切削载荷下机床主轴的振动响应分析_万海波
数控机床故障诊断与维修项目11 加工中心主轴振动故障诊断与排除_OK

若是,应加注润滑油;接着检查导油管是否漏润滑 油,若是,应更换导油管;最后检查润滑电路是否 故障,若是,应及时对其进行检修。 (2)主轴负载过大。尝试减少负载,如果故障消失, 则为主轴负载过大故障,此时,应重新考虑负载条 件,减轻负载。
常运行。
4
项目十一 加工中心主轴振动故障诊断与排除
【项目分析】
数控机床主轴振动故障属于典型的主传动系 统的混合型故障。数控机床主传动系统主要 包括主轴部件、主轴箱、调速主轴电动机。 其中主轴部件由主轴、主轴轴承、工件或刀 具自动松夹机构构成。数控机床的主传动系 统的功率大小与回转速度直接影响着机床的 加工效率,而主轴部件是保证机床加工精度 和自动化程度的主要部件,对数控机床的性 能有着决定性的影响。因此,主传动系统故 障将直接关系到数控加工的质量和效率。
6
项目十一 加工中心主轴振动故障诊断与排除
当主轴停止时每次机械手自动装取刀具,必须保 证刀柄上的键槽对准主轴的端面键, 为满足主轴 这一功能而设计的装置称为主轴准停装置或主轴 定向装置,如图11-1所示。在自动换刀的数控镗 铣加工中心上,切削转矩通常是通过主轴上的端 面键和刀柄上的键槽来传递的,这就要求主轴具 有准确轴向定位功能。
31
项目十一 加工中心主轴振动故障诊断与排除
(7)主轴部件上的动平衡不好。将主轴电动机以 最高速度运行,马上关掉电源,使其惯性运转, 用实用诊断技术中的“听”检查是否仍有异常 噪声,若有,应校核主轴部件上的动平衡条件, 然后将主轴部件调整到合适状态。
(8)轴承拉毛或损坏。此时,就需要拆开相关的机 械结构来目测观察,如果出现拉毛或损坏情况, 应更换轴承
23
浅析机床的振动及防治
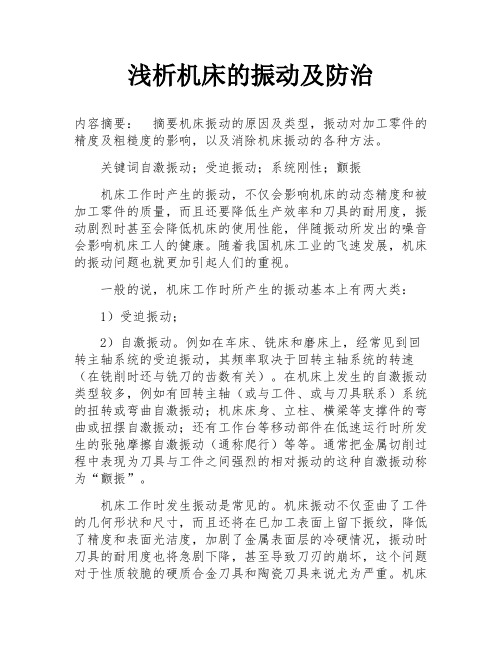
浅析机床的振动及防治内容摘要:摘要机床振动的原因及类型,振动对加工零件的精度及粗糙度的影响,以及消除机床振动的各种方法。
关键词自激振动;受迫振动;系统刚性;颤振机床工作时产生的振动,不仅会影响机床的动态精度和被加工零件的质量,而且还要降低生产效率和刀具的耐用度,振动剧烈时甚至会降低机床的使用性能,伴随振动所发出的噪音会影响机床工人的健康。
随着我国机床工业的飞速发展,机床的振动问题也就更加引起人们的重视。
一般的说,机床工作时所产生的振动基本上有两大类:1)受迫振动;2)自激振动。
例如在车床、铣床和磨床上,经常见到回转主轴系统的受迫振动,其频率取决于回转主轴系统的转速(在铣削时还与铣刀的齿数有关)。
在机床上发生的自激振动类型较多,例如有回转主轴(或与工件、或与刀具联系)系统的扭转或弯曲自激振动;机床床身、立柱、横梁等支撑件的弯曲或扭摆自激振动;还有工作台等移动部件在低速运行时所发生的张弛摩擦自激振动(通称爬行)等等。
通常把金属切削过程中表现为刀具与工件之间强烈的相对振动的这种自激振动称为“颤振”。
机床工作时发生振动是常见的。
机床振动不仅歪曲了工件的几何形状和尺寸,而且还将在已加工表面上留下振纹,降低了精度和表面光洁度,加剧了金属表面层的冷硬情况,振动时刀具的耐用度也将急剧下降,甚至导致刀刃的崩坏,这个问题对于性质较脆的硬质合金刀具和陶瓷刀具来说尤为严重。
机床发生振动后,往往迫使操作工人降低切削用量,因而限制了机床的生产率。
此外,在机床自动线中,只要有一台机床发生振动而被迫暂停运转,就会破坏生产的节律,引起生产过程的混乱。
可见机床振动是必须引起注意的一个重要问题。
随着科学技术的飞跃发展,对机床零件的制造精度和表面质量提出了更高的要求,从而使机床振动问题的研究成为研制、生产和使用机床等部门必须面对的重大课题,研究机床振动的目的在于探究机床振动的原因,谋求防止和消除机床振动的方法,以研制抗振性更佳的机床。
数控铣削时工件振动响应的试验研究

中圈分类号 :0 3 4 3 . 1 ;T G 7 1 3 . 3 文献标识 码ห้องสมุดไป่ตู้:A 文章编号 :1 0 0 1 — 3 8 8 1 ・ ( 2 0 1 3 J 5~ 0 3 0—3
Ex pe r i me nt a l St u d y o n t he Vi br a t i o n Re s p o ns e o f t he Wo r k- p i e c e dur i n g t he Nu me r i c a l Co nt r o l Mi l l i n g
2 0 1 3年 3月
机床与液压
MACHI NE TO0L & HYDRAUL I CS
