套印不准原因分析
柔印套准不准原因与解决办法

柔印套准不准原因与解决办法套印直接关系着印品质量及废品消耗,应运地卷筒纸印刷机来说,套印精度是非常重要的性能指标。
一些机器声称整机套印误差在0.1mm以内,实际上很难达到。
这时我们主要谈谈操作不当造成的套印不准。
1.粘版歪斜大多数柔印机都是采用人工粘版,粘版机的误差、人的视觉误差以及粘地的劲儿使用不匀都会造成粘版歪斜。
所以说粘版是一项非常细致的工作。
2.机器传动不良柔印机是高速运转的机器,在使用一段时间后,传动系各部件之间的顶丝、键、销等会松动,直接影响套印。
所以对机器的定期检修奶重要,可用的盘动皮带或用的摇动压印滚筒,看其是否松动。
最常见的就是压印滚劝面顶紧螺丝松动或键磨损。
在印刷时表现为该组的规线毫无规律地乱跑,尤其是在刚开机张国不稳定时,规矩总无法在一个位置上静止下来,而印刷正常后影响较小。
此外,齿轮的磨损也会民套印不准,应定期检查易磨损齿轮,给齿轮箱加油。
3.张力不合适柔印机的张力控制系统应包括张力检测、张力调节及张国招待等几个部分。
常见的张力控制方式有摩擦盘及分制动器。
如果气压(液压)、电流调节过大或过小均会影响套印。
不同质地的纸和在不同的印刷速度下,张力都有一些变化。
如果用的是手动张力控制仪,则要注意随着纸卷减小,主卷张力也要逐渐减小。
这是由于纸卷越小,它所需的阴力(制动力)越小。
另外,纸张生产或昨卷过程中收卷张国控制不好,也会造成张力不稳定而影响套印的准确性。
正常的纸卷边缘齐平,而张力不好的纸卷边缘不齐或纸芯偏斜。
4.压力过大压力过大,会使印版变形而导致套印不准。
两个专色叠印文字又是阴字时常会发生这种情况。
片面追求墨色实在而加大压力,会使阴字空隙缩小而两色叠印难度加大(对于这种活件,两块印版制版设计时要经过特殊处理;前面先印的版阴字稍大或仅有,称为扩版;后印的阴字稍小些,用于与前一块版套准,称为成型版)。
5.柔印机没有张力调节装置机组式柔印机各色组间若没有张力调节装置,在打版时,会在一段区域内形成局部张力,从而影响与其他色组的套印。
套印不准原因分析

套印不准原因分析套印是印刷品制作中最重要的一个步骤,其中套印精度对印刷品的质量和效果有着决定性的影响。
然而,由于种种原因,有时候套印不准就会发生,导致印刷品质量下降或者无法使用。
下面我们将分析套印不准的一些原因及其解决方法。
防伪印刷中套印不准的原因1. 印刷设备问题在防伪印刷中,套印不准的一个常见原因就是印刷设备问题。
印刷机的调节和维护不当会导致印刷品出现毛边、错位、噪点等问题。
此外,如果套印部件受到损坏或者磨损,也会导致套印不准的情况发生。
这时候需要对印刷设备进行检修,保证其调节和维护的良好性。
2. 印刷版问题印刷版是实现套印的重要组件,若印刷版的制作存在问题,就容易导致套印不准。
比如在制版过程中,如果版面位置、大小、精度等方面出现偏差,则会导致套印不准,需要重新制版。
此外,印刷版的使用寿命很有限,如果版面已经磨损、老化,也会导致套印不准的情况出现。
这时候需要对印刷版进行更换或是加强其使用寿命的管理。
3. 版面设计问题版面设计不良也是导致套印不准的原因之一。
由于版面设计方面的问题,可能会导致版面出现一些不规则的形状或者不对称的情况,从而影响套印的准确性。
解决这个问题的方法就是加强版面设计的风格规范性,确保设计的精度和准确性,并在印刷品制作之前进行严格的软件检测。
4. 印刷基材问题印刷品的基材也是导致套印不准的一个重要原因。
如果基材的表面质量不好,或者表面的平整度不够,也会导致套印不准。
这时候需要在选材和准备工作上进行更加严谨的操作,确保基材的表面质量符合要求,并且进行适当的清洁和处理工作。
