表面粗糙度理论与标准的发展
表面粗糙度标准

表面粗糙度标准粗糙度是指表面的粗糙程度,是表面性能的关键因素之一,是表面技术中重要的指标。
表面粗糙度是定量评价表面质量的技术指标。
表面粗糙度对工件表面加工精度、润滑性能及表面耐磨性有着重要的影响,因此引起了人们广泛重视。
表面粗糙度根据形貌计算方法、设备可测量表面粗糙度的细、细节等形式分类。
根据原理从表面粗糙度测量方法分为实际检测法和理论检测法。
实际检测法关注的是表面的粗糙度的实际测量结果,其主要标准包括:表面抛光度、表面粗糙度、表面失真率和表面形貌。
理论检测法则涉及到表面粗糙度的理论计算,它把表面粗糙度从表面形貌的角度分析出来,综合考虑表面的凹凸等因素,然后根据测量范围内的数据计算出来。
表面粗糙度的标准化是控制和调整表面粗糙度的关键环节。
特别是在各种表面技术的发展和新的表面技术的出现,表面粗糙度的标准化越来越受到重视。
根据表面技术的不同,表面粗糙度的标准可以分为表面抛光标准、表面粗糙度标准、表面失真率标准和表面形貌标准等。
表面抛光标准主要根据表面抛光件的表面抛光质量来定义,根据抛光件的表面形貌,评价抛光件的抛光质量。
它是表面粗糙度标准中最重要的一项,其中包括抛光质量的判定及抛光强度、表面光滑度的测量。
表面粗糙度标准的目的是评价表面粗糙度的大小,表面粗糙度标准的实施依赖于表面粗糙度测量仪器的可行性。
表面粗糙度的测量主要依靠抛光件的表面粗糙度、表面平滑度、表面弯曲度等多种参数,这些参数是表面粗糙度标准的主要指标。
表面失真率标准是根据表面失真率来进行评价表面技术质量的指标,失真率是表面粗糙度标准中最重要的指标,其实施依赖于表面失真率测量仪器的可行性。
由于表面失真率的测量技术比较复杂,失真率也是表面粗糙度标准中一项重要的指标,它可以衡量表面变形、抛光和锐度等基本特性。
表面形貌标准是指表面形貌的测量分析,探测表面形貌特征,并进行专业化计算和分析,反映出表面形貌状态和质量情况。
表面形貌分析仪器是表面粗糙度标准中必不可少的仪器,它可以探测表面凹凸形貌、曲线拟合、失真率等参数,可以用来分析表面的形貌、粗糙度和失真率。
表面粗糙度国家标准
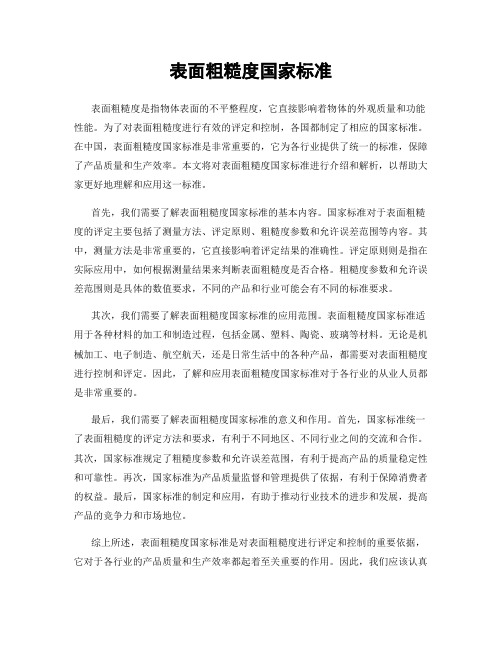
表面粗糙度国家标准表面粗糙度是指物体表面的不平整程度,它直接影响着物体的外观质量和功能性能。
为了对表面粗糙度进行有效的评定和控制,各国都制定了相应的国家标准。
在中国,表面粗糙度国家标准是非常重要的,它为各行业提供了统一的标准,保障了产品质量和生产效率。
本文将对表面粗糙度国家标准进行介绍和解析,以帮助大家更好地理解和应用这一标准。
首先,我们需要了解表面粗糙度国家标准的基本内容。
国家标准对于表面粗糙度的评定主要包括了测量方法、评定原则、粗糙度参数和允许误差范围等内容。
其中,测量方法是非常重要的,它直接影响着评定结果的准确性。
评定原则则是指在实际应用中,如何根据测量结果来判断表面粗糙度是否合格。
粗糙度参数和允许误差范围则是具体的数值要求,不同的产品和行业可能会有不同的标准要求。
