PID炉温控制
热处理炉温度的PID控制

2 0
2 运 行 程 序 的编 写
以图 1 碳素 鱼竿 固化 温 度 曲线 为例输 入 参 数 , 首 先 仪表从 室温 ( 始 炉 温 ) 0℃ 开始 加 温 , 3 i 起 2 经 0 mn
升温到 10 o 恒温 1 n 再 经 1 i 0 C, 0 mi, 5 m n升温 到 10 8 ℃ , 10℃恒温 3 i 后 , 在 8 0r n 程序停 止运行 自然 降温 。 a 第一步 : 按一下“ E ” ,V窗 口显示 “ T P , ST 键 P S E ” 再按
口显示参数 为 4 (0为开锁 密码 ) 此 时可 以对仪表 所 J4 D ,
自整定结束 后 ( 自整 定的时 间长短 因炉不 同 , 的 有 长 , 的短 ) 仪 表 自动 将 Cr 参数 调 整 为 3 s 有 , t l ,V窗 口 停止 “ t 与“ 8 ” A ” 10 的交替显 示 , 续 执行 程序第 四段 , 继
此类推 。C 1 2 ,0 = 0 C 2= 0 ,0 0 C 3= 0 , 0 = 0T 1 3 ,0 1 T2=1 ,0 10 0
T 3 =1 C0 = 1 0,D4 :3 C0 = 1 0, 0 = 一 1 1 I 5 0 5, 4 8 ] 0, 5 8 T5 2 。 o
参数为 一11为程序停止运行指令 。在第一 次调试运行 2, 时, 当程序运行到 10℃时 , 自 8 启动 整定。
状态。
将显示 一 个 参 数 , 当找 到 P 窗 口显 示 “ t ” , 动 V Cr 时 按 l
“ 或“ 键 , S 八” V” 使 V窗 口参数 为“ ” 此时 ,V窗 口上 2, S “ t 与“8 ” A ” 10 交替显示 , 说明仪 表进入 自整定状态 。 在 白整定过程 中 , 表可 以通 过 电脑 依 据 电炉 的 仪 功率 、 保温 效果 、 腔体积 、 升速率及滞 后 时间等 , 炉 温 对 电炉进行 测定 , 自动 调 整仪 表 的 M 0、 、 并 5 P T参 数 , 以
pid在温控中的作用

pid在温控中的作用PID控制是一种自动控制系统中常用的一种控制算法,它根据被控对象的实际运行情况不断调整控制量,以达到稳定的控制效果。
在温控中,PID控制器被广泛应用,可以有效地控制温度波动,保持温度稳定,提高生产效率。
本文将深入探讨PID在温控中的作用。
一、PID控制原理PID控制器是由比例(P)、积分(I)和微分(D)三部分组成的控制器。
它根据被控对象的反馈信号,通过计算偏差的大小和变化率来调整输出控制量,以实现对被控对象的精确控制。
1. 比例控制(P)比例控制是根据偏差的大小来调整控制量的大小,开环放大比例即为比例控制。
比例系数越大,控制量和偏差之间的关系越密切,对温度波动的抑制效果也越好。
但是,过大的比例系数可能引起震荡或过冲现象,影响控制效果。
2. 积分控制(I)积分控制是根据偏差随时间的积累来调整控制量的大小,通过累积偏差的方法来修正系统的静态误差。
积分系数越大,系统的稳态精度越高,但同时也容易导致系统的超调和振荡现象。
3. 微分控制(D)微分控制是根据偏差的变化率来调整控制量的大小,通过对偏差的变化速度进行调节以提高系统的动态响应能力。
微分系数越大,系统的响应速度越快,但同时也会增加系统的灵敏度,容易受到噪声的干扰。
综合比例、积分和微分三部分的作用,PID控制器可以根据实际情况进行调整,以实现对被控对象的精确控制。
二、PID在温控中的应用在温控中,PID控制器被广泛应用于各种工业生产过程中,如化工、食品加工、医药制造等。
