第五章 统计过程控制
统计质量管理第五章 统计过程控制(1)

❖ 这两天的变异原因消除后,失控点会从数据中消除。 ❖ 点的消除改变了过程的平均值和标准差。 ❖ 同时,中心线,上下控制限和各分区都会产生变化。
p15/428000.055
UCL(0p.)05350.0505.9450.123
100
LCL(0p.)0-5350.050.59450.0103.000
100
Number Cracked 的 P 控制图
0.14
0.12
+3SL=0.1234
0.10
+2SL=0.1006
比率
0.08
+1SL=0.0778
0.06
_ P=0.055
0.04 0.02 0.00
-1SL=0.0322
-2SL=0.0094 -3SL=0
❖ 如果一个过程的某个特征值是5%,拥有20个单位 的子组的平均计点数是1。而且每一个子组有一个 整数点,产出比例增加5%,那么中心线是0.05, 控制下限是0,控制上限是0.196。
❖ 子组的比例值只有四种情况(0,0.05,0.1,0.15) 是落在控制限以内。利用之前所述之方法寻找失 控点则是毫无意义的。
1
4
7
10
13 16 19 22 25 28
样本
❖ 通过改变过程,消除失控点,重新计算控制限和 区域界限,此时,最初判断为一般变异的点现在 可能会变成缺乏控制的状态。
❖ 这种现象发生时,需要再次进行评估,并消除变 异点。
❖ 但是,这种做法重复得多会产生两个问题,一是 数据库会因此萎缩,控制图的建立会基于越来越 少的子组,不能很好地描述原来的过程。
统计过程控制教学课件

选择正确的测量和数据收集方法, 如何处理因恶劣环境、人为误差 等控制图偏差问题。
在掌握基础统计方法的前提下, 熟练掌握结合分组、配对、方差 分析等方法的分析技巧。
控制图的构建及解读
在控制图上,展现数据波动趋势, 通过识别所处区域,进行及时的 调整。
统计过程控制的常见问题
1 控制图出现异常
掌握判断控制图中异常数据或规律变化的方法,选择正确的对策,重新调整控制图,以 保证其正确性。
未来发展方向
随着工业自动化的不断提升,数 据的获取和分析技术得到了进一 步的加强,统计过程控制在更广 泛范围内的实际应用将得以实现。
控制图的构建及解读
利用统计过程控制工具,制作了适当的 控制规程并建立了相关控制图,帮助改 进控制方案,明确了问题存在的时段和 难点。
结束语
应用前景
统计过程控制是一种基于数据分 析的反馈机制,在当今企业管理 和产品质量监控中扮演着重要的 角色。
重要性
实施统计过程控制将有助于挖掘 问题根本原因,推动质量改进和 成本优化,增强企业竞争力。
2 数据异常情况处理
其中包括控制图中的异常值排除,特殊因素分析确定及异常数据的原因分析和数据误差 的排除等实际问题。
3 连续改进中的难点
包括如何识别成本、如何判断业务重要性、是否需要专门的团队支持等。
案例分析
1
数据收集及处理过程
2
确定了准确的抽样方法,源数据的标准
化处理方案等,提取数千组数据,将它
统计过程控制教学课件 PPT
统计过程控制是一种有效的质量管理方法,通过监测和控制工业生产过程中 的变异性,实现质量稳定和连续改进。本课件旨在介绍统计过程控制的基本 概念、方法和实施过程,并通过案例分析深入探讨其实际应用。
