作业排序管理教材
运营管理-作业排序

作业排序测试题- 试答 1Question 1分数: 1/1在服务业与制造业中,给作业排序带来极大不同的根本原因是,服务不能存储,无法预先做出来,因此导致了安排方法上的根本不同()。
答案:对错误正确这次提交的分数:1/1。
Question 2分数: 1/1优先选择加工时间最短的工作应采用哪种调度原则()选择一个答案a. FCFSb. SPTc. SCRd. EDD正确这次提交的分数:1/1。
Question 3分数: 0/1用来描述多项工作在不同设备上所需时间、时间安排和现在进度的图表被称为甘特图中的作业进度图()。
答案:对错误正确这次提交的分数:1/1。
扣除先前的罚分,此次得分0/1。
Question 4分数: 1/1优先选择最早进入可排序集合的工件应采用哪种调度原则()选择一个答案a. FCFSb. SPTc. SCRd. EDD正确这次提交的分数:1/1。
Question 5分数: 1/1优先调度规则可以分为局部优先规则和整体优先规则,整体优先规则相对局部优先可以做更好的选择,但需要较多的信息。
答案:对错误正确这次提交的分数:1/1。
Question 6分数: 1/1机器图用来表示一项工程的计划开始日期、计划完成日期以及现在的进度()。
答案:对错误正确这次提交的分数:1/1。
Question 7分数: 0.9/1服务业为了平稳的满足顾客需求,通常可以通过以下集中方法安排顾客需求()选择至少一个答案a. 顾客预约b. 顾客预订c. 排队等待d. 安排工作人员调休e. 让顾客参与正确这次提交的分数:1/1。
扣除先前的罚分,此次得分0.9/1。
小班作业规律排序教案

小班作业规律排序教案在小班教学中,作业是巩固学生学习内容的重要环节。
然而,有时候学生对于作业的完成缺乏规律,导致效果不佳。
因此,制定一套,可以帮助学生养成良好的作业习惯,提高学习效果。
第一步:明确作业的目的和重要性在教学开始之前,教师应该向学生明确作业的目的和重要性。
作业不仅仅是为了完成任务,更是为了巩固和强化学习内容。
学生需要明白,只有通过认真完成作业,才能够巩固所学知识,提高学习效果。
第二步:分配合理的作业量小班教学中,教师应该根据学生的实际情况,合理分配作业量。
作业量过大会给学生带来压力,并可能导致学习效果不佳;作业量过小则无法达到巩固知识的目的。
教师可以根据学生的学习能力和时间合理安排,确保作业量适中。
第三步:制定作业时间和地点规律的作业时间和地点对于学生养成良好的作业习惯非常重要。
教师可以和学生商量,在每天固定的时间和地点完成作业。
例如,每天下午放学后,在教室内完成作业。
通过养成固定的作业时间和地点,学生可以更好地集中注意力,提高学习效率。
第四步:制定作业步骤和时间规划教师可以向学生详细介绍作业的步骤,并制定时间规划。
例如,先阅读题目,然后整理思路,接着完成作业,最后检查和修改。
同时,教师可以告诉学生每个步骤的时间限制,帮助学生合理安排时间,避免拖延和浪费。
第五步:鼓励学生独立完成作业小班教学中,教师应该鼓励学生独立完成作业。
只有通过自己的思考和努力,学生才能够真正理解和掌握所学知识。
当学生遇到困难时,可以提供适当的指导和帮助,但不要代替学生完成作业。
鼓励学生独立思考和解决问题,培养他们的学习能力和自信心。
通过以上五个步骤的规律排序教案,可以帮助小班学生养成良好的作业习惯,提高学习效果。
教师在实施教案时,应该关注学生的实际情况,灵活调整教学策略,确保每个学生都能够受益。
同时,教师还可以与家长保持密切的沟通,共同关注学生的作业情况,共同培养学生良好的作业习惯。
生产作业排序与控制培训教材(PDF 80页)

期除以作业时间) (6)综合规则(综合使用两种规则) (7)后到先加工规则 (8)随机规则
如何评价不同的排序规 则的优劣呢?
