模具表面精加工
冲压模具精加工分析
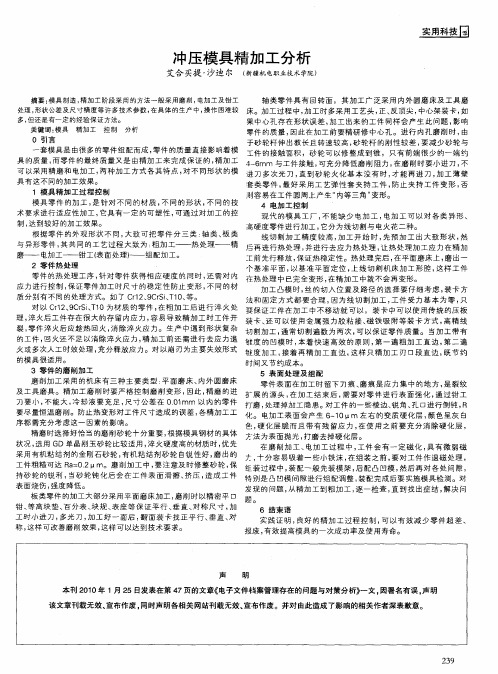
艾合 买提 ・ 沙迪 尔 ( 机电 新疆 职业技术学院)
摘要 : 具制造 , 加工阶段采 用的方法一般 采用磨 削, 模 精 电加工及钳 工
轴 类零件具 有回转面 ,其加工 广泛采用 内外圆磨 床及工 具磨
零件 的质 量 , 因此在加工 前要精研修 中, 。进行 内孔磨削 时 , C qL 由 0 引言 于砂 轮杆 伸 出教 长 且 转 速 较 高 , 轮 杆 的 刚 性 较 差 , 减 少 砂 轮 与 砂 要 套模 具是 由很多的零件组配而成 , 零件 的质量直接影 响着模 工件 的 接 触 面 积 ,砂 轮 可 以修 整 成 到 锥 ,只 有 前 端 很 少 的 一 端 约 具 的质量 , 而零件 的最终质量又 是由精加工来 完成保 证的 , 精加 工 4 6 — mm 与 工 件 接 触 , 充 分 降 低 磨 削 阻 力 , 磨 削 时 要 小 进 刀 , 可 在 不 可 以采用精 磨和电加工 , 两种加 工方式各其 特点 , 对不 同形状 的模 趁刀 多 次 光 刀 , 到 砂 轮 火 化 基 本 没 有 时 , 能 再 进 刀 , 工 薄 壁 直 才 加 具 有 这 不 同 的加 工 效 果 。 套类 零 件 , 好 采 用 工 艺 弹 性 套 夹 持 工 件 , 止 夹 持 工 件 变 形 , 最 过 程 控 制 则 容 易在 工 件 圆 周 上 产 生 “ 等 三 角 ” 形 。 内 变 模 具 零 件 的 加 工 , 针 对 不 同 的 材 质 , 同 的 形 状 , 同 的 技 是 不 不 4 电加 工 控 制 术 要 求 进 行 适 应 性 / T , 具 有 一 定 的 可 塑 性 , 通 过 对 加 工 的 控 ] a 它 可 现 代 的 模 具 工 厂 , 能 缺 少 电加 工 , 加 工 可 以对 各 类 异 形 、 不 电 制 , 到较 好 的加 工效 果 。 达 高 硬 度 零 件 进 行 ; 3 , 分 为 线切 割 与 电火 花 二 种 。 b :它 u 根 据 零 件 的 外 观 形 状 不 同 , 致 可 把 零 件 分 三 类 : 类 、 类 大 轴 板 线切割 加工精 度较 高 , 工 开始 时 , 预 加 工出大 致形状 , 加 先 然 与 异 形 零 件 , 共 同 的 工 艺 过 程 大 致 为 : 加 工— — 热 处 理 —— 精 后 再 进 行 热 处 理 , 进 行 去应 力 热 处理 , 热 处 理 加 工 应 力在 精 加 其 粗 并 让 磨 — — 电加 工— — 钳 工( 面 处理 ) — 组 配 加 工 。 表 — : 前 先 行 释 放 , 证 热 稳 定 性 。 热 处 理 完 后 , 平 面 磨 床 上 , 出 一 [ 保 在 磨 2 零 件 热 处 理 个基准 平面 , 以基准 平面定 位 , 上线 切割机 床加 工形腔 , 这样工 件 零 件 的 热 处 理 工 序 , 对 零 件 获 得 相 应 硬 度 的 同 时 , 需 对 内 在 热 处 理 中 已完 全 变形 , 精 ; T 中就 不 会 再 变 形 。 针 还 在 b i 应 力 进 行 控 制 , 证 零 件 ) T 时 尺 寸 的 稳 定 性 防止 变 形 , 同 的 材 保 J D 不 加 工 凸模 时 , 的切 入 位 置 及 路 径 的 选 择 要 仔 细 考 虑 , 卡 方 丝 装 质 分 别 有 不 同 的 处理 方 式 。 