分离过程 第三章
第三章 多组分精馏和特殊精馏(化工分离过程)
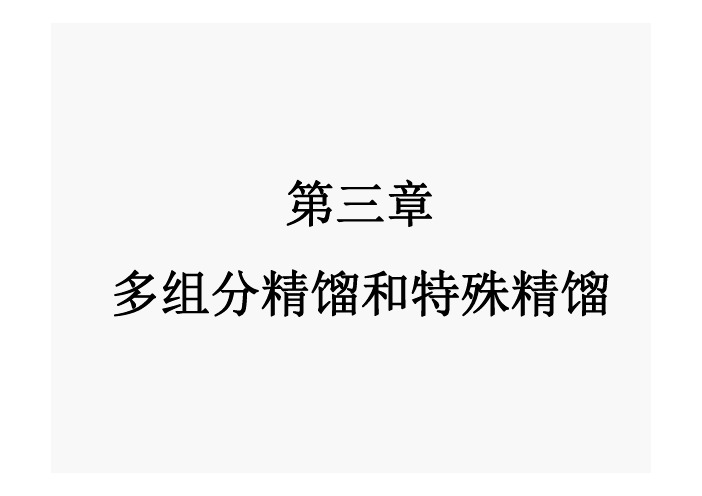
3.1.3 最少理论板数(Nm)和组分分配
全回流对应最少理论板数,但全回流下无产品采出, 因此正常生产中不会采用全回流。 什么时候采用全回流呢?
1、开车时,先全回流,待操作稳定后出料。 2、在实验室设备中,研究传质影响因素。 3、工程设计中,必须知道最少板数。
最少理论板数的计算
Fenske(芬斯克)方程推导前提: 1、塔顶采用全凝器,(若采用分凝器,则分凝器为第1块塔板) 2、所有板都是理论板。
一、关键组分(Key Components)
Na=串级数(2)+分配器(1)+侧线采出
F
(0)+传热单元(2) = 5
已被指定的可调变量: (1)进料位置;(2)回流比; (3)全凝器饱和液体回流或冷凝 器的传热面积或馏出液温度。
余下的2个可调设 计变量往往用来指 定组分在馏出液和 釜液中的浓度。
两组分精馏 指定馏出液中一个组分的浓度,就确定了馏 出液的全部组成;指定釜液中一个组分的浓 度,也就确定了釜液的全部组成。
下面通过实例分别对二组分精馏和多组分精馏过 程分析进行比较。
二组分精馏实例:苯-甲苯
图3-1 二组分精馏流率、温度、浓度分布
三组分精馏实例:苯(LK)-甲苯(HK)-异丙苯
图3-2 三组分精馏流量分布 图3-3 三组分精馏温度分布
四组分精馏实例:苯-甲苯(LK)-二甲苯(HK)-异丙苯
图3-6 四组分精馏液相组成分布
⎜⎜⎝⎛
yA yB
⎟⎟⎠⎞ 2
= ⎜⎜⎝⎛
xA xB
⎟⎟⎠⎞1
代入(3-2)式:
⎜⎜⎝⎛
yA yB
⎟⎟⎠⎞1
= α1 ⎜⎜⎝⎛
xA xB
⎟⎟⎠⎞1
=
⎜⎜⎝⎛
化工分离第三章-6解读
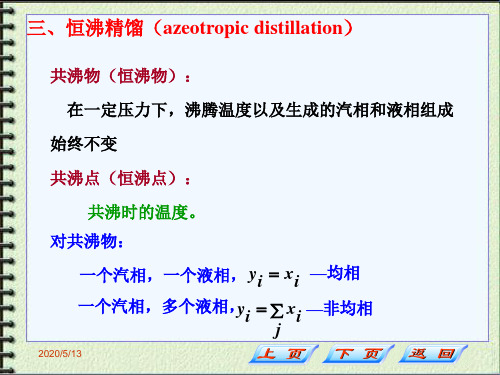
②
pis f (T )
又
x1 x2 1
解方程, 若有解即有恒沸
2019/4/16
B 求给定压力下的恒沸组成与恒沸温度
设恒沸温度 T
查出 计算出
p
s i
解方程①
xi
s p i ri xi P
No
调整
2019/4/16
例3—6 已知P=86.659kPa,求共沸时x、T。
在恒沸剂回收塔中,应与其它 物料有相当大的溶解度差异。
2019/4/16
(4)用量少,气化潜热小;
(5)不与进料中组分起化学反应; (6)无腐蚀、无毒、价廉易得 。
3、恒沸精馏的举例与计算 相图分析 三组分体系的相图
2019/4/16
三组分体系的相图及其应用
三组分体系相图类型
因为 C 3, f 3 2 -Φ 当 Φ 1, f 4 ,无法用三维空间表 示相图。
