液态金属凝固原理
液态金属的凝固

液态金属的凝固是一个复杂而有趣的过程。通过凝固,液态金属转化为固体 形式,形成结晶结构,展现出不同的特性和性质。
凝固过程概述
液态金属的凝固过程由多个阶段组成,包括原子或离子结构的重新排列和结 晶的形成。在凝固过程中,导致凝态金属凝固后形成的固态结晶结构决定了其物理和化学性质。不同金属具 有不同的结晶结构,如面心立方、体心立方和密排六方等。
应用前景和未来发展
液态金属的凝固在材料科学、工程和制造等领域具有广泛的应用前景。未来 的研究将进一步探索凝固过程的机理并开发新材料和技术。
凝固晶体缺陷及其特性
凝固过程中的晶体缺陷对于金属的性质和性能具有重要影响。包括点缺陷 (如空位和杂质)和线缺陷(如晶界和位错)等。这些缺陷可以改变金属的 机械、热学和电学特性。
液固相变热和界面活性
液态金属凝固时释放或吸收的相变热是决定凝固行为的重要参数。同时,金 属的界面活性也影响凝固过程中液态金属与固态晶界之间的相互作用。
影响金属凝固的因素
金属凝固的速度和结构受多种因素影响,包括温度、压力、合金成分、凝固剂的添加以及外界条件等。了解这 些因素对凝固行为的影响至关重要。
自发凝固和外界引导凝固的区 别
金属的自发凝固是指在合适的条件下,金属在没有外界干预的情况下从液态 转变为固态。而外界引导凝固则是通过添加凝固剂或改变凝固条件来主动诱 导凝固。
连铸坯的凝固原理
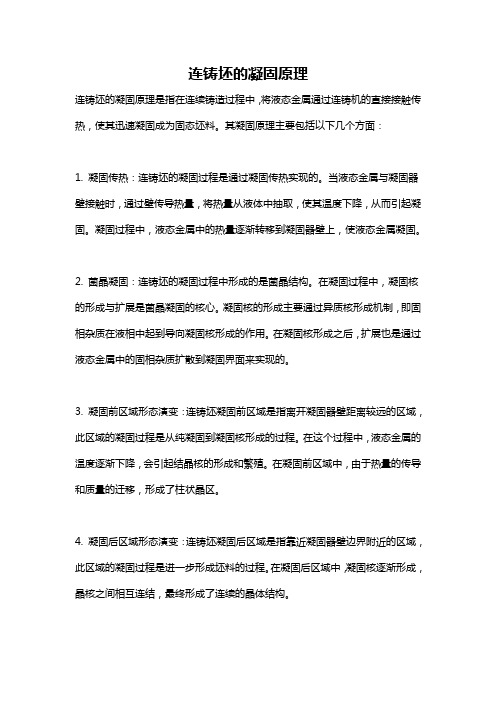
连铸坯的凝固原理
连铸坯的凝固原理是指在连续铸造过程中,将液态金属通过连铸机的直接接触传热,使其迅速凝固成为固态坯料。
其凝固原理主要包括以下几个方面:
1. 凝固传热:连铸坯的凝固过程是通过凝固传热实现的。
当液态金属与凝固器壁接触时,通过壁传导热量,将热量从液体中抽取,使其温度下降,从而引起凝固。
凝固过程中,液态金属中的热量逐渐转移到凝固器壁上,使液态金属凝固。
2. 菌晶凝固:连铸坯的凝固过程中形成的是菌晶结构。
在凝固过程中,凝固核的形成与扩展是菌晶凝固的核心。
凝固核的形成主要通过异质核形成机制,即固相杂质在液相中起到导向凝固核形成的作用。
在凝固核形成之后,扩展也是通过液态金属中的固相杂质扩散到凝固界面来实现的。
3. 凝固前区域形态演变:连铸坯凝固前区域是指离开凝固器壁距离较远的区域,此区域的凝固过程是从纯凝固到凝固核形成的过程。
在这个过程中,液态金属的温度逐渐下降,会引起结晶核的形成和繁殖。
在凝固前区域中,由于热量的传导和质量的迁移,形成了柱状晶区。
4. 凝固后区域形态演变:连铸坯凝固后区域是指靠近凝固器壁边界附近的区域,此区域的凝固过程是进一步形成坯料的过程。
在凝固后区域中,凝固核逐渐形成,晶核之间相互连结,最终形成了连续的晶体结构。
