表面粗糙度标准
表面粗糙度选用标准

表面粗糙度选用-----------------------------------------------------------序号=1Ra值不大于\μm=100表面状况=明显可见的刀痕加工方法=粗车、镗、刨、钻应用举例=粗加工的表面,如粗车、粗刨、切断等表面,用粗镗刀和粗砂轮等加工的表面,一般很少采用-----------------------------------------------------------序号=2Ra值不大于\μm=25、50表面状况=明显可见的刀痕加工方法=粗车、镗、刨、钻应用举例=粗加工后的表面,焊接前的焊缝、粗钻孔壁等-----------------------------------------------------------序号=3Ra值不大于\μm=12.5表面状况=可见刀痕加工方法=粗车、刨、铣、钻应用举例=一般非结合表面,如轴的端面、倒角、齿轮及皮带轮的侧面、键槽的非工作表面,减重孔眼表面-----------------------------------------------------------序号=4Ra值不大于\μm=6.3表面状况=可见加工痕迹加工方法=车、镗、刨、钻、铣、锉、磨、粗铰、铣齿应用举例=不重要零件的配合表面,如支柱、支架、外壳、衬套、轴、盖等的端面。
紧固件的自由表面,紧固件通孔的表面,内、外花键的非定心表面,不作为计量基准的齿轮顶圈圆表面等-----------------------------------------------------------序号=5Ra值不大于\μm=3.2表面状况=微见加工痕迹加工方法=车、镗、刨、铣、刮1~2点/cm^2、拉、磨、锉、滚压、铣齿应用举例=和其他零件连接不形成配合的表面,如箱体、外壳、端盖等零件的端面。
要求有定心及配合特性的固定支承面如定心的轴间,键和键槽的工作表面。
金属材料表面粗糙度标准
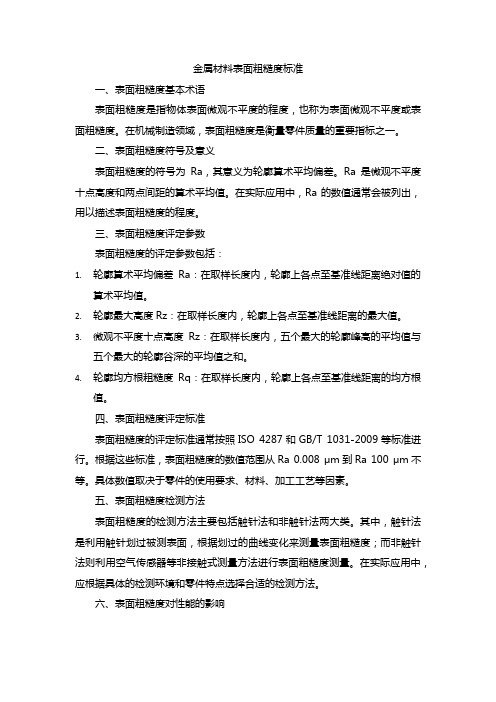
金属材料表面粗糙度标准一、表面粗糙度基本术语表面粗糙度是指物体表面微观不平度的程度,也称为表面微观不平度或表面粗糙度。
在机械制造领域,表面粗糙度是衡量零件质量的重要指标之一。
二、表面粗糙度符号及意义表面粗糙度的符号为Ra,其意义为轮廓算术平均偏差。
Ra是微观不平度十点高度和两点间距的算术平均值。
在实际应用中,Ra的数值通常会被列出,用以描述表面粗糙度的程度。
三、表面粗糙度评定参数表面粗糙度的评定参数包括:1.轮廓算术平均偏差Ra:在取样长度内,轮廓上各点至基准线距离绝对值的算术平均值。
2.轮廓最大高度Rz:在取样长度内,轮廓上各点至基准线距离的最大值。
3.微观不平度十点高度Rz:在取样长度内,五个最大的轮廓峰高的平均值与五个最大的轮廓谷深的平均值之和。
4.轮廓均方根粗糙度Rq:在取样长度内,轮廓上各点至基准线距离的均方根值。
四、表面粗糙度评定标准表面粗糙度的评定标准通常按照ISO 4287和GB/T 1031-2009等标准进行。