FxMS S 1 - xMS
FxFA MxMA
FxFB MxMB
FxFA xMA F S FxFB xMB F S
恒沸剂不混入塔釜液,
适宜的恒沸剂量
被分离的恒沸组分 A 完全和 恒沸剂形成恒沸物而蒸出
2019/4/16
恒沸剂适量
恒沸剂过量
恒沸剂不足
2019/4/16
由杠杆定律
2019/4/16
氯仿 61.2℃
二元共沸物 64.5℃
二硫化碳 46.25℃
二元共沸物 39.3℃
丙酮 56.4℃
恒沸剂用量的计算
利用三角相图 + 物料衡算
总物料衡算: M=F+S 组分 S 的衡算式:
生物分离-第三章-离心与沉降
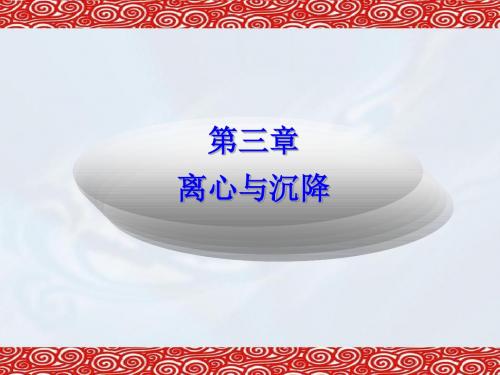
离心过滤
离心过滤就是应用离心力代替压力差作为过滤推动力的分离方法, 也称为过滤式离心机。 左图为工业上常用的篮式过滤离心 机,过滤离心机的转鼓为一多孔圆 筒,圆筒转鼓内表面铺有滤布。 操作时,被处理的料液由圆筒口连 续进入筒内,在离心力的作用下, 清液透过滤布及鼓壁小口被收集排 出,固体微粒则被截留于滤布表面 形成滤饼
沉降设备的分类:
• • • • 矩形水平流动池 圆形水平流动池 垂直流动式圆形池 方形池
传统
沉降设备
新型 • 斜板式沉淀池 • 斜管式沉淀池
矩形水平流动池: 沉降特性好,池壁可两池共 用,节省费用
圆形水平流动池: 截面是圆形,高径比小,但 处理量较大,液体从中进入, 向外筒壁流动,通过溢流堰 排出
v0-泵送作用下的液体流速,m/s vc- 粒子在离心力作用下的运动速度, m/s 在多数场合下,vo随r的变化而变化,即r减小时,vo增大,因碟片 间的环隙通道截面积随r减小而缩小。且vo还是微粒位置的y坐标的
函数,即在碟片表面v0=0。 vo可表示为:
Q---为离心机泵送液体的流量,m3/s
n—碟片间隙数
μ—介质黏度,Pa〃s;
v —微粒运动速度,m/s。
这个等式仅当球形微粒较小时方能成立,即:
如果Re>1时,阻力为 f—摩擦系数 当球形粒子在介质中运动时速度较小,因此作用其上的阻力也 较小,当阻力与浮力平衡时,微粒加速度为零。联立方程 3.1 和3.2,得到下式, 此式给出了微粒稳定状态和最终速度
单位面积上的过滤体积可改写为
可得近似离心式过滤机由开始操作至滤饼厚度为(R0-Rc)时的过滤时 间
从一种发酵液中分离提取类固醇,类固醇晶体的 浓度为16kg/m3,料液密度为1000kg/m3.在过滤分 离小试中,处理0.25L发酵液需32min,实验室装 置的过滤面积为8.3· 10-4m2,过滤压降为105Pa, 所得滤饼密度为1090kg/m3,过滤介质阻力可忽 略。扩大实验使用篮式过滤离心机处理发酵液, 离心机转鼓内径为1.02m,高0.45m,转速为 530r/min,在过滤转速时,测知转鼓内的液层和 滤饼的厚度之和为0.055m。求处理1.6m3这种发 酵液所需的分离时间
