窑炉设计的基础
《窑炉学》设计计算.ppt

现所需砖长:n′/110=630/110=5.73,取6块砖长;
实际装砖块数:110×6=660块/车; 实际装砖量:g=4.2×660=2.772t/车。 考虑到尚有部分特、异型砖,取g=2.8t/车,则
J g 60 24 350 0.90 2 . 8 60 24 G 10000 成 127 m in
168 192 216 240 264 288 312 336 360 384 408 432 455 480 504 528 552 576 601 624
7)窑的有效容积: V车=F断· l=1.805×2.0=3.61m3 8)平均装窑密度:
g 2 . 8 3 1000 776 kg / m V . 61 车 3
9)拱顶(内衬)配砖计算
高温带可选用(20#~31#车位处)中档镁铝砖 :
T-43(230×65/55×114)
镁铝砖2块/环
6092 60 N 46 辆 120
5)窑长L、各带长度
τ1=τ预热=42h;τ2=τ烧成=18h; τ3=τ冷却=32h
L l N 2 46 92 m 1 42 L1 L 92 42 m( 21车位 ) 92 2 18 L2 L 92 18 m9车位 92 L3 L L1 L2 32 m(16车位 )
倾斜角 180 (a a1 ) πb 15°05′ 10°03′ 5°02′
体积 cm3 1311.0 1442.1 1573.2
Tc-21 C1163 114 65 35 230 114×65/35×230 Tc-22 C1164 114 65 45 230 114×65/45×230
窑炉设计
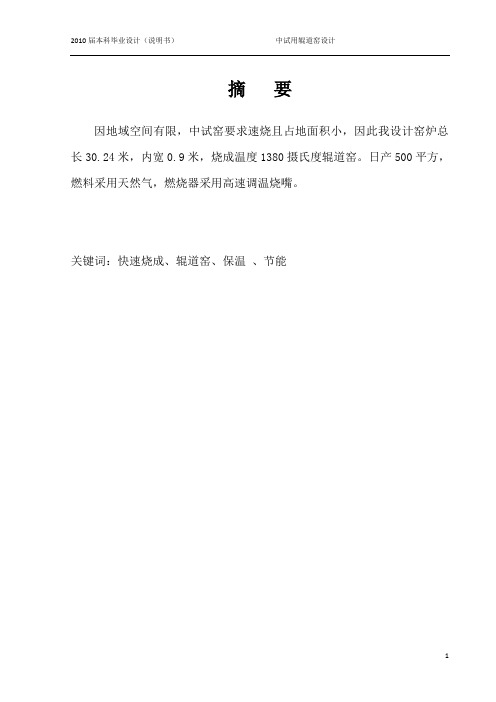
摘要因地域空间有限,中试窑要求速烧且占地面积小,因此我设计窑炉总长30.24米,内宽0.9米,烧成温度1380摄氏度辊道窑。
日产500平方,燃料采用天然气,燃烧器采用高速调温烧嘴。
关键词:快速烧成、辊道窑、保温、节能目录摘要 (1)前言 (3)1设计任务书及原始资料 (5)2.1 内宽的确定 (5)2.2 窑体长度的确定 (5)2.3 烧成制度的确定 (6)2.4 窑内高度的确定 (7)3工作系统的确定 (7)3.1 排烟系统 (7)3.2 燃烧系统 (8)3.3 冷却系统 (8)3.4 传动系统 (10)3.5 窑体附属结构 (11)4窑体材料确定 (13)5燃烧计算 (14)5.1 燃料组成: (14)5.2 燃烧所需空气量 (14)5.3 燃料产生烟气量 (15)5.4 燃烧温度计算 (15)6物料平衡计算 (16)7预热带烧成带热平衡计算 (17)7.1 热平衡计算准则 (18)7.2 热平衡示意图 (18)7.3 热收入项目 (18)7.4 热支出项目 (19)7.5 列热平衡方程并求解 (35)7.6 列热平衡表 (35)8冷却带热平衡计算 (36)8.1 热平衡计算准则 (36)8.2 热平衡示意图 (36)8.3 热收入 (37)8.4 热支出 (37)8.5 列热平衡方程 (43)8.6 列热平衡表 (44)9烧嘴选型 (44)10管道尺寸、阻力计算及风机的选用 (45)11工程材料概算 (52)后记 (55)参考资料 (56)前言随着经济不断发展,人民生活水平的不断提高,陶瓷工业在人民生产、生活中都占有重要的地位。
