连铸技术介绍讲解
连铸原理与工艺
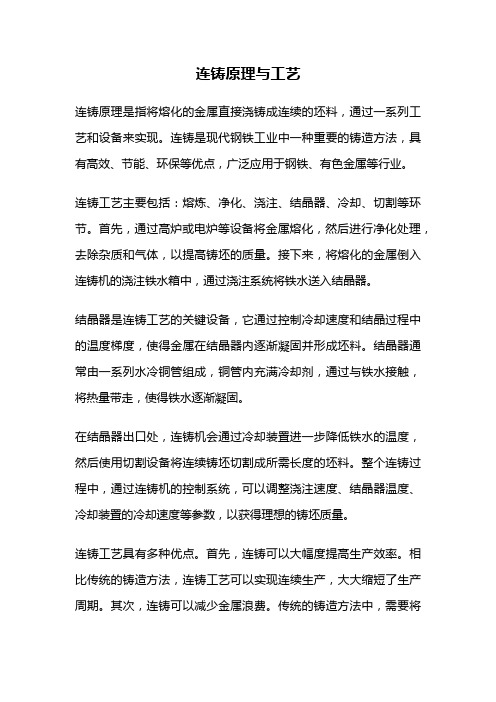
连铸原理与工艺连铸原理是指将熔化的金属直接浇铸成连续的坯料,通过一系列工艺和设备来实现。
连铸是现代钢铁工业中一种重要的铸造方法,具有高效、节能、环保等优点,广泛应用于钢铁、有色金属等行业。
连铸工艺主要包括:熔炼、净化、浇注、结晶器、冷却、切割等环节。
首先,通过高炉或电炉等设备将金属熔化,然后进行净化处理,去除杂质和气体,以提高铸坯的质量。
接下来,将熔化的金属倒入连铸机的浇注铁水箱中,通过浇注系统将铁水送入结晶器。
结晶器是连铸工艺的关键设备,它通过控制冷却速度和结晶过程中的温度梯度,使得金属在结晶器内逐渐凝固并形成坯料。
结晶器通常由一系列水冷铜管组成,铜管内充满冷却剂,通过与铁水接触,将热量带走,使得铁水逐渐凝固。
在结晶器出口处,连铸机会通过冷却装置进一步降低铁水的温度,然后使用切割设备将连续铸坯切割成所需长度的坯料。
整个连铸过程中,通过连铸机的控制系统,可以调整浇注速度、结晶器温度、冷却装置的冷却速度等参数,以获得理想的铸坯质量。
连铸工艺具有多种优点。
首先,连铸可以大幅度提高生产效率。
相比传统的铸造方法,连铸工艺可以实现连续生产,大大缩短了生产周期。
其次,连铸可以减少金属浪费。
传统的铸造方法中,需要将金属熔化后倒入铸型中,过程中会有一定的浪费。
而连铸工艺中,可以直接将熔融金属浇注成坯料,减少了金属的浪费。
此外,连铸还可以提高产品质量。
连铸的结晶过程中,金属凝固速度较快,晶粒细小,可以获得更均匀、致密的铸坯。
最后,连铸工艺对环境友好。
相比传统的铸造方法,连铸工艺中不需要使用砂型和砂芯,减少了对环境的污染。
然而,连铸工艺也存在一些挑战和问题。
首先,连铸过程中会产生较高的温度和压力,对设备和工艺的要求较高。
此外,连铸中还容易产生缺陷,如气孔、夹杂等,需要通过净化和控制工艺参数来解决。
另外,连铸工艺对结晶器的要求较高,结晶器的结构和材料需要经过精心设计和选择,以保证连续铸造的稳定性和质量。
连铸原理与工艺是一种高效、节能、环保的铸造方法,通过熔炼、净化、浇注、结晶器、冷却和切割等环节,将熔化的金属直接浇铸成连续的坯料。
连铸基础理论课件
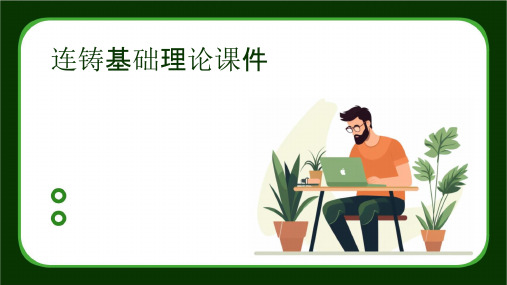
裂纹与夹杂物问题
裂纹
夹杂物
鼓肚与弯曲问题
鼓肚
鼓肚是指连铸坯在厚度方向上鼓出的现 象,主要由于结晶器内钢水热膨胀和凝 固收缩所致。为解决这一问题,可以优 化结晶器设计和操作,如降低冷却强度等。
VS
弯曲
连铸坯弯曲是由于钢水凝固过程中不均匀 收缩所致。为解决这一问题,可以调整引 锭杆的位置和速度,以及加强拉坯过程中 的矫直措施等。
表面质量与内部质量的问题
表面质量
内部质量
连铸过程中的生产事故及其预防措施
生产事故
预防措施
06
未来连铸技术的发展趋 势与研究方向
CHAPTER
提高生产效率与节能减排的措施
高效化生产
节能减排
优化工艺流程
智能化与自动化技术的应用与发展
智能化控制 自动化生产 信息化管理