其次,我们需要了解表面粗糙度国家标准的应用范围。
表面粗糙度国家标准适用于各种材料的加工和制造过程,包括金属、塑料、陶瓷、玻璃等材料。
无论是机械加工、电子制造、航空航天,还是日常生活中的各种产品,都需要对表面粗糙度进行控制和评定。
因此,了解和应用表面粗糙度国家标准对于各行业的从业人员都是非常重要的。
最后,我们需要了解表面粗糙度国家标准的意义和作用。
首先,国家标准统一了表面粗糙度的评定方法和要求,有利于不同地区、不同行业之间的交流和合作。
其次,国家标准规定了粗糙度参数和允许误差范围,有利于提高产品的质量稳定性和可靠性。
再次,国家标准为产品质量监督和管理提供了依据,有利于保障消费者的权益。
最后,国家标准的制定和应用,有助于推动行业技术的进步和发展,提高产品的竞争力和市场地位。
综上所述,表面粗糙度国家标准是对表面粗糙度进行评定和控制的重要依据,它对于各行业的产品质量和生产效率都起着至关重要的作用。
因此,我们应该认真学习和遵守国家标准的要求,不断提高对表面粗糙度的认识和应用水平,为推动行业的发展和提升产品质量做出积极的贡献。
表面粗糙度理论与标准的发展

1. 表面粗糙度理论与标准的发展表面粗糙度标准的提出和发展与工业生产技术的发展密切相关,它经历了由定性评定到定量评定两个阶段。
表面粗糙度对机器零件表面性能的影响从1918年开始首先受到注意,在飞机和飞机发动机设计中,由于要求用最少材料达到最大的强度,人们开始对加工表面的刀痕和刮痕对疲劳强度的影响加以研究。
但由于测量困难,当时没有定量数值上的评定要求,只是根据目测感觉来确定。
在20世纪20〜30年代,世界上很多工业国家广泛采用三角符号(▽)的组合来表示不同精度的加工表面。
为研究表面粗糙度对零件性能的影响和度量表面微观不平度的需要,从20年代末到30年代,德国、美国和英国等国的一些专家设计制作了轮廓记录仪、轮廓仪,同时也产生出了光切式显微镜和干涉显微镜等用光学方法来测量表面微观不平度的仪器,给从数值上定量评定表面粗糙度创造了条件。
从30年代起,已对表面粗糙度定量评定参数进行了研究,如美国的Abbott就提出了用距表面轮廓峰顶的深度和支承长度率曲线来表征表面粗糙度。
1936年出版了Schmaltz论述表面粗糙度的专著,对表面粗糙度的评定参数和数值的标准化提出了建议。
但粗糙度评定参数及其数值的使用,真正成为一个被广泛接受的标准还是从40年代各国相应的国家标准发布以后开始的。
首先是美国在1940年发布了ASAB46.1国家标准,之后又经过几次修订,成为现行标准ANSI/ASMEB46.1-1988《表面结构表面粗糙度、表面波纹度和加工纹理》,该标准采用中线制,并将R a作为主参数;接着前苏联在1945年发布了r OCT2789-1945《表面光洁度、表面微观几何形状、分级和表示法》国家标准,而后经过了3次修订成为:T OCT2789-1973《表面粗糙度参数和特征》,该标准也采用中线制,并规定了包括轮廓均方根偏差(即现在的R q)在内的6个评定参数及其相应的参数值。
