空间位置的不同,常用的有立式离心铸造机和卧式离心铸造机两种类型。
立式离心铸造机上的铸型是绕垂直轴旋转的,它主要用来生产高度小于直径的圆环类铸件,有时也可用此种离心铸造机浇注异形铸件。
卧式离心铸造机的铸型是绕水平轴旋转的(图2),它主要用来生产长度大于直径的套类和管类铸件。
由于离心铸造时,液体金属是在旋转情况下充填铸型并进行凝固的,因而离心铸造便具有下述的一些特点:
1)液体金属能在铸型中形成中空的圆柱形自由表面,这样便可不用型芯就能铸出中空的铸件,大大简化了套筒,管类铸件的生产过程,使铸造工艺大大简化,生产率高、成本低;
2)由于旋转时液体金属所产生的离心力作用,离心铸造工艺可提高金属充镇铸型的能力,因此一些流动性较差的合金和薄壁铸件都可用离心铸造法生产;
3)由于离心力的作用,改善了补缩条件,气体和非金属夹杂也易于自液体金属中排出,因此离心铸件的组织较致密,缩孔(缩松)、气孔、夹杂等缺陷较少,力学性能好;
4)消除或大大节省浇注系统和冒口方面的金属消耗,金属利用率高;
5)离心铸造的铸件易产生偏析,不宜铸造密度偏析倾向大的合金;而且内孔尺寸不精确,内表面粗糙,加工余量大;不适于单件、小批量生产,目前,离心铸造已广泛用于制造铸铁管、气缸套铜套、双金属轴承、特殊的无缝管坯、造纸机滚筒等;
6)便于生产双金属铸件,例如钢套镶铜轴承等,其结合面牢固,又节省铜料,降低成本。
离心铸造的第一个专利是在1809年由英国人爱尔恰尔特(Erchardt)提出的,直到二十世纪初期这一方法在生产方面才逐步地被采用。
我国在三十年代也开始利用离心管、筒类铸件如铁管、铜套、缸套、双金属钢背铜套等方面,离心铸造几乎是一种主要的方法;此外在耐热钢辊道、一些特殊钢无缝纲管的毛坯,
造纸机干燥滚筒等生产方面,离心铸造法也用得很有成效。
目前已制出高度机械化、自动化的离心铸造机,已建起大量生产的机械化离心铸管车间。
几乎一切铸造合金都可用于离心铸造法生产,离心铸件的最小内径可达8毫米,最大直径可达3m,铸件的最大长度可达8m,离心铸件的重量范围为几牛至几万牛(零点几公斤至十多吨)。
离心铸造工艺
1)离心铸型转速的选择
选择离心铸型的转速时,主要应考虑两个问题:(1)离心铸型的转速起码应保证液体金属在进入铸型后立刻能形成圆筒彩,绕轴线旋转;(2)充分利用离心力的作用,保证得到良好的铸件内部质量,避免铸件内产生缩孔、缩松、夹杂和气孔。
采用砂型离心铸造时,也要注意忽使液体金属对型壁具有太大的离心压力而引起铸件粘砂胀砂等的缺陷。
离心铸造转速计算参考公式:
1. 根据综合系数计算铸型转速:
n: 转速(r/min)
C:综合系数,由铸件合金种类、浇注速度、铸型种类等因素确定。
R:铸件内径(m)
2. 非金属铸型离心铸造:
n: 转速(r/min)
P:非金属铸型能承受的最大离心压力(Mpa)
ρ:合金密度(Kg/m3)
R、r:铸件外径和内径(m)
2)离心铸造用铸型
离心铸造时使用的铸型有两大类,即金属型和非金属型。
非金属型可为砂型、壳型、熔模壳型等。
由于金属型在大量生产、成批生产时具有一系列的优点,所以在离心铸造时广泛地采用金属型。
卧式悬臂离心铸造机上的金属型按其主体的结构特点可分为单层金属型和双层金属型两种。
在单层金属型中,型壁由一层组成,单层金属型结构简单,操作方便,但它损坏后需要制作新的铸型才能开始生产,在此铸型中只能浇注单一外径尺寸的铸件。
而在双层金属型中,型壁由两层组成,铸件在内型表面成形。
双层金属型结构虽复杂性,但只要改变内型的工作表面尺寸就可浇注多种外径尺寸的离心铸件。
长期工作后,只需更换结构较简单的内型就可把旧铸型当作新的铸型使用。
3)涂料
金属型离心铸造时,常需在金属型的工作表面喷刷涂料。
对离心铸造金属型用涂料的要求与一般金属型铸造时相同。
为防止铸件与金属型粘合和铸铁件产生白口,在离心金属型上的涂料层有时较厚。
离心铸造用涂料大多用水作载体。
有时也用于态涂料,如石墨粉,以使铸件能较易地自型中取出。
喷刷涂料时应注意控制金属型的温度。
在生产大型铸件时,如果铸型本身的热量不足以把涂料洪干,可以把铸型放在加热炉中加热,并保持铸型的工作温度,等待浇注。
生产小型铸件时,尤其是采用悬臂离心铸造机生产时,希望尽可能利用铸型本身的热量洪干涂料,等待浇注。
4)浇注
离心铸造时,浇注工艺有其本身的特点,首先由于铸件的内表面是自由表面,而铸件厚度的控制全由所浇注液体金属的数量决定,故离心铸造浇注时,对所浇注金属的定量要求较高。
此外由于浇注是在铸型旋转情况下进行的为了尽可能地消除金属飞溅的现象,要很好控制金属进入铸型时的方向。
液体金属的定量有重量法、容积法和定自由表面高度(液体金属厚度)法等。
容积法用一定体积的浇包控制所浇注液体金属的数量,此法较简便,但受金属的温度,熔渣等影响,定量不太准确,在生产中用的较多。
为尽可能地消除浇注时金属的飞溅现象,要控制好液体金属进入铸型时的流动方向。