一般来讲,一个作业排序是否为优可以从 两个方面考虑:
(1)拖期的工件数或拖期时间。
(2)工件在车间的停留时间或在制品量。
注:总的拖期数是5件, 平均拖期时间为:(0+3+5+17+17+20)/6=10.33, 平均流程时间:(7+15+25+27+32+38)/6=24
(3) 按照最短加工时间优先规则排序
作业排序 1 2 3 4 5 6 工件编号 4 5 6 1 2 3 加工时间 2 5 6 7 8 10 等待时间 0 2 7 13 20 28 完成时间 2 7 13 20 28 38 交货期 10 15 18 14 12 20 拖期时间 0 0 0 6 16 18
排序问题的表示法:n/m/A/B
n为工件数, m为机器数 A为作业车间类型,如 F——流水作业(加工路线相同); G——单件作业(加工路线不同)
B为目标函数,通常是求极小值,如 Cmax——最长完工时间最短 Fmax——最长流程时间最短
例如: 4/2/F/ Fmax表示4项工作在2台机器上流水作业 时以最长流程时间最短为目标的排序。
常用的排序规则(8): (1)最短加工时间优先规则SPT
(Shortest Processing Time)
(2)最短交货期优先规则EDD
(Earliest due date)
(3)先到先加工规则FCFS
(First come first served)
生产运作管理教学课件ppt-编制作业计划与作业排序
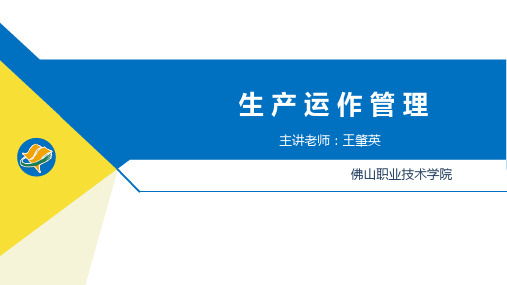
【导入案例解析】
首先,应用在制品定额法确定各个生产车间投入量和出产量 (1)装配1台空调配1件机箱,则装配2万台空调需要机箱数量 Qoj=20000×1 =20000(件); (2)装配车间的机箱的投入量
(件); (3)保证空调整机装配车间需要,机箱车间机箱的出产数量
(件); (4)加工车间机箱的投入数量
60
420
铸造过程
4
40
440
图3-2 连续流水线工作指示图表
生产运作管理
三、大量流水生产作业的期量标准
(2)间断流水线同期化程度不高,需要分工序规定每个工作地的工作时间顺序,确定标准计 划时间,计算工作地看管周期产量。间断流水生产的计划编制方法如下:
第一,确定看管周期。间断流水线中每道工序的节拍与流水线节拍可能不相等,为了使间断流 水生产线有节奏地工作,预先设定一个时间段,使每道工序在该时间段内生产相同数量的产品,在 这个预先设定的时间段内平衡各道工序的生产率达到一致,这个时间段称为看管周期。一般取一个 班、二分之一个班或四分之一个班的时间为看管周期。
生产运作管理
【案例分析】
编制大量生产作业计划考虑的问题及方法。 (1)产品品种单一连续生产,属于流水作业生产; (2)保证生产连续、均衡、稳定,必须规定合理的期量标准; (3)根据需求、期量标准计算出计划期的投入与产出; (4)根据大量流水作业生产连续、均衡、稳定的特点,将投入与产出量按日均匀地分配在计 划期内。
生产运作管理
四、大量流水生产作业计划的编制
式中:Qoi——i车间的产出量 Qij——j车间的投入量 Qsi——i车间外销半成品量 ZI——车间之间库存在制品定额 Z’I——期初预计库存量 QIi——i车间的投入量 Qwi——i车间的废品量 Ze——i车间内部在制品定额 Z’e——i车间内部期初在制品占用量
生产与运作管理生产作业计划与排序概述

(一)期量标准概念
为制造对象(产品、部件、零件)在生产过程中的 运动所规定的生产期限(时间)和生产数量的标准。
生产类型 大量生产
不同生产类型的期量标准 期量标准
节拍、流水线工作指示图表、在制品定额
成批生产 单件小批
批量、生产间隔期、生产周期、在制品定额、 提前期
生产周期、提前期
1. 生产周期(T)
检查和控制生产任务计划进度完成情况
生产作业计划的主要决策问题
• 确定批量的大小 • 确定适当的生产顺序 • 安排合理的生产进度日程
• 批量
(1)概念:
批量: 消耗一次准备结束时间所生产的同种产品或
零件的数量,以n记之(即相同产品或零件一次投
入和出产的数量)
