氧化铝焙烧温度控制系统课程设计-精品
过控课程设计报告-拜耳法生产氧化铝焙烧过程控制系统设计

《过程控制课程设计》任务书设计题目:拜耳法生产氧化铝焙烧过程控制系统设计姓名姓名姓名目录一、任务设计及要求 (3)1、任务 (3)二、相关背景及数据 (4)2.1氧化铝工艺 (4)2.2控制指标及要求 (4)三、各因素对主炉温度的影响 (5)3.1 煤气流量 (5)3.2氢氧化铝给料量的影响 (6)3.3空气流量 (6)四、方案选择 (7)4.1方案比较 (7)五、设备和仪表的选型 (9)5.1温度变送器 (9)5.2控制器 (10)5.3调节阀 (10)六曲线拟合及传递函数 (11)七、总结 (14)八、参考文献 (14)一、任务设计及要求1、任务1、了解生产工况:研究过程控制单元的生产工艺及工作环境,在这一阶段还需要收集工艺中有关的物性参数和重要数据。
2、明确控制要求:找出被控对象,针对可能出现的干扰因素分析控制目的及其应达到的控制效果。
3、拟定控制方案:按照现场的特点、控制室与现场的相对位置及系统的控制要求,确定合理的控制系统类型,定出各检测点、控制点的实际位置,初步分析控制系统的性能。
4、制定控制流程图:根据工艺特点以及控制方案画出系统的控制工艺流程图及控制方框图。
5、利用生产数据,进行拟合,得到控制对象传递函数,用于控制仿真。
6、选取被控变量和操纵变量:根据控制要求及工艺合理性进行选取,尽量选取容易检测、无容量滞后或滞后小的变量。
7、过程装置及仪表的选型:根据工艺提供的数据及仪表选型的原则(根据工艺数据和有关计算方法对调节阀进行相应的计算),调研产品的性能、质量和价格,选定检测、变送、显示、控制等各类仪表的规格、型号。
另外,对于仪表设备的辅助设备材料(仪表设备在安装过程中,还需要选用一些有关的其它设备材料)也需根据施工要求,进行数量统计,编制仪表安装材料表等。
8、设计总结:对整个设计过程做客观的评价,并阐述控制系统的优、缺点等。
二、相关背景及数据2.1氧化铝工艺目前,我国氧化铝工业采用的生产方法有烧结法,混联法和拜耳法三种,其中烧结法占20.2%,混联法占69.4%,拜耳法占10.4%.虽然烧结法的装备水平和技术水平在今年来有所提高,但是我国的烧结技术仍处于较低水平。
氧化铝厂焙烧炉合理化建议

氧化铝厂焙烧炉合理化建议
焙烧炉是氧化铝厂中用于将氧化铝粉末进行煅烧的设备。
针对氧化铝厂焙烧炉的合理化建议,我将按照段落排版,使用Word格式给出回答。
1. 炉内温度控制:合理控制焙烧炉内的温度对氧化铝的质量和产量有着重要影响。
建议引入先进的温度控制技术,如自动化控制系统和温度传感器,以确保炉内温度的准确控制和稳定性。
2. 燃料选择和燃烧控制:选择合适的燃料对焙烧炉的运行效率和煅烧质量至关重要。
建议评估不同燃料的能源效益和环境影响,并选择适宜的燃料类型。
同时,优化燃烧控制系统,确保燃料燃烧完全,减少污染物的排放。
3. 炉内气氛控制:氧化铝的煅烧过程对气氛的要求较高。
建议通过控制炉内氧气含量、气流速度和排气系统的设计来实现合适的气氛控制。
这有助于提高氧化铝的品质和煅烧效率。
4. 废气处理和能量回收:焙烧炉产生的废气中可能含有污染物和热能。
建议安装适当的废气处理设备,如除尘器和脱硫装置,以减少对环境的负面影响。
同时,开发热能回收技术,将废气中的热能回收利用,提高能源利用效率。
5. 运行参数监控和数据分析:建议建立完善的运行参数监控系统,实时监测焙