根据这些标准,表面粗糙度的数值范围从Ra 0.008 μm到Ra 100 μm不等。
具体数值取决于零件的使用要求、材料、加工工艺等因素。
五、表面粗糙度检测方法表面粗糙度的检测方法主要包括触针法和非触针法两大类。
其中,触针法是利用触针划过被测表面,根据划过的曲线变化来测量表面粗糙度;而非触针法则利用空气传感器等非接触式测量方法进行表面粗糙度测量。
在实际应用中,应根据具体的检测环境和零件特点选择合适的检测方法。
六、表面粗糙度对性能的影响表面粗糙度对金属材料的性能有着重要的影响。
例如,表面粗糙度会降低零件的耐磨性和疲劳强度,同时也会影响零件的抗腐蚀性能。
因此,在金属材料的加工过程中,应合理控制表面粗糙度,以达到最佳的使用性能。
七、表面粗糙度与其他参数的关系表面粗糙度与其他参数之间存在一定的关系。
例如,随着切削速度的提高,表面粗糙度会降低;而随着进给量的增加,表面粗糙度也会降低。
表面粗糙度标准
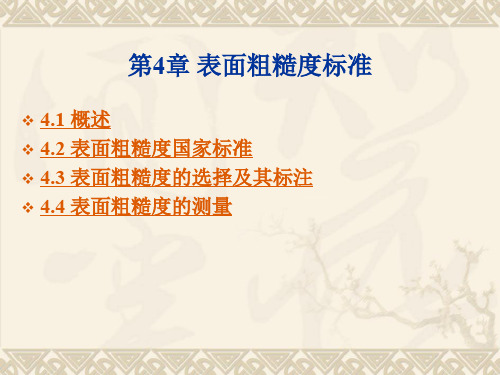
4.2 表面粗糙度国家标准
我国参照国际标准(ISO),对原表面粗糙度国家标准GB 1031-1983、 GB 131-1983作了修订和增订,新国标有GB/T 3505-2000《 表面结构的 术语、定义及参数 》、GB/T 1031-1995《表面粗糙度 参数及其数值》 和 GB/T 131-1993《机械制图 表面粗糙度符号、代号及其注法》。
间的距离。
(10)高度和间距辨别力:即应计入被评定轮廓的轮廓峰和轮廓谷的最 大高度和最小间距。轮廓峰和轮廓谷的最大高度通常用RZ或任一振幅参 数的百分率来表示;最小间距则以取样长度的百分率给出。
上一页 下一页 返回
4.2 表面粗糙度国家标准
4.2.2 表面粗糙度的评定参数及数值
为了能够定量描述零件表面微观几何形状特征,在国家标准中规定了表 面粗糙度评定参数及其数值和一般规定。表面粗糙度的评定参数应从轮 廓算术平均偏差(Ra)和轮廓最大高度(RZ)两个主要评定参数中选取。除 两个高度参数外。根据表面功能的需要。还可从轮廓单元的平均线高度 Rc、轮廓单元的平均宽度RSm和轮廓的支承长度率Rmr(c)三个附加参数 中选取。
上一页 下一页 返回
4.2 表面粗糙度国家标准
(9)在水条平行于中线的线与轮廓单元相截所得的各段截线长度之和,
如图4-5所示。
用公
式表示为
n
Ml c Mli
(4-1)
i 1
c为轮廓水平截距,即轮廓的峰顶线和平行于它并与轮廓相交的截线之
上一页 下一页 返回
4.1 概述
(5)影响零件表面的密封性。静力密封时,粗糙的零件表面之间无法 严密地贴合,容易使气体或液体通过接触面间的微小缝隙发生渗漏。同 理,对于动力密封,其配合面的表面粗糙度参数值也不能过低,否则受 压后会破坏油膜,从而失去润滑作用。
表面粗糙度标准
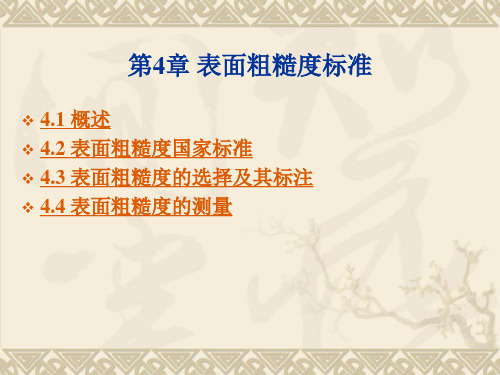
上一页
下一页
返回
4.2 表面粗糙度国家标准
