干货锂电池极片挤压涂布常见缺陷修订稿
锂电池辊压工艺中存在的问题及解决措施
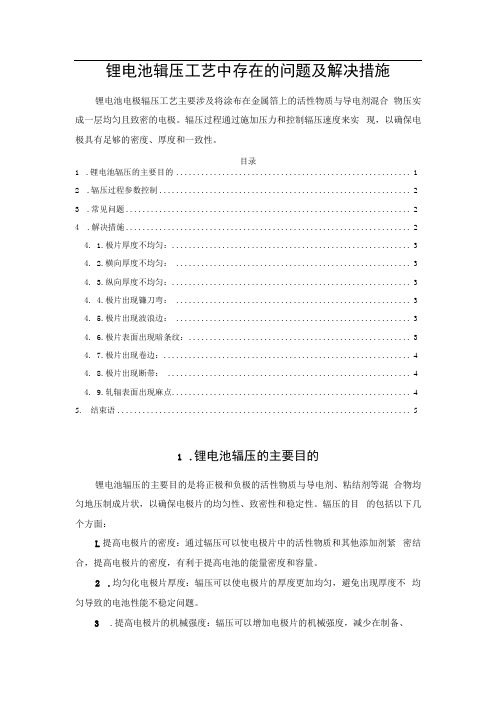
锂电池辑压工艺中存在的问题及解决措施锂电池电极辐压工艺主要涉及将涂布在金属箔上的活性物质与导电剂混合物压实成一层均匀且致密的电极。
辐压过程通过施加压力和控制辐压速度来实现,以确保电极具有足够的密度、厚度和一致性。
目录1.锂电池辐压的主要目的 (1)2.辐压过程参数控制 (2)3.常见问题 (2)4.解决措施 (2)4. 1.极片厚度不均匀: (3)4. 2.横向厚度不均匀: (3)4. 3.纵向厚度不均匀: (3)4. 4.极片出现镰刀弯: (3)4. 5.极片出现波浪边: (3)4. 6.极片表面出现暗条纹: (3)4. 7.极片出现卷边: (4)4. 8.极片出现断带: (4)4. 9.轧辐表面出现麻点 (4)5. 结束语 (5)1.锂电池辐压的主要目的锂电池辐压的主要目的是将正极和负极的活性物质与导电剂、粘结剂等混合物均匀地压制成片状,以确保电极片的均匀性、致密性和稳定性。
辐压的目的包括以下几个方面:L提高电极片的密度:通过辐压可以使电极片中的活性物质和其他添加剂紧密结合,提高电极片的密度,有利于提高电池的能量密度和容量。
2.均匀化电极片厚度:辐压可以使电极片的厚度更加均匀,避免出现厚度不均匀导致的电池性能不稳定问题。
3.提高电极片的机械强度:辐压可以增加电极片的机械强度,减少在制备、组装和使用过程中的断裂和变形。
4.改善电极片的电导率:通过辐压可以使电极片中的导电剂均匀分布,提高电极片的电导率,有利于提高电池的充放电性能。
2.辐压过程参数控制在锂电池制作中,辐压是电池正极和负极片时应控制好以下几个方面:1、辐压温度:控制辐压温度能够影响电池片与电解质层、隔膜的结合程度, 一般需要在一定的温度范围内进行辐压。
2、辐压压力:合适的辐压压力能够确保电池片与电解质层、隔膜的紧密结合,但过大的压力可能会导致电池片变形或损坏。
3、辐压速度:辐压速度的控制也是辐压过程中需要考虑的因素,适当的辐压速度可以确保复合过程的均匀性。
锂电浆料涂布瑕疵及改善方法
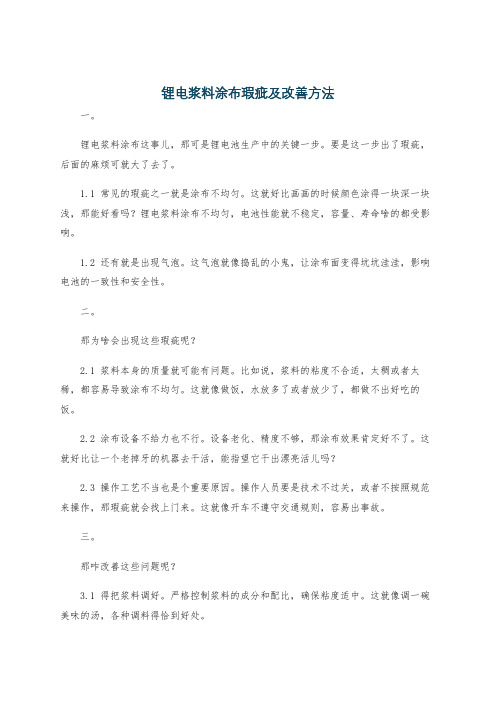
锂电浆料涂布瑕疵及改善方法
一。
锂电浆料涂布这事儿,那可是锂电池生产中的关键一步。
要是这一步出了瑕疵,后面的麻烦可就大了去了。
1.1 常见的瑕疵之一就是涂布不均匀。
这就好比画画的时候颜色涂得一块深一块浅,那能好看吗?锂电浆料涂布不均匀,电池性能就不稳定,容量、寿命啥的都受影响。
1.2 还有就是出现气泡。
这气泡就像捣乱的小鬼,让涂布面变得坑坑洼洼,影响电池的一致性和安全性。
二。
那为啥会出现这些瑕疵呢?