烧炉的工作状态和关键参数。
通过数据分析和异常报警功能,及时发现和解决潜在问题,提高生产效率和品质稳定性。
总结:针对氧化铝厂焙烧炉的合理化建议包括炉内温度控制、燃料选择和燃烧控制、炉内气氛控制、废气处理和能量回收以及运行参数监控和数据分析等方面的改进。
通过采取这些措施,可以提高焙烧炉的运行效率、煅烧质量和环境友好性。
氧化铝焙烧温度控制系统课程设计-精品

氧化铝焙烧温度控制系统课程设计-精品第一篇:氧化铝焙烧温度控制系统课程设计-精品氧化铝焙烧温度控制系统课程设计摘要:氧化铝是电解铝生产的主要原料,针对我国矿石特点,我国氧化铝的生产工艺主要采用的是拜尔法和烧结法以及混联法,在拜尔法中焙烧工序是氧化铝生产必不可少的一个过程,并且是整个氧化铝生产的最后一道工序,该生产过程的主要任务是将来自分解或平盘的带有附着水的氢氧化铝物质在焙烧炉中高温煅烧,脱除附着水和结晶水,从而生成物理化学性质符合电解要求的氧化铝。
氧化铝焙烧的主要工艺参数是灼烧温度.灼烧温度的高低与稳定与否直接决定着氧化铝的出厂质量,所以稳定控制氧化铝灼烧温度是保证氧化铝生产质量的主要途径。
本文以氧化铝焙烧生产过程控制系统为背景,开展了氧化铝焙烧生产过程控制策略的研究和控制系统的设计以及器件的选型。
关键词:氧化铝焙烧;器件选型;串级控制系统;PID参数整定一、氧化铝生产工艺生产氧化铝的方法大致可分为四类:碱法、酸法、酸碱联合法与热法。
目前工业上几乎全部是采用碱法生产。
碱法有拜耳法、烧结法及拜耳烧结联合法等多种流程。
目前,我国氧化铝工业采用的生产方法有烧结法,混联法和拜耳法三种,其中烧结法占20.2%,混联法占69.4%,拜耳法占10.4%。
虽然烧结法的装备水平和技术水平在今年来有所提高,但是我国的烧结技术仍处于较低水平。
而由于拜耳法和烧结混合法组成的混联法,不仅由于增加了烧结系统而使整个流程复杂,投资增大,更由于烧结法系统装备水平和技术水平不高,使得氧化铝生产的能耗增大,成本增高,降低我国氧化铝产品在世界市场上的竞争力。
拜耳法比较简单,能耗小,产品质量好,处理高品位铝土矿石,产品成品也低。
目前全世界90%的氧化铝是用拜耳法生产的。
拜耳法的原理是基于氧化铝在苛性碱溶液中溶解度的变化以及过氧化钠浓度和温度的关系。
高温和高浓度的铝酸钠溶液处于比较稳定的状态,而在温度和浓度降低时则自发分解析出氢氧化铝沉淀,拜耳法便是建立在这样性质的基础上的。
冶金沸腾焙烧炉温度控制系统的设计.

课程设计(论文)题目:冶金沸腾焙烧炉温度控制系统的设计摘要本设计是冶金沸腾焙烧炉温度控制系统的设计,锌精矿的焙烧,直接法制取高级氧化锌,首先是将锌精矿经过焙烧转变成氧化物,然后再经制团、韦氏炉冶炼得到高级氧化锌,焙烧工序是必不可少的第一步沸腾焙烧是目前应用最广泛的焙烧技术,它具有设备简单处理量大、控制容易、气一固间热质交换迅速、层内温度均匀、质量稳定、易于自动化等一系列优点。
考虑到鼓风量及其压力、炉膛压力、排烟量、循环冷却水量等的外界干扰。
从生产工艺出发,合理选择调节阀的气开气关方式,确保设备和人员的安全。
本设计选择温度传感器、压力变送器、温度变送器、温度控制器、压力控制器和执行器构成串级控制系统实现对沸腾焙烧炉温度的控制,串级控制系统的主回路是定制控制系统,副回路是随动控制系统,通过他们的协调工作,使主参数能够准确的控制在工艺规定的范围之内。
