轧机厚度自动控制系统设计
新钢1550mm冷连轧机厚度自动控制系统配置方案

4. 3 压力 AGC 压力 AGC控制见图 3。 ¹利用轧制压力根据弹跳方程间接测量带钢厚
度偏差, 以调节辊缝。 º响应快, 但精度低 [ 3] 。
DS2辊缝调节量; Q2轧件塑性系数; C 2轧机刚性数; DH 2来料厚差; H 02设定厚度; H i2测量厚度 图 1 前馈 AGC 控制原理
4. 2 厚度 AGC 厚度 AGC控制见图 2。 ¹利用测厚仪直接测量带钢出口厚度偏差, 从
而调节辊缝。 º响应滞后。
C 2轧机刚性数; Q2轧件塑性系数; Dh2厚差; DS2辊逢差; S2辊逢值; P2轧制压力; h2计算厚度
图 3 压 力 AGC控制原理
4. 4 张力 AGC 张力 AGC控制见图 4。 ¹改变后张力调节厚差。 º调节相邻机架速度差或调节开卷机或卷取机
ºB 方 式。适用范围: 轧制产品厚度小于 014 mm, 且材质较硬; 采用 / 张力极限控制 0方式, 允许 张力 在 15% 范 围内 调 节 以 控 制 厚 度, 如 果 超 过 15% , 还需要通过调整辊缝回到极限范围内, 然后回 到 A方式。
»C方式。适用范围: 在轧制一般低碳产品时, 如果来料平直度不好, 5号机架可作为平整机使用; 用 4号机架前后测厚仪对 4号 机架进行预控 + 监 控, 控制 4号速度; 通过调节 5号机架速度, 保 4号、 5号机架张力恒定; 用 5号机架出口厚度, 修正 5号 机架的设定厚度。
¼2 号 机架预控。根据 1 号机 架后测厚 仪厚 度, 由秒流量相等原则, 计算 1号机架速度调节量。 7. 2 精调 AGC
根据成品带钢厚度、带钢材质由操作员通过选 择开关进行选择。
¹A方式。适用范围: 轧制 产品厚度 大于 014 mm, 且材质较软; 采用 5号机架的预控和监控, 控制 5号机架速度; 通过调节 5号机架辊缝, 保持 4号机 架、5号机架张力恒定。
自动轧钢机的plc控制

PLC的编程语言和编程工具
PLC的编程语言通常采用类似于计算机高级语言的指令集,如Ladder Logic、Function Block Diagram(FBD)、Structured Text(ST)、Instruction List(IL)等。
常用的PLC编程工具包括PLC厂商提供的专用软件包和第三方软件,如Rockwell的RSLogix 5000、Siemens的STEP 7等。这 些软件提供了图形化编程界面,使得用户可以方便地编写、调试和监控PLC程序。
PLC控制技术基础
PLC的定义与特点
PLC(可编程逻辑控制器)是一种专为工业环境设计的数字电子设备,用于执行顺 序控制、逻辑运算、算术运算等操作,并通过数字或模拟输入/输出模块控制各种类 型的机器和设备。
PLC具有高可靠性、高灵活性、易于编程和易于扩展等特点,因此在工业自动化 领域得到了广泛应用。
程序优化与改进
优化算法
根据实际运行情况和性能要求,优化控制算 法,提高控制精度和响应速度。
改进功能
根据生产需求和设备升级,逐步增加或改进 控制功能,提高自动轧钢机的生产效率和产 品质量。
05
系统测试与运行
系统测试方案与实施
测试目的
确保PLC控制系统在自动轧钢机中的稳定性 和可靠性,提高生产效率。
PLC的基本组成和工作原理
PLC主要由中央处理单元(CPU)、存储器、 输入/输出模块、电源和编程设备等部分组成。
PLC的工作原理可以概括为输入采样、程序 执行和输出刷新三个阶段。在输入采样阶段 ,PLC读取输入信号的状态并将其存储在输 入映像寄存器中;在程序执行阶段,PLC按 照用户程序的顺序执行指令,并更新内部存 储器的值;在输出刷新阶段,PLC将输出映 像寄存器的值输出到输出模块,驱动外部设