生产间隔期: 相邻两批相同产品(零件)投入(或
周转半 前车间期初第 前车间
前车间
成品占 =( 一次出产零件 ÷ 交库间 )× 入库批
用量
入库标准日期 隔日数
量
= (3/5)×50 = 30 (件)
前车间成批入库,后车间整批领用
● 图表
工作日 1 2 3 4 5 6 7 8 910111213141516171819202122232425 1 2 3
解:
工作日 1 2 3 4 5 6 7 8 9 10111213141516171819202122232425 1 2 3
流
最
动 占
大用
占量
用
量
保险储备量
后领 前入
周转半
成品占 =
用量
前车 间批 量
-[
前车间计划最 后车间
后一批零件入 库的标准日期
÷
生产间 隔期
]
作业排序问题教材

CWU-HRM
对于单台设备作业排序问题
人力系
❖按照最短加工时间优先规则安排作业,可使 工作的平均完成时间最短,在制品最少;
❖按照最短交货期优先规则安排作业,可使最 长拖期时间与平均拖期时间最小化。
CWU-HRM
人力系
2. 流水线的作业排序
问题描述P207
CWU-HRM
人力系
❖多工件两台设备的排序问题算法
6
1
2
3
加工时间 2
5
6
7
8
10
等待时间 0
2
7
13
20
28
完成时间 2
7
13
20
28
38
交货期 10
15
18
14
12
20
拖延时间 0
0
0
6
16
18
CWU-HRM
人力系
作业排序 1 工件编号 4 加工时间 2 等待时间 0 完成时间 2 交货期 10 拖延时间 0
按照EDD
2
3
4
2
1
5
8
7
5
2
10
CWU-HRM
作业排序的目的
1. 满足交货期要求 2. 缩短生产周期 3. 使在制品库存最小 4. 使平均流程时间最小 5. 提高机器/工人的时间利用率 6. 使生产和人工成本最低
三、排序问题的一般假设
一个工件不能同时在几台设备上加工 工件数、机器数和加工时间是已知的,且加工时间与加工
顺序无关 每台设备同一时间只能加工一个工件(不考虑多工位组合
12
5
6
27
32
32
38
第七章 作业排序(生产运作与管理,陈荣秋)

星期一 星期二 星期三 星期四 星期五
4 工人1 4 3 3 4 4 2 2 3 3
星期六 星期日
1 1 2 * 2 * 2 * 1 1 * 0 * * *
工人2
工人3 工人4
3 2
1 0
2 1
0 0 *
3 2 1
1
1 0
* 0 0
2 2 1
0
*
1 1 1
0
工人5
作业 1、有7个作业必须全部进行A和B两种作业,顺序是先A后B。 用约翰逊规则决定各作业的顺序。 工件 1 2 3 4 5 6 7 (小时)
单班次问题: 1、保证工人每周有两个休息日; 2、保证工人每周有两个休息日为连休。
启发式算法:
第一步:从每周的人员需求量中,找出全部具有最少人员需求量 的两个连续日,再从中找出两日需求量总和最小者; 第二步:指定一名人员在上述两日休息,从其余准备安排该人员 工作的各日的人员需求量中减去1人的需求量; 第三步:重复第一、二步
Hale Waihona Puke 三、优先调度规则事例 在理论方面,排序问题的难度随着机床数量的增加而增大,而 不是随需加工的作业数量的增加而增大。 (一)n个作业单台机床的排序 零件 所需标准加工时间(h) 顾客预计取货时间(h) A 8 10 B 6 12
C D E
15 3 12
20 18 22
用SPT规则得出的作业排序 加工 开始 加工 结束 流程 预计取 实际取 提前小 拖延 顺序 工作 时间 工作 时间 货时间 货时间 时数 时间 D B A 0 3 9 3 6 8 3 9 17 3 9 17 18 12 10 18 12 17 15 3 7
生产作业排序对最终使用者或消费者无直接影响 (二)排序内容 服务要定义服务交易的时间和地点 制造业仅仅定义产品生产的操作步骤
生产管理课件 11作业排序
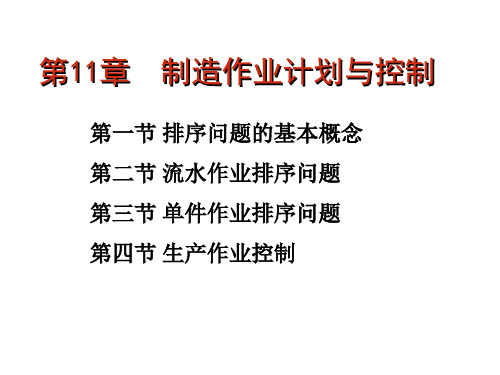
加工周期为46
课堂作业:求Fmax.
