加工过程中存在的误差
加工过程中存在的误差
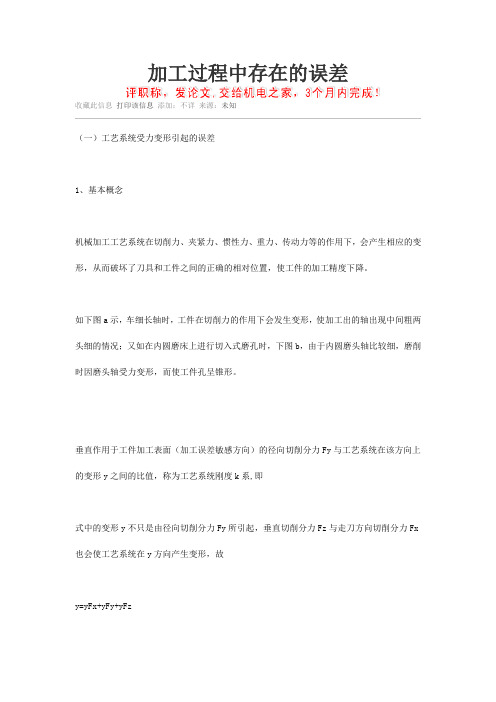
加工过程中存在的误差收藏此信息打印该信息添加:不详来源:未知(一)工艺系统受力变形引起的误差1、基本概念机械加工工艺系统在切削力、夹紧力、惯性力、重力、传动力等的作用下,会产生相应的变形,从而破坏了刀具和工件之间的正确的相对位置,使工件的加工精度下降。
如下图a示,车细长轴时,工件在切削力的作用下会发生变形,使加工出的轴出现中间粗两头细的情况;又如在内圆磨床上进行切入式磨孔时,下图b,由于内圆磨头轴比较细,磨削时因磨头轴受力变形,而使工件孔呈锥形。
垂直作用于工件加工表面(加工误差敏感方向)的径向切削分力Fy与工艺系统在该方向上的变形y之间的比值,称为工艺系统刚度k系,即式中的变形y不只是由径向切削分力Fy所引起,垂直切削分力Fz与走刀方向切削分力Fx 也会使工艺系统在y方向产生变形,故y=yFx+yFy+yFz2、工件刚度工艺系统中如果工件刚度相对于机床、刀具、夹具来说比较低,在切削力的作用下,工件由于刚度不足而引起的变形对加工精度的影响就比较大,其最大变形量可按材料力学有关公式估算。
3、刀具刚度外圆车刀在加工表面法线(y)方向上的刚度很大,其变形可以忽略不计。
镗直径较小的内孔,刀杆刚度很差,刀杆受力变形对孔加工精度就有很大影响。
刀杆变形也可以按材料力学有关公式估算。
4、机床部件刚度1)机床部件刚度机床部件由许多零件组成,机床部件刚度迄今尚无合适的简易计算方法,目前主要还是用实验方法来测定机床部件刚度。
分析实验曲线可知,机床部件刚度具有以下特点:(1)变形与载荷不成线性关系;(2)加载曲线和卸载曲线不重合,卸载曲线滞后于加载曲线。
两曲线线间所包容的面积就是加载和卸载循环中所损耗的能量,它消耗于摩擦力所作的功和接触变形功;(3)第一次卸载后,变形恢复不到第一次加载的起点,这说明有残余变形存在,经多次加载卸载后,加载曲线起点才和卸载曲线终点重合,残余变形才逐渐减小到零;(4)机床部件的实际刚度远比我们按实体估算的要小。
机械零件加工存在的问题及对策
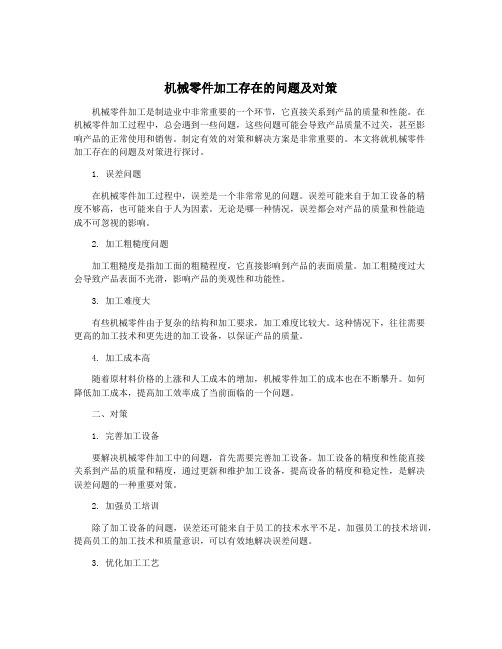
机械零件加工存在的问题及对策机械零件加工是制造业中非常重要的一个环节,它直接关系到产品的质量和性能。
在机械零件加工过程中,总会遇到一些问题,这些问题可能会导致产品质量不过关,甚至影响产品的正常使用和销售。
制定有效的对策和解决方案是非常重要的。
本文将就机械零件加工存在的问题及对策进行探讨。
1. 误差问题在机械零件加工过程中,误差是一个非常常见的问题。
误差可能来自于加工设备的精度不够高,也可能来自于人为因素。
无论是哪一种情况,误差都会对产品的质量和性能造成不可忽视的影响。
2. 加工粗糙度问题加工粗糙度是指加工面的粗糙程度,它直接影响到产品的表面质量。
加工粗糙度过大会导致产品表面不光滑,影响产品的美观性和功能性。
3. 加工难度大有些机械零件由于复杂的结构和加工要求,加工难度比较大。
这种情况下,往往需要更高的加工技术和更先进的加工设备,以保证产品的质量。
4. 加工成本高随着原材料价格的上涨和人工成本的增加,机械零件加工的成本也在不断攀升。
如何降低加工成本,提高加工效率成了当前面临的一个问题。
二、对策1. 完善加工设备要解决机械零件加工中的问题,首先需要完善加工设备。
加工设备的精度和性能直接关系到产品的质量和精度,通过更新和维护加工设备,提高设备的精度和稳定性,是解决误差问题的一种重要对策。
2. 加强员工培训除了加工设备的问题,误差还可能来自于员工的技术水平不足。
加强员工的技术培训,提高员工的加工技术和质量意识,可以有效地解决误差问题。