新材料与新工艺的应用与研究热点
电磁搅拌
电磁搅拌是利用电磁力作用,使钢水在结晶器内产生旋转运动,以增加坯壳的均匀性和减小坯壳的变形。电磁搅 拌分为在线搅拌和离线搅拌两种方式。
轻压下技术
轻压下技术是指在连铸过程中,通过施加一定的压力来控制铸坯的鼓肚和裂纹等缺陷。轻压下技术分为在线轻压 下和离线轻压下两种方式。
05
连铸技术中的常见问题 及解决方案
连铸基础理论课件
• 连铸技术概述 • 连铸机基本结构与工作原理 • 连铸坯凝固过程及控制要素 • 连铸工艺及控制要素 • 连铸技术中的常见问题及解决方案 • 未来连铸技术的发展趋势与研究方向 • 总结与展望
01
连铸技术概述
CHAPTER
连铸技术的定义
连铸技术的定义
连铸技术的特点
连铸技术具有高效、节能、环保等优 点,是金属材料制备和成型的重要手 段之一。
连铸的原理

连铸的原理
连铸是一种先进的铸造工艺,它通过在同一设备上连续进行浇铸和凝固,实现了铸坯的一次成型,大大提高了生产效率和产品质量。
连铸的原理主要包括连续浇铸、连续凝固和连续切割三个方面。
首先,连续浇铸是指在连铸设备上通过连续浇注熔融金属,使金属液不间断地流入结晶器中。
这样可以避免浇注过程中的温度变化和氧化,保证了金属液的纯净度和温度稳定性。
同时,连续浇铸还可以减少浇注过程中的气体夹杂和金属液的氧化,提高了产品的内部质量。
其次,连续凝固是指在结晶器中,熔融金属通过连续往复的凝固过程,逐渐形成固态铸坯。
在这个过程中,结晶器内部的冷却系统不断地将热量带走,使金属液逐渐凝固成固态金属。
通过控制结晶器的温度和冷却速度,可以实现对铸坯组织和性能的精确控制,从而获得更高质量的产品。
最后,连续切割是指在连铸设备的出口处,通过连续的切割装置将凝固成型的铸坯切割成所需长度的产品。
这样可以避免传统浇铸中的冷却等待时间,提高了生产效率。
同时,连续切割还可以减少铸坯表面的氧化和变形,保证了产品的表面质量和尺寸精度。
总的来说,连铸的原理是通过连续浇铸、连续凝固和连续切割,实现了铸坯的一次成型,大大提高了生产效率和产品质量。
这种先进的铸造工艺在现代工业生产中得到了广泛应用,为各种金属制品的生产提供了可靠的技术保障。
连铸技术的基本原理
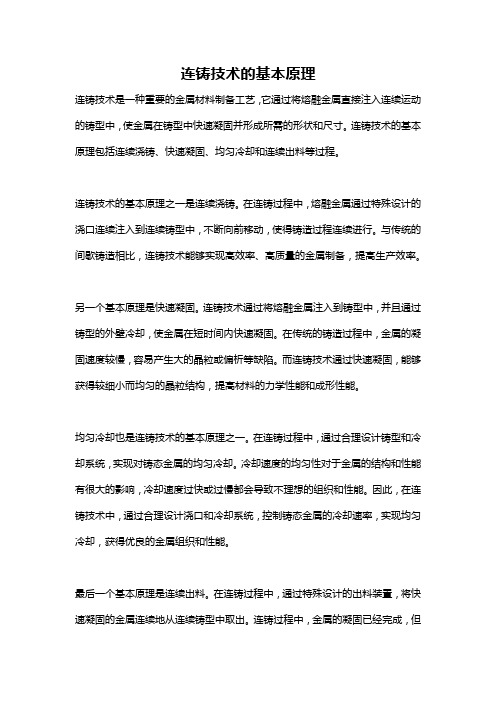
连铸技术的基本原理连铸技术是一种重要的金属材料制备工艺,它通过将熔融金属直接注入连续运动的铸型中,使金属在铸型中快速凝固并形成所需的形状和尺寸。
连铸技术的基本原理包括连续浇铸、快速凝固、均匀冷却和连续出料等过程。
连铸技术的基本原理之一是连续浇铸。
在连铸过程中,熔融金属通过特殊设计的浇口连续注入到连续铸型中,不断向前移动,使得铸造过程连续进行。
与传统的间歇铸造相比,连铸技术能够实现高效率、高质量的金属制备,提高生产效率。
另一个基本原理是快速凝固。
连铸技术通过将熔融金属注入到铸型中,并且通过铸型的外壁冷却,使金属在短时间内快速凝固。
在传统的铸造过程中,金属的凝固速度较慢,容易产生大的晶粒或偏析等缺陷。
而连铸技术通过快速凝固,能够获得较细小而均匀的晶粒结构,提高材料的力学性能和成形性能。