化工分离过程__第3章第一讲设计变量的确定

能量交换数: 1
+)
3C+7
Q V L
NDe = Nve-Nce
= C+4
NCe
物料衡算式: C
能量衡算式: 1
相平衡关系式: C+2
化学反应平衡式: 0 内在关系式: 0 2C+3
Nx = 进料+压力 =(C+2)+1=C+3
Na = ND-Nx =(C+4)-(C+3)=1
+)
33
精馏塔(塔内无压降)
相平衡关系式: C(P-1)+2=C+2
化学反应平衡式: 0 内在关系式: 0
Nc = 2C+3
V
L1
Q
L2
NDe = Nve-Nce
= C+4
Байду номын сангаас
14
V Q
L1
产物为两相的全凝器
L2
固定设计变量Nx = 进料+压力=(C+2)+1 可调设计变量Na = ND-Nx=(C+4)-(C+3)=1
如单元温度或引入的冷量
21
例1. 简单精馏塔(塔内无压降)
Nxu
进料变量数: C+2
F Q
压力等级数: 1
+)
C+3
Nau
分配器数: 0
侧线采出: 0
传热单元: 1
串级数: 2
+)
3
22
例2. 有侧采的精馏塔 Nxu
进料变量数: C+2 压力等级数: 1
C+3
Nau
分配器数: 1 侧线采出: 1 传热单元: 2
第三章汽液传质分离过程
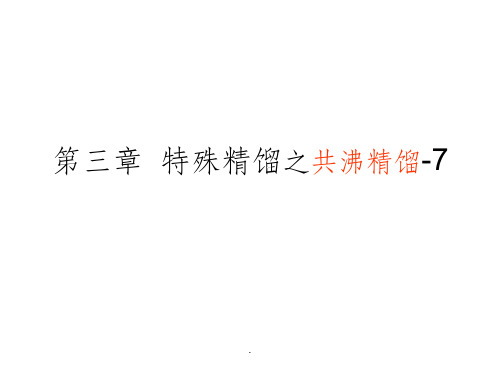
纯组分a、b作为不同精馏塔的 釜液采出。
.
选择中间沸点,并且与低沸点组分生成最低共沸物的物质 为共沸剂
Ta<Te<Tb, e-a生成最低共沸物T2<Ta。
xβ
若 xF < xα < xβ ,则应在1塔进料 物料衡算时,二塔塔釜多了一项水蒸气流量S。
假设1塔精馏段气相流量为V1液 相流量为L1。
在1塔精馏段的第n块塔板及2塔 釜出口之间作物料横算:
V1SL1B2
S
V 1y n 1 S L 1 x n B 2 x B 2
所以得1塔精馏段操作线方程:
yn1V L1 1xnV B1 2xB2
S (33)5
V1
.
假设1塔提馏段气相流量为V1’液 相流量为L1’。
在1塔提馏段的第n块塔板及1塔 塔釜出口之间作物料横算:
L'1V1' B1
L '1xnV 1'yn1B 1xB 1
S
所以得1塔提馏段操作线方程:
yn1V L1'1' xnV B11' xB1(332)
定节点。
.