3. 优化加工工艺对于加工粗糙度过大的问题,可以通过优化加工工艺来解决。
采用更先进的加工方法和工艺,提高加工精度和表面质量,可以有效地解决加工粗糙度问题。
4. 研究新材料和新工艺5. 引进自动化生产线随着科技的不断发展,自动化生产线的应用越来越广泛。
引进自动化生产线可以有效地提高加工效率,降低产品的加工成本,提高产品的一致性和稳定性。
6. 建立质量管理体系为了有效地控制机械零件加工中的问题,建立质量管理体系是非常重要的。
数控机床加工误差原因及对策分析

数控机床加工误差原因及对策分析数控机床是当今制造业的主要设备之一。
数控机床生产效率高,运行速度快,加工精度高,成品质量好,成本相对较低。
但是,在实际生产过程中,经常会出现加工误差,影响生产效率和成品质量。
因此,分析数控机床加工误差原因并寻找对策是很必要的。
本文将探讨数控机床加工误差的原因,以及如何通过改进措施来减少误差的发生。
一、误差的种类数控机床加工误差通常包括以下几种:1.轨迹误差。
轨迹误差是指数控机床加工时导致实际加工轨迹与期望轨迹之间的误差。
2.定位误差。
定位误差是指数控机床在加工中出现的位置偏差。
定位误差可能由机床本身、工件、刀具等方面的原因引起。
3.回转误差。
回转误差是指数控机床在进行旋转加工时出现的偏差。
回转误差通常由转台本身、传动系统和工件等原因引起。
4.表面误差。
表面误差是指数控机床加工表面的粗糙度、平整度、垂直度和平行度等参数上的误差。
二、误差产生的原因1.机床本身的精度。
数控机床的精度与质量直接相关,是影响加工质量的最重要因素。
如果机床本身的精度不高,则会直接导致加工误差的发生。
2.工具刃磨质量。
如果刀具的刃磨质量不好,切屑排出不畅等问题,也容易引起加工误差。
3.刀具稳定性。
刀具的稳定性是指在加工过程中刀具的稳定性,如果刀具不稳定,则极易引起加工误差的发生。
4.机床几何精度调整。
机床几何精度调整直接影响加工误差发生的概率,如果机床几何精度调整不当,则会引起加工误差的出现。
5.机床零部件磨损。
随着机床的使用,部件常会出现磨损,进而影响加工精度。
三、解决方案1.提高加工前的加工过程控制。
在加工前加强对加工过程的控制,可通过模具设计等预处理阶段减少误差出现的可能性。
2.注意刀具选择。
选择质量高的刀具,并保持刀具在加工过程中的稳定性。
3.指导及培训操作人员。
操作人员要具备相应的知识和技能,遵循正确的加工流程,熟练使用数控机床,能够及时发现和解决数控机床加工过程中的问题。
4.定期机床保养。
机械零件加工存在的问题及对策
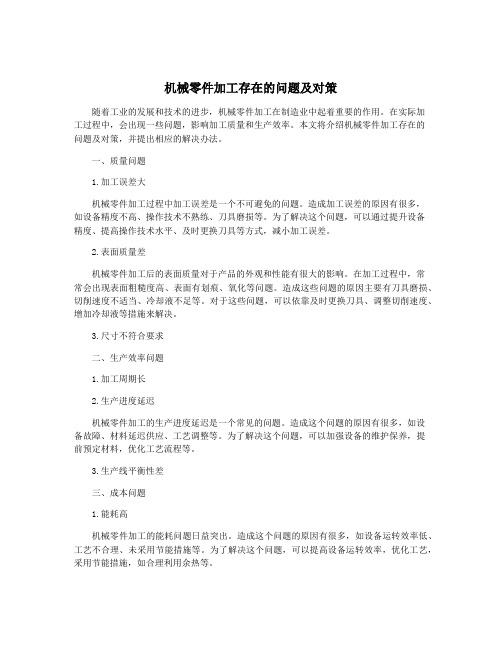
机械零件加工存在的问题及对策随着工业的发展和技术的进步,机械零件加工在制造业中起着重要的作用。
在实际加工过程中,会出现一些问题,影响加工质量和生产效率。
本文将介绍机械零件加工存在的问题及对策,并提出相应的解决办法。
一、质量问题1.加工误差大机械零件加工过程中加工误差是一个不可避免的问题。
造成加工误差的原因有很多,如设备精度不高、操作技术不熟练、刀具磨损等。
为了解决这个问题,可以通过提升设备精度、提高操作技术水平、及时更换刀具等方式,减小加工误差。
2.表面质量差机械零件加工后的表面质量对于产品的外观和性能有很大的影响。
在加工过程中,常常会出现表面粗糙度高、表面有划痕、氧化等问题。
造成这些问题的原因主要有刀具磨损、切削速度不适当、冷却液不足等。
对于这些问题,可以依靠及时更换刀具、调整切削速度、增加冷却液等措施来解决。
3.尺寸不符合要求二、生产效率问题1.加工周期长2.生产进度延迟机械零件加工的生产进度延迟是一个常见的问题。