总结套印不准是防伪印刷中不可忽略的问题,其涉及到印刷品的质量和效果。
我们需要在印刷设备、印刷版、版面设计和印刷基材等方面进行必要的准备和管理,才能保证套印的准确性和印刷品的质量。
同时,我们也需要根据具体情况采取相应的措施,及时解决套印不准的问题,从而保证印刷品的正常使用和良好的效果。
凹印机套印不准的原因与解决方法

凹印机套印不准的原因与解决方法随着人们对包装的感观和质量要求越来越高。
凹印机以其独特的印刷工艺,产量大,损耗低等优点,成为当今印刷业的主流。
况且,凹印机品种越来越多,整体机器构造和控制系统虽有所差异,但工作原理差异不大,产生的故障有一定的类似。
在生产中出现印品套印不准,影响产品质量是凹印最易的生的问题之一。
一、纸张在印刷中收缩严重,造成套印不准纸张是纸业印刷不可缺少的原辅材料之一。
由于受外界温度、湿度的影响,加上印刷车间温、湿度控制不当,对纸张干湿性产生一定影响。
印刷时,各色组烘干箱温度设置过高,纸张严重收缩,各色组套印识标产生不同程度偏差、跳动,致使套印“露白”,电脑自动跟踪套印系统接收的颜色感光信号强弱不同,未能把套印识标锁定在特定位置,造成套印偏差,影响印品质量。
一般处理方法是保持印刷车间恒温恒湿,适当降低烘干箱温度。
二、压印辊控制压力不平衡,造成跳动,影响套准此现象的出现先排除人为因素(如装卸压印辊时位置未完全吻合,出现偏差)。
造成压印辊两端压力不平衡,气路系统漏气是一个主要因素,造成连接压印辊两端的气缸,因气压不足或两端压力调节不平衡而未能使压印辊在印刷时保持恒定,产生上下跳动,时间长时造成压印辊外周变形,纸张拉力松紧不定,产生套印不准。
处理方法是检查气路系统,确保气路不漏气,并更换漏气的气动元件和更换新的压印辊,使压印辊与印版在印刷时吻合顺畅。
三、跟踪电眼自身问题造成套印不准跟踪电眼是一种感应式光电传感器,其工作原理是通过感应印刷识标上颜色,把反射加的光信号转换成电信号,经模/数转换电路处理,把数字信号送到电脑进行定位跟踪。
如果电眼与印刷识标之间距离太远,电眼聚光点未正对印刷识标,电眼外镜面纸粉覆盖,电眼内发光灯光烧坏,都会造成江信号变弱,或无光信号返回,致使电脑套准系统跟踪缓慢、失灵,未能及时纠正套印偏差,使到印品出现套印不准现象。
一般处理办法是清洁电眼镜面,调节纸与电眼间距离,并正对印刷识标,如果发现电眼发光灯泡烧坏,及时更换,同时仔细观察电脑套印波形,直到印刷色相内十字识标稳定为佳。
胶印常见套印不准故障及解决方法
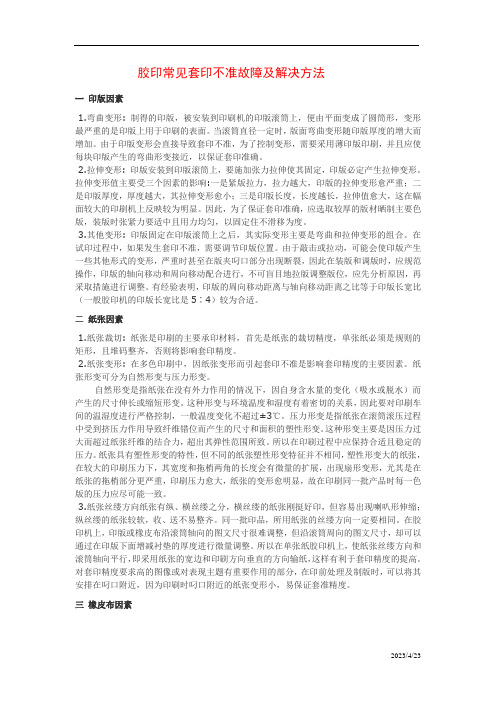
胶印常见套印不准故障及解决方法一印版因素1.弯曲变形: 制得的印版,被安装到印刷机的印版滚筒上,便由平面变成了圆筒形,变形最严重的是印版上用于印刷的表面。
当滚筒直径一定时,版面弯曲变形随印版厚度的增大而增加。
由于印版变形会直接导致套印不准,为了控制变形,需要采用薄印版印刷,并且应使每块印版产生的弯曲形变接近,以保证套印准确。
2.拉伸变形: 印版安装到印版滚筒上,要施加张力拉伸使其固定,印版必定产生拉伸变形。
拉伸变形值主要受三个因素的影响:一是紧版拉力,拉力越大,印版的拉伸变形愈严重;二是印版厚度,厚度越大,其拉伸变形愈小;三是印版长度,长度越长,拉伸值愈大,这在幅面较大的印刷机上反映较为明显。
因此,为了保证套印准确,应选取较厚的版材晒制主要色版,装版时张紧力要适中且用力均匀,以固定住不滑移为度。
3.其他变形: 印版固定在印版滚筒上之后,其实际变形主要是弯曲和拉伸变形的组合。
在试印过程中,如果发生套印不准,需要调节印版位置。
由于敲击或拉动,可能会使印版产生一些其他形式的变形,严重时甚至在版夹叼口部分出现断裂,因此在装版和调版时,应规范操作,印版的轴向移动和周向移动配合进行,不可盲目地拉版调整版位,应先分析原因,再采取措施进行调整。