连铸坯的凝固原理是液态金属通过传导传热和纯凝固形成晶核,然后通过晶核的繁殖和晶体的连结形成连续的晶体结构,最终实现连铸坯的凝固。
液态金属的传热与凝固方式
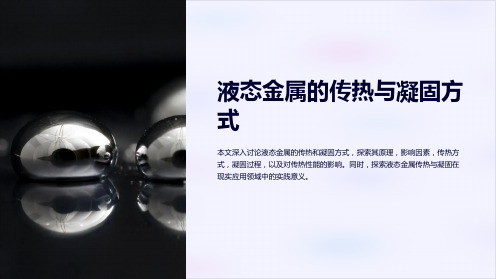
本文深入讨论液态金属的传热和凝固方式,探索其原理,影响因素,传热方 式,凝固过程,以及对传热性能的影响。同时,探索液态金属传热与凝固在 现实应用领域中的实践意义。
液态金属的传热原理
液态金属的传热原理是基于热传导机制,其中,热量通过金属中的自由电子 传播。这种电子传导机制使液态金属具有出色的导热性能。
液态金属的凝固过程
液态金属的凝固过程是指金属从液态向固态的相变过程。这个过程是由温度 和时间共同作用下的原子重新排列所导致。
凝固式对传热性能的影响
不同的凝固方式会对液态金属的传热性能产生不同影响,包括凝固结构的有 序性、晶粒尺寸和形态等。理解这些影响可以更好地优化传热性能。
液态金属传热与凝固的应用领域
液态金属传热的影响因素
液态金属传热的影响因素包括金属的物理特性、温度差、传热介质等。理解 这些因素对传热效果的影响能够优化液态金属的传热性能。
液态金属的传热方式
液态金属的传热方式包括对流传热、辐射传热和传热管传热等。不同的传热方式在不同的情况下有不同 的适用性和效果。了解这些方式可以为液态金属传热的设计和应用提供指导。
液态金属传热与凝固在众多领域都有广泛应用,包括航天、工业制造、能源等。这些应用为我们提供了 更高效、更可靠的传热技术。
结论和实践意义
深入理解液态金属的传热与凝固方式对于优化传热性能、改进工艺以及实现创新应用具有重要意义。这 将不仅推动液态金属传热技术的发展,也助力相关领域的进步与创新。
金属凝固原理
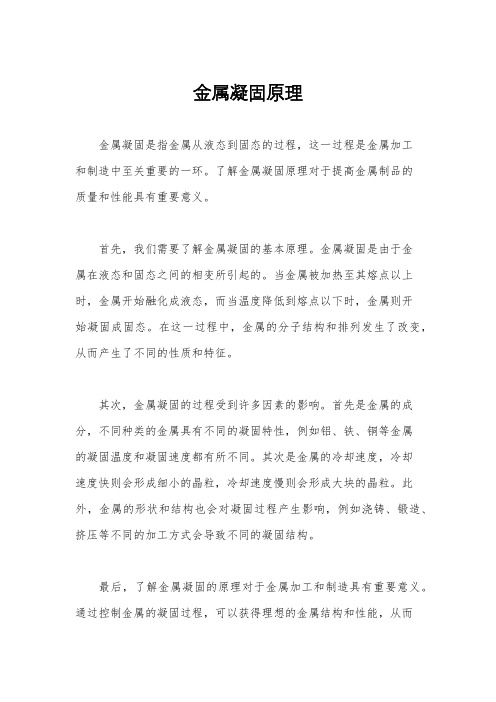
金属凝固原理金属凝固是指金属从液态到固态的过程,这一过程是金属加工和制造中至关重要的一环。
了解金属凝固原理对于提高金属制品的质量和性能具有重要意义。
首先,我们需要了解金属凝固的基本原理。
金属凝固是由于金属在液态和固态之间的相变所引起的。
当金属被加热至其熔点以上时,金属开始融化成液态,而当温度降低到熔点以下时,金属则开始凝固成固态。
在这一过程中,金属的分子结构和排列发生了改变,从而产生了不同的性质和特征。
其次,金属凝固的过程受到许多因素的影响。
首先是金属的成分,不同种类的金属具有不同的凝固特性,例如铝、铁、铜等金属的凝固温度和凝固速度都有所不同。
其次是金属的冷却速度,冷却速度快则会形成细小的晶粒,冷却速度慢则会形成大块的晶粒。
此外,金属的形状和结构也会对凝固过程产生影响,例如浇铸、锻造、挤压等不同的加工方式会导致不同的凝固结构。
