机械零部件可靠性设计方法研究
机械设计中的产品可靠性分析与评估

机械设计中的产品可靠性分析与评估在当今竞争激烈的市场环境中,机械产品的可靠性已成为企业赢得市场份额和用户信任的关键因素。
可靠性不仅关系到产品的质量和性能,更直接影响着用户的满意度和企业的声誉。
因此,在机械设计过程中,对产品可靠性进行深入的分析与评估具有重要的意义。
一、产品可靠性的概念与重要性产品可靠性,简单来说,是指产品在规定的条件下和规定的时间内,完成规定功能的能力。
这包括了产品在使用过程中的稳定性、耐久性、无故障工作时间等多个方面。
一个可靠的机械产品,能够在各种复杂的工作环境和使用条件下,持续稳定地运行,减少故障和维修的次数,从而为用户提供更好的服务,同时也降低了企业的售后成本。
对于企业而言,产品可靠性的重要性不言而喻。
首先,高可靠性的产品能够提升企业的市场竞争力。
在消费者选择产品时,往往更倾向于那些质量可靠、故障少的品牌。
其次,可靠的产品有助于降低生产成本。
虽然在提高可靠性的过程中可能需要增加前期的研发投入,但由于减少了后期的维修和更换成本,总体成本反而会降低。
再者,良好的可靠性能够增强企业的声誉和品牌形象,促进企业的长期发展。
二、影响产品可靠性的因素在机械设计中,有众多因素会影响产品的可靠性。
设计方面,不合理的结构设计、选用了不合适的材料、零部件之间的匹配度不足等,都可能导致产品在使用过程中出现故障。
制造工艺的优劣也直接关系到产品的质量和可靠性。
例如,加工精度不够、装配不当等都会影响产品的性能和寿命。
此外,使用环境也是一个重要的影响因素。
机械产品在高温、高湿、高压、强腐蚀等恶劣环境下工作,其可靠性会受到极大的挑战。
而用户的操作和维护方式同样不可忽视。
不正确的操作方法、不及时的维护保养,都可能加速产品的损坏。
三、产品可靠性分析方法为了准确评估机械产品的可靠性,需要采用一系列的分析方法。
故障模式与影响分析(FMEA)是一种常用的方法。
它通过对产品可能出现的故障模式进行分析,评估每种故障模式的影响程度和发生概率,从而找出潜在的薄弱环节,并采取相应的改进措施。
机械零部件的可靠性优化设计探究

机械零部件的可靠性优化设计探究1 机械零部件可靠性设计的作用可靠性设计是指以形成产品可靠性为目标的设计技术,又称概率设计,将外载荷、承受能力、零部件尺寸等各设计参数看作随机性的变量,并服从一定的分布,应用数理统计、概率论与力学理论,综合所有随机因素的影响,得出避免零部件出现破坏概率的相关公式,由此形成与实际情况相符合的零部件设计,确保零部件的可靠性和结构安全,控制失效的发生率在可接受的范围内。
概率设计法的作用体现在两个问题的解决。
首先,分析计算根据设计而进行,确定了产品的可靠度;其次,根据任务提出的可靠性指标,确定零部件的参数,从而帮助设计者和生产者对零部件可靠性有清晰明确的了解。