它可以对温度进行精确控制,提高生产效率,减少生产成本,保障产品质量。
下面我们将介绍几种常见的温控应用场景。
1. 温度恒温器温度恒温器是一种专门用于保持恒定温度的设备,它通常由PID控制器、加热元件和传感器组成。
PID控制器可以根据被控对象的温度反馈信号,通过比例、积分和微分的调节来控制加热元件的功率,以实现对温度的精确控制。
在实验室、医药制造等领域,温度恒温器被广泛应用于热源的稳定控制。
基于PID的电热炉温度智能控制系统设计

www�ele169�com | 31智能应用1.什么是PIDPID 即portID,通常指的是在生成树协议STP 中,如果在端口位置处所收到的BID 同path cost 相同,就需要通过比较PID 来进行阻塞端口的选择。
在现代化工厂生产及工程控制中,PID 主要是由8位端口的优先激加端口构成,端口号占据低位,默认优先级为128。
在工业自动化领域发展中,PID 控制水平是一项重要的参照标准指标,PID 控制以及相应的控制器,智能 PID 仪表产品有很多,而且这些PID 产品都在现代化工业工程项目中的得到了非常广泛的应用,一些公司创新开发了拥有PID参数自我调整和整定功能的智能调节器。
图1 PID 参数控制器如图1所示,PID 参数控制器拥有自动调整功能,可以开展智能化调整以及通过自校正、自适应算法来实现,充分利用PID 参数控制的方式来完成对工业化生产环节中的压力控制、温度调节、流量控制以及液位控制等作业,从而可以实现具有PID 参数控制功能的可编程控制器PLC 控制调节,完成对PC 系统的自动化操作与控制。
2.电热炉温度智能控制系统的工作原理基于PID 基础上设计而成的电热炉,主要被应用在我国工业自动化生产中,对工业产品的有效加热与烘干,一般在实际加热的时候,会使用封闭式的方式进行工业产品的工艺加热,而对电热炉文温度的自动控制与调控,需要使用PID 参数控制器来完成,从而完成对电热炉温度系统的有效控制。
为了能够满足电热炉温度控制系统的升温要求,首先需要对单片机进行科学选择,可以美国ATM 公司生产的AT89C52型号的单片机,AT89C52型号的单片机能够和51系列的单片机进行兼容与合并,从而满足C 语言可编程序控制软件的PID 控制啊要求,提高电热炉的整体温度控制水平,同时也可以提高温度控制系统的运行速度,保证系统运行的稳定性。
在真正的温度测量过程中,需要考虑测量温度的准确性以及温度测量的可靠性,一般可以采用四路采样的电路形式展开检测,也就是对四路采样中不同的点展开检测,然后计算得出四个测量点的平均温度值,平均值就是温度测量的结果,针对单片机的最小化优化系统设计,就是要对控制系统的内部存储水平进行拓展。
蒸汽锅炉PID温度控制系统设计

目旳:
对锅炉过热蒸汽温度控制系统进行分析和设计,而对 锅炉过热蒸汽旳良好控制是确保系统输出蒸汽温度稳 定旳前提。所以本设计采用串级控制系统,这么能够 极大地消除控制系统工作中旳多种干扰原因,使系统 能在一种较为良好旳状态下工作,同步锅炉过热器出 口蒸汽温度在允许旳范围内变化,并保护过热器管壁 温度不超出允许旳工作温度。
调整器接受过热器出口蒸汽温度t变化后,调整器才开始动作, 去控制减温水流量W ,W旳变化又要经过一段时间才干影响到 蒸汽温度t,这么既不能及早发觉扰动,又不能及时反应控制旳 效果,将使蒸汽温度t发生很大旳动态偏差,影响锅炉生产旳安 全和经济运营。
燃烧工况
温度设定值
控制信号
喷水流量
控制器
执行器
过热器
温度变送器
