VW01105-4_En_042001
VW_01105-1_电阻焊大众电焊标准中文版综述

草案 VW 011 05-1:2006-01 1适用范围下面的这些基本规则以从较低到高的机械化程度的经验、试验结果以及公开的标准和技术框架,例如 DVS-规则 2902-1、 -2、 -3作为基础。
本标准用于承受静态和动态应变的电阻点焊的钢板材结构的结构设计、计算和实施,以下称为“点焊连接”。
本标准的应用范围包括:板材厚度比≦ 5 : 1的,板材厚度范围从 0.5 至 4 mm的单边切口点焊连接的电阻点焊(根据 DIN EN ISO 4063,系数为 21,以及单点连接和多点连接的质量特征。
更大厚度比和厚度的焊接应取得技术部门的同意也可实施。
在板材厚度比较大时,熔核的直径一直由比较薄的钢板来决定。
依据 DIN EN 10139标准的钢板的最大可焊厚度应为 3.0 mm 。
镀锌板,比如依据 DIN EN 10142或者 DIN EN 10292标准,和高硬度及超高硬度的钢铁,必须使用较大的电极头和电极轴直径(16 mm或 20 mm。
在使用该电极时,有角度的点焊法兰处的焊接熔核将进一步远离焊接板。
然而,随着熔核与焊接板间距离的增大,工件的刚度和强度将降低。
(电阻点焊连接的其它要求包括:— VW 011 05-2铝材,— VW 011 05-4多板连接;两层或多层点焊连接。
对于焊点的质量 -Audit(奥迪特已在 PV 6702和 PV 6717检验标准中的流程中给出。
2定义2.1点焊电阻焊接时,待连接的部件中间的焊接区域将被电阻产生的热量和同时施加的电极力加热到可熔化状态。
被熔化的母材的大小,形状和位置取决于在焊接区域和其相邻区域所产生的和导走的热量在时间和空间上的相互作用。
在电极力的作用下,工件在熔化物凝固时被互相连接在一起。
在这过程中以点状,更确切的说是核状物所产生的熔核焊接连接被称为点焊(图 27,其将部件在焊接冲击区域统一起来(图6。
熔化材料在连接面上的磨片上所测得的直径被称为熔核直径。
2.2热影响区域 WEZ焊接过程中固定保留的母材,由于点焊带来的热能的影响而产生组织变化的区域。
VW60424_DE_2005-10-01

Seite 2VW 604 24: 2005-10Tabelle 1 – GewindeendenNr. Form Bild/Beispiel Bemerkung1 PF ZapfenNicht für NeukonstruktionenVerwende DIN EN IS O 4753 Form TC oderForm W1)+ Ausrichten der Schrauben+ Bedingtes Finden des Innengewindes+ Preisgünstiger als Formen W, AV, V und TC- zusätzliches Gewicht- Sortenvielfalt 2 WAnsatzspitze lang Vorzugsform 1)+ Finden des Mutterngewindes+ Ausrichten der Schrauben+Bevorzugt bei automatischer Montage bzw. nicht einsehbarer Handmontage - Reduzierung der Einschraubtiefe - zusätzliches Gewicht - teurer als Form TC, PF, K3 VAnsatzspitze kurz Nicht für NeukonstruktionenVerwende Form TC oder Form W1)+ Finden des Mutterngewindes - Teurer als Form TC und W - Reduzierung der Einschraubtiefe - zusätzliches Gewicht4 AVAnsatzspitzemittellang Nicht für NeukonstruktionenVerwende Form TC oder Form W1)+ Finden des Mutterngewindes - Teurer als Form TC und W - Reduzierung der Einschraubtiefe - zusätzliches Gewicht5 KKegelkuppeähnlichDIN EN ISO4753-CHDie Geometrie der Kegelkuppe CH nach DIN EN ISO 4753 ist nicht ausreichend, da im Extremfall keine Fase möglich ist (Ansetzen der Schraube kritisch).Seite 3VW 604 24: 2005-10Tabelle 1 – Gewindeenden (fortgesetzt)Nr. FormBild/Beispiel Bemerkung 6 GFNGewindefurchend(normal) Vorzugsform Beschrieben wird dieser Typ in DIN 267-30, jedoch Festigkeitsklasse 8.8 für Leichtmetall bis 120 HV zulässig7 CF Gewindefurchend(Corflex ®)Gewindeende Induktiv gehärtet (450+150) HVa = Übergangsbereich der Härtezoneein vollausgeformter Gewindegang mussmindestens gehärtet seinmax. 2 x P bei Schraubenlänge = 2 x d 1max. 3 x P bei Schraubenlänge > 2 x d 1b = Furchbereich Härtezone (2 bis 4) x PLochdurchmesser siehe DIN 7500-2 8 ET Gewindefurchend (Extrude-Tite)Gewindeende Induktiv gehärtet (450+150) HVFür Bleche bis 1,5 mm Dicke und Härtemax. 180 HVLochdurchmesser siehe DIN 7500-2Bei Verschraubungen mit diesen Schraubenwird Material nach oben und unten gedrückt,wodurch eine zusätzliche Gewindeüberdeckungerzielt wird (max. 2 x Blechdicke).Übergangsbereich der Härtezone siehe Nr. 6.9 ETLGewindefurchendlang Nicht für Neukonstruktionen Verwende Form ET Für Bleche bis 1,5 mm Dicke und Härte max. 180 HV10 ETKGewindefurchendkurz Nicht für NeukonstruktionenVerwende Form ET Für Bleche bis 1,5 mm Dicke und Härte max. 180 HV11 BSBohrspitzeGewindefurchendGewindeende Induktiv gehärtet (450+150) HV Schraube mit Bohrspitze bohrt und furcht das Gewinde in Blech mit Härte von max. 180 HV Übergangsbereich der Härtezone siehe Nr. 7.Seite 4VW 604 24: 2005-10Tabelle 1 – Gewindeenden (abgeschlossen)Nr. Form Bild/Beispiel Bemerkung12 BSSF (FDS ®) Bohrspitze Spanfrei GewindefurchendHärtezoneGewindeende Induktiv gehärtet (450+150) HVFür nicht vorgebohrte oder gestanzte Bleche bis 0,88 mmStahl mit Härte von max. 180 HV und 1,25 mm Aluminium.Beim Verschrauben dieser Schrauben wird Material nachoben und unten gedrückt, wodurch eine zusätzlicheGewindeüberdeckung erzielt wird (max. 3 x Blechdicke).Übergangsbereich der Härtezone siehe Nr. 6.Schutzrechte beachten SC SchabenutDIN EN ISO4753-CH d 1 M5M6 M8 M10 M12x1,5 l n 4-1,25-1,2 6,3-1,5 7,5-1,5 7,5-1,5 l k 2,4-13-1 3,8-1,2 4,5-1,2 4,5-1,2 d n 3,7-0,3 4,4-0,3 6-0,3 7,6-0,36 9,6-0,361) Vorteile sind mit einem “+“ und Nachteile sind mit einem “-“ gekennzeichnet2) Eindrückung zulässig3) Härtezone4) FurchbereichSeite 5VW 604 24: 2005-10Tabelle 2 – Maße und Gewindeenden (Vorzugsgrößen)Maße in mm Gewinde d1M3 M4 M5 M6 M8 M10 M12x1,5 M14x1,5 M16x1,5 M18x1,5 Steigung P 0,5 0,7 0,8 1 1,25 1,5 1,5 1,5 1,5 1,5 Nennlänge l1siehe ProduktnormenNennmaß - 2,9 3,8 4,5 6,1 7,8 9,6 11,4 13,5 -d2(h13) min. - 2,76 3,62 4,32 5,88 7,58 9,38 11,13 13,23 -max. - - 1,85 2,1 2,6 3,1 3,6 4,25 4,75 -d3min. - - 0,75 1 1,5 2 2,5 3,15 3,65 - Nennmaß - - 3,8 4,5 6 7,6 9,4 11,2 13,2 -d4(h13) min. - - 3,62 4,32 5,82 7,38 9,18 10,93 12,93 - Nennmaß 2,4 3,2 3,9 4,7 6,3 8 9,6 - - -d5(h12) min. 2,3 3,08 3,78 4,58 6,15 7,85 9,45 - - -d6Nennmaß 1,3 1,6 2,3 2,6 3,7 4,8 - - - - (h16) min. 0,7 1 1,7 2 2,95 4,05 - - - -d7Nennmaß - 3 - - - - - - - - (h16) min. - 2,4 - - - - - - - -l21)max. - - 4,5 5,5 7 8,5 10 11,5 13,5 - (-IT18) min. - - 2,7 3,7 4,8 6,3 7,8 8,8 10,8 -l31)max. - - 5 6 8 9,8 10,8 12,6 14,6 - (-IT18) min. - - 3,2 4,2 5,8 7,6 8,1 9,9 11,9 -l41)max. - - 3,6 4 5,2 6,6 8,1 8,8 - - (-IT18) min. - - 1,8 2,2 3,4 4,4 5,9 6,6 - -l51)max. 2,7 3,7 4,4 5,5 6,9 8,3 - - - - (-IT18) min. 1,3 1,9 2,6 3,7 4,7 6,1 - - - -l6max. - 3 - - - - - - - - (-IT16) min. - 2,4 - - - - - - - -z1max. - - 2,75 3,25 4,3 5,3 6,3 7,36 - - (+IT14) min. - - 2,5 3 4 5 6 7 - -max. - - 2 2,3 3 3,5 4 4,5 - -z2min. - - 1 1,3 2 2,5 3 3,5 - -z3max. - - 2,45 2,95 3,8 4,8 5,5 6,66 8,36 - (+IT14) min. - - 2,2 2,7 3,5 4,5 5,2 6,3 8 -z4min. - - 0,5 0,7 1 1,5 2 2,5 - -1) Nennmaße l2, l3, l4 und l5 beschreiben die Länge des Einführungszapfens bis zum 1. vollausgeformten GewindegangSeite 6VW 604 24: 2005-10Tabelle 3 – Maße und Gewindeenden (zu vermeidende Größen)Maße in mmGewinde d1M7 M8x1 M10x1 M12 7/16-20Steigung P 1 1 1 1,75 1,27Nennlänge l1siehe ProduktnormenNennmaß - 6,3 8 9,4 9,1d2(h13) min. - 6,08 7,78 9,18 8,88max. - 2,6 3,1 3,6 3,4d3min. - 1,5 2 2,5 2,3Nennmaß - - - - -d4(h13) min. - - - - -Nennmaß - - - 10,9 -d5(h16) min. - - - 9,8 -d6Nennmaß 3,6 - - 5,9 -(h16) min. 2,85 - - 5,15 -d7Nennmaß - - - - -(h16) min. - - - - -l21)max. - 7 8,5 10 9,1(-IT18) min. - 4,8 6,3 7,8 6,9l31)max. - 7,8 9,4 11,3 10,5(-IT18) min. - 5,6 7,2 8,6 7,8l41)max. - 5,2 6,6 8,1 -(-IT18) min. - 3,4 4,4 5,9 -l51)max. 5,5 - - 9,6 -(-IT18) min. 3,7 - - 7,4 -z1max. 3,8 4,3 5,3 6,3 -(+IT14) min. 3,5 4 5 6 -max. 2,8 3 3,5 4 -z2min. 1,8 2 2,5 3 -z3max. - 4,1 5 5,5 4,1(+IT14) min. - 3,8 4,7 5,2 3,8z4min. - 1 1,5 2 -1) Nennmaße l2, l3, l4 und l5 beschreiben die Länge des Einführungszapfens bis zum1. vollausgeformten GewindegangSeite 7VW 604 24: 2005-10Tabelle 4 – UnterkopfauflagenNr. FormBild/Beispiel Bemerkung 1 Sv System Ripp (Sperrver-riegelung)Rippe läuft im Außen-Ø aus und wird durch den Innen-Ø derAuflagefläche begrenzt (d r )Das Ripp-System reduziert die Gefahr des Lösens.GewindeM5 M6 M8 M10 M12x1,5 M14x1,5 M16x1,5 Rippenzahl28 36 48 48 60 60 72 max. 5,9 7 9,4 11,4 13,9 15,9 17,9 d r(-IT14) min. 5,6 6,64 9,04 10,97 13,47 15,47 17,47 2 SvD SystemDurloc(Sperrver-riegelung)Nicht für NeukonstruktionGewindeM5 M6 M8 M10 M12x1,5 M14x1,5 M16x1,5 Zähnezahl 20 24 30 45 60 70 Anmerkung: Verwende Form Sv (System Ripp) 3 SvTSystemTensiloc(Sperrver-riegelung)Nicht für Neukonstruktionen 24 Zähne bei allen Gewinde-Ø Anmerkung: Verwende Form Sv (System Ripp)4 SveSperrver-riegelungEinseitig aufgebrachtes Verzahnungssystem bei ScheibenGewinde M5M6 M8 M10 M12x1,5 M14x1,5 M16x1,5 Zähnezahl 24 28 40 48 56 68 725 Svd Sperrver-riegelung ohne BildBeispiel siehe Sve Doppelseitig aufgebrachtes Verzahnungssystem bei Scheiben Anzahl der Zähne siehe SveSchutzrechte beachten6 Tm mitTelleran-satzDie Form mit Telleransatz wurde bei Änderung derDIN 962: 2001-12 nicht mehr berücksichtigtd w, min = d c, max – 1,7 mm (bei Flanschprodukten) 7 ToohneTelleran-satz Die Form ohne Telleransatz wurde bei Änderung der DIN 962 nicht mehr berücksichtigt. Wird nur angegeben wenn die Produktnorm mit Telleransatz ausgeführt ist.1) 1) 1) 1)Seite 8VW 604 24: 2005-10Tabelle 4 – Unterkopfauflagen (abgeschlossen)Nr. Form Bild/Beispiel Bemerkung8 RSWRingschweiß-warze Ringschweißwarzen werden bei Schweißmuttern und Schweißschrauben abgewendet9 ITRInnenträger Innenträgerschrauben vermeiden weitgehendStick – Slip - Effekte (Kaltverschweißung unter Kopf beider Montage).Beim Innenträger kommt der Bereich Übergangsradius Auslauf zuerst zur Auflage (Bereich X). (Tragbild von innen nach außen)10 ATRAußenträger Nicht für NeukonstruktionBeim Außenträger kommt der Bereich des Flanschaußendurchmessers zuerst zur Auflage (Bereich X). Gefahr von Stick-Slip-Effekten Anmerkung: Verwende ITR (Innenträger)1) Konstruktiver Hinweis hinsichtlich Gegenlage siehe VW 011 102) Ausführung des Ripp-Profils3) TelleransatzSeite 9VW 604 24: 2005-10Tabelle 5 - ZusatzangabenNr. Form Bild/Beispiel Bemerkung1 Szmit Schlitz Nicht für NeukonstruktionSchlitzbreitentoleranz (n) nach DIN ISO 4759-1.d 1 M3M4 M5 M6 M8 M10 M16x1,5 n 0,8 1,2 1,2 1,6 2 2,5 32 SsSelbstsicherndDieser Sicherungstyp wird vorwiegend bei Schnappmuttern verwendet. 