2)a、b形成最高共沸物的情况 选择比原共沸温度更高的沸点且不形成共沸物的物质为共
沸剂
T2<Te, e-b和e-a均不形成共沸物。
e的加入使三角相图分为两个蒸 馏区域。
a、b分别位于不同区域,均为不 稳定节点。
纯组分a、b作为不同精馏塔的塔 顶馏出液采出。
纯组分e作为塔釜液采出。
化工分离过程(第8,9讲)(3.2多组分精馏过程分析)

15
3.2.3 最少理论塔板数和组分分配
对于非关键组分i有物料衡算式:
fi di wi
fi wi 1 d
可求得组分i在 将(3-12)式与上式联立得: 塔顶和塔釜的量
1 di fi wi wi
6
3.2.3 最少理论塔板数和组分分配
Fenske(芬斯克)公式推导前提
芬斯克推导了全回 流时二组分和多组 分精馏的严格解。 塔顶采用全凝器, 假设所有板都是理 论板,从塔顶第一 块理论板往下计塔 板序号。
7
3.2.3 最少理论塔板数和组分分配
Fenske方程推导过程:
从塔顶向下排序,由相对挥发度的定义有:
甲烷 乙烷(LK) 丙烯(HK) 丙烷 异丁烷 正丁烷
总计
5.0 35.0 15.0 20.0 10.0 15.0
100.0
15.0-0.025D 20.00 10.00 15.00
W
18
1.根据物料衡算可列方程组:
100 D W
解得:
5 35 0.05W 0.025D D
清晰分割假设对丙烷(4)不成立,须调整
21
5.调整(以前面的结果为初值,进行试差) 设d=0.6448,其它不变,重复1—4步 计算,至前面两次结果相近为止。
结果:
d d lg w l w h 6.805 Nm lg lh
校核
3.2.3 最少理论塔板数和组分分配
3、方程的变形形式:
摩尔分率可用摩尔数、体积或重量比来代替,因为换算 因子可以相互抵消,得到另一种常用的一般形式:
化工分离化工分离过程 11 - 第三章 3[1].6 吸收与解吸1
![化工分离化工分离过程 11 - 第三章 3[1].6 吸收与解吸1](https://img.taocdn.com/s3/m/6fd5b6462e3f5727a5e962eb.png)
LM c p, L / GM c p,V 0.2
46
热效应的处理方式:
(1)热效应忽略不计
当溶质浓度低、液气比大、溶解量小时,可视 为等温吸收,以吸收剂进塔温度作为全塔温度。 (2)仅考虑吸收热 当液气比较大时,可视为简单绝热吸收,全部 吸收热用于增加提高溶液的显热,提高溶液的温 度。
降低温度和提高压力具有相同的影响。
虽然吸收适于在低温下操作,但应避免采用冷冻 操作以减少动力消耗。
40
(3)液气比
液气比(L/V)与吸收剂用量直接相关,表示处 理单位原料气所需要的吸收剂量。 液气比大则吸收剂用量多。
液气比对吸收操作的影响与回流比对精馏操作的 影响相似。增大液气比将使各组分吸收因子增加, 因此增大液气比和增加操作压力或降低操作温度 有相同的效果。但随着液气比的增大,相应要增 大吸收剂的循环量和回收吸收剂的费用。
吸收过程气液平衡关系: 物理吸收:相平衡——亨利定律 化学吸收:相平衡——亨利定律; 化学平衡——化学平衡关系式
(1)物理吸收的气液相平衡关系