在本设计用到串级控制系统中,主对象为送入负荷设 备旳出口温度,副对象为减温器和过热器之间旳蒸汽 温度,经过控制减温水旳流量来实现控制过热蒸汽温 度旳目旳。
蒸汽锅炉工艺流程及控制要求
蒸汽锅炉工艺流程及控制要求
锅炉是一种具有多输入、多输出且变量之间相互关联 旳被控对象。 过热蒸汽温度控制系统:主要使过热器出口温度保持 在允许范围内,并确保管壁温度不超出工艺允许范围;
被控对象建模
根据在减温水量扰动时,过热蒸汽温度有较大旳容积迟延, 而减温器出口蒸汽温度却有明显旳导前作用,完全能够构成 以减温器出口蒸汽温度为副参数,过热蒸汽温度为主参数旳 串级控制系统
温度设定值
温度主调节器
副调节器
减温水流量
蒸汽流量或者烟
扰动
气热量扰动
阀 门
减温器 2
过热蒸汽温度
过热器 1
温度变送器 温度变送器
基于单片机PID算法的电加热炉温度控制系统设计
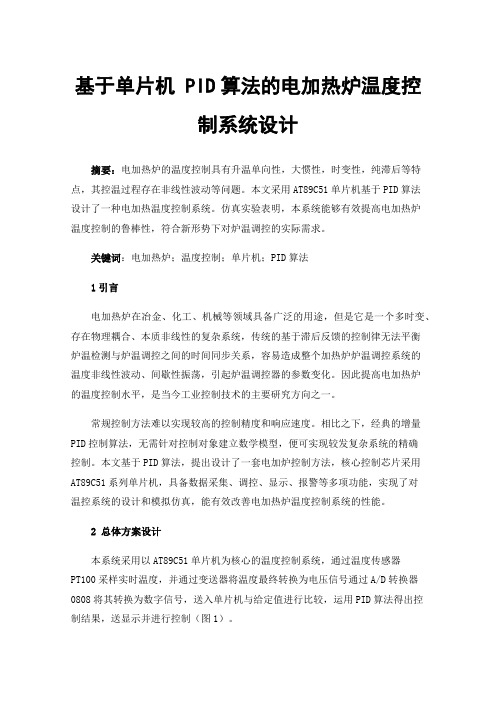
基于单片机 PID算法的电加热炉温度控制系统设计摘要:电加热炉的温度控制具有升温单向性,大惯性,时变性,纯滞后等特点,其控温过程存在非线性波动等问题。
本文采用AT89C51单片机基于PID算法设计了一种电加热温度控制系统。
仿真实验表明,本系统能够有效提高电加热炉温度控制的鲁棒性,符合新形势下对炉温调控的实际需求。
关键词:电加热炉;温度控制;单片机;PID算法1引言电加热炉在冶金、化工、机械等领域具备广泛的用途,但是它是一个多时变、存在物理耦合、本质非线性的复杂系统,传统的基于滞后反馈的控制律无法平衡炉温检测与炉温调控之间的时间同步关系,容易造成整个加热炉炉温调控系统的温度非线性波动、间歇性振荡,引起炉温调控器的参数变化。
因此提高电加热炉的温度控制水平,是当今工业控制技术的主要研究方向之一。
常规控制方法难以实现较高的控制精度和响应速度。
相比之下,经典的增量PID控制算法,无需针对控制对象建立数学模型,便可实现较发复杂系统的精确控制。
本文基于PID算法,提出设计了一套电加炉控制方法,核心控制芯片采用AT89C51系列单片机,具备数据采集、调控、显示、报警等多项功能,实现了对温控系统的设计和模拟仿真,能有效改善电加热炉温度控制系统的性能。
2总体方案设计本系统采用以AT89C51单片机为核心的温度控制系统,通过温度传感器PT100采样实时温度,并通过变送器将温度最终转换为电压信号通过A/D转换器0808将其转换为数字信号,送入单片机与给定值进行比较,运用PID算法得出控制结果,送显示并进行控制(图1)。
图1 系统总体设计方案图2.1系统硬件选择单片机是指将微处理器、存储器和输入/输出接口电路集成在一块集成电路芯版上的单片微型计算机。
单片机主要应用于工业控制领域,用来实现对信号的检测、数据的采集以及对应用对象的控制。
它具有体积小、重量轻、价格低、可靠性高、耗电少和灵活机动等许多优点。
单片机是微型计算机的一个重要分支,特别适合用于智能控制系统。
PID温度控制的实现
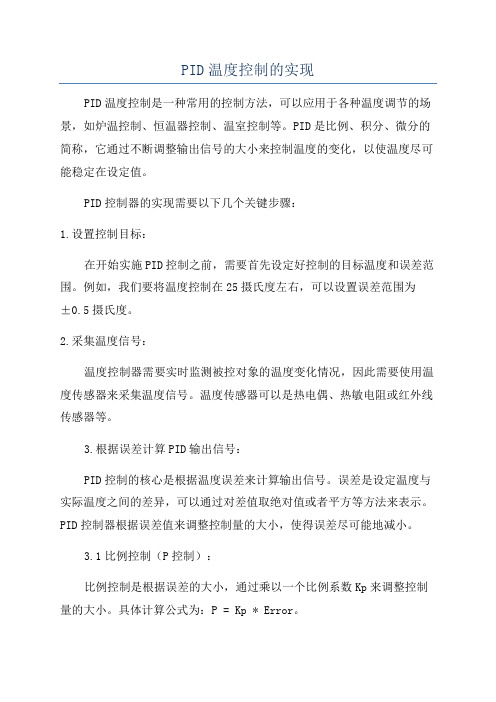
PID温度控制的实现PID温度控制是一种常用的控制方法,可以应用于各种温度调节的场景,如炉温控制、恒温器控制、温室控制等。
PID是比例、积分、微分的简称,它通过不断调整输出信号的大小来控制温度的变化,以使温度尽可能稳定在设定值。
PID控制器的实现需要以下几个关键步骤:1.设置控制目标:在开始实施PID控制之前,需要首先设定好控制的目标温度和误差范围。
例如,我们要将温度控制在25摄氏度左右,可以设置误差范围为±0.5摄氏度。