3 KLRKlemmendeRundum-beschichtungohne Bild Die klemmende Beschichtung ist in DIN 267-28 beschrieben. Sie dient als Verliersicherung und auch zum Zwecke der Abdichtung, da immer rundumbeschichtet. 4 KLDDichtendeRundum-beschichtungohne Bild Anforderungen an die dichtende Rundum-beschichtung sind in TL 195 beschrieben. 5 SgSchlussgerolltohne Bild Gewinde wird nach Vergütung gewalzt. Dadurch wird eine Erhöhung der Dauerfestigkeit erreicht. Für überelastische Verschraubung nicht sinnvoll. 6 Gn Gewindenachgerollt ohne Bild Schraubengewicht > 20 gGewinde wird nach der Ofl.-Behandlung nachgerollt um Schlagstellen zu reduzieren. Sinnvoll nur beiVerschraubung in Leichtmetall.7 BeflBeflockung Beflockungsbereich auf Zeichnung vorgeben. Angabe des Farbtons in FAKOM 3).8 MRmit Rastnase Verliersicherung für vormontierte Schnappmutter.Seite 10VW 604 24: 2005-10Tabelle 5 – Zusatzangaben (abgeschlossen)Nr. Form Bild/Beispiel Bemerkung9 a2 Gewinde-auslaufDIN 76-1 kurzGewindeauslauf min. 0,5mm, max. 2 xGewindesteigung (P) bei Schrauben mit geringerSchraubenlängel 1 = 2,5 x d 1 bis M10l 1 = 2 x d 1 größer M10 10 Duo Schrauben mit mindestenszwei AntriebenKurzzeichen für AntriebsartN = Innenvielzahn > M6T = Innensechsrund = M6H = Kreuzschlitz (Nicht für Neukonstruktion)I = Innensechskant (Nicht für Neukonstruktion)Sz = Schlitz (Nicht für Neukonstruktion) 1) 3 Schlitze auf dem Umfang verteilt2) Beflockung3) FAKOM System für Verknüpfung von Farbdaten mit Stücklisten4) Rastnase5) Kopfform beispielhaft (hier dargestellt mit Sechskantflansch)4Mitgeltende Unterlagen TL 195 Schrauben aus Stahl mit abdichtender BeschichtungVW 603 61 Mechanische Verbindungselemente, Teilereduzierung; AllgemeineRichtlinienVW 605 72 SechskantflanschschraubenDIN 76-1 Gewindeausläufe und GewindefreisticheDIN 267-28 Mechanische Verbindungselemente; Schrauben aus Stahl mit klemmenderBeschichtungDIN 267-30 Mechanische Verbindungselemente; TL für m etrische gewindefurchendeSchraubenDIN 962Schrauben und Muttern- Bezeichnungsangaben, Formen und Ausführungen DIN 7500-2Gewindefurchende Schrauben für metrisches ISO-Gewinde; Richtwerte für Kernlochdurchmesser DIN 34803Splintlöcher und Drahtlöcher für Schrauben DIN EN 20225 Mechanische Verbindungselemente Schrauben und Muttern; Bemaßung DIN ISO 4759-1(80.05)Mechanische Verbindungselemente; Toleranzen für Schrauben undMuttern, Produktklasse A, B, C, Ausgabe 1980-05DIN EN ISO 4753Verbindungselemente - Enden von Teilen mit metrischem ISO-Außengewinde DIN EN ISO 10644 Kombi-Schrauben mit flachen ScheibenSeite 11VW 604 24: 2005-10Anhang A (informativ)Tabelle 6 – Formen, Ausführungen und Zusatzangaben die in Normen beschrieben werden.Benennung mit Quelle Ersatz Formen,Ausführungen,ZusatzangabenA Produktklasse A-DIN ISO 4759-1AB Abdichtung – VW 602 61AK Ansatzkuppe – DIN 962ASP Ansatzspitze – DIN 962ASPX 1) Ansatzspitze – ähnlich DIN 962C Spitze – DIN EN ISO 1478 DIN EN ISO 1478 – RCX 1) Spitze – ähnlich DIN EN ISO 1478CFX 1) Gewindeende – ähnlich DIN 267-30KX 1)Kegelkuppe – ähnlich VW 604 24 – KF Zapfen – DIN EN ISO 1478FX 1) Zapfen – ähnlich DIN EN ISO 1478FL Kegelstumpf – DIN EN ISO 4753FLX 1) Kegelstumpf – ähnlich DIN EN ISO 4753Fo ohne Festsitz – DIN 962GF Gewindefurchend – DIN 267 30GZ GewindezapfenHr HaftrilleKL Klemmende Rundumbeschichtung –VW 604 24 – KLRDIN 267-28LD Langer Zapfen – DIN EN ISO 4753 VW 604 24 – PFLDX 1) Langer Zapfen – ähnlich DIN EN ISO 4753MK Gewinde mit klebender Beschichtung –DIN 267-27MKL Klebende Beschichtung mit eingestellterReibungszahl – DIN 267-27OR ohne RastnasePM Permanentmagnet – DIN 910Pow Powerloc-Gewinde – VW 605 59R gerundete Spitze – DIN EN ISO 1478RX 1) Gerundete Spitze mit AbweichungRi Gewindefreistich – DIN 76-1RiA Gewindefreistich (Regel) – DIN 76-1RiB Gewindefreistich (kurz) – DIN 76-1Seite 12VW 604 24: 2005-10Formen,Benennung und Quelle ErsatzAusführungenZusatzangabenRL ohne Kuppe – DIN EN ISO 4753RN Linsenkuppe – DIN EN ISO 4753S Splintloch – DIN 34803SB Schabenut – DIN EN ISO 4753 DIN EN ISO 4753 – SC SBX 1) Schabenut – ähnlich DIN EN ISO 4753SCX 1) Schabenut – ähnlich DIN EN ISO 4753SD Kurzer Zapfen – DIN EN ISO 4753SDX 1) Kurzer Zapfen – ähnlich DIN EN ISO 4753Sk Loch im Schraubenkopf – DIN 34803SkX 1) Loch im Schraubenkopf – ähnlich DIN 34803TCX 1) Spitze abgeflacht – ähnlich DIN EN ISO 4753TmX 1) mit Telleransatz – ähnlich VW 604 24U Hohlkehle – DIN EN ISO 10644VX 1) Ansatzspitze – ähnlich VW 604 24WX 1) Einführzapfen mit Spitze – ähnlich VW 604 241) Abweichungen von der in der Norm beschriebenen Formen und Ausführungen w erden zusätzlich mit einem “X“ (z.B. AVX) ergänzt.。
vW01105-1-2010版本
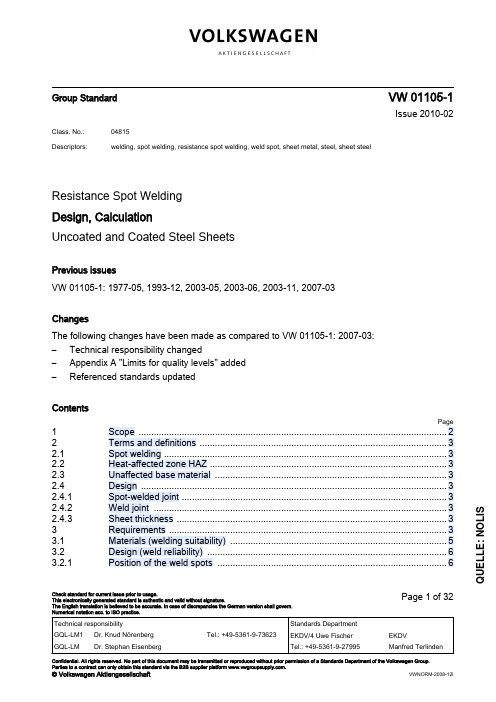
Resistance Spot WeldingDesign, CalculationUncoated and Coated Steel SheetsPrevious issuesVW 01105-1: 1977-05, 1993-12, 2003-05, 2003-06, 2003-11, 2007-03ChangesThe following changes have been made as compared to VW 01105-1: 2007-03:–Technical responsibility changed–Appendix A "Limits for quality levels" added–Referenced standards updatedContents PageScope (2)Terms and definitions (3)Spot welding (3)Heat-affected zone HAZ .............................................................................................3Unaffected base material (3)Design (3)Spot-welded joint (3)Weld joint (3)Sheet thickness (3)Requirements (3)Materials (welding suitability) (5)Design (weld reliability) (6)Position of the weld spots ..........................................................................................6122.12.22.32.42.4.12.4.22.4.333.13.23.2.1Group Standard VW 01105-1Issue 2010-02Class. No.:04815Descriptors:welding, spot welding, resistance spot welding, weld spot, sheet metal, steel, sheet steelCheck standard for current issue prior to usage.This electronically generated standard is authentic and valid without signature.The English translation is believed to be accurate. In case of discrepancies the German version shall govern.Numerical notation acc. to ISO practice.Page 1 of 32Technical responsibility Standards DepartmentGQL-LM1Dr. Knud Nörenberg Tel.: +49-5361-9-73623GQL-LM Dr. Stephan Eisenberg EKDV/4 Uwe Fischer EKDVTel.: +49-5361-9-27995Manfred Terlinden Confidential. All rights reserved. No part of this document may be transmitted or reproduced without prior permission of a Standards Department of the Volkswagen Group.Parties to a contract can only obtain this standard via the B2B supplier platform .© Volkswagen Aktiengesellschaft VWNORM-2008-12l QU E L L E : N O L I SWeld sequence ..........................................................................................................7Arrangement of spots (spot position) .........................................................................7Spot spacing ..............................................................................................................7Design examples and dimensions .............................................................................8Tolerances ...............................................................................................................13Manufacturing (welding capability) ...........................................................................14Basics .......................................................................................................................16Minimum shear force (F S ) .........................................................................................16Cross-tension force F K .............................................................................................17Peeling force F peel .....................................................................................................17Torsion .....................................................................................................................18Static