自动轧钢机的PLC控制系统设计

自动轧钢机的PLC控制系统设计自动轧钢机是一种用于将铁水或钢块进行加工、压制和轧制的关键设备。
它主要由温控系统、液压系统、轮辊线系统和PLC控制系统等组成。
PLC控制系统是整个轧钢机运行和控制的核心部分。
本文将详细介绍自动轧钢机的PLC控制系统设计。
一、系统框架设计自动轧钢机的PLC控制系统主要由中央控制器(CPU)、输入模块、输出模块、通信模块和用户界面组成。
其中,中央控制器用于处理和控制信号,输入模块用于接收传感器信号,输出模块用于控制执行器的操作,通信模块用于与外部设备进行数据交互,用户界面用于人机交互。
二、硬件设计1.中央控制器:选择可编程逻辑控制器(PLC)作为中央控制器,可根据实际需求选择合适的型号和规格。
PLC需要具备足够的输入和输出接口,以满足轧钢机的控制需求。
2.输入模块:根据实际需要选择合适的输入模块,用于接收传感器信号。
例如,温度传感器、压力传感器、位移传感器等。
输入模块需要具备稳定、可靠的信号传输性能。
3.输出模块:根据实际需要选择合适的输出模块,用于控制执行器的操作。
例如,液压阀、电磁阀、电动机等。
输出模块需要具备高效、可靠的控制性能。
4.通信模块:根据实际需求选择合适的通信模块,用于与外部设备进行数据交互。
例如,以太网通信模块、串口通信模块等。
通信模块需要具备稳定、可靠的数据传输性能。
5.用户界面:根据实际需要选择合适的用户界面,用于人机交互。
例如,触摸屏、按钮、指示灯等。
用户界面需要具备直观、易用的操作性能。
三、软件设计1.程序设计:根据轧钢机的工作流程和控制要求编写PLC程序。
程序包括输入信号的检测和处理、输出信号的生成和控制、故障检测和报警等功能模块。
2.控制算法设计:根据轧钢机的特点和要求设计合适的控制算法,包括温度控制、压力控制、轮辊线速度控制等。
控制算法需要满足精度要求,提高轧钢机的生产效率和产品质量。
3.系统调试和优化:在系统安装和调试过程中,根据实际情况对软件进行优化,提高系统的稳定性和可靠性。
轧机厚度自动控制AGC系统说明

轧机厚度自动控制AGC系统使 用 说 明 书中色科技股份有限公司装备所自动化室二零零九年八月二十五日目 录第一篇 软件使用说明书第一章 操作软件功能简介第二章 操作界面区简介第三章 操作使用说明第二篇 硬件使用说明书第一章 接口板、计算机板跨接配置图 第三篇 维护与检修第一章 系统维护简介及维护注意事项第二章 工程师站使用说明第三章 检测程序的使用第四章 常见故障判定方法第四篇 泵站触摸屏操作说明第五篇 常见故障的判定方法附录:第一章 目录第二章 系统内部接线表第三章 系统外部接线表第四章 系统接线原理图第五章 系统接口电路单元图第一篇软 件 说 明 书第一章 操作软件功能简介.设定系统轧制参数;.选择系统工作方式;.系统调零;.显示时实参数的棒棒图、馅饼图、动态曲线;.显示系统的工作方式、状态和报警。
以下就各功能进行分述:1、在轧机靠零前操作手需根据轧制工艺,设定每道次的入口厚度、出口厚度和轧制力等参数。
也可以在轧制表里事先输入,换道次时按下道次按钮,再按发送即可。
2、操作手根据不同的轧制出口厚度,设定机架控制器和厚度控制器的工作方式,与轧制参数配合以得到较理想的厚差控制效果。
3、在泄油状态下,操作手通过在规定状态下对调零键的操作,最终实现系统的调零或叫靠零,以便厚调系统正常工作。
4、在轧制过程中,以棒棒图、馅饼图和动态曲线显示厚调系统的轧制速度、轧制压力、开卷张力、卷取张力、操作侧油缸位置、传动侧油缸位置、压力差和厚差等实时值。
(注意:轧机压靠前操作侧油缸位置、传动侧油缸位置显示为油缸实际移动位置。