2.采集温度信号:温度控制器需要实时监测被控对象的温度变化情况,因此需要使用温度传感器来采集温度信号。
温度传感器可以是热电偶、热敏电阻或红外线传感器等。
3.根据误差计算PID输出信号:PID控制的核心是根据温度误差来计算输出信号。
误差是设定温度与实际温度之间的差异,可以通过对差值取绝对值或者平方等方法来表示。
PID控制器根据误差值来调整控制量的大小,使得误差尽可能地减小。
3.1比例控制(P控制):比例控制是根据误差的大小,通过乘以一个比例系数Kp来调整控制量的大小。
具体计算公式为:P = Kp * Error。
其中,Kp是比例系数,Error是温度设定值与实际温度的差异。
3.2积分控制(I控制):积分控制是对误差进行累计,以减小稳态误差。
它通过乘以一个积分系数Ki来调整控制量的大小。
具体计算公式为:I = Ki * ∑(Error * dt)。
其中,Ki是积分系数,∑(Error * dt)是误差的积分值,dt为采样时间间隔。
3.3微分控制(D控制):微分控制是根据误差变化的速率来调整控制量的大小,以抑制温度的过冲或超调。
它通过乘以一个微分系数Kd来调整控制量的大小。
具体计算公式为:D = Kd * (dError/dt)。
其中,Kd是微分系数,(dError/dt)为误差的微分值,表示误差的变化速率。
4.计算总的输出信号:总的输出信号可以通过加权求和来计算,即 Output = P + I + D。
北京交通大学水温炉温控制pid系统课程设计
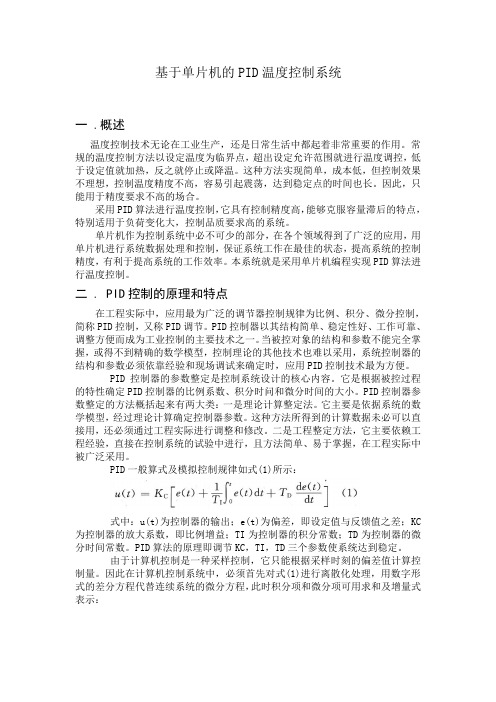
基于单片机的PID温度控制系统一 .概述温度控制技术无论在工业生产,还是日常生活中都起着非常重要的作用。
常规的温度控制方法以设定温度为临界点,超出设定允许范围就进行温度调控,低于设定值就加热,反之就停止或降温。
这种方法实现简单,成本低,但控制效果不理想,控制温度精度不高,容易引起震荡,达到稳定点的时间也长。
因此,只能用于精度要求不高的场合。
采用PID算法进行温度控制,它具有控制精度高,能够克服容量滞后的特点,特别适用于负荷变化大,控制品质要求高的系统。
单片机作为控制系统中必不可少的部分,在各个领域得到了广泛的应用,用单片机进行系统数据处理和控制,保证系统工作在最佳的状态,提高系统的控制精度,有利于提高系统的工作效率。
本系统就是采用单片机编程实现PID算法进行温度控制。
二 . PID控制的原理和特点在工程实际中,应用最为广泛的调节器控制规律为比例、积分、微分控制,简称PID控制,又称PID调节。
PID控制器以其结构简单、稳定性好、工作可靠、调整方便而成为工业控制的主要技术之一。
当被控对象的结构和参数不能完全掌握,或得不到精确的数学模型,控制理论的其他技术也难以采用,系统控制器的结构和参数必须依靠经验和现场调试来确定时,应用PID控制技术最为方便。
PID控制器的参数整定是控制系统设计的核心内容。
它是根据被控过程的特性确定PID控制器的比例系数、积分时问和微分时间的大小。
PID控制器参数整定的方法概括起来有两大类:一是理论计算整定法。
它主要是依据系统的数学模型,经过理论计算确定控制器参数。
这种方法所得到的计算数据未必可以直接用,还必须通过工程实际进行调整和修改。
二是工程整定方法,它主要依赖工程经验,直接在控制系统的试验中进行,且方法简单、易于掌握,在工程实际中被广泛采用。
PID一般算式及模拟控制规律如式(1)所示:式中:u(t)为控制器的输出;e(t)为偏差,即设定值与反馈值之差;KC为控制器的放大系数,即比例增益;TI为控制器的积分常数;TD为控制器的微分时间常数。
