活性染料Rf值和织物回潮率对轧染色差的影响
活性染料的性能指标及测定方法溶解性高品质的活性染料商品应
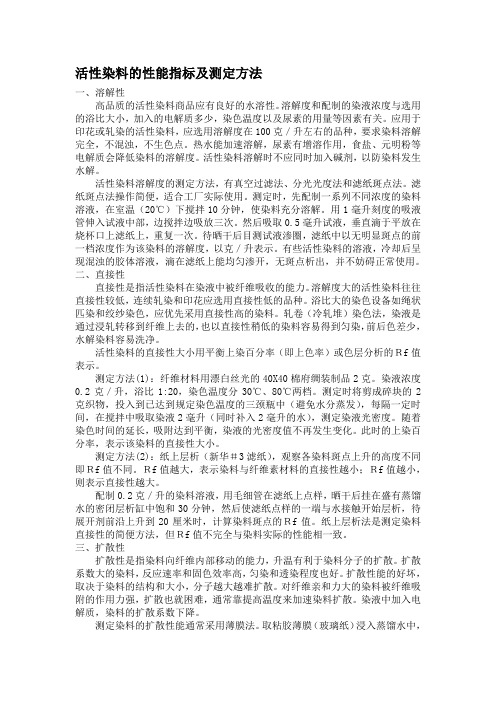
活性染料的性能指标及测定方法一、溶解性高品质的活性染料商品应有良好的水溶性。
溶解度和配制的染液浓度与选用的浴比大小,加入的电解质多少,染色温度以及尿素的用量等因素有关。
应用于印花或轧染的活性染料,应选用溶解度在100克/升左右的品种,要求染料溶解完全,不混浊,不生色点。
热水能加速溶解,尿素有增溶作用,食盐、元明粉等电解质会降低染料的溶解度。
活性染料溶解时不应同时加入碱剂,以防染料发生水解。
活性染料溶解度的测定方法,有真空过滤法、分光光度法和滤纸斑点法。
滤纸斑点法操作简便,适合工厂实际使用。
测定时,先配制一系列不同浓度的染料溶液,在室温(20℃)下搅拌10分钟,使染料充分溶解。
用1毫升刻度的吸液管伸入试液中部,边搅拌边吸放三次。
然后吸取0.5毫升试液,垂直滴于平放在烧杯口上滤纸上,重复一次。
待晒干后目测试液渗圈,滤纸中以无明显斑点的前一档浓度作为该染料的溶解度,以克/升表示。
有些活性染料的溶液,冷却后呈现混浊的胶体溶液,滴在滤纸上能均匀渗开,无斑点析出,并不妨碍正常使用。
二、直接性直接性是指活性染料在染液中被纤维吸收的能力。
溶解度大的活性染料往往直接性较低,连续轧染和印花应选用直接性低的品种。
浴比大的染色设备如绳状匹染和绞纱染色,应优先采用直接性高的染料。
轧卷(冷轧堆)染色法,染液是通过浸轧转移到纤维上去的,也以直接性稍低的染料容易得到匀染,前后色差少,水解染料容易洗净。
活性染料的直接性大小用平衡上染百分率(即上色率)或色层分析的Rf值表示。
测定方法(1):纤维材料用漂白丝光的40X40棉府绸装制品2克。
染液浓度0.2克/升,浴比1:20,染色温度分30℃、80℃两档。
测定时将剪成碎块的2克织物,投入到已达到规定染色温度的三颈瓶中(避免水分蒸发),每隔一定时间,在搅拌中吸取染液2毫升(同时补入2毫升的水),测定染液光密度。
随着染色时间的延长,吸附达到平衡,染液的光密度值不再发生变化。
此时的上染百分率,表示该染料的直接性大小。
轧染色差的原因及预防措施
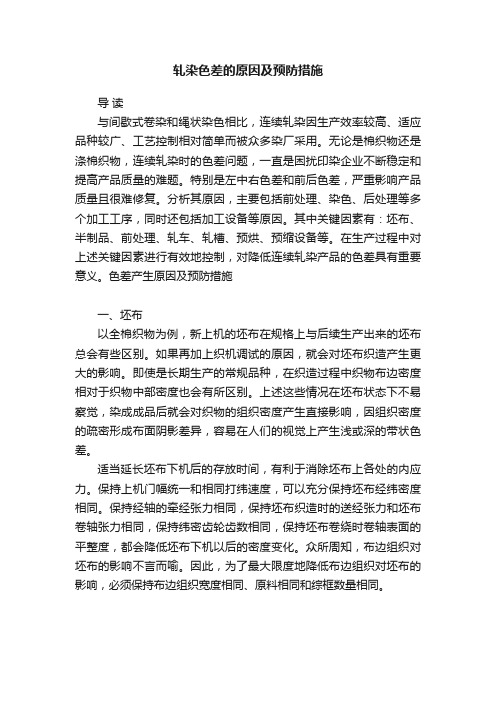
轧染色差的原因及预防措施导读与间歇式卷染和绳状染色相比,连续轧染因生产效率较高、适应品种较广、工艺控制相对简单而被众多染厂采用。
无论是棉织物还是涤棉织物,连续轧染时的色差问题,一直是困扰印染企业不断稳定和提高产品质量的难题。
特别是左中右色差和前后色差,严重影响产品质量且很难修复。
分析其原因,主要包括前处理、染色、后处理等多个加工工序,同时还包括加工设备等原因。