关键词:温度控制;串级控制;变送器;炉膛压力;目录第1章绪论 (1)第2章系统方案论证 (2)2.1任务分析 (2)2.2方案选择 (2)第3章仪表选择 (4)3.1变送器的选择 (4)3.2控制器选型 (6)3.3执行器的选择 (8)第4章系统控制算法 (10)4.1控制规律选择 (10)4.2气开气关选择 (10)4.3调节器正负作用选择 (10)第5章仿真 (11)第6章课程设计总结 (15)参考文献 (16)第1章绪论沸腾焙烧炉是湿法炼锌过程中的重要环节,当今世界随着湿法炼锌技术的不断发展,生产规模的不断大型化,要求沸腾焙烧炉的技术也不断的发展,沸腾焙烧炉在湿法炼锌中占有重要地位,沸腾焙烧的基础是固体流态化,用沸腾焙烧炉焙烧锌精矿,炉内热容量大且均匀,温差小,颗粒与空气接触表面积大,反应速度快,强度高,传热传质效率高,这些都使焙烧过程大大强化,产品质量稳定,生产效率高,设备与操作便于实现生产连续化和自动化等一系列优点,各国都很重视此项技术,因此得到了广泛应用。
氧化铝焙烧生产工艺

氧化铝焙烧生产工艺1. 简介氧化铝是一种重要的工业原料,广泛应用于陶瓷、耐火材料、电子材料等领域。
氧化铝的生产工艺中,焙烧是一个关键步骤。
焙烧过程中,通过控制温度和气氛,可以使氧化铝晶体结构发生变化,从而提高其物理化学性质。
本文将介绍氧化铝焙烧的生产工艺,包括焙烧设备、焙烧温度控制、气氛控制等方面的内容。
2. 焙烧设备氧化铝焙烧的设备主要包括焙烧炉和热风循环系统。
2.1 焙烧炉焙烧炉是氧化铝焙烧的关键设备,其主要功能是提供足够的热量,并控制焙烧过程中的温度。
焙烧炉通常采用间接加热方式,即通过燃烧器产生的热量,间接加热焙烧炉内的物料。
焙烧炉的结构一般包括炉体、燃烧器、温度控制系统等部分。
炉体通常采用耐高温材料制成,以保证焙烧过程中的高温环境不会对设备造成损坏。
燃烧器则负责燃烧燃料,产生热量。
温度控制系统则根据焙烧工艺要求,对炉内温度进行实时监测和控制。
2.2 热风循环系统热风循环系统是焙烧过程中的辅助设备,其主要功能是将炉内产生的热风重新循环利用,提高能源利用效率。
热风循环系统一般包括热风管道、风机和热风循环控制系统等部分。
热风管道将炉内产生的热风引导到需要加热的区域。
风机则负责将热风从炉外吸入,并通过管道循环到焙烧炉内。
热风循环控制系统可以根据焙烧工艺要求,调节热风的流量和温度,以达到最佳的焙烧效果。
3. 焙烧温度控制焙烧温度是影响氧化铝焙烧效果的重要参数。
在焙烧过程中,通过控制温度可以调控氧化铝晶体结构的形成和转化,从而影响其物理化学性质。
一般来说,氧化铝的焙烧温度通常在1000℃到1200℃之间。
具体的焙烧温度还需要根据原料的性质和所需的产品性能进行调整。
在焙烧过程中,温度的均匀性也是关键因素之一。
为了保证焙烧产物的质量一致性,需要在炉内设置合理的温度梯度,并通过温度控制系统对焙烧炉内的温度进行实时监测和控制。
4. 气氛控制焙烧过程中的气氛对氧化铝的性质也有重要影响。
不同的气氛可以改变氧化铝晶体结构的形成,进而影响其物理化学性质。
冶金沸腾焙烧炉温度控制系统的设计解析

课程设计(论文)题目:冶金沸腾焙烧炉温度控制系统的设计摘要本设计是冶金沸腾焙烧炉温度控制系统的设计,锌精矿的焙烧,直接法制取高级氧化锌,首先是将锌精矿经过焙烧转变成氧化物,然后再经制团、韦氏炉冶炼得到高级氧化锌,焙烧工序是必不可少的第一步沸腾焙烧是目前应用最广泛的焙烧技术,它具有设备简单处理量大、控制容易、气一固间热质交换迅速、层内温度均匀、质量稳定、易于自动化等一系列优点。
