液压缸结构设计的有限元分析方法
液压缸的有限元分析

城南学院液压缸有限元分析CHANGSHA UNIVERSITY OF SCIENCE &TECHNOLOGY毕业设计(论文)题目:液压缸的有限元分析学生姓名:学号:班级: 工程机械专业:机械设计制造及其自动化指导教师:2012 年6 月液压缸的有限元分析FINITE ELEMENT ANALYSIS OF HYDRAULIC CYLINDER学生姓名:学号:班级:工程机械所在院(系): 汽车与机械工程学院指导教师:完成日期: 2012年6月7日摘要液压缸是液压机的关键部件, 其设计质量的好坏直接影响主机的工作性能和使用寿命。
如果设计不当,过早失效将造成较大的经济损失。
因此采用现代设计方法对液压缸进行结构设计, 对提高使用寿命, 增加经济效益具有重要意义。
本文首先对液压缸的各零部件进行了设计及验算。
然后采用UG软件建立了动臂液压缸的几何模型,通过与Workbench的接口输入到该有限元分析软件里,建立了相应的有限元分析模型。
最后通过该软件对液压缸模型进行了线性静力分析和模态分析,获得了液压缸的振动特性和力学性能,这对液压缸的改进设计和预评液压缸的危险部位具有参考意义。
关键词:液压缸;UG;ANSYS;有限元分析FINITE ELEMENT ANALYSIS OF HYDRAULICCYLINDERAbstractSurface hydraulic bar hydraulic machine is the earliest use of hydraulic components. Nothing seems to change, in fact, the hydraulic cylinder has been great development. This is not only in the hydraulic cylinder work performance, work out of range expansion, varieties of different specifications of the increase and the improvement of the structure, but also in the study of hydraulic cylinder is gradually deepening, design, calculation theory is gradually perfect.In this paper, the hydraulic cylinder parts of the design and checking calculation. Then using UG software to establish a boom cylinder geometry model, through the Workbench interface with input to the finite element analysis software, established the corresponding finite element analysis model. Finally, the software of the hydraulic cylinder model for linear static analysis and modal analysis, obtained the vibration characteristics of hydraulic cylinder and mechanical properties, the improvement design of hydraulic cylinder hydraulic cylinder and assessment risk part has the reference significance.KEY WORDS: HYDRAULIC CYLINDER ;UG;ANSYS;FINITE ELEMENT ANALYSIS目录第一章-绪论 (1)1.1前言 (1)1.2液压缸的分类 (1)活塞式 (1)伸缩式 (2)摆动式 (2)1.3论文的主要内容 (2)1.4 论文的主要组成 (2)第二章-各零部件的设计及验算 (3)2.1 设计提要 (3)2.2 各零部件的设计及验算 (4)2.2.1-缸筒设计 (4)2.2.2-法兰设计 (12)2.2.3 活塞设计 (15)2.2.4 活塞杆的设计 (16)第三章 -动臂液压缸有限元分析 (20)3.1 液压缸三维模型的建立 (20)3.2 有限元分析的基本理论 (20)3.2.1有限元法的发展概况 (21)3.2.2 有限元分析的基本思想 (22)3.2.3有限元法分析过程 (24)3.2.4 ANSYS软件介绍 (25)3.2.5 有限元分析的发展发展趋势 (26)3.3 模态分析 (28)3.4 静力分析 (32)3.5 结果总结与分析 (33)参考文献 (34)致谢 (36)第一章-绪论1.1前言液压缸是将液压能转变为机械能的、做直线往复运动(或摆动运动)的液压执行元件。