其中关键因素有:坯布、半制品、前处理、轧车、轧槽、预烘、预缩设备等。
在生产过程中对上述关键因素进行有效地控制,对降低连续轧染产品的色差具有重要意义。
色差产生原因及预防措施一、坯布以全棉织物为例,新上机的坯布在规格上与后续生产出来的坯布总会有些区别。
如果再加上织机调试的原因,就会对坯布织造产生更大的影响。
即使是长期生产的常规品种,在织造过程中织物布边密度相对于织物中部密度也会有所区别。
上述这些情况在坯布状态下不易察觉,染成成品后就会对织物的组织密度产生直接影响,因组织密度的疏密形成布面阴影差异,容易在人们的视觉上产生浅或深的带状色差。
适当延长坯布下机后的存放时间,有利于消除坯布上各处的内应力。
保持上机门幅统一和相同打纬速度,可以充分保持坯布经纬密度相同。
保持经轴的牵经张力相同,保持坯布织造时的送经张力和坯布卷轴张力相同,保持纬密齿轮齿数相同,保持坯布卷绕时卷轴表面的平整度,都会降低坯布下机以后的密度变化。
众所周知,布边组织对坯布的影响不言而喻。
因此,为了最大限度地降低布边组织对坯布的影响,必须保持布边组织宽度相同、原料相同和综框数量相同。
二、半制品半制品的加工质量对成品质量的影响远远大于染色工序本身。
所以,从坯布准备开始,翻布、打印、缝头等准备工序的每次加工都会影响棉织物练漂的加工质量。
烧毛、退浆、煮练、漂白、丝光、轧水和烘干工序都可以决定染色质量。
半制品质量问题通常会在染色才体现出来,因此,严格控制棉织物前处理加工各工序的工艺参数、工艺配方和工艺流程就显得非常重要。
活性染料的性能
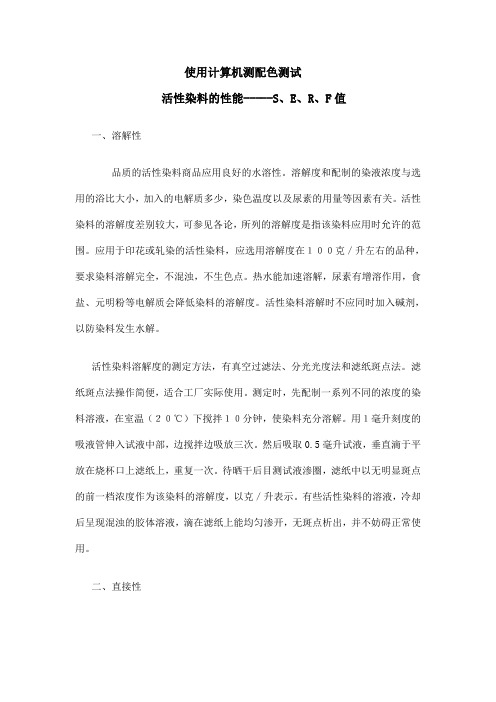
使用计算机测配色测试活性染料的性能-----S、E、R、F值一、溶解性品质的活性染料商品应用良好的水溶性。
溶解度和配制的染液浓度与选用的浴比大小,加入的电解质多少,染色温度以及尿素的用量等因素有关。
活性染料的溶解度差别较大,可参见各论,所列的溶解度是指该染料应用时允许的范围。
应用于印花或轧染的活性染料,应选用溶解度在100克/升左右的品种,要求染料溶解完全,不混浊,不生色点。
热水能加速溶解,尿素有增溶作用,食盐、元明粉等电解质会降低染料的溶解度。
活性染料溶解时不应同时加入碱剂,以防染料发生水解。
活性染料溶解度的测定方法,有真空过滤法、分光光度法和滤纸斑点法。
滤纸斑点法操作简便,适合工厂实际使用。
测定时,先配制一系列不同的浓度的染料溶液,在室温(20℃)下搅拌10分钟,使染料充分溶解。
用1毫升刻度的吸液管伸入试液中部,边搅拌边吸放三次。
然后吸取0.5毫升试液,垂直滴于平放在烧杯口上滤纸上,重复一次。
待晒干后目测试液渗圈,滤纸中以无明显斑点的前一档浓度作为该染料的溶解度,以克/升表示。