均匀冷却也是连铸技术的基本原理之一。
在连铸过程中,通过合理设计铸型和冷却系统,实现对铸态金属的均匀冷却。
冷却速度的均匀性对于金属的结构和性能有很大的影响,冷却速度过快或过慢都会导致不理想的组织和性能。
因此,在连铸技术中,通过合理设计浇口和冷却系统,控制铸态金属的冷却速率,实现均匀冷却,获得优良的金属组织和性能。
最后一个基本原理是连续出料。
在连铸过程中,通过特殊设计的出料装置,将快速凝固的金属连续地从连续铸型中取出。
连铸过程中,金属的凝固已经完成,但温度较高,通过连续出料并进行后续的热处理,可以获得所需的金属材料。
总的来说,连铸技术的基本原理包括连续浇铸、快速凝固、均匀冷却和连续出料。
这些原理相互作用,使得连铸技术成为一种高效、高质量的金属材料制备方法。
连铸技术的广泛应用,不仅能够提高金属材料的生产效率,提高材料的力学性能和成形性能,还能够减少金属材料的能源消耗和环境污染。
随着现代工业的发展,连铸技术在制造业中的地位和作用将越来越重要,对于推动金属材料制造业的发展具有重要的意义。
连铸技术总结范文

连铸技术总结随着工业的不断发展,连铸技术已经成为了铸造行业中的一项核心技术。
其将液态金属直接浇注到铸模中进行凝固,以实现铸件的快速制造。
连铸技术具有高效率、高精度、高质量等特点,被广泛应用于航空、轨道交通、汽车、管道等领域。
本文将对连铸技术进行分析总结,从连铸设备、浇注过程和生产工艺等方面进行讲解。
一、连铸设备1.连铸机连铸机是连铸生产过程中最重要的设备。
其主要由铸模系统、浇注系统、卸模系统、铸坯传动系统、自动控制系统和液压系统等部分组成。
连铸机的种类较多,包括直接液压连铸机、机械式连铸机、液压机械式连铸机和弯管式连铸机等。
其性能主要取决于流程控制、维护保养和质量监控等方面。
连铸机质量的好坏直接决定了连铸生产线的效率和产品质量的高低。
2.冷却设备冷却设备是连铸过程中至关重要的组成部分。
其作用是使铸坯的温度快速下降并达到所需的机械性能和物理性能。
目前,常用的冷却设备包括带式冷却机、盖式冷却器和水冷却器等。
其中,带式冷却机是目前最常用的冷却设备之一。
其通过铸坯在带式机上的快速传输和喷雾冷却,实现了高效的冷却效果,得到了广泛的应用。
二、浇注过程连铸技术的浇注过程是直接将高温液态金属浇注到铸模中,然后经过一系列的冷却处理后,获得具有一定形状和机械性能的铸造品。
其整个过程包括供料、浇注、冷却和卸模等环节。
其中,浇注环节是最为重要的一环,其直接决定了铸造品的质量和尺寸精度。
在浇注过程中,连铸设备的优劣和流程控制的稳定性对铸造品的性能有着重要的影响。
如果连铸设备的维护保养不当,或者流程控制存在失误,都会导致铸造品的不良品率增高。
三、生产工艺生产工艺是连铸技术的核心之一,它包括铸模设计、长料制备、浇注、冷却和卸模等环节。
铸模设计是铸造品质量的重要保证之一,铸模的设计直接影响了铸造件的表面质量和内部质量。
长料制备对铸造品的机械性能、化学性能和物理性能也有着重要的影响。