最后,了解金属凝固的原理对于金属加工和制造具有重要意义。
通过控制金属的凝固过程,可以获得理想的金属结构和性能,从而提高金属制品的质量和性能。
例如,通过控制金属的冷却速度和形状,可以获得细小、均匀的晶粒结构,从而提高金属的强度和硬度。
此外,还可以通过添加合金元素和调整工艺参数,来改善金属的凝固特性,从而获得更优异的金属制品。
总之,金属凝固原理是金属加工和制造中至关重要的一环。
了解金属凝固的基本原理和影响因素,可以帮助我们更好地控制金属的凝固过程,从而提高金属制品的质量和性能。
希望本文能够为大家对金属凝固原理有所了解,同时也能够在实际生产中加以应用。
液态金属凝固原理讲解

2、内部柱状晶区的形成
凝固壳层→界面处晶粒单向散热→ 晶粒逆热流方向择优生长而形成柱 状晶
柱状晶区影响因素: (1)铸型导热能力: 铸型导热能
力越强,有利于柱状区形成; (2)合金成分:溶质含量越少,
1.4 金属结晶组织和凝固缺陷的控制
• 晶区数目以及柱状晶区和等轴晶区的相对宽度随合金性质 和具体凝固条件而变化,在一定条件下,可获得完全由柱 状晶或等轴晶所组成的宏观结晶组织 :
完全柱状晶
完全等轴晶
1、表面细晶粒区的形成
形成原因:
(1)铸型壁附近熔体受到强烈的激冷作用而大量形核,形成无 方向性的表面细等轴晶组织,也叫“激冷晶”。
铸件结晶组织对铸件质量和性能的影响 表面细晶粒区薄,对铸件的质量和性能影响不大。 铸件的质量与性能主要取决于柱状晶区与等轴晶区的比
例以及晶粒大小。
1.4.2 铸件晶粒组织的控制
(1)柱状晶(组织致密、晶粒粗大、 各向异性):
生长过程中凝固区域窄,横向 生长受到相邻晶体的阻碍,枝晶不 能充分发展,分枝少,结晶后显微 缩松等晶间杂质少,组织致密。
• 细晶区形成的前提:抑制铸件形成稳定的凝固壳层。
2、内部柱状晶区的形成
• 稳定凝固壳层产生→→柱状晶区开始 • 内部等轴晶区形成→→柱状晶区结束 • 柱状晶区的宽度及存在取决于上述两个因素综合作用结果。 • 生长方式:择优生长
•择优生长:各枝晶主干方向互不 相同,主干与热流方向相平行的 枝晶生长迅速,优先向内伸展并 抑制相邻枝晶的生长。逐渐淘汰 掉取向不利的晶体过程中发展成 柱状晶组织。
溶质原子富集而使界面前方成分过冷增大发生非均匀形核 (2)随对流漂移到铸件中心的自由小晶体
《液态金属的凝固》课件
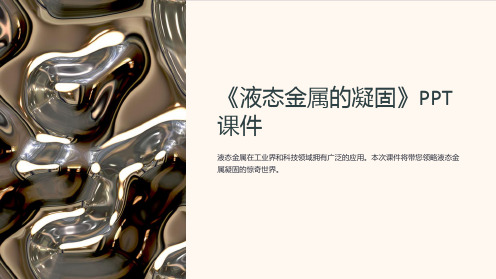
液态金属在工业界和科技领域拥有广泛的应用。本次课件将带您领略液态金 属凝固的惊奇世界。
液态金属凝固渐有序排列并形成 晶体。晶体的长大导致固态化。
表面张力
表面张力越大,固态金属的形态越规则。表面张力 也会影响凝固速度。
过冷现象
液态金属降温时,在本应结晶的温度下仍未结晶而 保持液态态势。可以通过添加晶核或增加凝固度来