陶瓷的发展与窑炉的改革密切相关,一定结构特点的窑炉烧出一定品质的陶瓷。
因此正确选择烧成窑炉是获得性能良好制品的关键。
陶瓷窑炉可分为两种:一种是间歇式窑炉,比如梭式窑;另一种是连续式窑炉,比如辊道窑。
辊道窑由于窑内温度场均匀,从而保证了产品质量,也为快烧提供了条件;而辊道窑中空、裸烧的方式使窑内传热速率与传热效率大,又保证了快烧的实现;而快烧又保证了产量,降低了能耗。
窑炉设计说明书

窑炉设计说明书窑炉设计说明书随着工业化进程的不断发展,窑炉作为重要的热处理设备,在各行各业中得到了广泛应用。
窑炉的设计直接关系到生产效率、产品质量和能源利用效率等多个方面,因此合理的窑炉设计对企业和社会具有重要的意义。
本篇说明书将从窑炉设计的主要内容、设计要求、设计流程等方面进行详细阐述,给设计师提供指导和参考。
一、窑炉设计的主要内容1. 窑炉的类型选择:根据不同的工艺要求,窑炉可以按照不同的类型进行选择,如干燥窑、煅烧窑、焙烧窑等。
需要根据具体工艺要求进行综合考虑和分析。
2. 窑炉的能源选择:窑炉的能源选择是设计中非常关键的环节,直接关系到窑炉的能耗和经济效益。
常见的能源有燃油、天然气、生物质、电力、太阳能等,需要针对性地进行选择。
3. 窑炉的结构设计:窑炉的结构设计包括炉体、炉膛、排风系统、进料系统等多个方面。
要考虑到热平衡、热损失、热扩散等因素,确保设计的结构具有较好的热工性能和稳定性。
4. 窑炉的控制系统设计:窑炉的控制系统设计是窑炉运行的重要保障,要根据工艺要求选用适当的自动化设备,并进行专业的编程和调试,以达到理想的自动化控制效果。
5. 窑炉的安全设计:窑炉是一种高温设备,必须注重安全设计,确保在窑炉的运行过程中不会出现火灾、爆炸等意外事故,同时还要注意排放尘埃、气体和废水等环保问题。
二、窑炉设计的要求1.符合国家安全标准和环保要求:窑炉设计应符合国家颁布的安全标准和环保要求,确保在生产过程中能够达到稳定、安全、高效、环保的目标。
2. 考虑生产规模和节能性:窑炉设计要考虑企业的实际生产规模,适当考虑窑炉的扩容设计,同时还要注重节能和资源的有效利用,减少能耗和环境污染。
3. 窑炉的稳定性和耐久性:窑炉的稳定性和耐久性是设计的重要指标之一,要考虑到窑炉在高温和受力状态下的耐磨性、耐腐蚀性和耐用性等因素。
4. 针对不同工艺要求进行专业设计:窑炉的设计需要根据不同的工艺要求进行专业设计,力求达到最佳的生产效果和品质标准。
窑炉热工设计方案

窑炉热工设计方案窑炉热工设计方案一、设计要求1. 窑炉热工效率高;2. 窑炉温度稳定,热量损失小;3. 窑炉操作简便,易于维护;4. 窑炉排放物符合环保要求。
二、设计方案1. 窑炉燃料选择考虑到热工效率和环保要求,选择使用天然气作为窑炉的燃料。
天然气燃烧完全,热效率高,且排放物少,符合环保要求。
2. 窑炉结构设计为了减少热量损失,窑炉的外壳应采用耐高温材料,如高铝砖。
内部衬砖的选择要具有优良的耐火性能和耐高温性能,以确保窑炉的稳定操作和长寿命。