Ma r . 2 01 3 Vo 1 . 41 No . 5
第4 1卷 第 5期
D OI :1 0 . 3 9 6 9 / j . i s s n . 1 0 0 1—3 8 8 1 . 2 0 1 3 . 0 5 . 0 0 8
Xu z h o u J i a n g s u 2 2 1 1 1 6, C h i n a;
2 . A e r o s p a c e G r o u n d D e p a r t m e n t ,T h e A i r F o r c e S e r v i c e C o l l e g e ,X u z h o u J i a n g s u 2 2 1 0 0 0,C h i n a )
CNC铣床切削颤振的动态性能试验分析

振稳定 性极 限理 论 , 通过动 力学试 验方 法 , 量 机床 刀 测 具和工 件 问 相 对 激 振 的频
式 中 为切 削极 限宽 度 ; 切 削 刀具 齿 数 ; c 动 b Z为 K为 态 切 削 力 系 数 ; ( )为 机 床 结 构 频 响 函 数 ; H
I 日() I 为机 床结 构频 响 函数 曲线 的最 大负 实部 。 一 C) … a
Ke ywo d r s:M iln b a in;M o a ay i ; Dy a c Pe fr n e Ex e i n li g Vi r t o d lAn lss n mi ro ma c p rme t
金属 切 削机床 在 使 用 中 经 常会 遇 到 强 烈 的 振 动 。 这 些振 动使加 工表 面 产 生 波纹 , 且使 切 削力 产 生 剧 并
i dig o h i n mi l n i r to fn n utt e man dy a c m i i g vb a in. Atf s , t e u n y r s o e c re o ea ie vb a l r t he f q e c e p ns u v fr ltv i r — i r t n bewe n c t ra d wo k ic so a n d fo t u tn x e i n . T e h x e i na d l i t e u t n r p e e i bti e r m he c ti g e p rme t h n te e p rme tlmo a o e
基于Qt和Matlab的数控机床主轴振动监测系统设计

第35卷第1期2020年2月北京信息科技大学学报Journal of Beijing Information Science &Technology UniversityVol.35No.1Feb.2020文章编号:1674-6864(2020)01-0078-04DOI :10.16508/j.cnki.11-5866/n.2020.01.015基于Qt 和Matlab 的数控机床主轴振动监测系统设计范文超(北京信息科技大学机电工程学院,北京100192)摘要:针对数控机床主轴振动信号,在Windows 平台下运用Qt 和Matlab 设计了信号监测系统。
采用JM5842无线振动传感器在不干扰机床工作的条件下实现振动信号采集,使用连续小波变换方法分析选取的振动信号数据,最后进行了实验验证。
结果表明,系统能够在主轴振动信号中解调出不同工况下的主轴信息,完成主轴振动信号的时频分析,从而实现了机床关键部件主轴的振动信号监测,为进一步实现数控机床健康状态的监测提供技术支持,具有一定的工程应用价值。
关键词:Qt ;Matlab ;连续小波变换;数控机床主轴中图分类号:TB 53/TH 86文献标志码:A Vibration monitoring system design of CNC machine tool spindlebased on the Qt and MatlabFAN Wenchao(Mechanical Electrical Engineering School ,Beijing Information Science &Technology University ,Beijing 100192,China )Abstract :In this paper ,the vibration signals of computer numerical control machine tool spindle are monitored by designing with the Qt and Matlab on the