2 机械零部件可靠性优化设计现状目前,主要使用可靠性优化设计方法还是传统的设计方法。
这种方法在设计机械零件时,一般都将零件的强度、应力和安全系数都是当作是单值的,将安全系数与根据实际使用经验规定的某一数值相比较,如果前者大于后者,就说明零件是安全的。
但是由于没有考虑到各参数的随机性,把各个设计参数看成是单一的确定值,因此并不能预测零部件可靠运行的概率,很难与客观实际的最优化方案相符,设计人员也不好把握其设计产品的可靠性。
以概率论和数理统计等作为工具的可靠性设计方法,避开了主观的人为因素在设计过程中的影响,外界条件变化得到了从整体上的把握,设计结果更贴近客观情况。
可靠性设计广泛应用在机械零部件可靠性设计的各种问题中,更科学地解决了许多繁琐的传统设计方法有心无力的问题。
3 机械零部件可靠性设计方法机械零部件可靠性的设计不仅需要的是与时俱进、把脉时代的创新精神,更需要把握零部件质量保证和可靠性优化设计的科学方法。
机械零部件可靠性设计是基于传统机械设计以及其他的优化设计方法进行的,由于机械产品有着千差万别的功能和结构相异之处,因此,机械零部件可靠性的设计方法以及优化方式的选择需要因地制宜。
3.1 权衡与耐环境设计权衡设计是对可靠性、质量、体积、成本等要素进行综合衡量后,制定出最佳方案的设计方法。
机械工程的可靠性优化设计分析
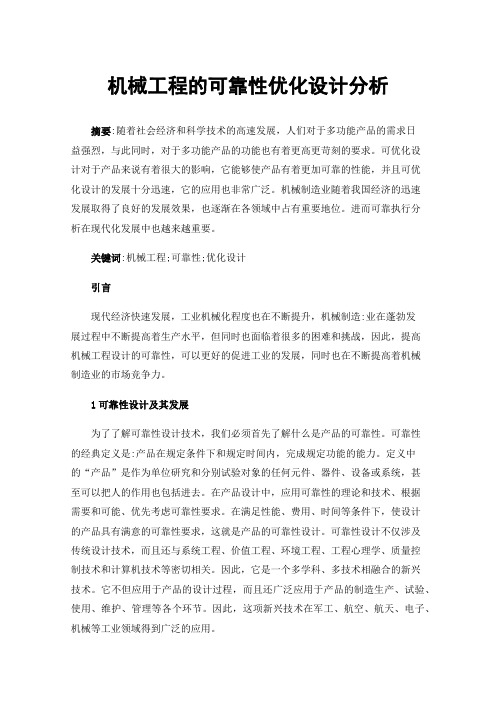
机械工程的可靠性优化设计分析摘要:随着社会经济和科学技术的高速发展,人们对于多功能产品的需求日益强烈,与此同时,对于多功能产品的功能也有着更高更苛刻的要求。
可优化设计对于产品来说有着很大的影响,它能够使产品有着更加可靠的性能,并且可优化设计的发展十分迅速,它的应用也非常广泛。
机械制造业随着我国经济的迅速发展取得了良好的发展效果,也逐渐在各领域中占有重要地位。
进而可靠执行分析在现代化发展中也越来越重要。
关键词:机械工程;可靠性;优化设计引言现代经济快速发展,工业机械化程度也在不断提升,机械制造:业在蓬勃发展过程中不断提高着生产水平,但同时也面临着很多的困难和挑战,因此,提高机械工程设计的可靠性,可以更好的促进工业的发展,同时也在不断提高着机械制造业的市场竞争力。
1可靠性设计及其发展为了了解可靠性设计技术,我们必须首先了解什么是产品的可靠性。
可靠性的经典定义是:产品在规定条件下和规定时间内,完成规定功能的能力。
定义中的“产品”是作为单位研究和分别试验对象的任何元件、器件、设备或系统,甚至可以把人的作用也包括进去。
在产品设计中,应用可靠性的理论和技术、根据需要和可能、优先考虑可靠性要求。
在满足性能、费用、时间等条件下,使设计的产品具有满意的可靠性要求,这就是产品的可靠性设计。
