注塑生产工艺知识
关于注塑的知识点总结

关于注塑的知识点总结一、注塑工艺流程1.设计模具:根据产品设计要求,设计和制造塑料注射成型所需的模具。
2.原料筛选:根据产品要求和加工特点,选择合适的塑料原料,并进行配料、干燥等处理。
3.塑料熔化:将塑料颗粒加热至熔化状态,形成流动状态的熔体。
4.模具注射:将熔化的塑料通过高压注射进入模具腔内,充填整个模具腔,成型出所需的塑料制品。
5.冷却固化:待塑料充填完成后,进行冷却固化,使塑料制品在模具中形成稳定的形状。
6.模具打开:冷却固化完成后,打开模具,取出成型的塑料制品。
7.脱模整理:将成型的塑料制品进行去除模具余料、修整、表面处理等工序,得到符合要求的塑料制品。
二、注塑设备1.注塑机:是进行塑料注射成型的核心设备,根据产品要求和生产规模选择合适型号的注塑机。
2.模具:塑料注塑成型所需的模具,根据产品设计要求和注塑工艺特点进行设计和制造。
3.辅助设备:如塑料干燥机、颜料添加机、冷却水机、除湿机、输送设备等,用于对塑料原料和成品进行辅助处理。
三、注塑工艺参数1.注射压力:即注塑机对塑料进行注射时的压力大小,决定了塑料充填模具的速度和充填度。
2.注射速度:注射机对塑料进行注射的速度,影响着塑料注射的充填时间和充填性能。
3.冷却时间:成型后的塑料制品需要在模具内进行冷却固化,冷却时间的长短影响着产品的成型质量和产能。
4.模具温度:模具温度的设置影响着塑料的冷却固化速度和塑料制品的表面质量。
5.料斗温度:对塑料进行熔化处理前,通常需要进行干燥,料斗温度要根据塑料的种类和湿度进行合理设置。
四、注塑材料1.常见的注塑材料有聚丙烯(PP)、聚乙烯(PE)、聚苯乙烯(PS)、聚氯乙烯(PVC)、工程塑料如聚酰胺(NYLON)、聚碳酸酯(PC)、聚苯醚(PEEK)等。
不同种类的塑料具有不同的物理性能、耐热性、耐化学性、机械性能等特点,因此在选择注塑材料时需要根据产品功能和性能要求进行合理的选择。
2.在注塑过程中,需要对塑料原料进行干燥处理,以保证塑料中的水分含量在合理的范围内,避免在注塑过程中出现气泡、状况等缺陷。
注塑工艺基础知识培训
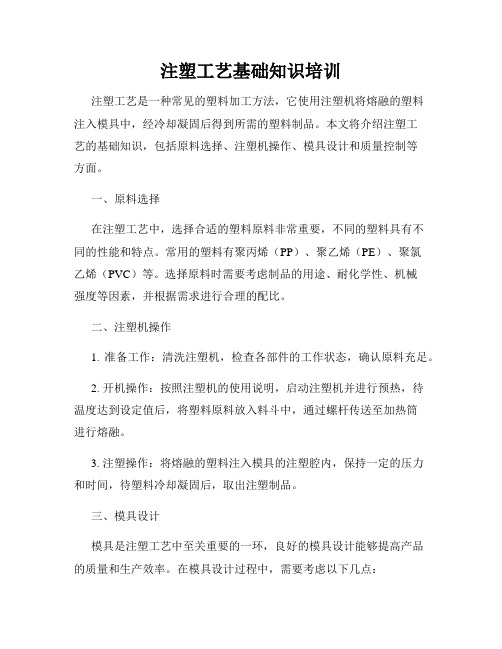
注塑工艺基础知识培训注塑工艺是一种常见的塑料加工方法,它使用注塑机将熔融的塑料注入模具中,经冷却凝固后得到所需的塑料制品。
本文将介绍注塑工艺的基础知识,包括原料选择、注塑机操作、模具设计和质量控制等方面。
一、原料选择在注塑工艺中,选择合适的塑料原料非常重要,不同的塑料具有不同的性能和特点。
常用的塑料有聚丙烯(PP)、聚乙烯(PE)、聚氯乙烯(PVC)等。
选择原料时需要考虑制品的用途、耐化学性、机械强度等因素,并根据需求进行合理的配比。
二、注塑机操作1. 准备工作:清洗注塑机,检查各部件的工作状态,确认原料充足。
2. 开机操作:按照注塑机的使用说明,启动注塑机并进行预热,待温度达到设定值后,将塑料原料放入料斗中,通过螺杆传送至加热筒进行熔融。
3. 注塑操作:将熔融的塑料注入模具的注塑腔内,保持一定的压力和时间,待塑料冷却凝固后,取出注塑制品。
三、模具设计模具是注塑工艺中至关重要的一环,良好的模具设计能够提高产品的质量和生产效率。
在模具设计过程中,需要考虑以下几点:1. 结构设计:合理的模具结构能够保证注塑制品的形状和尺寸精度,同时方便模具的装卸和维护。
2. 冷却系统设计:冷却时间对注塑周期有着重要影响。
优化冷却系统的设计,能够提高生产效率并避免制品缺陷。
3. 模具材料选择:模具需要具有足够的硬度和耐磨性,常见的模具材料有H13、S7等。
四、质量控制在注塑工艺中,质量控制是保证产品质量的关键。