轧机压靠后操作侧油缸位置、传动侧油缸位置显示的是辊缝值。
)5、显示系统的工作方式、系统状态和系统报警。
6、系统有两种与传动和测厚仪协调工作模式A.常用数据由厚控AGC发送到传动及测厚仪。
如人口厚度、出口厚度、轧制速度及张力等等。
传动以此为基准值,如调整需通过把手或其他方式加到此基准值上,然后返送回AGC。
厚度自动控制系统
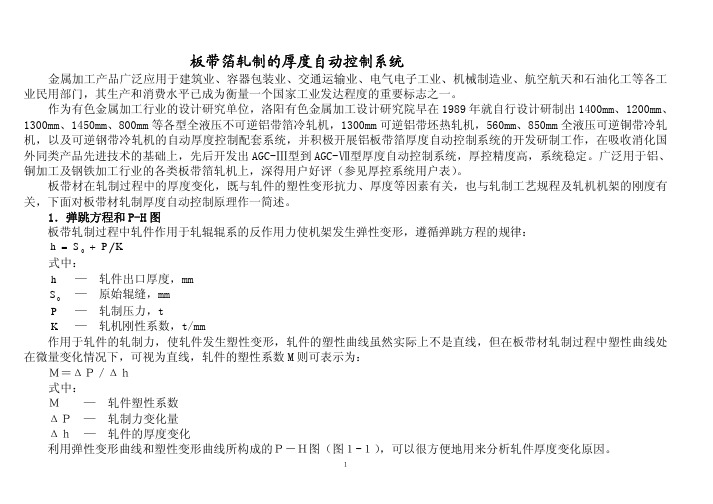
板带箔轧制的厚度自动控制系统金属加工产品广泛应用于建筑业、容器包装业、交通运输业、电气电子工业、机械制造业、航空航天和石油化工等各工业民用部门,其生产和消费水平已成为衡量一个国家工业发达程度的重要标志之一。
作为有色金属加工行业的设计研究单位,洛阳有色金属加工设计研究院早在1989年就自行设计研制出1400mm、1200mm、1300mm、1450mm、800mm 等各型全液压不可逆铝带箔冷轧机,1300mm 可逆铝带坯热轧机,560mm、850mm 全液压可逆铜带冷轧机,以及可逆钢带冷轧机的自动厚度控制配套系统,并积极开展铝板带箔厚度自动控制系统的开发研制工作,在吸收消化国外同类产品先进技术的基础上,先后开发出AGC-Ⅲ型到AGC-Ⅶ型厚度自动控制系统,厚控精度高,系统稳定。
广泛用于铝、铜加工及钢铁加工行业的各类板带箔轧机上,深得用户好评(参见厚控系统用户表)。
板带材在轧制过程中的厚度变化,既与轧件的塑性变形抗力、厚度等因素有关,也与轧制工艺规程及轧机机架的刚度有关,下面对板带材轧制厚度自动控制原理作一简述。
1.弹跳方程和P-H 图 板带轧制过程中轧件作用于轧辊辊系的反作用力使机架发生弹性变形,遵循弹跳方程的规律:K P S h 0+=式中:h — 轧件出口厚度,mm0S — 原始辊缝,mmP — 轧制压力,tK — 轧机刚性系数,t/mm作用于轧件的轧制力,使轧件发生塑性变形,轧件的塑性曲线虽然实际上不是直线,但在板带材轧制过程中塑性曲线处在微量变化情况下,可视为直线,轧件的塑性系数M 则可表示为:M=ΔP/Δh式中:M — 轧件塑性系数ΔP — 轧制力变化量Δh — 轧件的厚度变化利用弹性变形曲线和塑性变形曲线所构成的P-H图(图1-1),可以很方便地用来分析轧件厚度变化原因。
图1-1 弹性塑性变形的P-H图2.影响厚度变化的因素2.1 轧件的尺寸及性能的影响在其他条件不发生变化的情况下,轧件出口厚度的变化与其入口厚度的波动是成正比的,如图2-1所示,如果轧件入口厚度由0HH→,则会产生厚度波动h∆。
冷带轧机板厚自动控制系统

( )人 T 操 作 阶 段 。住 2 1 0世 纪 3 年 代 以 ( )
前 ,轧 机装 机水平 较低 ,板 厚控 制是 以手 动 卜 或简单 的 电动压 下来 移动辊 缝控 制板 厚 ,轧制 过
板 高端 产 品 的质 量 与产量 要求越 来越 高 ,故研 发
程 的实 时调 节依靠 操作 者 的经验 完成 。
( )常规 模 拟 式 调 节 的 自动 控 制 阶段 2 2 0 世纪 3 0年代 到 6 0年代 ,随 着经典 控制 理论 建 立 和技术 进 步 ( I PD控制技 术 在工业 中应 用 ) ,轧 机 板厚 控制 迈入 常规模 拟式 调 节的 自动 控制 阶段 、 ( )液 压 压 下 汁算 机 集 中控 制 阶 段 。2) 3 (
A s a t uo t a g o t l A C)i tek yt h o g r rd ci .H da l G yt b t c :A t i g u ec n o ( G r ma c r s h e c n l yi s i p o u t n y ru cA C ss m i e o n tp o i e s