如 了 C l 、 C S、 1 、 。 r2 9 r i 0 等 T 法和 固定 方式都要合 理 , 为线切 割加工 , 件 受力基 本为零 , 因 工 只 对 以 C l 、C S、 1 r2 9 r i 0为 材 质 的 零 件 , 粗 加 工 后 进 行 淬 火 处 要 保 证 工 件 在 加 工 中 不 移 动 就 可 以 , 装 卡 中 可 以 使 用 传 统 的 压 板 T 在 理 , 火 后 工 件 存 在 很 大 的 存 留 内应 力 , 易 导 致 精 加 工 时 工 件 开 装 卡 、 可 以 使 用 金 属 强 力 胶 粘 接 、 铁 吸 附 等 装 卡 方 式 , 精 线 淬 容 还 磁 高 裂 , 件 淬 火 后 应 趁 热 回火 , 除 淬 火 应 力 。 生 产 中 遇 到 形 状 复 杂 切 割 加 工 , 常 切 割 遍 数 为 两 次 , 以保 证 零 件 质 量 。 当 加 工 带 有 零 消 通 可 的工件 , 回火还 不足以消除淬火 应力 , 精加工前还 需进 行去应力退 锥 度 的 凹 模 时 , 本着 快 速 高 效 的 原 则 , 一 遍 粗 加 工 直 边 , 二 遍 第 第 火 或 多 次 人 工 时 效 处 理 , 分 释 放 应 力 。 对 以 崩 刃 为 主 要 失 效 形 式 锥 度 加 工 , 着 再 精 加 工 直 边 , 充 接 这样 只 精 加 工 刃 口段 直 边 , 节 约 既 时 间 又 节 约成 本 。 3 零件的磨削加工 5 表 面处 理及 组 配 磨 削加 工 采 用 的机 床 有 三 种 主 要 类 型 : 面磨 床 、 平 内外 圆 磨 床 零 件 表 面 在 加 工 时 留 下 刀 痕 、 痕 是 应 力集 中 的 地 方 , 裂 纹 磨 是 及 工 具 磨 具 。精 加 工 磨 削 时要 严 格 控 制 磨 削 变 形 , 此 , 磨 的进 扩 展 的 源 头 , 加 工 结 束 后 , 要 对 零 件 进 行 表 面 强 化 , 过 钳 工 因 精 在 需 通 刀 要 小 , 能 大 , 却 液 要 充 足 , 寸 公 差 在 OO mm 以 内 的 零 件 不 冷 尺 .1 打 磨 , 理 掉 加 工 隐患 。 工 件 的一 些棱 边 、 角 、 口进 行 倒 钝 , 处 对 锐 孔 R 要 尽 量 恒 温 磨 削 。防 止 热 变形 对 工 件 尺 寸 造 成 的 误 差 , 精 加 工 工 化 。 电加 工 表 面 会 产 生 6 1 m 左 右 的 变 质 硬 化 层 , 色 呈 灰 白 各 —O 颜 序 都 需 充 分 考 虑 这 一 因素 的影 响。 色 , 化层脆 而且 带有残 留应力 , 使用 之前要 充分 消除硬 化层 , 硬 在 精磨时选择好恰 当的磨 削砂轮十分重要 , 根据模具钢材 的具体 法为表面抛光 , 打磨去掉硬化层 。 状况, 选用 GD单晶刚玉砂轮比较适用 , 淬火硬度高的材质时 , 优先 在 磨 削 加 工 、 加 工 过 程 中 , 件 会 有 一 定 磁 化 , 有 微 弱 磁 电 工 具 采 用 有 机 粘 结 剂 的 金 刚 石 砂 轮 , 机 粘 结 剂 砂 轮 自锐 性 好 , 出 的 有 磨 十分容易 吸着 一些小铁沫 , 组装之前 , 在 要对 工件作退磁 处理 , 工 件粗 糙 可 达 R = . m。 磨 削 加 工 中 , 注 意 及 时 修 整 砂 轮 , a 02 要 保 缍装过程 中, 配一般先装模 架 , 配凸 凹模 , 后再对各 处间隙 , 装 后 然 持 砂 轮 的锐 利 , 当砂 轮 钝 化 后 会 在 工 件 表 面 滑 擦 、 压 , 成 工 件 特 别 是 凸 凹模 间 隙 进 行 组 配调 整 , 配完 成 后 要 实 施 模 具 检 测 。 对 挤 造 装 表 面烧 伤 , 度 降低 。 强 发 现的问题 , 从精加 工到粗加工 , 逐一检 查 , 直到 找出症结 , 解决 问 板 类 零 件 的加 工 大 部 分采 用平 面 磨 床 ) T , 削 时 以 精 密 平 口 题 。 J 磨 u
