基于Autoform的高强板大梁成形工艺分析及优化
基于Autoform和Dynaform软件的超高强钢零件仿真对比

基于Autoform和Dynaform软件的超高强钢零件仿真对比牛超;陈新平;崔振祥【摘要】目的研究商用软件Autoform和Dynaform对超高强钢零件的回弹预测精度.方法以某车型前围板中间横梁零件冲压成形过程为例,分别基于Autoform和Dynaform软件建立冲压有限元模型模拟冲压成形和回弹过程,对两种软件成形性和回弹计算结果进行比较和讨论分析.结果Dynaform和Autoform两种软件在成形性计算时结果比较一致,相同位置Autoform计算减薄率为16%,Dynaform为16.2%;Dynaform计算的最大减薄率为18%,比Autoform的16.2%略大;两种软件基本在相同位置预测出了起皱和开裂现象;比较修边后回弹仿真值与实测值,Dynaform计算的偏差满足设定阈值的占51.4%,高出Autoform约20%.结论Dynaform计算的最大减薄率更大一些,对应量产时较高的安全裕度;同时其回弹计算结果与实测回弹值更为接近,回弹预测精度更高.【期刊名称】《精密成形工程》【年(卷),期】2017(009)006【总页数】4页(P53-56)【关键词】Autoform;Dynaform;超高强钢;回弹;成形性【作者】牛超;陈新平;崔振祥【作者单位】宝山钢铁股份有限公司中央研究院,上海 2019002;汽车用钢开发与应用技术国家重点实验室(宝钢),上海 201900;宝山钢铁股份有限公司中央研究院,上海 2019002;汽车用钢开发与应用技术国家重点实验室(宝钢),上海 201900;宝山钢铁股份有限公司中央研究院,上海 2019002;汽车用钢开发与应用技术国家重点实验室(宝钢),上海 201900【正文语种】中文【中图分类】TG386近年来,随着汽车工业对汽车安全性能以及节能环保要求的提高,在开展车身轻量化工作的同时,还要兼顾汽车车身强度,超高强度钢板由于其具有重量较轻和安全性能较高的双重优势,越来越受到汽车企业的青睐,应用日益广泛[1—2]。
基于ThinkDesign及Autoform的汽车高强板制件参数化的回弹补偿解决方案

基于ThinkDesign及Autoform的汽车高强板制件参数化的回弹补偿解决方案曹振雨;刘万林;郭建峰;许德庆【摘要】根据Auto form软件对汽车高强板制件冲压工艺的CAE回弹仿真分析结果,运用ThinkDesign软件中GSM(Global Shape Modelling)功能,自动实现工艺数模的回弹补偿,并且将回弹补偿后的工艺数模再次运用Autoform软件进行冲压工艺的CAE回弹仿真分析,验证回弹补偿是否足够、正确,并且以实际案例表述了这种参数化回弹补偿的解决方案.【期刊名称】《模具制造》【年(卷),期】2013(013)012【总页数】3页(P80-82)【关键词】Autoform;ThinkDesign;GSM功能;参数化;回弹补偿;高强度板;汽车后地板纵梁【作者】曹振雨;刘万林;郭建峰;许德庆【作者单位】山东小鸭精工机械有限公司山东济南25000;山东小鸭精工机械有限公司山东济南25000;山东小鸭精工机械有限公司山东济南25000;山东小鸭精工机械有限公司山东济南25000【正文语种】中文【中图分类】TP391.71 引言目前随着汽车轻量化和高安全性要求的不断提高,高强度板制件在汽车车身制件中的比重越来越大。
高强度板制件在冲压成形中,面临的最大困难是回弹的控制与补偿,一般的冲压工艺方案生产出的高强度板制件往往都存在着很大的回弹,而且回弹量严重的超出制件所要求的公差范围,严重影响了制件的焊装。
而基于板料成形CAE软件对高强度板制件进行冲压工艺分析和回弹分析,得出回弹的仿真结果后,设计者根据回弹的仿真结果再运用CAD软件进行手动回弹补偿设计,整个修改过程需要反复修改、验证,非常费时、费力,准确性较低,而且可能影响甚至改变制件曲面本身的质量。
2 汽车高强板制件参数化的回弹补偿解决方案2.1 ThinkDesign软件中GSM功能简介ThinkDesign软件中GSM功能指的是全局形状建模技术,即Global Shape Modelling,通常简称GSM。
基于Autoform的高强度板回弹控制及其影响因素探究