2.1 浆料本身的质量就可能有问题。
比如说,浆料的粘度不合适,太稠或者太稀,都容易导致涂布不均匀。
这就像做饭,水放多了或者放少了,都做不出好吃的饭。
2.2 涂布设备不给力也不行。
设备老化、精度不够,那涂布效果肯定好不了。
这就好比让一个老掉牙的机器去干活,能指望它干出漂亮活儿吗?
2.3 操作工艺不当也是个重要原因。
操作人员要是技术不过关,或者不按照规范来操作,那瑕疵就会找上门来。
这就像开车不遵守交通规则,容易出事故。
三。
那咋改善这些问题呢?
3.1 得把浆料调好。
严格控制浆料的成分和配比,确保粘度适中。
这就像调一碗美味的汤,各种调料得恰到好处。
3.2 设备要更新维护。
定期检查设备,有问题及时修,该换新的就换新的。
别心疼那点钱,不然因小失大。
锂电浆料涂布这事儿可不能马虎,得用心去做,才能做出高质量的锂电池,让咱们的新能源产业越来越好!。
锂电池涂布工序常见故障和解决方法汇总

锂电池涂布工序是锂电池生产中非常关键的一环,涂布工序的质量直接影响着锂电池的性能和安全性。
然而,在实际生产过程中,涂布工序常常会出现各种故障,影响整个生产线的正常运转。
本文将就锂电池涂布工序常见的故障进行梳理和总结,并提供相应的解决方法,以期为从事锂电池生产的工程师和技术人员提供一定的参考和帮助。
1. 涂布机出现涂布不均匀情况1.1 可能原因:涂布刀片磨损不均匀,导致涂布厚度不均匀;涂布辊与输送辊之间的间隙不一致;涂布材料的粘度不一致。
1.2 解决方法:定期更换涂布刀片,保持其锋利度;调整涂布辊与输送辊的间隙,确保一致;加强涂布材料的粘度控制,确保一致。
2. 涂布机出现漏涂现象2.1 可能原因:涂布刀片损坏或安装不良;输送辊转速过快,导致涂布材料无法被充分涂覆;涂布材料的粘度过高,无法完全附着在电极上。
2.2 解决方法:检查涂布刀片的完好度并及时更换;适当调整输送辊的转速,确保涂布材料可以被充分涂覆;控制涂布材料的粘度,避免过高。
3. 涂布机出现起泡现象3.1 可能原因:涂布材料的挥发性成分过快,导致涂布过程中产生气泡;涂布刀片与电极间的间隙不一致,导致气体无法顺利逸出。
3.2 解决方法:调整涂布材料的挥发性成分,避免过快;确保涂布刀片与电极间的间隙一致,避免气泡产生。
4. 涂布机出现堵塞现象4.1 可能原因:涂布材料中有杂质,导致管道堵塞;输送辊转速过慢,无法及时排出涂布材料。
4.2 解决方法:加强涂布材料的过滤工作,确保无杂质;适当调整输送辊的转速,确保涂布材料能够顺利流动。
5. 涂布机出现电极破损现象5.1 可能原因:输送辊表面粗糙,易划伤电极;涂布刀片安装不稳,易引起电极损伤。
5.2 解决方法:定期对输送辊进行维护和更换,确保表面光滑;定期检查涂布刀片的安装情况,确保稳定可靠。
总结:通过对锂电池涂布工序常见故障和解决方法的梳理和总结,我们可以看到,涂布工序的质量受到多种因素的影响,需要全面而细致的管理和维护。
锂电技术之极片涂覆与干燥中的缩孔现象

锂电技术之极片涂覆与干燥中的缩孔现象
一、缩孔
1、关于缩孔
电极极片特别是负极极片表面出现的圆形或近乎于圆形凹陷,称之为缩孔。
如图1。
图1:涂布时出现的缩孔案例
缩孔这一涂布缺陷常见于涂料应用的涂膜过程中,并非锂离子电池电极片涂布时特有的现象。
2、缩孔的形成
在涂布过程中,膜面可能会产生各种各样的缺陷,气泡、肥边、火山口、多边形凹陷、橘皮状等,缩孔是最常见的问题之一。
