拉伸试验国家标准ppt.共38页
合集下载
金属材料拉伸试验方法PPT学习教案

计标距Le百分率时对应的应力。
第11页/共61页
断裂:当试样发生完全分离时的现象。 4.符号和说明(略)。 5.原理:试验系用拉力拉伸试样,一般拉至断裂,测定第3章定义的一项或几
项力学性能。 除非另有规定,试验一般在室温10℃-35℃范围内进行。对温度要求严格
的试验,试验温度应为23℃±5℃。
第12页/共61页
10.4.2测定屈服强度和规定强度的试验速率
10.4.2.1上屈服强度ReH
在弹性范围和直至上屈服强度,试验机夹 头的分离速率应尽可能保持恒定并在表3规定 的应力速率范围内。
注:弹性模量小于150 000MPa的典型材料包括锰、铝合金、 铜和钛。弹性模量大于150 000MPa的典型材料包括铁、钢、
如果拉伸试验仅仅是为了测定抗拉强度, 根据范围3或范围4第得29页到/共6的1页平行长度估计的应
10.4应力速率控制的试验速率(方法B)
10.4.1总则
试验速率取决于材料特性并应符合下列要求。 如果没有其他规定,在应力达到规定屈服强 度的一半之前,可以采用任意的试验速率。 超过这点以后的试验速率应满足下述规定。
金属材料拉伸试验方法
平行长度Lc:试样平行缩减部分的长度(对于未加工试样为两夹头间的距离) 伸长:试验期间任意时刻原始标距的增量。 伸长率:原始标距的伸长与原始标距之比的百分率。
残余伸长率:卸除指定应力后,伸长相对与原始标距L0的百分率。
断后伸长率A:断后标距的残余伸长(Lu-L0)与原始标距L0之比的百分率。
在屈服强度或塑性延伸强度测定后,根 据试样平行长度估计的应变速率eLc应转换 成下述规定范围之一的应变速率(见图9):
—范围2: eLc=0.000 25 S-1,相对误差 ±20%。
第11页/共61页
断裂:当试样发生完全分离时的现象。 4.符号和说明(略)。 5.原理:试验系用拉力拉伸试样,一般拉至断裂,测定第3章定义的一项或几
项力学性能。 除非另有规定,试验一般在室温10℃-35℃范围内进行。对温度要求严格
的试验,试验温度应为23℃±5℃。
第12页/共61页
10.4.2测定屈服强度和规定强度的试验速率
10.4.2.1上屈服强度ReH
在弹性范围和直至上屈服强度,试验机夹 头的分离速率应尽可能保持恒定并在表3规定 的应力速率范围内。
注:弹性模量小于150 000MPa的典型材料包括锰、铝合金、 铜和钛。弹性模量大于150 000MPa的典型材料包括铁、钢、
如果拉伸试验仅仅是为了测定抗拉强度, 根据范围3或范围4第得29页到/共6的1页平行长度估计的应
10.4应力速率控制的试验速率(方法B)
10.4.1总则
试验速率取决于材料特性并应符合下列要求。 如果没有其他规定,在应力达到规定屈服强 度的一半之前,可以采用任意的试验速率。 超过这点以后的试验速率应满足下述规定。
金属材料拉伸试验方法
平行长度Lc:试样平行缩减部分的长度(对于未加工试样为两夹头间的距离) 伸长:试验期间任意时刻原始标距的增量。 伸长率:原始标距的伸长与原始标距之比的百分率。
残余伸长率:卸除指定应力后,伸长相对与原始标距L0的百分率。
断后伸长率A:断后标距的残余伸长(Lu-L0)与原始标距L0之比的百分率。
在屈服强度或塑性延伸强度测定后,根 据试样平行长度估计的应变速率eLc应转换 成下述规定范围之一的应变速率(见图9):
—范围2: eLc=0.000 25 S-1,相对误差 ±20%。
金属拉伸试验标准对试验速度的ppt

• 对于位移控制的试验机,可用下式将应力速率转换 成位移速率:
1 L Lc E
L
C
• 例如,弹性模量E=200000N/mm2的钢试样平行长度LC =60mm,与应力速率30N/mm2· s-1对应的位移速率为:
