先进热加工工艺模拟技术创新研究
B93铝合金热加工特性模拟研究

般需 要 经过 高温 塑 性 加 工 成 型 。因此 , 对铝 合 金 近年 来 , 合 金 热 加 工 特 性 的 研 究 进 展 顺 铝
热加 工特 性 的研 究具 有重 要 的工程 意义 。
1 实 验 方 法
实 验 材料 为 B 3铝合 金 , 主要 合 金 成 分 ( 9 其 质
一
Ⅲl
J
。
跟 同一 系列 的 A— nMgc l . — u合 金相 比 , 9 z B3
化生 产需要 , 研究 热 加工 过 程 中 B 3铝合 金 变 形 温 9 度 , 形速率 对 组织 的影 响尤 为 重要 ¨ ’ 。本 工 作 变 J
铝 合金 未 添 加 Mn C 等 元 素 , 金 的铸 造 性 能 更 ,r 合 好 , 纹倾 向较小 , 裂 因此 , 别 适 用 于 制作 大型 锻 件 特 等 加 工 制 品 , 一 种 性 能 优 良 的 高 强 锻 造 铝 合 是
第3 2卷 第 2期
21 0 2年 4月
航
空
材
料
学பைடு நூலகம்
报
V0. 2.N . 13 o2 Ap i 2 1 r 0 2 l
J URN RON O AL OF AE AUT C T I S I AL MA ER AL
B 3铝 合 金 热 加 工 特 性 模 拟 研 究 9
1 m 的 圆柱 , Ge be1 0 5m 在 le l 5 0热 模 拟 试 验 机 上 进
行 圆柱 单 向热 压 缩 。实 验 中在 试 样 两 端 涂 上 高 温
石 墨 润滑 剂 ( 5 石 墨 +2 % 4 # 油 +5 硝 酸 7% 0 6机 %
的应用 , 有人 对不 同系 列 的铝 合 金 热 加工 进 行 了模 拟, 建立 了不 同的本构 方程 用于指 导实 际过程 , 有 也
1.5MW风机叶片模具加热工艺研究与技术创新
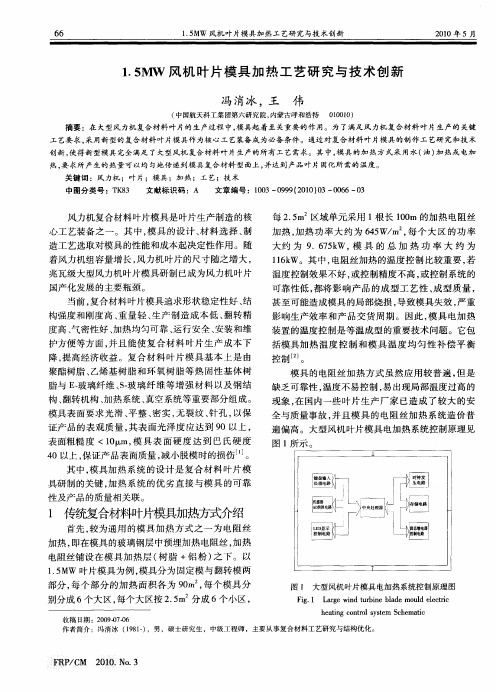
构、 翻转 机构 、 加热 系统 、 真空 系统 等重要 部分 组成 。
模 具表 面 要求 光 滑 、 整 、 平 密实 , 裂 纹 、 孔 , 无 针 以保 证 产 品 的表 观质 量 , 表 面光 泽度 应 达 到 9 其 0以上 , 表 面粗糙 度 <1 m, 具 表 面 硬 度 达 到 巴 氏硬 度 0 模
图 1 大型风机叶片模具 电加热系统控制原理 图
F g 1 L r e w n u b n ld u d ee t c i . a g i d t r i e ba e mo l lcr i h ai g c n rls se S h mai e t o to y t m c e t n c
风 力机 复合材料 叶 片模 具是 叶 片生产制 造 的核
每 2 5 区域单 元采 用 1根长 lO 的加 热 电 阻丝 .m Om 加热 , 加热 功 率 大 约 为 6 5 m , 4 W/ 每个 大 区 的 功 率
大 约 为 9 6 5 W , 具 的 总 加 热 功 率 大 约 为 . 7k 模
缺 乏可靠 性 , 温度不 易控 制 , 出现局 部 温度过 高 的 易 现 象 , 国 内一些 叶 片 生产 厂 家 已造成 了较 大 的安 在