快速冷却技术
利用快速冷却先对合金进行淬火处理,让金属快速 形变,形成亚晶状态,获得优化的力学性能。
电磁悬浮熔炉
通过在电磁场中悬浮液态金属,消除熔炼容器的物 理接触和热影响,避免金属污染,制备高纯度金属。
凝固过程的模拟与优化
液态金属凝固过程可以通过数值模拟进行优化,以达到更好的机械性能和良好的成型效果。 • 开发多尺度模拟技术 • 提高数值模拟精度 • 结合实验验证模拟结果
液态金属凝固的应用领域
汽车制造
液态金属可制造高强度和轻质 零件,如车架、刹车片等。
3D打印
利用增材制造技术,可以制造 出复杂形状的金属零部件。
电子器件
液态金属可用于导电涂层、承 载电路等领域。
液态金属的凝固:现象和应用
液态金属凝固可以带来革命性的变革,可以制造更轻便、更高强度的结构件或电子元器件。相信液态金属凝固 技术在不久的将来会迎来更广泛的应用。
常见的液态金属材料
铝
轻质、强度高、导电性好,应用广泛。
钛
密度小、强度高、抗腐、生物相容性好,具有 良好的结构材料潜力。
镁
密度小、强度高、韧性好,并可以降低磁性。
锆
具有良好的生物相容性和耐腐蚀性,广泛应用 于生物医学领域。
凝固过程和影响因素
1
金属凝固原理
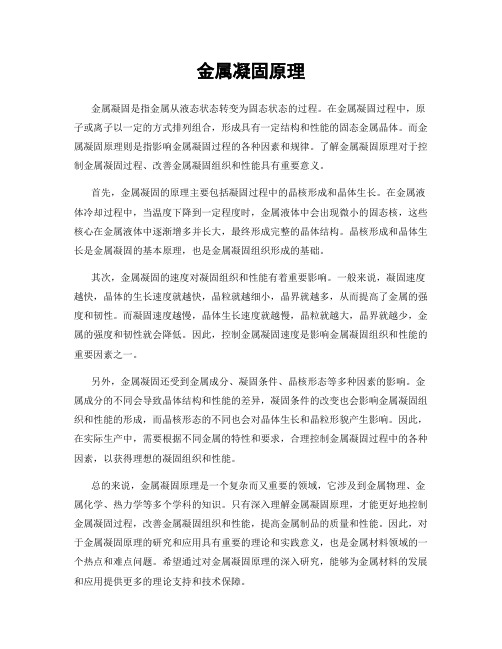
金属凝固原理金属凝固是指金属从液态状态转变为固态状态的过程。
在金属凝固过程中,原子或离子以一定的方式排列组合,形成具有一定结构和性能的固态金属晶体。
而金属凝固原理则是指影响金属凝固过程的各种因素和规律。
了解金属凝固原理对于控制金属凝固过程、改善金属凝固组织和性能具有重要意义。
首先,金属凝固的原理主要包括凝固过程中的晶核形成和晶体生长。
在金属液体冷却过程中,当温度下降到一定程度时,金属液体中会出现微小的固态核,这些核心在金属液体中逐渐增多并长大,最终形成完整的晶体结构。
晶核形成和晶体生长是金属凝固的基本原理,也是金属凝固组织形成的基础。
其次,金属凝固的速度对凝固组织和性能有着重要影响。
一般来说,凝固速度越快,晶体的生长速度就越快,晶粒就越细小,晶界就越多,从而提高了金属的强度和韧性。
而凝固速度越慢,晶体生长速度就越慢,晶粒就越大,晶界就越少,金属的强度和韧性就会降低。
因此,控制金属凝固速度是影响金属凝固组织和性能的重要因素之一。
另外,金属凝固还受到金属成分、凝固条件、晶核形态等多种因素的影响。
金属成分的不同会导致晶体结构和性能的差异,凝固条件的改变也会影响金属凝固组织和性能的形成,而晶核形态的不同也会对晶体生长和晶粒形貌产生影响。
因此,在实际生产中,需要根据不同金属的特性和要求,合理控制金属凝固过程中的各种因素,以获得理想的凝固组织和性能。