有经验表明,印版的周向移动距离与轴向移动距离之比等于印版长宽比(一般胶印机的印版长宽比是5∶4)较为合适。
二纸张因素1.纸张裁切: 纸张是印刷的主要承印材料,首先是纸张的裁切精度,单张纸必须是规则的矩形,且堆码整齐,否则将影响套印精度。
2.纸张变形: 在多色印刷中,因纸张变形而引起套印不准是影响套印精度的主要因素。
纸张形变可分为自然形变与压力形变。
自然形变是指纸张在没有外力作用的情况下,因自身含水量的变化(吸水或脱水)而产生的尺寸伸长或缩短形变。
这种形变与环境温度和湿度有着密切的关系,因此要对印刷车间的温湿度进行严格控制,一般温度变化不超过±3℃。
压力形变是指纸张在滚筒滚压过程中受到挤压力作用导致纤维错位而产生的尺寸和面积的塑性形变。
如何解决凹版印刷中套印不准的问题

如何解决凹版印刷中套印不准的问题随着印刷技术日新月异的发展,彩色印刷产品的质量也越来越受到重视,也可以说是一直是广大印刷产品生产企业及印刷机械生产厂家关注着的一个大问题。
而套色印刷(套印)不准是凹版印刷中经常遇到的问题之一,是件比较头疼的事情,有时问题很难找到。
我们认为影响套印不准的主要因素有:印刷材料、印刷材料的物理性能、张力不稳定、印刷机性能、使用者操作方法、印刷环境、凹版适应性等。
套印不准是凹版印刷中经常遇到的问题之一,影响的主要因素有:印刷材料、印刷机性能、操作方法、印刷环境、凹版适性等,出现问题后要在各有关因素中进行排查,分别予以协调解决。
1. 印刷材料对套印不准的影响,由于印刷环境温度、湿度的差异,必然引起承印材料的变形,所以建议在印刷前三天将承印材料放到车间,以提高其温湿适性,防止料卷出汗现象的产生;及时总结不同材料、不同品牌承印物和油墨的印刷适性;承印物本身的不平整、内部张力不均匀、边缘受潮(尤其是光电信号套色端)等,都会造成套印偏差。
2. 张力不稳定是影响套印不准的主要因素,也是最复杂的。
众所周知张力不稳定肯定会导致套印精度的下降。
但张力的不稳定又分为以下几种:(a)在放卷的过程中,放卷的直径是不断变化的,卷径检测的不准确,必然引起料带张力的变化。
(b)张力检测单元,检测到的信号失真,引起张力不稳。
如摆辊检测装置,若由于涨紧套的松动,导致检测失真,必然给PLC一个错误的信号,这样它也会发出来一个错误的指令,最终导致套印不准。
(c)凹印机各主要构件制造精度和装配精度超差,也是引起张力浮动的重要因素。
假如凹印机中导向辊加工精度差,就不能保证料的张力稳定,进而影响印刷效果,对导向辊的整体要求是:①导向辊之间要互相平行,平行度不超过0.05mm,在加工时要求导向辊圆跳动不能大于0.02mm。
跳动太大,料的张力会随着导向辊的转动而发生无规则的变化。
②导向辊平衡,如果不平衡,导向辊在一周内的转速时刻发生变化。
纸张套印不准产生的原因及解决方法

_
广 东 印刷 2 1 . _ 0 05
一3 3一
减 少 或 防 止 印 刷 质 量 故 障 的 发 生 。 实 际 上 , 大 油 墨 的 增
想 不 到 的 良好 工 艺 效 果 , 墨 的流 动 性 调 整 至 印 刷 时 纸 油 面 不 出现 掉 粉 等 质 量 问 题 后 , 不 但 印 刷 版 面 没 有 出 现 “ 花 ” 象 , 且 印 刷 墨 层 的色 彩 亮 度 高 , 品 的 印 刷 油 现 而 产 质量令人 满意 。 综 上 所 述 , 只 要 我 们 正 确 认 识 和 掌 握 四 色 纸 箱 印 刷 品 质 量 检 查 的 项 目和 要 素 ,并 通 过 工 艺 技 术 方 面 的 把 关
1纸 质 不 好 .