现代质量工程第五章质量控制常用技术
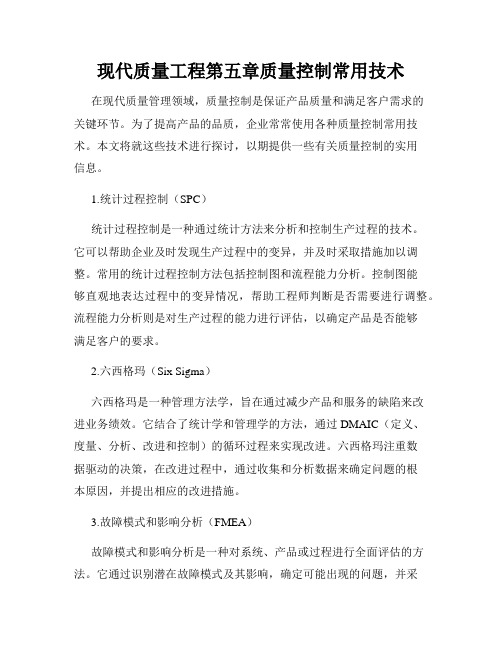
现代质量工程第五章质量控制常用技术在现代质量管理领域,质量控制是保证产品质量和满足客户需求的关键环节。
为了提高产品的品质,企业常常使用各种质量控制常用技术。
本文将就这些技术进行探讨,以期提供一些有关质量控制的实用信息。
1.统计过程控制(SPC)统计过程控制是一种通过统计方法来分析和控制生产过程的技术。
它可以帮助企业及时发现生产过程中的变异,并及时采取措施加以调整。
常用的统计过程控制方法包括控制图和流程能力分析。
控制图能够直观地表达过程中的变异情况,帮助工程师判断是否需要进行调整。
流程能力分析则是对生产过程的能力进行评估,以确定产品是否能够满足客户的要求。
2.六西格玛(Six Sigma)六西格玛是一种管理方法学,旨在通过减少产品和服务的缺陷来改进业务绩效。
它结合了统计学和管理学的方法,通过DMAIC(定义、度量、分析、改进和控制)的循环过程来实现改进。
六西格玛注重数据驱动的决策,在改进过程中,通过收集和分析数据来确定问题的根本原因,并提出相应的改进措施。
3.故障模式和影响分析(FMEA)故障模式和影响分析是一种对系统、产品或过程进行全面评估的方法。
它通过识别潜在故障模式及其影响,确定可能出现的问题,并采取相应的预防措施。
FMEA可以帮助企业在产品设计和生产过程中预先识别问题,并采取措施避免这些问题的发生。
它还可以提供有关故障影响的信息,有助于制定适当的修复和改进计划。
4.质量功能展开(QFD)质量功能展开是一种将客户需求转化为产品设计要求的方法。
它通过将客户需求与产品特性进行对应,构建质量指标,从而确保产品能够满足客户的期望。
QFD的核心思想是“从顾客出发,全员参与”,通过建立顾客需求转化矩阵,引导产品开发团队在设计过程中注重客户需求,提高产品的质量和竞争力。
5.品质管理工具除了以上几种常用技术,还有许多品质管理工具可以帮助企业进行质量控制。
例如,流程图能够帮助企业了解和分析工作流程,黄金样本提供了参考样本,使产品和服务的质量保持一致,直方图可以用于分析数据分布的情况,根本原因分析(RCA)可以帮助寻找问题的根本原因等。
统计过程控制(课件)
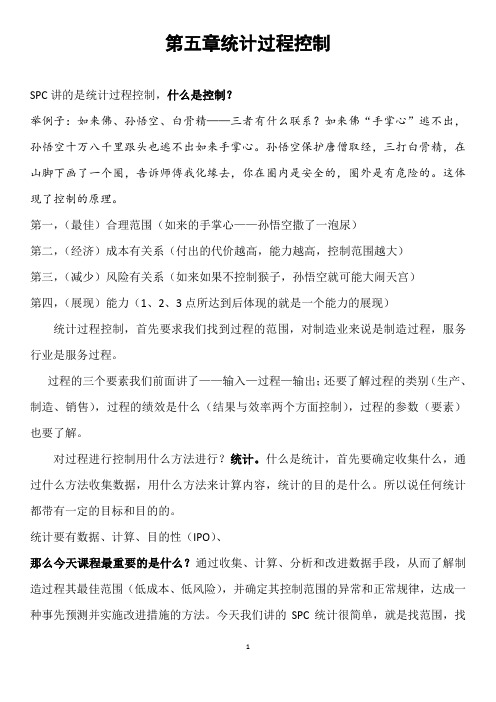
第五章统计过程控制SPC讲的是统计过程控制,什么是控制?举例子:如来佛、孙悟空、白骨精——三者有什么联系?如来佛“手掌心”逃不出,孙悟空十万八千里跟头也逃不出如来手掌心。
孙悟空保护唐僧取经,三打白骨精,在山脚下画了一个圈,告诉师傅我化缘去,你在圈内是安全的,圈外是有危险的。
这体现了控制的原理。
第一,(最佳)合理范围(如来的手掌心——孙悟空撒了一泡尿)第二,(经济)成本有关系(付出的代价越高,能力越高,控制范围越大)第三,(减少)风险有关系(如来如果不控制猴子,孙悟空就可能大闹天宫)第四,(展现)能力(1、2、3点所达到后体现的就是一个能力的展现)统计过程控制,首先要求我们找到过程的范围,对制造业来说是制造过程,服务行业是服务过程。
过程的三个要素我们前面讲了——输入—过程—输出;还要了解过程的类别(生产、制造、销售),过程的绩效是什么(结果与效率两个方面控制),过程的参数(要素)也要了解。