1) 低压下(low pressure) 气体在液体中的溶解度用Henry定律表示: x 2 p2 / H 或 p2 Hx2 x 2 ——溶质在液相中的溶解度(摩尔分数) p2 ——溶质在气相中的分压 H ——Henry系数,由溶质和溶剂的性质及温度 决定。
而反应平衡常数为:
K cM c Ac B c0 A cA c Ac B
则:
cA c0 A 1 K c B
总平衡又服从物理溶解时的亨利定律,因此:
pA
H c0 A A 1 K c B
(2) 化学吸收相平衡
H 0 A pA cA 1 k cB
化工分离过程第三章
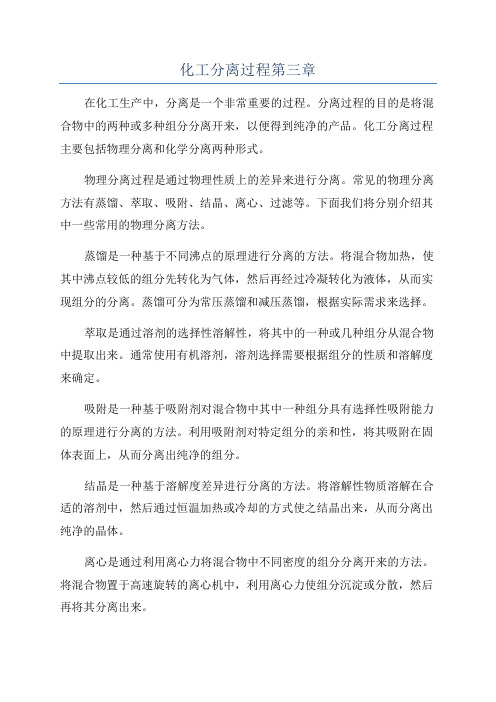
化工分离过程第三章在化工生产中,分离是一个非常重要的过程。
分离过程的目的是将混合物中的两种或多种组分分离开来,以便得到纯净的产品。
化工分离过程主要包括物理分离和化学分离两种形式。
物理分离过程是通过物理性质上的差异来进行分离。
常见的物理分离方法有蒸馏、萃取、吸附、结晶、离心、过滤等。
下面我们将分别介绍其中一些常用的物理分离方法。
蒸馏是一种基于不同沸点的原理进行分离的方法。
将混合物加热,使其中沸点较低的组分先转化为气体,然后再经过冷凝转化为液体,从而实现组分的分离。
蒸馏可分为常压蒸馏和减压蒸馏,根据实际需求来选择。
萃取是通过溶剂的选择性溶解性,将其中的一种或几种组分从混合物中提取出来。
通常使用有机溶剂,溶剂选择需要根据组分的性质和溶解度来确定。
吸附是一种基于吸附剂对混合物中其中一种组分具有选择性吸附能力的原理进行分离的方法。
利用吸附剂对特定组分的亲和性,将其吸附在固体表面上,从而分离出纯净的组分。
结晶是一种基于溶解度差异进行分离的方法。
将溶解性物质溶解在合适的溶剂中,然后通过恒温加热或冷却的方式使之结晶出来,从而分离出纯净的晶体。
离心是通过利用离心力将混合物中不同密度的组分分离开来的方法。
将混合物置于高速旋转的离心机中,利用离心力使组分沉淀或分散,然后再将其分离出来。
过滤是通过筛选方法将混合物中较大颗粒的固体分离出来的方法。
通过选用合适的过滤介质将混合物通过滤去,从而分离出较大颗粒的固体。
除了物理分离过程外,化工生产中还存在一种常见的化学分离过程,即化学反应。
化学反应是指在适当的条件下,将混合物中的不同组分通过化学变化转化为其他物质的过程。
化学分离过程通常需要借助催化剂和适当的反应条件来实现。
总之,化工分离过程是一项非常重要的工作,它能够将混合物中的各种组分分离出来,以获得纯净的产品。
物理分离过程包括蒸馏、萃取、吸附、结晶、离心和过滤等方法,化学分离过程则通过化学反应来实现。
在实际应用中,需要选择合适的分离方法和条件,以满足不同的生产需求。
- 1、下载文档前请自行甄别文档内容的完整性,平台不提供额外的编辑、内容补充、找答案等附加服务。
- 2、"仅部分预览"的文档,不可在线预览部分如存在完整性等问题,可反馈申请退款(可完整预览的文档不适用该条件!)。
- 3、如文档侵犯您的权益,请联系客服反馈,我们会尽快为您处理(人工客服工作时间:9:00-18:30)。
AB ( AB)顶( AB)釜
5.
或; AB 若分离要求
3(,式AB中)顶((xxABAB))釜(D、(xxABAB))进W
,Nm
.