原 因分析 : 印 不 同于 其 他 印 刷方 式 , 刷 过 程 中 要 胶 印
有 水 的 参 与 , 果 使 用 抗 水 性 不 好 的 纸 张 , 草 浆 ( 浆 如 或 草 里 含 有 大 量 的 半 纤 维 素 ,而 半 纤 维 素 中 的羟 基 含 量 更 高 于 纤 维 素 )含 量 高 的 纸 张 , 由于 其 形 状 尺 寸 的稳 定性 不
想。 来 , 者萌发 了利用亮光 ?调整 油墨的流动性 , 后 笔 E h 来 降 低 油 墨 的 粘 度 。 果 , 一 调 配 油 墨 的 工 艺 , 到 了 意 结 这 收
需求 。囤
作 者 单 位 : 建 莆 田 鸿 立 印 刷 包装 有 限 公 司 福 责 任 编 辑 /欧 定 军
纸 时 , 经 常 常 遇 到 纸 板 容 易 出现 掉 粉 、 毛 甚 至 出现 曾 掉
纸 面 起 泡 的 问 题 , 初 笔 者 采 用 在 油 墨 中 加 调 墨 油 和 去 起
印刷套印不准的原因解析
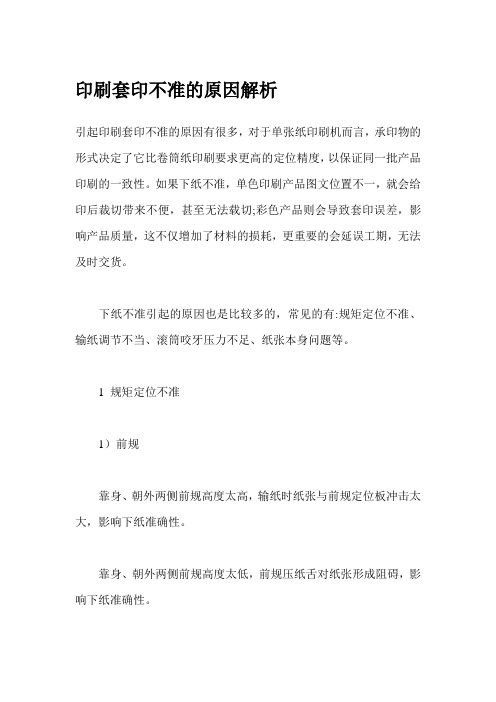
印刷套印不准的原因解析引起印刷套印不准的原因有很多,对于单张纸印刷机而言,承印物的形式决定了它比卷筒纸印刷要求更高的定位精度,以保证同一批产品印刷的一致性。
如果下纸不准,单色印刷产品图文位置不一,就会给印后裁切带来不便,甚至无法载切;彩色产品则会导致套印误差,影响产品质量,这不仅增加了材料的损耗,更重要的会延误工期,无法及时交货。
下纸不准引起的原因也是比较多的,常见的有:规矩定位不准、输纸调节不当、滚筒咬牙压力不足、纸张本身问题等。
1 规矩定位不准1)前规靠身、朝外两侧前规高度太高,输纸时纸张与前规定位板冲击太大,影响下纸准确性。
靠身、朝外两侧前规高度太低,前规压纸舌对纸张形成阻碍,影响下纸准确性。
靠身、朝外两侧前规高度调节不一致,极易造成较低一侧前规压纸舌对纸张的阻碍,从而影响纸张定位,引起下纸不准。
前规高度一般调至所印纸张三张纸厚度为宜,且两边要一致。
2)侧规调节时纸张离侧规定位板太近或太远,都会影响侧规定位的准确性。
侧规拉力的大小也会影响来去方向的定位,而且侧规压纸板的高度太低了会使纸张过不去。
侧规原因造成的来去方向下纸不准较为常见。
在调节时稍加注意,并不难解决。
即侧规拉纸距离约为3mm~5mm为宜,拉力以刚好能把纸拉到侧规定位板,又不至于使纸张拱起为限。
2 输纸调节不当1)飞达调节不当,造成输纸歪斜。
2)毛刷轮、压纸轮位置或压力不对,影响规矩定位较为常见,也容易解决。
恰当的调节是纸张定位时,压纸轮离开纸张后边缘大约1mm,毛刷轮压纸以稳定纸张,但压力不能太大,以纸张定位时不转为宜,避免影响规矩定位,而且无论是毛刷轮还是压纸轮两边一定要调节一致。
3 滚筒咬牙压力不足由于胶印机速度高,滚筒咬牙在使用一段时间后可能会出现滚筒咬牙压力不足的问题,从而影响印刷下纸的精确性。
印刷实地版时,如果滚筒咬牙压力不足,由于版面油墨粘性对印张产生一定程度的反剥离阻力,压印中的印张就很容易从咬牙里往外滑移。
其主要原因是滚筒咬牙的弹簧钢片压力不够,以致咬牙咬不紧纸边。
引起套印偏差的原因及解决经验