可靠性设计不仅涉及传统设计技术,而且还与系统工程、价值工程、环境工程、工程心理学、质量控制技术和计算机技术等密切相关。
因此,它是一个多学科、多技术相融合的新兴技术。
它不但应用于产品的设计过程,而且还广泛应用于产品的制造生产、试验、使用、维护、管理等各个环节。
因此,这项新兴技术在军工、航空、航天、电子、机械等工业领域得到广泛的应用。
2机械制造工艺可靠性的分析方法2.1管理工艺环节一个行业能否有效运行,关键点是不能离开其合理性与高效性,从机械制造行业的角度探寻问题,我们能够了解正常的运行也要讲求科学与合理,通过合理化的经营管理,能提升整个工艺流程。
机械零部件 的可靠性设计分析

机械零部件的可靠性设计分析摘要:机械零部件是机械设备的运行基础,其质量、性能等代表着机械设备的工作精度与生命周期。
为此,应定期对机械零部件进行维修养护,通过参数基准检测零部件动态化运行模式,以提升零部件的可靠性。
文章对机械零部件的可靠性进行论述,并对机械零部件的可靠性设计进行研究。
关键词:机械零部件;可靠性设计;分析对于机械零部件的质量来说,它的可靠性是十分重要的,它可以保证机械的使用寿命以及质量,是我国机械加工时应该注意的一项。
1 机械零部件的可靠性概述零部件在机械设备中起到负载、部件联动、动力传输的重要作用,在设备长时间工作状态下,零部件易发生是失效现象,令机械设备产生故障。
当零部件发生损毁现象时,例如老化、堵塞、松脱等,将增加联动部件的运行压力,提升零部件故障检测的难度。
此外,机械设备加工工艺、工作原理存在差异性,在零部件基准参数方面难以进行统一,只有少部分密封件、阀门、泵体等零部件实现通用化、标准化。
为此,在对零部件的可靠性进行设计时,零部件的荷载分布能力、材料强度等则应作为主要突破点。
2 机械零部件的可靠性设计分析2.1 可靠性优化设计可靠性优化设计是以可靠性为前提而开展的更完善的设计工作,不仅可以满足产品在使用过程中的可靠性,还将产品的尺寸、成本、质量、体积与安全性能等得到进一步的改善提高,进而保障结构的预测工作和实际工作性能更契合,能够把可靠性分析理论和数学规划方法合理地融合到一起。
在对各参数开始可靠性优化设计时,首先把机械零部件的可靠度当成优化的目标函数,把零部件的部分标准如成本、质量、体积、尺寸最大限度地缩小,再把强度、刚度、稳定性等设计标准作为约束基础设立可靠性优化设计数学模型,依据模型的规模、性能、复杂程度等确定适宜的优化方式,最后得出最优设计变量。
2.2 可靠性灵敏度设计可靠性灵敏度设计指的是确定机械零部件中的各个参数的变化情况对机械零部件时效的影响程度。
通过灵敏度设计,便于我们找到那些对可靠性设计敏感性较大的参数,后续对这些参数进一步分析并重新设计。
机械制造工艺过程可靠性分析
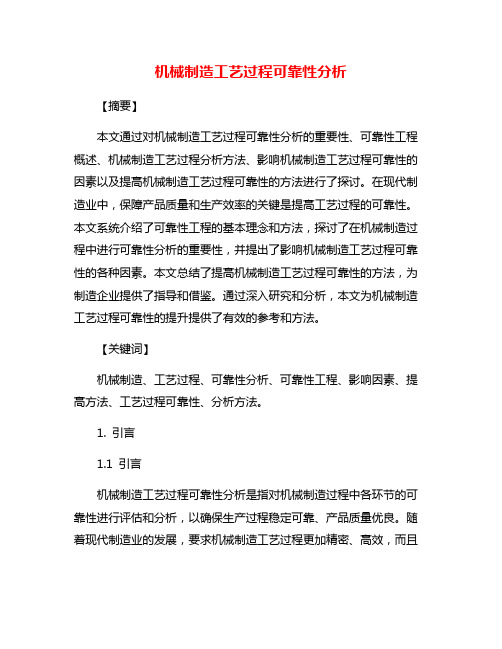
