金刚石涂层工具制备及其应用(陈明,孙方宏,马玉平著)思维导图
金刚石涂层刀具的制备及其切削性能研究

联系人:王世伟,工程师,河南.安阳(455004),安钢集团冷轧有限责任公司综合办公室; 收稿日期:2019 2 16
2019年第 3期 河 南 冶 金 · 1 5·
除沉积过程中元素 Co对金刚石薄膜生长的不利影 响;(4)在丙酮溶液中超声清洗 5min。 1.2 金刚石薄膜的制备
0 前言 金刚石是目前已知的硬度最高的物质,其独特
的结构决定了它具有许多优异的物理化学性质,如 具有最高的硬度和杨氏模量,极高的耐磨性,超高的 热导率和 极 低 的 热 膨 胀 系 数,优 异 的 化 学 稳 定 性 等[1-2]。将金刚石作为涂层材料制备成金刚石涂层 刀具可以显著增强刀具的耐用度,提高刀具的使用 寿命,减少切削过程中的污染,实现绿色加工。金刚 石涂层刀具常用来加工陶瓷、碳纤维材料、钛合金等 非铁难加工材料,发达国家制造业中涂层刀具的使 用量已经超过 70%,国内的使用量较低,因此具有 广阔的 市 场 前 景 。 [3-4] 热 丝 化 学 气 相 沉 积 法 (hot filamentchemicalvapordeposition,HFCVD)是指用灼 热的钨丝或钽丝,加热分解碳物质,激活化学气相反 应来制备金刚石膜的一种工艺方法。热丝法设备操 作简单,工艺参数易控制,价格低廉,可以在各种复 杂形状刀具上沉积涂层,已经在国外得到了大规模 的商业化应用[5-6]。
微细刀具表面金刚石涂层的制备及其应用基础研究

微细刀具表面金刚石涂层的制备及其应用基础研究目录第一章绪论 (1)1.1课题来源 (1)1.2课题的研究意义 (1)1.3国内外研究现状综述 (4)1.3.1CVD金刚石薄膜的制备及其耐磨损性能研究 (4)1.3.2微细切削加工技术 (7)1.3.3HFCVD法制备金刚石薄膜的温度场仿真研究 (10)1.3.4金刚石涂层刀具的制备及其应用研究 (11)1.3.5CVD金刚石涂层微细刀具的制备及其应用研究 (19)1.4本文主要研究内容 (22)第二章CVD金刚石薄膜的制备及其耐磨损性能研究 (27)2.1引言 (27)2.2金刚石薄膜的沉积原理 (27)2.3HFCVD法制备金刚石薄膜的设备与流程 (29)2.4CVD金刚石薄膜的表征分析 (31)2.4.1表面形貌 (31)2.4.2表面粗糙度 (32)2.4.3薄膜晶粒取向 (32)2.4.4拉曼光谱分析 (33)2.5膜基结合强度研究 (34)2.6MCD和NCD薄膜耐磨损性能研究 (35)2.6.1实验样品准备 (35)2.6.2实验过程描述 (37)2.6.3实验结果分析 (37)2.7本章小结 (43)第三章CVD金刚石涂层微细刀具制备过程温度场仿真研究 (45) - XI -3.1引言 (45)3.2计算流体动力学基础理论与F LUENT软件概述 (45)3.3单排微细刀具的温度场仿真与实验验证研究 (47)3.3.1模型的建立 (47)3.3.2仿真结果与讨论 (48)3.3.3测温实验验证 (49)3.4批量化微细刀具制备参数的仿真与优化 (51)3.4.1模型的建立 (51)3.4.2仿真结果与讨论 (52)3.4.3沉积实验验证 (56)3.5本章小结 (58)第四章CVD金刚石涂层微细刀具的制备工艺优化研究 (59) 4.1引言 (59)4.2微细刀具预处理工艺的优化 (60)4.2.1微细刀具的预处理过程 (60)4.2.2微细刀具预处理区域的优化 (62)4.2.3微细刀具预处理时间的优化 (64)4.3CVD金刚石涂层微细刀具的沉积工艺参数优化 (66)4.3.1形核反应气压的优化 (67)4.3.2基体温度的优化 (69)4.3.3碳源浓度的优化 (70)4.4动态掺硼过渡层工艺 (71)4.5本章小结 (76)第五章石墨加工用金刚石涂层微细刀具的制备与应用研究 (77) 5.1引言 (77)5.2石墨与金刚石薄膜的摩擦学性能研究 (77)5.2.1摩擦实验的准备 (78)5.2.2石墨与金刚石薄膜摩擦过程分析 (78)5.2.3石墨与金刚石薄膜摩擦磨损表面分析 (79)上海交通大学博士学位论文5.3钻削石墨时微细钻头涂层类型优化 (81)5.3.1微细钻头上不同涂层的性能表征 (81)5.3.2不同涂层微细钻头钻削石墨性能比较 (83)5.4微米金刚石涂层微细石墨钻头涂层厚度的优化 (86)5.4.1不同厚度微米金刚石薄膜性能表征 (86)5.4.2不同厚度MCD涂层微细钻头加工高纯石墨切削性能比较 (89) 5.5本章小结 (93)第六章CVD金刚石涂层微细PCB钻头的制备与应用研究 (95) 6.1引言 (95)6.2PCB板与CVD金刚石薄膜之间的摩擦学性能 (96)6.2.1硬质合金球表面金刚石薄膜的表征 (96)6.2.2PCB板与金刚石薄膜摩擦过程分析 (96)6.2.3金刚石薄膜及PCB板磨损表面分析 (97)6.3薄膜类型与厚度对微细PCB钻头切削性能的影响 (100)6.3.1涂层薄膜类型优化 (100)6.3.2NCD涂层厚度的优化 (105)6.4本章小结 (108)第七章CVD金刚石涂层微细铝合金刀具的制备与应用研究 (111) 7.1引言 (111)7.2铝合金与CVD金刚石薄膜的摩擦学性能 (111)7.2.1摩擦实验的准备 (112)7.2.2铝合金与金刚石薄膜间的摩擦实验过程分析 (113)7.2.3摩擦副中对磨区域的磨损表面分析 (114)7.3金刚石涂层微细铝合金钻头的优化制备 (117)7.3.1涂层类型对微细铝合金钻头钻削性能的影响 (117)7.3.2NCD涂层微细铝合金钻头涂层厚度的优化 (122)7.4本章小结 (126)第八章总结与展望 (127)目录8.1本文完成的主要研究工作和结论 (127)8.2本文主要创新点 (132)8.3下一步研究工作 (133)参考文献 (135)攻读博士学位期间获得的奖励 (149)致谢 (151)附录应用证明1 (153)附录应用证明2 (154)附录应用证明3 (155)- XIV -第一章绪论1.1 课题来源本课题来源于国家自然科学基金项目“纳米金刚石涂层微铣钻刀具制备新方法及应用基础研究”(项目编号:51375011)和上海市“晨光计划”项目“微/纳米金刚石多层复合膜摩擦学性能及其工具应用研究”(No. 12CG11)。
图层金刚石

三、涂层金刚石的发展研究现状
(2)硬质合金基体中的Co具有催石墨化的作用;
(3)金刚石与WC-Co硬质合金热膨胀系数不匹配导致 涂层内存在较大的残余应力。
选择合适的厚度是金刚石涂层刀具合理性价比的关键。
CVD金刚石薄膜太薄,磨损快,刀具使用寿命不高; CVD金刚石薄膜太厚,与硬质合金基体的粘附性变差 且制造成本增加。
但材料添加了硬质耐磨 颗粒作为强化剂,这无 疑增加了这些材料加工 难度,这些硬质颗粒会 造成刀具过早磨损产生 大量切削热。
一、涂层金刚石刀具出现的历史背景
因此,多数刀具用户认为, 普通刀具已经不能满足需 求,而迫切需要一种耐磨 性更高、能稳定实现高精、 高效、寿命更长的超硬刀 具。