and dynamic loads .........................................................................................18Process assurance ...................................................................................................19Weld spot geometry .................................................................................................19Number of weld spots ..............................................................................................23Surface quality class for spot-welded sheets ...........................................................23Drawing entries ........................................................................................................24Referenced documents ............................................................................................25Limit values for quality levels ...................................................................................263.2.23.2.33.2.43.2.53.2.63.344.14.24.34.44.54.64.6.14.6.24.6.356Appendix AScopeThe following basic regulations are based on experience with low to high degrees of mechanization,on test results, as well as on standards and technical regulations, e.g. DVS 2902-1, DVS 2902-2,DVS 2902-3.This standard is used for the design, calculation and workmanship of resistance-spot-welded sheet steel constructions subject to both static and dynamic loads. The joints used in these constructions are hereinafter referred to as "spot-welded joints".This standard covers resistance spot welding (reference number 21 acc. to DIN EN ISO 4063) on single-shear spot-welded joints with a sheet thickness ratio ≤ 3 : 1 for a thickness of 0,5 mm to 4,0 mm,as well as quality characteristics of single-spot and multiple-spot-welded joints. Larger sheet metal thicknesses and ratios are possible in agreement with the engineering departments. The nugget diameter is always determined by the thinnest sheet thickness.Sheets according to DIN EN 10139, however, are to be used only if their thickness does not exceed 3,0 mm.The introduction of zinc-coated sheets, e.g., according to DIN EN 10142 or DIN EN 10292, and the use of high-strength and higher-strength steels require higher electrode forces. This, in turn, may result in the necessity for larger electrode tip and electrode shank diameters (16 mm and 20 mm).When these electrodes are used, the weld nugget moves further away from the root face in the case of angled spot-welded flanges. However, as the distance between the weld nugget and the root face increases, component rigidity and strength decrease.Further requirements for (resistance) spot-welded joints are included in:–VW 01105-2 Resistance Spot Welding; Aluminum Materials,–VW 01105-4 Multiple-Sheet Joints; Dual- and Multiple-Shear JointsThe procedures described in the Test Specifications PV 6702 and PV 6717 are decisive for the quality audit of spot-welded joints.1 Page 2VW 01105-1: 2010-02Terms and definitions Spot weldingIn resistance spot welding, the weld zone between the parts to be joined is heated to the melting point using resistance heating with electrode force acting simultaneously. Size, shape and position of the melted base material depend on the temporal and spatial interaction of the heat quantities generated and dissipated in the weld zone and its surroundings. Under the influence of the electrode force, the workpieces are joined when the melt solidifies. The welded joint in the shape of a "weld nugget" that develops during this process is referred to as a …weld spot“ (Figure 26) that joins the parts (Section 2.4.2). The nugget diameter d L is the diameter of the melted material in the joining plane that is measured on the microsection.Heat-affected zone HAZArea of the base material that remains solid but experiences changes in microstructure due to the thermal energy applied during spot welding.Unaffected base materialArea of the base material that has experienced no recognizable changes in microstructure due to the energy applied during spot welding.Base materials that do not differ significantly in their chemical composition and suitability for spot welding are considered materials of the same type. Base materials that differ significantly in their chemical composition and suitability for spot welding are considered as different types of materials.Design Spot-welded jointThe spot-welded joint is a connection of two or more parts joined directly at the weld joint by one or more "weld spots" or "spot seams". The parts involved are designated on drawings as an ASSY (assembly) or WA (welded assembly).Weld jointThe weld joint is the configuration in which the parts are joined to each other by spot welding. The respective joint type is determined by the design relationships of the parts to each other.Sheet thicknesst 1 and t 2 are sheet thickness values of the single-shear spot-welded joint. For the purpose of uniform definition, especially for calculation, the thinnest sheet or the thinnest outer sheet of the joint must always be designated as t 1 if there are different sheet thicknesses. The thickest sheet of the joint is designated as t 2.RequirementsEach spot-welded construction must be "suitable for welding" in order to achieve the greatest possible design strength during manufacturing in the sense of the design goal with adequate safety and op‐timum cost-quality ratio. This means that the dimensions in the spot welding equipment, the electrode 22.1 2.2 2.3 2.42.4.1 2.4.2 2.4.3 3 Page 3VW 01105-1: 2010-02space requirement, as well as the accessibility of the workpiece must already be taken into consid‐eration during advance engineering. The weldability depends on three influencing variables:–welding suitability (material),–weld reliability (design),–welding capability (manufacturing).All three criteria have the same priority for weldability, see Figure 1. For a definition, please also refer to DIN Technical Report ISO/TR 581 "Weldability - Metallic Materials, General Principles".Figure 1 – Schematic representation of the weldability of spot-welded jointsPage 4VW 01105-1: 2010-02Materials (welding suitability)The welding suitability is a material property. Materials are suitable for welding if the material´s chemical composition allows a welded joint that meets the requirements set forth in the respective standards to be produced.For a first estimation of the welding parameters of a joining task, it is recommended to prepare a weldability lobe (time/current diagram, Figure 2) stating the limit lines for the minimum and maximumnugget or spot diameters for a constant electrode force and shape, see also DIN EN ISO 14327.Figure 2 – Weldability lobeFor estimation of the welding parameters, it is recommended to select the welding time and current values such that the following current differences result between the limit lines of d L min or d P min and d L max or d P max :–Δ ≥ 1,2 kA for resistance spot welding equipment with tip cutting device,–Δ ≥ 1,5 kA for resistance spot welding equipment without tip cutting device.The chemical composition basically influences the microstructure, hardening, nugget formation and strength of the spot-welded joint.The less the material-related factors have to be considered in manufacturing and design, the greater the welding suitability of a material within a material group (see DVS 2902-2).Testing of nugget position, nugget shape, and welding range is required for spot-welded joints of mixed materials (especially connections between unalloyed/low-alloyed steels and austenitic steels).All steels with a C content of up to 0,25% (max. 0,3%) are suitable for spot welding. In many cases,the equivalent carbon content (CE) is used for determining the welding suitability (hardening) of un‐alloyed and low-alloyed steels. According to DVS 2902-2, the following equation applies to a first estimation of the hardening of the weld metal:CE = C + Mn/6(1)3.1 Page 5VW 01105-1: 2010-02Figure 3 – Maximum hardness of the weld nugget as a function of the equivalent carbon content Figure 3 is an example illustrating the interdependence between the maximum hardness of the weld nugget and the equivalent carbon content.Special measures (e.g. reheating, multi-pulse welding, etc.) may be necessary for alloyed steels due to the alloying elements that influence hardness. Therefore, their use has to be agreed upon with the responsible engineering departments and tested separately.A hardness