L =1/200000×60×30×60=0.54mm/min
b)测定下屈服强度ReL的试验速率ຫໍສະໝຸດ 3)测定规定强度时的拉伸速率
• 规定强度是指:Rp 、 Rt 、 Rr
• 弹性范围内,与测定ReH的应力速率相同。 • 进入塑性范围后,应变速率不超过0.0025/s, 或者调节至上述应力速率。
4)测定伸长率的试验速率
• • • • •
测定屈服点延伸率Ae: 测定最大力总伸长率Agt: 测定最大力非比例伸长率Ag: 测定断裂总伸长率At: 测定断后伸长率A:
同测定ReL 同测定Rm 同测定Rm 同测定Rm 同测定Rm
a 夹具位移法
• 在弹性范围,由于试验机刚度不变,试样的变形 特性与弹簧类似,因而可从力-时间或应力-时间曲 线得到应力速率;从伸长-时间曲线或应力-时间曲 线得到应变速率。 • 对于前两种方法,在弹性范围,对于刚性差的试 验系统,位移速率需要很大,约为刚性良好的试验机 的10倍,从低刚性结构试验系统横梁位移-时间和应 变-时间比较曲线可以看出,当试验中横梁位移速度 为 0.257mm/s, 由于试验系统刚性差,在开始阶段 , 很 大分量的位移消耗在试样链上,引伸计所反映的试样 标距内的变形速度则很小,为0.0295mm/s。
但在塑性范围,应力-应变直线性关系已 不存在,试验塑性变形开始后,对于出现明 显屈服的材料,试样急剧变形而试验力并不 增加,试验系统的全部位移集中于试样上。 因此,用横梁位移法控制拉伸速度时,作用 到试样上的真正拉伸速度与试验机刚度密切 相关。
复合材料拉伸试验PPT

拉伸应力的传递
-通常采用自锁楔式夹头中的试样加载。
保证试件在夹头中加紧的条件:
ห้องสมุดไป่ตู้
1 F P 2
P:载荷; F:一个侧面的摩擦力;
F可由下式确定:
P f F =Pf 2 tg ( )
f 复合材料同楔形面间摩擦系数;
楔形夹钳的斜角; 夹头斜面上滚动摩擦的折算角; 正压的传递强度系数
弹性模量的计算:
pDi E 2h
p 橡胶对内环表面产生的压强; Di -圆环内径;
在圆环外表面测得的或用位移传感器测定的应变
强度计算:
u pu
Di 2h
pu 环状试件破坏时的强度;
液静压加载法 -利用流体产生内压的液静压试验,克服了上述各种方法所固有的 缺点,可保证精度;然而,所需设备特殊、昂贵。
根据试验的目的不同 选择不同形状、尺寸的 试件。 要测定弹性常数该选 哪一种呢?
强度呢?
板样试件的加载
各向异性杆的变形特征 -对于各向异性材料,受轴向拉伸的杆不仅沿加载方向延伸,沿横向收 缩,而且在所有平行于坐标平面的面上受剪。与各向同性材料相反。
-在约束变形条件下,出 拉伸应力外,还产生弯曲 力和剪切力,从而导致变 形不均匀。 -此时,弯曲和剪切的影 响不仅取决于被测试材料 的弹性常数,而且取决于 试样的长宽比。
lL : 试样在基长lT 上的纵向变形;
i i 式中: lL / lL L和-lT / lT T 可直接用电阻应变片测量;
破坏模式
-纤维聚合物的破坏模式主要是由于增强叠层形式、各组分的材料的力学 性能及组分间的作用,工艺缺陷(空隙、纤维波纹度等)、以及试样尺寸 所决定。
几种破坏模式:
GBT22820金属材料室温拉伸试验方法PPT
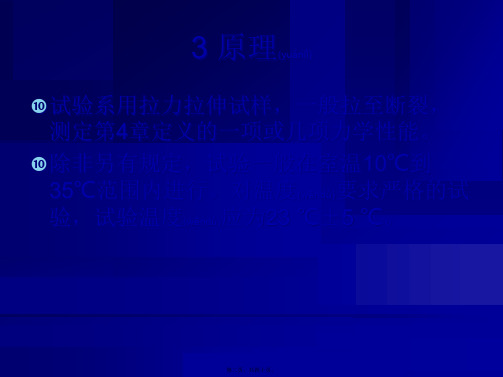
对于圆管纵向弧形试样,应在标距的两端 及中间三处测量宽度和壁厚,取用三处测 得最小横截面积。计算时管外径取其标称 值。
第三十七页,共四十页。
对于圆管横向矩形横截面试样,应在标距 的两端及中间三处测量宽度和厚度,取用 三处测得的最小横截面积。按照(ànzhào)式A1 计算