总的来说,金属凝固原理是一个复杂而又重要的领域,它涉及到金属物理、金属化学、热力学等多个学科的知识。
只有深入理解金属凝固原理,才能更好地控制金属凝固过程,改善金属凝固组织和性能,提高金属制品的质量和性能。
因此,对于金属凝固原理的研究和应用具有重要的理论和实践意义,也是金属材料领域的一个热点和难点问题。
希望通过对金属凝固原理的深入研究,能够为金属材料的发展和应用提供更多的理论支持和技术保障。
金属凝固原理范文
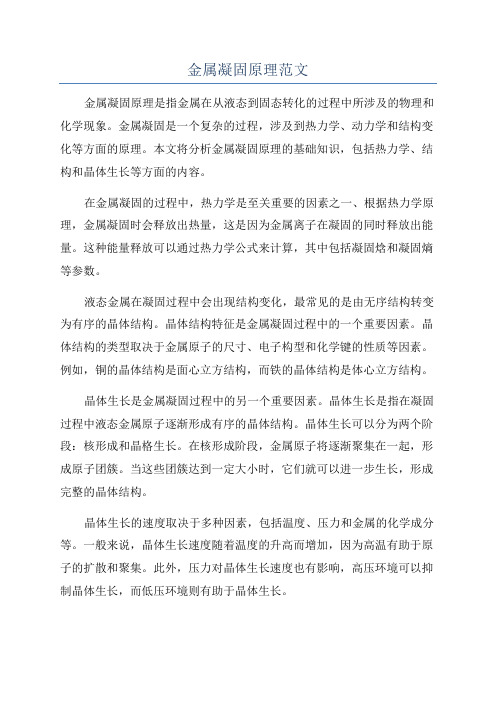
金属凝固原理范文金属凝固原理是指金属在从液态到固态转化的过程中所涉及的物理和化学现象。
金属凝固是一个复杂的过程,涉及到热力学、动力学和结构变化等方面的原理。
本文将分析金属凝固原理的基础知识,包括热力学、结构和晶体生长等方面的内容。
在金属凝固的过程中,热力学是至关重要的因素之一、根据热力学原理,金属凝固时会释放出热量,这是因为金属离子在凝固的同时释放出能量。
这种能量释放可以通过热力学公式来计算,其中包括凝固焓和凝固熵等参数。
液态金属在凝固过程中会出现结构变化,最常见的是由无序结构转变为有序的晶体结构。
晶体结构特征是金属凝固过程中的一个重要因素。
晶体结构的类型取决于金属原子的尺寸、电子构型和化学键的性质等因素。
例如,铜的晶体结构是面心立方结构,而铁的晶体结构是体心立方结构。
晶体生长是金属凝固过程中的另一个重要因素。
晶体生长是指在凝固过程中液态金属原子逐渐形成有序的晶体结构。
晶体生长可以分为两个阶段:核形成和晶格生长。
在核形成阶段,金属原子将逐渐聚集在一起,形成原子团簇。
当这些团簇达到一定大小时,它们就可以进一步生长,形成完整的晶体结构。
晶体生长的速度取决于多种因素,包括温度、压力和金属的化学成分等。
一般来说,晶体生长速度随着温度的升高而增加,因为高温有助于原子的扩散和聚集。
此外,压力对晶体生长速度也有影响,高压环境可以抑制晶体生长,而低压环境则有助于晶体生长。
除了热力学、晶体结构和晶体生长等方面的因素外,金属凝固还涉及到动力学过程。
动力学是指凝固过程中有关反应速率和能量转移的研究。
在金属凝固中,动力学过程包括原子之间的碰撞、扩散和团簇的生长等。
总之,金属凝固原理涉及到多个方面的知识,包括热力学、结构和晶体生长等。
了解这些原理可以帮助我们更好地理解金属凝固的过程,并为相关工业和科学研究提供指导。
- 1、下载文档前请自行甄别文档内容的完整性,平台不提供额外的编辑、内容补充、找答案等附加服务。
- 2、"仅部分预览"的文档,不可在线预览部分如存在完整性等问题,可反馈申请退款(可完整预览的文档不适用该条件!)。
- 3、如文档侵犯您的权益,请联系客服反馈,我们会尽快为您处理(人工客服工作时间:9:00-18:30)。