物收缩变形量也越大,在制版时考虑进去。安排
印刷色序时尽量将有套色要求的色别靠近,减少
受材料变形的影响。对于细小文字和图案的叠色
或套印应尽量避免,采用专色版的做法较好;必
须要套色的,应根据不同色相的具体情况和凹印 机的精度,适当做括缩边。
0c21f4ca 易博亚洲
印刷机本身的精度是影响套印的一个重要
因素,现在带自动套准装置的凹版印刷机精度一
般在 0.15mm 以内,设备精度越高当然越容易克
服套印偏差。如果精度下降,首先要恢复精度,
否则套印偏差较难克服。在操作上,引起套印偏 差的原因有:油墨刮刀调整不合适,光电信号端
油墨脏污,电眼接受信号失真。②凹版滚筒两端
残缺的皎月,稀疏梧桐木,残屋漏断夜雨声,却无一人。幽人独来独往尝尽人间冷暖
予一定的伸放量,以弥补承印材料的变形量。对
于轮转机来说,一般是周向依色序递增、轴向依
色序倒递增。对于单张凹印机来说,一般轴向和
周向均为依色序递增。对于单张凹印配胶印来
说,先凹印,后胶印,较易调整套印问题和确保 印品质量的稳定性。另外,着墨面积越大,承印
等,都会造成套印偏差。印刷厂首先应确保印刷
环境温湿度的稳定性;中国油墨刮刀网技术员余 佳认为:在印刷前三天将承印材料放到车间,以
提高其温湿适性,防止出汗现象的产生;及时总
结不同材料、不同品牌承印物和油墨的印刷适
性;首次印刷需协调张力拉伸、印刷压力、刮墨
刀位、油墨配比、稀料配比、油墨黏度、烘干温
度以及印刷机速等。制作凹印版滚时,在工艺条 件稳定、材料收缩量基本稳定的条件下,事先给
压力、张力拉伸以及烘干温度的作用,伴随承印
物中液体物的挥发,使纤维收缩后会产生变形,
- 1、下载文档前请自行甄别文档内容的完整性,平台不提供额外的编辑、内容补充、找答案等附加服务。
- 2、"仅部分预览"的文档,不可在线预览部分如存在完整性等问题,可反馈申请退款(可完整预览的文档不适用该条件!)。
- 3、如文档侵犯您的权益,请联系客服反馈,我们会尽快为您处理(人工客服工作时间:9:00-18:30)。
凹印啤酒铝箔帽标套印不准原因分析及解决在凹印生产啤酒铝箔帽标的过程中,套印不准是极为常见的故障。
随着市场竞争日趋激烈,五色以上的产品不断增多,客户对印刷品质量的要求越来越高,印刷的套印问题更为突出。
目前有相当一部分印刷损耗是由于套印不准造成的,要想提高啤酒铝箔帽标的印刷质量,降低生产成本,应有效地控制和减少因套印不准引起的浪费。
套印的基本原理啤酒铝箔帽标所用的铝箔厚度只有0.0102mm,主要成分是纯铝,质地十分柔软。
在凹印过程中,由于印刷路线较长,受拉伸变形、热胀冷缩和其他因素的影响,铝箔会不断产生套印误差,如果这些误差得不到及时纠正,积累超过一定限度就会导致产品报废。
要想提高套印精度,必须对这些误差进行连续监控,及时予以纠正。
对于低速铝箔帽标凹印机,可通过目测和手动调整的方法来纠正套印误差。
手动控制套印由于存在劳动强度大、人为操作误差大等弊端,已不能适应高速度,高质量的要求,因此现代高速铝箔帽标凹印机已普遍采用自动套准系统,印刷各色组套印情况的跟踪.检测和纠正全部由该系统自动完成。
套印不准的原因分析与处理造成凹印铝箔帽标套印不准的原因多种多样,主要有以下几种:1.铝箔褶皱引起套印不准。