3. 窑炉热风供应系统设计采用电风机将空气送入窑炉,通过调节电风机的转速来控制供氧量,从而控制窑炉的燃烧热量。
在热风进入窑炉前,设置预热装置对热风进行预热,以提高燃烧效率。
4. 窑炉温度控制系统设计采用智能控制系统对窑炉温度进行实时监测和调整。
系统根据设定的温度范围,自动调节燃料供应和热风供应,保持窑炉温度的稳定性。
5. 窑炉废气处理系统设计窑炉废气中的烟尘和有害气体需要进行处理,以符合环保排放标准。
设计废气处理系统,在烟道中设置过滤装置和脱硫装置,净化废气后再进行排放。
6. 窑炉维护与检修设计为了便于操作和维护,窑炉的各个部分应设计为模块化结构。
轴承、密封件等易损件应采用优质耐磨材料,并设置易于更换的装置,以方便日常维护和检修。
三、设计效益1. 窑炉热工效率高,能耗低,节约能源;2. 窑炉温度稳定,产品质量高;3. 窑炉操作简便,减少操作人员的劳动强度;4. 窑炉废气排放符合环保要求,保护环境。
综上所述,窑炉热工设计方案应综合考虑热工效率、温度控制、废气处理等因素,以提高窑炉的热能利用率和环保性能。
通过合理选择燃料、优化窑炉结构、设计先进的控制系统和废气处理系统,可以实现窑炉的高效运行和可持续发展。
玻璃窑炉设计技术

玻璃窑炉设计技术第一章单元窑用来制造E玻璃和生产玻璃纤维的窑炉,通常采用一种称为单元窑的窑型。
它是一种窑池狭长,用横穿炉膛的火焰燃烧和使用金属换热器预热助燃空气的窑炉。
通过设在两侧胸墙的多对燃烧器,使燃烧火焰与玻璃生产流正交,而燃烧产物改变方向后与玻璃流逆向运动。
因此在单元窑内的玻璃熔化、澄清行程长,比其它窑型在窑内停留时间长,适合熔制难熔和质量要求高的玻璃。
单元窑采用复合式燃烧器,该燃烧器将雾化燃料与预热空气同时从燃烧器喷出,经烧嘴砖进入窑炉内燃烧。
雾化燃料处在燃烧器中心,助燃空气从四周包围雾化燃料,能达到较好的混合。
所以与采用蓄热室小炉的窑型相比,燃料在燃烧过程中更容易获得助燃空气。
当空气过剩系数为1.05时能完全燃烧,通过调节燃料与助燃空气接触位置即可方便地控制火焰长度。
由于使用多对燃烧器,分别调节各自的助燃风和燃料量,则可以使全窑内纵向温度分布和炉内气氛满足玻璃熔化与澄清的要求,这也是马蹄焰窑所无法达到的。
单元窑运行中没有换火操作,窑内温度、气氛及窑压的分布始终能保持稳定,这对熔制高质量玻璃有利。
现代单元窑都配置有池底鼓泡,窑温、窑压、液面及燃烧气氛实行自动控制等系统,保证了难熔的E玻璃在较高熔化率下能获取用于直接拉制玻璃纤维的优质玻璃液。
所以迄今在国际上单元窑始终是E玻璃池窑拉丝的首选窑型。
单元窑与其它窑型相比的不足之处是能耗相对较高。
这是因为单元窑的长宽比较大,窑炉外围散热面积也大,散热损失相对较高。
采用金属换热器预热助燃空气的优点是不用换火,缺点是空气预热温度,受金属材料抗氧化、抗高温蠕变性能的制约,一般设计金属换热器的出口空气温度为650—850。
大多数单元窑热效率在15%以内,但如能对换热器后的废气余热再予利用,其热效率还可进一步提高。
配合料在单元窑的一端投入,投料口设在侧墙的一边或两边,也有设在端墙上的。
熔化好的玻璃从另一端穿过沉式流液洞流至称为通路的拉丝作业部。
第一节单元窑的结构设计一、单元窑熔化面积的确定单元窑熔化面积可用公式F= G/g表示。