对过程进行控制用什么方法进行?统计。
什么是统计,首先要确定收集什么,通过什么方法收集数据,用什么方法来计算内容,统计的目的是什么。
所以说任何统计都带有一定的目标和目的的。
统计要有数据、计算、目的性(IPO)、那么今天课程最重要的是什么?通过收集、计算、分析和改进数据手段,从而了解制造过程其最佳范围(低成本、低风险),并确定其控制范围的异常和正常规律,达成一种事先预测并实施改进措施的方法。
今天我们讲的SPC统计很简单,就是找范围,找制造过程的某一个范围,通过这个范围的找到确定它的一种规律性,来达到事先的预测。
用一句话“事实胜于雄辩”用事实说话,第二,就是改进再提高,未来的展现和管理。
最基本的统计概念:总体(N):调查研究对象的全部样本(n):研究总体的情形或一种目的,从总体中抽取一部分的样本变异:变化的范围,在统一条件下这些统一动作都存在一种变动性。
使用方法一样,但是群体不同可能产生变异。
算数平均数和中位数。
极差,一组数中最大值减去最小值。
控制图作图方法
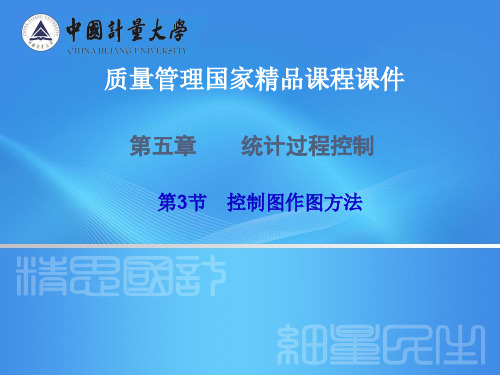
统 以上,计算试样的平均值x和标准偏差S
计 过
:
程
控
制
x x1 xn n
S x1 x2 xn x2
n 1
单值控制图(x控制图)
x 第 这时μ 和σ 值可由 和S近似得出,则:
五
章
统 计
CL= x UCL= x +3S
过 程
LCL= x -3S
控 制
求出CL、UCL、LCL后,就可以相应作出
统 UCL = np + 3√np(1- p) =2.6 +
计 过
3√2.6 (1 - 0.026) =7.4
程 控
LCL = np - 3√np(1- p) =2.6-
制
3√2.6(1- 0.026) = ( - ),无意义。
•
第 五 章
统 计 过 程 控 制
(二)不合格品率控制图(P控制图)
制
LCLX= X -A2R =3.861-0.729×1.028
=3.112
第
5)计算R图的参数
五 章
本例中n=4,查表,得D4=2.282,因n小于6,D3=0
统 ,所以下控制限可以不考虑,根据表5-4计算结
计 果如下:
过
程 控
CLR = R =1.028
制
UCLR = D4 R =2.282×1.028=2.346
3.861
程 控
样本平均极差 R 的计算公式为
制
R R1 R2 Ri Rk
R 25.7
K
25
1 K
K i1 Ri
1.028
4)计算 X 图的参数
第 五 章
本例中n=4,查表5-5得A2=0.729,根据表5-4计算 结果如下:
质量管理学 第五章 统计过程控制.doc

(1)计量值为双公差而且分布中心和标准中心重合的情况(如图5-1所示)。
图5-1
此时CP值的计算如下
σ可以用抽取样本的实测值计算出样本标准偏差S来估计。这时,
式中Tµ为质量标准上限,TL为质量标准下限。即T= Tµ-TL。
例5—1某零件的强度的屈服界限设计要求为4800—5200㎏/㎝2,从100个样品中测得样本标准偏差(S)为62㎏/㎝2,求过程能力指数。
(3)材料方面。如材料的成分,物理性能,化学性能处理方法,配套元器件的质量等。