基于Autoform的高强度板回弹控制及其影响因素探究刘莉;江波;徐浩;王淑俊;王肖英;孙晓【摘要】利用Autoform数值模拟软件探究压边力、凸、凹模间隙、板料厚度、摩擦系数等对DP980高强度板制件回弹的影响规律.【期刊名称】《模具制造》【年(卷),期】2018(018)001【总页数】6页(P10-15)【关键词】高强度板;回弹;材料性能;数值模拟【作者】刘莉;江波;徐浩;王淑俊;王肖英;孙晓【作者单位】江淮汽车技术中心安徽合肥230000;江淮汽车技术中心安徽合肥230000;江淮汽车技术中心安徽合肥230000;江淮汽车技术中心安徽合肥230000;江淮汽车技术中心安徽合肥230000;江淮汽车技术中心安徽合肥230000【正文语种】中文【中图分类】TG385.21 引言随着我国汽车工业的快速发展以及汽车保有量的不断增长,道路、停车场、交通安全和燃油紧张等问题也日趋突出。
因此,汽车的减重、节能、小型化、安全、环保等备受人们普遍关注,而高强钢汽车冲压件的大量采用对解决上述问题都有帮助。
近10年来,汽车用高强钢的发展速度很快。
为了适应汽车冲压件高强化的发展趋势,世界各国纷纷开展了高强钢的研发并取得了令人瞩目的进展。
本次研究主要针对高强钢在在板料冲压成形中应用的可行性进行分析,并进行CAE分析模拟,探究各控制要素对回弹的影响,为模具设计及后期制件质量提供强有力的保障。
2 高强钢材质冲压成形主要工艺缺陷高强钢已是汽车行业以后发展的趋势,但钢的强度和塑性一般是矛盾的,钢强度的提高必然导致塑性下降。
而钢材塑性的下降就为冲压件的成形带来了很多问题和难题,回弹就是其中冲压件成形过程中很难避免的缺陷之一。
如何预防、减少高强钢的回弹就成了摆在高强钢冲压件面前最大的问题。
2.1 板材成形回弹分析回弹是当载荷卸去后,变形体的形状得到了部分恢复,造成制件的形状及尺寸与冲压模具工作表面的形状和尺寸不符。
当模具形状与工件的设计形状一致时,卸载后回弹的产生就会使制件的尺寸超出公差范围,影响制件的装配精度。
基于autoform对先进高强钢成型边缘开裂的预测
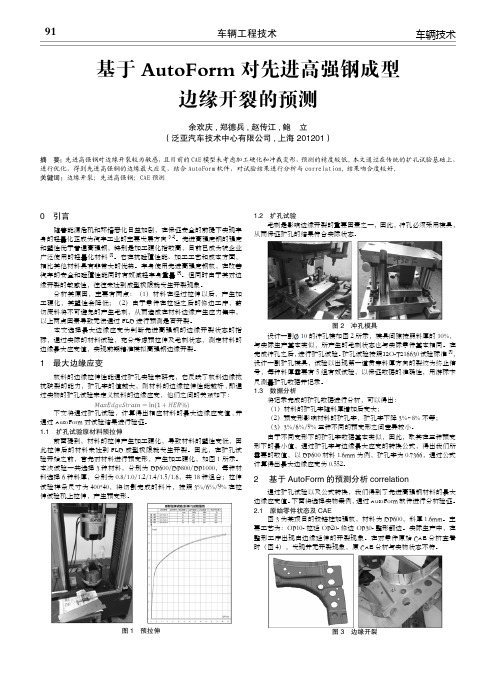
车辆工程技术91车辆技术0 引言 随着能源危机和环境恶化日益加剧,在保证安全的前提下实现车身的轻量化正成为汽车工业的主要发展方向[1,2]。
先进高强度钢的强度和塑性优于普通高强钢,特别是加工硬化指数高,目前已成为被企业广泛使用的轻量化材料[3]。
它在抗碰撞性能、加工工艺和成本方面,相比其他材料具有非常大的优势。
车身使用先进高强度钢板,在改善汽车的安全和碰撞性能同时有效减轻车身重量[4]。
但同时由于其对边缘开裂的敏感性,往往未达到成型极限就发生开裂现象。
分析其原因,主要有两点:(1)材料在经过拉伸以后,产生加工硬化,其塑性会降低;(2)由于零件在拉延之后的修边工序,剪切废料将不可避免的产生毛刺,从而造成在材料边缘产生应力集中,以上两点因素导致无法通过FLD 进行预测是否开裂。
本文选择最大边缘应变为判断先进高强钢的边缘开裂状态的指标,通过实际的材料试验,充分考虑预拉伸及毛刺状态,测定材料的边缘最大应变值,实现前期精准模拟高强钢边缘开裂。
1 最大边缘应变 板料的边缘拉伸性能通过扩孔实验来研究,它反映了板料边缘抵抗破裂的能力,扩孔率的值越大,则材料的边缘拉伸性能越好,即通过实物的扩孔试验来定义板料的边缘应变,他们之间的关系如下: 下文将通过扩孔试验,计算得出相应材料的最大边缘应变值,并通过AutoForm 对试验结果进行验证。
1.1 扩孔试验原材料预拉伸 前面提到,材料的拉伸产生加工硬化,导致材料的塑性变低,因此拉伸后的材料未达到FLD 成型极限就发生开裂。
因此,在扩孔试验开始之前,首先对材料进行预变形,产生加工硬化,如图1所示。
本次试验一共选择3种材料,分别为DP600/DP800/DP1000,每种材料选择6种料厚,分别为0.8/1.0/1.2/1.4/1.5/1.6,共18种组合;拉伸试验样条尺寸为400*40,将切割完成的料片,按照3%/6%/9%在拉伸试验机上拉伸,产生预变形。
图1 预拉伸1.2 扩孔试验 毛刺是影响边缘开裂的重要因素之一,因此,冲孔必须采用模具,从而保证扩孔的结果符合实际状态。
基于Autoform的车身B柱热成形工艺研究

摘要车的发展给人们的生活带来了极大的便利,但同时也带来了严重的能源消耗以及空气污染问题。