造成这个问题的原因有很多,如设备故障、材料延迟供应、工艺调整等。
为了解决这个问题,可以加强设备的维护保养,提前预定材料,优化工艺流程等。
3.生产线平衡性差三、成本问题1.能耗高机械零件加工的能耗问题日益突出。
造成这个问题的原因有很多,如设备运转效率低、工艺不合理、未采用节能措施等。
为了解决这个问题,可以提高设备运转效率,优化工艺,采用节能措施,如合理利用余热等。
2.材料浪费严重3.人力成本高机械零件加工存在的问题主要集中在质量、生产效率和成本三个方面。
针对这些问题,可以采取相应的对策,如提升设备精度、调整工艺流程、优化设备配置、提高操作技术水平等,从而提高机械零件加工质量和生产效率,降低生产成本。
还需加强员工培训和技术提升,推动机械零件加工工艺的发展和创新。
数控加工产生误差的根源及解决方案

数控加工产生误差的根源及解决方案数控加工是利用数控技术通过控制机床和刀具相对运动的方式,对工件进行加工的一种工艺。
虽然数控加工相对手工加工来说具有高精度、高效率、高一致性等优点,但是由于一些原因还是会在实际应用中产生一些误差,下面我们对数控加工误差的根源及解决方案进行详细介绍。
一、误差产生的根源1.机床本身问题机床是数控加工的基础,如果机床本身精度不高,则会直接影响到加工的精度。
例如机床的重复定位精度、圆度等问题都会导致数控加工中的误差。
2.编程和操作问题编程和操作的问题也是数控加工中产生误差的重要原因。
编写的程序是否符合实际加工的要求、操作人员能否正确的操作数控设备、调整数控设备的参数等都会影响加工的精度。
3.工件材料和加工工艺工件的材料和加工工艺也是数控加工中产生误差的原因之一。
因为不同的材料及加工工艺的选用,需要有不同的加工参数设置,否则加工出来的零件尺寸不稳定,而且不同的材料具有不同的热膨胀系数,会使得加工出来的工件产生偏差。
二、误差的解决方案1.提高机床精度如何提高机床精度呢?首先我们要选用性能稳定、精度高的数控机床。
同时,在加工过程中要注意定期检查机床的重复定位精度、圆形度等指标,及时进行维护和保养。
2.优化编程和操作流程软件程序的编写和操作过程是决定加工精度的重要环节之一,因此编写程序时要结合实际加工要求,同时要对操作流程进行规范化和标准化,让操作流程尽量简单,便于操作人员进行操作。
3.优化材料和加工工艺合理选用材料及加工工艺,是提高精度的重要环节之一,因此选择合适的加工工艺的同时,要注意材料的热膨胀系数等性质,以此来保证加工出来的工件符合设计要求。
总之,数控加工误差的根源较多,但只要我们能够从机器、人员和程序三个方面入手,针对性的进行优化,加工精度是能够得到不断提高的。
加工工艺技术的误差对装配质量的影响分析
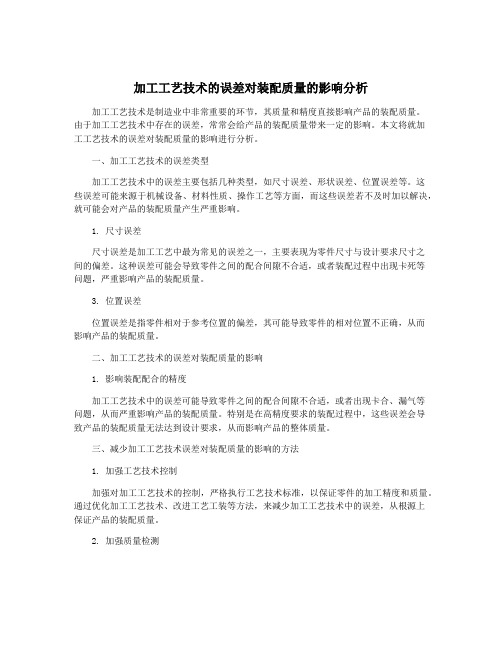
加工工艺技术的误差对装配质量的影响分析加工工艺技术是制造业中非常重要的环节,其质量和精度直接影响产品的装配质量。
由于加工工艺技术中存在的误差,常常会给产品的装配质量带来一定的影响。
本文将就加工工艺技术的误差对装配质量的影响进行分析。
一、加工工艺技术的误差类型加工工艺技术中的误差主要包括几种类型,如尺寸误差、形状误差、位置误差等。
这些误差可能来源于机械设备、材料性质、操作工艺等方面,而这些误差若不及时加以解决,就可能会对产品的装配质量产生严重影响。
1. 尺寸误差尺寸误差是加工工艺中最为常见的误差之一,主要表现为零件尺寸与设计要求尺寸之间的偏差。
这种误差可能会导致零件之间的配合间隙不合适,或者装配过程中出现卡死等问题,严重影响产品的装配质量。
3. 位置误差位置误差是指零件相对于参考位置的偏差,其可能导致零件的相对位置不正确,从而影响产品的装配质量。