标准规定:一般应以最小二乘中线作为基准线。 标准规定:一般应以最小二乘中线作为基准线。但由于在实际轮廓图形 上确定最小二乘中线的位置比较困难,通常在带有计算机的测量系统中, 上确定最小二乘中线的位置比较困难,通常在带有计算机的测量系统中, 可由相关的程序来确定。因此, 可由相关的程序来确定。因此,规定可用轮廓算术平均中线代替最小二 乘中线,以便用图解法近似确定最小二乘中线。在实际应用中, 乘中线,以便用图解法近似确定最小二乘中线。在实际应用中,最小二 乘中线与算术平均中线相差很小。轮廓算术平均中线的位置, 乘中线与算术平均中线相差很小。轮廓算术平均中线的位置,有时也可 用目测估计法确定。 用目测估计法确定。 (4)轮廓单元:一个轮廓峰和与其相邻的一个轮廓谷的组合,称为轮 )轮廓单元:一个轮廓峰和与其相邻的一个轮廓谷的组合, 廓单元, 所示。 廓单元,如图4-4所示。 所示 (5)轮廓峰高 P:即轮廓最高点距中线的距离。 )轮廓峰高Z 即轮廓最高点距中线的距离。 (6)轮廓谷深 V:即中线与轮廓最低点之间的距离。 )轮廓谷深Z 即中线与轮廓最低点之间的距离。 (7)轮廓单元的高度Zt:即一个轮廓单元的峰高和谷深之和。 )轮廓单元的高度 即一个轮廓单元的峰高和谷深之和。 (8)轮廓单元的宽度 s:即中线与轮廓单元相交线段的长度。 )轮廓单元的宽度X 即中线与轮廓单元相交线段的长度。
上一页
下一页
返回
4.1 概述
4.1.2 表面粗糙度对零件使用性能的影响
零件表面粗糙度的大小,对零件的使用性能有很大影响, 零件表面粗糙度的大小,对零件的使用性能有很大影响,主要表现在如 下几方面: 下几方面: (1)影响零件表面的耐磨性。表面粗糙度越大,零件工作表面的摩擦 )影响零件表面的耐磨性。表面粗糙度越大, 磨损和能量消耗越严重。如果表面越粗糙, 磨损和能量消耗越严重。如果表面越粗糙,配合面之间的有效接触面积 减小,压强增大,磨损就越快;表面越粗糙,摩擦系数加大, 减小,压强增大,磨损就越快;表面越粗糙,摩擦系数加大,由摩擦而 消耗的能量就越大。相反,如果要求表面粗糙度过小, 消耗的能量就越大。相反,如果要求表面粗糙度过小,则一方面将增加 制造成本,另一方面加大了金属分子间的吸附力,不利于润滑油的储存, 制造成本,另一方面加大了金属分子间的吸附力,不利于润滑油的储存, 容易使相互配合的工作表面之间形成干摩擦, 容易使相互配合的工作表面之间形成干摩擦,使金属接触面产生胶合磨 损而损坏。 损而损坏。
粗糙度检测标准
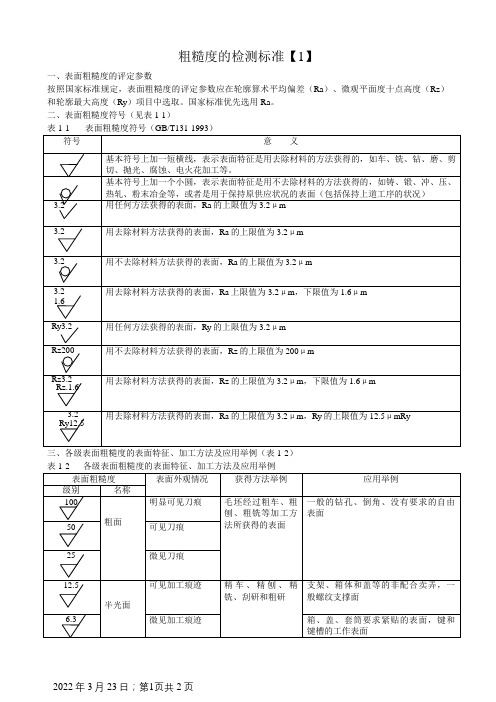
3.2
用任何方法获得的表面,Ra的上限值为3.2μm
3.2
用去除材料方法获得的表面,Ra的上限值为3.2μm
3.2
用不去除材料方法获得的表面,Ra的上限值为3.2μm
用去除材料方法获得的表面,Ra的上限值为3.2μm,Ry的上限值为12.5μmRy
三、各级表面粗糙度的表面特征、加工方法及应用举例(表1-2)
表1-2各级表面粗糙度的表面特征、加工方法及应用举例
表面粗糙度
表面外观情况