i h s at e t sp i td o tt a e c mp n ain c n r l n i u lrl n o t l st e r s a c i c in n ti r M .I i on e u t h o e s t o to a d v r a ol g c nr h e e r h dr t h t o t i oi e o
2 板 厚 控 制 发 展 历 程
板 带轧 机板厚 控制 的发 展历 程是 随着 1 ̄ 生 2l . k 产 对板带 尺 寸精度 要求 越来 越高 的市场 推动 _ 发 卜
第9章-轧钢厚度自动控制

材料与冶金学院李振亮课程名称:《材料成型控制工程基础》(第9章,共11章)编写时间:2010 年9月1日内 蒙 古 科 技 大 学 教 案连铸坯 液芯压下顶弯、 拉矫液压摆式切头均热炉高压水除磷 立辊轧边 F1- F6精轧内蒙古科技大学教案内蒙古科技大学教案图9-14 测厚仪型反馈式厚度自动控制系统 图9-15 δh 与δS 的关系曲线h 实—实测厚度;h 给—给定厚度 “压下有效系数”的概念? 由前式可知,当轧机的空载辊缝S0改变δS 时,所引起的轧件出口厚度变化量δS ,δh 与δS 之间的比值C=δh/δS 称为“压下有效系数”,表示压下螺丝位置改变量能造成多大的轧件出口厚度变化量。
h K Mh K M K S mm δδδ)1(+=+= 内 蒙 古 科 技 大 学 教 案GM-AGC工作原理图前馈式厚度自控系统原理”和“厚度计”测厚的反馈式AGC,都无法避免信号传递的滞后,因而限制了控制精度内蒙古科技大学教案图9-21 前馈AGC 控制示意图 图9-22 δh 、δS 、δH 之间的关系曲线H K M H M M mδδ=+) (9-10) 内 蒙 古 科 技 大 学 教 案内蒙古科技大学教案图9-25 入口和出口断面形状内蒙古科技大学教案内蒙古科技大学教案内蒙古科技大学教案图9-31 四辊钢板轧机的受力和变形[40]内蒙古科技大学教案图9-33 带钢良好板形线簇[40]众所周知,轧制压力波动对带钢板形的影响不是太敏感的,带钢愈厚,影响愈为迟钝。
其原因是带钢是一个整体,只要带钢宽度上各点的不均匀纵向延伸产生的内应力不超过一定限度,带钢就不会失去它维持自身平直的稳定状态,带钢愈薄,维持自身平直的能力愈差。
所以保证轧制带钢板形良好的条件,图上表现出来的不是一条直线,而是一个区间,这个区域随板厚增大而变得愈宽,见图图9-34 带钢板形良好区间[40]与区间上限AE的交点E是不产生边部浪形的临界点;塑性线是不产生中部浪形的临界点。
热轧带钢厚度自动控制系统的研究

热轧带钢厚度自动控制系统的研究提要:厚度精度是热轧带钢产品质量的关键指标,本文综合运用了厚度自动控制的典型模型以及补偿措施,取得了良好效果。
文章对于冶金带钢轧制宽度控制系统的设计应用有很大的参考价值。
关键词:厚度控制;监控AGC;补偿措施1.概述厚度自动控制系统(AGC),是英国钢铁协会于20世纪40年代末50年代初发明的,该方法称之谓BIRAAGC。
之后日本、德国、美国等发明了测厚计型AGC,称之谓GMAGC。
BISRAAGC控制模型中只有轧机参数M,没有轧件参数Q,从理论上讲是不完备的。
采用传统轧制力预报模型计算,最大偏差多在20%以上,所以传统的常规的数学模型不能提供足够精确的近似值。
即使采用自适应技术,利用实测数据重新计算模型参数,但由于模型本身结构的限制,也难于适应实际生产过程。
目前,板厚自动控制技术(AGC)已日益成熟,纵向厚差的控制精度基本得到了解决。
现代控制理论及智能控制理论与技术也被广泛地应用于轧制过程中的厚度控制。