有些活性染料的溶液,冷却后呈现混浊的胶体溶液,滴在滤纸上能均匀渗开,无斑点析出,并不妨碍正常使用。
二、直接性直接性是指活性染料在染液中被纤维吸收的能力。
溶解度大的活性染料往往直接性较低,连续轧染和印花应选用直接性低的品种。
浴比大的染色设备如绳状匹染和绞纱染色,应优先采用直接性高的染料。
轧卷(冷轧堆)染色法,染液是通过浸轧转移到纤维上去的,也以直接性稍低的染料容易得到匀染,前后色差少,水解染料容易洗净。
活性染料的直接性大小用平衡上染百分率(即上色率)或色层分析的Rf值表示。
测定方法(1):纤维材料用漂白丝光的40X40棉府绸装制品2克。
染液浓度0. 2克/升,浴比20:1,染色温度分30℃、80℃两档。
测定时将剪成碎块的2克织物,投入到已达到规定染色温度的三颈瓶中(避免水分蒸发),每隔一定时间,在搅拌中吸取染液2毫升(同时补入2毫升的水),测定染液光密度。
技术中温型活性翠蓝浸染染色,为什么容易产生色点、色渍染疵?该如何预防?

技术中温型活性翠蓝浸染染色,为什么容易产生色点、色渍染疵?该如何预防?1产生原因中温型活性翠蓝浸染染色时,之所以容易产生色点、色渍染疵,是由于活性翠蓝存在耐盐、碱溶解稳定性差的缺陷所致。
中温型活性翠蓝在电解质的常规浓度(<80g/L)下,耐盐溶解稳定性尚好。
染料的凝聚程度不足以危害染色质量。
在纯碱的常规浓度(<25g/L)下,耐碱溶解稳定性良好, 染料的聚集不明显。
但在盐、碱共存的固色液中,其溶解稳定性则会大幅度下降。
经检测,固色浴中的盐、碱混合浓度,一旦>80g/L,染液中的染料不仅会发生显著甚至严重的“絮聚”,而且会在染液液面形成含有染料絮聚体的大量泡沫。
这些泡沫一旦黏附到织物上,便会造成色点色渍染疵。
导致活性翠蓝在固色浴中产生絮聚的原因有以下两个:①在固色浴中盐、碱共存(纯碱也是电解质),使染液中的钠离子(Na+)浓度大幅度提高方面,由于同离子效应的影响,使染料中的亲水性基团电离度变小,从而导致染料的亲水性下降。
D-SO3 Na←→D-SO3+Na亲水性较弱亲水性较强另一方面,由于Na+具有较大的水合能力,它能以直接或间接水化层的形式吸附大量极性水分子,从而对已溶解的染料产生较大的盐析作用。
②在碱性浴中,染料中的β羟乙基砜硫酸酯活性基,会发生消去反应,硫酸酯基脱落,变为乙烯砜基。
从而使原本亲水性的基团变为疏水性基团,使染料自身的水溶性显著下降。
染料的亲水性骤然变小,受水的排斥力骤然增大,水中的染料为求得稳定而发生相互聚集。
2预防的措施电解质的施加①.施加浓度。
活性翠蓝的水溶性高。
在80℃的软化水中,其溶解度可达150g (注:活性翠蓝与其他活性染料有所不同,其染液的胶凝性十分突出,但与染料的凝聚性有着本质的区别,它不会因此产生色点、色渍染疵)。