以下是一些常用的质量控制措施:1. 注塑机参数控制:根据产品要求,合理设置注塑机的温度、压力、注塑速度等参数,保证制品的质量。
2. 模具维护:定期对模具进行检查和维护,及时修复损坏的部件,避免因模具问题引起的质量缺陷。
3. 制品检测:对注塑制品进行外观检查、尺寸测量等多项检测,确保产品符合设计要求。
总结:通过本文的培训,我们了解了注塑工艺的基础知识,包括原料选择、注塑机操作、模具设计和质量控制等方面。
合理运用这些知识,可以提高注塑制品的质量和生产效率,为塑料制品加工行业的发展做出贡献。
模具注塑知识点归纳总结
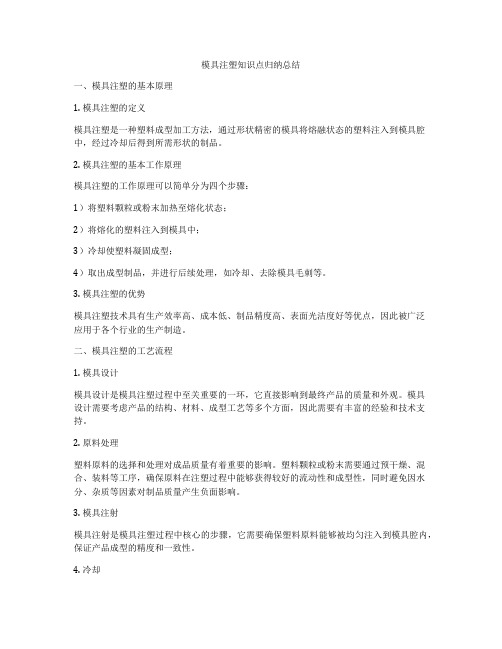
模具注塑知识点归纳总结一、模具注塑的基本原理1. 模具注塑的定义模具注塑是一种塑料成型加工方法,通过形状精密的模具将熔融状态的塑料注入到模具腔中,经过冷却后得到所需形状的制品。
2. 模具注塑的基本工作原理模具注塑的工作原理可以简单分为四个步骤:1)将塑料颗粒或粉末加热至熔化状态;2)将熔化的塑料注入到模具中;3)冷却使塑料凝固成型;4)取出成型制品,并进行后续处理,如冷却、去除模具毛刺等。
3. 模具注塑的优势模具注塑技术具有生产效率高、成本低、制品精度高、表面光洁度好等优点,因此被广泛应用于各个行业的生产制造。
二、模具注塑的工艺流程1. 模具设计模具设计是模具注塑过程中至关重要的一环,它直接影响到最终产品的质量和外观。
模具设计需要考虑产品的结构、材料、成型工艺等多个方面,因此需要有丰富的经验和技术支持。
2. 原料处理塑料原料的选择和处理对成品质量有着重要的影响。
塑料颗粒或粉末需要通过预干燥、混合、装料等工序,确保原料在注塑过程中能够获得较好的流动性和成型性,同时避免因水分、杂质等因素对制品质量产生负面影响。
3. 模具注射模具注射是模具注塑过程中核心的步骤,它需要确保塑料原料能够被均匀注入到模具腔内,保证产品成型的精度和一致性。
4. 冷却在模具注塑过程中,塑料充填后需要进行冷却,使其快速固化成型。
冷却的速度和均匀性会直接影响到产品的收缩率和内部应力分布,因此冷却系统的设计和控制非常重要。
5. 取模冷却后的成型制品将从模具中取出,这一步骤需要谨慎操作,避免对产品造成损伤或变形。
6. 后处理成型后的制品可能需要进行去除毛刺、修整、喷漆等后处理工序,以使其符合最终产品的要求。
三、模具注塑的材料选择1. 塑料原料的选择不同的塑料原料拥有不同的物理性能和化学性质,在模具注塑过程中需要根据产品的要求选择合适的塑料,如ABS、PC、PP、PE等。
2. 添加剂一些特殊的塑料制品可能需要添加颜色、增强剂、阻燃剂等添加剂,以满足产品的特殊需求。
注塑培训资料
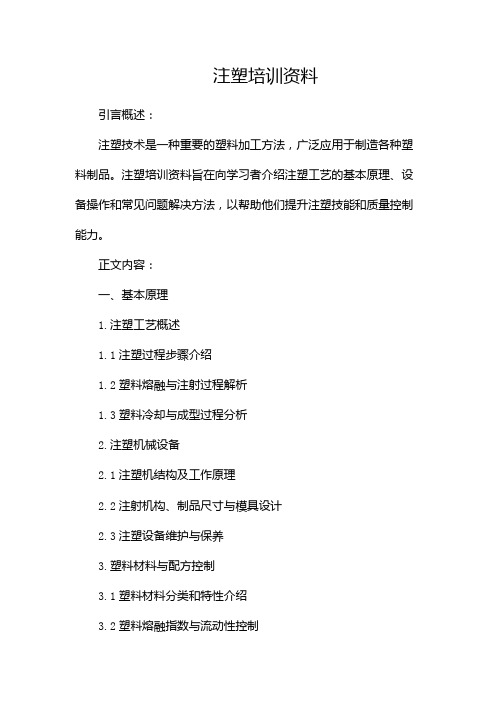
注塑培训资料引言概述:注塑技术是一种重要的塑料加工方法,广泛应用于制造各种塑料制品。
注塑培训资料旨在向学习者介绍注塑工艺的基本原理、设备操作和常见问题解决方法,以帮助他们提升注塑技能和质量控制能力。
正文内容:一、基本原理1.注塑工艺概述1.1注塑过程步骤介绍1.2塑料熔融与注射过程解析1.3塑料冷却与成型过程分析2.注塑机械设备2.1注塑机结构及工作原理2.2注射机构、制品尺寸与模具设计2.3注塑设备维护与保养3.塑料材料与配方控制3.1塑料材料分类和特性介绍3.2塑料熔融指数与流动性控制3.3配方设计及其对制品质量的影响二、设备操作1.注塑模具安装与调试1.1模具安装的步骤和注意事项1.2模具调试的原则和方法2.注塑机操作技巧2.1注塑机开机前的准备工作2.2注塑机操作面板及参数设置2.3操作中的常见问题及解决方法3.温度和压力控制3.1注塑过程中温度的控制与意义3.2注塑过程中流道压力的控制与优化3.3温度和压力异常的判断和处理三、质量控制1.