对于管段试样,应在其一端相互垂直方向 测量外径和四处壁厚,分别取其算术平均 值
相关产品标准可以规定不同于附录A和附录B的其他尺寸
矩形横截面试样。
不带头的试样,两夹头间的自由长度应足够,以使 试样原始标距的标记与最接近(jiējìn)的夹头间的距离不 小于1.5b。
应采用特别措施校直横向试样。
第三十五页,共四十页。
D2.4 管壁(ɡuǎn bì)厚度机加工的纵向圆形 横截面试样
第二十六页,共四十页。
22试验(shìyàn)结果处理
22.1试验出现以下情况之一其试验结果无 效,应重做同样数量试样的试验。
a)试样断在标距外或断在机械刻划的标距标 记上,而且断后伸长率小于规定最小值;
b)试验期间设备发生故障,影响了试验结果。 22.2试验后试样出现两个或两个以上的缩
颈以及显示出肉眼可见的冶金缺陷(quēxiàn)(例 如分层、气泡、夹渣、缩孔等),应在试验 记录和报告中注明。
机加工的纵向圆形横截面试样应采用附录B 的表B1规定的试样尺寸。相关产品标准应 根据管壁(ɡuǎn bì)厚度规定机加工的圆形横截面 试样尺寸。如无具体规定,按表D3选定试 样。
第三十六页,共四十页。
D3原始(yuánshǐ)横截面积S0的测定
试样原始横截面积的测定应准确(zhǔnquè)到 ±1%。
试样发生(fāshēng)屈服力首次下降前的最高应力
第三十七页,共四十页。
对于圆管横向矩形横截面试样,应在标距 的两端及中间三处测量宽度和厚度,取用 三处测得的最小横截面积。按照(ànzhào)式A1 计算
对于管段试样,应在其一端相互垂直方向 测量外径和四处壁厚,分别取其算术平均 值
相关产品标准可以规定不同于附录A和附录B的其他尺寸
矩形横截面试样。
不带头的试样,两夹头间的自由长度应足够,以使 试样原始标距的标记与最接近(jiējìn)的夹头间的距离不 小于1.5b。
应采用特别措施校直横向试样。
第三十五页,共四十页。
D2.4 管壁(ɡuǎn bì)厚度机加工的纵向圆形 横截面试样
第二十六页,共四十页。
22试验(shìyàn)结果处理
22.1试验出现以下情况之一其试验结果无 效,应重做同样数量试样的试验。
a)试样断在标距外或断在机械刻划的标距标 记上,而且断后伸长率小于规定最小值;
b)试验期间设备发生故障,影响了试验结果。 22.2试验后试样出现两个或两个以上的缩
颈以及显示出肉眼可见的冶金缺陷(quēxiàn)(例 如分层、气泡、夹渣、缩孔等),应在试验 记录和报告中注明。
机加工的纵向圆形横截面试样应采用附录B 的表B1规定的试样尺寸。相关产品标准应 根据管壁(ɡuǎn bì)厚度规定机加工的圆形横截面 试样尺寸。如无具体规定,按表D3选定试 样。
第三十六页,共四十页。
D3原始(yuánshǐ)横截面积S0的测定
试样原始横截面积的测定应准确(zhǔnquè)到 ±1%。
试样发生(fāshēng)屈服力首次下降前的最高应力
GBT228.1-2010 金属材料室温拉伸试验方法课件

(一)ReH和ReL的测定
•
• • • • •
•
1. 试验速率的选择
(1)A(应变速率控制的试验速率): 可选用下面两个范围之一: 范围1: 范围2:
e eL=0.00007s-1,相对误差±20% e eL=0.00025s-1,相对误差±20%(推荐)
应力速率/MPa/s
(2)B(应力速率控制的试验速率):
如仅测定上屈服强度,试验速率应恒定并保持在下表的规定范围内。
材料弹性模量E/MPa <150000 ≥150000
最小
2 6
最大
20 60
•
如仅测定下屈服强度,在试样平行长度的屈服期间应变速率应在 0.00025/s~0.0025/s之间,并尽可能保持恒定。
2. 试验方法的选择 (1)图解法