涂膜表面凹陷即缩孔,从根本上意义讲都是由于成膜时所产生的表面张力梯度造成的。
这种现象称之为Maragoni效应。
涂布浆料基本组成有三种:粘结剂、粉体材料、分散介质,此外还可能有各种功能性辅助材料。
材料之间表面张力不匹配,是产生缩孔的主要诱因,但涂料的粘度、液膜的流动性以及干燥成膜的风速和烘箱温度、热处理阶段条件和设备状况等等都可能改变表面张力及其作用过程,从而诱发缩孔的产生。
由于固化前可流动膜面中存在低表面张力的微粒(如粉体,油滴等,称之为“污染物”),造成中央表面张力较低,流体以污染物为中心向四周迁移,最终形成边缘高于中心的圆形下陷——缩孔。
也就是说,缩孔中心存在低表面张力的物质,它与周围的涂料存在表面张力差,这个差值是缩孔形成的动力,促使周围的液体沿360度方向背离污染物迁移。
图2:缩孔形成示意图
3、缩孔的防治。
涂布常见性问题解决方法

涂布常见性问题解决方法在谈关于锂电池涂布常见问题的解决方法之前,先说说个人对锂电池的一些想法,关于锂电池这个行业,说的有点广阔了,就说说自己的一些浅显的看法和想法吧!在这个锂电池行业做了快4年了,这是一段不停学习不停钻研的时间,这期间我学习了很多关于锂电池的相关知识,从一个门外汉慢慢摸索算是初窥门径了,因为部门原因很多东西我是不能研究的很深,只能懂些皮毛,在我看来锂电池的研发和制作甚至一些关键的岗位技术并不是想象中的那么难,难得是不肯去学不肯去钻研不愿意去了解的人,总是以为自己懂得已经够多,还有就是一些所谓的关键技术的保密性,其实只要研究一下也会懂些皮毛,但是我觉得对于需要盈利的公司来说有这些就已经做够了,因为做的电池就像生物上的杂交育种一样,是一种材料不断更替不断变化相互组合而实现与理论值最接近的一个过程,但是如何提高理论值却是与锂电池制造行业的相关材料供应商的专业饭,只有材料性能提高了,电池的理论性能才会真正提高,所谓的电池研发就是根据对客户的需求来改变电池的形状及性能,说到这里很多做技术或者职场老人肯定要批斗我这黄毛小二的肤浅,不懂什么是电池的真正内涵,我重申以上观点只是我一个刚刚对电池有点了解的人的观点,电池制作过程中的细节问题以及研发肯定是需要相关的专业知识做基础才能做好,所以大家不要气氛。
从事电池这一行很多人都喜欢把自己学到的东西藏起来,一般人从不会去传授所谓的技术,个人觉得烦三个臭皮匠顶个诸葛亮的话是很有道理的,假想我们要是把自己会的都无偿的与周边的人共享然后集思广益是不是能将电池做的更好就为了保住自己所谓饭碗,导致我们这个制造行业的平均水准难以提升,所以我个人很不赞成的这种做法,现在就将我自己对涂布这一块的一些常见问题的解决方法做一个简单的总结,希望不算是什么泄密,在作出总结之前我想知道在你们工厂的涂布新进人员要多长时间能够真正的掌握,并成为业内人士所谓的熟练涂布手甚至所谓的涂布工程师呢我的答案是最多3个月,因为我把常见的问题做了总结并在他学的过程中就已经教会他如何处理。
锂离子电池极片涂布与干燥过程中的缩孔现象

锂离子电池极片涂布与干燥过程中的缩孔现象锂离子电池的制造过程可以大致分为前工序及后工序两个主要过程,其中前工序包括浆料的制备及极片的涂布和干燥等过程,极片缩孔的问题主要出现在锂离子电芯制备的前工序中,本文主要对极片缩孔产生的原因及改善措施进行的初步的分析及阐述。