机械制造工艺过程可靠性分析【摘要】本文通过对机械制造工艺过程可靠性分析的重要性、可靠性工程概述、机械制造工艺过程分析方法、影响机械制造工艺过程可靠性的因素以及提高机械制造工艺过程可靠性的方法进行了探讨。
在现代制造业中,保障产品质量和生产效率的关键是提高工艺过程的可靠性。
本文系统介绍了可靠性工程的基本理念和方法,探讨了在机械制造过程中进行可靠性分析的重要性,并提出了影响机械制造工艺过程可靠性的各种因素。
本文总结了提高机械制造工艺过程可靠性的方法,为制造企业提供了指导和借鉴。
通过深入研究和分析,本文为机械制造工艺过程可靠性的提升提供了有效的参考和方法。
【关键词】机械制造、工艺过程、可靠性分析、可靠性工程、影响因素、提高方法、工艺过程可靠性、分析方法。
1. 引言1.1 引言机械制造工艺过程可靠性分析是指对机械制造过程中各环节的可靠性进行评估和分析,以确保生产过程稳定可靠、产品质量优良。
随着现代制造业的发展,要求机械制造工艺过程更加精密、高效,而且产品的质量也必须得到高度保障。
对机械制造工艺过程的可靠性进行分析变得至关重要。
在机械制造领域,任何一处疏漏都可能导致产品质量不稳定,甚至出现严重事故。
通过对机械制造工艺过程可靠性的分析,我们可以及时发现潜在的问题点,采取有效的措施进行改进,确保生产过程稳定、产品质量可靠。
本文将从可靠性工程的角度出发,介绍机械制造工艺过程可靠性分析的重要性、可靠性工程的概述、机械制造工艺过程分析方法、影响机械制造工艺过程可靠性的因素以及提高机械制造工艺过程可靠性的方法。
希望通过本文的介绍,读者能够深入了解机械制造工艺过程可靠性分析的重要性,为提升制造业的发展质量贡献自己的力量。
2. 正文2.1 机械制造工艺过程可靠性分析的重要性机械制造工艺过程可靠性分析的重要性在于确保产品的质量和性能达到客户要求,并提高生产效率和降低生产成本。
通过对机械制造工艺过程的可靠性进行分析,可以识别潜在的问题和风险,及时进行调整和改进,确保产品的稳定性和一致性。
机械可靠性设计系统可靠性设计
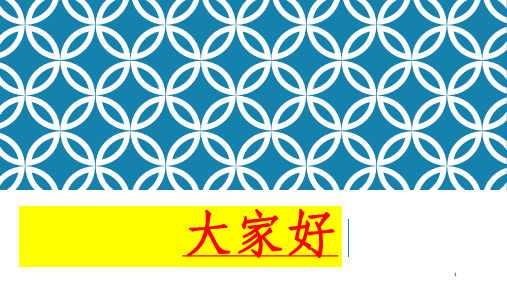
• 1 表决系统(工作储备系统)
55
1)2/3表决系统
56
57
58
例4-4
有一架装有3台发动机的飞机,它至少需要 2台发动机正常才能飞行,设飞机发动机的平 均无故障工作时间MTBF=2000h,试估计工作 时间为10h和100h的飞机可靠度。 解:n=3,k=2
RS (t) 3R 2 2R 3 3e 2t 2e 3t
73
1)冷储备系统 (1)两个单元(一个单元备用)的系统
74
75
(2)n个单元(n-1个单元备用)的系统
76
77
(3)多个单元工作的系统
Ri e t
RS(t )
e
Lt
1
Lt
(Lt )2 2!
(Lt )3 3!
(Lt )n n!