Windows platform.The JM5842wireless vibration sensor is used to realize vibration signal acquisition without interfering with the machine tool.The method of continuous wavelet transform is adopted to analyze the selected vibration signal data.Finally ,the experimental verification is carried out.The results indicate that the system can demodulate the spindle information in the spindle vibration signal under different working conditions ,analyze the time-frequency of the spindle vibration signals ,and realize the monitoring of the vibration signals of the key components of machine tool ,which provides technical support for the monitoring of computer numerical control machine ,and has a certain engineering application value.Keywords :Qt ;Matlab ;continuous wavelet transform ;CNC machine tool spindle收稿日期:2019-09-10第一作者简介:范文超,男,硕士研究生。
金属切削中的刀具动态负荷分析与振动控制

金属切削中的刀具动态负荷分析与振动控制随着制造业的发展和技术的进步,金属切削已成为现代加工工艺中不可或缺的环节。
金属材料的切削加工过程中,刀具承受着巨大的动态负荷,而这些负荷会导致刀具的振动,进而影响加工的精度和表面质量。
因此,对金属切削中刀具的动态负荷进行分析和振动控制具有重要意义。
刀具动态负荷分析主要通过建立数学模型来描述切削过程中的力学性能。
一般来说,刀具动态负荷分析需要考虑以下几个方面的因素:首先是切削力的分析。
切削力是指在切削过程中刀具受到的力的大小和方向。
切削力主要由切削阻力和切削热导致的材料变形引起的应力引起。
通过分析切削力的分布和变化规律,可以评估刀具的负荷程度,从而为刀具的设计和选择提供科学依据。
其次是动态特性的分析。
刀具的动态特性是指刀具在受力作用下振动的频率和振幅。
刀具的振动对加工过程和加工结果具有重要影响,因此需要进行动态特性的分析。
常用的分析方法包括有限元分析和模态分析等。
通过这些分析方法,可以得到刀具的振动模态及其频率等关键参数,为后续的振动控制提供依据。
最后是振动控制的方法。
根据刀具的动态特性分析结果,可以采取一系列的振动控制措施来减小刀具的振动。
常见的振动控制方法包括动平衡、刚性支撑和减振器等。
动平衡是指通过增加或减少刀具上的质量分布,使刀具的振动幅值减小。
刚性支撑是指在切削过程中给予刀具充分的支撑,使其振动减小。
减振器是一种通过阻尼材料或装置来减小振动幅值的方法。
通过采取这些振动控制方法,可以有效地降低刀具的振动,提高加工质量和效率。
在金属切削中的刀具动态负荷分析与振动控制中,还需要考虑到刀具和材料之间的磨损和热变形等因素。
刀具的磨损会导致切削力的变化,进而影响刀具的动态负荷和振动。
而材料的热变形会引起刀具的振动,甚至导致刀具的断裂。
因此,在分析和控制刀具的动态负荷时,还需要考虑到这些因素的影响,并采取相应的措施进行修正和优化。
总之,金属切削中的刀具动态负荷分析与振动控制是一项重要的技术研究领域。
金属切削过程中的振动与共振现象分析

金属切削过程中的振动与共振现象分析摘要:金属切削过程中的振动与共振现象对切削效果和加工精度有着重要影响。
本文通过分析金属切削中的振动与共振现象,探讨了造成振动和共振的原因,以及采取的一些控制措施。
通过合理的切削参数选择、工具结构设计和切削工艺优化等措施,可以降低振动和共振现象,提高金属切削加工的质量和效率。
1. 引言金属切削作为现代制造业中常用的一种加工方法,广泛应用于机械、汽车、航空等领域。