注塑制品缺陷与分析1.1常见的注塑制品缺陷类型1.2缺陷产生的原因与分析方法1.3预防和解决制品缺陷的措施2.注塑制品检测与测试2.1检测设备与方法概述2.2注塑制品物理性能测试2.3检测结果分析及质量控制措施3.注塑工艺参数的优化3.1注塑工艺参数的选择和调整3.2工艺参数优化的试验方法与流程3.3注塑工艺参数优化的实例和经验总结四、安全与环保1.注塑操作的安全措施1.1注塑设备安全使用规范1.2塑料材料储存和处理的安全注意事项1.3紧急事故处理与应急措施2.注塑过程的环保问题2.1废水、废气、废渣的处理与回收利用2.2资源节约和能耗优化措施五、未来发展趋势1.自动化与智能化1.1注塑生产线自动化控制1.2智能注塑机的应用前景2.环保和可持续发展2.1生物降解塑料的应用前景2.2注塑技术对环境的影响与改进方向3.新材料和新工艺3.1高性能塑料的研发和应用3.2先进注塑工艺的研究与实践总结:注塑培训资料涵盖了注塑技术的基本原理、设备操作、质量控制、安全与环保以及未来发展趋势等重要内容。
注塑工艺流程及原理
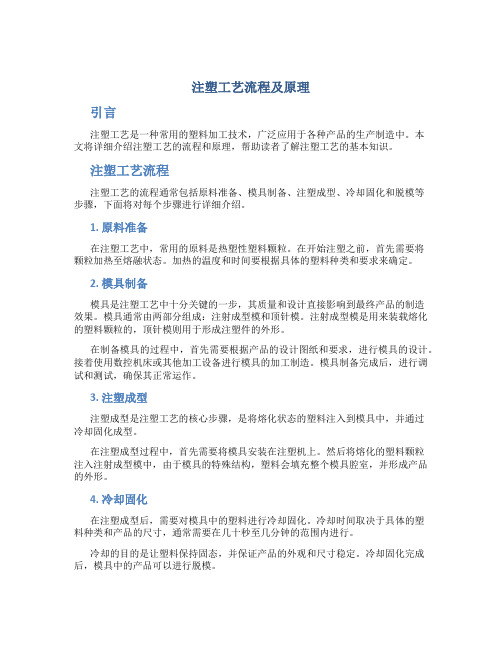
注塑工艺流程及原理引言注塑工艺是一种常用的塑料加工技术,广泛应用于各种产品的生产制造中。
本文将详细介绍注塑工艺的流程和原理,帮助读者了解注塑工艺的基本知识。
注塑工艺流程注塑工艺的流程通常包括原料准备、模具制备、注塑成型、冷却固化和脱模等步骤,下面将对每个步骤进行详细介绍。
1. 原料准备在注塑工艺中,常用的原料是热塑性塑料颗粒。
在开始注塑之前,首先需要将颗粒加热至熔融状态。
加热的温度和时间要根据具体的塑料种类和要求来确定。
2. 模具制备模具是注塑工艺中十分关键的一步,其质量和设计直接影响到最终产品的制造效果。
模具通常由两部分组成:注射成型模和顶针模。
注射成型模是用来装载熔化的塑料颗粒的,顶针模则用于形成注塑件的外形。
在制备模具的过程中,首先需要根据产品的设计图纸和要求,进行模具的设计。
接着使用数控机床或其他加工设备进行模具的加工制造。
模具制备完成后,进行调试和测试,确保其正常运作。
3. 注塑成型注塑成型是注塑工艺的核心步骤,是将熔化状态的塑料注入到模具中,并通过冷却固化成型。
在注塑成型过程中,首先需要将模具安装在注塑机上。
然后将熔化的塑料颗粒注入注射成型模中,由于模具的特殊结构,塑料会填充整个模具腔室,并形成产品的外形。
4. 冷却固化在注塑成型后,需要对模具中的塑料进行冷却固化。
冷却时间取决于具体的塑料种类和产品的尺寸,通常需要在几十秒至几分钟的范围内进行。
冷却的目的是让塑料保持固态,并保证产品的外观和尺寸稳定。
冷却固化完成后,模具中的产品可以进行脱模。
5. 脱模脱模是将固化的产品从模具中取出的过程。
在脱模之前,需要确保产品已经完全固化,并且模具中没有残留的塑料。
脱模的方法有很多种,可以使用顶针、顶板和冷却气体等设备将产品从模具中推出。
脱模后,就得到了最终的注塑产品。
注塑工艺原理注塑工艺的原理主要涉及到塑料的熔融、充模、冷却和固化过程。
首先,塑料颗粒在加热的作用下熔化成为可流动的熔融状态,这是塑料注塑成型的基础。
注塑工艺基础知识

Page 7
注塑设备—注塑机的组成结构
一台通用注塑机主要由塑化注射系统、合模机构、液压传动(或气动)装置、电器控制 系统等组成,如图所示:
Page 8
注塑设备—注塑机的组成结构
塑化注射系统 塑化注射系统的主要作用是使塑料加热塑化和熔融, 并能以足够的压力和速度下将一定量的溶料注入模具型腔中。塑化注射系 统主要由塑化部件(螺杆、机筒、喷嘴等组成)、料斗、计量装置、传动 装置、注射油缸、注射座整体移动油缸等组成。
注塑工艺基础知识
提纲
一、注塑工艺简介 二、注塑设备 三、注塑工艺过程 四、注塑制品的设计要点