窑炉设计

景德镇陶瓷学院《窑炉课程设计》说明书题目:年产860万件汤盘天然气隧道窑设计说明书目录前言一、设计任务书 (4)二、烧成制度的确定2.1 温度制度的确定 (5)三、窑体主要尺寸的计算..3.1棚板和立柱的选择 (5)3.2窑长及各带长的确定 (5)3.2.1 装车方法 (5)3.2.2 窑车尺寸确定 (6)3.2.3窑内宽、内高、全高、全宽的确定 (6)3.2.4 窑长的确定 (7)3.2.5 全窑各带长的确定 (7)四、工作系统的确定4.1 排烟系统 (7)4.2 燃烧系统 (8)4.3 冷却系统 (8)4.4 传动系统 (8)4.5 窑体的附属结构 (8)五、窑体材料及厚度的选择 (8)六、燃料燃烧计算 (12)七、物料平衡计算 (13)八、热平衡计算 (14)九.冷却带的热平衡计算 (18)十、烧嘴的选用 (21)十一、心得体会 (22)十二、参考文献 (23)前言隧道窑是耐火材料、陶瓷和建筑材料工业中最常见的连续式烧成设备。
是以一条类似铁路隧道的长通道为主体,通道两侧用耐火材料和保温材料砌成窑墙,上面为由耐火材料和保温材料砌成的窑顶,下部为由沿窑内轨道移动的窑车构成的窑底形成的一种烧成过程。
随着经济的不断发展,陶瓷工业在人民生产、生活中都占有重要的地位。
陶瓷的发展与窑炉的改革密切相关,某一种特定的窑炉可以烧制出其他窑炉所不能烧制的产品,而有时需要一种特定的产品,就需要对其窑炉的条件加以限制,因此,配方和烧成是陶瓷制品优化的两个重量级过程,每个过程都必须精益求精,才能得到良好,称心的陶瓷制品。
隧道窑是现代化的连续式烧成的热工设备,以窑车为运载工具,具有生产质量稳定、产量大、消耗低的特点,最适合于工艺成熟批量生产的日用瓷。
由于现在能源价格不断上涨,为了节约成本,更好的赢取经济利益,就需要窑炉在烧成过程中严格的控制温度制度、气氛制度,压力制度,提高生产效率及质量,更好的向环保节能型窑炉方向发展。
实验窑炉设计方案
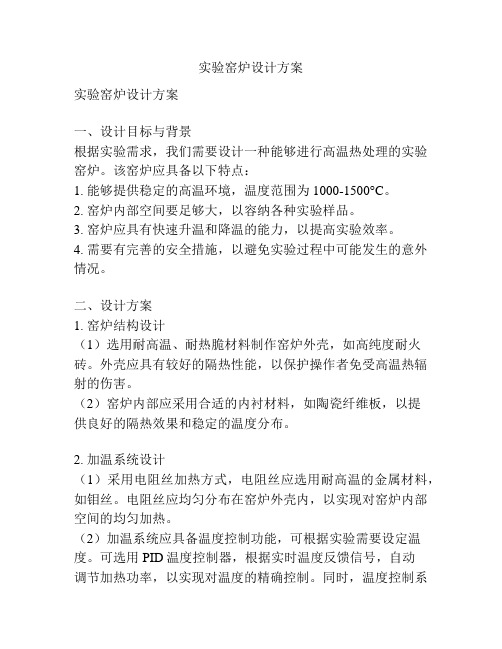
实验窑炉设计方案实验窑炉设计方案一、设计目标与背景根据实验需求,我们需要设计一种能够进行高温热处理的实验窑炉。
该窑炉应具备以下特点:1. 能够提供稳定的高温环境,温度范围为1000-1500°C。
2. 窑炉内部空间要足够大,以容纳各种实验样品。
3. 窑炉应具有快速升温和降温的能力,以提高实验效率。
4. 需要有完善的安全措施,以避免实验过程中可能发生的意外情况。
二、设计方案1. 窑炉结构设计(1)选用耐高温、耐热脆材料制作窑炉外壳,如高纯度耐火砖。
外壳应具有较好的隔热性能,以保护操作者免受高温热辐射的伤害。
(2)窑炉内部应采用合适的内衬材料,如陶瓷纤维板,以提供良好的隔热效果和稳定的温度分布。
2. 加温系统设计(1)采用电阻丝加热方式,电阻丝应选用耐高温的金属材料,如钼丝。
电阻丝应均匀分布在窑炉外壳内,以实现对窑炉内部空间的均匀加热。
(2)加温系统应具备温度控制功能,可根据实验需要设定温度。
可选用PID温度控制器,根据实时温度反馈信号,自动调节加热功率,以实现对温度的精确控制。
同时,温度控制系统应具备过温保护功能,一旦温度超过设定上限,应能自动切断加热电源,以确保实验安全。