然而,在金属切削过程中经常会遇到振动和共振现象,导致切削效果和加工精度下降,甚至带来安全隐患。
因此,研究金属切削中的振动与共振现象是提高切削质量和效率的重要问题。
2. 振动与共振现象的原因2.1 切削力激振金属切削过程中,切削力是主要的激振源。
当切削力在切削过程中频繁变化时,容易引起工件和刀具系统的振动。
切削力的大小和方向都会对振动引起的频率、振幅和相位角等产生影响。
2.2 切削系统的刚度和阻尼切削系统的刚度和阻尼是影响振动和共振现象的重要因素。
刚度过低会导致切削系统产生过大的挠度和变形,从而引起振动和共振。
而刚度过高会导致共振频率过高,难以找到合适的激振频率,也容易引起振动和共振。
阻尼过低则不利于振动的消除,阻尼过高则会降低系统的灵敏度。
3. 振动与共振的影响3.1 切削质量与效率下降金属切削中的振动和共振现象会导致加工表面粗糙度增加、刀具寿命缩短、加工精度降低等问题,从而影响切削质量和工件的功能性能。
同时,振动和共振还会降低切削效率,增加切削成本。
3.2 安全隐患振动和共振现象引起的高频振动会对切削系统和机械结构产生巨大的冲击和振动载荷,不仅会导致设备破坏,还可能造成安全事故。
因此,控制振动和共振现象也是确保切削操作安全的重要措施。
4. 振动与共振的控制策略4.1 合理选择切削参数合理选择切削参数是控制金属切削过程中振动和共振现象的关键。
通过调整进给速度、切削深度和切削速度等参数,可以控制切削力的大小和方向,从而减小振动和共振的产生。
《2024年考虑主轴-刀柄结合面特性的机器人铣削系统刀尖频响预测研究》范文

《考虑主轴-刀柄结合面特性的机器人铣削系统刀尖频响预测研究》篇一一、引言随着工业自动化和智能制造的快速发展,机器人铣削系统在机械加工领域扮演着越来越重要的角色。
精确地预测铣削过程中的刀尖频响特性对于优化加工效率、提升产品质量和确保加工过程的安全稳定至关重要。
尤其是在考虑主轴-刀柄结合面特性的情况下,刀尖频响的预测变得尤为重要。
本文将深入研究机器人铣削系统中主轴-刀柄结合面特性的影响,并探讨如何通过有效的方法预测刀尖频响。
二、主轴-刀柄结合面特性的重要性主轴与刀柄的结合是机器人铣削系统中的关键环节。
结合面的特性直接影响到铣削过程中的动力学性能,包括刀尖的振动、切削力等。
主轴和刀柄的结合稳定性决定了切削过程中的动力传递效率及系统动态响应。
因此,考虑主轴-刀柄结合面特性的因素在机器人铣削系统的设计与优化中具有重要意义。
三、机器人铣削系统的工作原理及影响因素机器人铣削系统的工作原理主要是通过机器人臂部的精确控制,实现刀具对工件的铣削加工。
在加工过程中,主轴的旋转速度、刀具的种类及几何形状、切削参数等都会对铣削过程产生影响。
同时,主轴-刀柄结合面的特性也会对铣削过程中的动力学行为产生重要影响。
四、刀尖频响预测的方法与步骤为了准确预测机器人铣削系统中刀尖的频响特性,本文提出以下方法和步骤:1. 建立机器人铣削系统的动力学模型:通过建立包括主轴、刀柄、刀具和工件在内的多体动力学模型,描述系统的运动学和动力学特性。
2. 分析主轴-刀柄结合面的特性:通过实验和理论分析,研究主轴-刀柄结合面的刚度、阻尼等特性对系统动力学性能的影响。
3. 引入频响预测算法:利用动力学模型和频响预测算法,对铣削过程中的刀尖频响进行预测。
预测算法应考虑到切削力、切削速度、切削深度等参数的影响。
4. 实验验证:通过实验对比预测结果与实际结果,验证预测方法的准确性和可靠性。
五、实验结果与分析通过实验验证,本文提出的刀尖频响预测方法能够有效地预测机器人铣削系统中的刀尖频响特性。
- 1、下载文档前请自行甄别文档内容的完整性,平台不提供额外的编辑、内容补充、找答案等附加服务。
- 2、"仅部分预览"的文档,不可在线预览部分如存在完整性等问题,可反馈申请退款(可完整预览的文档不适用该条件!)。
- 3、如文档侵犯您的权益,请联系客服反馈,我们会尽快为您处理(人工客服工作时间:9:00-18:30)。