Page 2
注塑工艺简介
各种各样的塑料制品是怎么制成的呢?塑料的主要成型方法 有挤出成型、注塑成型、吹塑成型、压延成型、浇铸成形等,其 中注射成型因形状适应性广,是热塑性塑料成型主要工艺。
注塑也称注射成型或注射模塑,是用注塑机将塑料粒子或塑 料粉的原料熔融后,施加压力使其注入温度较低的模具内冷却固 化形成与模腔形状一致的塑料制品的加工过程。
Page 6
注塑设备—注塑机分类
近年来注塑机发展很快,类型不断增加,分类的方法也较多。有的按塑料塑化 方式分为柱塞式和螺杆式;有的按锁模装置的传动方式分为液压式、机械式和液压 机械式;也有按机器操作方式分为自动、半自动和手动等,至今尚未完全形成统一 的分灯方法,目前使用较多的分类方法有以下几种:
注塑工艺入门知识点总结

注塑工艺入门知识点总结注塑工艺的原理是将塑料颗粒加热熔化后,通过一定的压力将熔化的塑料注入模具中,经冷却后形成制品。
在注塑工艺中,需要控制材料的温度、压力、流动速度等参数,以确保最终制品的质量。
本文将介绍注塑工艺的一些基础知识点,包括工艺流程、模具设计、材料选择、设备选型等方面的内容。
一、注塑工艺的基本工艺流程1. 配料:将塑料颗粒按照一定的配比放入料斗中,通过螺杆机械运动将塑料颗粒送入加热筒内,进行熔化加工。
2. 注射:熔化后的塑料通过螺杆的旋转被注入模具腔内,填充模具腔部形成制品的外形。
3. 压模:将注射机中的注射头封堵,同时施加一定的压力,使熔化的塑料得以冷却固化,形成最终的制品。
4. 开模:打开模具,取出成品,模具回到注射动作前的起始位置,为下一循环注射做准备。
以上是注塑工艺的基本工艺流程,整个过程需要通过控制注射机的温度、压力、速度等参数来保证最终制品的质量。
二、注塑模具设计1. 模具结构设计:注塑模具结构通常包括模具座、模具腔、射出系统、顶针机构、顶出机构、冷却系统等部分。
不同的制品形状、尺寸、要求等会影响模具的设计。
2. 模具材料选择:模具材料需要具有高硬度、高耐磨性、高热导率、高强度等特点。
常用的模具材料有P20钢、718钢、H13钢等。
3. 模具制造工艺:模具的制造需要经过雕模、车削、磨削、电火花、组装等一系列工艺流程,要求精密度高。
三、注塑材料选择1. 热塑性塑料:包括聚乙烯(PE)、聚丙烯(PP)、聚氯乙烯(PVC)、聚苯乙烯(PS)、聚碳酸酯(PC)等。
热塑性塑料的特点是可以多次加热冷却,具有良好的可塑性和加工性。
2. 热固性塑料:包括酚醛树脂、环氧树脂、酚醛树脂、酚醛树脂等。
热固性塑料在熔化后会固化,不可再次加工。
常用于制品要求高强度和耐腐蚀的场合。
四、注塑设备选型1. 注射机:注射机的型号和规格要根据制品的尺寸、材料、生产流程等方面的要求来选择。
一般包括注射量、射击力、螺杆直径、射出速度等参数。
塑料注塑成型工艺基本知识

塑料制品的尺寸精度影响因素
• 6) 填料影响:塑料材料进行增强或无机填充改性后,可提高塑料制品的尺寸精度 。
五、热塑性塑料注塑成型工艺
• 塑料注塑加工过程流程 :
…成型前的准备 加料 塑化 注射入模 保压冷却 脱模 (修整) (后处理 ) …
• 成型前的准备
• 1、原料或嵌件预处理
(并非所有原料或嵌件都需要进行预处理——干燥、预热,视产品技术要求程度、 原材料品种、气温状况而定,对于金属嵌件,在冬季一般都需要预热处理。)
• 成型前的准备
• 2—料筒清洗注意: • 在改变原料品种,或调换颜色时,必须对料筒进行清洗,清洗后
的料应做好标识。严禁误用!! • 被清洗料为*PC ,不得用ABS或PA ; • 被清洗料为POM ,不得接触PVC ;
• 注塑成型过程(加料 、塑化、注射入模 、保压冷却 、脱模、(修整))
• 关注:
脱模剂 使用应注意!!!
