浅谈宏程序加工梯形螺纹的两种方法
如何用宏程序编程车削梯形螺纹的方法

如何用宏程序编程车削梯形螺纹的方法梯形螺纹较之三角螺纹,其螺距和牙型都大,而且精度高,牙型两侧面表面粗糙度值较小,致使梯形螺纹车削时,吃刀深、走刀快、切削余量大、切削抗力大,这就导致了梯形螺纹的车削加工难度较大。
参考程序①编程分析用宏程序编程时变量的设置是核心内容,一是要变量尽可能少,避免影响数控系统计算速度,二是便于构成循环。
经过分析本例中要4个变量,#1为刀头到牙槽底的距离,初始值为5.5mm,#2为背吃刀量(半径值),#3为(牙槽底宽—刀头宽度)/2,#4为每次切削螺纹终点X坐标。
本例中编程关键技术是要利用宏程序实现分层切削和左右移刀切削。
利用G92螺纹加工循环指令功能,左右移刀切削只需将切削的起点相应移动0.268*[#1-#2]+#3(右移刀切削)或者-0.268*[#1-#2]-#3(左移刀切削)就可以实现。
分层切削的实现通过#1和#2变量实现,每层加工三刀后,让#1=#1-#2实现进刀,而在每层中螺纹的X坐标不变,始终为#4=69.0+2*[#1-#2]。
②参考程序参考程序注释O0001;程序号N10 T0101;换01号刀具,调用01号偏置值N20 M08;打开切削液N30 M03 S180;主轴正转,转速为180r/minN40 G00 X90.0 Z10.0;刀具快速移动到点(90,10)N50 #1=5.5;#1为刀头到牙槽底的距离,初始值为5.5mmN60 #2=0.2;#2为背吃刀量(半径值)N70 #3=/2;#3为(牙槽底宽—刀头宽度)/2N80 WHILE[#1GE0.2]DO1;当#1≥0.2,执行循环1,底部留0.2mm的精车余量N90 #4=69.0+2*[#1-#2];#4为每次切削螺纹终点X坐标N100 G00 Z5.0;移动到直进刀切削的循环起点N110 G92 X#4 Z-286.0 F10.0;直进刀车削螺纹N120 G00 Z[5+0.268*[#1-#2]+#3];移动到右移刀切削的循环起点N130 G92 X#4 Z-286.0 F10.0;右移刀车削螺纹N140 G00 Z[5-0.268*[#1-#2]-#3];移动到左移刀切削的循环起点N150 G92 X#4 Z-286.0 F10.0;左移刀车削螺纹N160 #1= #1- #2;构成循环N170 END1;当#1<0.2,跳出循环1N180 G00 X200.0 Z150.0;快速退刀N190 M09;关闭切削液N200 M30;程序结束说明:①参考程序以工件右端面中心为编程原点。
B类宏程序加工梯形螺纹的方法和技巧
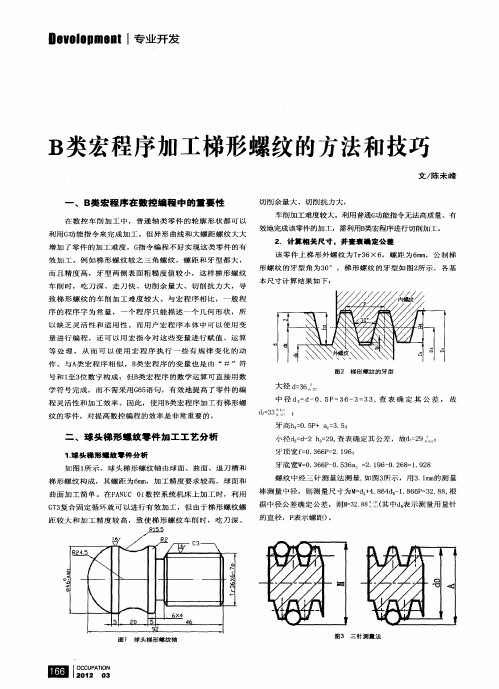
小径 d=一 32 , 表确 定其 公 差 ,故 2 ■ 3d 2h= 9 查 9
牙 顶 宽 fO 3 6= . 9 ; = . 6 P 2 1 6 牙 底 宽W O 3 6 一 . 3 a 2 1 6 0 2 8 i 9 8 = . 6 P 0 5 6 = . 9 — . 6 = . 2 螺 纹 中经 三 针测 量 法 测 量, 图3 示 ,用 3 1 m 如 所 . m 的测 量 棒 测 量 中径 ,则 测量 尺 寸 为M d+ . 6 d- . 6 P 3 . 8 根 = z4 8 4 D 1 8 6 = 2 8 , 据 中径 公差 确 定 公差 , ̄M 3 . 8 ( 中d表 示 测 量 用量 针 =28 其 。