二、加工工艺技术的误差对装配质量的影响1. 影响装配配合的精度加工工艺技术中的误差可能导致零件之间的配合间隙不合适,或者出现卡合、漏气等问题,从而严重影响产品的装配质量。
特别是在高精度要求的装配过程中,这些误差会导致产品的装配质量无法达到设计要求,从而影响产品的整体质量。
三、减少加工工艺技术误差对装配质量的影响的方法1. 加强工艺技术控制加强对加工工艺技术的控制,严格执行工艺技术标准,以保证零件的加工精度和质量。
通过优化加工工艺技术、改进工艺工装等方法,来减少加工工艺技术中的误差,从根源上保证产品的装配质量。
2. 加强质量检测加强对产品零部件的质量检测,及时发现并纠正加工工艺技术中的误差。
通过建立完善的质量检测体系,对产品的零部件进行全面的质量检测,及时发现并解决加工工艺技术中的误差问题,从而保证产品的装配质量。
3. 提高设备精度提高加工设备的精度和稳定性,降低加工工艺技术中的误差。
通过替换或升级加工设备、定期维护设备、优化设备调整方法等途径,以保证产品的零部件加工精度和质量。
浅谈机械加工误差的分析
浅谈机械加工误差的分析机械加工误差是指实际加工零件的尺寸、形状、位置、表面质量等与设计要求或测量结果之间的偏差。
在机械加工中, 误差是不可避免的, 因此对机械加工误差进行分析是非常重要的。
本文将详细分析机械加工误差的产生原因、种类以及对策措施,希望能够对读者有所帮助。
一、机械加工误差的产生原因1. 加工设备问题加工设备是机械加工的基础,设备的精度、稳定性和可靠性直接影响着加工零件的质量。
设备的老化、磨损和维护不当是导致机械加工误差的重要原因之一。
2. 工艺因素在机械加工中,工艺参数的选择直接关系到零件的加工质量。
切削速度、进给量、切削深度等技术参数的合理选择能够有效减小误差的产生。
3. 材料因素不同材料的物理性质不同,机械加工对材料的硬度、韧性、拉伸性等性能要求也不同,如果材料的性能不符合要求,会导致机械加工误差的产生。
4. 操作人员技术水平操作人员的技术水平直接影响着加工零件的质量,操作人员对设备的熟练程度、对工艺参数的把握能力、对材料性能的了解程度等都是直接影响误差产生的因素。
1. 尺寸误差尺寸误差是指零件的实际尺寸与设计要求的尺寸之间的偏差,通常包括线性尺寸误差和非线性尺寸误差。
2. 形状误差形状误差是指零件的实际形状与设计要求的形状之间的偏差,通常包括平面度、圆度、圆柱度、并行度、垂直度等。
1. 加强设备维护定期对加工设备进行维护保养、及时更换老化磨损的零部件,以保证设备的精度、稳定性和可靠性。
3. 严格控制材料质量在零件加工过程中,选用合格的优质材料,并对材料进行必要的热处理,以确保材料的性能符合加工要求。
5. 使用适当的检测手段在机械加工过程中,使用适当的检测手段对零件进行检验,及时发现误差并采取措施进行调整和修正。
除了上述措施之外,还可以通过优化加工工艺、提高加工精度和改进加工工艺等方法来减小机械加工误差。
机械加工误差是在机械加工过程中难以避免的问题,了解误差产生的原因和种类,采取相应的对策措施是保证零件加工质量的关键。
机械零件加工存在的问题及对策
机械零件加工存在的问题及对策机械零件加工是工业生产中的重要环节,但在实际操作中常常会遇到一些问题。
本文将探讨机械零件加工存在的问题,并提出相应的对策。
第一个问题是加工误差。
由于机械加工过程中不可避免地存在加工误差,导致加工后的零件尺寸与设计要求不符。
解决这个问题的对策有以下几点:1. 优化工艺流程:通过优化工艺流程,减少加工误差的产生。
合理设置刀具路径、减小切削力、控制切削速度等。
2. 提高加工精度:使用更加精密的机械设备和仪器,提高加工精度。
使用高精度的数控机床、高精度的测量仪器等。