极片缩孔定义锂离子电池极片在涂布或者干燥过程中由于非正常原因导致的,在极片表面出现圆形或者近于圆形的凹坑的现象称为极片缩孔,如下图所示。
极片缩孔产生的原因极片制备过程中产生缩孔现象的根本原因为表面张力的变化造成,简单的说就是极片出现凹坑位置的表面张力发生变化,造成局部力的不平衡,因此产生缺陷。
力的变化可以参考下图极片缩孔的改善极片涂布或者干燥过程中,极片缩孔一旦形成,则难以彻底解决,所以有效控制极片缩孔的形成,才是解决极片缩孔的终极办法,设计合理的浆料配方,控制涂布工艺等均可以有效减少涂布缩孔发生的几率。
(1)优化极片浆料的配方尽可能的选择相容性好的分散剂或分散介质,减少涂料本体中低表面张力大颗粒(包括大液滴)的存在;添加疏水表面活性分散剂和溶剂等可以控制缩孔的程度,如在浆料中添加PVP、CMC等具有表面活性的分散剂,保证对低表面张力的颗粒的乳化分散,提高石墨材料在水中的分散能力,即提高水对石墨材料的润湿程度。
(2)优化正负极原材料虽然为相应市场和国家政策的需要,多种新型负极材料不断涌现,但目前锂离子电池的负极材料依然主要集中在石墨材料上,石墨包括人工石墨和天然石墨,这二者都无法直接使用,必须通过包覆、氧化等方法对石墨进行化学深度改性和表面改性,改性的过程中会在石墨表面引入新的亲水基团以改变石墨的亲水性能,但是受工艺条件的限制,可能有部分改性石墨的一致性没有预想的情况那么理想,简单地说就是石墨表面的亲水基团数量并不完全一致,这样就造成石墨材料的亲水性不一致,也即是表面张力不同,这样就会引起锂离子电池极片制备过程中的缩孔现象。
所以对负极或者正极原材料的改进,也是有效预防锂离子电池极片缩孔的主要手段之一。
锂离子电池正极片辊涂存在的问题及解决措施

锂离子电池正极片辊涂存在的问题及解决措施
裴敬龙
【期刊名称】《新疆有色金属》
【年(卷),期】2012()S2
【摘要】锂离子电池正极片的制作是生产锂电池的一个重要工序。
一个性能优异的锂离子电池对其正、负极片的各项衡量指标有着严格的控制精度。
在实际生产中,借助于自动辊涂机如何使极片集体与活性物质料浆精密结合为一个有效的整体。
在极片外观、基体表面与料浆的结合处、料浆压实性、基体的延展性等测试因素上进行综合评价已成为一项不可或缺的技术。
由此产生的一系列问题及解决的方式方法,在这里做了大致的处理。
【总页数】2页(P112-113)
【关键词】极片;辊压机;涂布;锂离子电池
【作者】裴敬龙
【作者单位】新疆昊鑫锂盐开发有限公司
【正文语种】中文
【中图分类】TG146
【相关文献】
1.锂离子电池正极材料Li3V2(PO4)3存在的问题及改性研究进展 [J], 陈美娟
2.锂离子电池正极材料Li3V2(PO4)3存在的问题及改性研究进展 [J], 陈美娟;
3.道人山涂围涂工程的环境问题及解决措施 [J], 周志杰;赖豪杰
4.道人山涂围涂工程的环境问题及解决措施 [J], 周志杰;赖豪杰
5.锂离子电池正极材料LiNiO2存在的问题与解决办法 [J], 叶乃清;刘长久;沈上越因版权原因,仅展示原文概要,查看原文内容请购买。
锂电涂布丨涂布车间常见问题及解决方案
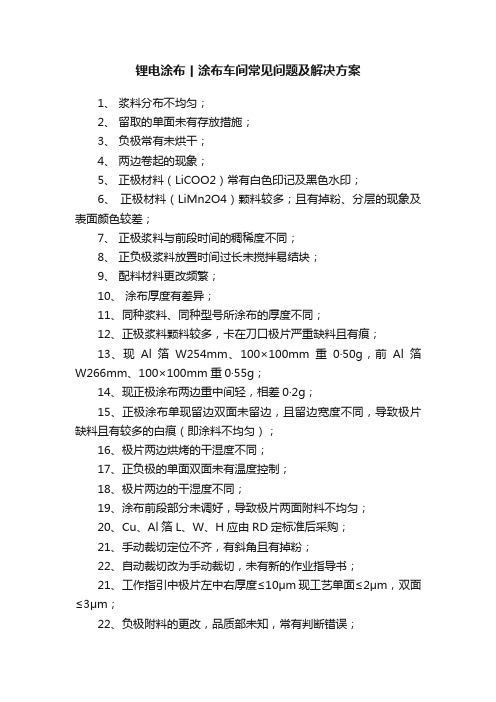