HSG型工程液压缸基于ANSYS的有限元分析

文章编号:(编辑给出)HSG型工程液压缸基于ANSYS的有限元分析张士营1张文辉1,2(1.丽水学院工学院,浙江丽水 323000;2. 哈尔滨工业大学航天学院,黑龙江哈尔滨 150001)摘要:HSG型液压缸在工程机械等领域有着广泛用途,当前还缺乏系统的有限元分析方法。
首先针对HSG型液压缸系统分别从力位移、全局应力及局部应力进行了静力计算;进而对液压缸的主要轴向载荷承受部件活塞杆进行了纵向弯曲强度的校核,分析构件稳定性;最后对液压缸系统进行模态分析,通过系统固有频率的计算能够有效避免共振危害的发生。
所提方法与分析结果对于HSG型液压缸研发具有重要借鉴价值。
关键字:有限元;液压缸;静力分析;屈曲分析;模态分析中图分类号:TH11 文献标识码:AFinite Element Analysis for HSG Hydraulic Cylinder Systembased on ANSYSZhang Shiying 1Zhang Wenhui1,2(1.Institute of Technology, Lishui University, Lishui 323000;2.School of Aerospace ,Harbin Institute of Technology,Harbin 150001;Abstract:HSG type hydraulic cylinder has widely used in engineering machinery and other fields, the system finite element analysis method is still lack in current. First system the global static calculation are done respectively for the force displacement, stress and local stress on HSG type hydraulic cylinder;And then strength check is done for the main axial load components under the piston rod of the buckling, stability analysis of components is done; The modal analysis is carried out on the hydraulic cylinder system, through calculating natural frequency of the system can effectively prevent the occurrence of resonance hazard. The proposed method and the analysis results have important reference value for research and development of HSG type hydraulic cylinder.Key words:Finite element; Hydraulic cylinder; Static analysis; Buckling analysis; Modal analysis收稿日期:2014年05月--日;修订日期:2014年--月--日基金项目:国家自然科学基金项目(61171189),国家科技支撑计划项目(2013BAC16B02),浙江省自然科学基金项目(LY14F030005),浙江省公益收稿日期:2014年05月--日;修订日期:2014年--月--日基金项目:国家自然科学基金项目(61171189),国家科技支撑计划项目(2013BAC16B02),浙江省自然科学基金项目(LY14F030005),浙江省公益1 引言液压缸是一种将液压能转变为机械能的、做直线往复运动(或摆动运动)的液压元件,具有结构简单,工作可靠的特性,能够在实现往复运动时无需减速装置,没有传动间隙,且运动平稳的优点,在能源、机械等各工业领域及日常设备中有着广泛用途,由于液压缸的刚度、强度、稳定性及振动特性等因素将直接影响到液压缸的使用寿命和工作性能,因此对其进行深入研究具有重要意义[1]-[2]。