模具表面涂层处理的6种方式
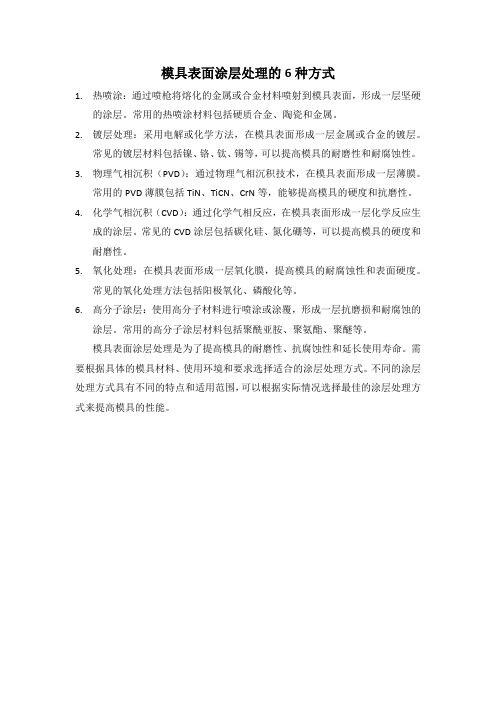
模具表面涂层处理的6种方式
1.热喷涂:通过喷枪将熔化的金属或合金材料喷射到模具表面,形成一层坚硬
的涂层。
常用的热喷涂材料包括硬质合金、陶瓷和金属。
2.镀层处理:采用电解或化学方法,在模具表面形成一层金属或合金的镀层。
常见的镀层材料包括镍、铬、钛、锡等,可以提高模具的耐磨性和耐腐蚀性。
3.物理气相沉积(PVD):通过物理气相沉积技术,在模具表面形成一层薄膜。
常用的PVD薄膜包括TiN、TiCN、CrN等,能够提高模具的硬度和抗磨性。
4.化学气相沉积(CVD):通过化学气相反应,在模具表面形成一层化学反应生
成的涂层。
常见的CVD涂层包括碳化硅、氮化硼等,可以提高模具的硬度和耐磨性。
5.氧化处理:在模具表面形成一层氧化膜,提高模具的耐腐蚀性和表面硬度。
常见的氧化处理方法包括阳极氧化、磷酸化等。
6.高分子涂层:使用高分子材料进行喷涂或涂覆,形成一层抗磨损和耐腐蚀的
涂层。
常用的高分子涂层材料包括聚酰亚胺、聚氨酯、聚醚等。
模具表面涂层处理是为了提高模具的耐磨性、抗腐蚀性和延长使用寿命。
需要根据具体的模具材料、使用环境和要求选择适合的涂层处理方式。
不同的涂层处理方式具有不同的特点和适用范围,可以根据实际情况选择最佳的涂层处理方式来提高模具的性能。
模具设计加工精度要求(更新)

研磨加工设备:厚度加工精度:±0.005,垂直度<100:0.01
2.模具制造的零件精度要求
①.模具材料精度要求
采购来料要求:所有材料均做正差0.3-0.5mm,平面度<0.2以内
精加工后尺寸要求:所有材料厚度公差控制在<0.02内
平面度公差控制在<0.01内
②.模具零件的精度要求
a.影响模具精度的导向零件采用MISUMI导柱、导套系列,公差可控制在0.02mm 以内。
度),则必须 保证模具凹凸模之间的间隙。
4.模具的结构精度要求
①. 模架精度的保证
从加工及装配角度看,模架的精度主要包括如下几个方面:
a.上、下模板的平面尺寸及导向孔位置的一致性;
b.模板大平面的平面度及平行度;
c.导向孔对大平面的垂直度;
d.模板相邻侧面间的垂直度;
e.导柱与导套间的配合精度。
模架精度的保证方法主要有: a.一次加工法 即模板的大平面加工完工后,将上、下模板一起装夹,一次加工出两块模板的平面尺 寸及导 向孔。
备注:为保证产品品质的优良和稳定,公司引进了一系列先进的生产设备,高精密的检测仪器,并重 力推行ISO900 1: 2000的的国际品质管理体系;另一方面公司广纳贤才,引用了在精密五金模具领域 10年以上工作经验的人才和技术骨干团队, 不断增强公司的技术力量。在模具制造的前期,公司对员 工进行专业技术培训和有效的激励管理,对模具设计进行评审;在模具制造的过程中由专业的品质人 员采用高精密的品检设备对模具零件进行精度检测,将模具精度有效控制在0.02以内;模具组装完成 后通过其冲压出来的合格产品进行验证,量试的产品经客户确认合格后,模具方投入正式生产......