所以,其竭染率受电解质的制约性较大,只有在较多电解质的存在下染色,才能获得较高的上染量。
然而,电解质浓度必须适当。
倘若浓度过高,最终的平衡上染率提高不明显,反而会使固色液的盐、碱混合浓度超高(>80g/L),导致染料发生过度凝聚,产生色点、色渍危害染色质量。
活性染料染全棉织物中常见疵病及预防措施

活性染料染全棉织物中常见疵病及预防措施1前言棉织物尤其是高档针织物用活性染料染色十分广阔,从目前形式看高质量、低成本、快速交货是工厂赖以生存的基础,因此如何减少棉织物的病疵,是我们的首要考虑因素。
然而要减少疵病的产生,不仅要考虑棉织物的质量,活性染料的好坏还必须要考虑到助剂、温度、PH值等多重因素。
本文对活性染料染棉织物常出现的病庛进行分析,并由此提出措施和方法[1]。
1.1活性染料的特点活性染料是在化学结构上带反应性基团的水溶性染料,在染色过程中,染料与纤维发生反应,最终生成共价键(酯和醚键),活性染料具有水溶性和直接性,根据结构不同又可分为X型、K型、KN型等,特点如下:(1)吸湿性能优良、手感柔软、穿着舒服(2)湿态强度大于干态强度,但整体上坚牢耐用(3)染色性能好,光泽柔和,有自然美感(4)耐碱,耐高温(5)抗皱性差,缩水率大1.2棉织物的特点棉织物是指以棉纱或棉型化纤混纺纱线织成的纺织品,特点如下:(1) 吸湿性能强,缩水率比较大,约为4%~10%(2)耐酸,织物对无机酸很不稳定,即使较弱的酸也会使棉织物受到破坏,但有机酸对棉织物作用微弱,几乎起不到破坏作用。
棉织物比较耐碱,一般弱碱在常温下对棉布不发生作用,但强碱作用后,棉布强度会下降。
常利用20%的烧碱液处理棉布,可得到“丝光”棉布。
(3)耐热性能一般,在阳光与大气中棉织物会缓慢地被氧化,使强力下降。
长期高温作用会使棉织物遭受破坏,但棉织物可以耐受125℃~150℃短暂高温处理。
(4)微生物对棉织物有破坏作用,表现在棉织物不耐霉菌。
1.3活性染料的染色理论染料之所以在较短时间内会如此快速的上染,是因为在活性染料中存在可与纤维发生反应的活性基。
活性染料的结构有别于其他染料,它们的结构可用下面的通式表示:S-D-B-R式中:S是水溶性基团;D为染料母体;B为桥基;R为活性基。
活性基是活性染料的核心,染色通过它与纤维发生化学键合,这一部分决定了活性染料的反应活性、固色率、色牢度和应用条件。
学习│回潮率的定义以及对染色面料的影响
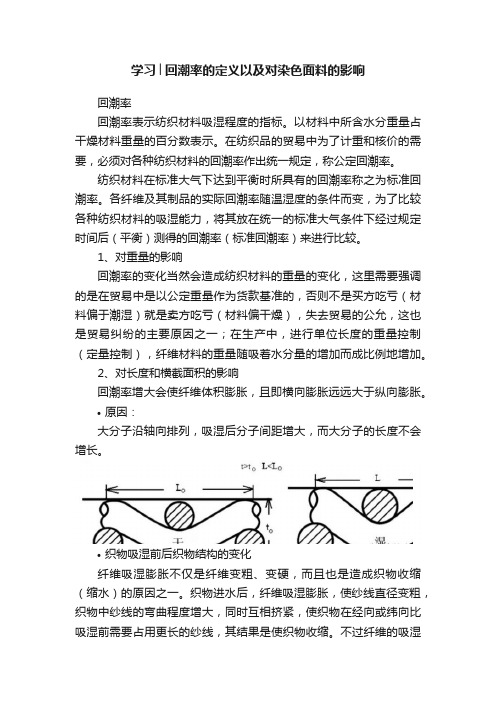
学习│回潮率的定义以及对染色面料的影响回潮率回潮率表示纺织材料吸湿程度的指标。
以材料中所含水分重量占干燥材料重量的百分数表示。
在纺织品的贸易中为了计重和核价的需要,必须对各种纺织材料的回潮率作出统一规定,称公定回潮率。