温控器PID调节方法

温控器PID调节方法比例(proportion)调节:是按比例反应系统的偏差,比例(P值)越小引发同样调节的所需的偏差越小,(即同样偏差引起的调节越大,即P值与调节作用成反比)可以加快调节,减少误差,但可使系统的稳定性下降,甚至不稳定。
比例越大,所需偏差越大,系统反应越迟钝。
积分(integral)调节:是使系统消除稳态误差,提高无差度。
只要有误差,积分调节就进行,直至无差,积分调节停止。
积分作用的强弱与积分时间常数(完成一次积分所需的时间)I值成反比。
积分时间短,调节作用强。
积分时间长,动态响应慢。
积分作用常与另两种调节规律结合,组成PI调节器或PID调节器。
微分(differential)调节:微分反映系统偏差信号的变化率。
能预见偏差变化的趋势,产生超前的控制作用,,减少超调,减少调节时间。
微分作用对噪声干扰有放大作用,因此D值太大,对系统抗干扰不利。
微分调节作用的大小与微分时间成正比。
微分作用需要与另外两种调节相结合,组成PD或PID控制器。
PID参数整定顺口溜参数整定斩乱麻,P I D 值顺序查调节作用反反正,小步试验找最佳曲线振荡很频繁,比例度盘要放大曲线漂浮绕大湾,比例度盘往小扳曲线偏离回复慢,积分时间往下降曲线波动摆得快,积分时间再加长,曲线振荡频率快,先把微分降下来动差大来波动慢。
微分时间应加长理想曲线两个波,前高后低4比1一看二调多分析,调节质量不会低。
比例:,加热电流与偏差(即实际值和设定值之差)成比例。
P的大小,在数量上是调节器闭环放大倍数的倒数。
P = 偏差电压∕调节器输出电压比例带越小(P越小),开始时调节电压上升越快,但易过冲。
当温差变小,实际比例越接近P,电压越小。
例如:设定温控于60度,在实际温度为20和40度时,加热的功率就不一样。
积分:如果长时间达不到设定值,积分器起作用,进行修正。
加热电流与偏差的累积(积分)成比例。
因此,只要有偏差存在,尽管偏差极微小,但经过长时间的累积,就会有足够的输出去控制炉丝加热电流,去消除偏差,减少小静态误差。
- 1、下载文档前请自行甄别文档内容的完整性,平台不提供额外的编辑、内容补充、找答案等附加服务。
- 2、"仅部分预览"的文档,不可在线预览部分如存在完整性等问题,可反馈申请退款(可完整预览的文档不适用该条件!)。
- 3、如文档侵犯您的权益,请联系客服反馈,我们会尽快为您处理(人工客服工作时间:9:00-18:30)。
在交流 220 V、50 Hz 交流市电回路中,图 3 中只给出了 A 相。移相触发脉冲由 ADuC845 用 软件在 P1.3 引脚上产生的,零同步脉冲同步后,经光耦合管和驱动器输出送到可控硅的控 制极。过零同步脉冲由过零触发电路产生,利用同步变压器和电压比较器 LM311 组成正弦交 流电的正半波过零检测电路,它在交流电每一个正半周的起始零点处产生上升沿.并在正半 周回零处产生一个下降沿,电压比较器 LM311 用于把 50 Hz 正弦交流电压变成方波。方波的 正边沿和负边沿分别作为两个单稳态触发器的输入触发信号,单稳态触发器输出的 2 个窄脉 冲经二极管或门混合后通过可重复触发集成单稳态触发器 MC14528,单稳态输出的两路窄脉 冲再叠加,就可得到对应于交流市电的 100 Hz 过零同步脉冲。脉冲宽度可由 MC14528 的外 接电阻 R4 和外接电容 C1、C2 调节。此脉冲加到 ADUC845 的 TO 作为计数脉冲和 INT1 中断口 触发 INT1 中断。可控硅的过流、过压保护采用一般阻容保护电路。R5 是触发器输出限流电 阻,R3 用以消除漏电流,防止 KP150 的误触发。