《2024年液压机机身有限元分析与优化》范文

《液压机机身有限元分析与优化》篇一一、引言随着工业制造的飞速发展,液压机在生产领域扮演着重要的角色。
作为液压机的核心组成部分,机身结构的稳定性和性能对整机的工作效率、使用寿命以及产品精度具有重要影响。
因此,对液压机机身进行有限元分析和优化设计,不仅有助于提高其工作性能,还能为生产过程中的安全性和效率提供保障。
本文旨在通过有限元分析方法,对液压机机身进行深入研究,并探讨其优化策略。
二、液压机机身有限元分析1. 模型建立首先,根据液压机机身的几何尺寸和材料属性,建立三维实体模型。
在模型中,需考虑机身的结构特点、材料属性以及可能的约束条件。
同时,为提高分析的准确性,需对模型进行网格划分,确保网格的密度和分布符合分析要求。
2. 加载与约束在有限元分析中,加载和约束的设置对于分析结果的准确性至关重要。
根据液压机机身的实际工作情况,设置合适的载荷和约束条件。
其中,载荷包括重力、工作压力等,约束条件则需考虑机身的固定方式和支撑条件。
3. 求解与分析利用有限元分析软件,对加载后的模型进行求解。
通过求解,可以得到机身的应力分布、位移变化以及振动模态等数据。
对这些数据进行深入分析,可以了解机身在不同工况下的工作性能和潜在问题。
三、液压机机身优化设计1. 问题识别通过有限元分析,可以发现机身结构中存在的问题和潜在风险。
例如,机身局部应力过大、振动模态不合理等。
这些问题会影响机身的工作性能和寿命,需要进一步优化。
2. 优化方案制定针对发现的问题,制定相应的优化方案。
优化方案包括改进结构、调整材料、优化工艺等。
在制定方案时,需充分考虑机身的工作环境、性能要求以及成本等因素。
3. 优化实施与验证将优化方案应用到机身结构中,重新进行有限元分析和实验验证。
通过对比优化前后的数据,评估优化效果。
若优化效果显著,则说明优化方案可行;若效果不明显或出现问题,则需进一步调整优化方案。
四、结论与展望通过有限元分析和优化设计,可以提高液压机机身的工作性能和寿命,为生产过程中的安全性和效率提供保障。
挡轮液压缸的改进设计及其有限元分析
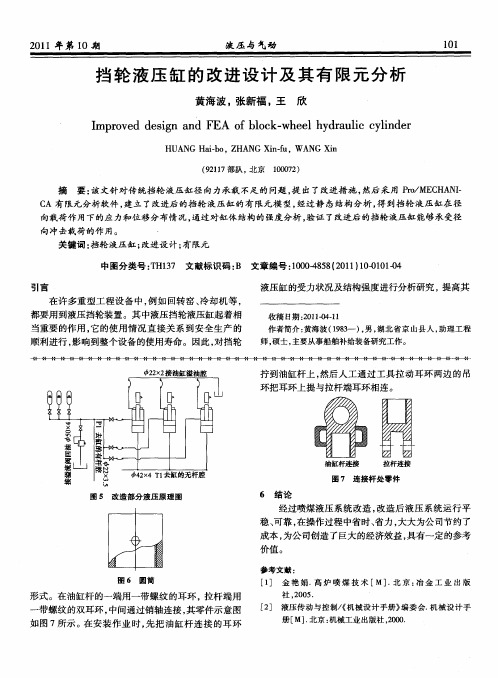
重、 易拉缸以及缸端盖处有外泄等n 。传统挡轮液压 ]
缸 基本 上不 能承受 径 向力 , 是上述 问题 存在 的根 源 , 因 此, 本文 对其 结构 凹槽 为参 考 点 , 独 对 右 边 滑 动活 塞 杆 组 单 件进 行力矩 分 析 :
一
由方程 ( ) ( ) ( ) 解得 : 6 、7 和 8 联 t一 一 Fs i n i n () 9 ( 0 1)
,= L 二
n
() 1 1
步减小 活 塞杆 与端 盖 上导 向套 之 间的 相 互作 用 力 , 如果 图 1 的导 向套磨损 或 者 图 1 a中 b中的辅 助支
F 3=F C S O F s =F l+F 2+F 4 i n
力矩 分析 :
() 5 () 6
实践表明, 传统结构形式的液压缸使用效果不佳 ,
所存 在 的主要 问题 是 密封失 效 、 内泄 大 、 向套磨 损严 导
以球 套 凹槽 为 参考 点 , 独 对 左 边 活 塞组 件 进 行 单
如 图 7所示 。在 安装 作 业 时 , 把 油 缸 杆 连 接 的 耳 环 先
12 0
液 压 与 气动
21 0 第 1 1年 0期
使 用性 能 , 无论 是 从 经 济 角 度 , 是 从 安 全 角 度 来 考 还 虑, 有着 极其 重要 的意 义 。
图 1 示活塞及活塞 杆 的整体受 力平衡方程 式为 b所
21 0 第 1 1年 0期
液 压 与 气动
11 0
挡 轮 液压 缸 的改进 设 计 及 其 有 限元分 析
黄海波 ,张新福 ,王 欣
盾构推进液压缸刚度有限元分析

要 由球铰 、活塞 杆和 缸体 组成 。
其 中 :k为 液压缸 的刚度 ; 为球铰 的刚度 。
在 液压 驱动机 构 静力 学分 析 中,一 般认 为液 压油 是 刚性的 、不可 压缩 的 ,只考 虑杆件 的变形 。液 压油
2 液压 缸的有 限元分 析 选 择 分 析类 型为 静 力 学 ,左 边 球 铰 端 面 固 定 约 束 ,为 了便 于分 析对 比 ,给右边 球铰端 面 施加相 当 于 3 0 ×1e N的应力载荷 。设定求解载荷步 结束 时间为 l S , 为 了减 少计 算 时间 , 定子 步数 为 1 ,N Y 设 2 A S S求解 液 压
18 .
24 .
3O .
变 形
m m
0
.
2l 5
044 .0
0. 4 50
06 . 5l
075 . 5
l 液压缸 的刚度计算模型
1 1 球铰 的刚度 模型 .