increase factor of ≤ 3,5 is recommended as the limit value for the hardness in both the weld nugget and the HAZ.Example:(2)The maximum hardness in the weld nugget and the HAZ must not exceed the value of 550 HV 0,2.See also DVS 2905.Design (weld reliability)Weld reliability is of particular importance for design. The design-related weld reliability is mainly influenced by the material and to a slight extent by manufacturing. Weld reliability is provided if, with the material used, a component remains functional under the intended operating conditions due to its design.Position of the weld spotsThe position of the weld spots must be specified by Design Engineering in consultation with Produc‐tion and Planning departments. If possible, the electrodes should contact the part perpendicular to the part surface. Otherwise, i.e. if they contact the part surface at a different angle, the nugget diam‐eter may be significantly smaller and elliptical.3.2 3.2.1 Page 6VW 01105-1: 2010-02The key criteria for the distance between the weld spot and the perpendicular flange are the minimum distance A = 2,0 mm from the current-carrying parts, the largest radius R i , as well as the electrode shank diameter d S or electrode tip diameter d K .Please refer to the drawing or DIN ISO 2768-1 for positional tolerances of the weld spots (spot spacing tolerance).Further information on the design of spot-welded joints can be obtained from DVS 2902-3.Weld sequenceContinuous rows of weld spots created using only one welding device must have spacings no smaller than 25 mm. For narrower spot spacings, the welding to gap method must be used (to prevent sub‐sequent spots from being too small or loose, see Figure 4).Arrangement of spots (spot position)The arrangement of spots must be selected such that the force F to be transferred is distributed as uniformly as possible over all spots. If the load distribution is not uniform, there will be a negative effect on both the vibration resistance and the crash behavior.With multiple-row spot seams, the spot arrangement is to be agreed upon with the Design Engineer‐ing, Calculation, Strength, Planning and Production departments.Spots that cannot be welded properly due to difficult accessibility are to be avoided (see Figure 7)."Quarter, third, half and three-quarter spots" reduce load bearing capacity. In checked exceptional cases, a defined portion of half and three-quarter spots can be permitted by the Testing department (Vehicle Strength and Vehicle Safety) in certain areas. This must be noted separately in the assembly drawing (Figure 29).Spot spacing The spot spacing e is the distance between the centers of two adjacent weld spots (Figure 4 and Figure 5). The spot spacing e Neb indicates the distance below which the shunt can no longer be ignored during the welding process.The shunt increases when–spot diameter,–sheet thickness,–electrode force, and –electrode contact surface increase, and when –the spot spacing decreases.Depending on the size of the shunt, the welding current must be increased more or less in order to create weld nuggets with the same diameter. The portion of the current that flows over spots of the seam that are already present does not contribute to heating the actual weld area. Therefore, the nugget diameter will be smaller starting from the 2nd spot of a seam if the spot spacing is too small and the setting data are constant. The influence of the shunt can be compensated for with the use of programmable and process-regulating controls. Generally, the following applies: e ≥ e Neb 4 x d L can be used as a reference value for the spot spacing e .Shunt can be ignored for a spot spacing e ≥ 10 (t 1 + t 2). In the case of multiple-row joints the following applies as a rule: e ≈ 5 x d L3.2.2 3.2.3 3.2.4 Page 7VW 01105-1: 2010-02Figure 4 – Left: double-row offset single-shear spot seam; right: double-row double-shear spot seam Figure 5 – Prevention of shunt in case of spot spacings that are too smallFigure 6 shows different forms of shunt.Figure 6 – Forms of shuntLegenda)Shunt at the sheet metal due to electrode contact b)Shunt via the centering pin (due to close distance)The Figure does not show shunt forms caused by c)clamps,dthe transformer grounding,e)the fixture.Design examples and dimensions Designs with poor accessibility are to be avoided, since specifically shaped electrodes and/or elec‐trode arms would be required (Figure 7 and Figure 12).3.2.5 Page 8VW 01105-1: 2010-02Figure 7 – Examples of unfavorable and favorable accessibility for the welding electrodes at the weldflangesOverlap Overlap b is the width of the contact surface of the weld flanges on the sections. The planes of thecontact surfaces must be parallel and touch each other (Figure 8).b is the shortest distance between the limit lines. The following applies: b ≥ 2v.Figure 8 – Left: single-row single-shear spot seam; right: double-row single-shear spot seamSeam spacing f For multiple-row spot seams, the seam spacing f is the shortest distance between the spot centers of adjacent seams (Figure 8 right). The following applies in general: f ≥ e.Seam length l The seam length l is the distance between the spot centers of the first and last spots of a spot seam (Figure 8).Edge distance v The edge distance v is the distance between the weld spot center and the closest limit line of the contact surface (Figure 9).3.2.5.1 3.2.5.2 3.2.5.3 3.2.5.4 Page 9VW 01105-1: 2010-02The following applies as a rule: v min = 1,25 x dL minFigure 9 – Edge distanceFlange width a The flange width a (Figure 10) is the value that is to be complied with in manufacturing, so that a)the position of the weld spot is not too close to the edge of the sheet metal,b)the welding equipment (electrode tip and shank) does not create any shunt to the bent sheet,c)the selected bending radius of the sheet is small enough to provide a longstraight portion of the flange width to ensure a sufficient contact surface forthe welding electrode.The flange width is to be agreed upon between Design Engineering, Planning and Production de‐partments.For calculation, see VW 01105-1 Supplement 1 "Resistance Spot Welding; Calculation of Flange Width ".In exceptional cases, it is possible to deviate from the flange width calculation. If this is the case, the flange width must be agreed upon between Design Engineering, Planning and Production depart‐ments.Figure 10 – Flange widthsFor multiple-row spot seams, the flange width a is to be increased according to the seam spacing f.The flange width is measured from the end of the flange to the angled sheet and is composed of the edge distance v and the clearance FM, as well as the tolerance T G .3.2.5.5 Page 10VW 01105-1: 2010-02Flange offset iThe flange offset i is the maximum projection of the primary flange with respect to the secondary flange, e.g. for the mounting of seals (Figure 10). The secondary flange must not protrude over the primary flange on the trim edge.Flange heights c and h, offset gThe dimensions c and h (Figure 10) take into consideration the dimensions of the spot weldingequipment, the electrode space requirements and the workpiece accessibility in manufacturing (see also Figure 13).The dimension g specifies the maximum permissible offset (Figure 11).The values must be agreed upon between Design Engineering, Planning and Production depart‐ments.Flange and overlap spacing kThe flange and overlap spacing k is the distance between overlap b and tangent line (Figure 11).Figure 11 – Offset g, spacing kThe following applies to k min : k ≥ 2,0 mm The following applies to g min : g ≥ sheet thickness3.2.5.6 3.2.5.73.2.5.8Flange geometryTable 1 – Weld flange geometry as a function of sheet thickness t min and welding condi‐tions (all dimensions in mm)Sheet thick‐nessSpot spacing Flange dimensions DiameterClearanceFlange width t mine Nebv min b min i g max k mind Kd SFMa0,5 to 0,6103,36,61,0–1,01,1213138,515,3> 0,6 to 0,8123,97,81,0–1,01,316181118,4> 0,8 to 1,0154,38,61,5–1,51,518,8> 1,0 to 1,2184,89,61,5–1,51,719,3> 1,2 to 1,5245,310,61,5–1,52,019,8> 1,5 to 1,6275,611,22,0–2,02,520,1> 1,6 to 2,0276,312,62,0–2,02,520201221,8> 2,0 to 2,5366,813,62,0–2,03,022,3> 2,5 to 3,0457,615,22,0–2,03,5241425,1> 3,0 to 3,5548,116,22,5–2,54,725,6> 3,5 to 4,0638,817,52,5–2,54,726,3Legend:v min = 1,25 d L min Edge distance (Figure 9) including tolerance b ≥ 2 v and b ≥ a - r Overlap (Figure 9)i Flange offset (Figure 10)g max Offset of the