纺织材料在标准大气下达到平衡时所具有的回潮率称之为标准回潮率。
各纤维及其制品的实际回潮率随温湿度的条件而变,为了比较各种纺织材料的吸湿能力,将其放在统一的标准大气条件下经过规定时间后(平衡)测得的回潮率(标准回潮率)来进行比较。
1、对重量的影响回潮率的变化当然会造成纺织材料的重量的变化,这里需要强调的是在贸易中是以公定重量作为货款基准的,否则不是买方吃亏(材料偏于潮湿)就是卖方吃亏(材料偏干燥),失去贸易的公允,这也是贸易纠纷的主要原因之一;在生产中,进行单位长度的重量控制(定量控制),纤维材料的重量随吸着水分量的增加而成比例地增加。
2、对长度和横截面积的影响回潮率增大会使纤维体积膨胀,且即横向膨胀远远大于纵向膨胀。
•原因:大分子沿轴向排列,吸湿后分子间距增大,而大分子的长度不会增长。
•织物吸湿前后织物结构的变化纤维吸湿膨胀不仅是纤维变粗、变硬,而且也是造成织物收缩(缩水)的原因之一。
织物进水后,纤维吸湿膨胀,使纱线直径变粗,织物中纱线的弯曲程度增大,同时互相挤紧,使织物在经向或纬向比吸湿前需要占用更长的纱线,其结果是使织物收缩。
不过纤维的吸湿膨胀也有有利的一面,如水龙带和雨衣可以利用它们遇水后纤维吸湿变粗使织物更加紧密,而使水更难通过。
膨胀在织物的起皱、干燥和染色等工艺过程中也是一个重要因素。
3、对密度的影响从上图可以看出。
纤维的密度随着回潮率的增加密度先上升而后下降。
4、对机械性质的影响对于大多数纤维而言,其强力随着回潮率的增加而下降,少数纤维几乎不变,个别纤维(棉、麻)的强力上升。
绝大多数纤维的断裂伸长率随着回潮率的增加而上升,少数纤维几乎不变。
这主要由于水分子进入之后拆开了大分子之间的交联,分子间力减小,大分子易滑脱,故强力降低。
活性染料Rf值和织物回潮率对轧染色差的影响
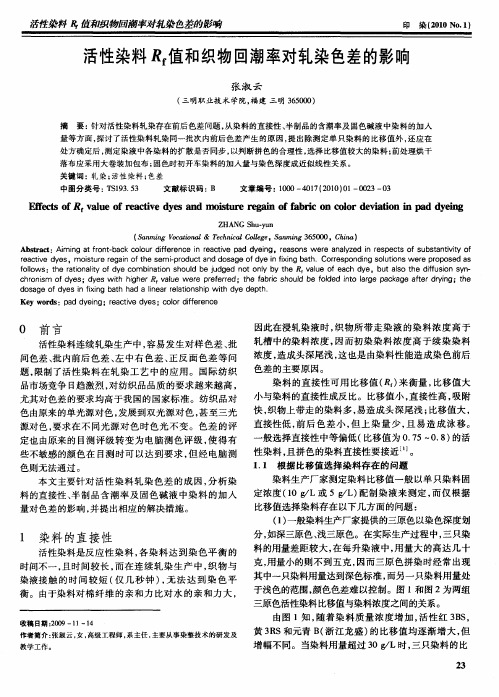
flws tert n l f y o i t ns o l b d e o n yteR au fe c y 。b ta o ted u i y— ol o : h ai ai o ec mbn i h ud ej g d n to l b h f l o a hd e u l h i s ns n o t y d ao u y v e s f o
题, 限制 了活性 染 料 在 轧染 工 艺 中 的应 用 。 国际 纺 织 色 差 的主要原 因 。 染 料 的直 接性 可 用 比移 值 ( ) 衡 量 , 蜀 来 比移 值 大 品市场竞 争 日趋 激烈 , 纺织 品品质 的要 求 越来 越 高 , 对 直 吸 尤其 对色 差 的要 求均 高于 我 国的 国家标 准 。纺 织 品对 小 与染料 的直 接性 成反 比。 比移值 小 , 接性 高 , 附 织物 上带走 的染料 多 , 易造成 头 深尾 浅 ; 比移 值大 , 色 由原来 的单光 源对 色 , 发展 到双 光 源对 色 , 至三 光 快 , 甚