考虑到鼓风量及其压力、炉膛压力、排烟量、循环冷却水量等的外界干扰。
从生产工艺出发,合理选择调节阀的气开气关方式,确保设备和人员的安全。
本设计选择温度传感器、压力变送器、温度变送器、温度控制器、压力控制器和执行器构成串级控制系统实现对沸腾焙烧炉温度的控制,串级控制系统的主回路是定制控制系统,副回路是随动控制系统,通过他们的协调工作,使主参数能够准确的控制在工艺规定的范围之内。
关键词:温度控制;串级控制;变送器;炉膛压力;目录第1章绪论 (1)第2章系统方案论证 (2)2.1任务分析 (2)2.2方案选择 (2)第3章仪表选择 (4)3.1变送器的选择 (4)3.2控制器选型 (6)3.3执行器的选择 (8)第4章系统控制算法 (10)4.1控制规律选择 (10)4.2气开气关选择 (10)4.3调节器正负作用选择 (10)第5章仿真 (11)第6章课程设计总结 (15)参考文献 (16)第1章绪论沸腾焙烧炉是湿法炼锌过程中的重要环节,当今世界随着湿法炼锌技术的不断发展,生产规模的不断大型化,要求沸腾焙烧炉的技术也不断的发展,沸腾焙烧炉在湿法炼锌中占有重要地位,沸腾焙烧的基础是固体流态化,用沸腾焙烧炉焙烧锌精矿,炉内热容量大且均匀,温差小,颗粒与空气接触表面积大,反应速度快,强度高,传热传质效率高,这些都使焙烧过程大大强化,产品质量稳定,生产效率高,设备与操作便于实现生产连续化和自动化等一系列优点,各国都很重视此项技术,因此得到了广泛应用。
氧化铝下料控制系统的设计

氧化铝下料控制系统的设计作者:胡荣颐陈振勇梁乔晓来源:《科学与财富》2018年第33期一、氧化铝生产方法酸法,碱法和电路熔炼法都可以从铝土矿中得到氧化铝的方法。
目前酸法和电路熔炼法生产氧化铝在经济上无法和碱法竞争,因此,在大规模工业生产氧化铝当中使用的是碱法生产。
碱法生产氧化铝又分为拜耳法、烧结法和联合法三种工艺流程,下面将逐一介绍这三种方法的工艺流程。
二、碱法生产氧化铝工艺介绍2.1拜耳法:生产氧化铝的方法大致可以分为四类:碱法、酸法、酸碱联合法与热法。
目前大多数工业生产采用的是碱法生产。
碱法主要是拜耳法、烧结法和拜耳烧结联合法等。
拜耳法的原理是基于氧化铝在可兴建溶液中溶解度的变化以及过氧化钠溶液和温度的关系。
高温和高浓度的铝酸钠溶液处于比较稳定的状态,而在温度和浓度降低时则自发分解析出氢氧化铝沉淀,拜耳法便是建立在这样性质的基础上的。
主要化学方程式拜耳法生产氧化铝的主要工序有原矿浆制备,高压溶出,压煮矿浆和稀释及赤泥分离和洗涤,晶种分解,氢氧化铝的分级与洗涤分解,氢氧化铝焙烧,母液蒸发和苏打苟性化。
2.1.1原矿浆制备。
首先将铝土矿破碎到符合要求的粒度与含有游离的NaOH的循环母液按一定的比例配合一道送入湿磨内进行细磨,制成合格的原矿浆,并在矿浆槽内贮存和预热。
2.1.2高压溶出。
原矿浆经预热后进入管道溶出器设备,在高压下溶出。
铝土矿内所含氧化铝溶解成铝酸钠进入溶液,而氧化钛以及大部分的二氧化硅等杂质进入固相残渣即赤泥中。
溶出所得矿浆称压煮矿浆,经自蒸发器减压降温后送入缓冲槽。
2.1.3压煮矿浆和稀释及赤泥分离和洗涤。
压煮矿浆含氧化铝浓度高,为了便于赤泥沉降分离和下一步的晶种分解,首先加入赤泥洗液将压煮矿浆进行稀释(称赤泥浆液),然后利用沉降槽进行赤泥与铝酸钠溶液的分离。