表3顺序S下的加工时间矩阵
i P i1 P i2 P i3 P i4
1 2 3 4 56
3
3
3 6 4 10 212 113 316
25 511 415 318 725 631
510 415 520 727 532 436
111 217 323 229 335 137
2、关键工件法
(1)计算每个工件的总加工时间,找出加工时间最长 的工件C,将其作为关键工件;
(2)对于余下的工件若Pi1≤Pim,则按Pi1不减的顺序排 成一个序列Sa,若Pi1>Pim,则按Pim不增的顺序排列成 一个序列Sb。 (3)顺序( Sa,C,Sb)即为所求顺序。
关键工件法求近优解举例
参数表示法:
n /m /P / Fmax所有零件在每台机器上的 加工顺序相同。如在M1上都是第一道工 序,M2上都是第二道工序。
n /m /F / Fmax不同零件在每台机器上的 加工顺序不同。如零件1在M1上不加工, 在M2上才是第一道工序;而零件2在M1上 是第一道工序。
第二节 流水作业排序问题
Johnson法则只是一个充分条件,不是必 要条件。不符合这个法则的加工顺序, 也可能是最优顺序。如对例11-2顺序(2 ,5,6,4,1,3)不符合Johnson法则, 但它也是一个最优顺序
对于3台机器的流水车间排序问题,只有 几种特殊类型的问题找到了有效算法。
对于一般的流水车间排列排序问题,可 以用分支定界法。
③ 若所有零件都已排序,停止。否则, 转步骤①。
例题:求表11-3所示的6/2/F/Fmax问题的最优解。
表11-3加工时间矩阵
- 1、下载文档前请自行甄别文档内容的完整性,平台不提供额外的编辑、内容补充、找答案等附加服务。
- 2、"仅部分预览"的文档,不可在线预览部分如存在完整性等问题,可反馈申请退款(可完整预览的文档不适用该条件!)。
- 3、如文档侵犯您的权益,请联系客服反馈,我们会尽快为您处理(人工客服工作时间:9:00-18:30)。
❖ (1)最短加工作业时间规则(SPT---shortest processing time或SOT---shortest operation time):优先选择加工所需时间最短的工件,然后是 第二短的,依次类推;
❖ (2)先到先服务规则(FCFS---first come first served):按照工件到达的先后顺序,优先选择最早 进入排队队列中的工件;
练习题20:各优先规则对比
为什么说SPT规则是在n/1作业排序中比其它规则都要好 的规则?
例12-1是根据FCFS、SPT、EDD和CR四种规则进行的n/1作业 排序实例。
12.1.3前向排序和后向排序
另一个区别作业排序系统特征的是看作业排序使 用的是前向排序还是后向排序。
前向排序(Forward scheduling)是指系统接 受某个订单后,立即对该订单所需的作业按从前 向后的顺序进行排序。前向排序系统能够显示出 完成某项订单的最早时间。
后向排序是指从未来的某个时期开始,按照从后向 前的顺序进行排序。后向排序可以显示在某个日 期前完成的订单的最晚开工时间。
❖ (3)交货期规则(EDD—Earliest Due Date): 优先选择交货期最早的工件进行加工。
❖ (4)开始日期规则:用约定的交货日期减去作业的正 常提前期。优先选择最早开工时间的工件进行加工;
❖ (5)剩余松弛时间规则(STR):剩余松弛时间=交 货期前的剩余时间-剩余的加工时间。优先选择剩余 松弛时间最短的工件进行加工;
于工作在进行中情况的排序
(8)排队比率规则(QR):
排队比率
计划中的剩余松弛时间 计划中的剩余排队时间
优先选择排队比率最小的工件进行加工
(9)后到先服务规则(LCFS):后到的订单放在先到 的订单上面,工作人员在操作的时候通常会先加工上 面的订单。
(10)随机原则:主管或工作人员选择自己喜欢的作业 先进行操作。