overlap (Figure 11)k min Flange and overlap spacing (Figure 11)d K Electrode tip diameter d SElectrode shank diameterFM = d S /2 + A Clearance for electrode shank diameter a ≥ v min + FM + T GFlange width, influence of electrode (f A=2; D shank )with T G = 3,5NOTE 1 Since the flange width values specified in Table 1 depend on several factors, and since at least T G must be agreed upon between Design Engineering, Planning and Production departments (see Section Section 3.2.6), the values still have to be corrected accordingly.Reference sheet thickness t vFor joints with different sheet thicknesses (t 1 ≠ t 2), the reference sheet thickness t v may be used instead of t min for determining the welding parameters.t v = 0,8 t 1 + 0,2 t 23.2.5.9 3.2.5.103.2.6TolerancesTolerance values must be agreed upon between Design Engineering, Planning and Production de‐partments.Trim tolerance T aThis value represents the trim tolerance during production of the individual part and must be included in the calculation.General body-in-white tolerance T RThis value considers the general tolerances in body construction, including the inaccuracies of in‐dustrial robots and must be included in the calculation.Design-related tolerance compensation T KThe value considers the flange displacements that are provided for secondary flanges and must be included in the calculation.Equipment tolerance T VThis value considers the repetition accuracy of the equipment and must be included in the calculation. Overall tolerance T GThe overall tolerance is made up of the tolerances T a, T R, T K and T V described above to the extent that these have to be considered.T G = T a + T R + T K + T VA total allowance of T G = 3,5 mm has been chosen for the calculation in Table 1.Manufacturing (welding capability)Care must also be taken in design to ensure that the component is capable of being welded (manu‐facturing-related weld reliability). It must be possible to produce the planned welds properly under the state-of-the-art manufacturing conditions.During the design of components, the following manufacturing aspects should be taken into consid‐eration:–If the designs require operating equipment with long arms spaced far apart, it must be determined early in the process whether the available welding equipment is suitable for this purpose.–If possible, the designs must allow short, straight and rigid arms, electrode brackets and elec‐trodes to be used (Figure 12).Figure 12 – Examples of electrode arm shapes to be avoided–Refer to VW 01105-4 for double-shear and multiple-shear joints.–The distance between the outer diameter of the electrode and/or the electrode bracket and theinner edge of the sheet must be at least (2 + 0,5) mm (Figure 13). Other specifications must be agreed upon between the responsible specialized departments.Figure 13 – Poor weld quality caused by electrodes that spring back and slide–During the welding process of high-strength and highest-strength sheets, the electrodes normally do not penetrate considerably into the base material. As a result, the risk of electrode sliding is increased. Especially if pneumatic electrode holder drives are used, it is important that the elec‐trodes are placed perpendicularly and that the electrode holder is as rigid as possible.–During welding of spot seams, the welding sequence must be selected such as to avoid the formation of cavities between the sheets (Figure 14).3.3Figure 14 – Welding sequence to avoid the formation of cavities–The electrode axis must be perpendicular to the sheet surface (90° ± 1°) (Figure 16, Figure 18).Figure 15 – Not per‐missible Figure 16 – Favor‐able Figure 17 – Permissi‐ble Figure 18 – Favor‐able–If asymmetrical electrode tips (Figure 17) are used, special measures are required in series production operation to ensure the proper alignment of the working surfaces (freedom from ro‐tation, orientation during tip change, special electrode tip milling cutters).BasicsDifferent types of loads occur depending on the design of a component (Section 2.4):–shear tension (Figure 19)–cross tension (Figure 20)–peeling tension (Figure 21)–torsion (Figure 22)If possible, spot-welded joints should only be loaded with shear tension since the highest forces per weld spot can be transferred with this type of load. Therefore, pure cross or peeling tensions and/or torsion are to be avoided.Minimum shear force (F S )For a single-shear joint, the shear force F s generates a bending moment M b = F s r s which increases with increasing load and also produces a portion of the cross tension force F K . r sis set as follows:Figure 19 – Shear tensionLegend A Prior to tensile testB After tensile test (exaggerated)C Outer notchF K Portion of the cross tension force of F max F SPortion of the shear force of F maxBecause of the realistic verification of requirements and the low variation of the test results, the cal‐culations of the spot-welded joints are based on the minimum shear force F s min that was determined from the shear test according to PV 6702:4 4.1F s min = F max - 2 s in kNLegend s Standard deviationF maxMean value of the maximum force determined in the shear test ac‐cording to DIN EN ISO 14273(3)Cross-tension force F KFigure 20 – Cross tensionWith this type of stress, the permissible load F K is only 60% of the shear force F min..The following applies according to DVS 2902-3 (to materials according to DIN EN 10130)F K ≤ 0,6 F min(4)Peeling force F peelFigure 21 – Peeling tensionWith this type of stress, the permissible load F peel perm is only 20% of the shear force F min as set forth in Table 2 and DVS 2902-3.F peel perm ≤ 0,2 F min(5)4.24.3TorsionFigure 22 – TorsionA durable joint is achieved with at least two weld spots, since, with twisting around one spot, the transferable torque M t is too low. Designs with only one load-bearing spot are not permissible.Static and dynamic loadsA basic distinction is made between calculations with static or dynamic loads. The formula relationship previously specified is used for calculation of static load.The following information applies to the proof of sufficient strength of dynamically loaded components:–Because of as yet inadequate knowledge about the influence of the design of the joint and the uncertainties in calculation, the load carrying capacity of the joints for vibration loads must always be verified through testing.–With a given material thickness, the service life of a joint depends on the load amplitude, the R value (stress ratio) and the type of load (Figure 23). The type of load may be shear or peeling.Cross tension and torsion usually do not occur. Generally no type of load occurs alone and in pure form.Figure 23 – Load amplitude–The single-row single-shear joint is to be preferred.–Dynamic cross tension, peeling tension and torsion are to be avoided due to the low permissible tension.4.4 4.5。
大众故障码
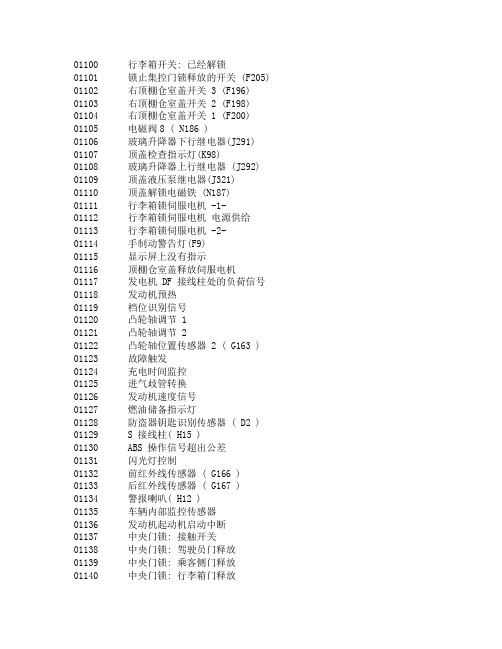
01101 锁止集控门锁释放的开关 (F205) 01102 右顶棚仓室盖开关 3 (F196) 01103 右顶棚仓室盖开关 2 (F198) 01104 右顶棚仓室盖开关 1 (F200) 01105 电磁阀8 ( N186 )01106 玻璃升降器下行继电器(J291) 01107 顶盖检查指示灯(K98)01108 玻璃升降器上行继电器 (J292) 01109 顶盖液压泵继电器(J321)01110 顶盖解锁电磁铁 (N187)01111 行李箱锁伺服电机 -1-01112 行李箱锁伺服电机电源供给01113 行李箱锁伺服电机 -2-01114 手制动警告灯(F9)01115 显示屏上没有指示01116 顶棚仓室盖释放伺服电机01117 发电机 DF 接线柱处的负荷信号01118 发动机预热01119 档位识别信号01120 凸轮轴调节 101121 凸轮轴调节 201122 凸轮轴位置传感器 2 ( G163 ) 01123 故障触发01124 充电时间监控01125 进气歧管转换01126 发动机速度信号01127 燃油储备指示灯01128 防盗器钥匙识别传感器 ( D2 ) 01129 S 接线柱( H15 )01130 ABS 操作信号超出公差01131 闪光灯控制01132 前红外线传感器 ( G166 ) 01133 后红外线传感器 ( G167 ) 01134 警报喇叭( H12 )01135 车辆内部监控传感器01136 发动机起动机启动中断01137 中央门锁: 接触开关01138 中央门锁: 驾驶员门释放01139 中央门锁: 乘客侧门释放01140 中央门锁: 行李箱门释放01142 中央门锁: 释放电机01143 中央门锁: 闭锁电机01144 中央门锁: 闭锁电机01145 中央门锁: 闭锁电机01146 中央门锁: 释放电机01147 行李箱释放电机 ( V120 )01148 门安全保险功能: 激活01149 门安全保险功能: 未激活01150 模拟仪表指针指示01151 柴油机安全停机开关 ( F207 ) 01152 档位监控开关( F209 )01153 自动节油开关( E163 )01154 离合器系统压力开关 ( F210 ) 01155 离合器01156 档位识别开关( F208 )01157 警报喇叭供给电压01158 转向信号供给电压01159 安全保险丝线路01160 预热塞冷却液继电器 ( J325 ) 01161 凸轮轴调节阀输出01162 气缸燃烧断火识别01163 点火故障01165 节流阀体控制单元( J338 )01166 发动机扭矩信号01167 满负荷截止阀( N194 )01168 怠速提升阀 ( N177 )01169 门接触开关司机侧 ( F2 )01170 喷油持续时间传感器 ( G175 ) 01171 温度传感器: 乘客侧坐椅 ( G60 ) 01172 温度传感器: 司机侧坐椅 ( G59 ) 01173 坐椅纵向调节电机: 司机侧 ( V28 ) 01174 坐椅高度调节电机: 司机侧 ( V138 ) 01175 坐椅加热调节: 司机侧 ( E94 ) 01176 点火钥匙01177 发动机控制单元未授权01179 点火钥匙匹配错误01180 发动机/附加电器电器连接故障01181 初始化: 仅仅识别 2 个钥匙01182 高度自适应01183 排气净化警告灯( K72 )01184 后出风口温度传感器 ( G174 )01185 后部新鲜空气鼓风机 ( V80 )01186 后部空气分配调节电机 ( V136 )01187 后部温度调节翻板电机( V137 )01188 控制单元/电磁铁 : 电器连接01189 气流分配电机: 前 ( V145 )01190 控制单元/伺服电机: 电气连接故障01191 坐椅调节电机01192 液力偶合器锁止离合器01193 小加热功率继电器( J359 )01194 大加热功率继电器 ( J360 )01195 结束01196 发动机/自动变速器: CAN 数据总线01197 动力系统数据总线: 无效状态01198 舒适系统数据总线: 无效状态01199 发动机/ABS: 电气连接故障01200 ABS 阀供给电压01201 ABS 泵供给电压01202 诊断线路01203 ABS/仪表板: 电气连接故障01204 发动机温度传感器 ( G27 )01205 全自动空调继电器( J254 )01206 点火开关关闭时间间隔信号01207 控制单元: 辅助加热系统01208 控制单元之间的数据交换01209 发电机端子 W 的速度信号01210 控制学习调节范围01211 安全带涨紧触发器: 司机侧后面( N196 ) 01212 安全带涨紧触发器: 乘客侧后面( N197 ) 01213 安全带涨紧触发器: 中央后面( N198 ) 01214 安全带涨紧碰撞数据已经存储01215 坐椅占用传感器: 司机侧后面 ( G177 ) 01216 坐椅占用传感器: 乘客侧后面( G177 ) 01217 侧面安全气囊触发器: 司机侧 ( N199 ) 01218 侧面安全气囊触发器: 乘客侧 ( N200 ) 01219 后面安全气囊触发器: 司机侧 ( N201 ) 01220 后面安全气囊触发器: 乘客侧 ( N202 ) 01221 侧面安全气囊碰撞传感器: 司机侧 ( G179 ) 01222 侧面安全气囊碰撞传感器: 乘客侧 ( G180 ) 01223 中央门锁信号: 已经打开01224 控制单元不能与车速相匹配01225 辅助加热器无线接收器 (R64)01226 碰撞数据侧面安全气囊: 司机侧01227 碰撞数据侧面安全气囊: 乘客侧01228 安全气囊关闭开关: 乘客侧 ( E224 ) 01229 湿度传感器: A/C ( G260 )01230 脚坑温度传感器: 左侧( G261 ) 01231 脚坑温度传感器: 右侧( G262 ) 01232 A/C 压缩机调节阀( N280 )01233 加热系统冷却锁止阀 (N279)01234 控制单元: 挡风玻璃加热器 ( J505 ) 01235 二次空气喷射电磁阀( N112 )01236 换档锁电磁铁 ( N110 )01237 燃油断油阀( N109 )01238 点火提前角调节01239 节气门位置调节旁通阀( N97 ) 01240 节气门位置调节放气阀( N117 ) 01241 EVAP 活性炭罐电磁阀( N115 ) 01242 控制单元中断放大器01243 进气歧管转换阀( N156 )01244 氧传感器加热器控制单元( J208 ) 01245 差压调节. ( J81 )01246 Early Fuel Evap Relay ( J81 ) 01247 EVAP 活性炭罐电磁阀( N80 )01248 全负荷加浓双向阀( N54 )01249 喷油器: 1 缸 ( N30 )01250 喷油器: 2 缸 ( N31 )01251 喷油器: 3 缸 ( N32 )01252 喷油器: 4 缸 ( N33 )01253 喷油器: 5 缸 ( N34 )01254 喷油器: 6 缸 ( N35 )01255 喷油器: 7 缸 ( N36 )01256 喷油器: 8 缸 ( N37 )01257 怠速空气控制阀 ( N71 )01258 空气翻板定位器 ( V63 )01259 燃油泵继电器 ( J17 )01260 滑行断油阀 ( N65 )01261 氧传感器频率阀( N7 )01262 增加压力限制电磁阀( N75 )01263 冷启动喷嘴 ( N17 )01264 二次空气喷射泵继电器( J299 ) 01265 EGR 真空调节电磁阀( N18 )01266 预热塞继电器 ( J52 )01267 预热时间自动调节控制单元( J179 ) 01268 流量调节器( N146 )01269 冷启动喷射阀( N108 )01270 A/C 空调电磁离合器 ( N25 )01271 温度调节翻板电机 ( V68 )01272 中央空气翻板电机 ( V70 )01273 新鲜空气鼓风机 ( V2 )01274 通风翻板电机( V71 )01275 后侧安全气囊开关( E280 )01276 ABS 液压泵( V64 )01277 ABS 液压泵继电器 ( J185 )01278 EDS 电子差速锁关闭继电器 (J263)01279 加速度传感器( G251)01280 安全气囊: 乘客侧: 已经禁止01281 安全气囊: 司机侧: 已经禁止01282 进气歧管转换阀( N239 )01283 进气歧管翻板电机 ( V157 )01284 侧面安全气囊: 司机侧: 已经禁止01285 侧面安全气囊: 乘客侧: 已经禁止01286 安全带涨紧器: 司机侧: 已经禁止01287 安全带涨紧器: 乘客侧: 已经禁止01288 接线柱 30: 辅助转向01289 接线柱 15: 辅助转向01290 参考电压: 辅助转向01295 仪表板控制单元编码错误01296 外部温度传感器: 中央 ( G191 )01297 外部温度传感器: 地板 ( G192 )01298 仪表板指示灯测试01299 数据总线诊断接口 ( J533 )01300 控制单元: 带CD-Rom的导航系统 ( J401 ) 01301 控制单元: 语音识别 ( J507 )01302 控制单元: 信息通讯 ( J499 )01303 电话收发器01304 收音机01305 数据总线显示器01306 快速数据总线显示器01307 LWL 数据总线显示器01308 控制单元: 车顶( J528 )01309 控制单元: 辅助转向( J500 )01310 控制单元: 车身自调平( J197 )01311 数据总线: 信息/显示01312 数据总线: 动力系统01313 数据总线: 动力系统( 紧急情况 )01314 发动机控制单元01315 变速器控制单元01316 ABS 控制单元01317 在仪表板之内的控制单元 (J285)01318 控制单元: 喷射泵 ( J399 )01319 控制单元: Following Distance ( J428 )01320 控制单元: 全自动空调( J255 )01321 控制单元: 安全气囊( J234 )01322 控制单元: MFA01323 控制单元: 自动化离合器01324 控制单元: AWD 全轮驱动01325 控制单元: 轮胎压力监控01326 控制单元: 方向盘电器01327 控制单元: 停车辅助系统01328 数据总线设备01329 数据总线设备( 紧急情况 )01330 中央控制单元: 舒适系统 ( J393 )01331 门控制单元: 司机侧 ( J386 )01332 门控制单元: 乘客侧 ( J387 )01333 门控制单元: 左后 ( J388 )01334 门控制单元: 右后 ( J398 )01335 坐椅/镜子位置控制单元: 司机侧01336 舒适系统数据总线01337 内部门把手照明灯01338 信号: 门未关闭01339 Exit 警告灯01340 镜子调节开关01341 在仪表板之内的控制单元/舒适系统 CAN ( J285 ) 01342 发动机控制单元 2 ( 附加 1 )01343 发动机控制单元 3 ( 附加 2 )01344 HID ( Xenon ) 大灯01345 点火模块01346 发往点火模块的信号01347 发往[Gasentladungslampe]的信号01348 内部监控开关指示灯( K162 )01349 报警: 防盗警报系统: 前部01350 报警: 防盗警报系统: 后部01351 通讯信号接地01352 总线时钟信号: 前部 5V01353 总线时钟信号: 后部 5V01354 电子防盗器释放信号01355 信号: 所有窗户已经打开01356 信号: 所有窗户已经关闭并且 STR01357 油箱盖闭锁电机 ( V155 )01358 内部中央门锁开关: 司机侧 ( E150 )01359 内部中央门锁开关: 乘客侧 ( E198 )01360 防盗系统警报开关: 已经打开01361 防盗系统警报开关: 已经关闭01362 行李箱关闭开关 ( F124 )01363 中央门锁开关: 司机侧门( F59 )01364 中央门锁开关: 乘客侧门( F114 )01365 闭锁/解锁开关: 内部01366 已经打开由于碰撞信号01367 中央门锁真空泵运转时间超过 ( 类似于泄漏 ) 01368 报警: 行李箱开关01369 报警: 引擎盖开关01370 报警: 内部监控01371 报警: 门接触开关: 司机侧01372 报警: 门接触开关: 乘客侧01373 报警: 收音机地线连接01374 报警: 接线柱 1501375 发动机装置阀门: 1 档01376 RPM 信号: 喷射泵01377 防盗警报超声波传感器: 左侧 ( G170 ) 01378 防盗警报超声波传感器: 右侧 ( G171 ) 01379 内部监控开关 ( E183 )01380 报警: 防盗传感器: 左后01381 报警: 防盗传感器: 右后01382 报警: 防盗传感器: 左前01383 报警: 防盗传感器: 右前01384 报警: 玻璃破碎传感器01385 警报系统指示灯 ( K95 )01386 警报清除发生器01387 供给电压导线01388 定时信号导线01389 后挡板开启开关( F124 )01390 激活内部监控01391 模拟碰撞信号01392 后续输出: > 已经激活01393 车身自调平控制传感器 ( G84 )01394 车身自调平控制指示灯( K134 )01395 车身自调平控制压缩机马达 ( V66 ) 01396 支柱阀: 后部 ( N150/151 )01397 车身调平控制旁路电磁铁 ( N111 ) 01398 中央门锁信号线: 门开路01399 车身自调平控制压缩机继电器 ( J403 )。
大众常用标准汇总

一、焊接标准VW 01101类似国标中描述焊接类型并用图例表示的标准;对各种焊接进行了概括的介绍,并规定了各种标准的图示符号,是焊接里很概括的一章;eg:VW 01103凸点焊标准weld projection,图示表示了不同的凸点焊情况,规定了不同厚度的板件进行凸点焊时凸点的直径、高度等;eg:VW 01105点焊标准spot weld,详细介绍了点焊的设计思想、焊点排布、强度计算和校合,以及焊接头的布置和形状参考,有图示、查表表格和例题,教科书般的详尽标准;规定了焊接点的熔深要求、焊接头大小标准、缩印要求;焊接后表面等级OG1\OG2\OG3的定义;规定了图纸表注标准;使用此标准焊接的熔深、劈凿或者母材撕裂都以VW01105为认可标准Acceptance criteria;实验方法也定义为VW01105,实际上此标准内第3 章有具体的实验标准比如PV6702等;考虑到VW01105比较全面而且大众认可,所以不把具体的小标准作为实验方法;VW 01105-2 针对铝制金属的特殊焊接要求,包括特殊的熔深、劈凿要求;eg:VW 01105-3 镀锌合金的特殊焊接要求,对焊板、焊接头有比较详细的描述,对校合计算过程有详细介绍, 熔深和劈凿依然参考VW01105-1;VW 01105-4 针对大厚度钢和高强度钢的焊接标准,介绍了特殊的技术要求和过程控制;介绍了“焊接强度——焊接时间”图,介绍了标准的图纸表注方法;eg:VW 01106弧焊、二氧化碳保护焊、熔焊标准;规定了图纸标注的标准;详尽规定了不同钢板焊接时的要求和标准,图例表示了各种焊接情况下焊缝的形式;介绍了应力计算标准、涂层材料;规定了不同钢材焊接时焊缝的评估标准;认可标准和实验方法均为VW 01106;eg:VW 01141激光焊接;标准不详,POLO上有使用,总体使用较少;二、表面处理标准VW 50详细描述了针对不同零件的表面处理方式的要求,介绍了图纸标注方法;eg:规定了不同载荷下表面处理的等级要求;规定了图纸标注方法;图表介绍了不同代号的表面处理含意;eg:图上有上标标注的一般是规定新的设计中不再使用这种标注方式,要根据文后付注中的要求进行处理;三、塑料件常用标准TL 1010非金属件阻燃性标准;介绍了各种缩写的含义,规定了距离乘客不同距离的非金属件的测试要求;规定非金属燃烧速率小于100mm/min;测试认可标准为TL1010, 实验方法为TL1010 与VW01105同样的道理,实际上直接的实验方法为标准中规定的PV 3904;GB8410,由于在中国内生产的原因,必须遵守中国的强制性法规GB8410-2006,同样是阻燃性标准;VW 50180挥发性要求;描述了不同的测试项目对应的实验标准、方法;附件有测试挥发性需要提交的完整表格;TL 52476POM材料标准;包括色调、密度、熔化温度和特性等等;四、环境要求VW 91101环境保护文件,概括说明汽车环境中的材料不得包含有害物质;一般运用在金属材料的标注中,防止有害金属污染环境或对人体产生伤害;eg:五、泡沫相关标准DIN_53579泡沫测试标准;解释图纸标注含义,规定了对测试机器的要求;图表表示了不同标准的压头的大小、压力使用要求;eg:规定了测试方法,以及具体的对不同厚度的泡沫测试硬度的不同要求;六、图纸上通常在右上角标注但实际操作中不太直接用到的标准;DIN_EN_10051热轧钢标准,针对原材料;规定了钢材原材料的厚度公差,规定了不同型号的钢材相对应的不同的标准;eg:规定了德国、欧洲、法国钢材标准的对照表;DIN_1451字体规定;规定了图纸、运输中字体的详尽比例、尺寸;DIN_EN_10130冷轧钢标准,针对原材料,不包含宽度小于600mm的窄型冷轧钢;冷轧钢各种规定概述,包括表面处理、机械性能、检测方法规定、样件规定、实验机器规定等;用图表列举出不同型号钢材的性能;DIN_EN_13131规定了冷轧钢原材料不同厚度、宽度钢材的厚度公差;DIN_EN_10149高强度热轧钢或特殊钢标准,针对原材料;概括了运输条件、钢材化学成分、表面处理、检测标准、方法、钢卷规定、尺寸、重量、公差等;图表列举了德国、法国、英国等钢牌号的对应关系;DIN_EN_10263 圆钢、圆条盘簧、钢丝标准,针对原材料;概括了运输条件、化学成分、机械性能、硬度要求、表面处理、质量、信息要求;规定了各种分类标准、检查方法、标准等;DIN_EN_10270非合金冷拔钢丝标准,针对原材料;规定了钢丝的等级、各等级材料含量,表面处理,以及不同直径的钢丝的直径公差、强度、密度等;VD260 图纸标注法则;解释图纸标注的形式和方式,介绍了各种缩写的意义;VW10514 大众商标规格和尺寸;。
VW01155
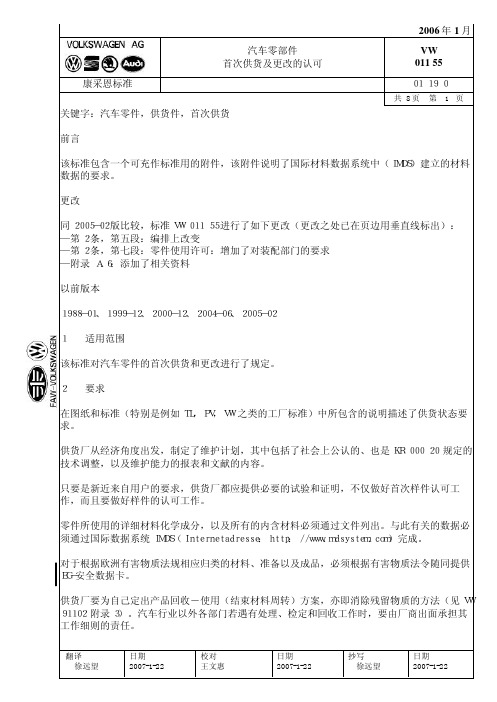
附件A(标准化)国际材料数据系统(IMDS)中材料数据卡(MDB)的技术要求 A.1 目的 本附件定义了大众公司接受国际材料数据系统(IMDS)的材料数据卡(MDB)时应遵循的准则。
要遵守这里面的规则,就必须避免: —首次样件过程中出现干扰 —从供货厂来的材料数据卡,必须进行校对,否则它将被大众公司拒绝。
A.2 适用范围 该标准适用于连同汽车一起交货给用户的配件,制品和全部物质材料,这些数据是首次样品试验报告的组成部分,它们最晚在首次样品试验之前必须提供。
A.3 符号 红色正方形是用来代表总成(ZSB),次总成(次ZSB)或一个单件。
红色正方形代表一个总成,在总成下一级也只允许红色正方形出现,因为它代表了组成该总成的所有零件。
黄色的圆圈代表半成品。
半成品就是有待继续加工的在制品。
半成品可以在下一级结构树中上由半成品组合而成。
半成品符号主要是用于卷轴纺织品(地毯),规定厚度的钢板,玻璃丝垫,坯件等等。
两个绿色小圆圈是表示材料的符号。
材料可以在下一级通过材料或高纯物质来描述。
材料可以通过外貌来描述,它们在成品中以何种形式存在(例如时效硬化的粘合剂,焙烧的油漆)。
符号用于复合材料及单一材料。
兰色三角形表示高纯物质。
高纯物质并不必然是化学概念上纯的物质,它也可能是一种混合物。
对这种物质,没有必要再把其各种成分区分开来。
高纯物质理应只归类于单一材料。
高纯物质特殊情况: —保密高纯物质(见 A.4.9条) —未知材料(见 A.4.10条) A.4 规则 接到材料数据卡(MDB)时,如下各种情况必须检查:—VW-零件号—零件名称—结构树(体系)—零件范围的完整性—材料名称—商品名称—材料分类按 VDA 231-106—保密高纯材料—未知材料(Joker)的应用—按VDA 232-101 的规定严格禁止的高纯材料和有义务申报的高纯材料—用于样件提供的数据(图号、图纸状态、供货厂代码) A.4.1 零件号 在“信息接收”卡中,VW 零件号是根据标准VW 01098给出。
大众奥迪车型电路图中电器系统原件代码查询说明
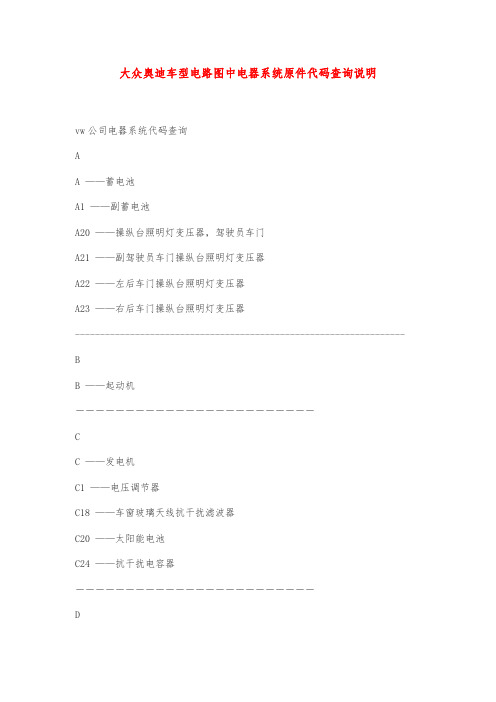