穿晶组织
3、中心等轴晶区的形成
--液态金属内部晶核自由生长的结果 • 晶核来源: (1)过冷液态金属直接形核 溶质原子富集而使界面前方成分过冷增大发生非均匀形核 (2)随对流漂移到铸件中心的自由小晶体 1)激冷游离晶 2)型壁晶粒脱落 3)液面晶粒沉降( 结晶雨) 上述晶粒随着液流漂移到铸件心部,通过增殖(枝晶熔 断),长大形成内部等轴晶 (3)共格的非金属夹杂物的非均匀形核
1. 等轴晶组织的获得和细化
(2)孕育处理
UCSD MAE-1 Fluid Dynamics Focus Area Lecture Notes, G.R.
1. 等轴晶组织的获得和细化
(3) 动力学细化法 1) 控制浇注条件
强化液流冲刷
(a)中心顶注法(Al-0.2%Cu合金)
UCSD MAE-1 Fluid Dynamics 图 不同浇注工艺铸锭的宏观组织 Focus Area Lecture Notes, G.R.
(1)浇注温度、铸型导热能力:浇注温度越高、铸型导热能力 越强,不利于细晶区形成;
(2)各种形式的晶粒游离(浇注时液体冲刷、液体对流造成)。
(2)合金成分:溶质含量越多,造成“颈缩”,利于细晶区形 成。
(3)非金属夹杂物含量:型壁附近熔体内大量的“非均匀形 核”,利于细晶区形成。 • 细晶区形成的前提:抑制铸件形成稳定的凝固壳层。
1.4.2 铸件晶粒组织的控制 对塑性较好的有色金属或奥氏体不锈钢锭,希望得到 较多的柱状晶,增加其致密度; 对一般钢铁材料和塑性较差的有色金属铸锭,希望获得 较多的甚至是全部细小的等轴晶组织; 对于高温下工作的零件,通过单向结晶消除横向晶界, 防止晶界降低蠕变抗力。
UCSD MAE-1 Fluid Dynamics Focus Area Lectu CO+[Mn] •(SiO2)+2[C] = 2CO+ [Si] •(Cu2O)+2[H] = 2[Cu]+H2O (气)
气孔的危害
1) 有效工作断面 ↓→ σb↓ δ↓
2)
3)
应力集中 →裂纹,如氢脆
疏松 → δ↓气密性 ↓ 耐蚀性↓
气孔的防止
•竞争淘汰:离开型壁的距离越远, 取向不利的晶体被淘汰得就越多, 柱状晶的方向就越集中,同时晶 粒的平均尺寸也就越大。
2、内部柱状晶区的形成
凝固壳层→界面处晶粒单向散热→ 晶粒逆热流方向择优生长而形成柱 状晶 柱状晶区影响因素: (1)铸型导热能力: 铸型导热能 力越强,有利于柱状区形成; (2)合金成分:溶质含量越少, 有利于柱状晶区形成。 (3)非金属夹杂物含量:非金属 夹杂物含量少,有利于柱状晶 区形成。
2)反应性气孔(皮下气孔) • 金属液-铸型之间、金属液内 部发生化学反应所产生的气孔。
含 氢 量
气孔的形成机理