在生产过程中,连铸技术还需要定期进行检修和维护保养,如清洗连铸机和冷却系统等,以确保设备的稳定运转。
连铸的名词解释
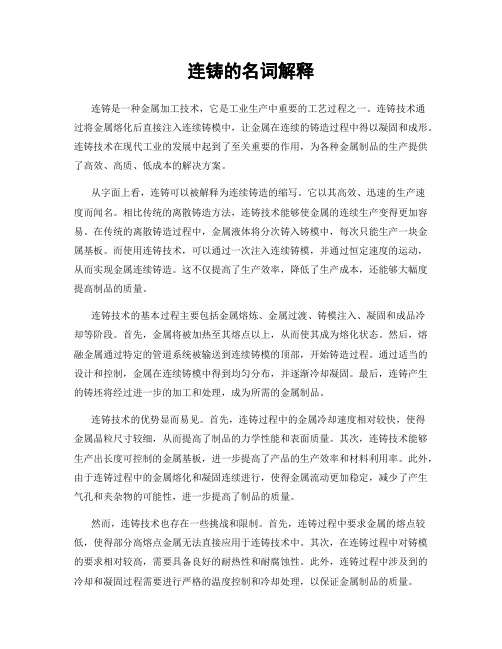
连铸的名词解释连铸是一种金属加工技术,它是工业生产中重要的工艺过程之一。
连铸技术通过将金属熔化后直接注入连续铸模中,让金属在连续的铸造过程中得以凝固和成形。
连铸技术在现代工业的发展中起到了至关重要的作用,为各种金属制品的生产提供了高效、高质、低成本的解决方案。
从字面上看,连铸可以被解释为连续铸造的缩写。
它以其高效、迅速的生产速度而闻名。
相比传统的离散铸造方法,连铸技术能够使金属的连续生产变得更加容易。
在传统的离散铸造过程中,金属液体将分次铸入铸模中,每次只能生产一块金属基板。
而使用连铸技术,可以通过一次注入连续铸模,并通过恒定速度的运动,从而实现金属连续铸造。
这不仅提高了生产效率,降低了生产成本,还能够大幅度提高制品的质量。
连铸技术的基本过程主要包括金属熔炼、金属过渡、铸模注入、凝固和成品冷却等阶段。
首先,金属将被加热至其熔点以上,从而使其成为熔化状态。
然后,熔融金属通过特定的管道系统被输送到连续铸模的顶部,开始铸造过程。
通过适当的设计和控制,金属在连续铸模中得到均匀分布,并逐渐冷却凝固。
最后,连铸产生的铸坯将经过进一步的加工和处理,成为所需的金属制品。
连铸技术的优势显而易见。
首先,连铸过程中的金属冷却速度相对较快,使得金属晶粒尺寸较细,从而提高了制品的力学性能和表面质量。
其次,连铸技术能够生产出长度可控制的金属基板,进一步提高了产品的生产效率和材料利用率。
此外,由于连铸过程中的金属熔化和凝固连续进行,使得金属流动更加稳定,减少了产生气孔和夹杂物的可能性,进一步提高了制品的质量。
然而,连铸技术也存在一些挑战和限制。
首先,连铸过程中要求金属的熔点较低,使得部分高熔点金属无法直接应用于连铸技术中。
其次,在连铸过程中对铸模的要求相对较高,需要具备良好的耐热性和耐腐蚀性。
此外,连铸过程中涉及到的冷却和凝固过程需要进行严格的温度控制和冷却处理,以保证金属制品的质量。
尽管如此,连铸技术在如今的工业生产中扮演了重要的角色。
连铸工艺讲义

1.2.2过热度的ΔT确定
中间包内钢水的过热度ΔT取决于钢种、铸坯断面及浇注条 件等因素。如钢中含碳低,铸坯断面小、过热度应大些;钢中 碳、硅、锰含量高,铸坯断面大,过热度可取低值。浇注条件 主要指钢包及中间包的热工状况,即钢水在钢包及中间包内热 量损失引起的温降。 ΔT=t出钢-Δt过程-tl 式中Δt过程是从出钢到开始浇注的过程温降,其表达式如下: Δt过程=Δt1+Δt2+Δt3+Δt4+Δt5 式中:Δt1--出钢过程中钢水的温降; Δt2--出钢后到钢包处理前钢水的温降; Δt3—钢包处理过程中钢水的温降; Δt4—处理后至钢包开浇前钢水的温降; Δt5—钢水从钢包注入中间包的温降。 钢水过程温降如下图所示:
3、Patience is bitter, but its fruit is sweet. (Jean Jacques Rousseau , French thinker)忍耐是痛苦的,但它的果实是甜蜜的。10:516.17.202110:516.17.202110:5110:51:196.17.202110:516.17.2021
2、Our destiny offers not only the cup of despair, but the chalice of opportunity. (Richard Nixon, American President )命运给予我们的不是失望之酒,而是机会之杯。二〇二一年六月十七日2021年6月17日星期四
⑴开浇期:由于中间包衬吸热,在15~20分种内钢水 温度偏离目标温度下降10~20℃
⑵正常浇注期:当中间包衬的散热损失与补充到中间 包钢水热量损失相等时,钢水温度恢复到目标温度。
⑶换钢包:连浇换钢包期间,中间包钢水温度又有所 降低,第二包钢水开浇后,又恢复正常。
钢铁冶炼中的连铸技术与应用

钢铁冶炼中的连铸技术与应用钢铁工业一直是国民经济中的重要支柱产业,而钢铁冶炼中的连铸技术是钢铁工业中至关重要的一部分。
在传统的钢铁冶炼中,钢锭需要经过多次翻转以达到均匀冷却的目的,这种方法费时费力且效率低下,同时还会有铁锈、气泡等因素影响精度。
在这种情况下,连铸技术应运而生。
什么是连铸技术?连铸技术即是将钢水在一定条件下,连续从注铸机中流出来,快速凝固形成坯料,在过程中进行加热、预混等操作,达到高精度的铸造方法。
这种技术不仅提高了钢铁的生产效率,更大程度上提高了钢铁的品质,为钢铁生产贡献了重要的技术手段。
连铸技术的分类目前,连铸技术主要分为四种。
1. 结晶器成形连铸技术结晶器成形连铸技术是将左右两极交流的工艺,通过结晶器对钢水进行凝固成形,具有无烟无尘和能耗低等优点。
2. 直流慢冷成形连铸技术直流慢冷成形连铸技术是一种新型结晶器技术,通过慢速加热和模拟摆动成形,可以让钢铁加快速冷,减少气泡和夹杂物,从而提高钢铁的质量。
3. 铁包注射成形连铸技术铁包注射成形连铸技术是通过铁包芯来加速钢水流动,减少钢水的接触时间和气体夹杂,确保钢的化学成分合格,提高铸坯质量,尤其是在超薄板材生产中应用较为广泛。
4. 氧化物增强连铸技术氧化物增强连铸技术是在钢铁冶炼中添加不同种类的氧化物,通过钢水的氧化作用来净化钢铁材料,从而提高钢铁的质量和坯料的品质。
连铸技术的应用连铸技术在钢铁工业中的应用十分广泛,相关产品具有以下几个方面的显著特点。
1. 降低了钢铁生产成本传统钢铁冶炼流程中,钢锭需要多次翻转以达到均匀冷却的目的,而在连铸技术的应用下,钢水流动迅速,制造速度提升,将钢锭连续地浇铸成长条状,时间短、效益大,节约了大量的人力资源和成本,使得钢铁生产更能够高效稳定运行。
2. 提高了钢铁质量连铸产品的品质在未来的钢铁工业发展中不可或缺,连铸技术制造出来的钢锭具有低碳低硫等优点,热性能稳定,甚至可以生产出高质量的薄板料,无论是经济利益还是技术趋势,都对钢铁市场产生了深远的影响和推动。
- 1、下载文档前请自行甄别文档内容的完整性,平台不提供额外的编辑、内容补充、找答案等附加服务。