4 结语 将系统温度设置不同的温度值,观测记录温度变化曲线。电加热炉温度控制系统实际输
出的响应曲线如图 6 所示。
从电加热炉温度控制的实际效果来看,Fuzzy-PID 复合控制器具有以下特点:①系统具 有较好动态特性。不仅升温速度快,而且超调量很小;②系统具有比较理想的稳态品质,稳 态过程没有振荡,温度控制精度在±3℃以内;③系统的抗干扰能力增强,对生产现场的各 种噪声和干扰具有较好的抑制作用;④当被控过程参数发生变化时,控制系统仍能保持较好 的适应能力和鲁棒性。
3.2 模糊自整定 PID 算法程序 模糊自整定 PID 算法程序程序的总流程为:首先模糊整定,然后根据误差和误差变化率
对 PID 的 3 个参数进行在线调整,把经过模糊调整后的 PID 参数作为最终的控制参数进行 PID 控制。温度误差 e 和温度误差变化率△e 的最坏情况值均取为 100℃,在此建立的温度 误差 e 和温度误差变化率△e 的基本论域,数字量化确定 e(k)的论域区间为[-128,128]。 这样就必须对温度误差 e 和温度误差变化率△e 超过 100°C.变换后的 e 和△e 其动态范围 限幅压缩,这样就可以使温度误差和温度误差变化率△e 在整个测控温度变化范围[0℃,1 112°C]内,控制量都可以起到作用。图 5 为模糊 PID 控制流程。
电阻炉的温度先由热电偶温度传感器检测并转换成微弱的电压信号,温度变送器将此弱 信号进行非线性校正及电压放大后,由单片机内部 A/D 转换器将其转换成数字量。此数字 量经数字滤波、误差校正、标度变换、线性拟合、查表等处理后。一方面将炉窑温度经人机 面板上的 LCD 显示:另一方面将该温度值与被控制值(由键盘输入的设定温度值)比较,根据 其偏差值的大小,提供给控制算法进行运算,最后输出移相控制脉冲,放大后触发可控硅导 通(即控制电阻炉平均功率)。达到控制电炉温度的目的。如果实际测得的温度值超过了该系 统所要求的温度范围,单片机就向报警装置发出指令,系统进行报警。 2.1 系统主控模块
基于模糊 PID 算法的电阻炉温度控制系统设计 来源:国外电子元器件 作者:蒋芳芳,郑颖
引言 电加热炉是典型工业过程控制对象,其温度控制具有升温单向性,大惯性,纯滞后,时
变性等特点,很难用数学方法建立精确的模型和确定参数。而 PID 控制因其成熟,容易实现, 并具有可消除稳态误差的优点,在大多数情况下可以满足系统性能要求,但其性能取决于参 数的整定情况。且快速性和超调量之间存在矛盾,使其不一定满足快速升温、超调小的技术 要求。模糊控制在快速性和保持较小的超调量方面有着自身的优势,但其理论并不完善,算 法复杂,控制过程会存在稳态误差。
系统主控模块电路如图 2 所示,它主要由 CPU 及数据存储器,晶体振荡器、复位电路、 图形液晶显示器(LCD)及控制电路、微型打印机接口控制电路、实时日历时钟,热电偶信号 处理电路等构成。这里,该系统设计可测量 3 点温度。传感器选择 K 型(镍铬-镍硅)热电偶, 可用于从室温到 1 200°C 的温度测量,测量范围宽,精度高。在温度测量范围内 K 型热电 偶的输出热电势只有 0~45.119 mV,为了和 ADuC845 的 A/D 转换器相匹配,采用 ACl226 和 1B51 作为信号调理电路,由 AC1226、1B51 构成热电偶冷端温度补偿Байду номын сангаас信号调理器电路。 当热端距测温仪表较远时,需利用热电偶匹配导线将冷端延长。