分离后的赤泥经过几次洗涤回收所含的附碱后排至赤泥场(国外有排入深海的),赤泥洗液用来稀释下一批压煮矿浆。
2.1.4晶种分解。
氧化铝生产焙烧过程计算机监控系统的设计与开发的开题报告
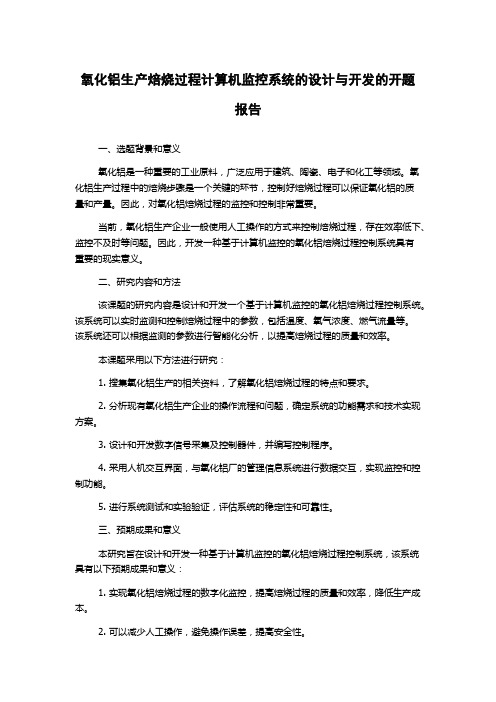
氧化铝生产焙烧过程计算机监控系统的设计与开发的开题报告一、选题背景和意义氧化铝是一种重要的工业原料,广泛应用于建筑、陶瓷、电子和化工等领域。
氧化铝生产过程中的焙烧步骤是一个关键的环节,控制好焙烧过程可以保证氧化铝的质量和产量。
因此,对氧化铝焙烧过程的监控和控制非常重要。
当前,氧化铝生产企业一般使用人工操作的方式来控制焙烧过程,存在效率低下、监控不及时等问题。
因此,开发一种基于计算机监控的氧化铝焙烧过程控制系统具有重要的现实意义。
二、研究内容和方法该课题的研究内容是设计和开发一个基于计算机监控的氧化铝焙烧过程控制系统。
该系统可以实时监测和控制焙烧过程中的参数,包括温度、氧气浓度、燃气流量等。
该系统还可以根据监测的参数进行智能化分析,以提高焙烧过程的质量和效率。
本课题采用以下方法进行研究:1. 搜集氧化铝生产的相关资料,了解氧化铝焙烧过程的特点和要求。
2. 分析现有氧化铝生产企业的操作流程和问题,确定系统的功能需求和技术实现方案。
3. 设计和开发数字信号采集及控制器件,并编写控制程序。
4. 采用人机交互界面,与氧化铝厂的管理信息系统进行数据交互,实现监控和控制功能。
5. 进行系统测试和实验验证,评估系统的稳定性和可靠性。
三、预期成果和意义本研究旨在设计和开发一种基于计算机监控的氧化铝焙烧过程控制系统,该系统具有以下预期成果和意义:1. 实现氧化铝焙烧过程的数字化监控,提高焙烧过程的质量和效率,降低生产成本。
2. 可以减少人工操作,避免操作误差,提高安全性。
3. 推动我国氧化铝生产的智能化、自动化发展,提高氧化铝产业的技术竞争力。
四、研究进度安排本课题的研究进度按以下安排开展:1. 前期调研和文献综述:1个月2. 系统设计和数字信号采集及控制器件开发:2个月3. 控制程序编写和人机交互界面开发:3个月4. 实验测试和系统评估:1个月5. 论文撰写和答辩准备:2个月五、课题预算本课题的预算总额为20万元,主要用于数字信号采集及控制器件的制造和组装、软件开发、实验费用等。
- 1、下载文档前请自行甄别文档内容的完整性,平台不提供额外的编辑、内容补充、找答案等附加服务。
- 2、"仅部分预览"的文档,不可在线预览部分如存在完整性等问题,可反馈申请退款(可完整预览的文档不适用该条件!)。
- 3、如文档侵犯您的权益,请联系客服反馈,我们会尽快为您处理(人工客服工作时间:9:00-18:30)。
氧化铝焙烧温度控制系统课程设计摘要:氧化铝是电解铝生产的主要原料,针对我国矿石特点,我国氧化铝的生产工艺主要采用的是拜尔法和烧结法以及混联法,在拜尔法中焙烧工序是氧化铝生产必不可少的一个过程,并且是整个氧化铝生产的最后一道工序,该生产过程的主要任务是将来自分解或平盘的带有附着水的氢氧化铝物质在焙烧炉中高温煅烧,脱除附着水和结晶水,从而生成物理化学性质符合电解要求的氧化铝。
氧化铝焙烧的主要工艺参数是灼烧温度.灼烧温度的高低与稳定与否直接决定着氧化铝的出厂质量,所以稳定控制氧化铝灼烧温度是保证氧化铝生产质量 的主要途径。