3. 加强质量控制:建立完善的质量控制体系,包括零件加工前的准备工作、加工过程中的监控和质量检验等。
还可以通过加强对操作人员的培训和监督,提高他们的专业技术水平和责任心。
第二个问题是加工效率低下。
机械零件加工过程中,由于一些原因,导致加工效率低下,影响生产进度和成本控制。
应采取以下对策:1. 提高设备利用率:合理安排生产计划,避免设备闲置或空转。
定期对设备进行维护和保养,确保设备的正常运行和长期稳定工作。
2. 优化加工工艺:通过重新设计工艺流程、调整工序和加工参数等措施,提高加工效率。
采用先进的数控设备和自动化生产线,可以快速完成生产任务,提高生产效率。
3. 加强工人培训:提高操作人员的技术水平和工作效率,减少操作错误和浪费。
可以通过定期培训、熟练操作和经验交流等方式,提高工人的工作能力。
第三个问题是材料浪费严重。
在机械零件加工过程中,由于没有合理使用材料或存在加工误差等原因,导致材料的浪费。
针对这个问题,应采取以下对策:1. 优化材料利用率:通过优化切削方向、减少切削余量、合理选择材料和切削工具等方式,提高材料利用率。
对于一些可回收利用的材料,应进行回收再利用,减少材料损失。
2. 强化质量控制:加强对零件加工过程的质量控制,减少加工误差,避免零件被废品。
可以通过采用先进的测量仪器和工作方式,进行实时监控和及时调整,确保零件尺寸的准确性和稳定性。
机械加工误差产生的原因及措施
机械加工误差产生的原因及措施汇报人:2024-01-01•机械加工误差产生的原因•减小机械加工误差的措施•机械加工误差的补偿措施目录•提高机械加工精度的途径01机械加工误差产生的原因原理误差总结词原理误差是由于加工原理的不完善而导致的误差。
详细描述原理误差主要表现在机床或刀具的转动和移动过程中,由于设计原理或机构原理的限制,导致加工出的零件与理论值存在偏差。
例如,齿轮加工中,由于齿轮的齿廓理论是完美的,但在实际加工中,由于机床和刀具的精度限制,无法完全复制理想的齿廓形状,从而产生原理误差。
工具、夹具与机床的制造误差总结词工具、夹具与机床的制造误差是由于这些设备的制造精度不足而导致的误差。
详细描述工具、夹具和机床是机械加工中的重要组成部分,它们的制造精度直接影响着零件的加工精度。
例如,刀具的制造误差会导致加工表面的粗糙度不均匀,夹具的定位精度不高会导致零件的位置精度偏差,机床的主轴回转误差则会影响零件的圆度等。
调整误差是由于加工过程中的调整不准确而导致的误差。
详细描述在机械加工过程中,需要对工具、夹具和机床进行多次调整,如刀具的更换、夹具的定位、机床的校准等。
由于调整过程中的人为操作和设备本身的特性,往往会产生一定的调整误差。
例如,刀具的安装角度偏差会影响切削深度和表面粗糙度,夹具的调整不当会导致零件的定位不准确。
总结词VS总结词测量误差是由于测量设备的精度限制和测量方法的不完善而导致的误差。
要点一要点二详细描述测量是机械加工中不可或缺的一环,但由于测量设备的精度限制和测量方法的不完善,往往会产生测量误差。
例如,使用卡尺测量时,由于卡尺的刻度精度有限,会导致测量结果存在误差;同时,测量方法的不正确也会导致误差的产生。
如测量时没有保证工件与卡尺之间的平行度或垂直度,就会产生测量误差。
02减小机械加工误差的措施直接减小或消除误差法直接减小或消除误差法是通过直接减少或消除原始误差来降低加工误差的方法。
例如,通过提高机床的几何精度、减小刀具和夹具的制造误差、提高工件的定位精度等措施,可以有效地减小加工误差。
机械加工工艺的技术误差问题及对策
机械加工工艺的技术误差问题及对策机械加工工艺的技术误差是指在加工过程中由于工艺、设备、操作等因素导致的加工尺寸与设计要求之间的偏差。