为了降低汽车的油耗和环境影响,汽车轻量化已成为汽车行业发展的重要方向。
热成形技术是汽车轻量化、提高汽车抗冲击形以及防撞性能的重要途径。
热成形过程数值模拟的准确性对热成型零件的设计和制造具有重要的指导作用。
本文基于Autoform软件,建立了 B 柱的热成形模型, 采用热力耦合数值分析的方法得到了热成形后零件的厚度,温度分布及破裂起皱的趋势分布等, 通过跟实际调试后的零件的对比,验证了模拟结果的准确性。
关键词:热成型有限元数值模拟 Autoform一、引言十四五时期,我国要努力趋向“碳达峰”和“碳中和”愿景,必须大力推动经济结构、能源结构、产业结构转型升级。
在“双积分”政策引导下,汽车行业也在大力开展节能减排工作,并以轻量化、新能源作为节能减排的主要手段。
对于传统燃油车,当汽车重量减少10%,燃油效率可以提高约8%;而纯电动汽车因为增加了三电系统导致其重量大幅上升,减轻重量可以减少电池容量或提升续航里程,因此新能源车型轻量化需求比传统燃油车更为迫切。
从汽车性能角度考虑,汽车的轻量化有助于汽车的“行驶、转弯、停车”三大基本性能的提高。
汽车白车身(解决碰撞安全性问题的车身骨架)是抵御碰撞侵入和能量吸收核心单元,约占汽车总重量的30%。
随着日益严格的碰撞安全法规,加强白车身成为必然应对手段,因此全球汽车企业均面临着日益增大的车身加强与轻量化间的矛盾。
其中热成形[1]技术对高强钢板进行成形, 在进行热成形前需将坯料加热到高温,使坯料奥氏体化,然后通过快速冷却,得到完全马氏体组织, 如图1,如采用 22 MnB5高强钢板热成形技术制造汽车保险杠,其强度可达1500MPa以上[ 2 ],该技术已成为世界上众多汽车生产厂商关注的热点。
图1 热成形技术原理通用、福特、大众、沃尔沃等汽车制造公司都在大量使用热成形的高强度汽车零件,某些车型上使用量高达30%。
基于autoform前门框上边梁内板热成形仿真试验
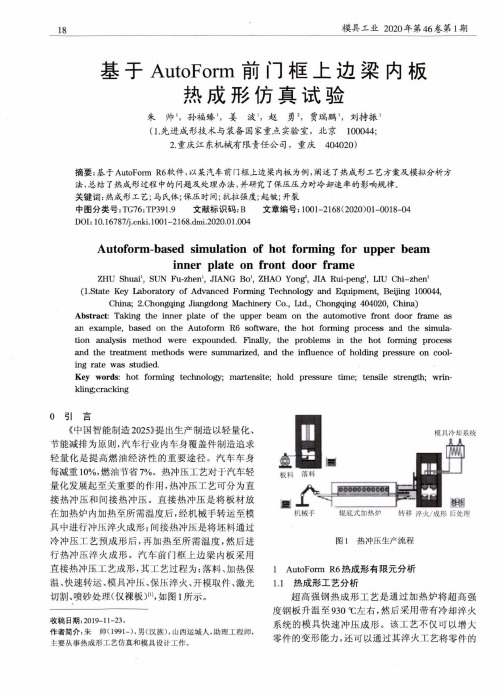
18模具工业2020年第46卷第1期基于AutoForm前门框上边梁内板热成形仿真试验朱帅',孙福臻打姜波打赵勇S贾瑞鹏',刘持振「(1.先进成形技术与装备国家重点实验室,北京100044;2.重庆江东机械有限责任公司,重庆404020)摘要:基于AutoForm R6软件,以某汽车前门框上边梁内板为例,阐述了热成形工艺方案及模拟分析方法,总结了热成形过程中的问题及处理办法,并研究了保压压力对冷却速率的影响规律。
关键词:热成形工艺;马氏体;保压时间;抗拉强度;起皱;开裂中图分类号:TG76;TP391.9文献标识码:B文章编号:1001-2168(2020)01-0018-04DOhlO.l6787/ki.l001-2168.dmi.2020.01.004Autoform-based simulation of hot forming for upper beaminner plate on front door frameZHU Shuai1,SUN Fu-zhen1,JIANG Bo1,ZHAO Yong2,JIA Rui-peng1,LIU Chi-zhen1(1.State Key Laboratory of Advanced Forming Technology and Equipment,Beying100044,China; 2.Chongqing Jiangdong Machinery Co.,Ltd.,Chongqing404020,China) Abstract:Taking the inner plate of the upper beam on the automotive front door frame as an example,based on the Autoform R6software,the hot forming process and the simulation analysis method were expounded.Finally,the problems in the hot forming process and the treatment methods were summarized,and the influence of holding pressure on cooling rate was studied.Key words:hot forming technology;martensite;hold pressure time;tensile strength;wrin-kling;crackmg0引言《中国智能制造2025》提出生产制造以轻量化、节能减排为原则,汽车行业内车身覆盖件制造追求轻量化是提高燃油经济性的重要途径。