CD4051 为多路模拟开关, 由 ABC 控制接通,当 5~3 接通时,输入接地,UO 输出 UOmin,用于零点校准;当 4~3 接通 时,单片机 1.25 V 稳定参考电压 Uref,再经电阻 R1、R2 分压,得到毫伏级参考输入电压, UO 输出 UOmax,用于增益校准;当 2~3、1~3、12~3 分别分时接通时,依次输入 3 个热电 偶正常测温所得变换电压,UO 从而输出 3 个温度点所对应的电压 UOA,UOB,UOC。在 HI 端 与+UISO 端之间串上一只 220 MΩ上拉电阻,一旦热电偶开路,HI 端即被偏置为+UISO,迫 使 1B51 的输出电压超量程,由此判定热电偶已开路。多路模拟开关和测量数据采集过程在 单片机协调下工作,每次数据采集都进行自动判断和校准阁。
将模糊控制算法引入传统的加热炉控制系统构成智能模糊控制系统,利用模糊控制规则 自适应在线修改 PID 参数,构成模糊自整定:PID 控制系统,借此提高其控制效果。 基于 PID 控制算法,以 ADuC845 单片机为主体,构成一个能处理较复杂数据和控制功能的智能控 制器,使其既可作为独立的单片机控制系统,又可与微机配合构成两级控制系统。该控制器 控制精度高,具有较高的灵活性和可靠性。
2 温度控制系统硬件设计 该系统设计的硬件设计主要由单片机主控、前向通道、后向通道、人机接口和接口扩展
等模块组成,如图 l 所示。由图 1 可见,以内含 C52 兼容单片机的 ADuC845 为控制核心.配 有 640 KB 的非易失 RAM 数据存储器、外扩键盘输人、320x240 点阵的图形液晶显示器进行 汉字、图形、曲线和数据显示,超温报警装置等外围电路;预留微型打印机接口,可以现场 打印输出结果;预留 RS232 接口,能和 PC 机联机,将现场检测的数据传输至 PC 机来进一步 处理、显示、打印和存档。
3 温度控制系统软件设计 3.1 主程序及其功能
软件设计采用模块化设计原则。控制程序主要由测量采样操作,温度参数设置界面的显 示,操作按键的管理,测量过程,数据算法处理,输出控制的处理及测量结果显示等模块组 成。主模块是为其他模块构建整体框架及初始化工作。调用运算和显示构成一个无限循环圈, 温控的所有功能都在该循环圈中周而复始有选择执行。除非掉电或复位,否则系统程序不会 跳出该循环圈。因浮点数运算占用时间较多,应将其作为单独模块。控制算法模块包括:PID 运算模块和 PID 参数自整定模块两部分,主要是相应控制算法的初始化及运算程序。数学运 算模块主要包括诸如带符号浮点数求补运算、带符号浮点数乘法、无符号浮点数除法以及浮 点数加减法等运算子程序,供其他模块根据算法的需要随时调用。显示设定和操作界面由菜 单显示,用 INTO 中断完成。界面中用线框框起来的符号和汉字表示当前起作用的按键,用 “上下左右”按键移动光标和改变数据,按下确认键后选中有效,开始执行所选功能,按下 返回键就回到上一级界面(菜单)。数据的采集及预处理模块由 TO 计数定时产生中断,包括 数字滤波、标度变换、显示刷新等部分,完成数据预处理及人机交互功能。过零同步由交流 过零触发产生 INT1 中断,并确定移相顺序,触发 T1 定时,产生移相脉冲,控制输出。一旦 中断,首先判断具体的中断源。若是定时中断,则调用相应的模块完成定时服务;若是人机 面板的按键中断,则在识别按键后,进入散转程序,随之调用相应的键盘处理服务模块。无 论是哪一个中断源产生中断,执行完相应的程序后均返回主模块,必要时修改显示内容,并 开始下一轮循环。图 4 所示为系统软件主程序流程。