Vibration Analysis for the Spindle of Machine Tools under Cutting Loads WAN Haibo ( Department of Mechanical Engineering,Zhejiang University of Water Resources and Electric Power,Hangzhou 310018 ,China ) Abstract: The vibration response of the spindle for a machine tool under cutting loads,significantly has a direct impact on machining quality and efficiency. The vibration response is numericaly studied through the dynamic modeling for the loaded spindle. Dynamic modeling is combined w ith modal analysis, and harmonic response analysis is further conducted on the output. Results show that the cutting depth is the main factor that influences the vibration of a NC spindle. Key words: cutting Loads; NC spindle ; vibration response ; modal analysis
1
切削载荷下数控机床主轴振动响应数学 模型
数控机床主轴一直在切削力作用下工作。切削力 [ 8 ] 其刀具平面切向力 的模型一般采用经验预估模型 ,
收稿日期: 2013 - 11 - 14 ; 修回日期: 2013 - 12 - 04 * 基金项目: 国家自然科学基金( 11172260 ) ; 浙江省教育厅科研计划资助项目( Y201224248 ) ; 浙江水利科技计划项目( RC1326 ) ( E - mail ) wanhb@ zjweu. edu. 作者简介: 万海波( 1981 —) , 男, 长沙人, 浙江水利水电学院讲师, 硕士, 主要从事机械振动、 故障诊断方面的研究, cn。
模态分析是动力学分析中最为基础的一个环节, 该分析能否准确确定结构的固有频率和振型, 是进行 后续诸如瞬态响应分析、 谐响应分析和谱分析等动力 学分析的基础。 对有限元 模 型 添 加 约 束 是 进 行 模 态 分 析 的 关 键步骤 。 根据 该 机 床 主 轴 的 结 构 分 析 在 主 轴 的 轴 承安装部 位 添 加 弹 簧 阻 尼 的 约 束 。 在 安 装 轴 承 的 圆周截面上建立横向纵向 各 两 个 弹 簧 阻 尼 单 元, 以 各处轴承的 内 外 圈 半 径 作 为 确 定 弹 簧 单 元 的 长 度 的依据 。 在保证弹簧阻尼单元的有限元划分数为 1 的前提下, 内外圈节点分别采用 Hard PT 和 KeyPoinis 方法建立 。 将所有 弹 簧 阻 尼 单 元 四 个 外 部 节 点 设为固定约束度, 并限制前 端 轴 承 支 承 内 部 所 有 节 [9] 鉴 于 Subspace 点的轴向自由 度 。 在 求 解 过 程 中, 法求解问题的范围广且计 算 精 度 高 的 特 点, 采用该 方法进行了模态仿真分 析, 得到了机床主轴的 5 阶 模态( 如图 3 至图 7 ) 。 模态分析后可求得主轴系统径向随工作频率变化 的振动响应图, 如图 8 。 由图 8 可知主轴的工作频率 远低于其共振频率。 但一旦工作频段逼近共振频率 时, 振幅 瞬 间 大 幅 提 升。 该 机 床 的 工 作 频 率 一 般 在 3000 ~ 4000 转范围内, 当在该范围内提升主轴转速加 快切削速度时, 在不考虑切削力变化的情况下机床主 轴的振动变化不明显。
sin( ωt - )
( 6)
图2
TH6350 加工中心主轴有限元仿真模型
2. 2
模态分析
2
2. 1
动力学仿真
动力学仿真模型构建
为提高计算效 在不影响计算结果精度的前提下, 率对 TH6350 加工中心主轴模型进行了局部的简化, 忽略 了 键 槽 倒 角 等 局 部 特 征。 使 用 三 维 构 图 软 件 Solidworks 绘制了 TH6350 加工中心主轴, 导入 ANSYS 中。
研究切削平面的单一振动时, 可将该模型简化为 单自由度系统, 如定义 x ( t ) 为刀具与工件在切削平面 的法向位移, 该系统在简谐激振力的作用下的振动模 型可简化为:
¨ ( t) + cx ( t) + kx( t) = F r cos( ωt + ) mx ( 5)
求解( 5 ) 式 其中 c 和 k 分别为阻尼比和刚度系数, 可得:
表1
杨氏模量( N / m) 2. 1 × 10 - 11
( 2)