获得方法举例
应用举例
级别
名称
100
粗面
明显可见刀痕
毛坯经过粗车、粗刨、粗铣等加工方法所获得的表面
粗糙度的检测标准【1】
一、表面粗糙度的评定参数
按照国家标准规定,表面粗糙度的评定参数应在轮廓算术平均偏差(Ra)、微观平面度十点高度(Rz)和轮廓最大高度(Ry)项目中选取。国家标准优先选用Ra。
二、表面粗糙度符号(见表1-1)
表1-1表面粗糙度符号(GB/T131-1993)
符号
意义
基本符号上加一短横线,表示表面特征是用去除材料的方法获得的,如车、铣、钻、磨、剪切、抛光、腐蚀、电火花加工等。
一般的钻孔、倒角、没有要求的自由表面
50
可见刀痕
25
微见刀痕
12.5
半光面
可见加工痕迹
精车、精刨、精铣、刮研和粗研
支架、箱体和盖等的非配合卖弄,一般螺纹支撑面
6.3
微见加工痕迹
箱、盖、套筒要求紧贴的表面,键和键槽的工作表面
表面粗糙度标准
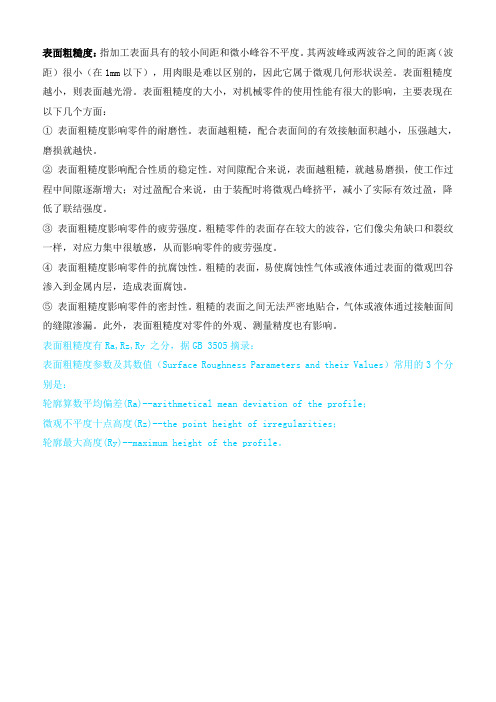
表面粗糙度:指加工表面具有的较小间距和微小峰谷不平度。
其两波峰或两波谷之间的距离(波距)很小(在1mm以下),用肉眼是难以区别的,因此它属于微观几何形状误差。
表面粗糙度越小,则表面越光滑。
表面粗糙度的大小,对机械零件的使用性能有很大的影响,主要表现在以下几个方面:① 表面粗糙度影响零件的耐磨性。
表面越粗糙,配合表面间的有效接触面积越小,压强越大,磨损就越快。
② 表面粗糙度影响配合性质的稳定性。
对间隙配合来说,表面越粗糙,就越易磨损,使工作过程中间隙逐渐增大;对过盈配合来说,由于装配时将微观凸峰挤平,减小了实际有效过盈,降低了联结强度。
③ 表面粗糙度影响零件的疲劳强度。
粗糙零件的表面存在较大的波谷,它们像尖角缺口和裂纹一样,对应力集中很敏感,从而影响零件的疲劳强度。
④ 表面粗糙度影响零件的抗腐蚀性。
粗糙的表面,易使腐蚀性气体或液体通过表面的微观凹谷渗入到金属内层,造成表面腐蚀。
⑤ 表面粗糙度影响零件的密封性。
粗糙的表面之间无法严密地贴合,气体或液体通过接触面间的缝隙渗漏。
此外,表面粗糙度对零件的外观、测量精度也有影响。
表面粗糙度有Ra,Rz,Ry 之分,据GB 3505摘录:表面粗糙度参数及其数值(Surface Roughness Parameters and their Values)常用的3个分别是:轮廓算数平均偏差(Ra)--arithmetical mean deviation of the profile;微观不平度十点高度(Rz)--the point height of irregularities;轮廓最大高度(Ry)--maximum height of the profile。
Ra--在取样长度L内轮廓偏距绝对值的算术平均值。
Rz--在取样长度内5个最大的轮廓峰高的平均值与5个最大的轮廓谷深的平均值之和。
Ry--在取样长度L内轮廓峰顶线和轮廓谷底线之间的距离。
如果图面没标注粗糙度选用Ra /Rz /Ry 的情况下默认为Ra。
表面粗糙度标准最新版
.