概括起来就是,作业排序需要解决“服务者”与“服务 对象”之间的关系。这里的“服务者”包括机器、工序、 工作地、员工等等;而“服务对象”则是指各项工作、客 户等。
12.1.2无限负荷和有限负荷
无限负荷(Infinite loading)指的是,在对工作中心(见本书第5 章5.4节工作单元的介绍)分配任务时,并不直接考虑该工作中心是否 具有足够的能力来完成所分配的工作,也不考虑每个工作中心中的每个 资源完成这项工作的实际顺序,而是只考虑它需要多长时间,大体上估 计所分配任务与该工作中心中的关键资源的能力是否匹配。
分配方法的匈牙利法请运用匈牙利分配方法给出将任务分
配至相应机器上的最佳分配方案。计算模板(续)
表12-1
表12-2
表12-3
表12-4
表12-5
表12-6
12.3 制造业作业排序
12.3.1 n/1作业排序
n/1作业排序就是n种工件在单台设备上加工的排序。这 是一种简单的排序问题。排序问题在理论方面的难度 是随着机器设备数量的增加而提高,而不是随着加工 工件数量的增加而提高。因此对n的惟一约束条件就 是它必须是确定的有限的数字。
(6)每个作业的剩余松弛时间规则(STR/OP):STR/OP计
算公式如下:
ST/O R P交 货货期 剩前 余 剩 的 作余 剩 业的 余 时 数加 时 余工
优先选择每个作业剩余的松弛时间最短的工件进行加工;
(7)关键比率规则(CR):
关键比 交 率剩 货小的工件进行加工;关键比率规则主要适用
有限负荷(Finite loading)是指,在对工作中心分配任务时,则需 要考虑该工作中心的能力是否与对所分配的任务匹配,并对他们做出详 细的安排,要细化到每个工作日的每一时刻,以及每一种资源要做的工 作的时间安排。如果有某个作业由于工件缺货而延迟,那么整个系统就 会停滞等待,一直到可以从前面的作业中获得所需的工件。理论上讲, 当采用有限负荷时,所有的计划都是可行的。
请运用匈牙利分配方法给出将任务分配至相应机器上的最佳 分配方案。计算模板:
匈牙利法的基本步骤如下: 1.将每行数字减去该行中最小数字,将每列数字减去该列中 最小数字。 2. 画数量最小的水平线和垂直线以盖住表中所有的零。若直 线数等于表的行或列数,那么最佳分配方案找到了。 3. 从未被直线盖住的所有数中减去其中最小的数,并将此最 小数加到所有直线两两相交之处的数上,再回到步骤2往下操 作直至出现可能的最佳分配。 4. 最佳分配总是在表中零位置出现。 利用上述求解算法进行4个工件与4台设备的作业指派。各种 指派方案所需的加工时间参见表12-1。表12-2、12-3、 12-4、12-5、12-6分别对应着求解算法的4个步骤。
12.1.4纵向加载和横向加载
纵向加载是指向工作中心分配作业任务时,采用无 限负荷法,并且不去考虑作业任务的优先性。
相反,横向加载是指在向工作中心分配作业任务时 ,采用有限负荷法,并且需要考虑作业任务的优先 性。
12.2 作业指派
作业指派是指为各生产或操作中心分配工作任务。 分配方法是一种特殊的可将任务或工作分配给相应资 源的线性规划模型。例如:将一种工作分配给某台机器; 某一合约分配给某个投标人:将人员分配到一定的项目上 等等。分配方法的分配目标是使完成现有任务的成本或时 间达到最少。 分配方法所分配的问题特征为:一件工作(或一个人) 仅分配给一台机器(或一个项目)。经常使用的分配方法 是匈牙利方法。 匈牙利方法的基本思想是,在各种指派方案的时间 (成本)预算表的基础上,通过表上作业法,得出总时间 (成本)最低的指派方案。
第12章 作业排序管理
12.1排序问题基本概念
12.1.1作业排序
作业排序(job sequencing)是指合理地安排各项作 业活动、运作资源利用或者配置设施的时间表。
具体说就是,为每台设备、每位员工详细地确定每天的 工作任务和工作顺序的过程。它要解决不同工件在同一设 备上的加工顺序问题、不同工件在整个生产过程中的加工 顺序问题,以及设备和员工等资源合理分配问题。