基于高强板冲压成型车架纵梁的关键技术
基于高强板冲压成型车架纵梁的关键技术摘要:作为汽车的重要组成部分,车架具有十分重要的作用,既要承载着汽车的负荷,同时也要承受着汽车运行中车轮等带来的冲击,因此在进行汽车制造时,必须注重车架质量的提升。
而在车架中,纵梁是主要的吸能元件,是提高行车安全的关键,因此相关人员应该注重车架纵梁的设计。
为提高车架纵梁质量,本文通过文献法和分析法,对高强板冲压的成型车架纵梁进行了研究,从高强板冲压成型车架纵梁的必要性、要求以及关键技术上展开论述,以供参考。
关键词:高强板;成型车架纵梁;关键技术引言:随着我国经济的不断进步,汽车保有量逐年递增,促使汽车行业实现了繁荣发展。
在这样的时代背景下,汽车企业间的竞争变得愈发激烈,只有提高汽车的质量和安全,才能够在激烈的市场竞争中占据有利地位。
提升汽车质量的关键在于车架的纵梁,通过高强板冲压成型车架纵梁,可以在很大程度上提高纵梁的品质。
因此设计人员应该注重对高强板冲压技术的研究,深入分析目前冲压成型车架纵梁存在的问题,结合实际进行优化,促使纵梁的作用能够充分发挥。
一、基于高强板冲压成型车架纵梁的必要性在进行成型车架纵梁设计的过程中,利用高强板冲压技术进行纵梁的制作十分必要,对于汽车质量的提升具有重要意义。
其一,可以减少整车的重量,降低汽车的能耗。
当今时代,随着经济的进步发展,人们生活水平不断提升。
在此背景下,人们对汽车有了越来越高的要求。
要求汽车的整体重量尽可能的轻,让人们在开车的过程中有轻盈之感。
同时在环保理念下,还应该注重汽车的环保性。
而通过高强板冲压以及模具成型技术,进行纵梁的制作,可以促进汽车减重十分之一,同时燃油效率也能够提高7%左右。
也就是说利用该技术能够做到减重减排,同时不会影响汽车的承载力,能够保证汽车安全稳定运行。
其二,能够推动汽车行业的发展。
通过对国内外重型汽车的研究,发现很多欧美国家的重型汽车均是使用高强钢进行制造的。
利用高强钢进行车架大梁的制作,可以让钢板变得更薄,从而促使整车重量的减轻。
基于AUTOFORM建立板材成形原理与方法专业课模拟实践平台
[摘要]近年来,随着汽车工业的高速发展,车辆快速更新换代已经成了汽车企业生存的基本前提,各大汽车企业对车身开发专业技术人员有了新的筛选标准,同时对高校的教育培养模式提出了新的要求。
因此,材料成型专业实验教学进行实践性创新活动具有重要意义。
以板材成形原理与方法专业课为依托,有限元数值模拟软件AUTOFORM 为工具,工程化零件为载体,综合规划,建设专业课模拟实践平台,着重培养学生的创新思维和工程化意识,提高学生的实践创新能力及工程化实践能力,形成了一套完整的综合实验教学实践创新体系。
[关键词]有限元分析;数值模拟;板材成形[中图分类号]G642[文献标志码]A[文章编号]2096-0603(2019)07-0216-02基于AUTOFORM 建立板材成形原理与方法专业课模拟实践平台刘发,赵洪运*,于静泊,杨海峰,周威佳(哈尔滨工业大学(威海)材料科学与工程学院,山东威海264209)板材成形原理与方法是材料加工专业非常重要的一门专业课,通过这门课程的学习,一方面为学生打下坚实的理论基础,同时也是学生理论联系实际进行工程化设计的重要参考依据。
现阶段各高校针对此课程还是以课本理论授课为主,实际工程化设计严重不足,学生所学的知识仍停留在理论阶段,未真正意义上升到实际应用。
近年来,随着塑性成形有限元数值模拟的应用,计算机辅助设计已成为主流,所以,以AUTOF-ORM 为工具,以工程化案例为载体,为板材成形原理与方法专业课建立模拟实践平台尤为重要。
一、专业课介绍(一)板材成形原理与方法介绍板材的主要成形方法为冲压成形。
冲压成形是指靠压力机和模具对板材、带材等施加外力,使之产生塑性变形或分离,从而获得所需形状、尺寸、性能的工件的加工成形方法[1]。
冲压成形几乎涉及各行各业,如汽车车身覆盖件、家用电器的金属部件、电脑金属部件等。