❖ 4.2.1 表面粗糙度的基本术语
❖ (1)取样长度lr:取样长度是用于判别被评定轮廓的不规则特征的X 轴 方向上的一段基准线长度,它在轮廓总的走向上量取,如图4-2所示。规
定和选择取样长度是为了限制和削弱表面波纹度(波距在1~10mm之间)
对表面粗糙度测量结果的影响。 lr过长,表面粗糙度的测量值中可能包 含有表面波纹度的成分;过短,则不能客观的反应表面粗糙度的实际情
❖ (7)影响产品的外观、表面涂层的质量和操作人员的使用舒适性(如机 床的操作手柄)等。
.
上一页 下一页 返回
4.1 概述
❖ (8)影响设备的振动和噪声及动力消耗。当运动副的表面粗糙度参数值 过大时,运动件将会产生振动和噪声,这种现象在高速运转的发动机曲 轴和凸轮、齿轮以及滚动轴承中很明显。显然,配合表面粗糙时,随着 摩擦系数的增大,摩擦力增大,从而动力消耗增加。Βιβλιοθήκη .上一页 下一页 返回
4.1 概述
❖ (2)影响配合性质的稳定性。对于间隙配合,表面越粗糙,就越容易磨 损,使工作过程中的配合间隙逐渐增大;对于过盈配合,由于压合装配 时会将微观凸峰挤平,减小了实际有效过盈量,降低了过盈配合的连接 强度。上述微观凸峰被磨损或被挤平的现象,对于那些配合稳定性要求 较高、配合间隙量或配合过盈量较小的高速重载机械影响更显著,故适 当的选定表面粗糙度参数值尤为重要。
4.2 表面粗糙度国家标准
表面粗糙度标准
表面粗糙度标准表面粗糙度:指加工表面具有的较小间距和微小峰谷不平度。
其两波峰或两波谷之间的距离(波距)很小(在1mm以下),用肉眼是难以区别的,因此它属于微观几何形状误差。
表面粗糙度越小,则表面越光滑。
表面粗糙度的大小,对机械零件的使用性能有很大的影响,主要表现在以下几个方面:表面粗糙度影响零件的耐磨性。
表面越粗糙,配合表面间的有效接触面积越小,压强越大,磨损就越快。
表面粗糙度影响配合性质的稳定性。
对间隙配合来说,表面越粗糙,就越易磨损,使工作过程中间隙逐渐增大;对过盈配合来说,由于装配时将微观凸峰挤平,减小了实际有效过盈,降低了联结强度。
表面粗糙度影响零件的疲劳强度。
粗糙零件的表面存在较大的波谷,它们像尖角缺口和裂纹一样,对应力集中很敏感,从而影响零件的疲劳强度。
表面粗糙度影响零件的抗腐蚀性。
粗糙的表面,易使腐蚀性气体或液体通过表面的微观凹谷渗入到金属内层,造成表面腐蚀。
表面粗糙度影响零件的密封性。
粗糙的表面之间无法严密地贴合,气体或液体通过接触面间的缝隙渗漏。
此外,表面粗糙度对零件的外观、测量精度也有影响。
表面粗糙度有Ra,Rz,Ry 之分,据GB 3505摘录:表面粗糙度参数及其数值(Surface Roughness Parameters and their Values)常用的3个分别是:轮廓算数平均偏差(Ra)--arithmetical mean deviation of the profile; 微观不平度十点高度(Rz)--the point height of irregularities;轮廓最大高度(Ry)--maximum height of the profile。
Ra--在取样长度L内轮廓偏距绝对值的算术平均值。
Rz--在取样长度内5个最大的轮廓峰高的平均值与5个最大的轮廓谷深的平均值之和。
Ry--在取样长度L内轮廓峰顶线和轮廓谷底线之间的距离。