- 2、"仅部分预览"的文档,不可在线预览部分如存在完整性等问题,可反馈申请退款(可完整预览的文档不适用该条件!)。
- 3、如文档侵犯您的权益,请联系客服反馈,我们会尽快为您处理(人工客服工作时间:9:00-18:30)。
引锭杆存放区域
输送辊道区域
输送辊道区域
出坯区域
连铸机出坯区域: 移钢机将冷床辊道上的铸坯移至液压推钢冷床。
移钢机 用途:
移钢机将冷床区辊道上的方坯移至步进翻转冷床上,或将矩形坯移至推钢机 上。
性能: 推头可摆动升降,推钢 主要参数: 横移速度:20 m/min 移钢数量: 160x160mm-9m 5根 150x150mm-9m 5根 传动电机: 功率 22 Kw /台x 2台 推头升降行程: 380 mm
• 纵向走行速度: 2-20m/min
• 纵向走行驱动电机: 7.5Kw 2个/台
• 升降行程:
400 mm
• 升降速度:
1.5 m /min
• 横向调节行程:
100 mm
结晶器振动装置及铸坯 一次及二次冷却区域
结晶器振动装置
结晶器振动装置 • 振动形式:四连杆半板簧机构
• 振动曲线:正弦
主要参数 驱动装置: 电机减速机 振幅: 0~±6mm 振动频率范围:30~300 c/min
主要技术特点及承诺:
1,充分发挥在工厂设计方面的技术实 力,综合考虑连铸机在车间内的合理布 置。
2,综合考虑车间内连铸机的电缆沟、 管廊及旋流井等设施的工艺布置,使之 更为合理,顺畅。
3,统一提出连铸机的各专业工厂设计 资料,达到统一技术管理的目的。
炼钢、连铸工艺参数
•转炉数量: •转炉公称容量: •最大出钢量: •转炉冶炼周期: •连铸机数量: •连铸坯断面:
形式:整体框架 特点: 快速吊装定位
主要参数:
辊径
Ф170 mm材料: 35CrMo
辊子轴承 连铸扇形段专用轴承
轴承间隙 采用C4系列
辊子润滑 油气润滑
二冷喷嘴 气水喷嘴
3#连铸机扇形三段
主要参数: 辊径 辊子数量 辊子结构 辊子材料 辊子轴承 轴承间隙 辊子润滑
液压推钢冷床
用途:
双向移钢机将冷床区辊道上的铸坯3根一组移至液压推钢冷床后,冷床由液 压移钢机将铸坯3根一组移至冷床端头,由吊钩吊运至地面储存。 主要参数:
铸坯长度:3000-6000mm; 铸坯断面: 165x225-500mm 冷床所承受负荷:80t 推钢机推头移动距离:1970mm
方坯收集台架 用途: 接受步进翻转冷床移送来的铸坯,以备吊装。 设备组成及结构特征: 主要参数: 铸坯长度: 12m; 铸坯断面:150x150mm, 120x120mm 承受负荷:45t 拨钢行程:1270mm 液压缸:C25WE125/90-700MIIB 2个
•连铸机弧形半径: •连铸机流间距: •连铸机流数:
1座 80t 85t 36 min/炉 1台 150x150 mm 160x160 mm
R9 m 1250mm 5流
产品品种及代表钢号
普碳钢 低合金钢
弹簧钢
带肋钢筋用钢
Q195,Q215,Q235
30MnSi
60Si2Mn 20MnSi、20Mn 20MnSi(V、Nb) 20Mn(Ti)
谢谢!