(4)操作者方面。如操作人员的技术水平、熟练程度、质量意识、责任心等。
(5)环境方面。如生产现场的温度、湿度、噪音干扰、振动、照明、室内净化、现场污染程度等。
过程能力是上述5个方面因素的综合反映,但是在实际生产中,这5个因素对不同行业、不同企业、不同过程,及其对质量的影响程度有着明显的差别,起主要作用的因素称为主导因素。如对化工企业来说,一般设备、装置、工艺是主导因素。又如机械加工的铸造过程则主要因素一般是工艺过程和操作人员的技术水平,手工操作较多的冷加工、热处理及装配调试中的操作人员更为重要等等。这些因素对产品质量都起着主导作用,因而是主导性因素。
所以不合格品率为:
由以上公式可以看出,只要知道CP值就可求出该过程的不合格品率。
例5---6当CP=1时,求相应不合格品率P。
解:
例5---7当CP=0.9时,求相应不合格品率P。
解:
由不合格品率的公式及上两例可知,CP值增大时,不合格品率下降,反之,当CP值减小时,不合格品率增大。
2.当分布中心和标准中心不重合时的情况(
分布中心和标准中心不重合时的情况如图5-6所示
图5-6
过程能力分析

控
1 (3 1 0.6) (3 1.4)
制
1 (1.8) (4.2)
1 0.9641 0.00001335
0.03591335 即 P 3.59%
三、 过程能力分析
第 1、过程能力的判定
五 章
过程能力判定是根据过程能力
统
计
过 程
指数判断过程加工能力满足产品质
6
第 五
σ可以用抽取样本的实测值计算出样本标
章 准偏差S来估计。
统 这时, 计 过
CP
T 6S
程 控 制
TU TL 6S
式中TU为质量标准上限,TL为质量标准下限。 即T= TU-TL。
第
五
章
例:某零件的强度的屈服界限设计要求为4800—
统 5200㎏/㎝2,从100个样品中测得样本标准偏差(S)为
控
%
%
制
1.00
99.730 99.865% 99.865% %
99.865%
1.33
99.994% 99.997%
99.997%
1.67
99.99994% 99.99997%
2.00
99.9999998%
过程能力的判断标准
第 五 CP≥1.67 章
统 计 过
1.67> CP≥1.33
程 1.33>
制
(
T
2
)
(
T
2
)
(3C P ) (3C P )
1 2(3C P )
(四)过程不合格品率的计算
第 所以不合格品率为: 五 章
统 计
P 1 P(TL x TU )
SPC 统计过程控制 浙大版
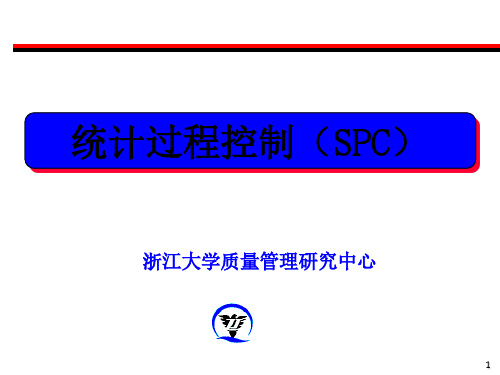
24
第三章 常规的休哈特控制图
数据 分布
控制图
简记
均值-极差 ……………..控制图 Χ一R 控制图
计量 值
正态 分布
均值-标准差 …………….控制图 中位数-极差……………. 控制图
X 一s ~X一R
控制图 控制图
单值-移动极差 ………….控制图 I一MR 控制图
计件 二项分 不合格品率 ……………..控制图 P
值
布
不合格品数 ……………..控制图 Pn
控制图 控制图
计点 泊松分 单位缺陷数 ……………..控制图 U
值
布
控制图
缺陷数 ………………….控制图 C
控制图
25
第四章 如何制作X-R控制图
还记得正态分布吗?