精磨 精磨 无弯曲变形 淬火/回火 精磨 精磨 同轴度 淬火/回火 精磨/线割 无弯曲变形 淬火/回火/其他处理 线割 线割 淬火/回火/其他处理 垂直度 淬火/回火/其他处理
模具的精加工技术研究

一
14 4一
中国新技术新产品
础 产业 。据 国家 税务 总局对历 多 家工业企 业 流转税平均 负担率 的统 计 , 模具行 业 比其 他行 业 高出: 8 6 个百 分点 , 2 这与 现代模具 产业 高投 入 的产 业特 点不 协调 ,制约 了模 具工业 的发
展。
2模具 加工的过程控 制 根据模 具零件 的外 观形状不 同 , 大致可把 零件 分三类 : 、 轴类 板类与 异形零件 , 其共 同的 工艺 过程大致 为 :粗加工一 热处 理 ( 淬火 、 调 质j —精磨 一 电加 工一 钳工 ( 表面处理 ) 一组 配 加工 。 21 件热处理 .零
刘 国 滨
( 尔滨哈影 电影机械有 限公 司, 哈 黑龙江 哈 尔滨 1 00 ) 5 0 0
摘 要 : 多的零件 构成 了一 副合 格 的模 具 , 许 零件 的质 量直接 影 响 的模 具 质 量 的好 坏 。 而零 件 质量 的好 坏 是 由精 加 工技 术来保 证 的. 因此控制 好精加 工技 术是 非 常重要 的 。要 通过 对精 细加 工的有 效控 制和 改革 , 障最 终 良好 的 加工 效果 。 保
.
1我 国模 具存在的 问题 1 . 具水平落后 1模 在模具制造水平 上 , 虽然我 国有 些设备 已 达到或近世界先进水平, 但总体上要比发达国 家落 后许多。 开发能力较差 , 济效益欠佳 ; 经 与 国际水平 相比 ,模具企业管 理上 的差 距更 大。 标准化 、 化、 专业 商品化程度 低 , 模具材 料及模 具相关 技术落后 , 是造成 与国外先进 水平 差 也 距大的重要原因。模具材料性能、 质量和品种 是影响模具 质量 、 寿命和成本 的重要 因 。国 产 模具钢 品种 、 不齐全 , 档次产 品多 , 规格 低 高 质量 、 高性能 的高端 产 品少 , 工高 端模 具所 加 需的模具钢相当部分依赖进1 , 5 加工模具所需 3 的其他材 料诸 如握料 、板 材的性 能也 不 如人 意, 加之 工艺设 备落后 , 直接 影响 国产 模具 水
模具表面处理技术PPT课件
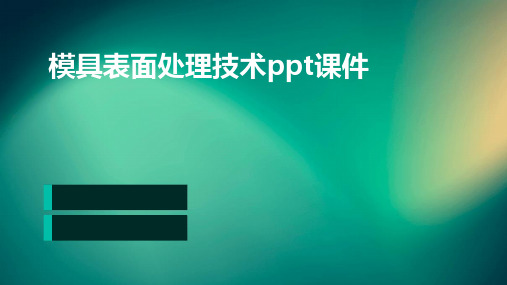
要点二
等离子喷涂技术
通过等离子喷涂将金属或非金属粉末熔融并喷射到模具表 面,形成均匀、致密的涂层,提高表面耐久性和抗腐蚀性 。
智能化和自动化技术的应用
智能监控系统
利用传感器和监测技术实时监测模具表面处理过程,实 现自动化控制和处理。
自动化处理设备
开发自动化表面处理设备,减少人工干预,提高处理效 率和一致性。
耐久性。
提高产品质量和生产效率
提高产品精度和一致性
通过表面处理技术,可以改善模具表 面的粗糙度和形貌,减小产品尺寸和 形状的误差,提高产品的精度和一致 性,从而提高生产效率。
降低生产成本
通过表面处理技术,可以提高模具的 耐磨性和耐久性,减少维修和更换模 具的频率和成本,降低生产成本。
降低生产成本