本文以氧化铝焙烧生产过程控制系统为背景,开展了氧化铝焙烧生产过程控制策略的研究和控制系统的设计以及器件的选型。
关键词:氧化铝焙烧;器件选型;串级控制系统;PID 参数整定一、氧化铝生产工艺生产氧化铝的方法大致可分为四类:碱法、酸法、酸碱联合法与热法。
目前工业上几乎全部是采用碱法生产。
碱法有拜耳法、烧结法及拜耳烧结联合法等多种流程。
目前,我国氧化铝工业采用的生产方法有烧结法,混联法和拜耳法三种,其中烧结法占20.2%,混联法占69.4%,拜耳法占10.4%。
虽然烧结法的装备水平和技术水平在今年来有所提高,但是我国的烧结技术仍处于较低水平。
而由于拜耳法和烧结混合法组成的混联法,不仅由于增加了烧结系统而使整个流程复杂,投资增大,更由于烧结法系统装备水平和技术水平不高,使得氧化铝生产的能耗增大,成本增高,降低我国氧化铝产品在世界市场上的竞争力。
拜耳法比较简单,能耗小,产品质量好,处理高品位铝土矿石,产品成品也低。
目前全世界90%的氧化铝是用拜耳法生产的。
拜耳法的原理是基于氧化铝在苛性碱溶液中溶解度的变化以及过氧化钠浓度和温度的关系。
高温和高浓度的铝酸钠溶液处于比较稳定的状态,而在温度和浓度降低时则自发分解析出氢氧化铝沉淀,拜耳法便是建立在这样性质的基础上的。
下面两项主要反映是这一方法的基础:42232)(2)3(2l OH NaAl O H x NaOH O xH O A =-++NaOH OH Al OH NaAl +=34)()(前一反映是在用循环的铝酸钠碱溶液溶出铝土矿时进行的。
铝土矿中所含的一水和三水氧化铝在一定条件下以铝酸钠形态进入溶液。
后一反映是在另一条件下发生的析出氢氧化铝沉淀的水解反应。
铝酸钠溶液在95-100度不致水解的稳定性可以用来从其中分离赤泥,然后使溶液冷却,转变为不稳定状态,以析出氢氧化铝。
拜耳法生产过程简介:原矿经选矿、原矿浆磨制、溶出与脱硅、赤泥分离与精制、晶种分解、氢氧化铝焙烧成为氧化铝产品。
破碎后进厂的碎高矿经均化场均化后,用斗轮取料机取料入输送机进入铝矿仓,石灰石经煅烧后输送到石灰仓,然后与循环母液经调配后按比例进入棒磨机、球磨机的两段磨和旋流器组成的磨矿分级闭路循环系统。
分级后的溢流经缓冲槽和泵进入原矿浆储槽,用高压泥浆泵输送矿浆进入多级预热和溶出系统,加热介质可用溶盐也可用高压新蒸气,各级矿浆自蒸发器排出的乏气分别用来预热各级预热器中的矿浆。
溶出设备可用套管加热与高压釜组成溶出器组。
溶出后的矿浆经多级降压自蒸发器降压后,与赤泥一次洗液一同进入矿浆稀释槽。
末级自蒸发器排出的乏气,用来预热赤泥洗水,洗水由循环水和不合格的冷凝水组成。
稀释矿浆进入分离沉降槽,其溢流经过叶滤和降温后送去晶种搅拌分解,分解后的氢氧化铝浆液经分离后,大部分氢氧化铝返回种分槽作为晶种使用,其余部分送去洗涤,洗水用纯净的热水,洗净后的氢氧化铝送去焙烧,焙烧后的氧化铝即为成品氧化铝。
分离后的种分母液送去蒸发,加入少量盐类晶种以诱导盐类晶种析出,其溢流与滤液、补充新的液体苛性钠后组成循环母液,送去调配制备原矿浆。
二、氧化铝生产焙烧过程工艺氢氧化铝焙烧是氧化铝生产工艺中的最后一道工序。
焙烧的目的是在高温下把氧化铝的附着水和结晶水脱除,从而生成物理化学性质符合电解要求的氧化铝。
(1)焙烧原理氢氧化铝经过焙烧炉的干燥段,焙烧段和冷却段使之烘干,脱水和晶形转变而变成氧化铝产品其化学变化可分为以下几个阶段。