• 所选脱模剂品种是否合适。(不能对产品有浸蚀) • 对产品表面要喷油漆的零件,严禁使用脱模剂;
注塑过程(工艺)参数应关注:
工艺参数:
• 注塑量 • 注塑料筒各段温度 • 各级注塑压力、塑化时背压、保压压力 • 各级注塑速度 • 注塑时间、保压时间、冷却时间 • 模具温度 • 使用回头料情况
• 注射成型(或注塑成型或注射模塑):
将粒状或粉状塑料从注射机的料斗送进加热的料筒,经加热熔化呈流动状后,由柱塞或螺杆的 推动而通过料筒端部的喷嘴并注入温度较低的闭合模具中,充满塑模的熔料在受压的情况况下,经 冷却因化后即可保持塑模型腔所赋予的形样。
二、塑料成型方法
• 注射成型(*) • 挤出成型:如管材类产品、型材类产品(建材用)… • 吹塑成型:如油箱、加注管、民用油/水壶… • 热成型(真空吸塑成型) :如轿车塑料地垫、防水帘等 • 浇铸成型:如方向盘、仪表板 • 压延与涂层:如人造革 • 烧结成型:主要PTFE制品 • 搪塑成型:如玩具类产品,车门扶手表皮 • 模压成型:(板材) • ……
- 1、下载文档前请自行甄别文档内容的完整性,平台不提供额外的编辑、内容补充、找答案等附加服务。
- 2、"仅部分预览"的文档,不可在线预览部分如存在完整性等问题,可反馈申请退款(可完整预览的文档不适用该条件!)。
- 3、如文档侵犯您的权益,请联系客服反馈,我们会尽快为您处理(人工客服工作时间:9:00-18:30)。
a) 塑化壓力(背壓)●保證螺杆在旋轉覆位時增加塑化壓力使熔膠的溫度均勻及把揮發性氣体包括空氣排出射料缸外.●把附加劑(如: 色粉. 色種. 擴散劑等)與熔膠均勻地混合起來●提供均勻穩定的塑化熔膠以便保證塑件重量穩定.●在保證塑件質量的情況下盡可能低以免徙耗損材料●背壓的大小調節視膠料不同而異, 一般不超過20KG/CM2(具体各膠料背壓值可參見本工藝資料第一部分有關內容)b) 注射壓力●克服塑料熔体從料筒流向型腔的滯阻力, 給予充模壓力及對充入的熔料進行壓質.●對于流動性差的塑料, 注射壓力要取大, 對于型腔阻力大的薄壁膠料, 注射壓力也要取大.(3) 時間參數(成型周期)充模時間注射時間保壓時間總冷卻時間成型周期閉模冷卻時間其它時間(如: 開模. 脫模. 噴脫劑等)●注射時間和冷卻時間是基本組成部分, 其多少對啤塑件的品質有決定性的影響.●充模時間一般不超過10S●保壓時間較長, 與膠件臂厚有關(厚壁取長時間), 以保證最小收縮.●冷卻時間取決于塑料結晶性, 制品料厚, 模具溫度等因素視具体情形調整.(4) 注射速度●注射速度通過調節單位時間內向注射油缸供油多少來實現.●一般說來(在不引負作用的前提下)盡量使用高射速充模, 以保證塑件熔接強度及表現質量, 而相對低的壓力也使塑件內應力減小提高了強度.●采用高壓低速進料的情況可使流速平穩, 剪切速度小, 塑件尺寸穩定, 避免縮水缺陷.二. 塑膠模的基本認識塑膠模具是注射成型生產中賦予塑料形狀所用部件的組合体, 塑模的結構視塑料性質. 制件形狀. 結構以及注射機的不同等因素而可能形式. 大小差異很大, 然而其基本結構大致相同, 即主要由澆注系統. 成型零件. 結構零件.三大部分組成. 其中澆注系統與成型零件是塑料直接接触的部分, 並隨塑料制品而變化, 它是模具中最重要. 最複雜. 變化最大. 要求表面精度及光潔度最高的部分.** 澆注系統&成型零件澆注系統指塑料從噴嘴進入型腔的流道部分, 包括:主流道. 冷料穴. 分流道和澆口等.成型零件指構成成品形狀的各零件, 包括: 動. 靜模型腔. 型芯. 排氣槽. (成型)頂針等.** 典型的模具結構典型的模具結構包括以下幾個主要部分:1. 主流道:是模具連接注射機噴嘴通至型腔或分流道的一段, 主流道進口頂部呈凹形, 以便與噴嘴連接. 主流道進口直徑應略大于噴嘴直徑(0.8mm)以免溢料並防止兩者連接不準而發生堵截. 進口直徑根據制品大小而定, 一般為ψ4-8mm主流道直徑應向內擴大, 呈3-5°角度, 以便流道順利出模.2. 分流道: 在多型腔模中連接主流道和各個型腔的通道. 為使熔料能等速度地充滿各型腔, 分流道在模里的排列應盡可能等距` 對稱, 而分流道的截面積形狀` 尺寸對熔料的流動有很大影響, 且對脫模` 造模的難易都有影響. 常用的分流道截面形狀是梯形或半圓形而且是開在帶有脫模杆的半模上. 流道的表面必須拋光以減小流動阻力而提供較快速度充模, 流道的尺寸決定于塑料品種, 制品尺寸及壁厚(具体參見有關資料數據)在滿足成型要求的前提下應盡量減少截面積, 以免增加水口料的比例及使冷卻時間增加, 降低了生產效率.3. 冷料位: 設在主流道末端的空穴, 用來容納噴嘴兩次注射之間所產生的冷料, 從而防止分流道或水口堵塞. 如果冷料進入型腔則會導致制件內應力加大或機械強度不足, 冷料位尺寸一般為ψ3-10mm, 深度6mm左右, 為便于脫模(拉出水口), 其底部通常都是拉料杆位(脫模杆), 拉料杆的頭部通常都設計成下凹陷或帶有溝槽形成, 便于拉出主流道連整個流道系統.4. 