切削力作用下, 机床主轴上的刀齿与工件接触时 工件受径向力 F r 的作用, 设主轴的瞬时转速为 n, 则其 频率为 Z * ( n /60 ) 。将该径向力进行的傅里叶级数展 开, 可得:
n
材料特性参数
泊松比 0. 3
3 材料密度( kg / m )
图1
TH6350 加工中心主轴结构模型
在 ANSYS 中定义单元属性, 其中包括单元类型、 单元的几何特性、 材料特性, 考虑 Solid92 单元是能较
· 24·
组合机床与自动化加工技术
+1 ?>.- @ / .,4 .,3 .,1
<58;
第4 期
.,/ . -,4 -,3 -,1 -,/ -
图3
切削载荷下机床主轴的振动响应分析
万海波
( 浙江水利水电学院 机电工程系,杭州 310018 )
*
摘要: 现代加工技术的发展对机床的加工精度的要求越来越 高。 切削 载荷下机 床 主 轴 的 振动 响 应 直 接影响数控机床的加工精度。通过建立 机 床 主 轴 的 动 力学 模型, 研究 切削 载荷下主 轴 的 振动 响 应。 通过建立主轴的动力学仿真模型, 进行模 态 分析, 进一 步 通 过 谐响 应 分析 切削 载荷下机 床 主 轴 的 振 动响应。分析结果表明, 切削转速对主 轴 振动 影响 不明 显, 切削 过程 中 切削 力 的 大 小 是 造 成机 床 主 轴振动变化的最主要原因, 且切削力大小与主轴的径向振动振幅成线性关系。 关键词: 切削载荷; 机床主轴; 振动响应; 模态分析 中图分类号: TH161 ; TG65 文献标识码: A
0
引言
的可靠性
[ 6 ]
。
机床主轴运转的正常与否直接影响机床的加工质 量以及生产效率。主轴系统切削载荷下的动态响应包 含了大量反映其工况的特征信息, 特别是切削载荷变 化时机床主轴的振动响应会直接影响到机床的加工质 量和精度。 因此研究不同切削载荷下主轴的振动响 应, 对如何提高现有机床的加工质量和精度有指导性 [ 13 ] 。 的意义 目前数控机床主轴系统动态特性主要采用有限元 分析方法和数学建模与试验测试相结合的方法。西安 交通大学曹宏瑞建立了可靠性较高的机床 - 主轴耦合 [ 4 ] 系统用于研究主轴的动力学特性 。山东理工大学吴 化勇通过建立机床主轴部件有限元模型, 对机床主轴 [ 5 ] 进行的优化设计 。河北工业大学的薛会民等使用有 限元方法建立了定梁龙门铣磨床主轴的三维模型, 得 到了该型主轴的固有频率和振型, 进一步分析了主轴
以此提高机 上述建模多用于主轴的设计和优化, 床主轴的稳定性, 直接用于分析机床主轴切削载荷下 的振动响应进而提升现有机床的加工质量还存在一定 难度。国内外很多学者采用了有限元或传递矩阵的方 法建立各类转子的动力学模型研究转子系统的振动响 [ 1, 7 ] , 这些大都需要将主轴简化为若干集中质量块, 应 与实际情况偏差较大。 本文提出了一种基于 ANSYS 的振动响应分析方法, 在建立动力学模型和有限元仿 真模型的基础上进行模态分析, 进一步通过加载切削 力进行谐响应分析, 通过数据提取对切削载荷下数控 机床主轴的振动响应进行研究。
2014 年 4 月
的数学模型如下:
万海波: 切削载荷下机床主轴的振动响应分析
· 23·
好适应不规则形状而且能满足一定精度要求的曲棱四
( 1)
. 88 0 . 72 - 0 . 88 F τ = C F α0 αf d αp Z e
切削宽度和 其中 C F 、 αe 、 α f 分别为切削力系数、 Z 分别为刀具直径、 d、 切削削深度和 每齿进给量, αp 、 铣刀齿数。刀具平面径向力模型为
x( t) = Ae - ζω nt sin( ω d + ) + F
2 2 2 2
( k - ω m) + ω c 槡 由上式不难看出在该系统的阻尼、 刚度等参数不 变的情况下, 刀具相对工件的位移会随着切削载荷力 的增大而增加, 且二者关系成线性。 在不同大小的切 削载荷力作用下, 主轴切削平面的振幅值也相应发生 变化。而切削力的频率变化造成的振幅变化不如切削 力大小变化的作用明显。
7800
P ( t ) = P0 +
∑P cos( iωt + )
i i i =1
( 3)
激振频率、 相位角。 其中 P 、ω 、 分别为幅值、 忽略高阶项影响, 且初相位 1 为 0 , 则该式可列为:
P( t) = F r cos( ωt + ) ( 4)
网格划分是有限元分析的第一步, 也是后续有限 元分析中的关键因素。 在定义好单元属性后, 指定网 格划分类型、 单元大小。考虑分析的准确性和经济性, 本研究采用的是自由划分类型和九级网格大小进行网 格划分。划分后如图 2 。