刚 度
Nm /m
25 00 0 7 0 3 3 0 36 7 0 39 30 0 9 0 29 00 0 30 0 8 0 3 0 7 0
缸 的轴 向位移 云 图和应 力 云图分别 见 图 5 图 6 和 。
的 体积 模 量 K=. P  ̄2 Ga 14 Ga P ,而钢 的体 积模 量 为
1 6 G a - 0 P ,是 液 压油 的 1 0倍 ~ 10倍 。在 9 P  ̄ 2 6 G a , 0 5
实 际推进 过程 中 ,液 压油 的压 缩量 会对 计算 结果 造成
盾构推进 液压缸 刚度 有 限元分析
袁 永 盛
( 华东交通 大学 机 电工程 学院 ,江西 南 昌 3 0 1 ) 3 03
基于有限元分析的液压缸支架结构优化设计

无法充分利用材料的许用应力,增加成本,也使支架整体质量
偏大。
128
Sheji yu Fenxi◆设计与分析
说明,如图6所示。为简化计算,将底板和底座之间作用力等效 为 施 加 于 各 螺 栓 中 心 的 集 中 力 ,螺 栓 和 底 座 变 形 分 别 以 ObA 和OmA 表示。
(a)传统结构
(b)优化后结构
实际工况下受力情况[8]。对设备施加500 kN载荷,液压缸与支
架为销轴连接,支架销轴孔受500 kN水平压力。通过螺栓组将
底板和侧液压缸支架固连,底板为固定约束,支架载荷约束模
型如图3所示。
(a)传统结构
(b)优化后结构
图1 支架的三维模型
液压缸支架由Q235-A焊接构成,在有限元分析软件中设
定材料属性[4],如表1所示。
(a)传统结构
(b)优化后结构
1.2 受力分析
图3 支架的载荷约束模型
传统形式与优化后形式支架受载后变形均为自上而下减
小 ,顶 部 由 于 受 力 集 中 ,变 形 量 最 大 ,两 种形 式 最 大 变 形 量 分
别为0.58 mm及0.82 mm。支架等效应力云图如图4所示。
传 统 支 架 最 大 等 效 应 力 位 于 销 轴 孔 - 螺 栓 连 接 处 ,为
(a)连接形式及力矩
(b)施加倾覆力矩前
(c)施加倾覆力矩后
图5 支架底板受力分析
上述过程可通过单个螺栓-底座的受力和变形情况进行
图6 单个螺栓-地基受力变形 在未施加M之前底座、螺栓工作点均为A 点,支架底板合 力为0;施加M后,轴线右侧螺栓工作点移至B2点,底座工作点 移至 C2点 ,底 板 上 两 者 合 力 与 载 荷 Fm相 等 ,方 向 向 上 ;在 轴 线 左 侧 ,螺 栓 工 作 点 移 至 B1点 ,底 座 工 作 点 移 至 C1点 ,底 板 上 两 者合力为螺栓工作载荷F,方向向下,载荷F与Fm大小相同。倾 覆力矩等于作用于两侧底板合力矩,即:
卡键式多级缸有限元分析报告

1.2328e+006 Minimum
Pa
89670 Pa
8048.7 Pa
20602 Pa
35638 Pa
2.1627e+008 5.7476e+007 9.8383e+007 7.8704e+007 1.373e+008
Maximum
Pa
Pa
Pa
Pa
Pa
Model (A4) > Static Structural (A5) > Solution (A6) > Results
图 13 卡键应力(WKJ197-NKJ226)
三、 应力计算结果
注下图中 E+0.06=1MPa
Model (A4) > Static Structural (A5) > Solution (A6) > Results
Object 应力-GT-117 应力-GT-135 应力-GT-154 应力-GT-175 应力-GT-197
1 / 10
卡键式多级缸结构分析报告
一、 有限元计算模型: 1.1 有限元模型
模型以实体单元 SOLID 建立; 约束条件:(模拟 25MPa 试验台状态)外缸筒吊耳固定约束;末级缸头固定约束。 加载载荷:25MPa 内压力; 重力加速度 9.85m/s2。
1.2 模型特性
图 1 模型建立
图 2 加载示意图
单作用多级套筒 液压缸
有限元分析 报告
2020.3
卡键式多级缸结构分析报告
目录 一、 有限元计算模型:.............................................................................................................2
液压缸系统基于ANSYS的有限元应力分析

Vo 1 . 4 2 No . 4
河 南 科 技 学 院 学 报 J o u r n a l o f He n a n I n s t i t u t e o f S c i e n c e a n d T e c h n o l o g y
c a l c u l a t i o n , t h e s t r e s s d i s t r i b u t i o n o f g l o b a l a n d l o c a l s t r e s s d i s t r i b u t i o n w e r e c a l c u l a t e d t o p r o v i d e a n i mp o r t a n t r e f e r e n c e f o r p r o d u c t d e v e l o p me n t a n d a n a l y s i s , T h e p r o p o s e d i f n i t e e l e me n t a n a l y s i s me t h o d s b a s e d o n t h e ANS YS h a v e i mp o r t a n t e n g i n e e r i n g v a l u e s or f t h e h y d r a u l i c c y l i n d e r s y s t e m r e s e a r c h .