随着冲压成形件的广泛应用,专业人才需求量急剧增加,板材成形原理与方法这门课的重要程度也逐步被提高。
基于AUTOFORM的板料高强度钢零件回弹补偿研究及应用
对每一步增量:
式中为当前时间,T p是总的分析计算时间。
牛顿迭代公式如下:
式中K(i)为当前切向刚度矩阵;F(i)为施加的载荷向(i)为内应力向量。
e
式中σ(i)为当前主应力。
在当前刚度矩阵
力刚度的计算基于等效应。
当假象应力完全去除后,可得到回弹后的零件形状及其相应的残余应力回弹仿真的结果是否正确,还有一个最主要的影响因
会产生变化。
板料在冲压成型之前就有一定的应力应变。
这种情况下,
MPa,N值=0.152。
成型分析参数设置:压边圈行程为100mm,压边力为150T,摩擦系数为0.17,分析模型设置见图2。
成型分析结果如图3所示。
5高强度钢零件的回弹分析及回弹补偿
回弹分析采用静式隐力算法,如图4所示,回弹主要集中在两端和侧壁,最大反弹量有5mm。
从图4可以得出,该零件回弹量较大,达不到所需的品质要求,因此需要对零件进行回弹补偿计算。
由于产品的法兰面用压边圈,同时压边圈也存在较大的反弹量,为了保证产品的相对关系,需要对整个形面进行整体补偿计算。
通过三次迭代补偿后,反弹量控制在1mm以内,再加上对于高强度板的经验数据,需要多补偿2.5-3.0mm。
图1零件形状
图2模型设置图3分析结果图4回弹结果。
基于AUTOFORM模拟的顶盖前边梁加强板热冲压工艺
精 密 成 形 工 程第12卷 第4期 146 JOURNAL OF NETSHAPE FORMING ENGINEERING2020年7月收稿日期:2020-04-01基金项目:国家科技重大专项(2018ZX04023002)基于AUTOFORM 模拟的顶盖前边梁加强板热冲压工艺朱帅,孙福臻,张泉达,贾瑞鹏(先进成形技术与装备国家重点实验室,北京 100044)摘要:目的 研究顶盖前边梁加强板热冲压成形过程中不同参数对零件成形的影响规律,为生产提供技术指导。
方法 通过AUTOFORM 模拟零件热成形过程,并对模拟结果对比分析,得到了板料尺寸、成形温度、保压时间、成形压力、冷却时间等工艺参数对成形性能的影响。
结果 优化了板料尺寸及板料定位,并通过调节模具间隙保证了零件的成形性,得到零件最大减薄率小于15%,平均抗拉强度达到1450 MPa ,平均硬度达到HV475,从而确定了顶盖前边梁加强板的热冲压工艺。
结论 结合此有限元分析方法试制出抗拉强度大于1450 MPa 的合格零件,为此类零件批量化生产提供理论依据。
关键词:AUTOFORM ;热成形;有限元;工艺参数DOI :10.3969/j.issn.1674-6457.2020.04.018中图分类号:TG306 文献标识码:A 文章编号:1674-6457(2020)04-0146-06Hot Stamping Process for the Front Side Beam StrengtheningPlate of the Roof Based on AUTOFORMZHU Shuai , SUN Fu-zhen , ZHANG Quan-da , JIA Rui-peng(State Key Laboratory of Advanced Forming Technology and Equipment, Beijing 100044, China)ABSTRACT: The paper aims to study the influence of different parameters in the hot stamping forming process of the front side beam strengthening plate of the roof to provide technical guidance for production. The hot forming process of parts was si-mulated through AUTOFORM. The influence of process parameters such as blank size, forming temperature, holding time, forming pressure and cooling time during the