全 与质量 事故 , 且模 具 的 电阻 丝加 热 系 统 造价 普 并 遍偏 高 。大 型风机 叶片模 具 电加热 系统控 制原 理见
图 1所示 。
收稿 日期 :2 0 -70 0 90 -6 作 者 简 介 :冯 消 冰 ( 9 1) 18 一 ,男 ,硕 士研 究 生 , 中级工程师 ,主要从事 复合材料工艺研究与结构优化 。
F / M 2 1 : . RP C 0 0 No 3
21 0 0年 第 3期
热传导和热工应用的创新

热传导和热工应用的创新热传导和热工应用的创新一直是研究领域的热点问题。
随着科技的不断发展和人们对能源利用效率的要求提高,寻找新的热传导方式以及改进热工应用的方法变得尤为重要。
本文将从热学原理、应用实践、创新技术和未来展望四个方面探讨热传导和热工应用的创新。
一、热学原理热学原理是研究热传导和热工应用的基础,通过对热学原理的理解和应用,可以实现热传导和热工应用的创新。
热传导是物体内部或者不同物体之间热量传递的过程,传导方式主要分为导热、对流和辐射。
目前,传统的导热技术在许多领域已经被广泛应用,但是其传热效率较低且受限于物质的导热性能。
因此,热学原理的创新成为研究的重点。
二、应用实践在实际应用中,热传导和热工应用的创新取得了一些重要成果。
例如,在建筑领域,采用新型的隔热材料和节能技术可以有效提高建筑物的热传导效率,减少能源的浪费。
在冶金领域,采用先进的非接触式温度测量技术可以实现对高温熔炼过程中物质的精确控制。
在电子领域,采用热管技术可以解决芯片散热难题,提高电子设备的性能和可靠性。
这些应用实践的创新不仅提高了热传导效率,还节约了能源资源。
三、创新技术为了进一步推动热传导和热工应用的创新,科学家们不断开发新的技术。
例如,基于纳米材料的热传导技术已经成为热传导领域的研究热点。
纳米材料具有较高的热传导率和特殊的热学性质,可以用于制作高效的隔热材料、热电材料等。
另外,热泵技术也是热传导和热工应用创新的重要技术之一。
热泵技术可以实现热能的转换和逆转,广泛应用于供暖、制冷和工业热能回收等领域。
四、未来展望随着科技的不断进步,热传导和热工应用的创新将在未来展现更广阔的前景。
首先,纳米材料的研究将会取得更大突破,这将为热传导和热工应用提供更多的可能性。
其次,新型的热泵技术将更加智能化和节能化,实现能源的可持续利用。
此外,基于人工智能的热工应用方向也将得到发展,通过智能控制和优化算法,实现热能的高效利用。
总结起来,热传导和热工应用的创新是当前科研领域的热点问题。
(工艺技术)材料热加工工艺的现状以及发展
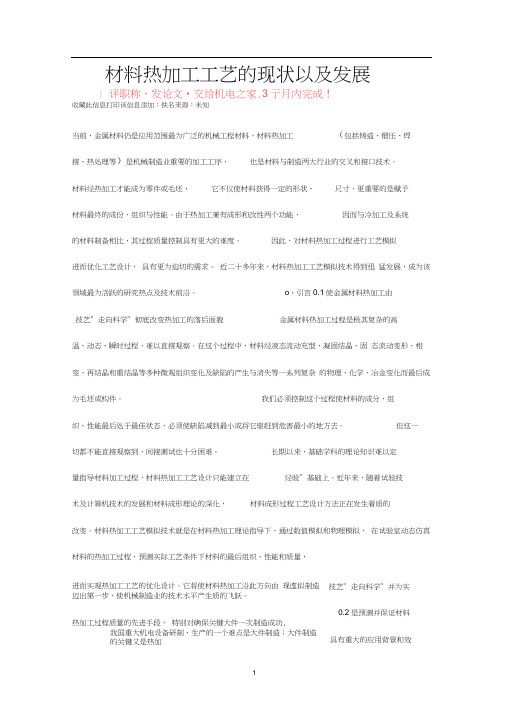
材料热加工工艺的现状以及发展| 评职称,发论文•交给机电之家.3亍月内完成!收藏此信息打印该信息添加:佚名来源:未知当前,金属材料仍是应用范围最为广泛的机械工程材料,材料热加工(包括铸造、锻压、焊接、热处理等)是机械制造业重要的加工工序,也是材料与制造两大行业的交叉和接口技术。
材料经热加工才能成为零件或毛坯,它不仅使材料获得一定的形状、尺寸,更重要的是赋予材料最终的成份、组织与性能。
由于热加工兼有成形和改性两个功能,因而与冷加工及系统的材料制备相比,其过程质量控制具有更大的难度。