d s g fd e n f ig b t a i e rr lt n hp w i y e t . o a e o y s i i n a h h d a l a ea i s i t d e d p h x n o h Ke r s:p d d e n y wo d a y ig;r a t e d e e c i y s;c l i e e c v oor f r n e d f
前 但 且 源对 色 , 求在 不 同光源 对 色 时 色 光 不 变 。色 差 的评 直 接性低 , 后 色 差 小 , 上 染 量 少 , 易 造 成 泳 移 。 要 般选择 直接性 中等偏低 ( 比移值 为 0 7 0 8 的 活 .5— . ) 定 也 由原 来 的 目测评 级 转 变 为 电脑 测 色 评 级 , 得 有 使
活性染料染深色的色差控制
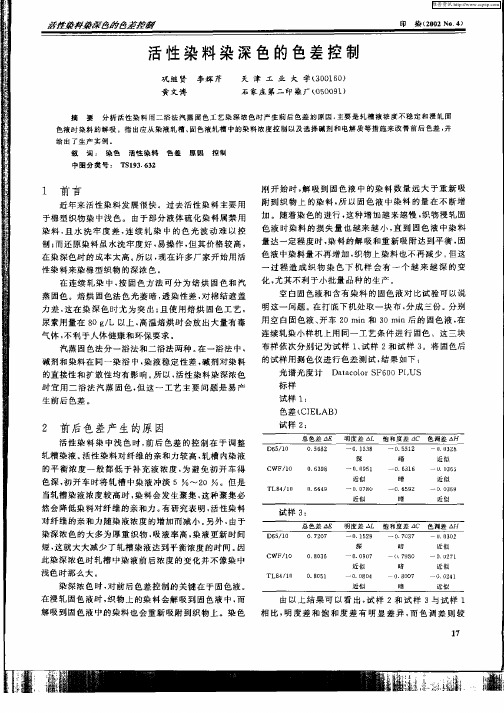
过 程造 成 织物 染 色下 机样 会 有 一 个 越 来 越 深 的变 空 白固色 液和 含有染 料 的固色 液对 比试验 可 以说
化 , 其不 利 于小批量 品种 的生产 。 尤
力 差 , 在染 深 色 时 尤 为突 出 ; 使用 焙 烘 固色 工艺 , 这 且
尿素用 量在 8 / 0g L以上 , 高温 焙烘 时 会放 出大 量有毒 气 体 , 利 于人体健 康 和环保 要求 。 不
汽 蒸 固色法 分一 浴法 和二 浴法两种 。 一 浴法 中 , 在
明这一 问题 。在打底 下机 处取 一块 布 , 分成 三份 。分别 用空 白固色 液 、 车 2 n和 3 n后 的 固色 液 , 开 0mi 0mi 在 连续 轧染小样 机 上用 同一 工 艺条 件进 行 固色 。这 三块 布样 依次 分别 记为试 样 1 试样 2和试 样 3 、 。将 固色后 的试 样用 测色 仪进行 色差 测试 , 结果 如 下 : 光 谱光 度计
刷 开始 时 , 吸 到 固色 液 中 的染 料 数 量远 大 于重 新 吸 解 附 到织 物 上 的染 料 , 以 固色 液 中染 料 的量 在不 断增 所 加 。随着染 色的进行 , 这种增 加 越 来越慢 , 物浸 轧 固 织 色 液 时染 料 的损 失 量 也 越来 越 小 , 到 固色 液 中 染料 直 量达 一定 程 度时 , 料 的解 吸和 重新 吸 附达 到平 衡 , 染 固 色液 中染料 量 不再增 加 , 织物上 染料 也不 再减 少 但这
4 2 工 艺 流 程 .