铝箔产生褶皱的原因及相应的对策如下: (1)印刷压力不均匀,压印胶辊一边高、一边低。
这时应对压印胶辊进行调整,使两边压力保持均匀一致。
(2)压印胶辊表面凹凸不平或者两边黏附上油墨。
解决方法是:①把表面凹凸不平的胶辊拆下,换上光滑、有韧性、有弹性的胶辊,凹凸不平的胶辊可以重新加工处理;②把黏附在胶辊两边的油墨擦干净。
(3)导辊不平或黏附有油墨。
铝箔印刷对各导辊的要求很高,平行度稍有偏差就会导致印刷时出现褶皱。
油墨很容易黏附在导辊上,从而导致铝箔走纸不平并产生褶皱,因此,平时要经常检查和清洁导辊,以确保印刷顺利进行。
(4)印刷过程中,铝箔放卷张力太大引起跳动,或者收卷张力过小引起收放卷受力不均匀都会导致褶皱。
解决方法是对收放卷张力进行调整,使前后张力一致、合理。
(5)铝箔材料本身的问题,如两边厚薄不一致,或者本身有褶皱等。
对此,需要更换铝箔材料。
(6)油墨的流动性和干燥速度、烘箱的热风温度等也会对铝箔产生一定的影响。
因此在印刷过程中出现铝箔褶皱时,也要对这些因素进行检查。
2.压印胶辊压力不平衡引起套印不准印刷过程中,压印胶辊两端的压力应保持一致,若气压不足或两端压力调节不平衡,会造成印刷过程中压印胶辊上下跳动。
解决的方法是:检查气路系统,如漏气,要对漏气的气动元件或者压印胶辊进行更换,使压印胶辊与印版在印刷时完全吻合,压力保持恒定、一致。
3.版滚筒松动引起套印不准铝箔帽标凹印机采用的是无轴版滚筒,如上版不紧,在高速印刷过程中,印版滚筒就会出现松动,产生运转不平稳或跳动,从而引起套印不准。
另外,锥头、锥孔有积墨或异物,也会影响上版效果及版滚筒运转的平稳性。
因此,上版时一定要把锥头、锥孔清理干净,确保版滚筒上紧。
4.导辊调节不当引起套印不准导辊调节不平行会影响走纸的平稳性,使铝箔两边输送速度不同步,从而出现套印不准现象。
因此,印刷机上的各导辊调平后应少作调整。
5.张力不稳定引起套印不准在铝箔帽标凹印过程中,放料卷直径逐渐变小,而收料卷的直径不断变大,因此印刷张力是不断改变的。
张力的变化直接影响着铝箔的伸长率,因此印刷时如果前后张力无规律地频繁变化,就会引起套印不准。
因此,除了要根据实际情况合理设定收、放卷张力,避免张力过大或过小外,还应尽可能保持张力相对恒定,避免发生较大的变化。
6.自动套准系统失灵引起套印不准自动套准系统中任一环节出问题,都直接影响整个系统的正常工作,导致套印误差不能及时得到纠正,造成套印不准。
因此,如果自动套准系统失灵,就要逐一检查系统的各组成部分,找出问题所在并进行排除,必要时请专业维修人员进一步检查和维修。
7.印版滚筒安排不当引起套印不准铝箔是软性的金属材料,印刷过程中会出现逐渐伸长的现象,从而对套印产生不利影响。
为了弥补由此产生的套印误差,制版时各色组的印版滚筒直径必须按色序以一定的系数逐色递增。
印版滚筒直径递增系数要符合印刷工艺的要求,否则就会使一些色组出现套印不准。
同时,装版时一定要看清色序,如果把色序搞错,印版滚筒递增的顺序不正确,同样会导致套印不准。
另外,制版时色序的安排、套色的处理等也会对印刷套印产生一定的影响。