因此,对材料热加工过程进行工艺模拟进而优化工艺设计,具有更为迫切的需求。
近二十多年来,材料热加工工艺模拟技术得到迅猛发展,成为该领域最为活跃的研究热点及技术前沿。
o、引言0.1使金属材料热加工由技艺”走向科学”彻底改变热加工的落后面貌金属材料热加工过程是极其复杂的高温、动态、瞬时过程,难以直接观察。
在这个过程中,材料经液态流动充型、凝固结晶、固态流动变形、相变、再结晶和重结晶等多种微观组织变化及缺陷的产生与消失等一系列复杂的物理、化学、冶金变化而最后成为毛坯或构件。
我们必须控制这个过程使材料的成分、组织、性能最后处于最佳状态,必须使缺陷减到最小或将它驱赶到危害最小的地方去。
但这一切都不能直接观察到,间接测试也十分困难。
长期以来,基础学科的理论知识难以定量指导材料加工过程,材料热加工工艺设计只能建立在经验”基础上。
近年来,随着试验技术及计算机技术的发展和材料成形理论的深化,材料成形过程工艺设计方法正在发生着质的改变。
材料热加工工艺模拟技术就是在材料热加工理论指导下,通过数值模拟和物理模拟,在试验室动态仿真材料的热加工过程,预测实际工艺条件下材料的最后组织、性能和质量,进而实现热加工工艺的优化设计。
它将使材料热加工沿此方向由现虚拟制造迈出第一步,使机械制造业的技术水平产生质的飞跃。
热加工过程质量的先进手段,特别对确保关键大件一次制造成功,我国重大机电设备研制、生产的一个难点是大件制造;大件制造的关键又是热加技艺”走向科学”并为实0.2是预测并保证材料具有重大的应用背景和效工。
国内外热作模具钢的研究进展

国内外热作模具钢的研究进展热作模具钢是一种用于制造热作模具的钢材,主要用于高温成型、锻造和压铸等工艺。
由于热作模具在工作过程中需要承受高温、高压和高摩擦力的作用,因此对热作模具钢的性能要求较高。
本文将综述近年来国内外热作模具钢的研究进展,以期为相关领域的研究提供参考。
在国外,热作模具钢的研究主要集中在生产工艺、材料制备和性能评估方面。
近年来,随着计算机技术和材料科学的不断发展,国外研究者利用模拟仿真技术对热作模具钢的生产和制备过程进行优化,取得了显著的成果。
在生产工艺方面,研究者通过调整冶炼、浇注和热处理等工艺参数,改善热作模具钢的内部组织和力学性能。
例如,采用真空熔炼技术制备的高纯净度热作模具钢,能够有效提高模具的韧性和耐磨性能。
通过应用快速冷却技术,可以获得具有细小晶粒组织和超高热强性的热作模具钢。
在材料制备方面,研究者致力于开发新型热作模具钢及其复合材料。
例如,日本住友金属公司研制的新型热作模具钢SUMITUBE,具有优良的抗高温氧化性能和较低的模温,有利于延长模具的使用寿命。
美国钢铁公司开发的具有高韧性、高耐磨性的热作模具钢H13A,也在航空、汽车等领域得到了广泛应用。
在性能评估方面,研究者主要材料的力学性能、抗疲劳性能和抗断裂性能等方面的研究。
通过开展系统的实验测试和数据分析,研究者建立了材料的本构模型和失效准则,为热作模具的设计和优化提供了重要依据。
研究者还利用有限元分析(FEA)等方法,对模具的应力分布、温度场和磨损行为等进行模拟分析,为改进模具设计和优化生产工艺提供了有效手段。
国内的热作模具钢研究主要集中在钢铁研究总院、北京科技大学、上海交通大学、华南理工大学等高校和科研机构。