纹 的零 件 ,对 提 高 数 控 编程 的效 率是 非 常 重要 的 。
牙 高h= . P a= . ; 30 5 + c 3 5
= 、球 头 梯 形 螺 纹 零 件 加 工 工 艺 分 析
1球 头 梯 形 螺 纹零 件 分析 . 如 图l 示 ,球 头 梯 形螺 纹 轴 由球 面 、 曲面 、退 刀槽 和 所
距 较 大 和 加 工 精 度 较 高 ,致 使 梯 形 螺 纹 车 削 时 , 吃 刀 深 、
C3
4
卜
4
图 1 球 头 梯 形 螺 纹 轴
图 3 三 针 测 量 法
专业开发 } e oe me t D v lp n
三 、梯 形 螺 纹 切 削 加 工 方 法
常 用 的 梯 形 螺 纹 加 工 方 法 有 直 进 法 、 斜 进 法 、 左 右 切 削 法 、 车 直 槽 法 、 分 层 法 等 等 。 由于 该 零 件 的 螺 距 和
mi n
2 参 考程 序 .
在数控车床上用宏程序加工梯形螺纹

不是理想的加工方法。
ቤተ መጻሕፍቲ ባይዱ
为了解决“直进分”和“斜进法”的缺点,就
必须改善刀具的切削方式。通过分析,最后选用
(见图3)“分层切削法”。“分层切削法”是先
把螺纹X向分成若干层,
每层Z向再进行若干次粗
切削,再进行左、右精车
切削。每层刀具只需沿左
右牙型线切削,背吃刀量
小,从而使排屑比较顺
利,刀具的受力和受热情
图3 分层切削法
起刀点Z轴偏 移量(CE)的计 算公式为
图7
CE=BE-BC=(AH+tan15°×HE)-BC =(P/4+tan15°×HE)-BC 即起刀点Z轴偏移量(螺纹右侧留0.1mm的精 加工量)参数变量为
#8=#2/4+TAN[15]*[#1-#3]/2-#6/2-0.1;
每层Z轴的切削余量(DF)的计算公式为
M 机床自动化 achine Tools Automation
在数控车床上用宏程序加工梯形螺纹
中国北车永济新时速电机电器有限责任公司 (山西 044502) 陈建军 永济电机高级技工学校 (山西 044500) 张丽波
一、梯形螺纹在数控车床上的加工工艺
数控车加工螺纹有三种指令:G32、G92、 G76。其中G32、G92的进刀方式为“直进法” (见图1);G76的进刀方式为“斜进法”(见图 2)。
DF=BF-BD=2(AH+tan15°×HE)-BD
即每层Z轴的切削余量(螺纹左侧留0.1mm的 精加工量)参数变量为
#9=#2/2+TAN[15]*[#1-#3]-#6-0.1
(3)外螺纹Tr36×6程序
O8888; M03S200; G00X100Z50; T0101; G00X40Z10; #1=36;(螺纹大径及公称直径) #2=6;(螺距) #3=#1-#2/2;(螺纹中径) #4=0.5;(牙顶间隙) #5=#1-#2-2*#4;(螺纹小径) #6=1(T型螺纹刀刀尖宽) #7=0.366*#2-2*TAN[15]*#4;(牙底槽宽) #8=#2/4+TAN[15]*[#1-#3]/2-#6/2-0.1;(起 到点Z轴偏移量,右侧留0.1mm) #9=#2/2+TAN[15]*[#1-#3]-#6-0.1;(每层Z 轴的切削余量,左侧留0.1mm) #10=0.5(X轴的吃刀量) N1IF[#1LE#5]GOTO4;(判断切削直径,如果X值 ≤小径,则执行N4程序段) N2IF[#9LE0.1]GOTO3;(判断每层Z轴切削余量如 