锂电涂布丨涂布车间常见问题及解决方案1、浆料分布不均匀;2、留取的单面未有存放措施;3、负极常有未烘干;4、两边卷起的现象;5、正极材料(LiCOO2)常有白色印记及黑色水印;6、正极材料(LiMn2O4)颗料较多;且有掉粉、分层的现象及表面颜色较差;7、正极浆料与前段时间的稠稀度不同;8、正负极浆料放置时间过长未搅拌易结块;9、配料材料更改频繁;10、涂布厚度有差异;11、同种浆料、同种型号所涂布的厚度不同;12、正极浆料颗料较多,卡在刀口极片严重缺料且有痕;13、现Al箔W254mm、100×100mm重0·50g,前Al箔W266mm、100×100mm重0·55g;14、现正极涂布两边重中间轻,相差0·2g;15、正极涂布单现留边双面未留边,且留边宽度不同,导致极片缺料且有较多的白痕(即涂料不均匀);16、极片两边烘烤的干湿度不同;17、正负极的单面双面未有温度控制;18、极片两边的干湿度不同;19、涂布前段部分未调好,导致极片两面附料不均匀;20、Cu、Al箔L、W、H应由RD定标准后采购;21、手动裁切定位不齐,有斜角且有掉粉;22、自动裁切改为手动裁切,未有新的作业指导书;21、工作指引中极片左中右厚度≤10μm现工艺单面≤2μm,双面≤3μm;22、负极附料的更改,品质部未知,常有判断错误;23、负极涂布双面温度无法升起(设125℃最多升至118℃);24、开窗后外面的温湿度对极片有影响吗;25、正、负单面涂布都是右边卷起,且正极收卷不齐易打皱;26、涂布机的温度与走速是成正比的,如何控制?未有标准;27、单面调机人员未带手套,留在Cu、Al上的手印(即汗渍),导致双面涂布后有明显的黑印迹;28、Al较窄不能留边,导致附在单面两干料,双面极易拉断且拉断次数较多,产生报废;29、涂布未有自检记录及习惯;30、刚停机,极片存放在烘箱中易掉粉;31、涂布完的极片未有明确规定如何存放;32、涂布后放Cu、Al箔位,未经其他部门认可已更换,且Cu、Al箔多次撞伤及两边松紧度不同;33、涂布机内辊轮未经常擦洗,易有干料附在极片上;34、加料未经常搅拌浆料稀稠不同,极片附料不均匀;35、同一大片分切后6小片,极片左中右厚度不稳定且重量在上中下限都有;36、加料最后的浆料(有干料、较稠、结块)对所涂极片都有影响;37、停机卡在刀口处的印记应切除,辊压后易断裂(正极);38、涂布工艺上所给的公差较大,能否缩小;39、涂布工艺两边附料不同,如063048 –ve单:1·7±0·05g双:3·41±0·05g ;083048 +ve单:3·74±0·08g双:7·48±0·15g ;40、未涂完的单面,用保鲜纸包后露置于空气中;41、Cu、Al箔未用后,露置于空气中且边缘未包;42、试机时所用碎布擦Cu、Al上浆料,对极片附为都有较多影响,且极片中有气泡(浆料);43、停机时,前段80mm处置于空气中,极片上浆料变色,有气泡;44、裁切大片定位不整齐,极片四角偏斜,不成直角,且切口处有毛剌及掉粉,手按片不稳定;45、RD规定涂布报废片回收,但放置空气中过久,+ve起泡-ve掉粉;46、未用电子称测量大片重量,也未规定多少时间分切小片测重;47、牵引极片受力不均,导致附料不均,试片调机应保留,经确认后方可执行;48、牵引Cu、Al箔的过程中,辅助转轴较多,箔两边受力不均;49、正极单面前加多一辊轮,负极未有;50、塞尺划痕,露基体极片较多;51、收卷越大,速度加速,应减慢,否则不能干;52、接带断带后,手拉附料不均匀(拉太快);53、负极拉完转拉正极时,极片存放烘箱过长;54、涂布机的保养未有当事人的审核;55、涂布机的排风扇未有见过清洗;56、裁切大片(手动)无设备操作、工位作业指导书,且工作台面太脏,极片易有±ve极粉到极片上;57、未调好机就涂布,造成两面附料不均匀。