3. 冷却系统设计(1)冷却系统应采用强制风冷方式,以提供快速降温的能力。
可选用风扇和散热片组成的冷却系统,通过强制循环冷却空气,将窑炉内部温度迅速降低至环境温度。
(2)冷却系统应具备温度控制功能,可根据实验需求设定降温速率。
可选用PID温度控制器,根据实时温度反馈信号,自动调节风扇转速,以实现对降温速率的控制。
4. 安全措施设计(1)在窑炉外壳上设置观察窗口,以便操作者观察实验过程。
(2)在窑炉外壳上设置紧急停止按钮,一旦发生意外情况,操作者可立即切断加热电源。
(3)在窑炉外壳上设置温度报警装置,一旦温度超过设定上限,报警装置应发出警报。
(4)为了保护操作者的安全,窑炉外壳应具备良好的隔热性能,避免高温热辐射对操作者造成伤害。
窑炉设计
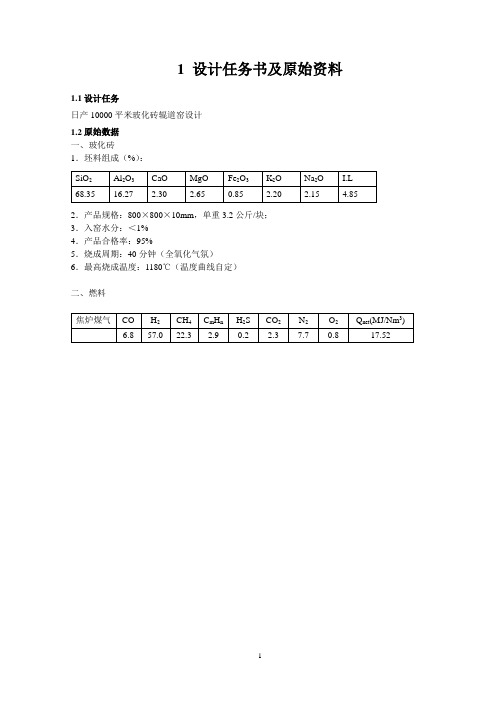
1 设计任务书及原始资料1.1设计任务日产10000平米玻化砖辊道窑设计1.2原始数据一、玻化砖1.坯料组成(%):2.产品规格:800×800×10mm,单重3.2公斤/块;3.入窑水分:<1%4.产品合格率:95%5.烧成周期:40分钟(全氧化气氛)6.最高烧成温度:1180℃(温度曲线自定)二、燃料2 窑体主要尺寸的确定2.1 窑内宽的确定产品的尺寸为800×800×10mm,设制品的收缩率为10%。
由坯体尺寸=产品尺寸/(1-烧成收缩),得坯体尺寸为:889mm两侧坯体与窑墙之间的距离取150mm,设内宽B=2.5m,取产品长边平行于辊棒,计算宽度方向坯体排列的块数为:n=(2500-150×2)/889=2.5,确定并排3块。
确定窑内宽 B=889×3+150×2=2967mm,取3000mm。
2.2 窑长及各带长度的确定2.2.1 窑体长度的确定窑容量=(日产量×烧成周期)÷[24×产品合格率]=(10000×40/60)÷(24×95%)=292.40(㎡/窑)装窑密度=每米排数×每排片数×每片砖面积=(1000÷889)×3×0.82=2.16(㎡/每米窑长)窑长L=窑容量(㎡/窑)÷装窑密度(㎡/每米窑长)=292.40÷2.16=135.37(m)利用装配式,由若干节联接而成,设计每节长度为2120mm,节间联接长度8mm,总长度2128mm,窑的节数=135370÷2128=63.61节,取整为64节。
所以算出窑长为L=2128×64=136192mm2.2.2 窑体各带长度的确定预热带占全窑总长的40%,节数=64×40%=25.6,取26节,长度=26×2128=55328mm;烧成带占全窑总长的22%,节数=64×22%=14.08,取14节,长度=14×2128=29792mm;冷却带占全窑总长的38%,节数=64×38%=24.32,取24节,长度=24×2128=51072mm。
- 1、下载文档前请自行甄别文档内容的完整性,平台不提供额外的编辑、内容补充、找答案等附加服务。
- 2、"仅部分预览"的文档,不可在线预览部分如存在完整性等问题,可反馈申请退款(可完整预览的文档不适用该条件!)。
- 3、如文档侵犯您的权益,请联系客服反馈,我们会尽快为您处理(人工客服工作时间:9:00-18:30)。