果余量≤0.1mm,则执行N3程序段) G00Z[10+#8];(Z轴起刀点) G92X#1Z-42F#2;(切削螺纹) #8=#8-0.3;(重新计算Z轴起刀点偏移量,递减0.3mm) #9=#9-0.3;(重新计算每层Z轴切削余量,递减0.3mm) GOTO2;(无条件执行N2程序段) N3#1=#1-#10;(重新计算切削直径X值) #8=#2/4+TAN[15]*[#1-#3]/2-#6/2-0.1(重新 计算Z轴起刀点偏移量) #9=#2/2+TAN[15]*[#1-#3]-#6-0.1;(重新计 算每层Z轴切削余量) IF[#1GE33]THEN#10=0.5(判断切削直径,对X轴吃刀 量重新赋值)
浅析用宏程序加工梯形螺纹的方法

梯形螺纹加工常用的方法有直进法、斜进法、左右车削法和车阶梯槽法等,这些加工方法由于其自身存在缺陷,生产效率较低,精度稳定性差,很难实现产品批量生产或产品的改型,这也极大地影响了产品的加工效率和加工质量。
以FAN UC系统数控车床为例,能够用来加工螺纹的基本指令有G32、G92、G76等,它们各有自身的优缺点。
如果单独使用其中某一指令来加工梯形螺纹的话,只能加工小螺距或精度较低的螺纹,切削效率低,难以满足更高的要求。
1 梯形螺纹加工的相关知识(1)车刀的选择与安装。
梯形螺纹加工选择的是成型车刀,车刀在安装时,车刀主切削刃必须与工件轴线等高,同时应和工件轴线平行。
刀头的角度平分线要垂直于工件轴线。
可以使用样板找正装夹,以免产生螺纹半角加工误差。
(2)工件的装夹。
一般采用两顶尖或一夹一顶的方式装夹。
(3)数控车床的选择和调整。
梯形螺纹加工选择C K 6140数控车床,F A N U C -0i -mate TC数控系统。
要求数控车床加工精度高、磨损少、滚珠丝杠反向间隙小。
2 梯形螺纹的车削方法2.1直进法刀具沿直径方向进刀,如图1所示,常用于小螺距普通螺纹的加工。
使用G32\G92指令代码编程常采用此种进刀方式。
该加工方式采用的是三刃同时参与切削,刀头负荷较大,为了均衡刀具的受力,常采用递减规律分配吃刀量。
对于大螺距普通螺纹和梯形螺纹如采用该种方式加工,刀头很容易受力过大而折断或者产生扎刀现象。
2.2斜进法刀具进刀方向沿牙形角方向,如图2所示,由于采用单刃切削,切削力减少,排屑顺畅,F A N U C 系统中的G 76指令即为典型①作者简介:张长红(1978.3—)女,江苏泗洪人,本科,机械讲师,江苏省连云港工贸高等职业技术学校/江苏省经贸技师学院,研究方 向:数控专业理论及实践教学。
浅析用宏程序加工梯形螺纹的方法①张长红(江苏省连云港工贸高等职业技术学校/江苏省经贸技师学院 江苏连云港 100084)摘 要:螺纹传动在机械传动中应用广泛,在传递较大动力的大型设备中梯形螺纹应用较多。
B类宏程序加工梯形螺纹的方法和技巧

B类宏程序加工梯形螺纹的方法和技巧作者:陈未峰来源:《职业·中旬》2012年第03期一、B类宏程序在数控编程中的重要性在数控车削加工中,普通轴类零件的轮廓形状都可以利用G功能指令来完成加工。
但异形曲线和大螺距螺纹大大增加了零件的加工难度,G指令编程不好实现这类零件的有效加工。
例如梯形螺纹较之三角螺纹,螺距和牙型都大,而且精度高,牙型两侧表面粗糙度值较小,这样梯形螺纹车削时,吃刀深、走刀快、切削余量大、切削抗力大,导致梯形螺纹的车削加工难度较大。
与宏程序相比,一般程序的程序字为常量,一个程序只能描述一个几何形状,所以缺乏灵活性和适用性。