另外,其它工业发达国家的标准大多是在50年代制定的,如联邦德国在1952年2月发布了DIN4760和DIN4762有关表面粗糙度的评定参数和术语等方面的标准等。
emd表面粗糙度标准_概述解释说明

emd表面粗糙度标准概述解释说明1. 引言在工程领域中,表面粗糙度是一个重要的参数,它对于材料表面质量和性能具有显著影响。
因此,表面粗糙度的测量与标准化已经成为质量控制与评估的必要步骤之一。
EMD表面粗糙度标准作为一种常用的评价方法,在工业生产和科学研究中得到了广泛应用。
本文旨在对EMD表面粗糙度标准进行概述解释和详细说明。
首先将介绍EMD 是什么以及它在表面粗糙度测量中的作用。
然后将阐述表面粗糙度的重要性,并探讨EMD表面粗糙度标准的发展历程和应用领域。
接下来,将详细介绍常用的EMD表面粗糙度测量方法,并介绍一些常用的参数来描述表面粗糙度特征。
同时,还会针对测量结果进行分析与解读,以便更好地理解和评估材料表面质量。
此外,本文还将通过对比分析EMD表面粗糙度标准与其他行业标准之间的差异和共同点,探讨EMD表面粗糙度标准在制造业和建筑行业中的应用情况,并对其他行业中类似的表面粗糙度标准进行比较。
最后,在结论与展望部分,将总结EMD表面粗糙度标准的重要性和应用价值,并对其不足之处进行讨论,提出改进方向。
同时,也将展望EMD表面粗糙度标准未来发展的可能性和前景。
通过本文的详细解释和阐述,读者将能够更全面地了解和掌握EMD表面粗糙度标准及其在工程领域中的应用。
同时,本文也为相关领域的研究者提供了参考和借鉴,以推动表面粗糙度测量方法的规范化和统一化。
2. EMD表面粗糙度标准:2.1 EMD是什么:EMD是英文“Equitemarked Dujidders”的缩写,意为“赋予杜耶斯尼音的振荡”。
EMD表面粗糙度标准是一种用于描述材料表面粗糙程度的标准,它基于杜耶斯尼音的时间与频率成分分析。
EMD表面粗糙度标准可用于对各种材料和工件的表面质量进行评估和比较。
2.2 表面粗糙度的重要性:表面粗糙度对于许多行业中的制造和加工过程来说都至关重要。
在制造业中,正确控制表面粗糙度可以确保产品性能、功能和寿命的稳定性。
钢板表面粗糙度的标准

钢板表面粗糙度的标准钢板表面粗糙度是指钢板表面的不平整程度,通常用于衡量钢板的质量和适用范围。
粗糙度的标准对于钢板的加工、制造和使用都具有重要的意义。
本文将对钢板表面粗糙度的标准进行详细介绍,以便读者对此有更深入的了解。
首先,钢板表面粗糙度的标准通常是根据国家标准或行业标准来制定的。
在中国,钢板的粗糙度标准主要由国家标准化管理委员会发布的国家标准来规定。
这些标准通常包括了对于钢板表面粗糙度的测量方法、测量工具、粗糙度值的要求等内容。
在实际生产和使用中,必须严格按照这些标准进行操作,以确保钢板的质量符合要求。
其次,钢板表面粗糙度的标准通常会根据不同的用途和要求进行分类。
例如,对于汽车制造领域来说,钢板表面粗糙度的要求可能会更加严格,因为汽车的外观和表面质量对于整车的质量和美观都有着重要的影响。