如果图面没标注粗糙度选用Ra /Rz /Ry 的情况下默认为Ra。
表面粗糙度的评定标准及方法
表面粗糙度的评定标准及方法当钢材表面经喷射清理后,就会获得一定的表面粗糙度或表面轮廓。
表面粗糙度可以用形状和大小来进行定性。
经过喷射清理,钢板表面积会明显增加很多,同时获得了很多的对于涂层系统有利的锚固点。
当然,并不是粗糙度越大越好,因为涂料必须能够覆盖住这些粗糙度的波峰。
太大的粗糙度要求更多的涂料消耗量。
一般的涂料系统要求的粗糙度通常为Rz40~75微米。
1.粗糙度的定义对表面粗糙度的定义有以下几种:hy:在取样长度内,波峰到波谷的最大高度,ISO8503-3(显微镜调焦法)Ry:在取样长度内,波峰到波谷的最大高度,ISO8503-4(触针法)Ra:波峰和波谷到虚构的中心线的平均距离,ISO 3274Ry5:在取样长度内,五个波峰到波谷最大高度的算术平均值,ISO8503-4(触针法)有关Rz的表述与Ry5其实是相同的,Rz的表述来自于德国标准DIN 4768-1。
Ra和Rz之间的关系是Rz相当于Ra的4~6倍。
2.表面粗糙度的评定标准为了测定钢板表面粗糙度,不同的标准规定了相应的仪器可以使用,测量值以微米(μm)为单位。
国际标准分ISO 8503成五个部分在来说明表面粗糙度:ISO8503-1:1995表面粗糙度比较样块的技术要求和定义ISO8503-2:1995喷射清理后钢材表面粗糙度分级―样板比较法ISO8503-3:1995 ISO基准样块的校验和表面粗糙度的测定方法―显微镜调焦法ISO8503-4:1995 ISO基准样块的校验和表面粗糙度的测定方法,触针法ISO8503-5:2004表面轮廓的复制胶带测定法我国的国家标准GB/T 13288-91《涂装前钢材表面粗糙度等级的评定(比较板块法)》,参照ISO8503所制订。
3.比较样块法评定表面粗糙度在涂装现场较为常用的粗糙度评定方法是比较样块法。
常用的粗糙度比较块有英国易高elcometer125,荷兰TQCLD2040、LD2050以及英国PTER2006、R2007等。
表面粗糙度参数及其数值的国家标准
(4)表面粗糙度各参数的数值应在垂直于基准面的各截面上获得。对给定的表面,如 截面方向与高度参数(Ra、Rz)最大值的方向一致时,则可不规定测量截面的方向, 否则应在图样上标出。
(5面缺陷(如沟 槽、气孔、划痕等)包含进去。必要时,应单独规定对表面缺陷的要求。
一、规定表面粗糙度要求的一般规则
2. 表面结构要求在图样和其它技术产品文件中的注法
(1)在规定表面粗糙度要求时,应给出表面粗糙度参数值和测定时的取样长度值两项 基本要求。必要时也可规定表面加工纹理、加工方法或加工顺序和不同区域的粗糙度 等附加要求。
(2)表面粗糙度的标注方法应符合GB/T 131-2006的规定;缺省评定长度值应符合 GB/T 10610-2009的规定。
二、评定表面结构的参数及其数值系列
三、分类及表面粗糙度参数
三、分类及表面粗糙度参数
(6)根据表面功能和生产的经济合理性,当选用标准系列值不能满足要求时,可选取 标准中规定的补充系列值。国家标准对Ra、Rz、Rsm的补充系列值作了明确规定,需 要时可从GB/T 1031-2009附录A中选取。
二、评定表面结构的参数及其数值系列