返回
3.1.4 实际回流比、理论板数、进料位置
一、实际回流比R 由操作费、设备费确定
由经验取:
R=(1.1~1.5)Rm 二、理论板数
R R
1
0.62
Rm Rm
1
0.566
查图:N m 0.47 \ N 14.( 5 包括釜) N
设再沸器效率100%,塔中实际塔板数:
N
1
13.5 0.75
1( 8 块)
三、确定进料位置
lg([ 采用:nm
d f
)(l
f d
lg l h
)h
]
3.6
已知:N m N
全部组分均存在于进料板上
1.进料板附近各组分浓度变化较大,原因是 引入的组分包含全部组成。
2.对非关键组分 精馏段:HNK迅速消失; LNK以接近于常数浓度在进料板以上各 板中出现,接近顶部急剧增加,在出料 液中达到最高。 提馏段:LNK迅速消失; HNK在再沸器中浓度最高,从釜向上几 板下降较大,然后变化不大,一直延伸到 进料板。
1. Gilliand图和拟合形式
图3-12
N Nm N 1
—
R Rm R1
(N m,N包括釜)
由Rm、R、N m N
用Gilliand图简便、但不准确,回归的经验式为:
设X R Rm ;Y N Nm
R1
N 1
Y 1 exp([ (1 1154.141X7).2(X)X x1)] (3 16)
\Nm
lg([
xA xB
)D
(
x x
A B
)W
lg AB
]
(3 8)
— —Fenske方程
Fenske方程的各种形式:
用摩尔浓度表示:
Nm
lg([
x x
A B
)D
(
xA xB
)W
lg AB
]
(3 — 8)
用摩尔量、体积量、重量表示:
Nm
lg([ wd )A
lg
(wd )B ]
AB
(3 — 11)
2. i h在全塔可看成常数
依据:恒浓区概念
关联式:相平衡、物料平衡
Underwood公式:
ir(
i
xi,D )m
r
Rm
1
(3 3a)
iirrxi,F 1 q
(3 3b)
式中: i r —— i 对基准组分 r 的相对挥发度
取基准:① 最难挥发的组分(最重的组分)
重关键组分, 塔顶 重 塔釜
一、关键组分
1.关键组分的引出
一般精馏:
N
u a
5
对于设计型计算,5个可调设计变量为:
回流温度;进料位置;R;xD(i Di);xW(j Wj)
这里: Di
DxDi FxFi
—
i 在塔顶回收率
Wj
WxWj FxFj
—
j 在塔釜回收率
i:轻关键组分,表示:LK,下 标:l
([
xh xl
)F(
xl ,W xh,D
)2
W D
]0.206
N n m
(3 18)
例3—4 分离烃类混合物 例3—1 求出Rm=1.306;
例3—2求出Nm=6.805和物料衡算表
本题求N,进料位置 解:1.求R R=1.25Rm=1.634
2.求N
采用Erbar and Maddox关联图
0.47
故: Nm N
nm n
\
n
3.6 0.47
7.7
塔中实际
精馏段实际板:7.7
7.7 0.75
10块
板为18块
\进料位置为从下向上数第8块(不包括再沸器);
或从上向下数第11块
四、不同回流比下物料分配的比较
不同回流比物料分配如图(3—14)
对于操作情况,R=(1.2~2)Rm,由Fenske方程:
第一节 多组分精馏过程
3.1 .1多组分精馏过程分析 3..12 最小回流比 3.1.3最少理论塔板数和组分分配 3.1.4 实际回流比、理论板数、进料
位置
3.1.1 多组分精馏过程分析
关键组分: 在设计或操作控制中,有一定分离要求, 且在塔顶、塔釜都有一定数量的组分称为关 键组分 轻关键组分,指在塔釜液中该组分的浓度 有严格限制,并在进料液中比该组分轻的组 分及该组分的绝大部分应从塔顶采出
或:Y 0.75 0.75X 0.5668 (3 17)
已知X,由(3—16)或(3—17)解出y
2. Erbar and Maddox关联图:
比Gilliand图精确,误差4.4%