相关镀铝纸特性及使用要求信息正确认识镀铝纸特性及使用要求国真空镀铝纸以表面金属质感强、色彩亮丽、印品高贵典雅,深受商家和包装业的青昧。
随着商品经济的不断际发展,真空镀铝纸将越来越广泛地用于啤酒、香烟、电子产品、化妆品以及其他食品商标、标签的印刷。
由流于镀铝纸表面不同于普通纸张、纸板材料,其表面的金属层是非吸收性的,因此,印刷工艺不同于普通的印行刷工艺,在印刷方面难度相应较大,质量控制的要求要高一些。
所以,正确认识真空镀铝纸材料的特性,掌新握印刷工艺技术知识,控制好原纸的质量和胶印工艺技术,才能更好地保证产品的整体质量,满足产品包装型的使用性能和质量要求。
食品包装印刷商标用的镀铝纸,一般采田70克左右的防水铜版纸或普通铜版纸为基材,通过在纸面上喷镀一层厚度为0.02mm左右的铝层,并在其表面涂布一层蜡克,使镀层具有良好的浸润作用和分子间的作用力,表面性欧能满足印刷着墨的要求。
洲纸一般镀铝纸的喷镀层有银色和金色两种。
其表面有素面(光面)的,也有压制布纹、细条纹、橘皮纹、亚麻纹、质树皮纹和雨点纹或其他的花纹、字纹等。
工艺实践情况表明,镀铝纸材料的特性必须符合商标的使用性能、食印刷工艺、模切、冲切、贴标和洗瓶脱标的要求,否则,就容易出现一些意想不到的质量问题。
所以,只有品正确认识镀铝纸商标的特性和相关的影响因素,才能有效地控制好镀铝纸材料质量和印刷质量,使镀铝纸商包标较好地满足客户的使用要求。
装发1.商标的使用性能对镀铝纸的要求展速粘贴瓶装啤酒的商标,要求镀铝纸应该具有良好的耐温、耐水性能,才能避免使用过程中出现掉铝脱色的度质量问题。
美多年前我厂在生产镀铝纸啤酒标时,就曾经有过深刻的质量教训。
有一次,由于镀膜生产厂家供货中途突然国PP改变镭射纸的生产工艺,使一批镭射纸啤酒标在市场使用中出现严重的掉铝脱色现象。
其掉铝脱色表现为:在夏天,啤酒在冰箱或冰块里冷藏取出来后,发现啤酒标表面的油墨层连同铝层出现大面积的脱落现象,严泡重影响了产品的市场形象,造成了库存的一部分原纸和商标全部报废,直接经济损失达数万元。
事故发生后,沫我们经过认真分析、研究和试验,发现出现容易掉铝脱色的镭射纸,只要放在水里浸泡几分钟,表面的铝层塑即出现自然脱落现象。
料进这次质量事故的原因,主要是由于我们对镭射纸这种新兴的包装材料缺乏正确的认识,在质量源头环节上没入有形成有效的检验措施,以致这批镭射纸因涂层质量、工艺存在质量隐患,使表面铝层与纸面结合不牢的镭食射纸投入使用后产生了不良的后果。
后来,我们认真吸取了失败的经验教训,制定了镭射纸耐低温、抗水性品能的检验措施,对入库的原纸进行检验控制,有效地避免了类似质量问题的发生。
复2.贴标、脱标对镀铝纸的要求。
合软完成印刷并且质量达到合格的商标还要经得起市场使用的考验。
贴瓶用的商标,它的使用特性不同于一般商包标。
特别是在高速生产线上自动贴标的啤酒商标,要经得起快速、连续贴标不能出现掉标、皱标、翘曲的使装用考验,这就要求在拼版印刷时,镀铝纸商标的纤维方向应与瓶轴的方向成垂直状态,才能避免出现贴标质中量事故问题的发生。
复合几年前,笔者在走访客户时曾经了解到这样的一起贴标质量事故:某印刷厂由于不了解啤酒厂的贴标工艺要方求,使印刷的商标纤维方向与瓶轴的方向成平行方向,以致啤酒厂在贴标时出现较厉害的卷曲和掉标现象,式无法实现高速、连续正常地贴标。