-3σ -2σ -1σ
1σ 2σ 3σ
21
第二章 SPC原理与作用
原理:1.普通原因导致的波动分布(稳态分布) 2.α=0.27% 小概率事件不会发生
3σ
A 2σ
B 1σ
C
C
-1σ
B
UCL= X+3σ组内
A
-2σ
CL=过程均值(X)
-3σ
LCL=X-3σ组内
22
第二章 SPC原理与作用
17
第一章 术语解释 普通原因和特殊原因
特殊原因(Assignable causes): 可避免原因、人为原 因、非机遇原因、异常原因、局部原因。
操作者未遵照操作标准而操作 虽然遵照操作标准,但操作标准不完善 机器设备的不正确调整 刀具的严重磨损 操作人员的更动 使用不合规格标准的原材料 量具不准确
- 1、下载文档前请自行甄别文档内容的完整性,平台不提供额外的编辑、内容补充、找答案等附加服务。
- 2、"仅部分预览"的文档,不可在线预览部分如存在完整性等问题,可反馈申请退款(可完整预览的文档不适用该条件!)。
- 3、如文档侵犯您的权益,请联系客服反馈,我们会尽快为您处理(人工客服工作时间:9:00-18:30)。
为:
Xi
X1
X2
X3 n
...
Xn
X i : 第i个子组的样本平均值 式中 X i : 第i个子组中的观测值
n :子组的大小
各子组样本的极差 R 的计算公式为 Ri max{ X i} min{ X i} 步骤三:计算所有样本总平均值和平均极差,总平均值的计算公式为
X
X1 X 2 X 3 ... X k k
X R
X S
X RS
中心线
X R
X S X RS
控制界限 UCL与LCL
X A2R D4R ,D3R
X A3S B3 S ,B4 S
X E2RS D4 RS,D3 RS
(1)X-R 控制图
[例5-1]:某制药厂片剂车间生产某种药品,以对颗粒水分的控制为例,绘制 X R
控制图。子组样本号 X1
控制图的分类
常规控制图
计量值控制图 计数值控制图
均值( X )与极差(R)控制图
均值( X )与标准差(S)控制图
单值( X)与移动极差(Rs)控制图 中位数( X~ )与极差(R)控制图
不合格品率(p)控制图 计件值控制图 不合格品率数(np)控制图
不合格数(c)控制图 计点值控制图 单位产品不合格数(u)控制图
0.0052 0.52%
20.59
LCLp p 3 p(1 p) / ni
LCLnp p 3 np(1 p)
0.00269 3 0.00269 (1 0.00269) / 4000 10.76 3 10.76 (1 0.00269)
0.0002 0.02%
0.93
子组号 检查的开关数n 不合格开关数np 不合格品百分数p
9
0.38%
9
单值X控制图的控制界限为:
CLX X 3.45% UCLX X E2RS 3.45% 2.66 0.38% 4.46% LCLX X E2RS 3.45% 2.66 0.38% 2.44%
移动极差Rs控制图的控制界限为:
CLRS RS 0.38% UCLRS D4RS 3.267 0.38% 1.24% LCLRS D3RS 0
1
16
3.9
3.7
3.2
4.8
3.9
1.6
17
4.4
4.3
4
3.7
4.1
0.7
18
3.6
3.2
3.6
4.4
3.7
1.2
19
3.2
4.4
4.2
4.5
4.075
1.3
20
4.7
4.6
3.8
3.2
4.075
1.5
21
4.8
4.2
4
3
4
1.8
22
4.5
3.5
3
4.8
3.95
23
3.8
3.2
4.2
3
3.55
控制图是判断生产过程是否处于统计控制状态的一种手段,利用它 可以判断过程是否存在异常。
1924年美国的休哈特(W. A. Shewhart)提出过程控制的概念与实 施过程监控的方法,并首先提出用控制图对生产过程质量进行监控。
控制图 ( CONTROL CHART ) 的形式
控制图:具有中心线 (central line, CL)、上控制限 (upper control limit, UCL) 和/或 下控制限 (lower control limit, LCL),某个统计指标的一系 列样本或子组的取值按照时间或样本号的顺序标在其上的图。
X2
X3
X4
Xi
Ri
1
3
4.2
3.5
3.8
3.625
1.2
2
4.3
4.1
3.7
3.9
4
0.6
3
4.2
3.6
3.2
3.4
3.6
1
4
3.9
4.3
4
3.6
3.95
0.7
5
4.4
3.4
3.8
3.9
3.875
1
6
3.7
4.7
4.3
3.6
4.075