(a )脱除附着水O H OH Al O H Al C 2310023)((OH)+−−→−当温度高于100C 时氢氧化铝中的附着水被蒸发,此反应发生在闪速干燥器。
(b)脱除结晶水结晶水的脱除分两步进行,250-300度时,失去两个结晶水,在500-600度的温度下它失去最后一个结晶水。
而成为32r O Al -。
O H O Al O H O Al C 23230025023223+−−−→−-O H O Al O H O Al C 232600500232+-−−−→−-γ(c)晶型转变氢氧化铝在脱水过程中伴随着晶体转变,32r O Al -在950度时开始进行晶型转变,逐渐由32r O Al -转变为32-a O Al 。
(2)氧化铝焙烧过程生产过程流程介绍流态化焙烧是世界上最先进的氢氧化铝焙烧技术与装置,流态化是一种固体颗粒与气体接触而变成类似流体状态的操作技术。
而固体物料在流态化状态下与气体或液体的热交换过程最为强烈。
(a)此炉型采用了在干燥段设计热发生器这一新颖措施,当供料氢氧化铝附着水含量增大时,不需象其它炉型那样采取增加过剩空气的方式来增加干燥能力,仅需启动干燥热发生器来增加干燥段热量,避免了废气量大增而大量损失热量,因此,与前二种炉型相比,气体悬焙烧炉热耗和电耗要低。
(b)整套装置设计简单。
一是物料自上而下流动,可避免事故停炉时的炉内积料和计划停炉时的排料;二是设备简单,除流化冷却器外无任何流化床板,没有物料控制阀,方便了设备维检修:三是负压作业对焙烧炉的问题诊断和事故处理有利。
这些都有利于故障后生产的快速恢复,给生产组织带来方便。
(c)控制回路简单,气体悬浮焙烧炉虽有多条自动控制回路,但在生产中起主要作用的仅有2条,一条是主燃烧系统的主炉温度控制回路,另一条是O2含量控制回路。
三、焙烧炉温度控制方案设计目前工业自动化水平已成为衡量各行各业现代化水平的一个重要标志。
一个控控制系统包括控制器、传感器、变送器、执行机构、输入输出接口。
控制器的输出经过输出接口、执行机构,加到被控系统上;控制系统的被控量,经过传感器,变送器,通过输入接口送到控制器。
(1)对于焙烧过程而言,主要控制焙烧炉出口温度。
而影响焙烧炉出口温度的因素主要就是燃料的流量,而流量又决定于主燃烧器的流量阀门的开度。
因此,我们引入中间点信号,即最能反应焙烧炉出口温度的进入主燃烧器中的燃料流量,作为调节器的补充信号,以便快速反应影响焙烧炉出口温度变化的扰动,引入该点作为辅助被调量,通过调节管道上流量阀的开度调整燃料的流量,组成了流量.温度串级调节系统,从而调节焙烧炉的出口温度,来保氧化铝的产量和质量口”。
焙烧炉温度控制回路流程图如图所示:图1 焙烧炉温度控制回路流程图焙烧炉温度控制回路设计为串级控制回路,主回路为温度控制回路,其输入为焙烧炉的出口温度的设定值,控制器输出为副回路的输入,测量仪表为一体化热电偶;副回路为流量控制回路,其输入为主控制器的输出或主燃烧器的流量设定,控制器输出为主燃烧器V19流量调节阀的百分比开度,执行机构为流量电动调节阀,测量仪表为电磁流量计。
从方框图可以看出,串级调节系统有两个闭环的调节回路:图2 温度控制回路结构图a)由PID控制器、调节阀、主燃烧器、流量计构成了副环回路。
b)由PID控制器、副环回路、焙烧炉、温度计构成了主环回路。
副环回路为流量调节系统,选用标准PID控制器来控制该系统。
主环回路为温度调节系统,也选用标准PID控制器来控制该系统。