关键 词 : 液压缸; 有限元 ; 静力分析; 应变分析
中图分 类 号 : T H 1 1
文献标 志 码 : A
文章 编号 : 1 0 0 8 — 7 5 1 6 ( 2 0 1 4 ) 0 4 — 0 0 6 7 — 0 3
- 1、下载文档前请自行甄别文档内容的完整性,平台不提供额外的编辑、内容补充、找答案等附加服务。
- 2、"仅部分预览"的文档,不可在线预览部分如存在完整性等问题,可反馈申请退款(可完整预览的文档不适用该条件!)。
- 3、如文档侵犯您的权益,请联系客服反馈,我们会尽快为您处理(人工客服工作时间:9:00-18:30)。
力值为 232.09MPA。
在 R5=0 的情况下,令 R6 取 8~20mm,每隔 2mm 取一个值,计算整理最大应力值如表
1 所示。
R6/mm
8
10
12
14
16
18
20
最大等效应力/MPa 223.37
234.73
189.98 199.22 177.99 187
那里一般是应力集中点,需要着重关注。图 2 显示网格划分情况,图 3 与图 4 显示两个倒角 处的网格划分情况。
图 2 整体划分
图 3 倒角 R5 划分
图 4 倒角 R6 划分
约束定义:
约束主要体现的是结构体与外界的相互关系,在本次仿真实验中,液压缸主要与固定横
梁接触,假定固定横梁是刚体,则与其接触的面上的垂直方向上位移为 0。因此约束条件为:
(1)
模型建立:
首先注意到这是一个个弹性力学轴对称问题,几何形状、外载荷与约束条件都是关于液 压缸的中心轴对称,因而在建立几何模型时,可以选取通过中心轴的纵截面的二分之一作为 计算模型,如图 1 所示。
图 1 液压缸计算模型
网格划分:
网格划分时,网格密度与采取的单元模型都会对计算精度产生影响,网格过于稀疏则明 显不能给出准确计算结果,但过于密集则在圆角处计算应力时会出现应力计算值过大的现 象。这里我们采用四边形单元,使用 face mapping 划分方式以尽量使划分出的网格规则而 均匀,同时我们需要注意保持一定的网格密度,而且需要在倒角处适当增大网格密度,因为
191.74
179.87 186.5
表 2 R6=20 时最大等效应力与 R5 的关系表
将上述结果整理成曲线图,如图 11 所示。
184.3 172.85 170.54
最大等效应力/MPA
最大等效应力/Mpa
208.07
210
206
202
198
191.74
194 190
186.5 184.3
186
表 1 R5=0 时最大等效应力与 R6 的关系表
将上述结果整理成曲线图,如图 10 所示。
172.7
最大等效应力/MPA
最大等效应力/Mpa
242
236 230
234.73
224 218
223.37
212
206
200 194 188 182 176 170
199.22
189.98
187
177.99
在计算模型中最右侧的竖直方向上边的 X 方向的位移为 0;在模型中与横梁水平面接触的边
上的 Y 方向的位移也为 0。
载荷定义:
液压缸主要受到来自高压液体产生的压力,本次仿真中需要 load 两项压力,一项垂直
作用于模型最上方部分内侧边,大小为 20MPa;另一项项垂直作用于模型最左边的边上,但
注意到这是一个分段函数,所以需要将这条边分成两部分,一部分的压力大小为常数 20MPa,
图 12 过渡圆角优化后极限工作压力下应力分布图
此时的最大应力为 194.418=350÷ 1.8,满足要求,故优化过渡圆角半径后极限工作压力 为 22.8MPa。
另一部分的压力大小用 y(mm)/25Mpa 来计算。载荷分布如图 5 所示。