大众奥迪车型电路图中电器系统原件代码查询说明vw公司电器系统代码查询AA——蓄电池A1——副蓄电池A20——操纵台照明灯变压器,驾驶员车门A21——副驾驶员车门操纵台照明灯变压器A22——左后车门操纵台照明灯变压器A23——右后车门操纵台照明灯变压器------------------------------------------------------------------BB——起动机------------------------CC——发电机C1——电压调节器C18——车窗玻璃天线抗干扰滤波器C20——太阳能电池C24——抗干扰电容器------------------------DD8——读卡器------------------------E1——车灯开关E2——转向信号开关E3——闪烁报警开关E4——手动变光开关E5——远光灯瞬时接通开关E6——后部车内照明灯开关E7——前雾灯开关E9——新鲜空气鼓风机开关E15——加热式后风窗开关E16——加热/加热功率开关E18——后雾灯开关E19——驻车灯开关E20——照明调节器,开关和仪表(仪表小灯亮度调节)E22——间歇式车窗玻璃刮水器运行开关E23——前,后雾灯开关(POLO还包括了尾灯开关)E24——驾驶员侧安全带开关E25——副驾驶员侧安全带开关E26——手套箱照明开关E28——雨刮器间歇工作控制器E34——后刮水器的开关E38——刮水器间歇转换控制器E39——后车窗升降器装置的锁止开关E40——左前车窗升降器开关E41——右前车门玻璃升降器开关E43——后视镜调节开关E45——GRA开关E48——后视镜调节转换开关E52——左后车窗升降器开关(在车门上)E53——左后车窗升降器开关,驾驶员车门E54——右后车窗升降器装置开关(在车门上)E55——右后车窗升降器开关,驾驶员车门E62——驾驶员座椅前部高度调节开关E63——驾驶员座椅后部高度调节开关E64——副驾驶员座椅纵向调节开关E65——副驾驶员座椅前部高度调节开关E66——副驾驶员座椅后不高度调节开关E68——副驾驶员座椅导轨终端调节开关E72——对讲机按钮E75——报警装置开关E76——对讲机按钮【C6特种车辆装备】E77——左侧加热式后座椅开关E78——右侧加热式后座椅开关E81——右前车窗升降器开关,驾驶员车门E87——空调控制和显示单元E91——功能选择开关E92——复位按钮E94——加热式驾驶员座椅调节器E95——加热式副驾驶员座椅调节器E96——驾驶员座椅靠背调节开关E97——记忆装置操作单元【带记忆功能的驾驶员座椅操作单元】【C6】E98——副驾驶员座椅靠背调节开关E102——大灯照程调节器E107——车窗升降器开关(在副驾驶员车门中)E111——定时器E128——左侧可加热后座椅调节开关E129——右侧可加热后座椅调节开关E132——ASR功能开关E138——出租车标示开关E139——滑动天窗调节器E149——后窗遮阳卷帘开关E150——驾驶员侧车内连锁开关E155——头枕调整开关E159——新鲜空气和换气风门控制控制开关E165——尾门开锁开关E167——转向柱调整装置开关E168——带折叠(收缩)功能的后视镜调节开关E175——后座椅右侧腰部支撑调节开关E176——驾驶员座椅腰部支撑调节开关E177——副驾驶员侧座椅腰部调节开关E183——车内监控开关E190——紧急关闭按钮E198——开关,用于副驾驶员侧车内连锁(车门接触开关)E212——驾驶员座椅纵向向前调节按钮E213——驾驶员座椅纵向向后调节按钮E217——报警装置关闭开关E218——带记忆功能的座椅按钮1E219——带记忆功能的座椅按钮2E221——方向盘中的操作单元E222——驾驶员座椅倾斜度调节开关E224——安全气囊关闭钥匙开关,副驾驶员侧E229——警示灯按钮E230——后风窗除霜器开关E231——后视镜加热开关E233——尾门遥控开锁按钮E234——开锁开关,行李箱盖E237——抽烟雾开关E243——危险警报开启按钮1E247——危险警报开启开关E250——危险警报音调转换开关E251——音调可变的特殊信号开关E252——特殊信号装置开关【C6防弹车】E253——对讲装置讲话按钮E255——定时器开关E256——ASR/ESP的按钮开关E265——后部climatronic自动空调的操作和显示控制单元E266——驻车辅助按钮E267——车内监控功能抑制开关E270——行李箱中的警报触发开关【C6防弹车】E273——左后车内上锁开关E274——右后车内连锁开关E277——副驾驶员座椅记忆功能操作单元E283——带记忆功能的驾驶员座椅按钮E284——车库门开启操作单元E316——手套箱按钮开关E317——车内照明开关E318——儿童安全锁按钮E319——燃油箱盖开锁按钮E325——滑动天窗按钮E326——前部车内照明灯按钮E332——头枕调节开关E333——安全带高度调节按钮E334——副驾驶员座椅倾斜度调节按钮E335——腰部支撑高度调整按钮E336——腰部支撑前后调整按钮E337——按摩按钮E338——带记忆功能的座椅按钮1和2E340——带记忆功能的副驾驶员座椅按钮E350——座椅深度调整开关E363——驾驶员座椅纵向调节开关E364——驾驶员座椅高度调节开关E365——副驾驶员座椅高度调节开关E368——武器箱按钮E369——驾驶员侧车门外把手中央门锁按钮E370——副驾驶员侧车门外把手中央门锁按钮E371——左后车门外把手中央门锁按钮E372——右后车门外把手中央门锁按钮E380——多媒体装置操作单元E383——左后侧卷帘按钮E384——右后侧卷帘按钮E385——后窗遮阳卷帘开关E392——车库门遥控器按钮1E393——车库门遥控器按钮2E394——车库门遥控器按钮3E406——后行李箱盖上锁按钮,在行李箱盖内E408——发动机启动/停止按钮【进入及起动许可按钮】E415——进入及启动许可开关E418——座椅前后调整开关E421——倾斜度调整开关E424——座椅高度调整开关E425——靠背调节开关E438——方向盘上部手动电控换档程序开关E439——方向盘下面的手动电控换挡程序开关E440——方向盘左侧的多功能开关E441——方向盘中的右侧多功能按钮E453——左后车内照明灯开关1E457——驾驶员侧阅读灯按钮E458——副驾驶员侧阅读灯按钮E461——前部中央控制台操作单元E462——前部显示屏的打开/关闭按钮E466——副驾驶员侧紧急关闭按钮E467——后车顶模块(天窗)操作单元E485——出租车报警系统激活按钮E486——出租车报警激活系统关闭按钮E487——免提通话按钮【C6特种车辆警车等】E489——发动机连续运转按钮E490——蓝色警告灯按钮E493——组合仪表操作按钮E505——特种信号转换开关【C6特种车辆警车等】E506——显示单元按钮E507——特种信号操作单元【C6特种车辆警车等】E510——左侧儿童安全锁按钮E511——右侧儿童安全锁按钮E512——驾驶员车门中的车窗升降器操作单元E522——方向盘加热按钮开关E532——车内照明关闭按钮-------------------------F——制动灯开关F1——机油压力开关F2——驾驶员—侧车门接触开关F3——副驾驶员侧车门接触开关F4——倒车灯开关F5——行李箱照明开关F8——强制低速开关F9——手动刹车控制的开关F10——左后车门接触开关F11——右后车门接触开关F18——冷却风扇热敏开关F34——制动液液面不足显示开关F34-制动液液面警报信号触点F36——离合器踏板开关F38——车外温度开关F47——车速控制装置(GRA)/柴油喷射制{动踏板开关}动踏板开关F47——C62.0T BPJ发动机制动踏板开关F54——冷却风扇热敏开关F66——冷却液不足显示开关F73——A/C低压开关F77——风窗清洗液警报触点开关F88——动力转向压力开关F96——大气压力/海拔高度传感器F118——A/C高压开关F120——发动机引擎盖子防盗报警接触开关F123——后盖中的防盗报警装置接触开关F124——行李箱锁/防盗警报装置/中央门锁接触开关F125——多功能开关F129——空调压力开关G130——尾气催化净化器后的氧传感器F131——左前门中央门锁执行元件F132——左后车门中央门锁执行元件F133——右前门中央门锁执行元件F134——右后车门中央门锁执行元件F137——ABS压力控制开关F138——安全气囊/带滑环的回位环螺旋弹簧{安全气囊卷簧和带滑环的复位环} F145——开关:左后座安全带F146——开关:右后座安全带F147——驾驶员一侧化妆镜接触开关F148——副驾驶员一侧化妆镜接触开关F158——安全带张紧器开关1F189——tiptronic手动电控换挡程序开关F189——Tiptronic开关F194——发动机起动离合器踏板开关F206——行李箱锁开关F218——中央门锁/行李箱锁开关F220——中央集中控制门锁单元(驾驶员侧)F221——中央集中控制门锁单元(副驾驶员侧)F222——中央集中控制门锁单元(左后)F223——中央集中控制门锁单元(右后)F234——驻车制动器压力开关F241——驾驶员侧车门锁接触开关F243——驾驶员车门锁接触执行元件(安全)F244——副驾驶员车门中央门锁执行元件(安全)F245——左后车门中央门锁执行元件(安全)F246——右后车门中央门锁执行元件(安全)F248——行李箱锁打开按钮F266——发动机舱盖接触开关F272——驾驶员侧车门外把手开关F273——副驾驶员侧车门外把手开关F274——左后车门外把手开关F275——右后车门外把手开关F305——变速器位置P识别开关F320——双氙气灯遮蔽电磁开关F321——手制动开关F332——关闭辅助功能极限开关,行李箱已经开锁状态识别开关F333——关闭辅助功能极限开关,行李箱已经闭锁状态识别开关F344——左后儿童安全锁接触开关F345——右后儿童安全锁接触开关F350——卷簧F354——手轮上的接触开关F355——锁止销上的接触开关----------------------G——燃油表传感器G1——燃油表G2——冷却液温度传感器G3——冷却液温度表G4——曲轴位置传感器G5——转速表G6——燃油泵(供油泵/预供应油泵)G9——机油温度表G14——电压表G17——外部温度传感器G18——温度传感器G19——空气流量计位置传感器G21——车速表G22——车速表传感器(霍尔传感器,在变速器上)G24——行车记录仪G28——发动机转速传感器G31——增压压力传感器G32——冷却液不足指示器的传感器G33——车窗玻璃清洗液液位传感器G34——左前制动摩擦片磨损传感器G35——右前制动磨擦片磨损传感器G38——变速器转速传感器G39——λ传感器G40——霍尔传感器G41——出租车计价器【C6特种车辆】G42——进气温度传感器G44——右后轮转速传感器G45——右前轮转速传感器G46——左后轮转速传感器G47——左前轮转速传感器G52——前部蓄电池温度传感器G53——后部蓄电池温度传感器G56——仪表板温度传感器G59——驾驶员座椅温度传感器G61——爆震传感器1G62——冷却液温度传感器G65——高压传感器G66——爆震传感器2G68——行驶速度传感器G69——节气门位置传感器G70——空气流量计G71——进气压力传感器G72——进气管温度传感器G74——CO电位计G76——车身自调平系统传感器:左后G77——车身自调平系统传感器:右后G78——左前汽车高度传感器G79——油门踏板位置传感器G80——针阀行程传感器G82——发动机(流出口)冷却液温度传感器G83——发动机(冷却器流出口)冷却液温传感器G85——方向盘转向角度传感器G89——新鲜空气进气温度传感器G90——垂直运动加速度传感器G92——温度活板伺服马达位置电位计G93——机油/变速器油温度传感器G95——右侧后座椅温度传感器G99——滑阀开度传感器G100——刹车踏板位置传感器G101——液压油泵传感器G102——后桥垂直加速传感器G104——安全气囊减速度传感器;左侧G105——安全气囊减速度传感器;右侧G106——外部温度指示器G107——阳光强度光敏电阻G108——λ传感器2G109——环境温度传感器G110——发动机冷却液温度传感器G112——中面翻板伺服电机电位计G113——通风翻板伺服电机电位计【速滞压力风门伺服马达电位计】G114——脚坑/除霜翻板伺服马达电位计G115——避震弹簧位移传感器:左前G116——避震弹簧位移传感器:右前G119——负荷传感器G120——水位传感器G121——加速度传感器:右前G123——减速度传感器G127——节气门位置传感器(G127)G128——安全气囊坐椅占用传感器G130——催化转换器后的λ传感器G131——催化转换器后的λ传感器2G135——除霜翻板伺服电机电位计G136——左中通风电机位置传感器G138——中间通风电机位置传感器G139——右侧脚坑翻板电机位置传感器G140——右侧脚坑翻板电机位置传感器G141——后部脚坑翻板电机位置传感器G142——中央通风电机位置传感器G143——伺服马达上的换气风门电位计【车内空气循环风门伺服马达电位计】G144——EVAP翻板电机位置传感器G146——蓄电池(电动车)通风系统传感器G147——驾驶员气体避震弹簧压力传感器G148——乘客侧气体避震弹簧压力传感器G149——调节滑杆行程传感器G150——左出风口温度传感器G151——右出风口温度传感器G152——前出风口温度传感器G153——后蒸发器温度传感器G154——后加热器温度传感器G155——左侧出风口温度调节器G156——右侧出风口温度调节器G163——霍尔传感器2G169——燃油存量传感器2G170——防盗警报左侧超声波传感器G171——防盗警报右侧超声波传感器G177——驾驶员侧后部座椅占用传感器G178——副驾驶员侧后部座椅占用传感器G179——驾驶员侧侧面安全气囊碰撞传感器G180——副驾驶员侧侧面安全气囊碰撞传感器G182——变速器输入转速传感器G183——左后玻璃破裂传感器G184——右后玻璃破裂传感器G185——油门踏板位置传感器2G186——节气门驱动装置(电子油门操纵机构)G187——节气门角度传感器1(电子油门操纵机构)G188——节气门角度传感器2(电子油门操纵机构)G189——过热传感器【驻车加热系统C6】G191——出风口温度传感器,中间G192——脚坑出风口温度传感器G200——横向加速度传感器G202——偏转率《横向加速度》传感器G203——左后倒车警报传感器G204——左后中部倒车警报传感器G205——右后中部倒车警报传感器G206——右后倒车警报传感器G212——EGR废气在循环系统电位计G220——左侧温度翻板伺服电机电位计G221——右侧温度翻板伺服电机电位计G222——左前轮胎压力传感器G223——右前轮胎压力传感器G224——左后轮胎压力传感器G225——右后轮胎压力传感器G227——驾驶员座椅纵向调节传感器G230——驾驶员座椅靠背调节传感器G231——驾驶员座椅高度调节传感器G232——驾驶员座椅倾斜调节传感器G238——空气质量传感器G247——燃油压力传感器G250——辅助转向开关G252——右前泊车辅助传感器G253——右前中部泊车辅助传感器G254——左前中部泊车辅助传感器G255——左前泊车辅助传感器G256——驾驶员侧后部侧面安全气囊碰撞传感器G257——副驾驶员侧后部侧面安全气囊碰撞传感器G263——出风口温度传感器,蒸发器,在蒸发器上方G266——机油油面高度/温度传感器,技术保养周期G267——温度选择钮电位计G273——车内监控传感器G283——驾驶员侧前部安全气囊碰撞传感器G284——副驾驶员侧前部安全气囊碰撞传感器G289——右前汽车高度传感器G290——水平高度调节系统压缩机温度传感器G291——水平高度调节系统的压力传感器G304——后窗玻璃破碎传感器G315——前冷风门伺服马达电位计G330——间接通风风门伺服马达电位计G336——进气管风门电位计G341——左前车身加速度传感器G342——右前车身加速度传感器G343——后部车身加速度传感器G344——左前座椅温度传感器G345——右前座椅温度传感器G347——左侧中间出风口传感器G348——右侧中间出风口开关G357——转向柱上下调整传感器G358——转向柱前后调整传感器G384——车辆倾斜角度传感器G387——左前仪表板出风口电位计G388——右前仪表板出风口电位计G395——制冷剂压力和温度传感器G397——雨量和光线识别传感器G410——低压的燃油压力传感器G415——驾驶员侧车门外把手接触传感器G416——副驾驶员侧车门外把手接触传感器G417——左后车门外把手接触传感器G418——右后车门外把手接触传感器G419——ESP传感器G428——可加热方向盘传感器G431——左前轮胎压力监控车轮腔内的发射器G432——右前轮胎压力监控车轮腔内的发射器G433——左后轮胎压力监控车轮腔内的发射器G434——右后轮胎压力监控车轮腔内的发射器G452——座位占用识别功能压力传感器G453——座位占用识别功能安全带拉力传感器G476——离合器位置传感器G474——左摆动模式定位传感器G475——右侧摆动模块位置传感器G514——驾驶员侧后视镜水平调节电位计G515——驾驶员侧后视镜垂直调节电位计G516——副驾驶员侧后视镜水平调节电位计G517——副驾驶员侧后视镜垂直调节电位计G518——左前制动压力传感器G519——右前制动压力传感器G551——驾驶员侧安全带拉力限制器-------------------------HH——信号喇叭操纵机构H2——高音喇叭H7——低音喇叭H12——报警喇叭H15——后部泊车辅助报警蜂鸣器H22——前部泊车辅助报警蜂鸣器--------------------I--------------------J1——闪光继电器J2——危险闪光继电器J4——喇叭继电器J5——雾灯继电器J6——稳压器(仪表内部JEEDA)J7——蓄电池断路继电器J8——停车加热继电器J9——可加热后玻璃继电器J17——燃油泵继电器J26——散热器风扇继电器J29——截止二极管(车门控制系统,典型应用在GOLF/BORA上)J31——清洗/雨刮-间歇继电器(JEEDA)J32——空调继电器J39——大灯清洗装置继电器J44——电磁离合器继电器J48——后风窗除霜器继电器J49——电动燃油泵继电器2J52——火化塞继电器J53——起动机继电器J59——X触点卸荷继电器(JEEDA)J69——启动机继电器J79——光电管组J81——进气歧管预热继电器(化油器车型装备)J99——可加热后视镜继电器J104——ABS控制单元(包括带EDS的)J105——ABS回油泵继电器J106——ABS电磁阀继电器J114——机油压力控制单元J119——多功能指示器(仪表内部组件)J123——灯泡控制器J126——新鲜空气鼓风机控制单元J130——超速切断控制器单元(仅仅用于USA规格捷达1.8L车型)J131——司机座椅加热控制单元J132——副司机座椅加热控制单元J135——散热器风扇第三级继电器J136——带记忆功能的座椅调节控制单元J138——散热器风扇启动控制单元J139——车窗升降和滑动天窗控制单元J140——延时关闭/内部照明控制单元J152——报警蜂鸣器J153——电磁离合器控制单元J162——加热控制单元(主要用于停车加热控制)J166——仪表照明放大器J189——自检系统控制单元J192——多点喷射控制单元(捷达王5V)J197——自动水平调节控制单元J201——保护二极管(空调系统压缩机保护)J207——启动锁止继电器(AUDI