• 引伸计标距应≥1/2L0。引伸计不劣于1级 • 记录力-延伸曲线数据,直至超过屈服阶段 • 判定原则: – 屈服前的第一个峰值力为上屈服力,不管其后的峰值力 比它大或小。 – 屈服阶段中如呈现两个或两个以上的谷值力,舍去第一 个谷值力,取其余谷值力中之最小者判为下屈服力。如 只呈现一个下降谷值力,此谷值力判为下屈服力。 – 正确的判定结果应是下屈服力必定低于上屈服力。
6.断后伸长率(A):断后标距的残余伸长(Lu-Lo)与原始标距Lo
之比的百分率。 注:对于比例试样,若原始标距不为5.65So1/2(So为试样平行长度的 横截面积),符号A 应附以下角标说明所使用的比例系数,例如, A11.3表示原始标距为11.3So1/2的断后伸长率。
与(引伸计)有关术语的定义
•
•
k=11.3的试样称为长比例试样,其断后伸长率为A11.3
试验时,一般优先选用短比例试样,但要保证原始标距不小 于15mm,否则,建议选用长比例试样或其他类型试样。
拉伸试验国家标准ppt课件

原则上断裂发生在引伸计标距以内方为有效但断后伸长率等于或大于规定值不管断裂位置处于何处测量均为有为了避免因发生在规定的范围以外的断裂而造成试样报废可以采用附录f的移位方法测定断后伸将测定的断裂总延伸除以试样原始标距得到断裂总伸长率
拉伸试验国家标准简述
学习交流PPT
1
提纲
金属材料室温拉伸试验方法
➢ 原理
如图拉伸曲线,Fm应为曲线上 的B点,而不是旧标准中的取 其A点的力(上屈服力)计算抗 拉强度。
学习交流PPT
13
1.6试样
形状与尺寸
➢试样的形状与尺寸取决于被试验的金属产品的形状与尺寸。
➢试样横截面可以为圆形、矩形、多边形、环形,特殊情况下可 以为某些其他形状。
➢ 比例试样与非比例试样:
K:5.65 或11.3
量准确度等。 • 材料和试验参数:例如材料的特性,试样的几何形状和制备,
试验速率、温度、数据采集和分析技术等。
学习交流PPT
31
1.17试验结果处理
试验出现下列情况之一其试验结果无效,应重做同 样数量试样的试验。
➢试样断在标距外或断在机械刻划的标距标记上,而 且断后伸长率小于规定最小值;
➢试验期间设备发生故障,影响了试验结果。
学习交流PPT
15
1.8原始标距(L0)的标记
应用小标记、细划线或细墨线标记原始标距,但不 得用引起过早断裂的缺口作标记。对于比例试样, 应将原始标距的计算值修约至最接近5mm的倍数, 中间数值向较大一方修约。
原始标距的标记应准确到±1%。如平行长度(Lc) 比原始标距长许多,例如不经机加工的试样,可以标 记一系列套叠的原始标距。有时,可以在试样表面 划一条平行于试样纵轴的线,并在此线上标记原s万能材料试验机
拉伸试验国家标准简述
学习交流PPT
1
提纲
金属材料室温拉伸试验方法
➢ 原理
如图拉伸曲线,Fm应为曲线上 的B点,而不是旧标准中的取 其A点的力(上屈服力)计算抗 拉强度。
学习交流PPT
13
1.6试样
形状与尺寸
➢试样的形状与尺寸取决于被试验的金属产品的形状与尺寸。
➢试样横截面可以为圆形、矩形、多边形、环形,特殊情况下可 以为某些其他形状。
➢ 比例试样与非比例试样:
K:5.65 或11.3
量准确度等。 • 材料和试验参数:例如材料的特性,试样的几何形状和制备,
试验速率、温度、数据采集和分析技术等。
学习交流PPT
31
1.17试验结果处理
试验出现下列情况之一其试验结果无效,应重做同 样数量试样的试验。
➢试样断在标距外或断在机械刻划的标距标记上,而 且断后伸长率小于规定最小值;
➢试验期间设备发生故障,影响了试验结果。
学习交流PPT
15
1.8原始标距(L0)的标记