澆口(入水口)是熔料通過直` 分流道后進入型腔的通道, 澆口的截面積通常是整個流道系統中截面積最小的部分.內澆口的尺寸形狀對制件的質量影響很大, 其主要的作用可列述以下幾點:1) 控制料流速度2) 成型中水口位早凝結可防其倒流3) 使料通過時產生較高的剪切力使料溫提升, 從而降低其表面粘度, 提高其流動性.4) 便于制件與流道分離澆口的形狀尺寸和位置設計都須根據塑料品種, 制件結構和形狀等具体情況做出選擇, 一般來說, 澆口的位置都是開在制件厚壁位(以利補縮)及不影響外觀的位置.澆口尺寸設計應考慮熔体的性質.三. 型腔是制件在模具中成型的部分, 用來構成型腔的零件稱為成型零件, 一般包含以下:凹模------構成制件外形的成型零件凸模/型芯------構成制件內部形狀, 如: 溝` 孔` 槽等由于熔体進入型腔后產生很高的壓力, 故對成型零件的材料強度` 剛度要求較高,且材料應具耐腐蝕性. 成型零件一般都經過熱處理提高硬度.注: 常用于塑膠模的鋼材有: 718. S-136.而合金模具是用熱作鋼8407.四. 排氣位開設在模具內的槽形排氣位, 防止熔料進入型腔時卷入氣体. 當熔料進入型腔時原存入型腔的空氣及熔料帶入的氣体必須在料流的盡頭通過排氣槽向外排出, 如排出不完全, 則可能會造成件帶氣孔, 熔接痕, 充模料不齊, 甚至困入高溫壓縮空氣而燒傷膠件的情況出現.一般情況下, 排氣孔既可開設在型腔內熔料流動的盡端, 也可開設在模具的分模面上.(在凹模上開一般0.03-0.06mm深, 1.5-6.0mm寬的槽)注射件排氣孔是不會有很多熔料滲(迫)出的, 因為熔料會在該處冷卻固化而自動將通道堵死. 此外, 實際應用中亦可利用頂出杆與頂出孔配合間隙, 頂塊和脫模皮與型芯的配合間隙來排氣.(附件一)●鎖模力太小, 換用大機●機器鎖模力不穩定c) 檢查模具●外來物粘附于分型面, 致鎖模不密合.●模具物料配合不準, 針對性檢修.多型腔模需調整分流道及澆口尺寸以平衡壓力.三. 氣泡(BUBBLES)如果熔膠中含有氣体(揮發物質)那麼熔膠去除壓力后會在塑件中留下氣泡.** 改善指引a) 檢討成型工藝●提高注射壓力●將注射速度降低●降低料筒溫度(特別是后段的)●增加背壓, 並适當調低螺杆轉速, 防止透入空氣量增多●注射熔膠量不足, 需适當增加b) 檢查模具●增加澆口尺寸, 防止材料在澆口處過早固化●增加排氣槽或加深現有排氣槽, 改善型腔排氣●模具上澆口位置開設不合理, 致膠料流不均, 有空氣困于其中●檢查運水情況是否使模溫不均並改善, 模溫不能過低●加粗流道●制件厚壁薄壁的轉角處圓滑過渡, 避免膠料流速變化過大裹入空氣●塑件壁過厚: 改模將原料處偷空減薄c) 檢查膠料主要是干燥問題, 要保證充分干燥及避免在成型前回潮四. 縮水痕(SINK MARKS)通常表現為塑件表面收縮缺料所致凹痕** 改善指引a) 檢討成型工藝●溫度太高或過低, 都會使保壓補縮達不到效果●适當增加冷卻時間, 減少熱收縮●膠料射入量不足: 增加射膠量●增加注射壓力和速度b) 檢查注塑模●螺杆磨損, 注射保壓時熔料漏流●增加加料量, 保留一定緩沖區以發揮保壓作用●減小加料量, 減小緩沖墊厚度, 使注射壓力不過份消耗而發揮作用c) 檢查模具●模具溫度太高使膠料冷凝太慢●模具溫度太低使膠料沖填不完全●模上局部高溫區: 改善冷卻水布置●适當加大澆口以增加進膠量●增大縮短流道/注口, 減少壓力損失, 使料流順●通過改變澆口位置及流道粗細, 必要時增加多澆口●如可能將件厚處改模偷空減小厚壁料位收縮差異五. 熔接痕(POOR WELD LINE)產生在塑件表面的冷料熔接的痕線.** 改善指引a) 檢討成型工藝●增加熔膠溫度及噴嘴溫度●适當增加背壓力及調整螺杆轉速以獲得更高的均勻的熔膠溫度●有效型腔壓太低: 增加注射壓力, 增加螺杆向前時間●增加注射速度b) 檢查模具●使用了過多的清潔劑: 省模或對模做其它處理, 盡可能不用脫模劑●模具表面太冷 : 增高模溫, 限制冷卻液速度●模內排氣不足 : 在熔接區加排氣孔或增大排氣孔尺寸●澆口` 流道太小 : 增加澆口尺寸, 增大流道直徑●澆口離熔接區太遠 : 改變澆口位置或增加輔助澆口●塑件在熔接區部位太薄: 改模加厚料c) 檢查塑料●保證原料干燥良好, 以改善其流動性六. 銀條紋(SILVER STREAKS)由于氣泡及充填過程中沿拉應力的垂直方向產生應力集中點使塑件對外呈現銀現象.** 改善指引.a) 檢討成型工藝●熔膠溫度太高至揮發物過多: 降低料筒溫度(尤其是后端溫度)●也可能熔膠溫度太低至充填不穩定, 內應力增大: 相應增高料溫及噴嘴溫度●可能膠料滯留在料筒內時間過長, 需減短總周期時間●增加或減小射膠速度●适當調低注射壓力●适當增高背壓(如過高需調低)及減小螺杆轉速b) 檢查注射機●是否溫度控制器不精確, 控制有差異.