开口度: 110—300mm
驱动电机: YTAFE160M-6 7.5Kw 共3个/流
减速机: LTRY280-300 速比:300
液压缸: C25WE125/90-220
4个
切前辊道及切割辊道区域
切割前辊道(含夹送辊装置)和切割辊道
设备组成及结构特征:由自由辊装配、驱动辊装配、夹送辊装置、摆动辊装置、
1、2号连铸机冷却区
3#铸机一次二次冷却区
3#连铸机扇形一段
形式:整体框架 特点: 快速吊装定位
主要参数:
辊径
Ф170 mm
辊子数量 内外弧各11个
辊子结构 整体辊
辊子材料 辊子轴承 轴承间隙
35CrMo 连铸扇形段专用轴承 采用C4系列
辊子润滑 油气润滑 二冷喷嘴 气水喷嘴
3#连铸机扇形二段
• 钢包加盖回转: • 钢包加盖升降行程: • 钢包定位:
正常:1 r/min 事故:0.5 r/min 正常:无限; 事故:180度 0.65 r/min 200mm 液压锁紧块
• 升降: • 横移: • 走行:
液压缸 液压缸 电机减速机
中包车性能参数
• 承载能力:
80t
• 纵向走行距离: 16m
Ф250 mm 外弧5个 整体辊。通水冷却。
35CrMo 双列球面滚子轴承 采用C4系列 油气润滑
拉矫机及辊道
拉矫机 电机,框架,轴承座, 辊身均水冷
脱引锭头装置 用途:将铸坯和引锭头脱开 性能:液压驱动
功能: 拉铸坯、送引锭杆
矫直方式: 连续矫直。
主要参数:
拉速范围: 0.3—4.0m/min
连铸机性能及配置
• 采用升降大包回转台,并装有连续称量装置,有利于快速更换钢包, 提高连浇率及收得率;
• 采用全封闭浇注,防止钢水二次氧化; • 采用大容量中间包,使中间包内大颗粒夹杂物有时间上浮,并使钢流
合理流动; • 中包车具备行走、升降、横移微调及连续称重功能; • 结晶器冷却水设置事故状态的供水管路; • 采用高频率、小振幅机械振动装置产生正弦振动,以减少铸坯粘结; • 气雾二冷方式,防止裂纹、鼓肚、角裂等缺陷的产生; • 采用整体可更换式二冷段,方便检修维护; • 采用连续矫直技术,防止铸坯矫直变形时内裂的产生; • 采用基础级计算机控制,装备水平满足要求,节省投资,可实现生产
顺序控制、定尺切割、画面显示、报表打印等功能; • 结晶器液面采用塞棒自动控制;
二、 5机5流小方 坯连铸机
二、 连铸机主要 设备介绍
浇注平台以上设备
承载能力:160t (单臂) 回转半径:R4500 mm 功能:回转、加盖、称量、
事故回转
大包转台性能参数 • 回转速度:
• 回转角度:
第一部分 连铸方案介绍
投标技术文件组成:
1,连铸车间工艺系统设计总说明 2, 5机5流小方坯连铸机
一、连铸车间工艺 布置及总体说明
连铸车间厂房布置
钢水接受跨: 连铸跨: 出坯跨1: 出坯跨2:
24 m 轨面标高: 23 m 27 m 轨面标高: 23 m 21m 轨面标高: 18 m 33 m 轨面标高: 12 m