研究领域涵盖了材料制备、性能评估和改性处理等方面,取得了一系列重要成果。
在材料制备方面,国内研究者通过引进先进的冶炼、浇注和热处理设备,不断优化生产工艺,成功开发出多个新型热作模具钢。
例如,北京科技大学研发的GT35新型热作模具钢,具有良好的高温强度、韧性和抗疲劳性能,已广泛应用于锻造、压铸等领域。
《一种Q-P-T热处理的新工艺研究》范文

《一种Q-P-T热处理的新工艺研究》篇一一种Q-P-T热处理新工艺研究一、引言随着现代工业技术的快速发展,金属材料的性能要求日益提高。
热处理技术作为提高金属材料性能的重要手段,其新工艺的研究与应用显得尤为重要。
Q-P-T热处理工艺作为一种新型的热处理技术,其独特性和优越性在金属材料性能提升方面表现出显著的效果。
本文旨在研究一种Q-P-T热处理新工艺,探讨其原理、应用及优势,为金属材料性能的提升提供新的思路和方法。
二、Q-P-T热处理新工艺的原理Q-P-T热处理新工艺是一种结合了淬火(Quenching)、分时(Partitioning)和回火(Tempering)三个步骤的热处理工艺。
该工艺的原理是在保持金属材料组织稳定性的基础上,通过调整淬火温度、保温时间以及回火温度等参数,使金属材料在保持良好塑性的同时,提高其强度和硬度。
三、Q-P-T热处理新工艺的步骤1. 淬火(Quenching):将金属材料加热至一定温度,保持一段时间后迅速冷却,使金属材料获得一定的奥氏体组织。
2. 分时(Partitioning):在保持淬火后金属材料的组织稳定性的基础上,通过调整保温时间和温度,使碳、合金元素在奥氏体中进行充分的扩散和分配。
3. 回火(Tempering):将经过分时处理的金属材料进行回火处理,使金属材料在保持高强度的同时,提高其塑性和韧性。
四、Q-P-T热处理新工艺的应用Q-P-T热处理新工艺广泛应用于汽车、航空、军工等领域。
在汽车制造中,采用Q-P-T热处理工艺可以提高汽车零部件的强度和耐磨性,降低重量,提高燃油效率。
在航空领域,该工艺可以提高飞机零部件的抗疲劳性能和耐腐蚀性能,保证飞行安全。
在军工领域,该工艺可以提高武器装备的战斗性能和可靠性。
五、Q-P-T热处理新工艺的优势1. 提高金属材料的综合性能:Q-P-T热处理新工艺可以在保持金属材料良好塑性的同时,提高其强度和硬度,使金属材料具有更好的综合性能。
材料热加工工艺模拟的研究现状及技术发展趋势
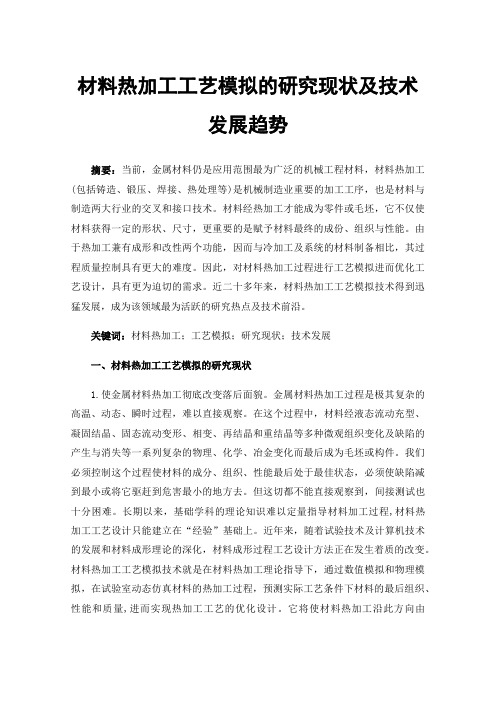
材料热加工工艺模拟的研究现状及技术发展趋势摘要:当前,金属材料仍是应用范围最为广泛的机械工程材料,材料热加工(包括铸造、锻压、焊接、热处理等)是机械制造业重要的加工工序,也是材料与制造两大行业的交叉和接口技术。
材料经热加工才能成为零件或毛坯,它不仅使材料获得一定的形状、尺寸,更重要的是赋予材料最终的成份、组织与性能。
由于热加工兼有成形和改性两个功能,因而与冷加工及系统的材料制备相比,其过程质量控制具有更大的难度。
因此,对材料热加工过程进行工艺模拟进而优化工艺设计,具有更为迫切的需求。
近二十多年来,材料热加工工艺模拟技术得到迅猛发展,成为该领域最为活跃的研究热点及技术前沿。