而对于建筑结构中使用的钢板来说,粗糙度的要求可能相对宽松一些,因为其主要作用是提供结构支撑和承载荷载。
因此,钢板表面粗糙度的标准需要根据具体的使用领域和要求来进行调整和制定。
另外,钢板表面粗糙度的标准也会受到生产工艺和材料特性的影响。
在钢板的生产过程中,不同的生产工艺和材料特性都会对钢板表面的粗糙度产生影响。
例如,热轧钢板和冷轧钢板的表面粗糙度就有所不同,因为它们的生产工艺和材料特性不同。
因此,在制定钢板表面粗糙度的标准时,必须考虑到这些因素,以确保标准的科学性和实用性。
最后,钢板表面粗糙度的标准对于质量控制和质量检验具有重要的意义。
在钢板的生产和使用过程中,必须对钢板表面的粗糙度进行严格的控制和检验,以确保钢板的质量符合要求。
只有通过科学合理的标准,才能够有效地进行质量控制和质量检验,从而保证钢板的质量和可靠性。
综上所述,钢板表面粗糙度的标准是钢板行业中非常重要的一部分,它直接关系到钢板的质量和使用效果。
只有通过严格的标准制定和执行,才能够保证钢板的质量和可靠性,促进钢板行业的健康发展。
希望本文对于钢板表面粗糙度的标准有所帮助,让读者对此有更加深入的了解。
表面din iso 1302 ra标准

表面din iso 1302 ra标准表面diniso1302ra标准是一种获得平滑表面粗糙度的国际标准,被广泛应用于各种表面加工,如研磨、珩磨和钻孔等,有效地提高加工表面的光洁度和精度。
它建立在可量化描述加工表面粗糙度的基础上,使得表面抛光形成和粗糙表面检测成为一项精准可行的标准,为生产改进提供了参考指南。
DIN ISO 1302 RA标准的发展始于20世纪50年代,当时德国着力于开发表面形貌测量及质量控制方面的技术,而后该标准不断发展,演进成为当今最新的表面测量和粗糙度控制标准。
该标准主要分为三个部分,即粗糙度测量、表面粗糙度定义和表面粗糙度测量装置。
粗糙度测量的基础是在测量中引入的几何形状及表面质量的测量方法,主要有视觉粗糙度测量和数字粗糙度测量两种。
其中,视觉粗糙度测量是指手持观察表面的粗糙程度,并用RA(Root Average)来衡量表面的光洁度;数字粗糙度测量是采用专用仪器来测量表面粗糙度,并用模糊数字值(Fuzzy Number)来衡量表面粗糙度。
这两种测量方法是德国DIN ISO 1302 RA标准中最重要且最常用的测量方式。
表面粗糙度定义根据表面粗糙度测量方法的不同而不同,在视觉粗糙度测量中,将表面粗糙度定义为RA (Root Average)系数;而在数字粗糙度测量中,将表面粗糙度定义为模糊数字值;在实际应用中,两者可以结合使用,也可以单独使用。
表面粗糙度测量装置是表面粗糙度的关键设备,它可以测量出表面粗糙度的大小,提供准确的粗糙度参数。
德国DIN ISO 1302 RA标准中,推荐使用的表面粗糙度测量装置为激光表面粗糙度测量仪,它可以对表面进行快速高精度的粗糙度测量,可以帮助检测表面粗糙度变化。