78
(4)考虑检测器和开关可靠性的系统
Rs(t ) e 1t
84
85
86
87
88
89
2 全概率公式法(分解法)
90
91
92
3 检出支路法(路径枚举法)
93
94
95
4.3 系统可靠性预计
1 可靠性预计的目的
可靠性预计是指产品的设计与研制阶段,根据产品的功能 结构、工作环境以及组成产品单元的相互关系和可靠性数据, 推测产品可能达到的可靠性指标。可靠性预计是一个由局部 到整体、由小到大、由下到上的过程,是一个综合的过程。
52
• Rs1=R1R2R3 Rs2=R4R5 Rs3=1-(1-Rs1)(1Rs2) Rs4=1-(1-R6)(1R7) Rs=Rs3Rs4R8
53
• 储备模型 当采用串联模型的设计不能满足设计指标要求时,
FMEA在机械设计中的可靠性分析

FMEA在机械设计中的可靠性分析简介在机械设计领域中,可靠性是一个至关重要的指标,决定了产品在使用过程中的稳定性和安全性。
为了评估和提高机械产品的可靠性,工程师们通常会采用FMEA(Failure Mode and Effects Analysis)分析方法。
什么是FMEAFMEA是一种系统性的分析方法,旨在识别产品或系统可能存在的潜在故障模式和故障对系统功能的影响。
通过对潜在故障模式的识别和评估,可以帮助设计团队在设计阶段识别和消除设计缺陷,从而提高产品的可靠性。
FMEA的工作原理FMEA分析通常分为三个关键步骤:识别潜在故障模式、评估潜在故障的影响和严重性、确定并实施改进措施。
在识别潜在故障模式阶段,团队会收集和整理可能的故障模式,包括设备失效、材料损坏、操作错误等。
接着进行评估,根据潜在故障的影响和严重性对它们进行排序,并确定优先处理的故障。
最后,设计团队根据评估结果提出改进和预防措施,避免潜在故障的发生。
FMEA在机械设计中的应用在机械设计中,FMEA的应用可以帮助设计团队避免或减少设计缺陷,降低产品的故障率和维修成本。
通过FMEA分析,设计团队可以识别潜在的故障模式和问题,及早进行改进,确保产品在生产和使用过程中的可靠性和安全性。
例如,在设计一个机械零部件时,可以通过FMEA分析识别可能的故障模式,如材料疲劳、装配不当等,从而改进设计和工艺,提高产品的可靠性。
结论FMEA作为一种重要的分析方法,在机械设计中扮演着关键的角色。
通过FMEA分析,设计团队可以及早发现并解决潜在的故障问题,提高产品的可靠性和安全性。
因此,在机械设计过程中,设计团队应该充分利用FMEA这一工具,从而设计出高质量、可靠性强的机械产品。
机械设计中的可靠性分析
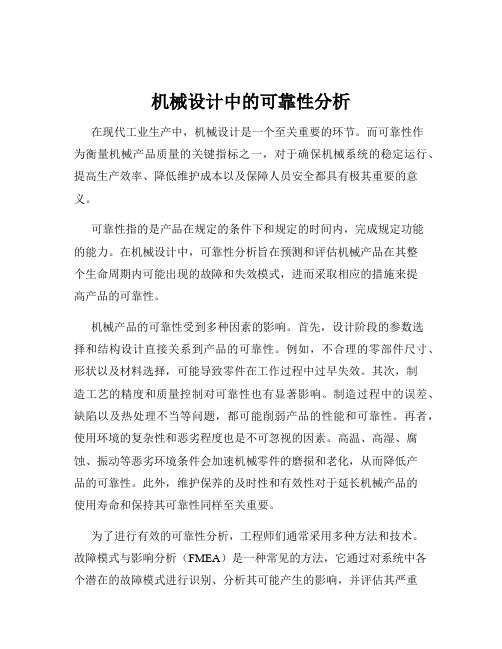
机械设计中的可靠性分析在现代工业生产中,机械设计是一个至关重要的环节。
而可靠性作为衡量机械产品质量的关键指标之一,对于确保机械系统的稳定运行、提高生产效率、降低维护成本以及保障人员安全都具有极其重要的意义。
可靠性指的是产品在规定的条件下和规定的时间内,完成规定功能的能力。
在机械设计中,可靠性分析旨在预测和评估机械产品在其整个生命周期内可能出现的故障和失效模式,进而采取相应的措施来提高产品的可靠性。
机械产品的可靠性受到多种因素的影响。
首先,设计阶段的参数选择和结构设计直接关系到产品的可靠性。
例如,不合理的零部件尺寸、形状以及材料选择,可能导致零件在工作过程中过早失效。
其次,制造工艺的精度和质量控制对可靠性也有显著影响。
制造过程中的误差、缺陷以及热处理不当等问题,都可能削弱产品的性能和可靠性。
再者,使用环境的复杂性和恶劣程度也是不可忽视的因素。
高温、高湿、腐蚀、振动等恶劣环境条件会加速机械零件的磨损和老化,从而降低产品的可靠性。
此外,维护保养的及时性和有效性对于延长机械产品的使用寿命和保持其可靠性同样至关重要。