3 控 制前 后色 差 的方 法
3 1 初开 车染液 轧槽 冲淡 . 上述 已分 析 了染 深 浓色 时 , 槽 中染 液 的前 后 浓 轧
- 1、下载文档前请自行甄别文档内容的完整性,平台不提供额外的编辑、内容补充、找答案等附加服务。
- 2、"仅部分预览"的文档,不可在线预览部分如存在完整性等问题,可反馈申请退款(可完整预览的文档不适用该条件!)。
- 3、如文档侵犯您的权益,请联系客服反馈,我们会尽快为您处理(人工客服工作时间:9:00-18:30)。
活性染料Rf值和织物回潮率对轧染色差的影响
0前言
活性染料连续轧染生产中,容易发生对样色差、批间色差、批内前后色差、左中右色差、正反面色差等问题,限制了活性染料在轧染工艺中的应用。
国际纺织品市场竞争日趋激烈,对纺织品品质的要求越来越高,尤其对色差要求均高于我国的国家标准。
纺织品对色由原来单光源对色,发展到双光源对色,甚至三光源对色,要求在不同光源对色时色光不变。
色差的评定也由原来的目测评级转变为电脑测色评级,使得有些不敏感的颜色在目测时可以达到要求,但经电脑测色则无法通过。
本文主要针对活性染料轧染色差的成因,分析染料的直接性、半制品含潮率及固色碱液中染料的加入量对色差的影响并提出相应的解决措施。
1 染料的直接性
活性染料是反应性染料,各染料达到染色平衡的时间不一,且时间较长,而在连续轧染生产中,织物与染液接触的时间较短(仅几秒钟),无法达到染色平衡。
由于燃料对棉纤维的亲和力大,因此在浸轧染液时,织物所带走染液的染料浓度高于轧槽中的染料浓度,因而初染染料浓度高于续染染料浓度,造成头深尾浅,这也是由染料的性能造成染色前后色差的主要元因。
染料的直接性可用比移值(R f)来衡量,比移值大小与染料的直接性成反比。
比移值小,直接性高,吸附快,织物上带走的染料就多,易造成头深尾浅;比移值大,直接性低。
前后色差小,但上染量少,且易造成泳移。
一般选择直接性中等偏低(比移值为0.75~0.8)的活性染料,且拼色的染料直接性要接近。
1.1根据比移值选择染料存在的问题
染料生产厂家测定染料比移值一般以单只染料固定浓度(10g/L或5g/L)配制染液来测定,而仅根据比移值选择染料存在以下几方面问题:
(1)一般染料生产厂家提供的三原色以染色深度划分,如深三原色、浅三原色。
在实际生产过程中,三只染料的用量差距较大,在每升染液中,用量大的高达几十克,用量小的则不到五克,因而三原色拼染时经常出现其中一只染料用量达到深色标准,而另一种染料用量处于浅色的范围,颜色色差难以控制。
图1和图2为两组三原色活性染料比移值与染料浓度之间的关系。
实验说明,随着染料质量浓度增加,活性红3BS,黄3RS和元青B的比移值均逐渐增大,但增幅不同。
当染料超过30g/L时,三只染料的比移值趋于一致,即三只染料的用量都要达到30g/L以上,该组染料拼色才可获得较好的稳定性和较小的色差;若三只染料的用量差距大,则比移值偏差较大,拼色的稳定性差。
用量相同时,染料红3BS和黄3RS的比移值基本一致;两只染料用量相差10g/L,比移值的差距不大,因而在实际生产中红黄拼色的色差容易控制。
当用量低于30g/L时,元青B与红3BS和黄3RS的比移值差距较大,而在生产中往往是以元青B为主色拼红3BS和黄3RS,元青B用量远大于红黄染料的用量,因此在实际生产中色差很难控制。
对于某些易出现色差的颜色,如中灰色等,不宜选用活性染料,而改用还原染料染色。
由此可以看出,在燃料用量相同的条件下,活性C系列三原色染料的比移值基本一致。
三只染料的用量差距较小时,比移值差距较小,色差易控制。
因此,用该组染料拼染浅色时,稳定性较好,色差较小。
由上可知,对于任何一组在某一特定浓度下测定的比移值接近的染料,在实际生产中,随着染料用量的变化,比移值会出现较大的差异,直接影响色差的控制。
(2)比移值的测定误差大。
在实际测定中发现,染料和水在滤纸的上升轨迹并不是一条直线,而是呈锯齿形,因此读数时会产生误差。
若以单只染料来分别测定,则误差更大。
(3)染料中添加剂对染料比移值的影响。
染料生产厂家在燃料中要加入一定量的添加剂,如无机盐和扩散剂、增溶剂等表面活性剂,这些添加剂会影响比移值的测定。
以下是盐用量对染料比移值的影响。