金刚石涂层刀具因其具有 十分接近天然金刚石的硬 度和耐磨性、高的弹性模 量、极高的热导率、良好 的自润滑性和化学稳定性 等优异性能,成为加工难 加工材料的理想刀具。
三、涂层金刚石的发展研究现状
典型的硬质合金表面预处理方法主要有:
(1)除去或钝化刀具表面层的粘结相Co; (2)施加过渡层; (3)机械处理等。 在实际应用中,为了更好地提高金刚石薄膜与硬质合 金基体的结合强度,往往同时综合采用多种表面预处 理方法。
广东工业大学匡同春等人发表了《CVD金刚石涂层硬质
石的热膨胀系数最为接近,因此一直被认为是CVD金 刚石涂层较为理想的基体材料。 缺点:由于Si3N4陶瓷本身脆性大,抗冲击性能差,一
二、涂层金刚石刀具的含义及其组成
般认为,Si3N4基金
刚石涂层刀具仅宜 用于精加工,而不 宜进行冲击切削加工。
(2) WC系硬质合金
二、涂层金刚石刀具的含义及其组成
四、涂层金刚石刀具的发展前景展望
《金刚石涂层刀具》课件

优点:可以提高刀具的使用寿 命,降低加工成本,提高加工
精度和效率
原料准备:金刚石粉、粘结剂、溶剂等 混合搅拌:将金刚石粉与粘结剂、溶剂混合均匀 涂覆:将混合好的金刚石粉涂覆在刀具表面 固化:将涂覆好的刀具放入固化炉中,加热固化 打磨抛光:对固化后的刀具进行打磨抛光,提高刀具的表面质量 检测:对刀具进行性能检测,确保其符合使用要求
PPT,a click to unlimited possibilities
汇报人:PPT
CONTENTS
PART ONE
PART TWO
特性:耐磨性高、耐热性好、 硬度高、化学稳定性好
金刚石涂层刀具是一种在刀具 表面涂覆一层金刚石颗粒的刀 具
应用领域:广泛应用于机械加 工、航空航天、汽车制造等领
挑战:金刚石涂层刀具的制造 过程中,需要解决金刚石涂层 的加工精度和表面粗糙度问题
解决方案:采用先进的加工技 术和设备,提高金刚石涂层刀 具的加工精度和表面粗糙度
挑战:金刚石涂层刀具在加工过程中容易磨损 解决方案:采用先进的涂层技术,提高刀具的耐磨性 挑战:金刚石涂层刀具在加工过程中容易产生热量 解决方案:采用冷却技术,降低刀具的温度,提高加工精度 挑战:金刚石涂层刀具在加工过程中容易产生振动 解决方案:采用先进的加工工艺,降低刀具的振动,提高加工
在汽车、航空航天、电子等领 域,金刚石涂层刀具被广泛用 于磨削和研磨加工
金刚石涂层刀具在磨削和研磨 中的应用广泛,可以提高加工 效率和精度
金刚石涂层刀具在磨削和研磨 加工中具有耐磨、耐热、耐腐
蚀等优点
金刚石涂层刀具在磨削和研磨 加工中可以实现高精度、高效
率的加工效果
医疗领域:用于制造手术刀、 牙科钻头等医疗器械
6第十一章火焰法沉积金刚石薄膜(1)PPT课件

二、原料
气体:所用气体均为工业用气体,纯度分别为: C2H2 99.7%; O2 99.5%; H2 99.7%。
基底:钼,纯度为99.5%。
基底上下底面均用砂纸磨光,沉积表面再进行 抛光处理,下底面磨光的目的是为了保证基底与水 冷铜台接触良好。
11
三、合成条件
本实验合成条件范围如下: 气氛:空气; 压力(KPa):101 反应气体: O2+C2H2+H2; O2(L/min)1~5; C2H2 (L/min) 1~5; H2 (L/min)0~5; 基底: Mo; 基底温度:800-950℃。
对于一般样品,沉积温度在800~950℃之间,可以 采用红外光学高温计来测量。对于用于低温测量且要 求准确度较高的样品,则采用图11-2所示热电偶进行 测温。本方法的优点是测温范围宽(20~1500℃),测温 准确,但对于一些薄样品及难加工样品则不能采用此 方法。