而用户宏程序本体中可以使用变量进行编程,还可以用宏指令对这些变量进行赋值、运算等处理,从而可以使用宏程序执行一些有规律变化的动作。
与A类宏程序相似,B类宏程序的变量也是由“#”符号和1至3位数字构成;但B类宏程序的数学运算可直接用数学符号完成,而不需采用G65语句,有效地提高了零件的编程灵活性和加工效率。
因此,使用B类宏程序加工有梯形螺纹的零件,对提高数控编程的效率是非常重要的。
二、球头梯形螺纹零件加工工艺分析1.球头梯形螺纹零件分析如图1所示,球头梯形螺纹轴由球面、曲面、退刀槽和梯形螺纹构成,其螺距为6mm,加工精度要求较高,球面和曲面加工简单。
在FANUC 0i数控系统机床上加工时,利用G73复合固定循环就可以进行有效加工,但由于梯形螺纹螺距较大和加工精度较高,致使梯形螺纹车削时,吃刀深、切削余量大、切削抗力大,车削加工难度较大。
利用普通G功能指令无法高质量、有效地完成该零件的加工,需利用B类宏程序进行切削加工。
2.计算相关尺寸,并查表确定公差该零件上梯形外螺纹为Tr36×6,螺距为6mm,公制梯形螺纹的牙型角为30°,梯形螺纹的牙型如图2所示,各基本尺寸计算结果如下:大径中径d2=d-0.5P=36-3=33,查表确定其公差,故;牙高h3=0.5P+ ac=3.5;小径d3=d-2 h3=29,查表确定其公差,故;牙顶宽f=0.366P=2.196;牙底宽W=0.366P-0.536ac =2.196-0.268=1.928螺纹中经三针测量法测量,如图3所示,用3.1mm的测量棒测量中径,则测量尺寸为M=d2+4.864dD-1.866P=32.88,根据中径公差确定公差,则(其中dD表示测量用量针的直径,P 表示螺距)。
用宏程序编程车削梯形螺纹方法

用宏程序编程车削梯形螺纹梯形螺纹螺距和牙型都大,而且精度高,牙型两侧面表面粗糙度较小,致使梯形螺纹车削时,吃刀深、走刀快、切削余量大、切削力大,这就导致了梯形螺纹的车削加工难度较大。
1 普通车床车削梯形螺纹方法车削梯形螺纹时,通常采用高速钢材料刀具进行低速车削,低速车削梯形螺纹一般有四种进刀方法:直进法、左右切削法、车直槽法和车阶梯槽法。
通常直进法只适用于车削螺距较小(P<4mm)的梯形螺纹,而粗车螺距较大(P>4mm)的梯形螺纹常采用左右切削车直槽法和车阶梯槽法。
下面分别梯形螺纹车削的四种进刀方法:2 数控车削梯形螺纹方法的选用根据上述分析,数控车床车削梯形螺纹采用“分层法“比较合适。
分层法”车削梯形螺纹实际上是直进法和左右切削法的综合应用。
在车削梯形螺纹时,“分层法”通常不是一次性就把梯形槽切削出来,而是把牙槽分成若干层(每层深度根据具体情况设定),转化成若干个较浅的梯形槽来进行切削,从而降低了车削难度。
每一层的切削都采用先直进后左右的车削方法,由于左右切削时槽深不变,刀具只须做向左或向右的纵向进给即可,因此它比上面提到的左右切削法的运动轨迹要简单得多。
3应用宏指令将梯形螺纹加工程序模块化应用宏指令,将左右排刀法加工梯形螺纹模块化,应用时只需将主宏程序指令中的自变量赋值修改一下即可加工不同尺寸的梯形螺纹,而子宏程序中的内容不需修改。
(1)数值计算①梯形螺纹加工尺寸计算及其参数值:②左(右)移刀量的计算如上图可以得出当刀头宽度小于牙槽底宽时左(右)移刀量计算式为:左(右)移刀量=tan15°×每一刀的进刀深度(半径值)+(牙槽底宽—刀头宽度)/2(2)“分层法”车削梯形螺纹的刀具选择“分层法”车削梯形螺纹所用的粗车刀和精车刀与其它加工方法基本相同,只是粗车刀的刀头宽度小于牙槽底宽,刀具刀尖角略小于梯形螺纹牙型角。