关键词:材料热加工;工艺模拟;研究现状;技术发展一、材料热加工工艺模拟的研究现状1.使金属材料热加工彻底改变落后面貌。
金属材料热加工过程是极其复杂的高温、动态、瞬时过程,难以直接观察。
在这个过程中,材料经液态流动充型、凝固结晶、固态流动变形、相变、再结晶和重结晶等多种微观组织变化及缺陷的产生与消失等一系列复杂的物理、化学、冶金变化而最后成为毛坯或构件。
我们必须控制这个过程使材料的成分、组织、性能最后处于最佳状态,必须使缺陷减到最小或将它驱赶到危害最小的地方去。
但这切都不能直接观察到,间接测试也十分困难。
长期以来,基础学科的理论知识难以定量指导材料加工过程,材料热加工工艺设计只能建立在“经验”基础上。
近年来,随着试验技术及计算机技术的发展和材料成形理论的深化,材料成形过程工艺设计方法正在发生着质的改变。
材料热加工工艺模拟技术就是在材料热加工理论指导下,通过数值模拟和物理模拟,在试验室动态仿真材料的热加工过程,预测实际工艺条件下材料的最后组织、性能和质量,进而实现热加工工艺的优化设计。
它将使材料热加工沿此方向由“技艺”走向“科学”,并为实现虚拟制造迈出第一步,使机械制造业的技术水平产生质的飞跃。
2.是预测并保证材料热加工过程质量的先进手段,具有重大的应用背景和效益。
国内外热加工工艺模拟技术的现状与发展趋势1
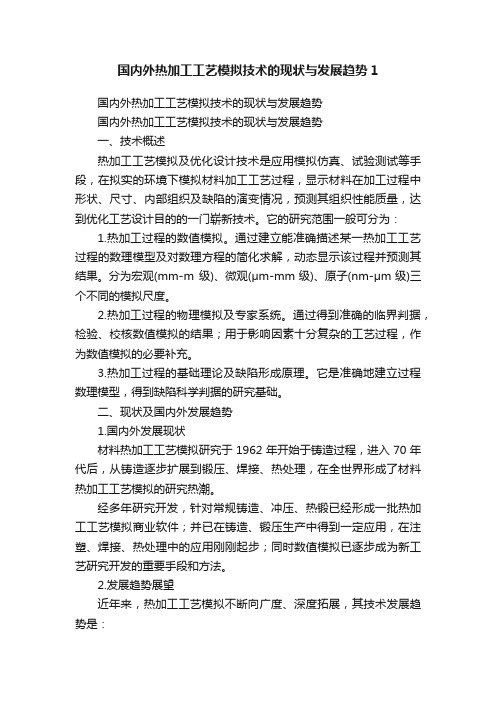
国内外热加工工艺模拟技术的现状与发展趋势1国内外热加工工艺模拟技术的现状与发展趋势国内外热加工工艺模拟技术的现状与发展趋势一、技术概述热加工工艺模拟及优化设计技术是应用模拟仿真、试验测试等手段,在拟实的环境下模拟材料加工工艺过程,显示材料在加工过程中形状、尺寸、内部组织及缺陷的演变情况,预测其组织性能质量,达到优化工艺设计目的的一门崭新技术。
它的研究范围一般可分为:1.热加工过程的数值模拟。
通过建立能准确描述某一热加工工艺过程的数理模型及对数理方程的简化求解,动态显示该过程并预测其结果。
分为宏观(mm-m 级)、微观(μm-mm级)、原子(nm-μm级)三个不同的模拟尺度。
2.热加工过程的物理模拟及专家系统。
通过得到准确的临界判据,检验、校核数值模拟的结果;用于影响因素十分复杂的工艺过程,作为数值模拟的必要补充。
3.热加工过程的基础理论及缺陷形成原理。
它是准确地建立过程数理模型,得到缺陷科学判据的研究基础。
二、现状及国内外发展趋势1.国内外发展现状材料热加工工艺模拟研究于1962年开始于铸造过程,进入70年代后,从铸造逐步扩展到锻压、焊接、热处理,在全世界形成了材料热加工工艺模拟的研究热潮。
经多年研究开发,针对常规铸造、冲压、热锻已经形成一批热加工工艺模拟商业软件;并已在铸造、锻压生产中得到一定应用,在注塑、焊接、热处理中的应用刚刚起步;同时数值模拟已逐步成为新工艺研究开发的重要手段和方法。
2.发展趋势展望近年来,热加工工艺模拟不断向广度、深度拓展,其技术发展趋势是:(1)宏观-中观-微观已普遍由建立在温度场、速度场、变形场基础上的旨在预测形状、尺寸,轮廓的宏观尺度模拟(mm-m级)进入到以预测组织、结构、性能为目的的中观尺度模拟(毫米量级)及微观尺度模拟(微米量级)阶段。