8
9
热电偶由X-Y记录T,℃),典型的T-△t图 形见图11-3。可以发现, 在沉积时,进入火焰内 基底的温度很快就达到 平衡值,其后一直稳定 在该值直到结束。
第十一章 火焰法沉积金刚石薄膜
1
第一节 概 述 炔(C21H928)燃8年烧,火H焰iro在se大首气次中采合用成氧出(O了2)金-乙刚 石薄膜。
燃烧气体采用O2,和C-H化合物(如 C2H2、C2H4、C3H8和CH4)的混合气体, 常用的是C2H2与O2的混合气体,这种气 体被引入燃烧嘴并在空气中不完全燃烧, 基底放在有水冷装置的支持台上,并置于 燃烧火焰的内焰当中.当具有相当高温的 内焰喷到600~1100℃的基底上时,就会 形成金刚石。
〔2)火焰枪及位置控制系统: 火焰枪为普通气焊用焊枪。喷口内径为φ0.5~1.0mm,由
【实用】金刚石薄膜PPT资料

新一代计算机,使同体积计算机功能将扩大二万倍或体积 热沉领域:金刚石在室温下具有最高的热导率,是铜、银的5倍,又是良好的绝缘体,因而是大功率激光器件、微波器件、高集成电子
器件的理想散热材料。
大大缩小,同时抗酸碱、搞幅射、抗高温,从而能使计算 工具领域:随着科技的发展,需要大量加工和使用轻量化、高强度的材料,用具有最高硬度的金刚石制成的刀具所显示出来的长寿命
❖ 五、金刚石薄膜 工具还能加工各种超硬材料;
❖ 六、美、日利用金刚石薄膜 能发射冷阴极电子的特点制
造出高清晰、超薄、超大屏幕的电视机、计算机显示器,
而且极省电。
金刚石薄膜性质
❖ 金刚石薄膜除了具有与天然金刚石相同的晶体结构,也具 有高硬度、高耐磨、宽的禁带宽度、宽的光波透过性、耐 腐蚀等特性。但其特性强烈依赖于制备方法和沉积条件, 取决于金刚石的纯度和质量、杂质和缺陷的含量、微观形 貌等诸多因素,同时也取决于所采用的测量方法。 目前,高质量金刚石薄膜的硬度、致密度、热导率、折射 率、介电常数等指标已达到或接近天然金刚石。
成的金刚石价格昂贵。
热沉领域:金刚石在室温下具有最高的热导率,是铜、银的5倍,又是良好的绝缘体,因而是大功率激光器件、微波器件、高集成电子
器五件、的 金理刚想石散薄不热膜材工磨料具。还损能加的工各摄种超像硬材机料;、照相机等各种红外光学镜头;
热沉领域:金刚石在室温下具有最高的热导率,是铜、银的5倍,又是良好的绝缘体,因而是大功率激光器件、微波器件、高集成电子 器件的理想散热材料。
❖ 目前国际上开发方向有六个方面。 目前,高质量金刚石薄膜的硬度、致密度、热导率、折射率、介电常数等指标已达到或接近天然金刚石。
根据天然金刚石存在的事实以及热力学数据,人们一直想通过碳的另一同素异形体——石墨来合成金刚石。
CVD金刚石涂层硬质合金刀具TaxC过渡层的制备及其性能研究
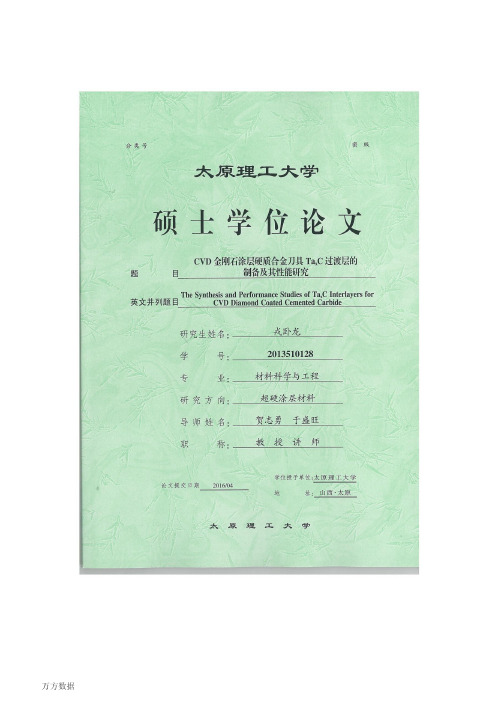
太原理工大学硕士研究生学位论文CVD金刚石涂层硬质合金刀具Ta x C过渡层的制备及其性能研究摘要化学气相沉积法(CVD)制备的金刚石涂层硬质合金刀具,因其同时兼备金刚石的高硬度和硬质合金的强韧性,在有色金属及其合金、碳纤维复合材料以及高硅铝合金等材料加工领域有着广阔的应用前景。
然而,在金刚石涂层刀具工业化应用过程中,存在两个发展局限:金刚石涂层与硬质合金基底间结合强度不足和金刚石涂层表面粗糙度较大。
金刚石涂层的结合强度不足主要由于硬质合金中粘结相Co会抑制金刚石形核、促进石墨相的产生所致,这使得金刚石涂层刀具不适用于高速、高进给等产生较大切削力的工作情况。