己经取得了巨大成果和经济效益。
2厚差产生原因分析(1)轧机机械及液压装置的干扰因素。
轧机机械装置本身的缺点及某个参数的变化将会使轧机的刚度及空载下的辊缝产生人们所不希望的一些变化,从而影响出口带钢的厚度,表现为轧辊直径及宽度的变化、轧辊磨损、轧辊偏心、轧辊热胀冷缩、轧辊轴承油膜厚度、压下螺丝及附件、液压缸及附件、轧机牌坊、轧机震动等。
(2)轧机控制系统的干扰因素。
轧制速度、带钢张力、弯辊、辊缝、轧制力、厚度监控器等系统的控制品质也是造成带钢厚度变化的主要因素。
(3)轧件的干扰因素。
来料厚度、来料宽度、来料硬度、来料断面、来料平直度的变化直接影响着成品厚度。
3热轧带钢AGC控制方式的综合研究与运用3.1 GMAGCGM(厚度计)方式AGC即为轧制力反馈AGC,简称GMAGC。
对于带钢热连轧机精轧机组,除入口和出口处设置有测厚仪外,其他各机架的出口处无法装设测厚仪,因此采用间接测厚AGC系统。
- 1、下载文档前请自行甄别文档内容的完整性,平台不提供额外的编辑、内容补充、找答案等附加服务。
- 2、"仅部分预览"的文档,不可在线预览部分如存在完整性等问题,可反馈申请退款(可完整预览的文档不适用该条件!)。
- 3、如文档侵犯您的权益,请联系客服反馈,我们会尽快为您处理(人工客服工作时间:9:00-18:30)。
轧机厚度自动控制系统设计
摘要:随着社会经济的发展,对板带产品的质量和精度要求越来越
高。
厚度精度就是板带产品的重要质量指标之一。
本文针对轧机AGC技术的现状,以及轧机厚差产生的原因进行了分析。
在此基础上,对轧机AGC 进行分析,以APC为主要研究对象,选用PLC作为系统的控制器,将位移传感器测得的位移量经A/D转换送给PLC来控制步进电机,从而控制阀,通过轧制力来改变辊缝厚度实现轧机厚度控制。
1 引言
轧机又称轧钢机,轧钢机就是在旋转的轧辊之间对钢件进行轧制的机械,轧钢机一般包括主要设备(主机)和辅助设备(辅机)两大部分。
轧钢机按轧辊的数目分为二辊,三辊式,四辊式和多辊式,轧钢机通常简称为轧机。
板带厚度精度是板带材的两大质量指标之一,板带厚度控制是板带轧制领域里的两大关键技术之一。
带钢纵向厚度不均是影响产品质量的一大障碍,因此,轧机的一项重要课题就是带钢厚度的自动控制。
厚度自动控制系统是通过测厚仪或传感器对带材实际轧出厚度连续进行测量,并根据实测值与给定值比较后的偏差信号,借助于控制回路或计算机的功能程序,改变压下装置、张力或轧制速度,把带材出口厚度控制在允许的偏差范围内。
实现厚度自动控制的系统称为“AGC"。
我国近年来从发达国家引进的一些大型的现代化的板带轧机,其关键
技术是高精度的板带厚度控制和板形控制。
板带厚度精度关系到
金属的节约、构件的重量以及强度等使用性能,为了获得高精度的产品厚度,AGC系统必须具有高精度的压下调节系统及控制系统的支持。
而对于轧机来说产生厚差的原因大致可分为三大类:
(1)轧机方面的原因:轧辊热膨胀和磨损、轧辊弯曲、轧辊偏心和支撑辊轴承油膜厚度等都会产生厚度波动。
它们都是在液压阀位置不变的情况下,使实际辊缝发生变化,从而导致轧出的带钢厚度产生波动。
(2)轧件方面的原因:厚度偏差会直接受到坯料尺寸变化的影响。
它包括来料宽度不均和来料厚度不均的影响。
(3)轧制工艺方面的原因:轧制时前后张力的变化、轧制速度的变化等。
2系统总体设计
厚度自动控制AGC (Automatic Gauge Control )是指钢板轧机在轧制过程中通过动态微调使钢板纵向厚度均匀的一种控制手段。
厚度自动控制系统是通过测厚仪或传感器对带材实际轧出厚度连续进行测量,并根据实测值与给定值比较后的偏差信号,借助于控制回路或计算机的功能程序,改变压下装置、张力或轧制速度,把带材出口厚度控制在允许的偏差范围内。