(2)单-分散-耦合集成模拟功能已由单一的物理场模拟普遍进入到多种物理场相互耦合集成的阶段,以真实模拟复杂的热加工过程。
(3)共性、通用-专用、特性由于普通铸造、冲压、锻造工艺模拟的日益成熟及商业软件的出现,研究工作的重点和前沿已由共性通用问题转向难度更大的专用特性问题。
- 1、下载文档前请自行甄别文档内容的完整性,平台不提供额外的编辑、内容补充、找答案等附加服务。
- 2、"仅部分预览"的文档,不可在线预览部分如存在完整性等问题,可反馈申请退款(可完整预览的文档不适用该条件!)。
- 3、如文档侵犯您的权益,请联系客服反馈,我们会尽快为您处理(人工客服工作时间:9:00-18:30)。
先进热加工工艺模拟技术创新研究
清华大学制造科学工程学院
一、技术概述
热加工工艺模拟及优化设计技术是应用模拟仿真、试验测试等手段,在拟实的环境下模拟材料加工工艺过程,显示材料在加工过程中形状、尺寸、内部组织及缺陷的演变情况,预测其组织性能质量,达到优化工艺设计目的的一门崭新技术。
它的研究范围一般可分为:
1.热加工过程的数值模拟。
通过建立能准确描述某一热加工工艺过程的数理模型及对数理方程的简化求解,动态显示该过程并预测其结果。
分为宏观(mm-m级)、微观(µm-mm 级)、原子(nm-µm级)三个不同的模拟尺度。
2.热加工过程的物理模拟及专家系统。
通过得到准确的临界判据,检验、校核数值模拟的结果;用于影响因素十分复杂的工艺过程,作为数值模拟的必要补充。
3.热加工过程的基础理论及缺陷形成原理。
它是准确地建立过程数理模型,得到缺陷科学判据的研究基础。
二、现状及国内外发展趋势
1.国内外发展现状
材料热加工工艺模拟研究于1962年开始于铸造过程,进入70年代后,从铸造逐步扩展到锻压、焊接、热处理,在全世界形成了材料热加工工艺模拟的研究热潮。
经多年研究开发,针对常规铸造、冲压、热锻已经形成一批热加工工艺模拟商业软件;并已在铸造、锻压生产中得到一定应用,在注塑、焊接、热处理中的应用刚刚起步;同时数值模拟已逐步成为新工艺研究开发的重要手段和方法。
2.发展趋势展望
近年来,热加工工艺模拟不断向广度、深度拓展,其技术发展趋势是:
(1)宏观-中观-微观
已普遍由建立在温度场、速度场、变形场基础上的旨在预测形状、尺寸,轮廓的宏观尺度模拟(mm-m级)进入到以预测组织、结构、性能为目的的中观尺度模拟(毫米量级)及微观尺度模拟(微米量级)阶段。
(2)单-分散-耦合集成
模拟功能已由单一的物理场模拟普遍进入到多种物理场相互耦合集成的阶段,以真实模拟复杂的热加工过程。
(3)共性、通用-专用、特性
由于普通铸造、冲压、锻造工艺模拟的日益成熟及商业软件的出现,研究工作的重点和前沿已由共性通用问题转向难度更大的专用特性问题。
主要方向一是解决特种热加工工艺(如压铸、金属型铸造、楔横轧等)模拟及工艺优化问题;二是解决加工件的缺陷(混晶、回弹、热裂、冷裂、变形等)消除问题。
(4)重视提高数值模拟精度和速度的基础性研究
主要有:热加工基础理论、缺陷形成机理及判据、新的数理模型、新的算法、前后处理等基础性研究及物理模拟与精确测试技术等。
(5)重视集成技术,使工艺模拟成为先进制造系统的重要组成部分。
包括:在并行环境下,与产品、模具CAD/CAE/CAM系统集成,与零件加工制造系统集成,与零件的安全可靠性能实现集成。