为了进行有效的可靠性分析,工程师们通常采用多种方法和技术。
故障模式与影响分析(FMEA)是一种常见的方法,它通过对系统中各个潜在的故障模式进行识别、分析其可能产生的影响,并评估其严重程度、发生概率和检测难度,从而为设计改进提供依据。
另一种常用的方法是故障树分析(FTA),它以系统的故障为顶事件,通过逻辑推理逐步找出导致故障发生的各种原因组合,有助于深入了解系统的故障机理和制定针对性的预防措施。
可靠性试验也是可靠性分析的重要手段之一。
通过对机械产品进行模拟实际工作条件的试验,可以直接观察和记录产品的性能变化和故障情况,为可靠性评估提供真实可靠的数据。
此外,基于概率统计的可靠性计算方法,如应力强度干涉模型,可以定量地评估机械零件在给定工作条件下的可靠度。
在机械设计过程中,提高可靠性的措施多种多样。
- 1、下载文档前请自行甄别文档内容的完整性,平台不提供额外的编辑、内容补充、找答案等附加服务。
- 2、"仅部分预览"的文档,不可在线预览部分如存在完整性等问题,可反馈申请退款(可完整预览的文档不适用该条件!)。
- 3、如文档侵犯您的权益,请联系客服反馈,我们会尽快为您处理(人工客服工作时间:9:00-18:30)。
机械零部件可靠性设计方法研究
作者:常秀旺宋晓艳
来源:《汽车世界·车辆工程技术(中)》2019年第07期
摘要:随着经济的发展以及科技的进步,人们对于机械产品的要求也越来越高。
所以机械产品在满足功能性和多样性的同时,更需要满足可靠性的要求,所以本文针对机械产品的可靠性设计方面加以阐述分析。
关键词:机械零件;可靠性;设计
1 机械零部件的可靠性概述
零部件在机械设备中起到负载、部件联动、动力传输的重要作用,在设备长时间工作状态下,零部件易发生是失效现象,令机械设备产生故障。
当零部件发生损毁现象时,例如老化、堵塞、松脱等,将增加联动部件的运行压力,提升零部件故障检测的难度。
此外,机械设备加工工艺、工作原理存在差异性,在零部件基准参数方面难以进行统一,只有少部分密封件、阀门、泵体等零部件实现通用化、标准化。
为此,在对零部件的可靠性进行设计时,零部件的荷载分布能力、材料强度等则应作为主要突破点。
2 可靠性设计方法
可靠性优化设计主要采用的方法有鲁棒设计法和降额设计法。
2.1 鲁棒设计法
鲁棒设计法,是由日本的机械设计师田口玄一首次提出,以统计分析为基础,主要是根据产品的不可用性为用户产生的损失来评判设计的可靠性。
其中的损失指的是流失的可用性与合格可用性的比值,流失的可用性越大则可靠性越差,即产品合格性越差,说明产品质量不合格。
因此,降低流失可用性是关键因素,也是提升产品质量的重点,可以通过严格审核产品设计、加强生产材料质量检验,优化生产加工工艺、强化产品调试试验等提升产品可靠性。
任何一种机械产品都具有不同程度的敏感性,这是因为,机械产品设计功能的实现受到制造因素、使用环境因素以及使用年限等因素的影响。
产品在制造过程中如温度等可变因素有很多,使用过程中环境中的粉尘、烟雾、高温等可变因素也很多,由于产品使用的时间变长,产品的结构会发生变化,某些参数可能会发生改变,系统不可避免地会老化,以上种种因素都会使得产品变得敏感,这种设计方法正是以降低这种敏感性为主要目的。
2.2 降额设计
跟踪机械产品的应用过程,获悉大量的数据,分析表明故障率较低的产品在使用时的实际工作压力都小于额定工作压力。
所以为了获取最佳的降额方法,需要在反复的实践过程中,将产品以及内部的各个零件的平均应力减小,将尽可能多的零件的强度提高。
这样就可以提高机械产品的可靠性。
总而言之,降额设计的宗旨就是首先确保产品的所有零部件实际承受的应力都在额定的范围之内,然后再进一步降低所有零部件的应力以提高产品的质量。