04 模具表面处理技术的优势 与挑战
提高模具使用寿命
增强模具表面硬度和耐磨 性
通过表面处理技术,可以在模具表面形成一 层高硬度的硬化层,从而提高模具的耐磨性 和抗疲劳性能,延长模具的使用寿命。
降低摩擦系数
通过表面处理技术,可以在模具表面形成一 层低摩擦系数的涂层,减小模具与材料之间 的摩擦力,降低磨损和摩擦热,提高模具的
优化生产流程
通过表面处理技术,可以优化模具的 设计和制造流程,减少加工时间和成 本,提高生产效率。
降低能耗和资源消耗
一些表面处理技术可以降低模具的能 耗和资源消耗,例如离子注入和激光 熔覆等,从而降低生产成本。
技术更新换代快
技术发展迅速
随着科学技术的不断发展,模具 表面处理技术也在不断更新换代 ,新的技术和工艺不断涌现。
常用的五金模具表面处理技术包括喷涂、电镀和化学热处理等。这些技术可以提 高模具表面的硬度和耐久性,降低生产成本和提高产品质量。
注塑模具精加工工艺流程
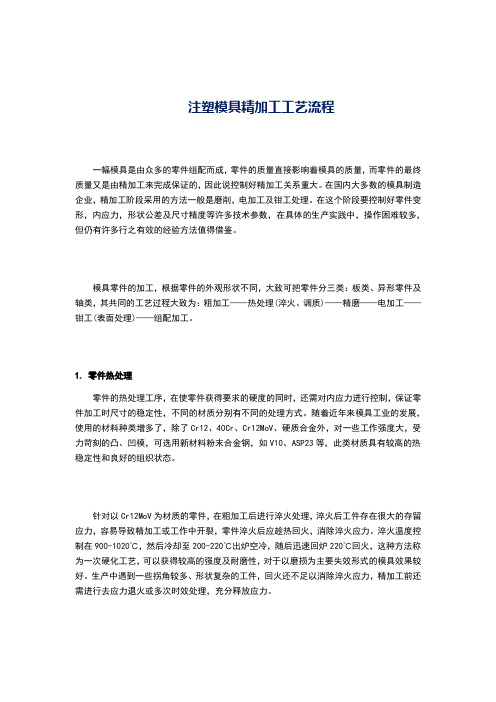
注塑模具精加工工艺流程一幅模具是由众多的零件组配而成,零件的质量直接影响着模具的质量,而零件的最终质量又是由精加工来完成保证的,因此说控制好精加工关系重大。
在国内大多数的模具制造企业,精加工阶段采用的方法一般是磨削,电加工及钳工处理。
在这个阶段要控制好零件变形,内应力,形状公差及尺寸精度等许多技术参数,在具体的生产实践中,操作困难较多,但仍有许多行之有效的经验方法值得借鉴。
模具零件的加工,根据零件的外观形状不同,大致可把零件分三类:板类、异形零件及轴类,其共同的工艺过程大致为:粗加工——热处理(淬火、调质)——精磨——电加工——钳工(表面处理)——组配加工。
1. 零件热处理零件的热处理工序,在使零件获得要求的硬度的同时,还需对内应力进行控制,保证零件加工时尺寸的稳定性,不同的材质分别有不同的处理方式。
随着近年来模具工业的发展,使用的材料种类增多了,除了Cr12、40Cr、Cr12MoV、硬质合金外,对一些工作强度大,受力苛刻的凸、凹模,可选用新材料粉末合金钢,如V10、ASP23等,此类材质具有较高的热稳定性和良好的组织状态。
针对以Cr12MoV为材质的零件,在粗加工后进行淬火处理,淬火后工件存在很大的存留应力,容易导致精加工或工作中开裂,零件淬火后应趁热回火,消除淬火应力。
淬火温度控制在900-1020℃,然后冷却至200-220℃出炉空冷,随后迅速回炉220℃回火,这种方法称为一次硬化工艺,可以获得较高的强度及耐磨性,对于以磨损为主要失效形式的模具效果较好。
生产中遇到一些拐角较多、形状复杂的工件,回火还不足以消除淬火应力,精加工前还需进行去应力退火或多次时效处理,充分释放应力。
针对V10、APS23等粉末合金钢零件,因其能承受高温回火,淬火时可采用二次硬化工艺,1050-1080℃淬火,再用490-520℃高温回火并进行多次,可以获得较高的冲击韧性及稳定性,对以崩刃为主要失效形式的模具很适用。
冲压模具表面处理方法
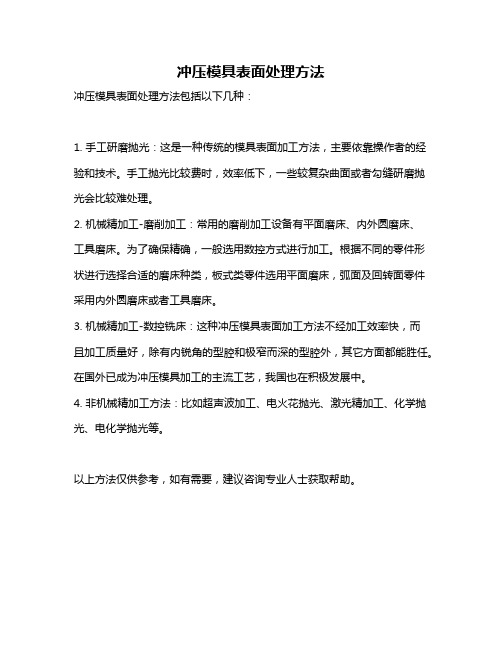
冲压模具表面处理方法
冲压模具表面处理方法包括以下几种:
1. 手工研磨抛光:这是一种传统的模具表面加工方法,主要依靠操作者的经验和技术。
手工抛光比较费时,效率低下,一些较复杂曲面或者勾缝研磨抛光会比较难处理。
2. 机械精加工-磨削加工:常用的磨削加工设备有平面磨床、内外圆磨床、
工具磨床。
为了确保精确,一般选用数控方式进行加工。
根据不同的零件形状进行选择合适的磨床种类,板式类零件选用平面磨床,弧面及回转面零件采用内外圆磨床或者工具磨床。
3. 机械精加工-数控铣床:这种冲压模具表面加工方法不经加工效率快,而
且加工质量好,除有内锐角的型腔和极窄而深的型腔外,其它方面都能胜任。
在国外已成为冲压模具加工的主流工艺,我国也在积极发展中。
4. 非机械精加工方法:比如超声波加工、电火花抛光、激光精加工、化学抛光、电化学抛光等。
以上方法仅供参考,如有需要,建议咨询专业人士获取帮助。
第十章-模具表面强化技术

*
表面化学热处理技术
二、渗氮(氮化)
(一)气体渗氮
表2 部分模具钢的气体渗氮工艺规范
牌号
处理 方法
渗氮工艺规范
渗氮层 深度/mm
表面硬度
阶段
渗氮温度/℃
时间/h
氨分解率/%
30CrMnSiA
一段
—
500±5
25~30
20~30
0.2~0.3
(一)气体渗氮
(1) 经过渗氮后钢表面形成一层极硬的合金氮化物,渗氮层的硬度一般可达到68~72HRC,不需要再经过淬火便具有很高的表面硬度和耐磨层,而且还可以保持到600~650℃而不明显下降。
(2) 渗氮后钢的疲劳极限可提高15%~35%。这是由于渗氮层的体积增大,使工件表面产生了残余压应力。
(3) 渗氮后的钢具有很高的抗腐蚀能力。
>58HRC
Cr12MoV
760~800HV
*
表面化学热处理技术
二、渗氮(氮化)
(二)离子渗氮
离子渗氮有如下特点:
(1) 渗氮速度快,生产周期短。
(2) 渗氮层质量高。
(3) 工件的变形小。
(4) 对材料的适应性强。
氮碳共渗
提高硬度、耐磨性、抗粘附性、抗蚀性、耐热疲劳性
冷挤模、拉深模、挤压模穿孔针
渗硼
具有极好的表面硬度、耐磨性、抗粘附性、抗氧化性、热硬性、良好的抗蚀性
挤压模、拉深模
碳氮硼三元共渗
提高硬度、强度、耐磨性、耐疲劳性、抗蚀性
挤压模、冲头针尖
盐浴覆层 (TD处理)
提高硬度、耐磨性、耐热疲劳性、抗蚀性、抗粘附性、抗氧化性
- 1、下载文档前请自行甄别文档内容的完整性,平台不提供额外的编辑、内容补充、找答案等附加服务。
- 2、"仅部分预览"的文档,不可在线预览部分如存在完整性等问题,可反馈申请退款(可完整预览的文档不适用该条件!)。
- 3、如文档侵犯您的权益,请联系客服反馈,我们会尽快为您处理(人工客服工作时间:9:00-18:30)。
模具表面精加工
模具表面精加工是模具加工中未能很好解决的难题之一,也正是模具钳工劳动强度大、成为模具加工瓶颈的原因之一。
特别反映在硬度较大的金属、压铸模具进行最后组装过程。
我国目前仍以手工研磨抛光为主,不仅质量不稳定、周期长,而且工人作业环境差,制约了我国铸造模具向更高层次发展。
对于模具复杂型腔和一些狭缝的曲面精加工,传统的机加工方法已无法胜任,必须采用其它的工艺措施,如电化学或电化学机械光整加工技术。