图3—13
Rm — R — Nm Rm 1 R 1 N
三、适宜进料位置的确定
1. 设n为精馏段理论板数
◆工艺要求先分出A:
则:A为LK;B为HK
多组分精馏过程的复杂性
①求解方法 二组分精馏:无需试差 多组分精馏:反复试差求解 ②摩尔流率 二元精馏:在进料板处液体组成有突变, 各板的摩尔流率基本为常数 多组分精馏:液、汽流量有一定的变化, 但液汽比接近于常数
二组分精馏 流量、温度、 浓度分布
二元精馏
1. Rm 时,恒浓区出现的情况
二元精馏:
e
恒浓区
Rm
xD ye ye xe
y
恒浓区:一个,出现在
xW x xD
进料板
——上恒浓区
——下恒浓区
所有组分 为分配组 分
只有LNK为 非分配组分
只有HNK为 非分配组分
LNK和HNK 都为非分配 组分
2. Rm 的计算
采用Underwood法计算: 该法假设:1.恒摩尔流
3.关键组分
变化复杂
▼ 若无LNK时:HK分别在二段出现两个最高点, LK表现象LNK。
▼ 若无HNK时:LK分别在二段出现两个最高点, HK表现象HNK。
▼有LNK、HNK,且都不同时出现在顶、釜时:
LK在精馏段出现一个最大值,然后降到所规定 的浓度;
HK在提馏段出现一个最大值,然后降到所规的
浓度。
由(1):(
yA yB
)1
(
AB)(1
xA xB
)1
(
xA xB
)D
将(2)代入:( 又由(1):( yA
yB
xA xB )2
)(D (AB)(A2B)xx(1BA )yy2BA
)2
又将(2)代入:(
y y
A B
)2
(
AB)(2
yA yB
)3
\
(
x x
A B
)D
(
AB)(1
意义:◆操作前的准备工作
◆ 测出 N m
特点:★F=D=W=0 ★ L=V;L/V=1
★操作线方程: yn1,i xn,i
★板效率 最高
采用Fenske方程求最少理论板数,推导如下:
设A、B分别表示二个不同组分,板序由上向下
AB
(
y x
A A
)(
yB xB
)(
yA yB
)(
x x
不用对数表示:
(wd )A AB N m(wd )B
(3 — 12)
Fenske方程说明:
1. 全凝器,( xA xB)D 为其液相产品浓度比; 分凝器,( xA xB)D 为其汽相产品浓度比。
2. 求出的Nm数,包括塔釜、分凝器二级。 3. 公式由A、B导出,可用于二元和多元
二元:BA为为挥挥发发性性小大的的组组分分;多元:BA为为HLKK 4. ( AB)均的一般计算
清晰分割:轻组分在塔顶产品的收率为1。重组分 在塔釜产品的收率为1 轻组分全部从塔顶馏出液中采出,重组分全部从 塔釜排出 非关键组分为非分配组分 非清晰分割:非关键组分为分配组分
4. 关键组分的指定原则 由工艺要求决定
例:ABCD(按挥发度依次减少排列)混合物 分离 ◆工艺要求按AB与CD分开:
则:B为LK;C为HK
温度分布:在塔顶塔底处变化较慢,其它 位置变化较快;多元精馏此情形不明显, 在接近塔顶、塔底和进料处变化较快,且 全塔温差变大。
浓度分布:在精馏段、提馏段中部变化明 显,塔顶、塔底附近变化较慢,其它位置 变化较快。
苯、甲苯、异丙苯精馏 塔内汽液流量分布
多元精馏的流量分布:
影响L、V的几个因素: 1)摩尔汽化潜热变化使沿塔向上的摩尔流率 有增加的趋势; 2)蒸汽上升中需被冷却,导致向上流量增加;
l r , hr之间试差出几个,解出
几个Rm,最后取平均值。
例3—1 计算最小回流比
已知:xi,F , xi,D ,q 1.0
解:由(3—3b)试差 1.325
返回
将 1.325代入(3—3a)得 Rm 1.306
3.1.3 最少理论板数和组分分配
1.最少理论板数
R 时, N Nm
本章目录
温 度 分 布
苯、甲苯、异丙苯精馏塔内温度分布
温度分布从再沸器到冷凝器单调下降 进料板处温度变化明显
浓 度 分 布
只有HK,LK,HNK情况
浓 度 分 布
只有LK,HK,LNK