图 5 载荷分布
计算结果:
将计算结果导入 APDL 进行分析,得到液压缸的变形情况及应力分布情况(计算等效应 力)如图 6、图 7 所示。
图 6 位移分布
图 7 等效应力分布
可以得到液压缸内的最大应力为 217.81MPa。因为材料的屈服强度为 350MPa,安全系数
值,圆角部分应适度疏密,而适度疏密也没有具体的数值标准,一般看圆弧部分在划分网格
后还是比较光滑的圆弧便可。
所以为了选择最合适的参数,我们可以先确定 R6 取为 20mm,此时令 R5 取 8~20mm,
每隔 2mm 取一个值,计算整理最大应力值如表 2 所示。
R5/mm
8
10
12
14
16
18
20
最大等效应力/MPa 208.07
2)基于有限元分析,在保持液压缸内半径 R1、长度 h1 和密封长度 h2 等主要结构尺寸 不变的前提下,过渡圆角半径 R5 和 R6 可以在 8-20mm 之间变动,分析过渡圆角半径选择对 液压缸受力状态和变形的影响。
3)根据计算结果选择过渡圆角半径,优化过渡圆角半径后液压缸与过渡圆角优化
根据结构尺寸和材料参数建立液压缸工作状态的有限元分析模型,完成液压缸的应力和 变形分析并写出分析报告。
1)根据图 3 建立液压缸的有限元模型,简要说明建模的思路。假定工作压力为 20MPa, 分析液压缸的受力和变形情况,分析单元网格划分方案对计算结果的影响。在 20MPa 工作 压力下,该液压缸的强度是否满足要求?在液压缸的哪个部位出现应力集中?
179.87
182
178 174
172.85 170.54
170
8
10
12
14
16
18
20
R5半径/MM
图 11 最大等效应力与 R5 的关系曲线
其仿真计算结果与 R6 的结果一致。
结论:
根据计算结果我们可以看出随着过渡圆角半径的增大,应力集中现象被削弱;而且也可 以看出过渡圆角半径对于液压缸变形的影响很小,几乎没有(因此应变分布图不需要、也没 有在报告中体现),这与之前的分析也是吻合的,在报告中不需要进行数据分析。
172.7
8
10
12
14
16
18
20
R6半径/MM
图 10 最大等效应力与 R6 的关系曲线
可以看出,总体趋势是随着过渡圆角的增大,最大等效应力的值减小,这与过渡圆角的
作用是相一致的,至于中间出现的偏离趋势线的数据与 R6 倒角处受力和约束情况复杂有关,
还与 ansys 计算误差有关,主要影响因素是网格的划分密度,不同的划分密度会得到不同的
(3)
根据计算结果选择过渡圆角为 R5=R6=20mm,在工作压力为 20MPa 时的最大应力为 170.54MPa,而材料的屈服强度为 350MPa,安全系数为 1.8,所以极限工作压力大小350⁄1.8 ÷ 170.54 × 20 = 22.8������������������。
重新定义载荷条件进行仿真验证,结果如图 12 所示。
为 1.8,因为350⁄1.8 = 194.44 < 217.81,所以液压缸的强度不满足要求。 分析液压缸的应力分布图,可以看出在两个倒角处出现了应力集中现象,其应力分布图
如图 8 与图 9 所示。
图 8 倒角 R5 处应力集中现象
图 9 倒角 R6 处应力集中现象
(2)
过渡圆角半径 R5 和 R6 可以在 8-20mm 之间变动,且注意到过渡圆角起到用于改善应 力分布的作用,对于整体结构的变性的影响不大,而且 R5 与 R6 两个圆角所处的位置相隔 较远,从应力分布图中可以看出两个区域是互不影响的。所以,在保持主要结构尺寸不变的 情况下,我们可以分别考虑两个倒角半径对最大应力值的影响。