A6)(POLO126#)J208——氧传感器加热控制单元J213——GRA控制单元J215——左侧可加热后座椅控制单元J216——右侧可加热后座椅控制单元J217——自动变速器控制单元J218——仪表板控制单元J219——倒车灯继电器J220——多点喷射发动机控制单元J226——启动锁止及倒车灯继电器(AT车)J234——安全气囊控制单元J236——SERVOTRONIC控制单元J243——油压和冷却液报警及转速表控制单元(仪表JEEDA)J245——滑动车顶控制单元(主要用在GOLF/BORA/AUDI上)J248——柴油直接喷射引擎控制单元J250——电子调节减震器控制单元J255——自动空调控制单元【Climatronic控制器】J262——后风窗电动卷帘控制单元J267——后视镜记忆功能控制单元J268——动力转向位置传感器J269——动力转向压力传感器J271——多点喷射供电继电器(编号428,主要用在GOLF/BORA上)J276——控制单元:遥控/中央门锁J278——氧传感器加热器继电器J285——带显示器的控制单元,在仪表内(泛指仪表)J293——冷却风扇控制单元J299——二次空气喷射泵继电器(控制号100,主要用在GOLF/BORA上)J301——防盗控制单元(第二代防盗系统)/空调控制单元J317——供电—接线30的供电继电器J329——总线端K1.15供电继电器J338——节气门控制单元J343——左侧气体放电灯控制器J344——右侧气体放电灯控制器J345——拖车识别装置控制单元J347——超声波传感器控制单元J351——后视镜收缩功能控制单元J355——太阳能模式控制器J361——SIMOS控制单元(主要用在GOLF/BORA上)J362——防盗器控制单元(第三代防盗,仪表内部组件)J364——辅助加热装置控制单元J367——蓄电池监控控制单元J379——中央门锁以及防盗报警控制单元(主要用在GOLF/BORA上)J386——车门控制单元,司机一侧J387——车门控制单元,副司机侧J388——车门控制单元,左后车门J389——车门控制单元,右后车门J393——舒适系统中央控制单元(包含了车内监控功能主要用在GOLF/BORA/A4上)J400——刮水器马达控制单元J401——带CD光盘驱动器的导航控制系统的控制单元J403——水平高度调节系统压缩机继电器J412——车载电话控制单元J413——信号喇叭继电器J428——车距控制单元J429——中央门锁控制单元J431——大灯光线水平调整控制单元J445——燃油冷却泵继电器(TDI)J446——超声波倒车报警系统控制单元J448——4AV/4LV/4MV控制单元J453——多功能方向盘控制单元J476——危险警报控制器J489——无线电时钟接收器J492——四轮驱动控制单元(主要用在GOLF/BORA和早期A4上)J495——二次空气泵继电器(V8/TDI)J496——冷却泵辅助继电器J500——转向助力控制单元(电动助力转向系统POLO)J502——轮胎压力监控单元J503——带显示器的控制单元(用于收音机或者导航系统)J505——可加热风档玻璃控制单元J507——收音机R和语音输入控制单元J509——动力转向电机继电器J518——访问和启动授权控制单元J519——车载电源(电网)管理控制单元J520——车载电网控制器2【C6】J521——副驾驶员侧带记忆功能的座椅调整装置的控制单元J522——带记忆的后部座椅调节控制单元J523——前部信息显示和操作单元的控制模块J525——数字式声音套件控制单元J526——电话/电子通讯系统控制单元J527——转向柱电子装置控制单元J528——天窗电子系统控制单元J530——车库门开启装置控制单元J533——数据总线诊断接口,在组合仪表内(支持自诊断的仪表系统)网关J536——增压空气冷却泵继电器(V8TDI)J537——4MV的控制单元(喷射装置)J538——燃油泵控制器J540——电动驻车制动器和手制动器控制单元J542——制动助力控制单元J545——二次空气喷射泵继电器(VR12)J546——行李箱盖开启控制单元J555——风扇控制器J559——交通信息控制单元J569——制动助力继电器J587——换档杆传感器控制器【奥迪C6]J605——尾门控制单元J608——特种车辆控制器J616——信号装置控制器J623——发动机控制单元J643——燃油预供应继电器(404#)J644——电源管理系统控制单元J648——左后信息显示和操作控制单元J649——右后信息显示和操作控制单元J655——蓄电池断开继电器J657——关闭辅助功能控制器【行李箱开启控制单元C6选装】J667——左侧大灯电源模块J668——右侧大灯电源模块J671——冷却液风扇控制器2J676——芯片卡读卡器控制器J680——供电继电器1—总线端K1.75J681——供电继电器2—总线端K1.15J682——接线端50供电继电器{帕萨特cc}继电器编号433J685——前部信息显示和操作单元的显示单元J690——左尾灯控制单元J691——右尾灯控制单元J692——尾门尾灯控制单元J693——尾门右侧尾灯控制单元J694——端子75x供电继电器J695——起动机继电器2(J706——座位占用识别功能控制器J711——清洗液加热装置继电器J723——无匙进入系统天线读入单元J728——显示和操作单元的转换装置【C6日本规格】J745——弯道灯和大灯照明距离调节控制器J749——辅助加热装置燃油泵继电器J756——后盖控制器2J757——发动机部件供电继电器J764——电控转向柱锁止装置控制单元J769——辅助变道系统控制单元J770——辅助变道系统控制单元2J771——闭锁继电器【C6驻车暖风系统】J772——倒车摄像头控制单元J791——驻车转向辅助系统控制单元J800——踏步灯继电器(POLO449#)J801——左门踏步灯继电器(POLO449#)J802——右门踏步灯继电器(POLO449#)E87——空调控制和显示单元---------------------------------KK3——机油压力指示灯【C6】K4——停车灯的指示灯K13——后雾灯指示灯K17——前雾灯指示灯K28——冷却液温度和冷却液不足显示指示灯【C6】K32——制动摩擦片指示灯K106——清洗液不足指示灯【C6】K118——制动系统指示灯【C6】K133——中央门锁Safe功能指示灯K136——泊车辅助指示灯K139——驻车制动器指示灯【C6】K145——副驾驶员侧安全气囊关闭指示灯K213——电动驻车制动器和手制动器指示灯K214——电动驻车制动器和手制动器故障指示灯K226——锁闭拖车挂钩的指示灯K227——解锁拖车挂钩的指示灯----------------------LL5——旋转警告灯炮L9——大灯开关照明灯泡L13——左侧气体放电灯L14——右侧气体放电灯泡L15——烟灰缸照明灯泡L22——左侧前雾灯灯泡L23——右侧前雾灯灯泡L28——点烟器照明灯泡L36——出租侧车顶标志灯泡L46——左侧后雾灯灯泡L47——右侧后雾灯灯泡L48——左后烟灰缸照明灯泡L49——右后烟灰缸照明灯泡L65——照明灯泡,滑动天窗开关内L67——左侧仪表板出风口照明灯泡L68——中间仪表板出风口照明灯泡L69——右侧仪表板出风口照明灯泡L87——后座中间出风口照明灯L88——后座左出风口照明灯泡L89——后座右出风口照明灯L108——驾驶员侧车门开门器照明灯泡L110——左后车门开启照明灯L111——右后车门开门器照明灯泡L121——杯架照明灯泡L163——右前车门外把手照明灯泡L164——驾驶员车门操纵台照明灯泡L165——副驾驶员车门操纵台照明灯泡L166——左后车门操纵台照明灯L167——右后车门操纵台照明灯L174——左侧白天行车灯灯泡L175——右侧白天行车灯灯泡L178——带灯管和文字的特种信号装置-------------------------MM1——左侧停车灯灯泡M2——右侧尾灯灯泡M3——右侧停车灯灯泡M4——左侧尾灯灯泡M5——左前转向信号灯灯泡M6——左后转向信号灯灯泡M7——右前转向信号灯灯泡M8——右后转向信号灯灯泡M9——左侧制动信号灯灯泡M10——右侧制动信号灯灯泡M16——左侧倒车灯灯泡M17——右侧倒车灯灯泡M18——左侧侧面转向信号灯灯泡M19——右侧侧面转向信号灯灯泡M25——高位制动信号灯灯泡M29——左侧近光灯灯泡M30——左侧远光灯灯泡M31——右侧近光灯灯泡M32——右侧远光灯灯泡M33——左前示宽灯灯泡M34——右前示宽灯灯泡M37——后左侧面示宽灯灯泡M38——后右侧面示宽灯灯泡M47——左侧闪光灯M48——右侧闪光灯--------------------------。
大众汽车标准_VW_01105-1_电阻点焊
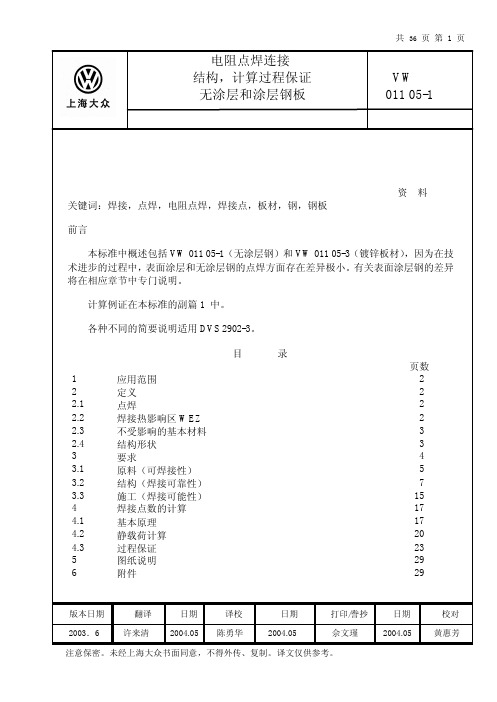
共36页第 1 页关键词:焊接,点焊,电阻点焊,焊接点,板材,钢,钢板前言本标准中概述包括术进步的过程中,将在相应章节中专门说明。
计算例证在本标准的副篇各种不同的简要说明适用12变更 相对于VW 011 05-1:2003-05有如下更改处:-第4.3.1节公差一章增加较小的点焊直径和松动的焊接点内容。
先前版本 1977-05;1993-12;2003-051应用范围 下列基本原则是以少批量到大批量机械化点焊程度和研究结果的经验为基础,以及公开发表的标准和技术规则,例如DVS-规则2902-1,-2,-3。
本标准适用有关静态和动态要求的电阻点焊的钢板结构的形状、计算和实施,在其他的文件中称之为“点焊连接”。
本标准应用范围包括接口点焊连接上的(电阻)点焊(特性因数21按照DIN EN ISO 4063),其在无涂层的板材上的板材厚度比例,板材厚度从0.5~4 mm,以及有关单点和多点焊接的过程保证的质量特征。
在特殊情况下,遇到较大的板材厚度和比例情况请与专业部门进行协调。
按照DIN EN 10 139使用的板材其厚度最多只能够是3.0 mm 。
引进镀锌板材,例如按照DIN EN 10 142或DIN EN 10 292, 和高和高硬度钢的部件要求具备直径较大的电极罩和电极套筒(16 mm 及 20 mm)。
该电极的部件上,当点焊法兰盘发生弯曲时焊核脱离连接片部位。
随着焊核与连接片之间出现的增大的距离现象构件的坚固性和构件强度随之降低。
另外有关(电阻)点焊连接的要求包括:VW 011 05-2(铝材料)VW 011 05-4(多板材连接;两层和多层接口的点焊连接)有关点焊连接的质量评审是检验标准PV 6702和PV 6717中给出的方法。
2 定义 2.1点焊 进行(电阻)点焊连接时,在所连接部分之间的焊接区域,通过电阻加热的方法借助于同时作用的焊条对零件的压力,加热直至其熔化。
尺寸、形状和被熔化的基材的位置取决于在焊接区域和环境中所产生的时间和空间的相互作用和散发的热量。
- 1、下载文档前请自行甄别文档内容的完整性,平台不提供额外的编辑、内容补充、找答案等附加服务。
- 2、"仅部分预览"的文档,不可在线预览部分如存在完整性等问题,可反馈申请退款(可完整预览的文档不适用该条件!)。
- 3、如文档侵犯您的权益,请联系客服反馈,我们会尽快为您处理(人工客服工作时间:9:00-18:30)。
Vertragspartner erhalten die Norm nur über die zuständige Beschaffungsabteilung.Confidential. All rights reserved. No part of this document may be transmitted or reproduced without the prior written permission of a Standards Department of the Volkswagen Group.Parties to a contract can only obtain this standard via the responsible procurement department.© VOLKSWAGEN AGN o r m v o r A n w e n d u n g a u f A k t u a l i t ät p r üf e n / C h e c k s t a n d a r d f o r c u r r e n t i s s u e p r i o r t o u s a g e .T h e E n g l i s h t r a n s l a t i o n i s b e l i e v e d t o b e a c c u r a t e . I n c a s e o f d i s c r e p a n c i e s t h e G e r m a n v e r s i o n s h a l l g o v e r n .Page 2VW 011 05-4: 2001-04•The perpendicular contact of the electrodes must be ensured by the design of the part.•Special electrodes are not permitted (i.e. ensure accessibility for standard electrodes).•The use of adhesives between the sheets requires further testing and coordination between the operator, planning department, quality assurance department and the design engineering department.•Zinc layers are permitted up to a maximum nominal thickness of 12 µm per side.•Individually zinc-coated sheets are not permitted.•All 3-sheet weld points must be accessible on the finished welding group for test purposes.•The component fit must be ensured (requirement for R&D and the planning department, the supply part supplier and the production department).•3-sheet point flanges in the welding group drawings and data models must be represented asa section such that the accessibility of the tongs can be assessed.•Flange widths shall be calculated according to VW 011 05 – 1.•When determining the point diameter d P (destructive testing) or the nugget diameter d L (trans-verse microsection), respectively, the smallest sheet thickness of the relevant joining plane is relevant (see Figure 1).Figure 1 - Nugget diameter in the joining planes2.2 Special Technical and Process-Specific Specifications•When planning new systems, automated welding of 3-sheets is preferred (in the case of man-ual production an increased level of testing shall be taken into consideration)•It must be possible to select an individual welding program for every spot weld.•Sufficient and even cooling of both electrodes is required (target: 4.0 l/min).•Electrode forces depending on the sheet thickness combination up to 5.0 kN (total sheet metal thickness of up to 4.5mm).•For permissible electrode penetration depths see VW 011 05-1.•Max. "movement" of the tong arms up to 1.5 mm (Caution: Note the throat depth, see design guideline 11-59D 6770 and VW 011 05-1).Page 3VW 011 05-4: 2001-04•3-sheet joints can be performed using 50Hz alternating current or with direct current (1000Hz medium frequency).•Medium frequency technology is recommendable (e.g. in the event of a very large throat opening and weight problems arising because the medium frequency transformer weight is less, or if a very fast adjustment is required).•Pulsation welding is recommended for coated sheets. Weld times (process time) >1000ms must be given general consideration during cycle time studies.•Welding using copper back-up bars is not permissible. Direct welding is required.•Cap milling with start milling required (flange and work surface milling).•The aim when determining the weld parameters: required shear diameter (d pmin) +20%. Pay due consideration to milling cycles in cycle time studies.•Process reliability when determining parameters: Welding range of min. 1.5 kA in width, see Figure 2.Weld time t[Periods]A Spot weld too smallS SpatteringD∆ > 1.5kAWelding current I [kA]Figure 2 - Welding range•For rows of weld points, the orientation of the welding tongs may not be changed (polarity!).•Increased vigilance is required with regard to leakages (e.g. equipment, fault current monitor-ing, point spacing). Flange width a shall if required be greater than that calculated according to VW 01105-1. The required extra width shall be coordinated between the design engineering department, the planning department and the operator and specified in the drawing.•Due to the influence of the coating, there shall not, wherever possible, be any change in coat-ing from point to point.•Control technology: Only weld, once the required force has been completely built up.Page 4VW 011 05-4: 2001-042.3 References in DrawingsAn overview of all 3-sheet points in the assembly shall be given.The nugget diameter must be indicated for every joining plane (d L1, d L2, see Figure 1 and Figure 3).Legend:d L1, d L2,Nugget diametern Number of pointse Point spacingv Peripheral spacingOG2Surface quality class (see VW 011 05-1)Figure 3 - Representation in drawings3 Referenced StandardsVW 011 05 – 1Resistance Spot Weld Joints,Design, Calculation and Process Monitoring;Uncoated SteelsOperating equipment design guideline 11-59D 6770。