随着科学技术的不断发展,各种模具的加工工艺要求越来越高。
提高模具抛光的速度和质量使我国模具制造工艺达到世界先进水平,已成为刻不容缓的重要课题。
在模具表面精加工技术中,主要的可以分为两大部分,即传统精加工技术和非传统精加工技术。
传统精加工技术主要是以手工研磨抛光为主和现在发展起来的机械精加工;非传统精加工主要包括化学抛光、电化学抛光、电解研磨、电化学机械光整加工、超声波加工、磁流变抛光、激光抛光技术以及电火花抛光等。
下面就主要的加工方法和工具进行介绍。
图1 各种加工方法所得表面形貌对比
1. 方法与设备
(1) 手工研磨抛光
该方法是传统模具精加工所采用的主要手段,也是我国目前仍广泛采用的方法之一。
该方法不需要特殊的设备,适应性比较强,主要依赖于操作者的经验技艺水平,但效率低(约占整个模具周期的1/3),且工人劳动强度大,质量不稳定,制约了我国模具加工向更高层次发展。
但就目前的社会经济技术发展状况,暂时还不能完全淘汰这种加工手段。
(2) 数字式模具抛光机
最近看到一款数字抛光机的报道,这种抛光工具采用数字化控制,数字式显示和控制工艺参数,备有整套磨头及磨料,半自动抛光,具有体积小、使用方便的优点。
其工艺特点主要有:
具有平整功能,最大可平整的波纹长度为75mm。
和手工抛光相比,功效提高一倍,质量提高一个数量级。
质量稳定,重复性好。
应用围:a,材料:各种模具材料,包括铸钢、锻钢、铝合金及锌基合金。
b,模具表面尺寸:100×100-1,500×3,000mm。
(3) 超声波模具抛光机
该抛光工具采用高频电火花脉冲电源与超声波快速振动研磨的原理进行抛光。
它能完成一般抛光工具(电磨软轴等)难以伸入的窄槽、窄缝、边、角等曲折部位的抛光,抛光后不塌棱角,不影响模具的精度。
该工具可以解决用户过去因工件形状复杂难以达到抛光要求这一难题。
并且缩短了抛光时间提高了工作效率。
为了提高粗糙度大于Ra1.6工件的抛光速度,工具采用超声波与专用的高频窄脉冲高峰值电流的脉冲电源复合进行抛光,由超声波的冲击和电脉冲的腐蚀同时作用于工件表面,能迅速降低其粗糙度,对各种特殊加工后的粗硬表面十分有效。
采用该工具进行抛光,可快速对粗糙表面整形抛光,不受工件形状、材料硬度限制,对原始表面粗糙度没有要求,功效比较高。
(4)用高速铣削技术作为模具半精加工和精加工的手段
从80年代以来,随着高速铣削技术的成熟与发展,模具型面加工已多采用此项加工工艺手段,用EDM进行模具型面精加工和抛光的工艺已逐渐减少,这主要是因为:除有锐角的型腔和极窄而深的型腔外,基本都可用高速铣削代替ED M加工;采用高速铣削加工模具型面可比EDM加工节省25%~60%加工工时;高速铣削的型面表面质量好,可避免EDM加工可能出现的表面微细型纹;高速铣削能加工45~60HRC硬表面,精铣面粗糙度可达Ra=0.63mm,减少手工抛光工时;省却EDM加工电极的制造环节,显著缩短制模周期。
“高速铣削”在德国和日本已成为模具半精加工、精加工的主流工艺手段,我国正积极发展中。
(5) 电化学和电化学机械光整加工
电化学及其复合光整加工技术主要是靠金属工件的电化学阳极溶解原理来加工,属于离子的去除。