实证明,这种改进在降低烧成成本,提高制品的质量方面却是真正有效的。
确定改进窑炉设计是否真的值得进行也是个问题。
令人遗憾的是整个陶瓷行业在烧成技术的细节方面都缺乏训练。
判断设计改造是否合理的最佳方法是发挥那些热工工程师的作用。
用户往往去找硬件供应者来解决窑炉的问题。
人们往往过多地注意应用,而忽略了优秀设计所提供的详细数学计算。
窑体的构件有助于窑体结构构成,然而真正重要的还是热能向制品的热传递。
如果传热过程合理,那么其它问题都迎刃而解了。
要求用户对打算建造的窑炉作出评价或在向一件件个别的制品传热的基础上对窑炉提出改进意见是不可能的。
有时涉及传热的讨论只是对整个窑体而言,而这种讨论并不充分。
成功的窑炉总是来自对制品提供最佳的传热尝试,要做到这一点,就必须对那些传热理论基础有很好的理解。
常见的陶瓷烧成方法主要有两种:即燃料加热和电加热。
烧成方式有时是由所采用的工艺过程来决定的。
也有些特殊情况,如热压和真空烧成,都清楚地说明了烧成的方式。
在电加热或马弗式加热的烧成情况下,能源几乎都是直接辐射,所以,发热体的类型、发热体的布局和窑室的形状都十分重要。
不同形状窑室的作用可以进行精确计算。
合理的窑炉应建立在经验和计算这两种基础上。
窑炉的用途越新,设计工作越应建立在计算的基础上。
在有些场合,窑炉的详细计算不仅是为了安装,也是为了让用户的工程师们进行验证。
采用燃料烧成的陶瓷窑炉几乎全部传热都是通过辐射来完成的。
尽管在有些窑炉内存在着烧成制品的运动(如采用高速喷燃器),但对流缺乏足够的速度以向各个部分传递更多的热量。
如果跨越每件制品之间的对流速度达到足以传递大量的热能,那么即使在低温下,热空气也会在各小件制品间分布得很均匀。
因为对流传热即使在低温下也小于15%,所以热量还是必须通过辐射来传递。
辐射以两种方式产生:一种是来自喷燃器的直接辐射(甚至在低温);另一种是对传热具有重要贡献的来自热的燃烧产物的辐射。
此外,水蒸汽和CO2能进行强烈的辐射并能在窑室内流动。
喷燃器相对于装烧物和烟气的位置以及烟气相对于装烧物和喷燃器的位置的精确安排至关重要,这些因素是决定燃烧型窑炉内温度均匀性的主要因素。
每个热源的作用可以重新计算,但很繁琐,因为涉及到象装烧制品的形状及装烧物作为一个整体的形状这样许多技术问题。
可这项工作又很值得做,它可以清晰地反映出所建窑炉期望达到的工作效率。
各类窑炉的相关计算是相同的,主要差别是与窑内的气体运动有关的计算方法不同。
在充满H2和N2气体的辐射型窑炉内不存在来自气体辐射的实际作用,只有一定的对流作用(虽然这种对流作用很小)。
由于装烧物自身会成为其后面装烧物的辐射屏障,所以计算出装烧物之间的空间及与热源之间的距离十分重要。
这再次不可避免地使人们想到向一件件个别装烧物的传热。
陶瓷行业的大多数电窑只不过是个获取热能的容器,如果时间足够长,那么整个装烧物就会达到相同的温度,但整个装烧物中的每件制品所经受的热处理却绝对不相同。
究竟采用直接辐射还是采用燃料燃烧的方式加热,关键在于制品的装烧位置是否能使辐射热正好落在制品上并包围着制品。
如果采用电加热直接辐射,那么制品周围的辐射距离应当很窄,一个典型的设计是制品与周围的发热体间的空间窄而高。