hot forming process were obtained by comparing and analyzing the simulation re-sults. The blank metal size and blank positioning were optimized, and the formability of the parts was ensured by adjusting the die gap. The largest thinning ratio of the parts was less than 15%; the average tensile strength reached 1450 MPa; and the aver-age hardness reaches HV475, thus determining the hot stamping process of the front side beam strengthening plate of the roof. Qualified parts with tensile strength greater than 1450 MPa are produced on the basis of this finite element analysis method, providing a theoretical basis for the mass production of such parts.KEY WORDS: AUTOFORM; hot stamping; finite element; process parameters当今汽车轻量化依然是众多车企共同追求的目标,在保证汽车安全性的前提下,研究超高强度钢板热成形技术以降低车重是目前解决轻量化的有效方法之一[1]。
- 1、下载文档前请自行甄别文档内容的完整性,平台不提供额外的编辑、内容补充、找答案等附加服务。
- 2、"仅部分预览"的文档,不可在线预览部分如存在完整性等问题,可反馈申请退款(可完整预览的文档不适用该条件!)。
- 3、如文档侵犯您的权益,请联系客服反馈,我们会尽快为您处理(人工客服工作时间:9:00-18:30)。
基 于 A u t o f o r m 的 高 强 板 大 梁 成 形 工 艺 分 析 及 优 化
李 松 ,张 少辉 ,谷 晓玉
( 长城 汽车股份有限公司,河北 保定
0 7 1 0 0 0 )
摘要 : 介绍 了高强板 大梁成形工艺和产生 的问题 , 对原 工艺方案 、 拉深造型及模具结构进行 了模拟 、 优 化, 解决 了制件 的壁厚减薄及回弹变形等问题 , 制件合格 率达 9 5 % ̄ X 。
关键词 : 高强板成形; 回弹 变形; 工艺优化 ; 模具 中图分类号: T G 3 8 6 . 3 2 文献标识码 : B 文章编号: 1 0 0 1 — 2 1 6 8 ( 2 0 1 ห้องสมุดไป่ตู้ ) 0 9 — 0 0 4 4 — 0 3
Au t o f o t i n. b a s e d p r o c e s s a n a l y s i s a n d o p t i mi z a t i o n o f
Ab s t r a c t : Ac c or d i n g t o t he pr ob l e m i n f o r mi ng pr o c e s s o f hi g h s t r e n g t h s t e e l g i r d e r ,t h e f or mi ng p r oc e s s ,d r a wi ng mod e l i ng a n d di e s t r uc t u r e we r e s i mul a t e d a nd o p t i mi z e d.Fi na l l y , t he p r o b l e m o f s e r i o us t h i nn i n g a n d s p r i n g b a c k of g i r de r wa s s o l v e d .The q ua l i t y r a t e o f
p r o du c t s Wa s e x t r e me l y i m pr o v e d.