德国DIN ISO 1302 RA标准不仅提供了表面粗糙度测量和表面粗糙度调整的参考依据,而且为表面质量控制提供了详实的验证及调整过程,为表面精度的提高奠定了坚实的基础。
在表面抛光、表面处理、机械加工和机械设备等领域,DIN ISO 1302 RA标准都可以得到广泛应用,更加便捷、精确、快速地完成表面检测、表面抛光及粗糙度设定等过程,为行业发展和实现了质量改进打下了重要的基础。
公差配合的基本概念

公差配合的基本概念互换性概述 机械和仪器制造业中的互换性,通常包括几何参数(如尺寸)和机械性能(如硬度、强度)的互换,这里仅讨论几何参数 的互换。
允许零件尺寸和几何参数的变动量就称为“公差”。
零、部件在几何参数方面的互换性体现为公差标准。
而公差标准又是机械和仪器制造业中的基础标准,它为机器的标 准化、系列化、通用化提供了理论依据,从而缩短了机器设计时间,促进新产品的高速发展。
“尺寸”术语与定义 尺寸:用特定单位表示长度值的数字。
基本尺寸:是设计给定的尺寸。
实际尺寸:是通过测量获得的尺寸。
极限尺寸:是指允许尺寸变化的两个极限值。
最大实体状态(简称 MMC)和最大实体尺寸:最大实体状态系指孔或轴在尺寸公差范围内,具有材料量最多时的状态。
在此状态下的尺寸,称为最大实体尺寸,它是孔的最小极限尺寸和轴的最大极限尺寸的统称。
最小实体状态(简称 LMC)和最小实体尺寸:最小实体状态系指孔或轴在尺寸公差范围内,具有材料最少时的状态。
在 此状态下的尺寸,称为最小实体尺寸,它是孔的最大极限尺寸和轴的最小极限尺寸的统称。
作用尺寸:在配合面的全长上,与实际孔内接的最大理想轴尺寸,称为孔的作用尺寸。
与实际轴外接的最小理想孔的 尺寸,称为轴的作用尺寸。
“公差与偏差”的术语和定义 尺寸偏差:是指某一个尺寸减其基本尺寸所得的代数差。
尺寸公差:是指允许尺寸的变动量。
零线:在公差与配合图解(简称公差带图)中,确定偏差的一条基准直线,即零偏差线。
公差带:在公差带图中,由代表上、下偏差的两条直线所限定的一个区域。
基本偏差:是用来确定公差带相对于零线位置的上偏差或下偏差,一般指靠近零线的那个偏差。
当公差带位于零线上 方时,其基本偏差为下偏差;位于零线下方时,其基本偏差为上偏差。
标准公差:国标规定的,用以确定公差带大小的任一公差。
“配合”的术语和定义 配合:是指基本尺寸相同的、互相结合的孔和轴公差带之间的关系。
表面粗糙度培训教材(东京精密)
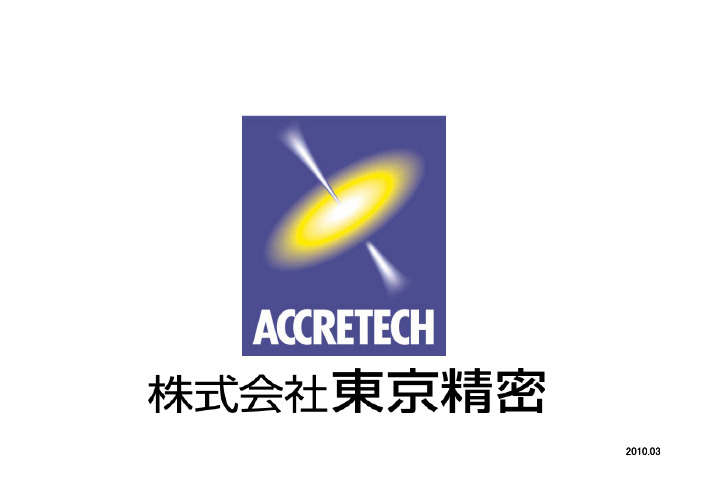
λ =h σ
σ: 复合粗糙度
σ = Rq12 + Rq22
Large roughness
Wear or damage
油膜 & 粗糙度 9
滑动摩擦力 & 粗糙度
• 滑动表面接触在少数微小的点上
■ 巨大的应力 ■ 支撑在接触点上 ■ 滑行运动在两表面间产生
摩擦力
■ 滑行轨道的特性 ● 提高硬度较少磨损 ● 降低 Rz以较少峰点间的应力集中度
Appearance area A
实际接触区域 ai
10
如何测量粗糙度?