而金刚石涂层表面粗糙度较大影响了加工面的加工精度和表面光洁度。
鉴于此,本论文提出采用施加过渡层法来提高金刚石涂层的结合强度,而这其中的关键是提高过渡层与硬质合金间的结合强度。
双辉等离子体表面合金化技术(DGPSA)能够在基体表面制备出呈冶金结合的涂层,膜/基结合强度高。
因此,本论文采用DGPSA技术在硬质合金表面制备了Ta x C 过渡层,并采用微波等离子体化学气相沉积法在过渡层表面沉积了一层金刚石涂层。
之后,为降低金刚石涂层的表面粗糙度,在性能最优的Ta x C过渡层表面制备一层Mo促形核层,形成Ta x C/Mo双层过渡层,然后进行金刚石涂层的沉积。
采用扫描电子显微镜、X射线衍射仪、X射线光电子能I太原理工大学硕士研究生学位论文谱仪、原子力显微镜、洛氏压痕实验等多种方法对Ta x C过渡层、Ta x C/Mo 双层过渡层及金刚石涂层进行了一系列组织和性能的表征分析。
论文研究了不同基体温度对所得Ta x C过渡层的影响,结果表明所制备的过渡层由Ta2C和TaC纳米晶粒组成,过渡层表面呈现出特殊的圆环或凹坑形貌,且过渡层的成膜机制符合薄膜区域结构模型。
基体温度对过渡层的组织性能有较大的影响,800℃时所制备的Ta x C过渡层组织最致密,显微硬度最高,耐磨性最好,与基体结合强度最大,综合性能最为优异,并且在其表面沉积的金刚石涂层与基体间结合强度较高,这说明Ta x C过渡层有效地抑制了基体中Co元素的向外扩散。
拉丝模具结构组成及其选材

摘要:本文介绍了铜拉丝模具的结构组成、各工作区间对拉丝工艺的影响,以及几种常用拉丝模材质分类和它们的使用特点、性能。
关键词:拉丝模材质磨损因素硬质合金模天然金刚石模聚晶金刚石模在金属压力加工中,借助外力让金属从模具中强行通过,压缩金属横截面积,使其集合尺寸、形状符合设计要求的工具,我们通常称之为拉丝模。
拉制线材时,拉丝模是非常重要的辅助工具。
一些钢铁、铜、钨、钼等金属和合金材料的直线型物体(如棒材、线材、丝材、管材等)不易拉拔,大多数厂家也都使用拉丝模辅助操作。
1拉丝模结构组成拉丝模具包括模芯和模套两个部分。
1.1拉丝模模芯结构及作用。
根据拉丝模芯的工作性质,通常将之分为五大区间,即入口区、润滑区、工作区、定径区、出口区,各区的功能如下:入口区:便于穿线,同时避免入口处的钢丝与拉丝模发生摩擦;润滑区:借助润滑剂增大钢丝的润滑度;工作区:它是模孔的关键部。
钢丝在本区完成形变过程。
它能按照规定的截面尺寸控制钢丝的截面尺寸。
拉拔圆锥面金属的过程中,区内钢丝的体积所占空间为一圆台,即通常所说的变形区。
拉拔时用多大的力主要根据圆锥半角α而定;定径区:取得被拉拔钢丝的准确尺寸;出口区:保证钢丝平稳地出模具口,避免其表面被擦伤。
另外,压缩线材时拉力的大小以及拉拔后线材内残余多少应力,主要根据模具内径轮廓而定。
1.2入口角度、工作区、定径区对拉丝工艺的影响。
①入口角度。
拉拔时,线材先到达模芯入口区。
入口区锥角如果过小,会增大线材和内孔的接触面积,从而增大摩擦力,线材不易带入润滑剂,降低了润滑效果,增大了模具损耗。
适当增大入口角,可降低线材和拉丝模之间的摩擦力,确保润滑剂被顺利带入,增大润滑度,从而保护模芯。
入口角的调整使得线材表面质量更接近技术要求,并且延长了拉丝模的使用寿命。
②工作区。
拉拔线材时,工作区越长,摩擦力越小且分布越均匀,同时拉丝模内孔磨损度越小,拉丝模使用得越久。
工作区越窄越长,越能避免润滑剂退出拉丝模的进口端。