且因为是非接触加工,没有加工变形层、变质层和残余应力;工具无磨损,可以长期应用;不产生飞边及毛刺。
图1为各种加工方法所得表面形貌对比。
图2 电化学机械精整加工效果图
图2为理工大学周锦进教授课题组用电化学机械方法对轴承进行的光整加工。
它取代滚道超精工艺,可以大幅度提高滚道表面质量,改善和弥补磨加工缺陷,粗糙度、波纹度及圆度与滚道超精后的“三度”相比量化后的精度储备在80%以上。
采用电化学机械加工比一般超精加工的寿命可提高5倍以上。
虽然这里以轴承为例,但该技术同样完全可以应用到模具表面的精整加工中。
2. 模具表面精加工的发展趋势
模具研磨抛光将向自动化、智能化方向发展。
日本已研制了数控研磨机,可实现三维曲面模具的自动化研磨抛光。
另外,由于模具型腔形状复杂,任何一种研磨抛光方法都有一定局限性。
应注意发展特种研磨与抛光方法,如挤压研磨、电化学抛光、超声抛光以及复合抛光工艺与装备,以提高模具表面质量。
随着模具向精密化和大型化方向发展,加工精度超过1mm的超精加工技术和集电、化学、超声波、激光等技术综合在一起的复合加工将得到发展。
兼备两种以上工艺特点的复合加工技术在今后的模具制造中前景广阔。
模具表面精加工中的磨削加工
磨削加工采用的机床有三种主要类型:平面磨床、外圆磨床及工具磨具。
精加工磨削时要严格控制磨削变形和磨削裂纹的产生,即使是十分微小的裂纹,在后续的加工使用中也会显露出来。
因此,精磨的进刀要小,不能大,冷却液要充分,
尺寸公差在0.01mm以的零件要尽量恒温磨削。
由计算可知,300mm长的钢件,温差3℃时,材料有10.8mm左右的变化,10.8=1.2×3×3(每100mm 变形量1.2mm/℃),各精加工工序都需充分考虑这一因素的影响。
精磨时选择好恰当的磨削砂轮十分重要,针对模具钢材的高钒高钼状况,选用G D单晶刚玉砂轮比较适用,当加工硬质合金、淬火硬度高的材质时,优先采用有机粘结剂的金刚石砂轮,有机粘结剂砂轮自磨利性好,磨出的工件粗糙可达Ra =0.2mm,近年来,随着新材料的应用,CBN砂轮,也即立方氮化硼砂轮显示出十分好的加工效果,在数控成型磨,坐标磨床,CNC外圆磨床上精加工,效果优于其它种类砂轮。
磨削加工中,要注意及时修整砂轮,保持砂轮的锐利,当砂轮钝化后,会在工件表面滑擦、挤压,造成工件表面烧伤,强度降低。
板类零件的加工大部分采用平面磨床加工,在加工中常会遇到一种长而薄的薄板零件,此类零件的加工较难。
因为加工时,在磁力的吸附作用下,工件产生形变,紧贴于工作台表面,当拿下工件后,工件又会产生回复变形,厚度测量一致,但平行度达不到要求,解决的办法可采用隔磁磨削法,磨削时以等高块垫在工件下面,四面挡块抵死,加工时小进刀,多光刀,加工好一面后,可不用再垫等高块,直接吸附加工,这样可改善磨削效果,达到平行度要求。
轴类零件具有回转面,其加工广泛采用外圆磨床及工具磨床。
加工过程中,头架及顶尖相当于母线,如果其存在跳动问题,加工出来的工件同样会产生此问题,影响零件的质量,因此在加工前要做好头架及顶尖的检测工作。
进行孔磨削时,
冷却液要充分浇到磨削接触位置,以利于磨削的顺利排出。
加工薄壁轴类零件,最好采用夹持工艺台,夹紧力不可过大,否则容易在工件圆周上产生“三角”变形。
发布时。