●清理噴嘴部位有可能堵塞●減小螺杆蓄壓段距離c) 檢查模具●模表面溫度太低, 增高模溫(限制冷卻劑流量` 流速)●檢查澆口及流道是否有堵塞情況, 如有需增加澆口深度和流道直徑●模具表面過多脫模劑: 限制脫模劑使用, 或轉用無硅型脫模劑●成型檢查是否有油` 水泄漏致模腔物料受污染●檢查排氣情況要保持良好, 必要時加深或增加排氣d) 檢查膠料●要保證原料的充分干燥, 清除水份●膠料已被(其它種料)污染, 糾正改善. 另外, 需徹底將料筒清洗干淨後再使用潔淨料生產.●原料中(水口)細粉末過多或是多次回料導玫在料筒中易降解, 需過篩清除及控制多次回料加入量.* 註: 對成品塑件可試用退火方法消除銀紋: 對PS類, 78℃保持15分鍾對PC類, 160℃以上保持數分鍾七. 空洞(VOLDS)塑件料截面出現的空心孔(如是透明件清晰可見), 常因材料收縮所致.** 改善指引:a) 檢討成型工藝●增加注射量●增加注射壓力●增加保壓時間及适當增加射膠時間●降低溶液溫度●降低或增加注射速度(例如: 對非結晶性料要增加速度)●增加料溫使流動暢及降低料溫減小收縮(視情形而調節)●縮短塑件在模內冷卻時間, 必要時投入熱水緩冷b) 檢查模具●适當提高模溫, 特別是形成“真空泡”位的局部模溫●將模具澆口開設在塑件厚壁位, 檢討改善流道. 澆口流動情況, 必要時將其加粗加大.●改善模腔排氣* 可參見“3.氣泡(BUBBLE)”部分八. 彎曲彎形(WARPAGE DISTORTION)塑件形狀與型腔相似, 但呈現彎曲或彎形.** 改善指引:a) 檢討成型工藝●增加冷卻時間●調整注射壓力, 減小螺杆向前時間●在保證充料情況下, 減小螺杆轉速和背壓, 降低料密度●料溫太高或太低: 根據具体情況調整(流動性差的塑料溫度不可調低)●頂出塑件時要緩慢●出模后借助夾具定型在水中快速冷卻b) 檢查模具●增加模具冷卻能力, 使冷卻液速度加快, 將模溫降低(以增硬塑件外表面)●塑件不均勻的收縮導致變形: 檢討件的設計及運水分布情況並修正●澆口位置是否開在最厚位處●增大澆口尺寸及流道尺寸且盡可能使流道粗而短, 減少成型取向性●檢查是否型芯` 型腔偏移導致壁厚變化引起變形●模內有倒扣, 導致出模時變形, 改善方法是減少倒扣深度及在任何可能處增加轉角R及省滑模具●頂針太小, 數量太少或分布不合理, 這些都會使頂出不平衡, 針對性做改善●改善排氣, 減小塑件內應力不平衡程度●在設計上的可能位增加加強筋.●調整模溫: 厚壁位強水冷, 偏遠薄壁位應提高溫度, 以使整件收縮均勻, 減小內應力c) 檢查膠料●結晶性塑料變縮率普遍偏大, 易產生應力變形九. 困氣燒痕(TRAPPED GAS BURN MARKS)表現為塑件表部變色(從黃到黑)通常出現在塑流道尾處和空氣壓縮地帶.** 改善指引a) 檢討成型工藝●膠料過熱, 降低熔液溫度●降低注射速度, 太快使氣体不易排出●降低背壓, 減小螺杆轉速●鎖模力過度, 在不致披鋒情況下稍降低●材料在料筒內滯留時間過長, 需減少總循環時間b) 檢查模具●檢查並清潔排氣位, 並在燃燒痕處加多加深排氣位●澆口太小: 增加澆口深度, 寬度c) 檢查材料●必須保證徹底干燥去除水份十. 黑褐斑點(BLACK—BROWN SPECKS)注塑件呈現黑色` 褐色` 濃淡的斑或條紋, 塑件染色無根本變化.** 改善指引:a) 檢討成型工藝●降低熔液溫度(特別是后料筒區), 避免過熱●注射速度過快引致過度剪切●調低注射壓力●減少冷卻時間b) 檢查注射機●膠料困于炮筒裝置的“死角”或不流動區, 使它在高溫下停留時間過久: 將筒和螺杆拆下來徹底清潔與聚合物接触的表面c) 檢查模具●澆口過小, 增大澆口尺寸●塑件壁部分太窄, 材料在高壓下流過時產生衰變, 需檢查修正, 保持壁厚的正確性和一致性d) 檢查膠料●材料中混入的熱敏感的其它已多次回用的膠料, 檢查來源, 清除雜質十一.脆弱性(BRITTLE NESS)表現為注塑件在頂出時斷裂, 或在出模后易斷裂.** 改善指引:a) 檢討成型工藝●熔膠溫度太低: 增加料筒(后區)溫度及噴嘴溫度●熔膠溫度過高致膠料降解, 需降低各區域料筒溫度以及調低背壓力, 降低螺杆轉速.●增加注射速度, 保證熔合強度b) 檢查模具●增加模溫, 限制冷卻劑循環速度●流道和澆口過小, 注射中過度剪切, 需加粗加大流道及澆口c) 檢查膠料●塑件內應力過大沒釋放出來, 需進行退火處理(如尼龍件浸熱水)●水口料過多, 或多次回用雜料的使用, 需通過試驗控制用量●異類膠料混入(熔點低的), 查明改善並將料筒徹底洗淨●模內膠料過度充填: 減低注射量, 減低注射壓力及注射速度●料溫過高需适當調低●保壓時間過長:減少螺杆向前時間●增加冷卻時間或縮短冷卻時間(視型腔或型芯粘模而不同)●在允許的情況下借助脫模劑脫模b) 檢查模具●模具表面刮傷` 擦花等, 需做拋光處理●模內出模角不夠: 改模加大●設計有不合理的倒扣●高度拋光的模面會使塑件在真空負壓作用下難以出模●頂出機構不适當, 如頂出面不足等十三. 