1比较法 将被测表面与标有一定评定参数值的表面粗糙度样板比较 从判断被测表面的粗糙度。 2光切法 应用光切原理测量表面粗糙度的一种测量方法。按光切原 理制成的仪器叫做光切显微镜。这种方法用来测量Rz。 3干涉法 利用光波干涉原理测量表面粗糙度的一种方法。按干涉原 理制成的仪器叫做干涉显微镜,一般用来测量粗糙度值要 求低的表面 4针描法 接触式测量表面粗糙度的方法,最为常见。
Surfcom - 仪器结构
立柱
与工件竖直宽度垂直 Z轴
X轴
来回移动
驱动部
工件实表面
测针
放大器
测针顶端形状
θ rtip
θ= 60°(or 90°) r tip = 2μm (or 5,10μm)
工件
夹具 / 定位
测针 (Pickup)
LVDT (模拟) 测针压力 : 0.75mN
(测针顶端为0.2 μm)
粗糙度的参数
主要参数说明
间距参数
n
(1) S:轮廓单峰平均间距
S = ∑ Sn 1
(JIS B0601:’82)
n
i =1
- 1、下载文档前请自行甄别文档内容的完整性,平台不提供额外的编辑、内容补充、找答案等附加服务。
- 2、"仅部分预览"的文档,不可在线预览部分如存在完整性等问题,可反馈申请退款(可完整预览的文档不适用该条件!)。
- 3、如文档侵犯您的权益,请联系客服反馈,我们会尽快为您处理(人工客服工作时间:9:00-18:30)。
1.表面粗糙度理论与标准的发展表面粗糙度标准的提出和发展与工业生产技术的发展密切相关,它经历了由定性评定到定量评定两个阶段。
表面粗糙度对机器零件表面性能的影响从1918年开始首先受到注意,在飞机和飞机发动机设计中,由于要求用最少材料达到最大的强度,人们开始对加工表面的刀痕和刮痕对疲劳强度的影响加以研究。
但由于测量困难,当时没有定量数值上的评定要求,只是根据目测感觉来确定。
在20世纪20~30年代,世界上很多工业国家广泛采用三角符号(▽)的组合来表示不同精度的加工表面。
为研究表面粗糙度对零件性能的影响和度量表面微观不平度的需要,从20年代末到30年代,德国、美国和英国等国的一些专家设计制作了轮廓记录仪、轮廓仪,同时也产生出了光切式显微镜和干涉显微镜等用光学方法来测量表面微观不平度的仪器,给从数值上定量评定表面粗糙度创造了条件。
从30年代起,已对表面粗糙度定量评定参数进行了研究,如美国的Abbott就提出了用距表面轮廓峰顶的深度和支承长度率曲线来表征表面粗糙度。
1936年出版了Schmaltz论述表面粗糙度的专著,对表面粗糙度的评定参数和数值的标准化提出了建议。
但粗糙度评定参数及其数值的使用,真正成为一个被广泛接受的标准还是从40年代各国相应的国家标准发布以后开始的。
首先是美国在1940年发布了ASA B46.1国家标准,之后又经过几次修订,成为现行标准ANSI/ASME B46.1-1988《表面结构表面粗糙度、表面波纹度和加工纹理》,该标准采用中线制,并将R a作为主参数;接着前苏联在1945年发布了ΓOCT2789-1945《表面光洁度、表面微观几何形状、分级和表示法》国家标准,而后经过了3次修订成为ΓOCT2789-1973《表面粗糙度参数和特征》,该标准也采用中线制,并规定了包括轮廓均方根偏差(即现在的R q)在内的6个评定参数及其相应的参数值。
另外,其它工业发达国家的标准大多是在50年代制定的,如联邦德国在1952年2月发布了DIN4760和DIN4762有关表面粗糙度的评定参数和术语等方面的标准等。
以上各国的国家标准中都采用了中线制作为表面粗糙度参数的计算制,具体参数千差万别,但其定义的主要参数依然是R a(或R q),这也是国际间交流使用最广泛的一个参数。
2.2 表面粗糙度标准中的基本参数定义随着工业的发展和对外开放与技术合作的需要,我国对表面粗糙度的研究和标准化愈来愈被科技和工业界所重视,为迅速改变国内表面粗糙度方面的术语和概念不统一的局面,并达到与国际统一的作用,我国等效采用国际标准化组织(ISO)有关的国际标准制订了GB3505-1983《表面粗糙度术语表面及其参数》。