- 1、下载文档前请自行甄别文档内容的完整性,平台不提供额外的编辑、内容补充、找答案等附加服务。
- 2、"仅部分预览"的文档,不可在线预览部分如存在完整性等问题,可反馈申请退款(可完整预览的文档不适用该条件!)。
- 3、如文档侵犯您的权益,请联系客服反馈,我们会尽快为您处理(人工客服工作时间:9:00-18:30)。
干货锂电池极片挤压涂
布常见缺陷
WEIHUA system office room 【WEIHUA 16H-WEIHUA WEIHUA8Q8-
干货|锂电池极片挤压涂布常见缺陷目前,电动车、储能电池等新能源产业在全球范围内发展迅速。
作为公认的理想储能元件,动力锂电池也得到高度关注。
涂布机是动力锂电池极片的生产关键工艺设备。
目前,锂电池极片涂布工艺主要有刮刀式、辊涂转移式和狭缝挤压式等。
我在工作过程中,这三种涂布方式都接触过。
一般实验室设备采用刮刀式,3C电池采用辊涂转移式,而动力电池多采用狭缝挤压式。
刮刀涂布
工作原理如图1所示,箔基材经过涂布辊并直接与浆料料槽接触,过量的浆料涂在箔基材上,在基材通过涂辊与刮刀之间时,刮刀与基材之间的间隙决定了涂层厚度,同时将多余的浆料刮掉回流,并由此在基材表面形成一层均匀的涂层。
刮刀类型主要逗号刮刀。
逗号刮刀是涂布头中的关键部件之一,一般在圆辊表面沿母线加工成形似逗号的刃口,这种刮刀具有高的强度和硬度,易于控制涂布量和涂布精度,适用于高固含量和高黏度的浆料。
图1 逗号刮刀涂布示意图
辊涂转移式
涂辊转动带动浆料,通过逗号刮刀间隙来调节浆料转移量,并利用背辊和涂辊的转动将浆料转移到基材上,工艺过程如图2所示。
辊涂转移涂布包含两个基本过程:(1)涂布辊转动带动浆料通过计量辊间隙,形成一定厚度的浆料层;(2)一定厚度的浆料层通过方向相对的涂辊与背辊转动转移浆料到箔材上形成涂层。
图2 辊涂刮刀转移涂布工艺示意图
狭缝挤压涂布
作为一种精密的湿式涂布技术,如图3所示,工作原理为涂布液在一定压力一定流量下沿着涂布模具的缝隙挤压喷出而转移到基材上。
相比其它涂布方式,具有很多优点,如涂布速度快、精度高、湿厚均匀;涂布系统封闭,在涂布过程中能防止污染物进入,浆料利用率高、能够保持浆料性质稳定,可同时进行多层涂布。
并能适应不同浆料粘度和固含量范围,与转移式涂布工艺相比具有更强的适应性。
图3 狭缝挤出式涂布示意图
要形成稳定均匀的涂层,涂布过程中就需要同时满足这几个条件:(1)浆料性质稳定,不发生沉降,粘度、固含量等不变化。
(2)浆料上料供应稳定,在模头内部形成均匀稳定的流动状态。
(3)涂布工艺在涂布窗口范围内,在模头与涂辊之间形成稳定的流场。
(4)走箔稳定,不发生走带滑动,严重抖动和褶皱。
涂布操作窗口是狭缝涂布一个重要的工艺参数,在实际生产中,当工艺参数超出操作窗口的范围时,涂布缺陷便会产生。
而涂布膜出现的缺陷种类众多,原因各异,本文主要针对锂离子电池狭缝挤压涂布,就几种常见缺陷进行分析,并给出相应解决方案。
常见缺陷有点缺陷、边缘效应、锯齿缺陷等。
1 点状缺陷