(3)通过上述分析,梯形螺纹加工需要的自变量有:#1=(A)每一刀的进刀深度(半径值),#2=(B)背吃刀量;#3=(C)刀头宽度偏差=(牙槽底宽—刀头宽度)/2;#4=(I)螺纹小径;#5=(J)螺距;#6=(K)螺纹长度;(1)主程序(2)子宏程序4 结束语宏程序是程序编制的高级形式,程序编制的质量与编程人员的素质息息相关,因为宏程序中应用了大量的编程技巧,如数学关系的表达、加工刀具的选择、走到方式的取舍等。
基于宏程序编程的梯形螺纹加工

幽
呈! 至墨 塑
www. e a| m t wOr ng1 50 com kl 9 ,
参磊 工冷 工 加
计算机实现数字控制 。本文正是根据此 法 ,利用 系统 的
子 程 序
00 2 00
基本螺纹切 削指令 G 2或 G2和宏 程 序 的变量 控制 技 3 9
术 ,实现梯形螺纹的编程与加工。梯形螺 纹数控 车削程 序设计及加工工艺本程序主要 由宏指令 完成 ,所有 的数 值都可根据实际加工情况很方便地实 现调整 ,程序 的适
是 簧
M 8 0 0 ( 9 03 P 调用每层切削子程序切 削 Z向剩余量 )
M9 9
子 程 序
0 00 0 3
/ 车削螺纹l \ \ 左牙侧面I 车削螺纹
f 右牙 侧 面
C O X4 O 2
Z [O+ 1 ( 1 # ] 螺纹 Z向右侧起刀点 ) X[ 0—2}#0 ] ( 4 12 螺纹 向起 刀点 ) G 2Z一 0F ( 3 5 6 切削螺纹长度 5 rm,螺距 6 0 a mm)
C OX 2 ( 刀 ) O 4 退
图 2 Biblioteka 下面就以车削 4 —7 n 0X 6 e为例 ,分析加工工艺及 宏程序 的编制 ,此列 编写 了两种加工工艺 即工艺 A与工 艺 B和其相应 的宏程序 ,并 进行 了详 尽的分析 和 比较 。 梯形螺纹的计算 公式及其参数值如附表所示 。
只须做 向 左或 向右的纵向进给 即可 ,从而降低 了车削难
度 ,完成粗 车后再对槽两侧进行精 车。这种方法 ,一方
1 .基于宏程序编程的分层法车削梯形螺纹
分层法是直进法和左右切削法的综合应用 ,其原理 如图l 、图2 示 ,它可 以克 服传统 加工 方法 的缺 陷。 所
梯形螺纹的宏程序加工

梯形螺纹的宏程序加工摘要:梯形螺纹是数控车工加工的难点,宏程序是数控编程的难点,然而二者结合起来就会使数控机床加工梯形螺纹,操作者只要修改参数的数值就可以完成不同螺距与长度的梯形螺纹加工,十分的方便快捷。
关键词:数控车床FANUC系统梯形螺纹宏程序#1=A 梯形螺纹大径#2=B 梯形螺纹小径#3=B 梯形螺纹牙底槽宽#4=I 梯形螺纹车刀刀头宽度#5=J 梯形螺纹长度L#6=K 梯形螺纹螺距#7=D 升速段长#8=E 减速段长#9= 粗车转速#10= 精车转速#19=S 精加工余量(直径值)主程序:O0001;N10 G54 G40 G21;N20 T0404;调用梯形螺纹车刀N30 G65 P333;调用梯形螺纹宏程序N40 M05;主轴停止转动N50 M30;程序结束并返回程序开头宏程序;O333N10 M03 S#9;主轴正转,转速为#9N20 #30=FUP[[#1-#2-#19]/2/#18];根据背吃刀量和精加工余量计算径向粗车循环次数(下取整)N30 #31=[#1-#2-#19]/#30;计算径向粗加工每次背吃刀量(直径值)N40 #40=FUP[#3-#4-#19/2]/2/#20;计算Z向粗车循环次数;N50 #41=[#3-#4-#19/2]/2/#40;计算Z向粗加工每次背吃刀量N60 #28=1;径向切削次数初始值赋值N70 WHILE[#28GT#30]DO1;N80 G00 X[#1+3];车刀快速移动到X方向起刀位置N90 Z#7;车刀快速移动到Z方向起刀点N100 X[#1-#31];车刀径向切入一个背吃刀量N120 G32 Z-[#5+#8]F#6;粗车梯形螺纹N110 #29=1;Z向切削次数初始值赋值N130 WHILE[#29GT#40]DO2;N140 G00 X[#1+3];车刀快速返回到X方向起刀位置N150 Z#7;车刀快速移动到Z方向起刀点N160 W-#41;车刀Z向负向移动一个切削量N170 X[#1-#31];车刀径向进刀#31N180 G32 Z-[#5+#8]F#6;粗车梯形螺纹N190 G00 X[#1+3];车刀快速返回到X方向起刀位置N200 Z#7;车刀快速移动到Z方向起刀点N210W#41;车刀Z向正向移动一个切削量N220X[#1-#31];车刀径向进刀#31N230G32Z-[#5+#8]F#6;粗车梯形螺纹N240G00X[#1+3];车刀快速返回到X方向起刀位置N250Z#7;车刀快速移动到Z方向起刀点N260#29=#29+1;Z向移动次数增加1N270#41=#41*#29;Z向移动量递增N280END2;N290#28=#28+1;X向切削次数增加1N300#31=#31*#28;X向切削量递增N310END1;N320 #41=[#3-#4-#19/2]/2/#40;计算Z向粗加工每次背吃刀量N330#29=1;Z向切削次数初始值赋值N340S#10;选用精加工转速N350G00X[#1+3];车刀快速返回到X方向起刀位置N360Z#7;车刀快速移动到Z方向起刀点N370X#2;车刀进给到X向精车位置N380G32Z-[#5+#8]F#6;精车螺纹牙底N390WHILE[#29GT#40]DO3;N400G00X[#1+3];车刀快速返回到X方向起刀位置N410Z#7;车刀快速移动到Z方向起刀点N420X#2;车刀进给到X向精车位置N430W-#41;车刀Z向负向移动一个切削量N440G32Z-[#5+#8]F#6;精车螺纹牙底N450G00X[#1+3];车刀快速返回到X方向起刀位置N460Z#7;车刀快速移动到Z方向起刀点N470X#2;车刀进给到X向精车位置N480W#41;车刀Z向正向移动一个切削量N490G32Z-[#5+#8]F#6;精车螺纹牙底N500#29=#29+1;Z向移动次数增加1N510#41=#41*#29;Z向移动量递增N520END3;N530G00X[#1+3];车刀快速返回到X方向起刀位置N540Z#7;车刀快速移动到Z方向起刀点N550X#2;车刀进给到X向精车位置N560W-[#3-#4]/2;车刀移动到螺纹牙右侧面起点N570G32Z-[#5+#8]F#6;精车螺纹牙牙右侧面N580G00X[#1+3];车刀快速返回到X方向起刀位置N590Z#7;车刀快速移动到Z方向起刀点N600X#2;车刀进给到X向精车位置N610W[#3-#4]/2;车刀移动到螺纹牙左侧面起点N620G32Z-[#5+#8]F#6;精车螺纹牙牙左侧面N630G0X100;N640Z100;N650M99。