GB3505专门对有关表面粗糙度的表面及其参数等术语作了规定,其中有三个部分共27个参数术语:a.与微观不平度高度特性有关的表面粗糙度参数术语。
其中定义的常用术语为:轮廓算术平均偏差R a、轮廓均方根偏差R q、轮廓最大高度R y和微观不平度十点高度R z等11个参数。
b.与微观不平度间距特性有关的表面粗糙度参数术语。
其中有轮廓微观不平度的平均间距S m、轮廓峰密度D、轮廓均方根波长λq 以及轮廓的单峰平均间距S等共9个参数。
c.与微观不平度形状特性有关的表面粗糙度参数术语。
这其中有轮廓偏斜度S k、轮廓均方根斜率∆q和轮廓支承长度率t p等共5 个参数。
3.3 精密加工表面性能评价的内容及其迫切性表面粗糙度参数这一概念开始提出时就是为了研究零件表面和其性能之间的关系,实现对表面形貌准确的量化的描述。
随着加工精度要求的提高以及对具有特殊功能零件表面的加工需求,提出了表面粗糙度评价参数的定量计算方法和数值规定,同时这也推动了国家标准及国际标准的形成和发展。
在现代工业生产中,许多制件的表面被加工而具有特定的技术性能特征,诸如:制件表面的耐磨性、密封性、配合性质、传热性、导电性以及对光线和声波的反射性,液体和气体在壁面的流动性、腐蚀性,薄膜、集成电路元件以及人造器官的表面性能,测量仪器和机床的精度、可靠性、振动和噪声等等功能,而这些技术性能的评价常常依赖于制件表面特征的状况,也就是与表面的几何结构特征有密切联系。
因此,控制加工表面质量的核心问题在于它的使用功能,应该根据各类制件自身的特点规定能满足其使用要求的表面特征参量。
不难看出,对特定的加工表面,我们总希望用最(或比较)恰当的表面特征参数去评价它,以期达到预期的功能要求;同时我们希望参数本身应该稳定,能够反映表面本质的特征,不受评定基准及仪器分辨率的影响,减少因对随机过程进行测量而带来参数示值误差。
但是从标准制定的特点和内容上我们容易发现,随着现代工业的发展,特别是新型表面加工方法不断出现和新的测量器具及测量方法的应用,标准中的许多参数已无法适应现代生产的需求,尤其是在一些特殊加工场合,如精加工时,用不同方法加工得到的R a值相同(或很相近)的表面就不一定会具有相同的使用功能,可见,此时R a值对这类表面的评定显得无能为力了,而且传统评定方法过于注重对高度信息做平均化处理,而几乎忽视水平方向的属性,未能反映表面形貌的全面信息。
近年来在表面特性研究的领域内,相对地说,关于零件表面功能特性方面的研究本身就较为薄弱,因为它牵涉到很多学科和技术领域。
机器的各类零件在使用中各有不同的要求,研究表面特征的功能适应性将十分复杂,这也限制了对表面形貌与其功能特性关系的研究。
工业生产的飞速发展迫切需要更加行之有效且适应性更强的表面特征评价参数的出现,为解决这一矛盾,各国的许多学者都在这方面加大研究力度,以期在不远的将来制订出一套功能特性显著的参数。
另一方面,为了防止“参数爆炸”,同时也防止大量相关参数的出现,要做到用一个参数来评价多个性能特性,用数量很少的一组参数实现对表面的本质特征的准确描述。
4.4 表面粗糙度理论的新进展表面形貌评定的核心在于特征信号的无失真提取和对使用性能的量化评定,国内外学者在这一方面做了大量工作,提出了许多分离与重构方法。
随着当今微机处理技术、集成电路技术、机电一体化技术等的发展,出现了用分形法、Motif法、功能参数集法、时间序列技术分析法、最小二乘多项式拟合法、滤波法等各种评定理论与方法,取得了显著进展,下面对相对而言比较成熟的分形法、Motif法、特定功能参数集法进行介绍。
4.1. 1. 分形几何理论最近,国内外在表征和研究机加工表面的微观结构、接触机理和表面粗糙度等方面越来越多地使用分形几何理论这一有力的数学工具。
研究表明,很多种机加工表面呈现出随机性、多尺度性和自仿射性,即具有分形的基本特征,因而使用分形几何来研究表面形貌将是合理地、有效地。