主调节器出的的信号不是直接调节温度,而是作为副调节器的可变给定值,与燃料流量信号比较,再通过副调节器去控制电动阀动作,以调节燃料流量,保证焙烧炉出口温度能较快的跟踪设定值并最终保持在设定值附近不变。
(2)从动态特性的角度考虑,优化控制器性能与结构,提高系统的响应速度。
在对控制系统进行设计时,尽量根据被控制对象选择一组较为合适的控制器参数,提达到更好可控制效果。
而通过对系统建立数学模型,根据模型特性,通过设定某种性能指标,在实现最优指标的前提下,对控制器参数进行寻优可谓是个好的优化控制器性能的办法。
对于串级控制系统来说,有两个控制器,因此需要分别对两个控制器的参数进行整定,整定的顺序先调节副回路,待副回路调节达到要求后,在调节主回路。
(3)如果测量元件的延迟和惯性比较大,就不能及时反映温度的变化,就会造成系统不稳定,影响控制质量。
因此,在系统的仪表选型上尽量使用快速的测量元件,安装在正确的位置,保证测量信号传递的快速性,减小延迟和惯性。
四、焙烧炉温度回路对象模型的建立与验证建立数学模型的方法有许多种,像机理建模、系统辨识等。
机理建模有较大的普遍性,但是多数工业过程的机理较为复杂,其数学模型很难建立,虽然在建模过程中作了一些具有一定实际依据的近似和假设,但是逼近不能完全反映过程的实际情况,有时甚至会带来一些估计不到的影响。
因此,在工程目前主要采用试验建模一过程辨识和参数估计的方法。
建模的方法我们采用响应曲线法,响应曲线法主要用于阶跃响应曲线和矩形脉冲响应曲线。
图3 阶跃响应法图4 矩形脉冲响应法(1)阶跃响应曲线的试验测定:将被控过程的输入量作一阶跃变化,同时记录其输出量随时间而变化的曲线,则称为阶跃响应曲线。
阶跃响应曲线能直观,完全描述被控过程的动态特性。
实验测试方法易于实现,只要是阀门的开度作一阶跃变化即可,实验时必须注意:(a)合理选择阶跃扰动量,既不能太大,以免影响正常生产,也不能太小,以防被控过程的不真实性。
通常取阶跃信号值为正常输入信号的5%一15%,以不影响生产为准。
(b)试验应在相同的测试条件下重复做几次,需获得两次以上的比较接近的相应曲线,减少干扰的影响。
(c)试验应在阶跃信号作正,反方向变化时分别测出其相应曲线,以检验被控过程的非线性程度。
(d)试验前,即在输入阶跃信号前,被控过程必需处于稳定的工作状态。
在一次试验完成后,必须是被控过程稳定一段时间后再施加测试信号作第二次试验。
考虑到实际工程的方便,对主炉温度控制我们采用阶跃响应曲线试验建模法。
根据控制理论来分析,设计或改进一个过程控制系统,只有过程的阶跃响应曲线显然是不够的,还必须有阶跃响应曲线来辨识被控过程数学模型,如微分方程、传递函数、频率特性、差分方程等。
在确定模型参数时,首先分析阶跃响应曲线的形状,选取一种模型结构,然后进行参数估计。
由阶跃响应曲线辨识数学模型的方法很多,一阶惯性环节是一种常用的估计方法。
在过程输入阶跃信号x0的瞬时,其响应曲线的斜率最大,如图5所示。
图5 阶跃响应曲线此时,其数学模型可用一阶惯性环节来近似,即1s )s (w +=τK式中参数K 、τ的求法如下:(1)过程的静态放大系数0)0()(y x y K -∞=(2)过程的时间常数对于上式所示的过程模型,在阶跃信号x 0作用下的时间特性为:)1(Kx t y 0τt e --=)(式中,K 为过程的放大系数,可由上式可确定。