这些误差会对零件的质量和性能造成不利影响,因此需采取相应的对策来减小误差。
本文将从设备选型、工艺参数控制、工艺改进等方面探讨机械加工工艺的技术误差问题及对策。
一、设备选型方面的对策设备选型是机械加工工艺误差控制的重要方面。
在选购加工设备时,应确保设备的精度、稳定性、刚性等方面符合加工要求,以减小误差的产生。
1.选择精度更高的设备对于要求加工高精度零件的工艺,应选择精度更高的加工设备,如高精度数控机床等,以提高加工精度,并减小误差的产生。
2.选用稳定性较好的设备设备的稳定性对加工精度影响很大。
选用稳定性较好的设备可以减小外界因素(如温度、振动等)对加工精度的影响,降低误差的发生率。
3.考虑设备的刚性刚性是指设备在加工过程中承受载荷时变形程度的能力。
设备刚性好,能够更好地抵抗加工过程中的振动和变形,从而提高加工精度,降低误差的发生。
二、工艺参数控制方面的对策控制合理的工艺参数是减小机械加工工艺误差的关键,下面将从切削速度、进给量、切削深度等角度分析工艺参数的控制对策。
1.合理控制切削速度切削速度是指加工过程中工件与刀具相对运动的速度。
切削速度的选择要根据加工材料的硬度、材料的切削性能以及机床和刀具的性能等因素综合考虑。
如果切削速度过快,容易导致刀具寿命下降,加工表面质量下降,误差增大;而切削速度过慢,则不仅会影响生产效率,还容易产生负载过重等问题。
在实际加工过程中要根据具体情况调整切削速度,以确保加工精度。
三、工艺改进方面的对策工艺改进是减小机械加工工艺误差的重要手段。
通过改进现有的工艺流程、技术手段来减小误差的产生,提高加工精度。
1.优化工艺流程通过优化加工工艺流程,合理安排加工顺序,避免二次调整导致误差的累积。
合理的工艺流程有助于提高加工效率,降低误差的发生率。
2.改进工艺技术手段利用先进的数控技术、自动化技术以及传感技术等,改进加工工艺技术手段,提高机床的加工精度,减小误差的产生。
- 1、下载文档前请自行甄别文档内容的完整性,平台不提供额外的编辑、内容补充、找答案等附加服务。
- 2、"仅部分预览"的文档,不可在线预览部分如存在完整性等问题,可反馈申请退款(可完整预览的文档不适用该条件!)。
- 3、如文档侵犯您的权益,请联系客服反馈,我们会尽快为您处理(人工客服工作时间:9:00-18:30)。
加工过程中存在的误差
收藏此信息打印该信息添加:不详来源:未知
(一)工艺系统受力变形引起的误差
1、基本概念
机械加工工艺系统在切削力、夹紧力、惯性力、重力、传动力等的作用下,会产生相应的变形,从而破坏了刀具和工件之间的正确的相对位置,使工件的加工精度下降。
如下图a示,车细长轴时,工件在切削力的作用下会发生变形,使加工出的轴出现中间粗两头细的情况;又如在内圆磨床上进行切入式磨孔时,下图b,由于内圆磨头轴比较细,磨削时因磨头轴受力变形,而使工件孔呈锥形。
垂直作用于工件加工表面(加工误差敏感方向)的径向切削分力Fy与工艺系统在该方向上的变形y之间的比值,称为工艺系统刚度k系,即
式中的变形y不只是由径向切削分力Fy所引起,垂直切削分力Fz与走刀方向切削分力Fx 也会使工艺系统在y方向产生变形,故
y=yFx+yFy+yFz
2、工件刚度
工艺系统中如果工件刚度相对于机床、刀具、夹具来说比较低,在切削力的作用下,工件由于刚度不足而引起的变形对加工精度的影响就比较大,其最大变形量可按材料力学有关公式估算。
3、刀具刚度
外圆车刀在加工表面法线(y)方向上的刚度很大,其变形可以忽略不计。
镗直径较小的内孔,刀杆刚度很差,刀杆受力变形对孔加工精度就有很大影响。
刀杆变形也可以按材料力学有关公式估算。
4、机床部件刚度
1)机床部件刚度
机床部件由许多零件组成,机床部件刚度迄今尚无合适的简易计算方法,目前主要还是用实验方法来测定机床部件刚度。