对于活性CA系列三原色而言,加入无机盐后,CA蓝的比移值变化不大,而CA红和CA黄的比移值分别增加了10%和15%;3BS红和3RS黄的比移值分别增加了13%和10%,而RIS蓝的比移值变化较小。
同样,各种表面活性剂对各染料比移值的影响也有所不同。
1.2比移值测定方法的改进
由于影响比移值的因素众多,仅采用单只染料在特定浓度下的比移值作为拼色染料组合的依据不够准确,因而在确定染色处方后,应按处方的要求配制染液,取染液滴在滤纸上观察各染料扩散的程度是否同步,是否出现分层,进而判断该组染料拼色的合理性。
1.3 染料比移值对前后色差的影响
对轧染而言,选择比移值大的染料,则染料向织物转移的速度慢,初染的浓度与续染的浓度差异较小,头尾色差小,但易出现泳移;选择比移值小的染料,则初染染料浓度与续染
染料的浓度差异较大,头尾色差大,但不容易出现泳移。
在实际生产中,染料的泳移可通过加入防泳移剂,或改进烘干方式加以解决;而初染染料浓度与续染染料浓度的差异却难以解决,通常采用开车冲淡的方式,或提高补充液浓度的方法来解决。
冲淡系数或追加染料的系数会因染料不同、染料用量不同以及织物不同而不同,在实际操作中难度较大。
由于生产批量小,而初染染料浓度与续染染料浓度的平衡需要400~600m布。
因此根据比移值选择染料首先要考虑是减少头尾色差,可选择比移值较大的染料。
实践证明,深三原色的染料或染料浓度高时,比移值较大,因而染深色时初染染料浓度与续染染料浓度差异很小,甚至可以开车无需冲淡轧槽染液;而浅中色染料或染料用量少时,比移值一般较小,初染染料浓度与续染染料浓度差异大,需冲淡染液。
2半制品的含潮率
织物前处理的质量对染色前后色差影响较大,主要影响因素有:半制品的毛效,丝光效果,布面pH值,退浆效果以及半制品的含潮率。
其中半制品含潮率的影响常被忽视。
棉织物的回潮率一般为7%~8%。
印染车间的湿度大,加之在前处理的烘燥过程中,经常过烘落布,堆放在储布车上的织物很快吸湿,造成布边与中间、外层与内部的含潮率不同。
半制品的干湿度对活性染料的浸染影响不大,但对轧染则影响很大。
从而可以看出,半制品水分含量越高,则上染率越低,某些颜色上染率甚至相差15%以上。
由于轧染的轧余率是设定的,半制品局部的含潮率不同,浸轧染液带走的染液量不等,导致织物各部分由于吸附染料的不等而产生色差。
这类色差一般无法通过调整轧车轧余率而纠正,尤其是左中右色差。
实际上,除了半制品的含潮率,印染车间内空气中各种酸、碱、还原剂等对对方的半制品也会产生影响,造成染色色差。
因此,半制品对方过程中要加强现场管理,合理安排前处理的生产量,改进落布堆放方式、采用大卷装加包布,设立半制品对房间,隔离堆放。
3固色碱液中染料的加入量
活性染料轧染常用的染色工艺是轧烘轧蒸法,织物浸轧染液烘干后,再浸轧碱固色液汽蒸固色。
由于织物染液烘干后,染料并未与纤维形成化学结合,而只是物理吸附,浸轧碱液
时织物上的染料会溶落到碱液中,再沾染至后面的织物,从而出现刚开车的布色浅,后续的布色深的现象。
这可以通过开车时在浸轧的碱液中追加染料来克服。
但是在实际生产中,染料的加入量较难掌握,不同颜色、不同深度加入的染料量不同,完全凭经验操作,在生产中会产生批与批之间的色差。
通过对大样生产的跟踪,发现染料的加入量与染色深度以及染料的直接性有关
得知,固色碱液中染料的加入量随着染色深度增加而增大,染色深度在2g/L以下时可以不用加入染料。
同时,染料的加入量还与染料的直接性有关,直接性大,加入量小;直接性小,则加入量大。
实验发现,染料的加入量与染料的比移值有关,当染色深度超过10g/L时,染料的加入量与染色深度成近似线性关系:
染料的加入量=染色深度×比移值/20
对大多数颜色,用上述公式计算染液的加入量,可基本解决由于固色液染料浓度不平衡带来的前后色差,同时,也在很大程度上减少了翻单生产批与批之间的色差。
4总结
(1)活性染料轧染的色差与染料的比移值有关,除了测定单只染料的比移值,还应在处方确定后,测定染液中各种染料的扩散是否同步,是否出现分层,从而判断拼色的合理性。
(2)根据比移值选择染料对解决轧染前后的色差至关重要,选择比移值较大的染料可以解决由于染料直接性带来的前后色差。
(3)半制品的含潮率对染色的影响很大,前处理烘干落布应采用大卷装加包布,并加强现场管理。
(4)固色碱液中染料的加入量与染色深度和染料的比移值有关,加入量与染色深度成近似线性关系。