国家标准规定,表面粗糙度参数从下列两项中选取: ——轮廓的算术平均偏差Ra; ——轮廓的最大高度Rz。 在幅度参数(峰和谷)常用的参数值范围内(Ra为0.025μm~6.3μm,Rz为 0.1μm~25μm)推荐优先选用Ra。
- 1、下载文档前请自行甄别文档内容的完整性,平台不提供额外的编辑、内容补充、找答案等附加服务。
- 2、"仅部分预览"的文档,不可在线预览部分如存在完整性等问题,可反馈申请退款(可完整预览的文档不适用该条件!)。
- 3、如文档侵犯您的权益,请联系客服反馈,我们会尽快为您处理(人工客服工作时间:9:00-18:30)。
况,使测得结果有很大随机性。可见,取样长度与表面粗糙度的评定参
数有关,在取样长度范围内,一般应包含五个以上的轮廓峰和轮廓谷。
常用的取样长度的推荐值见表4-1。
-
下一页 返回
4.2 表面粗糙度国家标准
❖ 在一般情况下,测量Ra和Rz时,推荐按表4-1选用对应的取样长度及评定 长度值,此时在图样上可省略标注取样长度值。当有特殊要求不能选用 表4-1中数值时,应在图样上注出取样长度值。
-
上一页 下一页 返回
4.1 概述
❖ (2)影响配合性质的稳定性。对于间隙配合,表面越粗糙,就越容易磨 损,使工作过程中的配合间隙逐渐增大;对于过盈配合,由于压合装配 时会将微观凸峰挤平,减小了实际有效过盈量,降低了过盈配合的连接 强度。上述微观凸峰被磨损或被挤平的现象,对于那些配合稳定性要求 较高、配合间隙量或配合过盈量较小的高速重载机械影响更显著,故适 当的选定表面粗糙度参数值尤为重要。
4.2 表面粗糙度国家标准
❖ 我国参照国际标准(ISO),对原表面粗糙度国家标准GB 1031-1983、 GB 131-1983作了修订和增订,新国标有GB/T 3505-2000《 表面结构的 术语、定义及参数 》、GB/T 1031-1995《表面粗糙度 参数及其数值》和 GB/T 131-1993《机械制图 表面粗糙度符号、代号及其注法》。
第4章 表面粗糙度标准
❖ 4.1 概述 ❖ 4.2 表面粗糙度国家标准 ❖ 4.3 表面粗糙度的选择及其标注 ❖ 4.4 表面粗糙度的测量
-
4.1 概述
❖ 表面粗糙度主要是指切削加工过程中由刀具和工件表面之间的强烈摩擦、 切屑分离过程中的物料破损残留以及工艺系统的高频振动等原因在工件 表面上引起的具有较小间距和微小峰谷不平度的微观误差现象。这种表 面微观几何形状误差,对机械零件的配合性质、工作精度、耐磨损性、 抗腐蚀性等有着十分密切的关系,它直接影响到机器或仪器的可靠性和 使用寿命。本章所涉及的国家标准为:
-
上一页 下一页 返回
4.1 概述
❖ (5)影响零件表面的密封性。静力密封时,粗糙的零件表面之间无法严 密地贴合,容易使气体或液体通过接触面间的微小缝隙发生渗漏。同理, 对于动力密封,其配合面的表面粗糙度参数值也不能过低,否则受压后 会破坏油膜,从而失去润滑作用。
❖ (6)影响机器或仪器的工作精度。表面粗糙度越大,配合表面之间的实 际接触面积就越小,致使单位面积受力增大,造成峰顶处的局部塑性变 形加剧,接触刚度下降,影响机器工作精度和精度稳定性。
❖ GB/T 3505-2000《 表面结构的术语、定义及参数 》 ❖ GB/T 1031-1995《表面粗糙度制图 表面粗糙度符号、代号及其注法》
-
下一页 返回
4.1 概述
❖ 4.1.1 基本概念