1、析出性气孔形成 形核、长大、上浮三阶段 上浮受阻 → 保留于凝固金属 →气孔
铸件中气孔的形成示意图
气孔的形成机理
2、反应性气孔形成
(1)金属液与铸型(芯)反应性气孔 原因:铸型水分高、透气性低; 合金中有易氧化成分。 类型:H2O、CO、CH4、渣气孔。 例 钢中氧或氧化物与碳反应形成CO ,CO不溶钢。 •(FeO)+[C] = CO+[Fe]
1.4.2 铸件晶粒组织的控制
1.等轴晶组织的获得和细化
强化非均匀形核 促进晶粒游离 抑制柱状晶区
1. 等轴晶组织的获得和细化
(1) 降低浇注温度 熔体的过热度较小,与浇道内壁接触就能产生大量的游 离晶粒。有助于已形成的游离晶粒的残存,这对等轴晶的 形成和细化有利。
1. 等轴晶组织的获得和细化
1.4
金属结晶组织和凝固缺陷的控制
• 晶区数目以及柱状晶区和等轴晶区的相对宽度随合金性质 和具体凝固条件而变化,在一定条件下,可获得完全由柱 状晶或等轴晶所组成的宏观结晶组织 :
完全柱状晶
完全等轴晶
1、表面细晶粒区的形成
形成原因:
(1)铸型壁附近熔体受到强烈的激冷作用而大量形核,形成无 方向性的表面细等轴晶组织,也叫“激冷晶”。 • 细化程度取决于
2.柱状晶组织的获得
定向凝固
功率降低法
UCSD MAE-1 Fluid Dynamics Focus Area Lecture Notes, G.R.
单晶体的制备 (1)基本原理:保证一个晶核形成并长大。 (2)制备方法:尖端形核法和垂直提拉法。
UCSD MAE-1 Fluid Dynamics Focus Area Lecture Notes, G.R.
第一章
液态金属凝固原理
1.4
金属结晶组织和凝固缺陷的控制
1.4.1 铸件典型晶粒组织的形成及其影响因素
铸件的典型晶粒凝固组织(三个 晶区 ):
表面细晶粒区:紧靠型壁的外壳 层,由紊乱排列的细小等轴晶所 组成,仅几个晶粒厚。 柱状晶区:由自外向内沿着热流 方向彼此平行排列的柱状晶所组 成。 内部等轴晶区:由紊乱排列的粗 大等轴晶所组成 。
1)激冷游离晶
非均质形核的激冷游离晶
因浇注温度低,浇注中形成的激冷游离晶
凝固初期形 成的激冷游 离晶
2)型壁晶粒脱落和枝晶熔断、游离
型壁晶体或柱状枝晶在凝固界面前方的熔断、游离和 增殖——理论基点为溶质再分配。
图 型壁晶粒脱落示意图
2)型壁晶粒脱落和枝晶熔断、游离
图 枝晶分枝“缩颈”的形成
a) b) c)为二、三次分枝时缩颈形成过程示意图。 V为生长方向。d) 分枝缩颈
1.偏析
(2)宏观偏析
宏观偏析后果:造成产品各部位性能不均匀。 不能通过均匀化退火消除。 消除宏观偏析的方法:控制凝固速度
UCSD MAE-1 Fluid Dynamics Focus Area Lecture Notes, G.R.