Ke y wo r d s :h ig h s re t n g t h s t e e l ;s pr ing ba c k ;pr o c e s s o pt i mi z a io t n;d ie nd a mou ld
h i g h s t r e n g t h s t e e l g i r d e r
LI S o ng ,Z HANG S ha o — hu i ,GU Xi a o — y u
( T e c h n o l o g y C e n t e r o f Gr e a t Wa l l Mo t o r Co mp a n y ,He b e i Au t o mo t i v e En g i n e e r i n g T e c h n o l o y g Re s e a r c h C e n t e r ,Ba o d i n g ,He b e i 0 7 1 0 0 0 ,C h i n a )
汽车大梁数字模型如 图 1 所 示 。制 件 外 形 尺 寸为 l 6 6 0 am ̄ r 1 4 5 mmX 1 2 0mm, 料厚 1 . 6 mm, 材 质
为B 3 4 0 / 5 9 0 D P , 自动线生产 。该制件的成形难点在
_ 『 ‘ :
( 1 ) 制件材 质 为高强 钢厚 板 , 抗 拉强度 I >5 9 0 MP a , 高度 1 2 0 m m, 此 类 制件 的成 形难 度 很 人 , 侧 壁
为 了保 证 高强 板制 件 的尺 寸 精度 , 会 对 同弹 的 制件 进 行 反 复整 改 , 直 到 满足 尺 寸 要求 。反 复整 改
使整车开发周期无法保证 , 开发成 本大大提 高, 降 低 了企业 的竞争力 。此外 , 模 具的反 复整 改, 还会 严重影响模具质量及使用寿命 。
l 引 言
2 制件 成形 工艺 分析
近年来随着汽车 L 业 飞速发展 , 消费者对汽车 的 铃能 、 环保 、 轻 量 化 要 求越 来 越 高 。 轻 量 化 也 成 为 了汽 车 企 业 关键 的 竞 争指 标 , 这使得强度高 、 质
量 轻 的 高 强 板 在汽 车 车 身 零件 中 的应 j { j 比例 越 来 越犬 , 其 材料 种类 越来越 多 , 强度 级别 也越 来越 高 。
收 稿 日期 : 2 0 1 3 - 0 4 一 O 1 。
根 据制件形状特 点, 初 步制 定成形 一 _ 【 : 艺方案 为: ①拉深 , 见 图2 ( a ) , 拉深侧壁角度达 2 。 , 且侧壁
成上 斜 直 的折 线形 状 , 这 一 形状 可 以减 小制件 翘 曲变 形 , 为 了控 制 金 属流 动 , 选j { j 圆形 拉 深 筋 ; ② 修
力, 制件脱模后, 残 留应力释放造成很大同弹 , 直接 影 响 制 件 尺 寸 精 度及 整 车 装 配 、 焊接质量 , 进 而 影
响整 车 质量 。
( 3 ) 制 件侧 壁 为 重要 配 合 面 , 成 形性 差 , 极 易 回 弹, 拉深 后 需要通 过再 次整 形才 能保证 尺 寸精 度 。 2 . 1 初始 成形 工艺
会 严重 减薄 。
冲压件材料强度升级, 其制造 的工艺性却急剧
下 降 。 高 强 板 的 强度 很 高 , 变 形 抗 力 也 随之 增 高 ,
使得其伸 长 率很差 , 成 形 后 会 存 在 很 大 的残 留应
( 2 ) 制 件 整 体 S形 状 , 侧壁夹角为 2 。 , 容 易 产 生扭 曲变形 。