确定分形的重要参数有分形维数D和特征长度A,它们可以衡量机加工表面轮廓的不规则性,理论上不随取样长度变化和仪器分辨率变化,并能反映表面形貌本质的特征,能够提供传统的表面粗糙度评定参数(如R a、R y、R z等)所不能提供的信息。
美国TopoMetrix公司生产的扫描探针显微镜(SPM)软件体系中,已将分形维数作为评价表面微观形貌的参数之一。
机械加工表面分形维数表达了表面所具有的复杂结构的多少以及这些结构的微细程度,微细结构在整个表面中所占能量的相对大小。
分形维数越大,表面中非规则的结构就越多,并且结构越精细,精细结构所具有的能量相对越大,具有更强的填充空间的能力。
Mandelbrot 于1982年在Weierstrass 函数基础上提出一种分形曲线的函数表达式,称为Weierstrass-Mandelbrot 函数,结合工程表面的特性,往往将W-M 函数写成如下形式。
n D n n n D r x r A x Z )2(12cos )(1-∞=-∑⨯=π 211<<>D R (1) Z(x)为机械加工表面轮廓。
这样,就在工程表面的函数描述中引入了分形维数D 这一参数,式中r n是表面上各次谐波的频率。
它的取值范围取决于采样长度L 和采样的最高分辨率,即截止频率,A 为特征长度。
对W-M 函数求功率谱可以得到D D Lnr A S 25)1(212)(--⨯=ϖϖ(2)轮廓的功率谱服从幂定律,在式(2)两端取对数为52)2()1(2)(-=--=+=D k Lnr Lg LgA D B kLg B LgS ϖϖ (3) 在双对数坐标lgs(ω)-lg ω中,k 是斜率,ω是截距,从上式可以看出分形维数D 决定着图线的斜率,特征长度A 和分形维数D 决定着图线的位置(截距)。
因此对于机械加工表面,可以通过其双对数坐标下的功率谱图,由(3)式算得分形维数D 和特征长度A 。
分形理论在实际应用中还有许多工作有待进一步研究。
一是并非所有表面都具有分形特征,分形维数能否完全表征实际表面,还有待进一步研究;二是现有的分形数学模型并没有考虑表面的功能特性,也没有一种方法能唯一确定分形参数。
4.2. 2. Motif 法随着制造技术的不断进步,表面质量不仅表现为表面的形状误差、波度、表面粗糙度等要求,而且对表面的峰、谷及其形成的沟、脉走向与分布等也有要求,需要对与表面功能密切相关的表面纹理结构进行综合评定。
显然,现在普遍采用的以2维参数为基础的表面形貌评定方法过于注重高度信息,对高度信息做平均化处理,而几乎忽视水平方向的属性,不能反映表面的其实形貌。
Motif 法基于地貌学理论从表面原始信息出发,不采用任何轮廓滤波器,通过设定不同的阈值将波度和表面粗糙度分离开来,强调大的轮廓峰和谷对功能的影响,在评定中选取了重要的轮廓特征,而忽略了不重要的特征,该方法被引入法国汽车工业表面粗糙度和波度标准,也已制订成国际标准ISO12085。
Motif 由两个单个轮廓峰的最高点之间的基本轮廓部分组成,两个峰之间的谷为一个单个的Motif ,如图1所示,并用平行于轮廓的总走向的长度AR ,垂直于基本轮廓总走向的两个深度H j 和H j+1,以及特征量T(T=min[H j ,H j+1])表征。
在设定阈值条件下,Motifs经过 图1 粗糙度Motif不断的合并,得到评定表面功能的Motifs集合,ISO12085推荐的参数见表1。
f的合并应遵循4个条件,否则2个相邻的峰不能被合并,只能作为单个的Motif处理。
1.包络条件如果两个相邻Motif的中间峰大于两边的峰,则2个Motif不能合并。
2.宽度条件2个相邻Motif合并后的长度不大于A(对表面粗糙度Motif)或B(对表面波度),则可以合并。
预先设定的Motif宽度的最大值A可以分离表面粗糙度和表面波度,实际上即为阈值。
设定的B值则可以分离波度和残留形状。
3.扩大条件2个Motif合并后的高度必须大于或等于原来的2个Motif。