尺寸差異(DIMENSIONAL VARISTIONS)注塑件尺寸變化超過允許範圍** 改善指引a) 檢討成型工藝●注射壓力低: 提高注射壓力●适當增加射膠時間及保壓時間●料筒溫度/ 噴嘴溫度過高, 相應調整●模型充填太慢: 增加注射速度/ 采用多級充填速度b) 檢查注塑機●不同機種的注塑機所致成型工藝條件的差別●螺杆轉速, 停止動作不穩定●不穩定的注射壓力: 如檢查是否每次循環都有恒定的熔膠緩沖, 返回塑流閥是否泄漏等, 相應修理或更換●熔料溫度波動: 檢查熱電偶及溫度控制器是否出現故障c) 檢查模具●水料回用時注意篩去細粉末不用十四. 碎裂(CRAZING)注塑件表面有細小裂紋或裂縫** 改善指引:a) 檢討成型工藝●調整注射壓力: 升高壓力, 使充模順暢, 降低粘度過高壓力致內應力大易開裂, 故需降低.●調整料筒溫度: 過高溫度, 使料降解過低溫度, 使熔接位強度不足●适當增大射膠速度●适當提高模溫, 減小分子取向性●降低背壓及調低螺杆轉速, 避免膠料降解●冷卻時間太短, 未充分硬化, 頂出時發白或開裂b) 檢查注塑機●機器的塑化能力不足(塑化容量小, 不充分), 需換用大機器c) 檢查模具●增加頂針直徑, 降低頂針頂出速度●頂針油傳到模腔表面, 檢修模具●型腔或型芯內漏水, 檢查是否模有細裂痕, 或是“0”封閉環不良引起漏水●澆口過大使塑件過分受壓: 減小澆口尺寸●塑件設計過于單薄, 需增加加強筋●檢查型腔. 型芯是否足夠脫模斜度●模具排氣不良, 易形成夾水紋使強度下降d) 檢查膠料●原料被污染: 查明原因作出控制●過多的水口料加入: 用試驗結果確定适宜的加入量●保證充分的干燥去除水份十五.表面粗糙(MATT PATCHES)塑件表面精度不一, 有些部分比其它部分有光澤** 改善指引:a) 檢討成型工藝●增加噴嘴溫度●增加熔膠溫度(檢查是否料筒加熱帶混亂失調, 局部過熱或過冷)●可能填充過快過度剪切: 适當調低注射速度●增加射出壓力●廷長射料時間●背壓不足, 熔料疏松並帶有氣体b) 檢查注塑機●檢查噴嘴處有否滴漏有冷膠c) 檢查模具●增大或增加冷料穴收集冷料●模表面質量不良, 拋光改善並檢查是否有運水泄漏●提高模溫●料流在模型內突然轉變: 模內避免尖利邊緣, 盡可能用圓角過度●型腔內的噴射痕: 增大澆口或用薄片形澆口入水●在表面光澤差的部位加排氣位改善●使用脫模劑的影響: 停止使用脫模劑d) 檢查膠料●摻入水口料過多, 或多次回用料降解十六. 顏色分布差(POOR COLOR DISPERSION)塑件顏色不一致, 局部有濃淡差別或有條紋, 斑塊形狀出現 ** 改善指引:a) 檢討成型工藝●增加背壓, 降低料筒溫度以使色料混合充分●嚴格限定生產工藝參數: 特別是不可隨便變更料溫及生產周期b) 檢查膠料●混料不均勻●新料與水口料配比的差異●色粉擴散不良, 加入擴散劑改善附件二常用塑膠材料干燥條件塑料焗料溫度(℃)焗料時間(HRS) ABS80--903--4POM90--1001--2PMMA80--902--3707--8離子交換聚合物SURLYNNYLON80--904--5PC1203--4SAN80--903--4PBT120--1302--3熱塑性彈体90--1002--3 TPE(HYTREL)702--3熱塑性橡膠TPR(SANTOPRENE)80--902--3聚氨酯PUR附件三塑料著色性比較塑料名稱顏色透明狀況可染色種類熱穩定性遷移性PE白半透明半透明. 珠光. 不透明穩定易PP白半透明半透明. 珠光. 不透明穩定易GPPS無色透明透明. 半透明. 珠光. 不透明穩定無HIPS白不透明不透明穩定無AS(SAN)無色透明透明. 半透明. 不透明不穩定無ABS微黃色不透明不透明易變色無MBS無色至微黃透明透明. 不透明穩定無PMMA無色透明透明. 半透明. 珠光. 不透明穩定無PC無色至微黃透明透明. 半透明. 不透明穩定無PA白色至微黃半半透明至不透明半透明. 不透明穩定無POM白色至微黃不透明不透明穩定無PBT白色不透明不透明穩定無PVC白色透明透明. 半透明. 珠光. 不透明易變色易*** 塑料著色時注意的幾個問題:1.PE. PP. PVC. GPPS. PMMA. SAN. PC. PBT染不透明色時需加入鈦白粉.2.PVC. GPPS. SAN. PMMA. PC染透明或珠光色時不得加入鈦白粉. 鋅鋇白或其它無機物.3.需注意多種色劑用于PE. PP. PVC時會發生不同程度的遷移現象, 選用時注意.4.由于ABS. SAN類中有A(丙烯睛)組份, 而氰基(-CN)會引起著色不理想(色不穩定, 不夠鮮艷), 另一方面, A組份會使熔体粘度增大, 摩擦剪切熱較多, 所以對色劑的耐熱性要求較高.5.PMMA及PC因含有酯基而易水解, 故混色后在成型前須徹底結予干燥.6.PA中含有極性很強的胺基, 吸水性強, 故混色后在成型前亦必須徹底進行烘焗.7.因PVC(尤其是軟PVC)中含有大量的增塑劑. 熱穩定劑等添加劑會使著色鮮艷性差, 而且添加劑的析出易使色劑滲出發生遷移現象. 另外, PVC在高溫下分解出的氯化氫(HCL)也會使色劑顏色發生變化.。