2.气孔与夹杂
(1)气孔
1)析出性气孔 • 在冷却及凝固过程中,因气体 溶解度下降,析出气体,来不 及从液面排出而形成气孔。H2 孔、N2孔、O2孔。
1.4.2 铸件晶粒组织的控制 (1)柱状晶(组织致密、晶粒粗大、 各向异性): 生长过程中凝固区域窄,横向 生长受到相邻晶体的阻碍,枝晶不 能充分发展,分枝少,结晶后显微 缩松等晶间杂质少,组织致密。 但柱状晶比较粗大,晶界面积 小,排列位向一致,其性能具有明 显的方向性:纵向好、横向差。凝 固界面前方常汇集有较多的第二相 杂质 ,将导致铸件热裂。
5 10 15 -3 振幅/(in×10 )
20
振动对晶粒大小的影响(lin=2.54cm)
1. 等轴晶组织的获得 和细化
(3) 动力学细化法 图 利用旋转磁场控制 晶粒组织 柱状晶区(未加磁场) 细等轴晶区(加磁场)
1. 等轴晶组织的获得和细化
(4)提高冷却速度 薄壁铸件:激冷使整个断面同时产生较大的过冷,采用 金属型容易获得细等轴晶。
1. 等轴晶组织的获得和细化
(3) 动力学细化法 2)铸型振动: 熔体在凝固过程中存在长时间、激烈的对流。 (晶粒或枝晶脱落、破碎、游离、增殖) 振动--机械振动、电磁振动、音频或超声波振动 搅拌--机械、电磁搅拌 旋转振荡 -周期性地改变铸型的旋转方向和旋转速度
晶粒平均直径/mm
3 2 1 0 0
2、内部柱状晶区的形成
• • • • 稳定凝固壳层产生→→柱状晶区开始 内部等轴晶区形成→→柱状晶区结束 柱状晶区的宽度及存在取决于上述两个因素综合作用结果。 生长方式:择优生长
•择优生长:各枝晶主干方向互不 相同,主干与热流方向相平行的 枝晶生长迅速,优先向内伸展并 抑制相邻枝晶的生长。逐渐淘汰 掉取向不利的晶体过程中发展成 柱状晶组织。
1.偏析 (1)微观偏析:胞状偏析、晶内偏析(枝晶偏析)、 晶界偏析.
1.偏析 (2)宏观偏析 由于结晶过程中液相 与固相内溶质原子的重新 分布造成的。 包括:正偏析、 反偏析、 比重偏析。
UCSD MAE-1 Fluid Dynamics Focus Area Lecture Notes, G.R.
型壁较厚或导热性较差的铸件,采用金属型容易形成凝 固壳层,易形成柱状晶;采用砂型可防止形成凝固壳层, 有利于形成等轴晶,但晶粒粗大。
2.柱状晶组织的获得
定向凝固
发热剂法、功率降低法、高 速凝固法、液态金属冷却法 等
发热剂法
2.柱状晶组织的获得
定向凝固
UCSD MAE-1 Fluid Dynamics Focus Area Lecture Notes, G.R.
1. 等轴晶组织的获得和细化
(3) 动力学细化法 1) 控制浇注条件 强化液流冲刷
(b)沿型壁浇注法
(c)靠近型壁(6孔)顶注法
图 不同浇注工艺铸锭的宏观组织
1. 等轴晶组织的获得和细化
(3) 动力学细化法 1) 控制浇注条件 强化液流冲刷
UCSD MAE-1 Fluid Dynamics Focus Area Lecture Notes, G.R.
TiC、VC可起到细化晶粒的作用。
1. 等轴晶组织的获得和细化
(2)孕育处理 铝液中加入Ti,形成 TiAl3.
UCSD MAE-1 Fluid Dynamics Focus Area Lecture Notes, G.R.
1. 等轴晶组织的获得和细化
(2)孕育处理 B.造成溶质偏析 通过在生长界面前沿的富集而使晶粒根部和树枝晶分枝 根部产生细弱缩颈,从而促进晶粒的游离。如,钢中加入B 可起到细化晶粒的作用。 溶质平衡分配系数: 在一定温度下,固、 液两平衡相中溶质浓 度的比值: k0 = CS / CL
(2)孕育处理 孕育——向液态金属中添加少量孕育剂促进液态金属内部 形核,以达到增加晶核数、细化晶粒、改善组织之目的。