3.我国的优势及不足
我国于70年代末期开始研究铸造工艺模拟,以后逐步扩展至锻造、冲压、焊接、热处理及注塑等各专业,吸引了一大批优秀的科技人员投身该领域研究。
在多年研究的基础上,国内多家研究院所及高校联合投标,于1997年“金属材料热成形过程的动态模拟及组织性能质量的优化控制”入选国家攀登B项目,为攀登国际前沿提供了很好的条件。
我国在铸造微观组织模拟,大锻件混晶预测,焊接工艺性的物理模拟及精确测试等方面的研究居世界先进水平。
但在模拟软件的商品化开发,研究工作的硬、软件环境等方面有较大的差距。
三、“十五”目标及主要研究内容
1.目标
针对金属材料铸造、锻压、焊接、热处理及非金属材料注塑等热加工过程,以材料热加工理论分析为基础,通过数值模拟和物理模拟研究,开发一系列商品化软件及实验技术,能对热加工过程的组织、性能、质量进行预测和优化控制,实现工艺优化设计,并在材料热加工基础理论及缺陷形成机理的某些方面有所发展和创新,并行工程环境下的虚拟制造成形的基础性研究取得进展。
通过本项研究,使该研究领域全面赶上当代国际水平,在某些方面达到国际领先水平。
2.主要研究内容
(1)金属材料热加工过程的基础理论及缺陷形成原理的研究
研究材料热加工过程中的液态流动充型、凝固结晶、固态流动变形、相变、再结晶与重结晶等一系列复杂的物理、化学、冶金变化原理及数理模型;揭示充型过程的卷气、夹渣、冷隔,凝固结晶过程的缩松、热裂、偏析,固态流动变形过程的孔洞、裂纹、混晶、皱折、回弹,焊接过程的凝固裂纹、氢致裂纹,固态相变过程的畸变、裂纹等缺陷的形成原理,得出临界判据。
(2)金属材料热加工的宏观数值模拟、工艺优化及商品化软件技术
完成金属材料主要热加工方法(铸造、锻造、冲压、焊接、热处理)的宏观模拟及工艺优化的研究开发,解决大铸件、大锻件、大型焊接结构件及一些特种毛坯件(压铸、电渣熔铸、金属型铸造、楔横轧等)的工艺优化问题,提出消除其宏观缺陷的方法,并推出具有我国自主版权的热加工工艺模拟商品化软件。
(3)金属材料热加工的微观数值模拟及组织性能质量的观测
通过研究微观组织模拟的理论及模型算法,塑性成形晶粒度演化,焊接过程氢扩散与集聚,高温区熔池尾部应力应变,加热冷却过程应力一组织转变的定量关系等微观数值模拟技术,完成微米量级(µm)的热加工微观数值模拟的研究工作,解决热加工常见的微观缺陷(偏析、气孔、混晶、氢致裂纹等)问题,并初步推出部分商品化软件。
纳米量级的模拟工作开始起步。
(4)金属材料热加工工艺性的物理模拟和精确评价技术
配合数值模拟,研究并掌握凝固结晶过程直观的观测方法,材料焊接熔池尾部高温应力应变及凝固裂纹形成阻力测试技术,焊接过程局部区域氢浓度的测试方法,相变塑性及应力诱发相变的实验验证方法等相关的物理模拟及工艺性的精确测试、评价技术,能为宏观及微观数值模拟提供精确、适用的基础数据,基本判据和合宜的校核、检验方法。
(5)并行环境下热加工工艺模拟与其它技术环节集成技术
完成并行环境下,铸造、锻压两个专业的工艺模拟、优化与零件CAD/CAM的集成,推出商品化的CAD/CAE/CAM一体化系统软件;完成冲压工艺模拟与冲压生产系统的集成研究并用于生产;工艺模拟与零件性能及安全可靠性的集成研究开始启动,并获得初步结果。