分析实验曲线可知,机床部件刚度具有以下特点:
(1)变形与载荷不成线性关系;
(2)加载曲线和卸载曲线不重合,卸载曲线滞后于加载曲线。
两曲线线间所包容的面积就是加载和卸载循环中所损耗的能量,它消耗于摩擦力所作的功和接触变形功;
(3)第一次卸载后,变形恢复不到第一次加载的起点,这说明有残余变形存在,经多次加载卸载后,加载曲线起点才和卸载曲线终点重合,残余变形才逐渐减小到零;
(4)机床部件的实际刚度远比我们按实体估算的要小。
2)影响机床部件刚度的因素
(1)结合面接触变形的影响
(2)摩擦力的影响
(3)低刚度零件的影响
(4)间隙的影响
5、工艺系统刚度及其对加工精度的影响
在机械加工过程中,机床、夹具、刀具和工件在切削力作用下,都将分别产生变形y机、y 夹、y刀、y工,致使刀具和被加工表面的相对位置发生变化,使工件产生加工误差。
工艺系统刚度的倒数等于其各组成部分刚度的倒数和。
工艺系统刚度对加工精度的影响主要有以下几种情况:
1)由于工艺系统刚度变化引起的误差
工艺系统的刚度随受力点位置的变化而变化。
例如:用三爪卡盘夹紧工件车削外圆的加工,随悬壁长度的增加,刚度将越来越小。
因而,车出的外圆将呈锥形。
2)由于切削力变化引起的误差
加工过程中,由于工件的加工余量发生变化、工件材质不均等因素引起的切削力变化,使工艺系统变形发生变化,从而产生加工误差。
若毛坯A有椭圆形状误差(如下图)。
让刀具调整到图上双点划线位置,由图可知,在毛坯椭圆长轴方向上的背吃刀量为ap1,短轴方向上的背吃刀量为ap2。
由于背吃刀量不同,切削力不同,工艺系统产生的让刀变形也不同,对应于ap1产生的让刀为y1,对应于ap2产生的让刀为y2,故加工出来的工件B仍然存在椭圆形状误差。
由于毛坯存在圆度误差△毛=ap1-ap2,因而引起了工件的圆度误差△工=y1-y2,且△毛愈大,△工愈大,这种现象称为加工过程中的毛坯误差复映现象。
△工与△毛之比值ε称为误差复映系数,它是误差复映程度的度量。
尺寸误差(包括尺寸分散)和形状误差都存在复映现象。
如果我们知道了某加工工序的复映系数,就可以通过测量毛坯的误差值来估算加工后工件的误差值。
3)由于夹紧变形引起的误差
工件在装夹过程中,如果工件刚度较低或夹紧力的方向和施力点选择不当,将引起工件变形,造成相应的加工误差。
4)其它作用力的影响
6、减小工艺系统受力变形的途径
由前面对工艺系统刚度的论述可知,若要减少工艺系统变形,就应提高工艺系统刚度,减少切削力并压缩它们的变动幅值。
具体如下:
1)提高工艺系统刚度
(1)提高工件和刀具的刚度减小刀具、工件的悬伸长度:以提高工艺系统的刚度;
(2)减小机床间隙,提高机床刚度:采用预加载荷,使有关配合产生预紧力,而消除间隙。
(3)采用合理的装夹方式和加工方式
2)减小切削力及其变化
合理地选择刀具材料,增大前角和主偏角,对工件材料进行合理的热处理以改善材料地加工性能等,都可使切削力减小。
(二)工艺系统受热变形引起的误差
工艺系统热变形对加工精度的影响比较大,特别是在精密加工和大件加工中,由热变形所引起的加工误差有时可占工件总误差的40%~70%。
机床、刀具和工件受到各种热源的作用,温度会逐渐升高,同时它们也通过各种传热方式向周围的物质和空间散发热量。
当单位时间传入的热量与其散出的热量相等时,工艺系统就达到了热平衡状态。
1、工艺系统的热源
内部热源:如系统内部的摩擦热(由轴承副、齿轮副等产生)、切削热等;
外部热源:如外部环境温度、阳光辐射等。
2、工艺系统受热变形引起的误差
1)工件受热变形:工件受热温度升高后,热伸长量△L为:△L=αL△t
式中:α为工件材料的热膨胀系数; L为工件长度;△t为工件的温升。