❖ 零件表面不论是用机械加工方法还是用其他方法获得,都不可能是绝对 光洁平滑的,总会存在着由微小间距和微观峰谷组成的微小高低不平的 痕迹。这是一种微观几何形状误差,称为微观不平度。这种微观几何形 状误差可用表面粗糙度来表达,表面粗糙度越小,表面越光滑。因此, 表面粗糙度是评定零件表面质量的一项重要指标。
上一页 下一页 返回
4.1 概述
❖ 4.1.2 表面粗糙度对零件使用性能的影响
❖ 零件表面粗糙度的大小,对零件的使用性能有很大影响,主要表现在如 下几方面:
❖ (1)影响零件表面的耐磨性。表面粗糙度越大,零件工作表面的摩擦磨 损和能量消耗越严重。如果表面越粗糙,配合面之间的有效接触面积减 小,压强增大,磨损就越快;表面越粗糙,摩擦系数加大,由摩擦而消 耗的能量就越大。相反,如果要求表面粗糙度过小,则一方面将增加制 造成本,另一方面加大了金属分子间的吸附力,不利于润滑油的储存, 容易使相互配合的工作表面之间形成干摩擦,使金属接触面产生胶合磨 损而损坏。
❖ (3)影响零件的疲劳强度。粗糙的零件表面存在较大的微观峰谷,它们 的尖锐缺口和裂纹对应力集中十分敏感,从而使零件的疲劳强度大大降 低。
❖ (4)影响零件表面的抗腐蚀性,比较粗糙的表面,易使腐蚀性气体或液 体通过微观峰谷渗入金属内层造成表面锈蚀。同时,微观凹谷处容易藏 污纳垢,容易产生化学腐蚀和电化学腐蚀。
❖ 4.2.1 表面粗糙度的基本术语
❖ (1)取样长度lr:取样长度是用于判别被评定轮廓的不规则特征的X 轴 方向上的一段基准线长度,它在轮廓总的走向上量取,如图4-2所示。规
定和选择取样长度是为了限制和削弱表面波纹度(波距在1~10mm之间)
对表面粗糙度测量结果的影响。 lr过长,表面粗糙度的测量值中可能包 含有表面波纹度的成分;过短,则不能客观的反应表面粗糙度的实际情
❖ 此外,表面粗糙度对零件的镀涂层、导热性和接触电阻、反射能力和辐 射性能、液体和气体的流动阻力、导体表面电流的流通等都会产生不同 程度的影响。综上所述,表面粗糙度在零件的几何精度设计中是必不可 少的项目,是一种十分重要的零件质量评定指标。为了保证零件的使用 性能和寿命,应对其加以合理限制。
-
上一页 返回
❖ (7)影响产品的外观、表面涂层的质量和操作人员的使用舒适性(如机 床的操作手柄)等。
-
上一页 下一页 返回
4.1 概述
❖ (8)影响设备的振动和噪声及动力消耗。当运动副的表面粗糙度参数值 过大时,运动件将会产生振动和噪声,这种现象在高速运转的发动机曲 轴和凸轮、齿轮以及滚动轴承中很明显。显然,配合表面粗糙时,随着 摩擦系数的增大,摩擦力增大,从而动力消耗增加。
❖ (2)评定长度ln :评定长度是用于判别被评定轮廓的表面粗糙度特性所 需的X轴方向上的长度,由于零件表面存在不均匀性,规定在评定时它 包括一个或几个取样长度,称为评定长度ln。在评定长度内,根据取样 长度进行测量,此时可得到一个或几个测量值;取其平均值作为表面粗 糙度数值的可靠值。一般情况下,取ln=5lr ,如表4-1所示。当表面比较 均匀时,可取ln<5lr;当表面均匀性较差时,可取ln>5lr 。
❖ 如图4-1所示,零件同一表面存在着叠加在一起的三种误差,即:形状误 差(宏观几何形状误差)、表面波度误差和表面粗糙度误差。三者之间, 通常可按相邻波峰和波谷之间的距离(波距)加以区分:波距在10mm 以上属形状误差范围,波距在1~10mm之间属表面波度范围,波距在 1mm以下属表面粗糙度范围。
-