结果这批镀铝纸纤维方向用错的商标被判定为不合格品,全部作报废处理,的经济损失达数万元。
分除原纸的纤维方向影响贴标外,镀铝纸的伸长率、卷曲性指标对贴标质量也有一定的影响。
某啤酒厂在一次包贴标时,发现皱标现象比较厉害,对机器进行反复的调整并更换胶水也无济于事。
后来查到标纸上,发现镀装铝纸商标的伸长率过大,卷曲过快,结果将这批5万套的商标报废处理。
凹印还有一次,某印刷厂中途更换使用另一生产厂家的镀铝纸。
由于该镀铝纸的背面吸收性过差,亲胶性不好,的结果印刷后的商标不能适应啤酒厂灌装生产线的贴标适性,贴标中频繁出现掉标现象,也被判定为不合格品,发作了报废处理,损失达几万元。
展趋此外,镀铝纸碱液渗透性能,则会影响啤酒厂的洗瓶脱标。
若碱液渗透性差,则会造成生产线上洗瓶不脱标势现象,影响下道工序的正常贴标。
这种质量事故啤酒厂也曾经出现过。
所以,对印刷厂来说,印刷镀铝纸商标仅注重控制印刷质量是不够的,更重要的还应注重质量源头的控制:一是要加强与啤酒厂的沟通,了解啤包酒厂的生产工艺和要求;二是选择具有一定的生产规模、生产工艺技术比较先进、质量比较稳定的供应商,装保证镀铝纸质量的稳定;三是要建立原材料检验制度,对镀铝纸的碱液渗透性、吸水率、卷曲性、伸长率和市抗拉强度等指标进行全面的检测,防止质量事故的发生,确保印刷的镀铝纸商标很好地满足啤酒厂的使用要场求。
的三3.印刷工艺对镀铝纸的要求大发为保证产品的印刷质量,要求镀铝纸表面应光亮、光滑、压纹深浅一致,无明显的断纹和坏纹现象。
压纹也展不可过深,镀层要具有良好的耐磨性能,并且铝层的润湿性、干燥性、亲墨性要好,印刷后不出现褪色和掉潜色现象。
铝层表面不得有斑点、色差和氧化现象。
纸面还应保持清洁,无粉尘、无其他影响印刷质量的异物力粘连现象,确保正常的呈色效果和印品色相的均匀一致。
塑从印刷工艺和商品包装的角度考虑,要求镀铝纸纸质平整度良好,纸面应平直坚挺,不翘角、不卷曲、不变料形,无皱折痕迹,纸边应无明显波浪和卷边。
镀铝纸的表面强度要高,镀铝层与纸基层的结合牢固,抗剥离包性能强,用胶带粘拉表面铝层不易拉脱,以保证正常的印刷着墨。
装材镀铝纸若存放过久,表面的铝层容易出现氧化产生白斑而失去光泽感,影响正常的显色和印刷质量。
所以,料镀铝纸的使用周期一般应控制在1个月左右。
但是也要注意,刚生产的镀铝纸,若马上投入印刷也容易出现已卷曲变形现象,影响套印精度和产生其他连锁质量问题。
镀铝纸的含水率也是影响印刷质量的重要因素,一成般镀铝纸水分应控制在4%—6%之间,存放环境的温湿度应该与印刷车间的温湿度相适应,以保证产品的套为印质量。
一般温度可控制在23±50C之间,湿度控制在50%一70%之间,以防止温湿度上的悬殊,使镀铝纸药出现变形而产生套印质量问题。
包装4.模切、冲切对镀铝纸的要求楞商标的成型工艺通常采用平压平结构的模切机或卧式商标冲切机进行冲切。
商标的冲切要求镀铝纸的抗张强纸度性能和平整度要好,纸质的厚薄必须均匀一致,整令纸不应存在明显的厚薄差异情况,这样才能较好地防市止因冲切时纸面受力不均而引起边缘撕裂或出现冲歪现象。