3 机械零部件的可靠性设计研究
3.1 定性、定量设计相融合
定性与定量结合的设计模式,定量设计是针对零部件的可靠性来进行量化分析、通过内部参数的精准核对来完成计算,令可靠性设计实现科学化、精细化,在定性设计的实际应用下,可令可靠性设计偏向于智能化、自动化,以增强零部件在各项工作环节中运行的合理性。
在进行融合设计模式下,应注意以下几点:(1)在对可靠性进行分析时,应依据零部件的性能、工作机理来进行研究,并从质量、效率、生命周期、故障发生率等方面提出定性、定量等方面的需求。
(2)保证可靠性设计与整体设备运行基础参数相符合,机械设备中的零部件在运行过程中,其内控措施是保障设备正常运行的基础,为此,定性设计应建立在成功方案的基础上,以保证可靠性设计的科学性、合理性。
(3)定量设计应对零部件工作过程中的各项数据参数进行采集与整合,并将其作为定量设计体系中的基准参数值,以为可靠性体系的建设提供精准数据保障,进而推动下一步设计程序的开展。
(4)在对零部件可靠性设计时,应利用故障模式分析模型(FMECA)软件来建立拟态化工作模型,找出零部件在联动系统运行中的故障类型以及潜在故障风险,然后设计人员再依据故障参数来制定相应的方案,以降低零部件失效现象产生的几率。
3.2 传统、可靠性设计相融合
在可靠性设计体系尚未成熟之前,大部分机械零部件是以传统设计模式为主,具有直观性、简便性、工作量小等优势,可基本满足机械零部件运转模式,在稳定性方面,也为机械设备提供基本保障。
在科学技术以及检测设备的应用下,对传统的安全系数法设计模式进行优化,通过线性函数来进行概率类算法,通过对零部件工作情况下的数据参数进行采集整合,以概率算法提升故障检测的精准度。
3.3 系统、零部件的可靠性设计相结合
在精细化加工过程中,零部件的精度、衔接度等作为机械设备运行的基准,零部件基准化统一范围较窄,内部结构、功能、形态、工作机理等存在较大的差异性,在进行可靠性设计时,应保证零部件单元故障发生几率在可控范围内。
通过对零部件的连接形式、负载特性、工作环境、润滑因素等进行立体化分析,以得出较为精准的数据参数,进而逐步完善可靠性设计体系。
3.4 使用及维修的可靠性设计
机械产品使用过程对产品的可靠性影响具有举足轻重的地位。
因此,首先,在机械产品设计过程中需要针对产品的特点确定合理的使用年限,明確使用环境要求。
其次,需要针对进行有效维修设计。
通过对产品使用状况的综合评估,明确可以进行维修的内容,可以选择的维修方式,明确零部件可能出现的故障类型,各种故障类型出现的平均周期,设计合理的维修方案。
产品在使用过程中针对实际的环境条件再加以合理性评估与维修方案加以整合,提出切实可行的维修策略,保证整个产品的可靠性满足最优化要求。
4 结束语
文章对机械零部件的可靠性进行分析,并从定性、定量设计相融合,传统、可靠性设计相融合,系统、零部件的可靠性设计相结合等方面,对机械零部件的可靠性设计进行研究。
通过对机械设备在实际工作过程中的参数、性能分析,来对零部件进行定期维护,可有效提升零部件的工作稳定性,进而为机械设备的运行质量提供保障。
参考文献:
[1]闫思宏,陶凤和,贾长治.多失效模式履带车辆传动齿轮可靠性灵敏度分析[J].机械强度,2019,41(03):641-646.
[2]李臻,尚伟.基于Wiener强度退化过程的机械零部件可靠性灵敏度分析[J].组合机床与自动化加工技术,2018(07):22-24+30.
[3]于繁华,刘仁云,张义民等.机械零部件动态可靠性稳健优化设计的群智能算法[J].吉林大学学报(工学版),2017,47(06):1903-1908.
[4]张云博.机械零件可靠性设计理论研究[J].南方农机,2017,48(04):
67.。