除非是在真空,否则周围的发热体必须被分段测量和控制,以使上下温度一致。
另一种典型的设计是使制品的上下都具有低而宽的加热空间。
当然,上下
两部分的发热体也必须分别检控。
如果采用燃料燃烧的方法加热,那么热源就不那么重要,在这种情况下,燃烧产物的运行途径显得非常重要。
燃烧产物必须按照一定的途径确定自己通往烟道的运行路线,以便使这些燃烧所产生的气体从被烧制品的周围和上方通过后再进入烟道。
使用燃料烧成窑炉的一种典型设计是让燃烧产生的气体沿某个方向在狭窄的通道穿过窑内。
装烧物被窑中心的烟道分割成许多小单元。
最典型的是烟气倒流以维持对燃烧产物流向的完全控制。
烟气负压把热的辐射气体吸引通过一细柱制品以产生非常均匀的传热。
图1、图2和图3是一小型间歇窑的剖面图。
图1是匣体柱沿着窑体长度的排布方式;图2是窑的末端可能出现的排列方式,注意喷燃器刚好被设在钵柱旁边的开阔通道处,另外还需要注意到烟道开口正好对着钵柱之间的烟气。
通向烟道的通道只穿过钵柱很短的距离。
倒焰烟道促进了窑内烟气的定向排出,这是设计者所希望的。
要想强化的每个匣钵周围均匀出现的燃烧产物的辐射,严格控制烟气的方向是关键。
图3是该窑的空间视图。
它可以帮助看清窑的装法、喷燃器和气体运动路线,如果各独立控制范围可保证在3—4英尺高,则这种窑的匣钵柱可以装得很高,窑的宽度可视喷燃器的允许程度而定。
若窑较窄,采用低速喷燃器就可以了,若窑较宽,则需要高速喷燃器,以保证所有喷嘴喷出的热气都能够喷到窑的另一边。
高速喷燃器不仅是为了满足均匀传热的需要,更重要的是它恰如其分地开创了一种新的装窑方式,并适当地确定了喷燃器和烟道的位置。
在燃烧系统中使用动力确实有助于均匀传热,但是为了保证其有效性动力的应用必须适当。
高速喷燃器能够造成湍流,但失控的湍流蔽多利少。
最关键的是使
建成的窑炉能把热量引向均匀环绕每件个别陶瓷制品流动的通道。
应当注意,传热设计的运用是决定一座窑炉是新颖还是陈旧的基础。
在准备改进一座现存窑炉时,工程师在作出任何决定前,必须注意先前这座窑炉设计中的传热情况。
在这样一种研究的基础了,工程师便可得出如下结论:某窑只需作些简单的改变便可使制品的烧成产生重大差别。
工程师也可能得出这样的结论:某窑需要作复杂的大手术。
在这种情况下,必须从经济角度进行细致的研究,以决定是对现存窑炉进行改造,还是另建一座新窑。
只简单地改造一下喷燃器或控制系统就能达到所需要的改进情况是罕见的。
如果窑炉设计得好,就会建造出一座低成本、短周期烧出高质量产品的窑炉。
对窑炉做出较有效的改进比只简单地改变窑炉的硬件往往更省钱。
窑体结构和建筑材料设计得当固然重要,但千万不要忘记建窑的首要目的。
不要被较低的建窑费用引入歧途,因为烧成每件陶瓷器的长期成本更为重要。
不要把一个砌筑良好的窑体同一座把向制品的传热设计得很适当的窑混为一谈。
今天,人们更加要求陶瓷工业满足越来越高的质量标准。
陶瓷器的烧成质量与窑的传热密切相关。
传热卓越的窑也就是烧成周期最短,单件制品烧成成本最低的窑。
经济效益不易看见,但却值得重视。
任何窑如果不按最佳传热原则进行设计和建造都会遭到失败。
能理解窑内传热复杂性的工程师,同样能够很好地完成窑体结构和筑窑材料的设计。