1.1
7
3.8
3.9
4.3
4.5
4.125
0.7
8
4.4
4.3
3.8
0.35%
总计
100000
269
表5-7:开关的预备数据
p 控制图(使用MiniTab15) np控制图(使用MiniTab15)
四、控制图的观测分析
控制图的控制界限是根据正态分布原理计算的,根据 ±3σ原理,点子应随机排列,且落在控制限内的概率仅 为99.73%,因此控制图中点子未出界,且点子的排列也 是随机的,则可以认为生产过程处于稳定状态或控制状 态。如果控制图点子出界或界内点排列非随机,就认为 生产过程失控。 由此得出控制图的两类判异准则 1. 点出界就判异; 2. 界内点排列不随机判异。
2.样本量n的大小
当3σ控制区域一定时,样本量n增大, α和β减小,控制图的检出力增大。
三、控制图的应用程序和作图方法
(一)合理选择应用控制图的场合 (二)选择控制对象 (三)选择控制图 (四)合理子组 (五)绘制分析用控制图 (六)确定控制标准 (七)控制图的管理
1、计量值控制图的作图方法:
控制图
1 k
k i 1
Xi
式中 X —— 所有观测值的总平均值
K —— 子组的个数
R
R1 R2 R3 ... Rk k
1 k
k
Ri
i 1
步骤四:计算控制图的参数 本例中 n=4 ,查表 5-3 得 A2=0.729 ,D4=2.282 ,D3=0 ,根据控制限表 5-2 计算控制图参数。
X 图的控制界限:
1
4000
8
0.20%
2
4000
14
0.35%
3
4000
10
0.25%
4
4000
4
0.10%
5
4000
13
0.33%
6
4000
9
0.23%
7
4000
7
0.18%
8
4000
11
0.28%
9
4000
15
0.38%
10
4000
13
0.33%
11
4000
5
0.13%
12
4000
14
0.35%
13
4000
12
能有效地分析判断生产过程质量的稳定性,从而降 低检验、测试费用。
可查明设备和工艺手段的实际精度,以便作出正确 的技术决定,为真正地制定生产目标和规格界限, 特别是配合零部件的最优化确立了可靠的基础,也 为改变未能符合经济性的规格标准提供了依据。
使生产成本和质量成为可预测的参数,并能以较快 的速度和准确性测量出系统误差的影响程度,从而 使同一生产批内的产品之间的质量差别减至最小, 提高产品质量和经济效益。
步骤五:画控制图(使用MiniTab15)
(2)单值(X)与移动极差(Rs)控制图
[例5-2]:表5-5给出了连续10 批脱脂奶粉的样本“水分含量百分比”的实验结X 果R。 将一个样本的奶粉作为一个批的代表,希望将该过程的产品水分含量控制在4%以 下,利用单值控制图对过程进行监控。
表5-5:连续10个脱脂奶粉样本的水分含量百分比
二、控制图的统计原理
(一)3σ原理
如果质量特性值服从正态分布,即XX~N~ (N (μ,,σ22))。当生
产过程中仅有偶然性原因存在时,则从过程中测得的产品质 量特性值 X有99.73%在μ+ 3σ的范围内,也可以理解为如果 抽取少数产品测得的质量特性值应均落在μ+ 3σ范围内,如 果有特性值落在+ 3σ的界限外,可以认为过程出现系统性原 因时,X的分布发生了偏离。这就是休哈特控制图的3σ原理。
第五章 统计过程控制的原理和方法
本章内容要点 控制图的分类和统计原理 控制图的作图程序和方法 控制图的分析 过程能力、过程能力指数的意义和计算 不合格品率的计算方法 过程能力指数的分析 过程性能指数的概述
第一节 控制图的基本原理
一、控制图概述
SPC(Statistical Process Control)即统计过程控制是应用统计技术 对生产过程的各阶段进行监控,并对过程出现的异常进行预警,从 而达到改进与保证质量的目的。其中控制图理论是SPC保证全过程 预防的最常用统计技术。
UCL
样
本
统
计
CL
量
数
值
LCL
时间或样本号
控制图的解释
Control charts are run charts with superimposed normal distributions.
Copyright 2009 Wen-Hui, Zhou
控制图的作用
能及时发现生产过程中的异常现象和缓慢变异,预 防不合格品发生,从而降低生产费用,提高生产效 率。
0.30%
14
4000
8
0.20%
15
4000
15
0.38%
16
4000
11
0.28%
17
4000
9
0.23%
18
4000
18
0.45%
19
4000
6
0.15%
20
4000
12
0.30%