气孔:一是气泡产生(搅拌过程、输运过程、涂布过程); 气泡产生的针孔缺陷比较容易理解,湿膜中的气泡从内层向膜表面迁移,在膜表面破裂形成针孔缺陷。
气泡主要来自搅拌、涂液输运以及涂布过程。
异物缩孔:各种颗粒(灰尘、油污、金属颗粒等) 产生。
外来颗粒的存在导致颗粒表面处的湿膜存在低表面张力区域,液膜向颗粒周围发射状迁移,形成缩孔点状缺陷,如图4所示。
预防措施主要有:涂液过滤除铁、环境粉尘控制、基材表面清洁。
图4 异物颗粒处表面张力低,涂液向四周迁移
团聚体颗粒凸起:如果浆料搅拌不均匀,导电剂没有分散开,形成团聚体时就会产生此类缺陷,如图5所示,极片表面出现大面积的凸起,放大这些地方观察,发现这是导电剂的团聚体。
这种缺陷主要还是改善浆料搅拌工艺来消除。
图5 团聚体颗粒凸起SEM形貌
2 线状缺陷
划痕:与涂布方向平行的线状薄区或漏箔线条,如图6所示。
图6 涂布极片划痕缺陷
可能原因
–异物或大颗粒卡在狭缝间隙内或涂布间隙上
–基材质量不佳,造成有异物挡在涂辊与背辊的涂布间隙上–模具模唇损伤
对策
–清除唇口或涂布间隙的颗粒、检查模头唇口
竖条道:与涂布方向平行的波纹,如图7所示。
图7 涂布极片竖条道缺陷
可能原因
–通常发生于接近涂布窗口的速度上限,薄涂层更明显。
对策
–调整浆料粘度
–降低涂布速度
–降低涂辊与背辊之间的涂布间隙
横向纹:垂直于涂布方向,固定间隔所产生的波纹或线条。
可能原因
–机械震动
–走带速度波动
–浆料供料的流动发生周期性波动
对策
–确认机械扰动频率与横纹发生频率是否相同
3 边缘效应
厚边:涂布过程,经常出现边缘厚,中间薄的现象,即厚边。
产生厚边的原因是表面张力驱动下的物质迁移。
如图8所示,开始时,湿膜的边缘处较薄,溶剂挥发速度较中间快,导致边缘固含量迅速升高,边缘的表面张力远大于中间湿膜的表面张力,边缘处较大的表面张力以及较快的溶剂挥发驱动内侧液体向边缘移动,烘干后形成厚边。
图8 干燥过程中厚边现象产生过程
涂布厚边现象是一种不利的缺陷,阻止和缓解厚边现象的措施有:
(1)浆料流量一定时,减小狭缝尺寸能够增加浆料在模头的出口速度,从而降低浆料的拖曳力比值,进而减小厚边涂层的厚度,但是狭缝尺寸变小模头内部的压力更大,更容易造成模头出口形状的膨胀,从而出现涂层横向厚度不均匀性,这需要更高精度的涂布设备配合。
(2)涂布间隙减小能够有限减小厚边涂层的厚度和宽度。
(3)降低浆料的表面张力,如添加界面活性剂等,抑制干燥过程中浆料向边缘的流延。
(4)优化狭缝垫片出口形状,改变浆料流动速度方向和大小,降低边缘浆料的应力状态,减弱浆料边缘膨胀效应。
参考文献:
[1]迟彩霞, 张双虎, 乔秀丽,等. 狭缝式涂布技术的研究进展[J]. 应用化工, 2016, 45(2):360-363.
[2]MohantyD, Hockaday E, Li J, et of electrode manufacturing defects onelectrochemical performance oflithium-ion batteries: Cognizance of the batteryfailure sources[J]. Journal of Power Sources. 2016, 312: 70-79.
[3]刘大佼. 狭缝式模具涂布技术及模具设计操作讲义.2015。