应用小标记、细划线或细墨线标记原始标距,但不 得用引起过早断裂的缺口作标记。对于比例试样, 应将原始标距的计算值修约至最接近5mm的倍数, 中间数值向较大一方修约。
原始标距的标记应准确到±1%。如平行长度(Lc) 比原始标距长许多,例如不经机加工的试样,可以标 记一系列套叠的原始标距。有时,可以在试样表面 划一条平行于试样纵轴的线,并在此线上标记原s万能材料试验机
金属材料拉伸试验PPT(完整版)

、 是衡量材料塑性的指标。 低碳钢的拉伸曲线大致分为四个阶段——弹性、屈服、强化、颈缩。
数据。 可计算低碳钢的屈服极限 ,强度极限 ,延伸率 和断面收缩率 。
4、观察以上两种材料在拉伸过程中的各种实验现象,并进行比较。 铸铁的强度极限 、延伸率 是由拉伸试验测定的。
2、开启机器,运行测试应用程序。 微机显示万能材料试验机
测量试件的初在始长试度即标样距 ,标并记距录数据段。 的两端和中间三处用游标卡尺 测量试样直径,最小值取作试样的初始直径 3、强化阶段:CD阶段。
可知铸铁不仅不具有 ,而且测定它的 和 也没有实际意义。 5、取下试样,测量断后最小直径d1,断后标距长度 。
d。测量试件的初始长度即标距 l ,并记录 铸铁试件是在非常微小的变形情况下突然断裂的,断裂后几乎测不到残余变形。
三、实验原理与方法
• 铸铁的强度极限 b 、延伸率 是由拉伸试
验测定的。 • 试验采用的圆截面标距 l 与直径d的比例规
定 l 5d ,称为5倍试件。
三、实验原理与方法
• 铸铁这类脆性材料拉伸时的载荷——变形曲线如图。
它不像低碳钢拉伸那样明显可分为
四个阶段,而是一根非常接近直线
F
状的曲线,并且没有下降段。铸铁
试验采用的圆截面标距 与直径d的比例规定为
它不像低碳钢拉伸那样明显可分为四个阶段,而是一根非常接近直线状的曲线,并且没有下降段。
四、实验步骤
4、在电子计算机应用程序界面中执行以下操作: (2)填写试验参数。 (3)首先清零,单击“运行”按钮。试验开始。 (4)注意观察试样的变形情况和“颈缩”现象,
金属材料拉伸试验
一、实验目的
1、了解试验设备——万能材料试验机的构造和
工作原理,掌握其操作规程及使用时的注意事
数据。 可计算低碳钢的屈服极限 ,强度极限 ,延伸率 和断面收缩率 。
4、观察以上两种材料在拉伸过程中的各种实验现象,并进行比较。 铸铁的强度极限 、延伸率 是由拉伸试验测定的。
2、开启机器,运行测试应用程序。 微机显示万能材料试验机
测量试件的初在始长试度即标样距 ,标并记距录数据段。 的两端和中间三处用游标卡尺 测量试样直径,最小值取作试样的初始直径 3、强化阶段:CD阶段。
可知铸铁不仅不具有 ,而且测定它的 和 也没有实际意义。 5、取下试样,测量断后最小直径d1,断后标距长度 。
d。测量试件的初始长度即标距 l ,并记录 铸铁试件是在非常微小的变形情况下突然断裂的,断裂后几乎测不到残余变形。
三、实验原理与方法
• 铸铁的强度极限 b 、延伸率 是由拉伸试
验测定的。 • 试验采用的圆截面标距 l 与直径d的比例规
定 l 5d ,称为5倍试件。
三、实验原理与方法
• 铸铁这类脆性材料拉伸时的载荷——变形曲线如图。
它不像低碳钢拉伸那样明显可分为
四个阶段,而是一根非常接近直线
F
状的曲线,并且没有下降段。铸铁
试验采用的圆截面标距 与直径d的比例规定为
它不像低碳钢拉伸那样明显可分为四个阶段,而是一根非常接近直线状的曲线,并且没有下降段。
四、实验步骤
4、在电子计算机应用程序界面中执行以下操作: (2)填写试验参数。 (3)首先清零,单击“运行”按钮。试验开始。 (4)注意观察试样的变形情况和“颈缩”现象,
金属材料拉伸试验
一、实验目的
1、了解试验设备——万能材料试验机的构造和
工作原理,掌握其操作规程及使用时的注意事