AGC系统一般包括有:
1)压下位置闭环:为了轧出给定厚度的轧件,首先必须在轧件进入辊缝之前,准确地设定空载辊缝。
其次,在轧制过程中,为了使轧后的轧件厚度均匀一致,还必须随着轧制条件的变化及时的调整空
载辊缝的大小。
这些都是通过正确地设定和控制压下位移(位置)来完成。
压下位置闭环的作用就是通过对位移传感器测得的辊缝实际值与给定值进行比较,准确的控制轧辊的压下位移,达到设定和控制空载辊缝的目的。
辊缝值是通过操作侧和传动侧液压缸的位移取平均值得到的。
它是整个厚度自动控制系统的基础。
压下位置控制系统又称为APC(Automatic Position Control )系统。
2)轧制力闭环:通过控制轧制力来实现对厚度的控制。
在控制时是通过不断的修正实际压力值与设定压力值之间的偏差来实现的。
3)测厚仪监控闭环:由于出口厚度和辊缝、轧制力、张力、速度、温度、润滑液等多种因素有关,所以单靠设定辊缝大小是无法准确控制出口厚度的。
为此在出口侧装有侧厚仪,利用监控系统对位置闭环系统的辊缝设定值进行修正,从而达到准确标准出口厚度。
本系统以APC空制为主,将位移传感器安装在轧机上,测量轧制后钢板的厚度,与设定值进行比较后,通过控制器PLC调节步进电机的速度,进而通过步进电机空制伺服阀,改变油的流量,得以改变轧制力,从而改变辊缝的大小,达到厚度自动控制的要求。
3硬件设计
根据总体设计,系统结构框图如下:
本设计所需的可编程控制器采用日本三菱公司的FX2N-32MT型PLC,点数是由系统需要决定,输出采用晶体管输出以获得快速性;
A/D转换模块采用的是三菱的FX2N-4AD该模块有四通道的A/D输入,最大分辨率是12位,总体精度+1%,转换速度2.1ms。
系统通过位移传感器是磁栅位移传感器,将其检测到的模拟信号经FX2N-4AD 转换成数字量送入PLC,将它与辊缝设定值进行比较,并按照控制规律对误差值进行运算,用运算结果来控制步进电机,驱动执行机构伺服阀工作,利用伺服阀去控制
油缸,从而控制轧制力,达到改变辊缝大小的目的,进而实现厚度自动控制。
步进电机位移控制系统以三菱FX2N为主控单元,以步进电机驱动器为驱动单元,以两相混合式步进电机为执行单元。
通过PLC控制脉冲的发生个数,从而控制步进电机的运转角度。
4软件设计系统软件的控制流程主要分预压靠、调零、穿带、厚度控制等为几部分。
预压靠模块是在冷轧机系统第一次运行时必须要执行的模块,目的是测出轧机的辊缝补偿表。
在本系统中,采用控制步进电机进而控制轧制力的方法。
由于选择的磁栅传感器的分辨率为io卩m即每读取100个脉冲,步进电机相当于产生了1mm勺位移。
根据磁栅位移传感器的分辨率以及步进电机的步距角来初始化高速计数器的技术初始值以及步进电机的脉冲周期。
5 结语
本研究以轧机为对象,在进行了大量的理论研究与资料查询的基础上,针对液压厚度控制的自身特点,通过理论分析建立了液压AGC 电液位置伺服系统模型。
对轧机厚度自动控制系统的研究仅仅是起了抛砖引玉的作用,还
有许多方面考虑的可能不够全面,比如一些波动没考虑到,控制精度
差等,并且很多控制参数需要在工程进一步调试的过程中完善修正。
参考文献
[1] 华建新,王贞祥. 全连续冷轧机过程控制[M] 北京:冶金工业出版社,2000:1-4.
[2]彭天乾.微米级冷轧带钢厚度控制系统[J].冶金自动化.1996 ,20 (6):1-5.
[3]宋文宇.鞍钢厚板厂液压AGC系统分析[M].鞍钢技术.1995.
[4]李刚.中厚板液压APC&AG计算机控制系统设计及仿真[C].
东北大学硕士论文.1996.。