例如:死顶尖装夹工件时,热变形将造成工件弯曲。
在磨床上为消除热变形的影响,而采用弹簧顶尖。
2)机床受热变形:当机床受热不均时,造成机床部件产生变形。
例如:机床主轴前、后端受热不均,将造成主轴抬高,并倾斜。
3)刀具受热变形:刀具受热以后,引起刀具热伸长,刀尖位置发生变化,因而影响加工精度。
3、减小工艺系统热变形的途径
1.减少发热和隔热
2.改善散热条件
3.均衡温度场
4.改进机床结构
5.加快温度场的平衡
6.控制环境温度
(三)刀具的磨损引起的误差:
刀具在切削过程中,由于摩擦,刀具将产生磨损,使刀具尺寸发生变化,而造成加工误差。
三、加工后存在的误差:
(一)工件残余应力引起的误差
1、基本概念
没有外力作用而存在于零件内部的应力,称为残余应力(又称内应力)。
工件上一旦产生内应力之后,就会使工件金属处于一种高能位的不稳定状态,它本能地要向低能位的稳定状态转化,并伴随有变形发生,从而使工件丧失原有的加工精度。
2、内应力的产生
热加工中内应力的产生
在热处理工序中由于工件壁厚不均匀、冷却不均、金相组织的转变等原因,使工件产生内应力。
上图示一个内外壁厚相差较大的铸件。
浇铸后,铸件将逐渐冷却至室温。
由于壁1和壁2比较薄,散热较易,所以冷却比较快。
壁3比较厚,所以冷却比较慢。
当壁1和壁2从塑性状态冷到弹性状态时,壁3的温度还比较高,尚处于塑性状态。
所以壁1和壁2收缩时壁3
不起阻挡变形的作用,铸件内部不产生内应力。
但当壁3也冷却到弹性状态时,壁1和壁2的温度已经降低很多,收缩速度变得很慢。
但这时壁3收缩较快,就受到了壁1和壁2的阻碍。
因此,壁3受拉应力的作用,壁1和2受压应力作用,形成了相互平衡的状态。
如果在这个铸件的壁1上开一个口,则壁1的压应力消失,铸件在壁3和2的内应力作用下,壁3收缩,壁2伸长,铸件就发生弯曲变形,直至内应力重新分布达到新的平衡为止。
推广到一般情况,各种铸件都难免产生冷却不均匀而形成的内应力,铸件的外表面总比中心部分冷却得快。
特别是有些铸件(如机床床身),为了提高导轨面的耐磨性,采用局部激冷的工艺使它冷却更快一些,以获得较高的硬度,这样在铸件内部形成的内应力也就更大些。
若导轨表面经过粗加工剥去一些金属,这就象在图中的铸件壁1上开口一样,必将引起内应力的重新分布并朝着建立新的应力平衡的方向产生弯曲变形。
为了克服这种内应力重新分布而引起的变形,特别是对大型和精度要求高的零件,一般在铸件粗加工后安排进行时效处理,然后再作精加工。
丝杠一类的细长轴经过车削以后,棒料在轧制中产生的内应力要重新分布,产生弯曲,如下图示。
冷校直就是在原有变形的相反方向加力F,使工件向反方向弯曲,产生塑性变形,以达到校直的目的。
在F力作用下,工件内部的应力分布如图b所示。
当外力F去除以后,弹性变形部分本来可以完成恢复而消失,但因塑性变形部分恢复不了,内外层金属就起了互相牵制的作用,产生了新的内应力平衡状态,如图c所示,所以说,冷校直后的工件虽然减少了弯曲,但是依然处于不稳定状态,还会产生新的弯曲变形。
3、减小内应力变形误差的途径
1.改进零件结构——设计零件时,尽量做到壁厚均匀,结构对称,以减少内应力的产生。
2.增设消除内应力的热处理工序
1)高温时效:缓慢均匀的冷却,适用于铸、锻、焊件;
2)低温时效:缓慢均匀的冷却,适用于半精加工后的工件,主要是消除工件的表面应力;3)自然时效:自然释放。
3.合理安排工艺过程——粗加工和精加工宜分阶段进行,使工件在粗加工后有一定的时间来松弛内应力。
(二)测量误差:
1、量具本身的制造误差
2、测量条件引起的误差
1)冷却后测量与加工后马上测量尺寸有变化;2)测量力的变化也引起测量尺寸的变化。